Top 30 Warehouse Manager Interview Questions and Answers [Updated 2025]
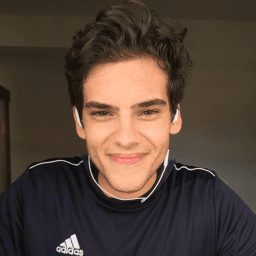
Andre Mendes
•
March 30, 2025
Navigating the competitive landscape of warehouse management requires not only skill but also the ability to effectively communicate your expertise during interviews. In this post, we delve into the most common interview questions for the Warehouse Manager role, providing insightful example answers and practical tips to help you respond confidently and effectively. Prepare to showcase your qualifications and stand out in your next interview with ease.
Get Warehouse Manager Interview Questions PDF
Get instant access to all these Warehouse Manager interview questions and expert answers in a convenient PDF format. Perfect for offline study and interview preparation.
Enter your email below to receive the PDF instantly: