Top 28 Wheel Alignment Mechanic Interview Questions and Answers [Updated 2025]
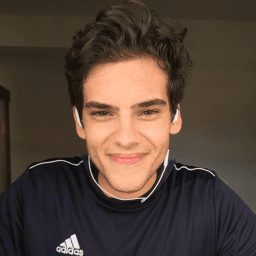
Andre Mendes
•
March 30, 2025
Preparing for a wheel alignment mechanic interview can be daunting, but we're here to help. In this post, you'll find the most common interview questions for this crucial role, complete with example answers and tips for responding effectively. Whether you're a seasoned professional or new to the field, this guide will equip you with the insights needed to impress your interviewers and secure the job.
Download Wheel Alignment Mechanic Interview Questions in PDF
To make your preparation even more convenient, we've compiled all these top Wheel Alignment Mechanicinterview questions and answers into a handy PDF.
Click the button below to download the PDF and have easy access to these essential questions anytime, anywhere:
List of Wheel Alignment Mechanic Interview Questions
Behavioral Interview Questions
Describe a time when you faced a difficult wheel alignment issue. How did you diagnose and resolve it?
How to Answer
- 1
Start by briefly describing the issue and its symptoms.
- 2
Explain the diagnostic steps you took to identify the root cause.
- 3
Discuss the specific tools or techniques you used in the process.
- 4
Share the solution you implemented and the outcome achieved.
- 5
Conclude with what you learned from that experience.
Example Answers
I once encountered a vehicle that pulled to the right despite correct settings. I checked tire pressure and found a significant difference in the front tires. After equalizing the pressure, I re-aligned the wheels, and the issue resolved completely, teaching me to always check tire conditions first.
Can you give an example of how you worked with a team to complete a complex wheel alignment project?
How to Answer
- 1
Choose a specific project you worked on.
- 2
Explain your role and contributions to the team.
- 3
Specify the challenges you faced and how the team overcame them.
- 4
Highlight the outcome of the project.
- 5
Mention any feedback from the team or customers.
Example Answers
In a recent project, our team was tasked with aligning the wheels of a fleet of trucks. I was responsible for diagnosing alignment issues and coordinating with the other mechanics. We faced a challenge when we discovered uneven tire wear on several vehicles. We worked together to develop a plan to rotate the tires and adjust the alignment accordingly. As a result, we improved the fleet's handling and extended tire life, receiving positive feedback from the fleet manager.
Don't Just Read Wheel Alignment Mechanic Questions - Practice Answering Them!
Reading helps, but actual practice is what gets you hired. Our AI feedback system helps you improve your Wheel Alignment Mechanic interview answers in real-time.
Personalized feedback
Unlimited practice
Used by hundreds of successful candidates
Tell me about a time you had to explain a wheel alignment issue to a customer. How did you ensure they understood?
How to Answer
- 1
Choose a specific example from your experience.
- 2
Describe the issue clearly and simply.
- 3
Use analogies or visuals if possible.
- 4
Ask if they have any questions during your explanation.
- 5
Summarize the main points to reinforce understanding.
Example Answers
Once, I had a customer who was confused about why their car was pulling to one side. I explained that their alignment was off due to hitting a pothole. I used a diagram of the wheels to show how alignment affects tire wear and handling. I asked if they had any questions and made sure to clarify everything before they left.
Describe a situation where you had to learn a new skill or technique related to wheel alignment quickly. How did you handle it?
How to Answer
- 1
Identify the specific skill or technique that was new.
- 2
Explain the context and why it was necessary to learn it quickly.
- 3
Discuss the resources you used to learn the skill, like manuals or online tutorials.
- 4
Highlight how you practiced and applied the skill in a real situation.
- 5
Conclude with the outcome of your learning and how it benefited your work.
Example Answers
In my previous job, we upgraded to a new wheel alignment machine that used digital technology. I had to learn how to operate it within a day to handle the incoming work. I quickly read the manual and watched instructional videos provided by the manufacturer. After a few practice runs during a quieter moment in the shop, I successfully completed my first alignment using the new machine, which helped improve our efficiency significantly.
Tell me about an experience where your attention to detail prevented a potential issue with a vehicle's wheel alignment.
How to Answer
- 1
Recall a specific instance where your observation made a difference.
- 2
Explain how you identified the alignment issue prior to it becoming critical.
- 3
Describe the steps you took to correct the alignment or prevent the problem.
- 4
Highlight any feedback you received from the customer or employer acknowledging your work.
- 5
Emphasize the importance of attention to detail in your role as a mechanic.
Example Answers
In one instance, during a routine alignment check, I noticed uneven tire wear that indicated a potential misalignment issue. I double-checked the alignment specs and adjusted the angles, which improved the vehicle’s handling. The customer appreciated my thoroughness when I explained the situation.
Give an example of feedback you received from a peer or supervisor about your alignment work. How did you incorporate it?
How to Answer
- 1
Reflect on a specific instance in your past work.
- 2
Mention the specific feedback given to you.
- 3
Describe how you changed your approach or technique based on the feedback.
- 4
Highlight any improved outcomes from incorporating the feedback.
- 5
Keep your answer focused on alignment work and its importance.
Example Answers
During my last job, my supervisor pointed out that I wasn't double-checking the caster angle after adjustments. I started using a more thorough checklist, which improved my alignment accuracy by 15%.
Describe a time when you took the initiative to improve a process related to wheel alignment in your workplace.
How to Answer
- 1
Think of a specific example where you identified a problem.
- 2
Describe the steps you took to address the issue.
- 3
Highlight the positive results from your actions.
- 4
Use metrics or feedback if available to demonstrate impact.
- 5
Keep the example relevant to wheel alignment.
Example Answers
At my previous job, I noticed that our wheel alignment process was taking too long due to manual measurements. I proposed implementing a digital alignment tool and trained the team on it. As a result, we reduced alignment time by 30% and increased customer satisfaction scores.
Describe how you've managed your time effectively during busy periods in your work as a mechanic.
How to Answer
- 1
Prioritize tasks based on urgency and importance.
- 2
Use checklists to keep track of daily responsibilities.
- 3
Communicate with your team to delegate tasks when necessary.
- 4
Break larger jobs into smaller, manageable parts.
- 5
Stay organized and maintain a well-structured workspace.
Example Answers
During busy times, I prioritize my tasks by addressing the most urgent jobs first. For instance, if there are multiple cars needing wheel alignments, I focus on those scheduled for the earliest pickup, ensuring customer satisfaction.
Technical Interview Questions
What are the steps you take when performing a standard 4-wheel alignment?
How to Answer
- 1
Start by inspecting the vehicle's current alignment and tire condition.
- 2
Measure the initial angles using alignment equipment to determine current settings.
- 3
Adjust the toe, camber, and caster angles as necessary according to manufacturer specifications.
- 4
Recheck the measurements to ensure they are within the specified tolerances.
- 5
Test drive the vehicle to confirm handling and check for any further issues.
Example Answers
I begin by checking the tire pressure and inspecting the tires for wear. Then, I use alignment tools to measure the current angles. After that, I adjust the toe, camber, and caster to meet the manufacturer's specifications. Finally, I recheck the measurements and take the vehicle for a test drive to ensure everything is properly aligned.
What types of tools and equipment do you commonly use for wheel alignment, and how do you ensure they are properly maintained?
How to Answer
- 1
List specific tools like alignment machines, gauges, and lifts.
- 2
Mention routine maintenance checks for the equipment.
- 3
Explain how to calibrate tools regularly.
- 4
Discuss the importance of keeping tools clean and organized.
- 5
Share your experience with troubleshooting equipment issues.
Example Answers
I commonly use a computerized wheel alignment machine, laser alignment tools, and pneumatic lifts. I ensure they are properly maintained by performing regular calibration checks and keeping them clean and organized after each use.
Don't Just Read Wheel Alignment Mechanic Questions - Practice Answering Them!
Reading helps, but actual practice is what gets you hired. Our AI feedback system helps you improve your Wheel Alignment Mechanic interview answers in real-time.
Personalized feedback
Unlimited practice
Used by hundreds of successful candidates
How do you diagnose whether a vehicle's misalignment is caused by suspension issues or tire wear?
How to Answer
- 1
Start with a visual inspection of the tires for uneven wear patterns.
- 2
Check tire pressure to rule out inflation issues influencing alignment.
- 3
Inspect the suspension components for any signs of damage or wear.
- 4
Conduct a test drive to feel how the vehicle handles during acceleration and braking.
- 5
Use alignment tools to measure angles and compare with manufacturer specifications.
Example Answers
I begin by inspecting the tires for uneven wear, which can indicate tire issues. Then, I check the tire pressure to ensure it isn’t contributing to the misalignment. After that, I examine the suspension components for wear and tear. Finally, I analyze the alignment using specialized tools to confirm the diagnosis.
Explain the difference between toe, camber, and caster in wheel alignment.
How to Answer
- 1
Start with a brief definition of each term.
- 2
Highlight the key role each angle plays in vehicle handling.
- 3
Use clear examples to illustrate how incorrect settings affect performance.
- 4
Keep your answer structured, mentioning toe first, then camber, and finally caster.
- 5
Conclude with the importance of proper alignment for tire wear and safety.
Example Answers
Toe refers to the angle of the tires in relation to the centerline of the vehicle. If the front of the tires is closer together than the back, it's called toe-in. Proper toe keeps the vehicle stable during straight driving. Camber is the tilt of the wheels when viewed from the front; positive camber leans outwards, while negative camber leans inwards. Camber affects cornering grip and tire wear. Caster is the angle of the steering axis; positive caster helps with steering stability and return to center after a turn. Having these angles set correctly ensures even tire wear and better vehicle control.
How proficient are you with computerized alignment systems? Can you describe how you use them in your work?
How to Answer
- 1
Mention specific computerized alignment systems you have used.
- 2
Explain your familiarity with their setup and calibration.
- 3
Discuss how you interpret the data these systems provide.
- 4
Share an example of a challenging alignment and how the system helped.
- 5
Highlight the importance of accuracy in measurements for safety.
Example Answers
I have extensive experience with Hunter and John Bean alignment systems. I routinely set them up and calibrate them for accurate readings. For instance, I recently faced a car with significant misalignment, and the computerized system allowed me to quickly identify the issue and correct it.
What safety protocols do you follow when performing alignments, and why are they important?
How to Answer
- 1
Start by stating the key safety protocols you implement during alignments.
- 2
Mention the importance of proper vehicle support and how you ensure it.
- 3
Talk about the personal protective equipment (PPE) you use, like gloves and goggles.
- 4
Explain the significance of following manufacturer guidelines for equipment use.
- 5
Discuss the importance of inspecting tools and equipment for safety before use.
Example Answers
I always ensure the vehicle is properly supported with jack stands before starting any work. This is crucial to prevent accidents during the alignment process.
How can improper tire pressure affect wheel alignment, and how do you check for this?
How to Answer
- 1
Explain the relationship between tire pressure and wheel alignment.
- 2
Mention specific impacts of low or high tire pressure on alignment.
- 3
Describe how to check tire pressure accurately using a gauge.
- 4
Suggest regularly checking tire pressure as part of vehicle maintenance.
- 5
Emphasize that proper tire pressure contributes to even tire wear and handling.
Example Answers
Improper tire pressure can lead to uneven tire wear and can throw off the alignment since the tires aren't making full contact with the road. I check tire pressure using a gauge to ensure it matches the manufacturer's recommended PSI, and I recommend checking it regularly to maintain proper alignment.
What common signs indicate that a vehicle is in need of alignment?
How to Answer
- 1
Look for uneven tire wear patterns as a key indicator.
- 2
Check if the steering wheel is off-center when driving straight.
- 3
Listen for changes in the vehicle's handling, such as pulling to one side.
- 4
Watch for vibrations in the steering wheel at certain speeds.
- 5
Note if the vehicle drifts or requires constant correction to stay straight.
Example Answers
Common signs that a vehicle needs alignment include uneven tire wear, an off-center steering wheel, and the car pulling to one side while driving.
How does the wheel alignment process differ for trucks compared to passenger vehicles?
How to Answer
- 1
Understand the differences in weight and size between trucks and passenger vehicles.
- 2
Know the specific alignment specifications for trucks, like camber and toe adjustments.
- 3
Consider the type of suspension systems used in trucks compared to passenger cars.
- 4
Be aware of the impact of different tire sizes on alignment settings.
- 5
Mention how driving conditions and load can affect alignment needs for trucks.
Example Answers
The wheel alignment process for trucks differs mainly due to their weight and size. Trucks usually require more precise adjustments because they handle heavier loads and have larger tires. For instance, trucks often need specific camber and toe settings to ensure they can handle the stress of their load effectively.
How do you educate customers about the importance of regular wheel alignments?
How to Answer
- 1
Explain how misalignment can cause uneven tire wear and reduce tire life.
- 2
Discuss the impact on vehicle handling and safety when alignment is off.
- 3
Mention how alignment affects fuel efficiency and overall vehicle performance.
- 4
Use visual aids like charts or sample tires to illustrate wear patterns.
- 5
Share real-life examples of customers who benefited from regular alignments.
Example Answers
I explain to customers that regular wheel alignments prevent uneven tire wear, which can save them money in the long run by extending tire life.
Don't Just Read Wheel Alignment Mechanic Questions - Practice Answering Them!
Reading helps, but actual practice is what gets you hired. Our AI feedback system helps you improve your Wheel Alignment Mechanic interview answers in real-time.
Personalized feedback
Unlimited practice
Used by hundreds of successful candidates
Situational Interview Questions
If a customer returns a vehicle claiming that their wheel alignment is still off after you worked on it, how would you handle the situation?
How to Answer
- 1
Listen to the customer's concerns without interrupting.
- 2
Apologize for the inconvenience and assure them you will help resolve the issue.
- 3
Ask specific questions to understand the symptoms they are experiencing.
- 4
Re-check the alignment and perform any additional tests needed.
- 5
Communicate findings clearly to the customer and explain the next steps.
Example Answers
I would first listen carefully to the customer's description of the problem, making sure they feel heard. Then, I would apologize for the inconvenience and assure them I will get to the bottom of it. I'd ask about specific symptoms like pulling to one side, and then I'd re-check the alignment to ensure everything is correct.
Imagine you encounter a technical failure in your alignment equipment while servicing a vehicle. What steps would you take to manage the situation?
How to Answer
- 1
Pause the service to ensure safety and avoid further issues.
- 2
Assess the nature of the failure by checking error messages and equipment.
- 3
Attempt basic troubleshooting steps such as rebooting or recalibrating the equipment.
- 4
Communicate the issue to the customer and document the situation.
- 5
Seek assistance from a colleague or technician if the problem persists.
Example Answers
If I encounter a failure, I would first pause the service for safety. Then, I would check for any error messages and try to identify the problem. If it's simple, I might reboot the system. I would keep the customer informed about the delay and document everything. If I still can't fix it, I’d ask a colleague for help.
Don't Just Read Wheel Alignment Mechanic Questions - Practice Answering Them!
Reading helps, but actual practice is what gets you hired. Our AI feedback system helps you improve your Wheel Alignment Mechanic interview answers in real-time.
Personalized feedback
Unlimited practice
Used by hundreds of successful candidates
You have multiple vehicles waiting for alignment services. How do you prioritize which vehicles to work on first?
How to Answer
- 1
Assess the urgency based on customer appointment times
- 2
Consider the vehicle type and size for ease of service
- 3
Prioritize vehicles with specific alignment issues reported
- 4
Check for repeat customers or complaints needing immediate attention
- 5
Manage workflow to minimize waiting times for customers
Example Answers
I prioritize vehicles based on their appointment times, starting with those that were scheduled earlier. Then, I consider any specific issues the customers reported, focusing on critical problems first.
How would you adjust your techniques if you needed to align a newer car model with advanced technology?
How to Answer
- 1
Familiarize yourself with the specific technologies used in the newer models.
- 2
Refer to the manufacturer's alignment specifications and software.
- 3
Use appropriate diagnostic equipment to assess alignment issues accurately.
- 4
Understand how features like lane assist and stability control may affect alignment.
- 5
Stay updated on training and tools necessary for modern alignment procedures.
Example Answers
I would start by checking the manufacturer's specifications for the vehicle's alignment settings, since newer models often have unique requirements due to advanced technology.
If you realize that your last alignment was incorrectly performed after the vehicle has left the shop, what would be your response?
How to Answer
- 1
Acknowledge the mistake honestly and take responsibility.
- 2
Contact the customer immediately to inform them of the issue.
- 3
Offer to recheck the alignment at no charge to the customer.
- 4
Ensure to document the mistake and your response for future reference.
- 5
Learn from the experience to prevent similar issues in the future.
Example Answers
I would reach out to the customer right away and let them know about the misalignment. I'd offer to recheck and correct it for free, ensuring their vehicle is safe.
If you were faced with a vintage car that has unique alignment specifications, how would you approach the alignment?
How to Answer
- 1
Research the car's alignment specifications beforehand
- 2
Use specialized tools or equipment suited for vintage cars
- 3
Consult with manuals or expert forums for detailed guidelines
- 4
Perform a thorough inspection of suspension components
- 5
Test-drive the car post-alignment to ensure proper handling
Example Answers
First, I would research the specific alignment specifications for that vintage model, then use vintage alignment tools suited for the task. I would inspect the suspension for any wear and make necessary adjustments according to the manual.
If you discover a significant issue with a vehicle while performing alignment that requires collaboration with another technician, how would you proceed?
How to Answer
- 1
Identify the issue clearly and document it.
- 2
Communicate the issue to the other technician promptly.
- 3
Suggest a collaborative approach to resolve the issue.
- 4
Ensure to share any relevant information that may help.
- 5
Follow up on the progress after initial discussions.
Example Answers
I would first document the issue I find clearly, then communicate with my colleague, explaining the problem and asking for their input. We could then troubleshoot together, sharing information to resolve it effectively.
If a vehicle experiences an alignment issue on the road shortly after you completed the service, what steps would you take to address this?
How to Answer
- 1
Listen carefully to the driver's concerns and details of the issue.
- 2
Ask about the specific symptoms the vehicle is experiencing.
- 3
Schedule a follow-up appointment as soon as possible.
- 4
Review the alignment service performed and check for any missed adjustments.
- 5
Conduct a thorough re-evaluation of the alignment to diagnose the problem.
Example Answers
I would first listen to the driver to understand their experience. Then, I would ask about the symptoms they're noticing. After this, I'd arrange for them to come back in so I can review our previous work and check if there was an oversight.
How would you handle a situation where you have multiple customers in the shop all needing immediate attention for alignment issues?
How to Answer
- 1
Assess the urgency of each customer's issue quickly.
- 2
Communicate clearly with all customers about expected wait times.
- 3
Prioritize based on severity and safety concerns.
- 4
Offer to schedule follow-ups or appointments for less urgent issues.
- 5
Use teamwork to manage workload and keep customers informed.
Example Answers
I would first evaluate which alignment issue poses the greatest safety risk or urgency. Then, I'd inform all customers of the situation, letting them know their expected wait times. If someone has a more critical issue, I'd focus on that vehicle first while keeping the others updated.
Wheel Alignment Mechanic Position Details
Recommended Job Boards
CareerBuilder
www.careerbuilder.com/jobs/wheel-alignment-mechanicThese job boards are ranked by relevance for this position.
Related Positions
- Wheel Aligner
- Vehicle Mechanic
- Automobile Mechanic
- Car Mechanic
- Motor Tune-Up Specialist
- Chassis Mechanic
- Automobile Technician
- Undercar Specialist
- Race Car Mechanic
- Headlight Adjuster
Similar positions you might be interested in.
Ace Your Next Interview!
Practice with AI feedback & get hired faster
Personalized feedback
Used by hundreds of successful candidates
Ace Your Next Interview!
Practice with AI feedback & get hired faster
Personalized feedback
Used by hundreds of successful candidates