Top 32 Air Compressor Engineer Interview Questions and Answers [Updated 2025]
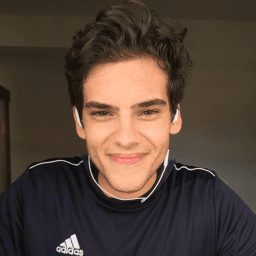
Andre Mendes
•
March 30, 2025
Preparing for an Air Compressor Engineer interview can be daunting, but this blog post is here to help you succeed by providing the most common interview questions for this specialized role. Dive into expertly crafted example answers and insightful tips to help you respond confidently and effectively. Whether you're a seasoned professional or new to the field, this guide is designed to boost your interview readiness and confidence.
Download Air Compressor Engineer Interview Questions in PDF
To make your preparation even more convenient, we've compiled all these top Air Compressor Engineerinterview questions and answers into a handy PDF.
Click the button below to download the PDF and have easy access to these essential questions anytime, anywhere:
List of Air Compressor Engineer Interview Questions
Behavioral Interview Questions
Can you describe a time when you had to troubleshoot a complex issue with an air compressor? What steps did you take?
How to Answer
- 1
Identify the specific issue with the air compressor.
- 2
Explain the diagnostic steps you took to isolate the problem.
- 3
Describe the solution you implemented and why you chose it.
- 4
Mention any tools or techniques you used during troubleshooting.
- 5
Highlight the outcome and any lessons learned from the experience.
Example Answers
At my previous job, I faced a situation where an air compressor was not building pressure. I began by checking the gauge and listening for unusual sounds. I discovered a leaking air hose, which I replaced. This resolved the issue, allowing the compressor to operate normally. I learned the importance of routine inspections.
Tell us about a time you worked in a team to implement a new air compressor system. What was your role and how did you contribute?
How to Answer
- 1
Choose a specific project that showcases your teamwork in implementing an air compressor system.
- 2
Clearly define your role and responsibilities within the team.
- 3
Highlight your contributions, such as design input, problem-solving, or project management.
- 4
Mention any challenges faced and how the team overcame them with your help.
- 5
Conclude with the positive outcome of the project and what you learned.
Example Answers
In my previous role at XYZ Company, our team was tasked with implementing a new air compressor system for a manufacturing line. I was the lead engineer responsible for the design specifications. I collaborated closely with the procurement team to ensure we sourced the right equipment and worked with technicians to integrate the system effectively. We faced a challenge with space constraints, which I addressed by redesigning the layout. The project was completed on time, resulting in a 30% efficiency increase.
Don't Just Read Air Compressor Engineer Questions - Practice Answering Them!
Reading helps, but actual practice is what gets you hired. Our AI feedback system helps you improve your Air Compressor Engineer interview answers in real-time.
Personalized feedback
Unlimited practice
Used by hundreds of successful candidates
Describe a situation where you led a project involving air compressor maintenance. What challenges did you face?
How to Answer
- 1
Start with a clear overview of the project and your role.
- 2
Mention specific technical skills you applied during maintenance.
- 3
Discuss particular challenges you faced, such as equipment failure or scheduling issues.
- 4
Explain how you overcame these challenges and what the outcomes were.
- 5
Conclude with what you learned or how it improved your skills.
Example Answers
In my previous position, I led a project to maintain a fleet of air compressors in our manufacturing plant. One major challenge was a critical compressor failing right before a production deadline. I coordinated an emergency repair, ensuring we had the parts and labor scheduled. We met the deadline, and I learned the importance of having contingency plans.
Give an example of how you communicated technical information about air compressors to non-technical stakeholders.
How to Answer
- 1
Identify the audience and their level of understanding
- 2
Simplify the technical jargon into everyday language
- 3
Use analogies or metaphors to explain complex concepts
- 4
Focus on the benefits and impacts of the information provided
- 5
Encourage questions to ensure understanding
Example Answers
In a recent project, I explained the efficiency of our air compressors to the sales team by comparing it to a car engine's fuel efficiency. I highlighted how better efficiency means lower operational costs for our customers, ensuring they understood the product benefits.
Tell me about a time you had to learn a new air compressor technology quickly. How did you approach it?
How to Answer
- 1
Identify a specific instance of learning a new air compressor technology.
- 2
Explain the steps you took to learn it quickly, such as studying manuals or online resources.
- 3
Discuss how you applied the knowledge practically, like in a project or maintenance task.
- 4
Highlight any challenges faced and how you overcame them.
- 5
Conclude with the outcome and what you learned from the experience.
Example Answers
In my previous role, I was tasked with implementing a new rotary screw air compressor. I quickly reviewed the technical manuals and watched instructional videos available from the manufacturer. I then shadowed a senior technician to see the installation process in action. Despite some initial challenges with the software setup, I was able to troubleshoot quickly and successfully completed the project ahead of schedule.
Have you ever suggested an innovative solution for an air compressor problem? What was it?
How to Answer
- 1
Identify a specific problem you encountered with an air compressor.
- 2
Describe the innovative solution you proposed.
- 3
Explain the impact of your solution on efficiency or performance.
- 4
Use metrics or outcomes if possible to quantify improvements.
- 5
Highlight teamwork or collaboration if it was part of the solution.
Example Answers
At my previous job, we faced frequent breakdowns due to overheating in our air compressors. I suggested implementing a regular thermal imaging inspection routine to identify hot spots early. This proactive approach reduced downtime by 30% and saved costs on repairs.
Describe a time you successfully planned and executed a maintenance schedule for air compressors.
How to Answer
- 1
Outline the problem that needed addressing with the compressor maintenance.
- 2
Describe the planning process you undertook, including scheduling and logistics.
- 3
Mention any tools or software used for tracking maintenance schedules.
- 4
Share how you communicated with the team or stakeholders during the process.
- 5
Highlight the results of your maintenance schedule, such as decreased downtime or increased efficiency.
Example Answers
At my previous job, we had frequent breakdowns of our air compressors. I developed a maintenance schedule based on the manufacturer's recommendations, scheduled downtime during less busy hours, and used software to track maintenance history. As a result, we reduced breakdowns by 30%.
Can you give an example of how you have managed costs effectively in an air compressor project?
How to Answer
- 1
Identify specific cost-saving measures you implemented.
- 2
Quantify the savings where possible.
- 3
Discuss collaboration with suppliers for better pricing.
- 4
Mention any innovative solutions you applied.
- 5
Describe the impact on project timeline and performance.
Example Answers
In a recent air compressor upgrade project, I negotiated with suppliers for bulk discounts which saved us 15% on parts. This allowed us to complete the project under budget while maintaining quality.
Can you describe an experience where you had to deal with a customer's complaint regarding an air compressor malfunction?
How to Answer
- 1
Listen carefully to the customer's complaint
- 2
Acknowledge their feelings and express empathy
- 3
Describe the steps you took to investigate the issue
- 4
Explain how you resolved the problem or what solution you provided
- 5
Emphasize the positive outcome and follow-up with the customer
Example Answers
I once received a call from a client whose air compressor kept shutting down. I listened to their frustration, apologized for the inconvenience, and scheduled a visit to diagnose the problem. I found a faulty pressure switch and replaced it, ensuring everything worked flawlessly. The customer thanked me for the quick resolution and even gave positive feedback on our service.
Don't Just Read Air Compressor Engineer Questions - Practice Answering Them!
Reading helps, but actual practice is what gets you hired. Our AI feedback system helps you improve your Air Compressor Engineer interview answers in real-time.
Personalized feedback
Unlimited practice
Used by hundreds of successful candidates
Describe a time when you had to manage your time effectively while working on multiple compressor projects.
How to Answer
- 1
Identify specific projects and deadlines you were juggling.
- 2
Explain how you prioritized tasks based on urgency and importance.
- 3
Discuss any tools or methods you used to track progress and manage time.
- 4
Mention teamwork or delegation if applicable in managing workload.
- 5
Conclude with positive outcomes or lessons learned from the experience.
Example Answers
In my previous role, I was managing two major compressor upgrades simultaneously. I prioritized tasks by setting clear deadlines for each phase. I used a project management tool to track milestones and weekly check-ins with my team to ensure we stayed on schedule. As a result, both projects were completed on time, and we received positive feedback from the clients.
Technical Interview Questions
What are the key maintenance tasks you perform regularly on an air compressor to ensure optimal performance?
How to Answer
- 1
List specific tasks that contribute to compressor efficiency.
- 2
Focus on routine maintenance and any troubleshooting steps.
- 3
Mention safety checks and environmental factors.
- 4
Include frequency of tasks where applicable.
- 5
Highlight any experience with different compressor types.
Example Answers
I regularly check and change the oil in the compressor every 500 hours to ensure smooth operation and optimal performance.
Can you explain the differences between rotary screw compressors and reciprocating compressors?
How to Answer
- 1
Start with a brief definition of each type of compressor
- 2
Highlight the mechanism of operation for both types
- 3
Discuss the typical applications for each type
- 4
Mention any advantages and disadvantages specific to each
- 5
Conclude with a summary that emphasizes their suitability for different needs
Example Answers
Rotary screw compressors use two rotating screws to compress air, providing continuous airflow. They are often used in large-scale applications due to their efficiency and low maintenance. Reciprocating compressors, on the other hand, use pistons to compress air, making them suitable for smaller applications but with higher maintenance needs. Each type has its place depending on the air demand and operational requirements.
Don't Just Read Air Compressor Engineer Questions - Practice Answering Them!
Reading helps, but actual practice is what gets you hired. Our AI feedback system helps you improve your Air Compressor Engineer interview answers in real-time.
Personalized feedback
Unlimited practice
Used by hundreds of successful candidates
How would you diagnose a sudden drop in air pressure from a compressor unit?
How to Answer
- 1
Check for visible air leaks in hoses and fittings.
- 2
Inspect the air filter for blockages or damage.
- 3
Examine the compressor's discharge pressure gauge for anomalies.
- 4
Review the belt and motor function to ensure proper operation.
- 5
Look for signs of mechanical failure in the compressor components.
Example Answers
First, I would check for any air leaks in the lines and connections. After that, I would inspect the air filter to ensure it's not clogged, as this can restrict airflow. I would then look at the pressure gauge to see if there are any strange readings.
What safety considerations do you keep in mind when working with high-pressure air systems?
How to Answer
- 1
Always wear appropriate personal protective equipment like goggles and gloves.
- 2
Regularly inspect and maintain equipment to prevent leaks or failures.
- 3
Ensure pressure relief valves are functioning and accessible.
- 4
Be aware of the hazards associated with compressed air, such as flying debris.
- 5
Follow lockout/tagout procedures during maintenance or repairs.
Example Answers
I prioritize wearing protective equipment such as safety goggles and gloves. I also conduct regular inspections of the systems to catch any potential issues before they become dangerous.
What types of control systems do you have experience with in managing air compressor operations?
How to Answer
- 1
Detail specific control systems you've worked with.
- 2
Discuss your role in managing these systems.
- 3
Mention any software or technology you used.
- 4
Include any relevant metrics or outcomes from your management.
- 5
Be prepared to explain challenges and solutions encountered.
Example Answers
I have experience with PLC-based control systems for air compressor operations, where I programmed the logic for optimized performance. In my last role, I used Siemens software to monitor pressure levels and adjust compressor output accordingly, achieving a 15% increase in efficiency.
What methods do you use to enhance the energy efficiency of existing air compressor systems?
How to Answer
- 1
Assess current system performance using data logging and monitoring tools
- 2
Consider using variable speed drives to match compressor output with demand
- 3
Regularly maintain and optimize filters and piping to reduce pressure drop
- 4
Implement heat recovery systems to utilize wasted energy from the compressor
- 5
Evaluate and adjust system controls for optimal operating conditions
Example Answers
I start by using data logging to monitor the current efficiency of air compressors. I then implement variable speed drives which adjust the compressor speed based on demand, saving energy when full output is unnecessary.
Are you familiar with any industry standards or regulations regarding air compressor operation?
How to Answer
- 1
Mention key standards such as ISO 8573 or OSHA regulations
- 2
Highlight any relevant certifications or training you've completed
- 3
Discuss your experience with compliance in past roles
- 4
Emphasize the importance of safety and efficiency in operations
- 5
Be prepared to explain how you stay updated on industry changes
Example Answers
Yes, I am familiar with ISO 8573, which specifies contaminants and quality classes for compressed air. In my previous job, I ensured compliance with these standards by regularly testing air quality.
What are the key considerations when installing a new air compressor system?
How to Answer
- 1
Evaluate the air demand of the application to size the compressor correctly.
- 2
Consider the installation location for adequate ventilation and access.
- 3
Plan for the necessary power supply and electrical requirements.
- 4
Ensure compliance with local regulations and safety standards.
- 5
Design an efficient piping layout to minimize pressure drops.
Example Answers
When installing a new air compressor, it’s critical to size the compressor based on the specific air demand. Additionally, the installation site should have proper ventilation and be easily accessible for maintenance.
How do you ensure that air compressors integrate well with other systems, like pneumatic tools?
How to Answer
- 1
Understand the requirements of the pneumatic tools and their air consumption needs
- 2
Ensure proper sizing of the air compressor to meet peak demands
- 3
Implement appropriate piping and fittings to minimize pressure loss
- 4
Incorporate moisture separation and filtration systems to protect tools
- 5
Regularly review system performance and adjust for any inefficiencies
Example Answers
To ensure air compressors integrate well with pneumatic tools, I first assess the tools' air consumption requirements. I then select a compressor that effectively meets those demands, paying close attention to peak usage. Proper piping is essential, so I design the layout to reduce pressure loss. Additionally, I install moisture separators to protect the tools from water damage. Finally, I regularly check the entire system's performance to adjust and optimize as needed.
What troubleshooting techniques do you find most effective for diagnosing compressor issues?
How to Answer
- 1
Start by gathering data on the compressor's performance and system parameters.
- 2
Check for common mechanical issues like leaks or wear in components.
- 3
Use diagnostic tools like pressure gauges or thermal cameras to identify problems.
- 4
Review maintenance logs and previous issues that might inform your diagnosis.
- 5
If possible, consult with team members or experts for additional insights.
Example Answers
I begin by collecting operational data such as pressure and temperature readings. This helps me identify trends or anomalies that could signal a problem. Then, I inspect the unit for leaks or unusual sounds, and use thermal imaging to find hot spots that could indicate failing components.
Don't Just Read Air Compressor Engineer Questions - Practice Answering Them!
Reading helps, but actual practice is what gets you hired. Our AI feedback system helps you improve your Air Compressor Engineer interview answers in real-time.
Personalized feedback
Unlimited practice
Used by hundreds of successful candidates
What are the main components of an air compressor and their functions?
How to Answer
- 1
Identify the primary components like the motor, pump, and storage tank.
- 2
Briefly describe the function of each component.
- 3
Mention any additional components like filters or regulators.
- 4
Use simple language to explain complex functions.
- 5
Prepare to give examples of different types of compressors if asked.
Example Answers
An air compressor consists of the motor, which powers the unit, the pump that compresses air, and the storage tank that holds the compressed air. It may also include filters to clean the air and regulators to control the pressure.
How do you calculate the appropriate size of an air compressor for a specific application?
How to Answer
- 1
Identify the total CFM required for your tools and processes.
- 2
Determine the max PSI needed for your application.
- 3
Account for duty cycle and how often the compressor will run.
- 4
Consider any additional factors like piping losses or altitude.
- 5
Select a compressor with a rating that exceeds your calculated requirements.
Example Answers
To calculate the proper size, I first determine the total CFM needed by adding up the requirements of all tools. Then, I identify the maximum PSI required. After that, I factor in the duty cycle to ensure the compressor can handle regular use, and I consider piping losses. Finally, I choose a compressor rated higher than my calculations.
Situational Interview Questions
Imagine you are called to fix a compressor that is making unusual noises. What steps would you take to identify the issue?
How to Answer
- 1
Listen carefully to the type of noise the compressor is making
- 2
Check for loose components and tighten them if necessary
- 3
Inspect the oil level and quality to ensure proper lubrication
- 4
Examine the belts and pulleys for wear or damage
- 5
Run diagnostics if available to check for error codes or alerts
Example Answers
First, I would listen to the compressor to determine the nature of the noise, whether it is a grinding or a rattling sound. Then, I would check for any loose parts and tighten them as needed. After that, I would inspect the oil level to make sure it’s adequate and not contaminated. I would also look at the belts and pulleys for any signs of wear. Finally, I would run any diagnostic tools to see if there are error codes present.
If you discover a failure in a compressor during a routine check, how would you handle the situation?
How to Answer
- 1
Assess the severity of the failure immediately
- 2
Document the findings accurately
- 3
Follow safety protocols before taking further action
- 4
Notify your supervisor and relevant personnel
- 5
Develop a plan for repair or further investigation
Example Answers
I would first assess the severity of the compressor failure, documenting everything carefully. Then, I would follow safety procedures to ensure that no one is endangered before notifying my supervisor. Based on the situation, I would work on a plan for repairs or further investigation.
Don't Just Read Air Compressor Engineer Questions - Practice Answering Them!
Reading helps, but actual practice is what gets you hired. Our AI feedback system helps you improve your Air Compressor Engineer interview answers in real-time.
Personalized feedback
Unlimited practice
Used by hundreds of successful candidates
You are assigned to install a new air compressor system under a tight deadline. How would you plan the installation?
How to Answer
- 1
Assess the site and gather all necessary information about the installation location
- 2
Create a detailed timeline breaking down the installation into key phases
- 3
Identify all required tools and equipment ahead of time
- 4
Communicate with stakeholders to manage expectations and ensure everyone is aligned
- 5
Prepare for potential issues by having contingency plans in place
Example Answers
I would begin by assessing the installation site to understand the layout and requirements. Then, I'd create a timeline that includes all phases of the installation, such as preparatory work, equipment setup, and final testing. I’d ensure that all tools are gathered in advance to avoid delays and keep clear communication with the team and stakeholders throughout the process.
How would you handle a disagreement with a colleague over the best approach to a compressor issue?
How to Answer
- 1
Listen actively to the colleague's viewpoint.
- 2
Present your perspective with facts and data.
- 3
Seek common ground between both approaches.
- 4
Suggest a trial or testing phase to compare solutions.
- 5
Maintain professionalism and focus on problem-solving.
Example Answers
I would first listen to my colleague's viewpoint carefully to understand their reasoning. Then I would present my own perspective backed by relevant data on compressor performance. Next, I would suggest that we look for common ground and possibly run a test to see which approach yields better results.
You are given a limited budget for compressor repairs. How do you prioritize what needs to be fixed?
How to Answer
- 1
Evaluate the severity of the issue and its impact on operations
- 2
Consider the safety implications of each repair
- 3
Identify repairs that will prevent further damage or downtime
- 4
Review maintenance history to prioritize critical components
- 5
Consult with team members to gather insights on urgent needs
Example Answers
I start by assessing which repairs have the most severe impact on operations and safety. If a compressor is critical to production and poses safety risks, I prioritize that. I also look at past maintenance records to see if any issues could lead to bigger problems if ignored.
If there was a compressor failure during peak production hours, how would you respond to minimize downtime?
How to Answer
- 1
Assess the situation immediately to determine the cause of failure.
- 2
Communicate with production team to manage expectations and keep them informed.
- 3
Activate contingency plans such as switching to backup compressors if available.
- 4
Coordinate with maintenance staff for rapid diagnostics and repairs.
- 5
Document the incident and analyze for future prevention.
Example Answers
I would first assess the compressor to identify the cause of failure while keeping the production team informed on the status. If we have backup compressors, I would switch to one to minimize disruption. Meanwhile, I would call maintenance to expedite repairs on the primary compressor.
Imagine you need to train a new technician on operating and maintaining air compressors. What key points would you cover?
How to Answer
- 1
Explain the basic components of air compressors like the motor, pump, and receiver tank
- 2
Discuss safe operating procedures including pressure settings and emergency shut-off
- 3
Teach routine maintenance tasks such as oil changes and filter replacements
- 4
Highlight troubleshooting common issues and how to resolve them
- 5
Demonstrate proper use of personal protective equipment (PPE) when working with air compressors
Example Answers
I would start by explaining the basic components of an air compressor, including the motor, pump, and tank. Then, I'd discuss safe operating procedures, emphasizing the importance of correct pressure settings and how to use the emergency shut-off. I would also show them essential maintenance tasks such as changing oil and replacing filters.
If a compressor was found to be operating at above the prescribed pressure levels, what immediate actions would you take?
How to Answer
- 1
Check the pressure readings and verify with calibrated instruments
- 2
Identify the cause of the pressure increase, such as blockages or mechanical failures
- 3
Implement immediate measures to reduce pressure, like adjusting settings or releasing pressure safely
- 4
Notify relevant personnel about the situation to ensure safety protocols are followed
- 5
Document the incident for further analysis and maintenance planning
Example Answers
I would first confirm the pressure levels using calibrated instruments. Then, I would inspect the compressor for blockages or malfunctions. If necessary, I would safely release excess pressure and notify my supervisor immediately.
If you were tasked with choosing between two different compressor technologies for a new application, what factors would influence your decision?
How to Answer
- 1
Identify the specific application and its requirements.
- 2
Consider efficiency and energy consumption of each technology.
- 3
Evaluate maintenance needs and reliability of the compressors.
- 4
Compare initial cost and total cost of ownership over time.
- 5
Assess noise levels and environmental impact.
Example Answers
I would first analyze the application requirements to understand the necessary pressure and flow rates. Then, I would look at the efficiency ratings of each compressor and the energy costs associated with running them. Reliability and maintenance history would also be key factors, as well as the overall cost including installation. Lastly, I'd consider the noise levels and the expected environmental impact of each technology.
Air Compressor Engineer Position Details
Recommended Job Boards
CareerBuilder
www.careerbuilder.com/jobs/air-compressor-engineerThese job boards are ranked by relevance for this position.
Related Positions
Ace Your Next Interview!
Practice with AI feedback & get hired faster
Personalized feedback
Used by hundreds of successful candidates
Ace Your Next Interview!
Practice with AI feedback & get hired faster
Personalized feedback
Used by hundreds of successful candidates