Top 31 Wheel Aligner Interview Questions and Answers [Updated 2025]
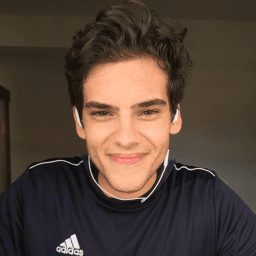
Andre Mendes
•
March 30, 2025
Preparing for a wheel aligner interview can be daunting, but we've got you covered. In this blog post, you'll find the most common interview questions for the wheel aligner role, complete with example answers and insightful tips to help you respond confidently and effectively. Whether you're a seasoned professional or a newcomer, this guide will equip you with the tools to succeed and impress your potential employers.
Download Wheel Aligner Interview Questions in PDF
To make your preparation even more convenient, we've compiled all these top Wheel Alignerinterview questions and answers into a handy PDF.
Click the button below to download the PDF and have easy access to these essential questions anytime, anywhere:
List of Wheel Aligner Interview Questions
Behavioral Interview Questions
Can you describe a time when you had to troubleshoot a complex wheel alignment issue?
How to Answer
- 1
Start with a specific example from your experience
- 2
Explain the issue clearly and concisely
- 3
Describe the steps you took to diagnose the problem
- 4
Mention any tools or techniques you used
- 5
Conclude with the outcome and what you learned
Example Answers
During a routine alignment, I noticed that the vehicle was pulling to the right. I first checked tire pressures and verified they were correct. Next, I used the alignment machine to check the camber and toe settings, which were off. After adjusting those, I test drove the vehicle and confirmed it drove straight. This taught me the importance of double-checking all settings before making adjustments.
Tell me about a time when you worked as part of a team to achieve a challenging goal in vehicle service.
How to Answer
- 1
Choose a specific team project you were part of.
- 2
Outline the goal clearly and explain why it was challenging.
- 3
Describe your individual contribution to the team's efforts.
- 4
Highlight teamwork and collaboration aspects.
- 5
Mention the positive outcome and what you learned.
Example Answers
In my previous role, our team had to align the wheels on a fleet of delivery trucks before a major deadline. The challenge was that we had limited time and resources. I organized the schedule for the team, ensuring everyone knew their roles and that we had the correct equipment ready. Our collaboration allowed us to complete the project ahead of time, improving the fleet's operational efficiency. I learned the importance of clear communication in achieving team goals.
Don't Just Read Wheel Aligner Questions - Practice Answering Them!
Reading helps, but actual practice is what gets you hired. Our AI feedback system helps you improve your Wheel Aligner interview answers in real-time.
Personalized feedback
Unlimited practice
Used by hundreds of successful candidates
Describe how you communicated technical issues to non-technical team members or customers.
How to Answer
- 1
Use clear and simple language, avoid jargon.
- 2
Provide analogies or examples that relate to common experiences.
- 3
Be honest about the technical issue but remain positive about the solution.
- 4
Encourage questions to ensure understanding.
- 5
Follow up with written summaries if necessary.
Example Answers
In my last role, we had a recurring issue with the wheel alignment process that affected vehicle handling. I explained it to our sales team by comparing it to adjusting the wheels on a shopping cart to ensure it rolls straight. This made it relatable and they understood the importance of technical precision.
Provide an example of a situation where you had to adapt to a new technology or tool in your alignment work.
How to Answer
- 1
Think of a specific technology or tool you used recently.
- 2
Explain the context and why the change was necessary.
- 3
Describe how you approached learning the new technology.
- 4
Highlight the impact of adapting to this new tool on your work.
- 5
Conclude with any feedback you received or results achieved.
Example Answers
At my previous job, we upgraded to a new computer-based alignment system. I took the initiative to learn it before it was rolled out by spending time with the manual and online tutorials. This allowed me to assist my colleagues during the transition, and as a result, we completed alignments more efficiently and reduced errors.
Describe a time when your attention to detail helped prevent a major issue during an alignment service.
How to Answer
- 1
Think of a specific incident where details mattered.
- 2
Explain the steps you took to address the situation.
- 3
Highlight the outcome and how it affected the customer or service quality.
- 4
Use metrics or clear results if possible, such as improved vehicle performance.
- 5
Keep it concise and focused on your role in the situation.
Example Answers
During a routine alignment, I noticed uneven tire wear patterns that indicated incorrect pressure. I double-checked the tire specifications and found that one tire was over-inflated. Correcting this not only prevented further tire damage but also ensured optimal vehicle handling for the customer.
Have you ever trained or mentored a junior technician? Describe that experience.
How to Answer
- 1
Share a specific instance where you trained someone.
- 2
Highlight the skills or knowledge you imparted.
- 3
Discuss the methods you used to explain concepts.
- 4
Mention how you assessed their understanding.
- 5
Reflect on the outcome of the training experience.
Example Answers
I mentored a junior technician last year when he joined our team. I focused on teaching him the basic diagnostic techniques for wheel alignment. I used hands-on demonstrations and regular check-ins to ensure he understood the processes. Over time, he became proficient and even started helping to train other new hires.
Give an example of how you have taken feedback from a supervisor and applied it to your work.
How to Answer
- 1
Identify a specific piece of feedback you received.
- 2
Explain how you processed and understood that feedback.
- 3
Describe the specific action you took after receiving the feedback.
- 4
Mention the outcome or improvement resulting from your action.
- 5
Keep the example related to wheel alignment or automotive work.
Example Answers
During my last job, my supervisor noted that my wheel alignment measurements could be more precise. I took this feedback seriously and began to double-check my readings using a calibration tool. As a result, my alignment accuracy improved, which led to fewer customer complaints and a more efficient workflow.
Technical Interview Questions
What are the key factors to consider when performing a wheel alignment?
How to Answer
- 1
Check tire pressure and condition before alignment
- 2
Verify that suspension components are in good condition
- 3
Ensure the vehicle is on a level surface during alignment
- 4
Use the manufacturer's specifications for alignment angles
- 5
Test drive after alignment to confirm handling and tracking
Example Answers
It's important to start with checking tire pressure and overall tire condition, then ensure that all suspension components are in good shape. The vehicle must be on a level surface, and we should always follow the manufacturer's specifications for alignment angles to guarantee accuracy.
Can you explain how to operate a laser alignment system?
How to Answer
- 1
Start by explaining the setup of the laser alignment system, including the importance of ensuring the vehicle is on a level surface.
- 2
Describe the calibration process of the laser units before use to ensure accuracy in measurements.
- 3
Outline how to position the laser units on the wheels and how to read the measurements from the display.
- 4
Mention the significance of making adjustments based on the readings to align the vehicle properly.
- 5
Conclude with safety considerations, ensuring that the system is turned off and stored correctly after use.
Example Answers
To operate a laser alignment system, first set up the system on a level surface and ensure the vehicle is properly positioned. Next, calibrate the laser units according to the manufacturer's instructions. Attach the laser units to each wheel and take note of the readings on the display. Adjust the alignment based on these readings, ensuring to follow the correct specs for wheel alignment. Finally, make sure to turn off the system and store it safely after use.
Don't Just Read Wheel Aligner Questions - Practice Answering Them!
Reading helps, but actual practice is what gets you hired. Our AI feedback system helps you improve your Wheel Aligner interview answers in real-time.
Personalized feedback
Unlimited practice
Used by hundreds of successful candidates
How do you diagnose uneven tire wear issues related to wheel alignment?
How to Answer
- 1
Examine the tire wear pattern closely to identify specific issues.
- 2
Check the tire pressure to rule out improper inflation as a cause.
- 3
Measure the alignment angles using appropriate equipment.
- 4
Look for signs of suspension or steering component wear.
- 5
Consult the vehicle's service history for past alignment issues.
Example Answers
First, I would inspect the tire wear pattern. If I see more wear on the inner or outer edges, it usually indicates a misalignment. I would then check tire pressure to ensure it's at the correct level. After that, I'd perform an alignment check with precise tools to measure camber and toe angles.
What safety protocols do you follow while performing a wheel alignment?
How to Answer
- 1
Always wear appropriate personal protective equipment like gloves and safety glasses.
- 2
Ensure the vehicle is properly secured on the alignment rack before starting any work.
- 3
Use wheel chocks to prevent the vehicle from rolling during the alignment process.
- 4
Check that all tools and equipment are in good condition and properly calibrated.
- 5
Follow manufacturer guidelines for the specific vehicle being aligned.
Example Answers
I always wear safety glasses and gloves, secure the vehicle with wheel chocks, and make sure it's on a stable alignment rack before starting.
Explain how camber, caster, and toe affect vehicle handling and tire wear.
How to Answer
- 1
Define camber, caster, and toe in simple terms.
- 2
Explain the effects of camber on cornering stability and tire contact.
- 3
Describe how caster contributes to steering feel and stability.
- 4
Discuss toe settings and their impact on tire wear and handling.
- 5
Use examples to illustrate the practical implications of these angles.
Example Answers
Camber refers to the tilt of the wheels. Positive camber can improve cornering at the cost of inside tire wear, while negative camber offers better grip during turns. Caster helps maintain straight-line stability and affects steering response; more caster can mean more effort in turning but better stability. Toe affects tire wear; toe-in can lead to better straight-line stability but excessive toe-in causes inside tire wear.
What common tools do you use in wheel alignment, and how do you use them?
How to Answer
- 1
List specific tools like alignment machines and tools for adjusting toe, camber, or caster.
- 2
Explain the basic function of each tool you mention.
- 3
Share a brief description of how you use each tool in a typical wheel alignment procedure.
- 4
Mention any experience with specific brands or models that you are proficient with.
- 5
Be prepared to discuss why each tool is important in the alignment process.
Example Answers
I commonly use a digital alignment machine that measures angles like camber and toe. I set up the vehicle on the machine and adjust the wheels according to the manufacturer's specifications. Additionally, I use a torque wrench to ensure that all adjustments are correctly tightened.
What differences in alignment procedures can you identify between front-wheel and four-wheel drive vehicles?
How to Answer
- 1
Identify the key differences in the wheel alignment process for each type.
- 2
Discuss how drivetrain layout affects alignment specifications.
- 3
Mention any additional components specific to four-wheel drive vehicles.
- 4
Highlight the importance of adjustment points for each vehicle type.
- 5
Consider the impact on tire wear and handling for both alignments.
Example Answers
Front-wheel drive vehicles primarily require alignment adjustments at the front wheels due to the drivetrain, while four-wheel drive vehicles may involve aligning both front and rear wheels due to a more complex system including transfer cases and differentials.
How many different vehicle makes and models have you performed alignments on?
How to Answer
- 1
List a variety of makes and models you have worked with
- 2
Emphasize experience with both common and less common brands
- 3
Mention any specialized vehicles like trucks or performance cars
- 4
Include the total count if possible for quantifiable evidence
- 5
Share any training or certifications that enhanced your alignment skills
Example Answers
I have performed alignments on over 50 different makes and models, including popular ones like Ford, Toyota, and Honda, as well as specialty brands like Tesla and Land Rover.
Can you explain the procedure for aligning a vehicle with adjustable suspension components?
How to Answer
- 1
Start with the vehicle on a level surface.
- 2
Check the tire pressure and condition before beginning.
- 3
Use an alignment machine to read the current angles.
- 4
Adjust camber, caster, and toe based on the manufacturer's specifications.
- 5
After adjustments, check the alignment again to confirm accuracy.
Example Answers
First, I place the vehicle on a level surface and ensure the tires are properly inflated. Then, I use an alignment machine to measure the current alignment angles. I adjust the camber, caster, and toe using the manufacturer's specifications. Finally, I double-check the alignment to ensure it meets the required standards.
How do you analyze alignment data to determine necessary adjustments?
How to Answer
- 1
Review the alignment specifications for the vehicle model.
- 2
Use diagnostic tools to gather and record alignment data.
- 3
Compare current alignment measurements against the specifications.
- 4
Identify any deviations or inconsistencies in angles.
- 5
Determine the corrections needed and document the recommended adjustments.
Example Answers
I start by checking the manufacturer's alignment specifications for the vehicle. After gathering data using alignment tools, I compare the actual measurements to these specs. If there are discrepancies, I note what needs adjusting, such as camber or toe, and plan the corrections accordingly.
Don't Just Read Wheel Aligner Questions - Practice Answering Them!
Reading helps, but actual practice is what gets you hired. Our AI feedback system helps you improve your Wheel Aligner interview answers in real-time.
Personalized feedback
Unlimited practice
Used by hundreds of successful candidates
What industry standards do you follow for wheel alignments?
How to Answer
- 1
Mention specific standards such as SAE and ISO that apply to wheel alignment.
- 2
Discuss the importance of manufacturer specifications for each vehicle.
- 3
Talk about using alignment equipment calibrated to industry standards.
- 4
Highlight the need for ongoing training and certification in wheel alignment.
- 5
Emphasize the significance of following safety protocols and best practices during wheel alignments.
Example Answers
I follow the SAE J1234 standard for wheel alignment which helps ensure precision and accuracy. I also strictly adhere to the manufacturer's specifications for each vehicle to guarantee optimal performance.
Situational Interview Questions
If a customer complains about their steering after an alignment, how would you handle the situation?
How to Answer
- 1
Listen carefully to the customer's concerns and take detailed notes
- 2
Apologize for any inconvenience caused and assure them you will help
- 3
Ask specific questions to understand their issue better, like when it occurs
- 4
Check the alignment settings and inspect for any possible errors
- 5
Communicate clearly about the next steps and follow up with them after the service
Example Answers
I would first listen to the customer's complaint, apologize for any inconvenience, and ask what specific issues they are experiencing with the steering. Then, I'd check the alignment settings and verify if any adjustments are necessary. Finally, I would explain the steps I'm taking and reassure them that I'll resolve the issue promptly.
Imagine a disagreement arises between you and a technician about alignment specifications. How would you resolve it?
How to Answer
- 1
Stay calm and listen to the technician's perspective.
- 2
Ask questions to understand the reasons behind their point of view.
- 3
Refer to manufacturer specifications and industry standards during the discussion.
- 4
Suggest a practical test to evaluate both viewpoints if applicable.
- 5
Aim to reach a consensus that prioritizes vehicle safety and performance.
Example Answers
I would first listen to the technician's concerns to understand their reasoning. Then, I would refer to the provided specifications to ensure we're on the same page. If we still disagree, I would suggest conducting a test alignment to see which method yields better results.
Don't Just Read Wheel Aligner Questions - Practice Answering Them!
Reading helps, but actual practice is what gets you hired. Our AI feedback system helps you improve your Wheel Aligner interview answers in real-time.
Personalized feedback
Unlimited practice
Used by hundreds of successful candidates
You have multiple vehicles waiting for alignment. How would you prioritize and manage your time?
How to Answer
- 1
Assess the urgency based on customer needs or appointment times
- 2
Evaluate the complexity of each alignment job
- 3
Consider potential for quick fixes to maximize output
- 4
Organize vehicles by type, prioritizing those that are easier to align first
- 5
Communicate clearly with your team and customers about wait times
Example Answers
I would first look at the appointment schedule and prioritize vehicles based on their arrival times and customer needs. Then I would assess which vehicles have simpler alignments and tackle those first to keep up the workflow. After that, I’d communicate with customers to let them know about estimated wait times.
Suppose a vehicle comes in that has a complicated suspension setup. How would you approach the alignment?
How to Answer
- 1
Assess the suspension setup thoroughly before starting any alignment work
- 2
Use specific tools designed for complex suspensions, like advanced alignment machines
- 3
Check manufacturer specifications for optimal alignment angles
- 4
Evaluate any previous alignment history and adjustments made
- 5
Test drive the vehicle after alignment to ensure proper handling
Example Answers
First, I would review the suspension design carefully, then use an advanced alignment machine to get precise measurements according to the manufacturer's specs.
If you notice a potential mechanical issue while aligning a vehicle, what steps would you take?
How to Answer
- 1
Identify the specific mechanical issue clearly
- 2
Document the issue with detailed notes
- 3
Communicate the findings to the technician or supervisor promptly
- 4
Stop the alignment process to avoid further issues
- 5
Suggest a thorough inspection or repair before proceeding
Example Answers
I would first identify and document the mechanical issue I noticed. Then, I'd inform my supervisor or technician immediately to ensure we address it before continuing with the alignment.
What would you do if you needed to ensure compliance with new safety regulations for wheel alignment?
How to Answer
- 1
Review the new safety regulations thoroughly to understand all requirements.
- 2
Train staff on the new procedures to ensure everyone is informed and compliant.
- 3
Implement a checklist system to ensure all safety protocols are followed during wheel alignment.
- 4
Schedule regular audits of the wheel alignment process to assess compliance.
- 5
Stay updated on any future regulatory changes to maintain ongoing compliance.
Example Answers
I would start by reviewing the new safety regulations to fully understand them. Then, I would organize a training session for the team to ensure everyone knows the new procedures. To maintain compliance, I would create a checklist that mechanics can use during each wheel alignment.
How would you improve the efficiency of the alignment process in your shop?
How to Answer
- 1
Implement regular maintenance checks on alignment equipment to prevent downtime.
- 2
Train staff on the latest alignment techniques to reduce errors and speed up the process.
- 3
Streamline the workflow by arranging tools and equipment for easy access during the alignment.
- 4
Use digital alignment systems to quickly analyze and adjust wheel angles.
- 5
Set up a checklist to ensure all steps are completed efficiently without missing any important tasks.
Example Answers
To improve efficiency, I would schedule regular maintenance for our alignment equipment to avoid unexpected breakdowns. Training my team on the latest techniques would also help minimize mistakes and speed up our workflow.
If you notice that equipment is not functioning properly, what steps would you take to address this?
How to Answer
- 1
Immediately assess the specific issue with the equipment.
- 2
Refer to the equipment manual for troubleshooting steps.
- 3
Isolate the equipment and inform your supervisor about the problem.
- 4
Check for any safety issues before attempting repairs.
- 5
Document the issue and the steps taken for future reference.
Example Answers
I would first determine the exact nature of the malfunction and refer to the manual to troubleshoot. If I couldn't resolve it, I'd isolate the equipment and notify my supervisor, ensuring no safety risks.
How would you handle the stress of a busy shop during peak hours while performing alignments?
How to Answer
- 1
Prioritize tasks and focus on one alignment at a time.
- 2
Maintain clear communication with teammates about workload and progress.
- 3
Stay organized with tools and equipment to avoid delays.
- 4
Take deep breaths and stay calm to think clearly under pressure.
- 5
Use experience to predict and plan for busy times to manage workflow.
Example Answers
During peak hours, I focus on one alignment at a time and make sure I have everything ready before I begin. This helps me stay efficient and keep stress levels down.
If you've tried to fix a persistent alignment issue without success, how would you approach it next?
How to Answer
- 1
Review the alignment history and previous adjustments made.
- 2
Check for any component wear or damage affecting alignment.
- 3
Consult with team members for any insights or alternative approaches.
- 4
Consider using diagnostic tools or equipment to gather more data.
- 5
Ensure that all specifications are being correctly adhered to.
Example Answers
First, I would review the previous alignment history to see what has been attempted. Then I would check for any worn components that might be causing issues. If the problem persists, I would consult with my colleagues to see if anyone has experienced similar issues, and consider using diagnostic tools to gather more data for precise adjustments.
Don't Just Read Wheel Aligner Questions - Practice Answering Them!
Reading helps, but actual practice is what gets you hired. Our AI feedback system helps you improve your Wheel Aligner interview answers in real-time.
Personalized feedback
Unlimited practice
Used by hundreds of successful candidates
How would you implement a new tool or technique for wheel alignment in your shop?
How to Answer
- 1
Assess the current alignment process to identify areas for improvement
- 2
Research and select a beneficial tool or technique that fits our needs
- 3
Train staff on the new tool to ensure everyone is proficient
- 4
Implement the tool in a phased approach to monitor effectiveness
- 5
Gather feedback and make adjustments based on staff and customer experiences
Example Answers
I would start by analyzing our current alignment methods, then research state-of-the-art tools that could enhance our accuracy. I'll propose the best option and organize training sessions for all technicians. We can introduce it gradually over a month to ensure smooth adaptation and collect feedback.
Wheel Aligner Position Details
Recommended Job Boards
CareerBuilder
www.careerbuilder.com/jobs/wheel-alignerZipRecruiter
www.ziprecruiter.com/Jobs/Wheel-AlignerThese job boards are ranked by relevance for this position.
Related Positions
- Wheel Alignment Mechanic
- Headlight Adjuster
- Wheelwright
- Motor Tune-Up Specialist
- Light Adjuster
- Brake Adjuster
- Vehicle Mechanic
- Undercar Specialist
- Car Mechanic
- Automobile Mechanic
Similar positions you might be interested in.
Ace Your Next Interview!
Practice with AI feedback & get hired faster
Personalized feedback
Used by hundreds of successful candidates
Ace Your Next Interview!
Practice with AI feedback & get hired faster
Personalized feedback
Used by hundreds of successful candidates