Top 32 Wire Spooler Interview Questions and Answers [Updated 2025]
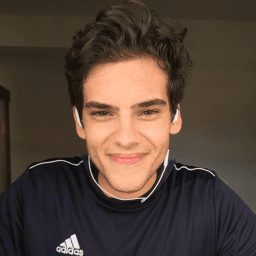
Andre Mendes
•
March 30, 2025
Are you preparing for a Wire Spooler interview and want to make a lasting impression? This blog post is your go-to resource, featuring the most common interview questions for the Wire Spooler role. Dive into expertly crafted example answers and insightful tips that will help you respond confidently and effectively. Get ready to tackle your interview with ease and stand out from the competition!
Download Wire Spooler Interview Questions in PDF
To make your preparation even more convenient, we've compiled all these top Wire Spoolerinterview questions and answers into a handy PDF.
Click the button below to download the PDF and have easy access to these essential questions anytime, anywhere:
List of Wire Spooler Interview Questions
Situational Interview Questions
If a safety alarm goes off while you are operating a wire spooling machine, what steps would you take?
How to Answer
- 1
Stay calm and do not panic.
- 2
Immediately stop the machine and follow proper shutdown procedures.
- 3
Assess the situation for any apparent hazards or risks.
- 4
Notify your supervisor and report the alarm details.
- 5
Check if it's a false alarm; follow safety protocols for confirmation.
Example Answers
I would first remain calm and stop the machine following the shutdown procedures. Then, I'd quickly assess the area for any dangers before notifying my supervisor about the alarm.
If you notice a significant delay in wire spooling output, how would you address this issue?
How to Answer
- 1
Identify the root cause of the delay by analyzing production metrics
- 2
Communicate with the team to gather insights on potential issues
- 3
Implement immediate corrective actions like adjusting machine settings
- 4
Monitor the output closely after changes are made
- 5
Document the findings and solutions for future reference
Example Answers
I would first check the production metrics to see if there are specific patterns causing the delay. Then, I would talk to the team to understand any operational issues they might be facing. I might adjust machine settings if needed and keep a close watch on the output after making these changes to see if performance improves.
Don't Just Read Wire Spooler Questions - Practice Answering Them!
Reading helps, but actual practice is what gets you hired. Our AI feedback system helps you improve your Wire Spooler interview answers in real-time.
Personalized feedback
Unlimited practice
Used by hundreds of successful candidates
You are informed that the wire material for your spool is delayed. How would you adjust your workflow?
How to Answer
- 1
Identify and prioritize immediate tasks that do not rely on the wire material
- 2
Communicate with the team about the delay and adjust deadlines as needed
- 3
Explore alternative wire suppliers or materials if feasible
- 4
Document the delay and its impact on production to keep stakeholders informed
- 5
Plan for increased efficiency in wire processing once materials arrive
Example Answers
I would first assess what tasks I can complete without the wire, like preparing spools or maintenance on the machinery. Next, I'd inform my team about the delay and we'll adjust our schedules accordingly. If possible, I would look into alternative suppliers to mitigate the delay. Finally, I would document this situation for reporting purposes.
If you find that the wire spooled in the previous batch does not meet quality standards, what actions would you take?
How to Answer
- 1
Immediately stop the spooler to prevent further production of non-compliant wire.
- 2
Assess the batch to identify the specific quality issues, documenting them.
- 3
Report the findings to the supervisor and quality assurance team promptly.
- 4
Determine if the issue is related to machine settings or material defects.
- 5
Suggest corrective actions to prevent recurrence, such as adjustments or training.],
- 6
sampleAnswers
Example Answers
I would first stop the spooler to prevent producing more faulty wire. Then I'd assess the batch to document the quality issues, report to my supervisor, and work on identifying the source of the problem.
How would you handle receiving feedback from a colleague about your spooling technique?
How to Answer
- 1
Listen actively to the feedback without interrupting.
- 2
Ask clarifying questions if you don't understand the feedback.
- 3
Thank your colleague for their input and perspective.
- 4
Reflect on the feedback before responding or making changes.
- 5
Demonstrate willingness to improve your technique and apply the feedback.
Example Answers
I would listen carefully to the feedback, ensuring I understand their perspective. Then, I might ask a couple of questions to clarify how I can improve. I appreciate constructive feedback as it helps me grow.
If you were short-staffed during a major spooling project, how would you prioritize tasks?
How to Answer
- 1
Assess the urgency of each task to meet project deadlines
- 2
Identify critical tasks that directly impact product quality or safety
- 3
Collaborate with remaining team members to distribute workload efficiently
- 4
Utilize any available technology or tools to streamline processes
- 5
Communicate openly with stakeholders about potential delays and adjustments
Example Answers
I would assess which tasks are critical for the project's completion, focusing on those that impact deadlines and quality. Next, I'd delegate any non-essential tasks among the team to ensure key areas are covered effectively.
During peak production times, how would you manage stress to maintain productivity?
How to Answer
- 1
Prioritize tasks to focus on what is most critical
- 2
Use deep breathing techniques to stay calm
- 3
Take short breaks to recharge during long hours
- 4
Communicate with team members for support
- 5
Stay organized to reduce feelings of overwhelm
Example Answers
I prioritize my tasks based on urgency, focusing on critical deadlines, and I take deep breaths when I feel overwhelmed. Additionally, I make sure to take short breaks to clear my mind.
If two team members are disagreeing on the method of spooling, how would you mediate?
How to Answer
- 1
Listen to both team members' perspectives without interrupting.
- 2
Ask questions to clarify their viewpoints and the reasons behind their methods.
- 3
Encourage a collaborative discussion to find common ground.
- 4
Suggest experimenting with both methods to see which is more effective.
- 5
Follow up after implementation to ensure the team moves forward together.
Example Answers
I would first listen to both team members to understand their viewpoints. Then I would ask clarifying questions to get to the root of their disagreement. After that, I would facilitate a discussion between them to explore a compromise or a new combined approach. If needed, I might suggest testing both methods to see which works better.
If the wire spooler breaks down during a crucial task, what steps would you take?
How to Answer
- 1
Stay calm and assess the situation quickly
- 2
Check for any alerts or indicators on the machine
- 3
Notify the supervisor about the breakdown and its impact on production
- 4
Attempt a basic troubleshooting process, like resetting the machine if safe
- 5
Prepare to implement a temporary solution or reallocate tasks to minimize downtime
Example Answers
I would first stay calm and assess the situation to understand what caused the breakdown. I'd check for any error indicators on the spooler and notify my supervisor right away. If it's safe, I'd try to reset the machine and see if that resolves the issue. Meanwhile, I would think about reallocating tasks to keep production moving.
How would you ensure that all safety and operational procedures are consistently followed by the team?
How to Answer
- 1
Establish clear safety and operational procedures that are easy to understand.
- 2
Conduct regular training sessions to reinforce knowledge of procedures.
- 3
Implement a system for checking compliance during operations.
- 4
Encourage open communication where team members can report issues.
- 5
Recognize and reward adherence to safety policies to promote a culture of safety.
Example Answers
I would start by ensuring that all procedures are clearly documented and accessible. Then, I would hold regular training sessions to keep safety top of mind. During operations, I would perform routine checks to confirm compliance, and I would foster an environment where team members feel comfortable sharing any concerns about safety practices.
Don't Just Read Wire Spooler Questions - Practice Answering Them!
Reading helps, but actual practice is what gets you hired. Our AI feedback system helps you improve your Wire Spooler interview answers in real-time.
Personalized feedback
Unlimited practice
Used by hundreds of successful candidates
If you have a report showing decreased efficiency in your spooling section, how do you approach your manager?
How to Answer
- 1
Prepare data and facts to support your observation.
- 2
Identify potential reasons for the decreased efficiency.
- 3
Propose actionable solutions or improvements.
- 4
Schedule a dedicated time to discuss this matter.
- 5
Express willingness to collaborate on resolving the issue.
Example Answers
I would first review the report in detail to understand the specific areas of decreased efficiency. Then, I would gather additional data to identify trends. Once I have a clear picture, I would approach my manager with a summary of my findings and suggest possible solutions.
Behavioral Interview Questions
Tell me about a time when you had to resolve a conflict while working with a team on a wire spooling project.
How to Answer
- 1
Identify the conflict clearly and explain the roles involved
- 2
Describe your approach to addressing the conflict
- 3
Highlight the actions you took to facilitate resolution
- 4
Discuss the outcome and any lessons learned
- 5
Emphasize the importance of teamwork and communication
Example Answers
During a wire spooling project, two team members disagreed on the best method to secure cables. I facilitated a meeting where each person shared their perspective, and we collectively discussed the pros and cons. We decided on a compromise approach that incorporated both ideas, leading to a more efficient workflow and better team morale.
Can you describe a situation where you had to collaborate with others to meet a tight deadline for wire spooling?
How to Answer
- 1
Choose a specific project that had a tight deadline.
- 2
Highlight your role and the team's dynamics.
- 3
Discuss the strategies you used for effective communication.
- 4
Explain any challenges faced and how you overcame them.
- 5
Mention the positive outcome and what you learned.
Example Answers
In my previous job, we had a large order that needed to be spooled within a week. I coordinated with the production team daily to track progress. We held brief meetings to address any issues and reallocated tasks based on strengths. This collaboration ensured we met the deadline with quality work, and I learned the importance of clear communication.
Don't Just Read Wire Spooler Questions - Practice Answering Them!
Reading helps, but actual practice is what gets you hired. Our AI feedback system helps you improve your Wire Spooler interview answers in real-time.
Personalized feedback
Unlimited practice
Used by hundreds of successful candidates
Give an example of when your attention to detail made a difference in the quality of the wire spooling work.
How to Answer
- 1
Think of a specific project where quality was critical.
- 2
Describe a problem you noticed due to your attention to detail.
- 3
Explain the actions you took to resolve the issue.
- 4
Highlight the positive outcome of your actions.
- 5
Use metrics if possible to quantify the improvement.
Example Answers
In my previous job, I noticed that after spooling, some wires had inconsistent tension. I checked the setup and adjusted the tension settings as needed. This resulted in a 20% reduction in wire defects and improved overall production quality.
Describe a time when you encountered a problem during the wire spooling process and how you solved it.
How to Answer
- 1
Think of a specific incident that demonstrates problem-solving skills.
- 2
Clearly explain the nature of the problem you faced.
- 3
Describe the steps you took to analyze and resolve the issue.
- 4
Mention any tools or techniques you used to improve the process.
- 5
Conclude with the positive outcome of your actions.
Example Answers
During a wire spooling operation, I noticed that the wire was tangled and not feeding correctly. I paused the operation, assessed the spool alignment, and discovered it was set up improperly. I adjusted the spool position and showed the team how to secure it better in the future. This resolved the issue, and we completed the spooling without further complications.
Describe a time when you took the lead on a project to improve wire spooling efficiency.
How to Answer
- 1
Identify a specific project where you led the initiative.
- 2
Highlight the challenge you faced in wire spooling efficiency.
- 3
Explain the steps you took to address the issue.
- 4
Discuss the outcome and any measurable improvements.
- 5
Emphasize teamwork and how you involved others in the solution.
Example Answers
In my previous role, I led a project to streamline wire spooling by analyzing the workflow. We were facing delays due to manual handling, so I implemented a new automated system. This reduced our spooling time by 30% and increased output. I involved the team in training and feedback, ensuring everyone was onboard with the changes.
Can you give an example of when you took the initiative to improve a process related to wire spooling?
How to Answer
- 1
Identify a specific problem in the wire spooling process.
- 2
Explain the steps you took to address the problem.
- 3
Highlight the positive outcomes from your actions.
- 4
Use quantifiable metrics if possible to show improvement.
- 5
Demonstrate your ability to work collaboratively with the team.
Example Answers
In my previous role, I noticed that our wire spooling process had frequent delays due to tangled wires. I proposed implementing a new organization system that separated wires by type and length, which reduced spool preparation time by 30%. The team adopted this method, and we saw fewer errors in the spooling stage.
Tell me about a time you received constructive criticism regarding your work. How did you respond?
How to Answer
- 1
Think of a specific example where you received feedback.
- 2
Describe the criticism clearly and honestly.
- 3
Explain how you processed the feedback and what actions you took.
- 4
Emphasize the positive outcome or learning experience.
- 5
Show your willingness to grow and improve from feedback.
Example Answers
In my previous role, my supervisor pointed out that my reports needed more detail. I took this feedback seriously, asked for specific examples, and then worked on adding more comprehensive information in my next reports. This not only improved my reports but also helped me develop better analytical skills.
Describe a situation where you had to go above and beyond your regular duties as a wire spooler.
How to Answer
- 1
Choose a specific situation that illustrates your initiative.
- 2
Highlight the extra steps you took and the impact they had.
- 3
Emphasize teamwork or collaboration if applicable.
- 4
Use clear metrics or results to quantify your efforts.
- 5
Keep it concise but detailed enough to show your dedication.
Example Answers
In my last role, we were behind schedule on a large order. I volunteered to stay late to help package and label the spools, ensuring we met our deadline. This effort enabled us to deliver the order a day early, impressing the client and securing additional business.
Can you discuss a time when you suggested a new method that improved wire spooling?
How to Answer
- 1
Choose a specific method you suggested.
- 2
Explain the problem that the method addressed.
- 3
Describe the process of implementation and any challenges faced.
- 4
Highlight the positive outcomes of your suggestion.
- 5
Use metrics or feedback to show improvement if possible.
Example Answers
In my previous role, I noticed that the wire spooling process was slow due to manual adjustments. I suggested implementing an automated tension control system. This reduced setup time by 30% and improved spool quality, which led to fewer defects.
Don't Just Read Wire Spooler Questions - Practice Answering Them!
Reading helps, but actual practice is what gets you hired. Our AI feedback system helps you improve your Wire Spooler interview answers in real-time.
Personalized feedback
Unlimited practice
Used by hundreds of successful candidates
Describe a time when you achieved a challenging goal in a wire spooling project.
How to Answer
- 1
Choose a specific project where you faced significant challenges.
- 2
Clearly outline the goal you set and the obstacles you encountered.
- 3
Explain the actions you took to overcome those challenges.
- 4
Highlight the positive outcome and what you learned from the experience.
- 5
Keep your answer focused and concise, using the STAR method.
Example Answers
In a recent project, we needed to spool 500 meters of high-tension wire in a tight timeline. We faced delays due to equipment failure. I organized a team to troubleshoot and implemented a backup plan to use alternative spooling machines. We completed the project on time and improved our process for future projects.
Technical Interview Questions
What types of wire spooling machines are you familiar with, and what are their key features?
How to Answer
- 1
Identify specific models of wire spooling machines you have worked with.
- 2
Highlight key features like speed, capacity, and automation.
- 3
Discuss any unique mechanisms like adjustable tension or guided feeding.
- 4
Mention your experience with troubleshooting or maintenance on these machines.
- 5
Relate features to how they improve efficiency or product quality.
Example Answers
I am familiar with the XYZ wire spooling machine, which features a high-speed spooling mechanism with a capacity of up to 1000 meters. It also has automated tension control to ensure even winding.
Explain the importance of calculating the correct tension when spooling wire.
How to Answer
- 1
Identify the impact of tension on wire quality and performance.
- 2
Emphasize how incorrect tension can lead to wire damage.
- 3
Discuss the role of tension in preventing tangles and ensuring smooth spooling.
- 4
Mention safety concerns related to improper tension.
- 5
Highlight industry standards or best practices for tension calculation.
Example Answers
Calculating the correct tension is crucial because it directly affects the quality of the wire. Too much tension can damage the wire, while too little can cause tangling. Proper tension ensures a smooth spooling process, which is vital for operational efficiency.
Don't Just Read Wire Spooler Questions - Practice Answering Them!
Reading helps, but actual practice is what gets you hired. Our AI feedback system helps you improve your Wire Spooler interview answers in real-time.
Personalized feedback
Unlimited practice
Used by hundreds of successful candidates
What safety precautions should be taken while operating wire spooling equipment?
How to Answer
- 1
Always wear appropriate personal protective equipment such as gloves and eye protection.
- 2
Ensure the area is clear of obstructions and potential hazards before starting work.
- 3
Conduct a thorough inspection of the spooling equipment before use to check for damage.
- 4
Follow proper locking and tagging procedures when performing maintenance or repairs.
- 5
Be aware of your surroundings and communicate with team members to avoid accidents.
Example Answers
When operating wire spooling equipment, I always wear gloves and safety glasses to protect myself. I also make sure that the area is free of any obstacles before starting.
How would you diagnose and fix a malfunctioning wire spooler?
How to Answer
- 1
Start by observing the spooler for any unusual sounds or movements.
- 2
Check the power supply and ensure the machine is plugged in and receiving power.
- 3
Inspect the mechanical parts for any obstructions or wear and tear.
- 4
Run diagnostic tests if available, to identify any error codes or malfunctions.
- 5
Consult technical manuals for troubleshooting steps specific to the model.
Example Answers
First, I would listen for any abnormal noises from the spooler and check if it's plugged in and powered on. Then, I would inspect for any blockages in the feed mechanism and help clear them. If the problem persists, I'd run any diagnostics provided by the machine.
What factors do you consider when selecting wire material for specific applications?
How to Answer
- 1
Evaluate the electrical conductivity required for the application
- 2
Consider the mechanical strength and flexibility needed
- 3
Assess the environmental conditions the wire will be exposed to
- 4
Look at the cost and availability of the wire materials
- 5
Understand the compatibility with connectors and components
Example Answers
I consider the electrical conductivity first; for high-performance applications, I would choose copper due to its excellent conductivity.
What techniques can be implemented to optimize the wire spooling process?
How to Answer
- 1
Analyze the current spooling setup for efficiency
- 2
Implement automation where possible to reduce manual handling
- 3
Ensure consistent tension is maintained during spooling
- 4
Regularly train workers on best practices for wire handling
- 5
Monitor and adjust the speed of the spooling machine for optimal performance
Example Answers
We can optimize the wire spooling process by automating certain tasks to minimize manual effort. Regular training for employees on wire handling techniques can also ensure consistency and quality during spooling.
What industry standards should be followed in wire spooling operations?
How to Answer
- 1
Understand the relevant ANSI and ISO standards for wire handling and safety.
- 2
Familiarize yourself with best practices for material handling to prevent damage.
- 3
Know the specifications for the type of wire being processed, including gauge and insulation standards.
- 4
Ensure compliance with safety regulations to protect workers and equipment.
- 5
Stay updated with industry innovations and standard updates that impact wire spooling.
Example Answers
In wire spooling operations, we need to adhere to ANSI and ISO standards related to wire handling and safety. This ensures that the materials are managed properly and reduces the risk of accidents.
How do you determine the appropriate spool size for different wire types?
How to Answer
- 1
Consider the wire diameter and its material properties.
- 2
Match the spool size to the length and weight of the wire needed.
- 3
Ensure the spool design supports wire storage without damage.
- 4
Document spool specifications for easy reference and safety.
- 5
Consult manufacturer recommendations for specific wire types.
Example Answers
I determine spool size by first assessing the wire's diameter and material, ensuring it can support the length I'll use while preventing deformation.
What routine maintenance practices do you believe are essential for wire spooling machines?
How to Answer
- 1
Inspect and clean the spooling area regularly to prevent debris buildup.
- 2
Lubricate moving parts according to the manufacturer's specifications.
- 3
Check and tighten all bolts and connections to ensure machine stability.
- 4
Monitor electrical components for wear and replace as necessary.
- 5
Perform regular calibration tests to maintain spool dimensions and tension.
Example Answers
Routine inspections and cleaning of the spooling area are crucial to keep the machine running smoothly. I always lubricate moving parts as recommended to reduce wear.
How do you calibrate a wire spooling machine for different wire specifications?
How to Answer
- 1
Identify the wire specification required for the spool.
- 2
Adjust the tension settings according to the wire type to prevent damage.
- 3
Set the spool diameter and width according to the specification manual.
- 4
Calibrate the feed rate to match the wire's material properties.
- 5
Run a test spool to verify that the calibration holds under operational conditions.
Example Answers
To calibrate a wire spooling machine, I first check the wire specification such as diameter and material. Then, I adjust the tension settings according to what is recommended for that wire type. After that, I ensure the spool size matches the specifications and set the feed rate accordingly. Lastly, I run a test spool to confirm the setup is correct before full production.
Don't Just Read Wire Spooler Questions - Practice Answering Them!
Reading helps, but actual practice is what gets you hired. Our AI feedback system helps you improve your Wire Spooler interview answers in real-time.
Personalized feedback
Unlimited practice
Used by hundreds of successful candidates
Wire Spooler Position Details
Recommended Job Boards
ZipRecruiter
www.ziprecruiter.com/Jobs/Wire-SpoolerThese job boards are ranked by relevance for this position.
Related Positions
- Film Spooler
- Wire Twister
- Wire Spinner
- Wire Insulator
- Wire Taper
- Cable Reeler
- Wire Roller
- Wire Inserter
- Ribbon Winder
- Winding Machine Operator
Similar positions you might be interested in.
Ace Your Next Interview!
Practice with AI feedback & get hired faster
Personalized feedback
Used by hundreds of successful candidates
Ace Your Next Interview!
Practice with AI feedback & get hired faster
Personalized feedback
Used by hundreds of successful candidates