Top 30 Warehouse Manager Interview Questions and Answers [Updated 2025]
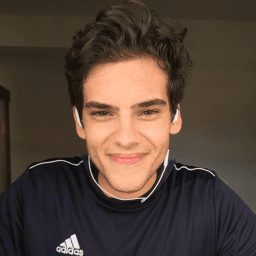
Andre Mendes
•
March 30, 2025
Navigating the competitive landscape of warehouse management requires not only skill but also the ability to effectively communicate your expertise during interviews. In this post, we delve into the most common interview questions for the Warehouse Manager role, providing insightful example answers and practical tips to help you respond confidently and effectively. Prepare to showcase your qualifications and stand out in your next interview with ease.
Download Warehouse Manager Interview Questions in PDF
To make your preparation even more convenient, we've compiled all these top Warehouse Managerinterview questions and answers into a handy PDF.
Click the button below to download the PDF and have easy access to these essential questions anytime, anywhere: