Top 33 Water Pump Operator Interview Questions and Answers [Updated 2025]
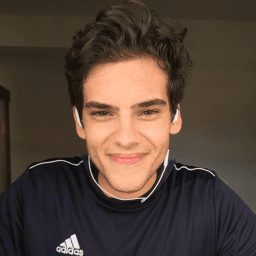
Andre Mendes
•
March 30, 2025
Preparing for a water pump operator interview can be a daunting task, but our comprehensive guide is here to help. In this post, you'll find a collection of the most common interview questions for the water pump operator role, along with example answers and practical tips to help you respond confidently and effectively. Whether you're new to the field or a seasoned professional, these insights will set you on the path to success.
Download Water Pump Operator Interview Questions in PDF
To make your preparation even more convenient, we've compiled all these top Water Pump Operatorinterview questions and answers into a handy PDF.
Click the button below to download the PDF and have easy access to these essential questions anytime, anywhere:
List of Water Pump Operator Interview Questions
Behavioral Interview Questions
Can you describe a time when you worked closely with a team to achieve a common goal?
How to Answer
- 1
Choose a specific project where teamwork was essential
- 2
Highlight your role and contributions within the team
- 3
Emphasize the outcome achieved as a result of teamwork
- 4
Mention any challenges faced and how the team overcame them
- 5
Keep it concise and focused on the team dynamic
Example Answers
In my last job, our team was tasked with reducing production downtime. I coordinated daily meetings to track our progress and identify obstacles. By streamlining communication, we managed to reduce downtime by 20% within three months.
Tell me about a time you faced a significant challenge in your last job as an operator and how you overcame it.
How to Answer
- 1
Identify a specific challenge you faced in your operator role.
- 2
Explain the impact of the challenge on your work or team.
- 3
Describe the steps you took to address the challenge.
- 4
Highlight the outcome and what you learned from the experience.
- 5
Keep your answer structured and focused on your actions.
Example Answers
In my last job, we faced a major equipment breakdown that halted production. I quickly coordinated with the maintenance team, arranged for emergency repairs, and kept the team informed to minimize downtime. As a result, we resumed operations in two hours instead of the expected four, ensuring we met our daily targets. This taught me the importance of communication during a crisis.
Don't Just Read Water Pump Operator Questions - Practice Answering Them!
Reading helps, but actual practice is what gets you hired. Our AI feedback system helps you improve your Water Pump Operator interview answers in real-time.
Personalized feedback
Unlimited practice
Used by hundreds of successful candidates
Describe a situation where you had to quickly adapt to changes in your work environment or operational procedures.
How to Answer
- 1
Think of a specific instance when changes occurred unexpectedly.
- 2
Use the STAR method: Situation, Task, Action, Result.
- 3
Highlight your ability to stay calm under pressure.
- 4
Show how you communicated with your team during the change.
- 5
Mention any positive outcomes that resulted from your adaptation.
Example Answers
In my previous role as an operator, we were notified of a sudden change in our production schedule due to supply chain issues. I quickly assessed the situation, prioritized tasks that could be completed with available resources, and communicated these changes to my team clearly. As a result, we managed to meet our revised targets without delay.
Have you ever taken on a leadership role in a project? What was the outcome?
How to Answer
- 1
Choose a specific project where you led a team or initiative
- 2
Begin with the project's purpose and your role within it
- 3
Discuss the challenges you faced and how you addressed them
- 4
Highlight the positive outcome and any metrics of success
- 5
Reflect on what you learned and how it impacted your leadership style
Example Answers
In my last job, I led a project to streamline our inventory management. I coordinated a team of five and implemented new software. We faced initial resistance but addressed it through training. As a result, we reduced inventory discrepancies by 30% in three months.
What motivates you to perform well in an operational role?
How to Answer
- 1
Identify key factors that drive your performance, such as goals, team success, or efficiency.
- 2
Relate personal satisfaction and fulfillment from solving problems.
- 3
Highlight the importance of contributing to the company’s mission and objectives.
- 4
Mention ways you track and measure your success in operations.
- 5
Include examples of past experiences that illustrate your motivation.
Example Answers
I'm motivated by achieving measurable results and improving processes. When I see that my efforts lead to higher efficiency and cost savings, it drives me to continue innovating.
Describe a decision you made in a previous position that had a significant impact on operations.
How to Answer
- 1
Think of a specific decision that improved efficiency or reduced costs.
- 2
Use the STAR method: Situation, Task, Action, Result.
- 3
Quantify the impact when possible (e.g., percentage savings, time saved).
- 4
Focus on your role and contributions in the decision process.
- 5
Be prepared to discuss any challenges faced and how you overcame them.
Example Answers
In my last job, we faced frequent delays in the supply chain. I decided to implement a new inventory management system. This reduced order processing time by 30%, allowing us to meet customer demand more effectively.
How do you keep up with new developments in operational technology?
How to Answer
- 1
Subscribe to industry newsletters and journals focused on operational technology.
- 2
Participate in relevant online forums and discussion groups to share insights and trends.
- 3
Attend conferences and workshops related to operations management and technology.
- 4
Take online courses or certifications in emerging technologies relevant to operations.
- 5
Follow thought leaders in operational technology on social media platforms to gain new perspectives.
Example Answers
I subscribe to several industry newsletters and attend local workshops to stay informed about the latest technologies. Recently, I attended a conference where I learned about IoT applications in operations.
Tell me about a time when you received constructive feedback. How did you respond to it?
How to Answer
- 1
Choose a specific example that highlights your growth.
- 2
Explain the feedback you received clearly.
- 3
Describe your immediate reaction and how you processed the feedback.
- 4
Discuss the steps you took to implement the feedback.
- 5
Reflect on the outcome and what you learned from the experience.
Example Answers
In my last job, my supervisor pointed out that I needed to improve my time management skills. I took this feedback seriously, reflected on my current habits, and started using a project management tool to organize my tasks. As a result, my productivity improved significantly, and I was able to meet deadlines more consistently.
Can you describe a time when you introduced a new idea or practice that improved operations?
How to Answer
- 1
Identify a specific situation where you saw a need for improvement.
- 2
Briefly explain the idea or practice you introduced.
- 3
Describe the implementation process and any challenges faced.
- 4
Quantify the results if possible; mention metrics or feedback.
- 5
Keep it concise and focused on your contributions.
Example Answers
In my previous role at XYZ Company, I noticed that our inventory management was causing delays. I proposed implementing a new software tool that allowed for real-time tracking of inventory levels. After getting approval, I led the training sessions for staff. As a result, we reduced inventory discrepancies by 30% and improved order fulfillment speed by 20%.
Describe a time when you set a professional goal for yourself related to your role as an operator.
How to Answer
- 1
Identify a specific goal relevant to your operator role
- 2
Explain the steps you took to achieve that goal
- 3
Highlight any challenges you faced and how you overcame them
- 4
Quantify the outcome or improvement resulting from your goal
- 5
Reflect on what you learned from the experience and how it shaped you
Example Answers
I set a goal to improve my machine efficiency by 15% over three months. I analyzed my work patterns and identified time-wasting steps. By restructuring my workflow and using better tools, I achieved a 20% increase in efficiency, which boosted overall production.
Don't Just Read Water Pump Operator Questions - Practice Answering Them!
Reading helps, but actual practice is what gets you hired. Our AI feedback system helps you improve your Water Pump Operator interview answers in real-time.
Personalized feedback
Unlimited practice
Used by hundreds of successful candidates
Give an example of how you successfully communicated a complex idea to someone without a technical background.
How to Answer
- 1
Identify the complex idea you communicated.
- 2
Break the idea down into simple terms.
- 3
Use analogies or real-life examples for clarity.
- 4
Ensure to check for understanding by asking open-ended questions.
- 5
Be patient and ready to re-explain if needed.
Example Answers
I explained how our automated system works to a colleague in sales by comparing it to a vending machine: just like you insert money and select a product, the system requires inputs to generate the necessary reports.
Technical Interview Questions
What types of equipment have you operated, and what maintenance tasks are you familiar with?
How to Answer
- 1
List specific equipment you have experience with, such as forklifts, conveyors, or heavy machinery.
- 2
Mention the maintenance tasks you routinely performed, like lubricating parts or changing filters.
- 3
Highlight any specialized training or certifications you hold related to the equipment.
- 4
Be prepared to discuss how you troubleshoot common issues with the equipment.
- 5
Keep your answers concise and relevant to the job you're applying for.
Example Answers
I have operated forklifts and pallet jacks extensively. I regularly performed maintenance tasks like checking oil levels and replacing worn-out parts.
Can you explain the operational processes you have experience with in your previous roles?
How to Answer
- 1
Identify key operational processes you were involved in.
- 2
Use specific examples from your previous roles to illustrate your experience.
- 3
Highlight how these processes improved efficiency or outcomes.
- 4
Be prepared to discuss any metrics or results from your contributions.
- 5
Keep your explanation clear and focus on relevant experiences.
Example Answers
In my last role as a warehouse operator, I managed inventory processes by implementing a real-time tracking system. This reduced discrepancies by 30% and improved order fulfillment speed by 20%.
Don't Just Read Water Pump Operator Questions - Practice Answering Them!
Reading helps, but actual practice is what gets you hired. Our AI feedback system helps you improve your Water Pump Operator interview answers in real-time.
Personalized feedback
Unlimited practice
Used by hundreds of successful candidates
What do you consider to be the most important safety protocols for an operator and why?
How to Answer
- 1
Identify key safety protocols relevant to the operation, such as lockout/tagout, PPE usage, and emergency response.
- 2
Explain the rationale behind each protocol and its impact on safety and efficiency.
- 3
Use specific examples from past experiences to illustrate your understanding.
- 4
Emphasize teamwork and communication in maintaining safety protocols.
- 5
Conclude with the importance of continuous training and following regulatory standards.
Example Answers
Effective communication is vital in safety protocols. For example, using clear signals and maintaining open lines when operating machinery prevents accidents.
How do you approach analyzing data to improve operational efficiency?
How to Answer
- 1
Identify key performance indicators relevant to operations
- 2
Use data visualization tools to reveal trends and outliers
- 3
Perform a root cause analysis on inefficiencies found in the data
- 4
Implement data-driven solutions and monitor their impact
- 5
Regularly review and adjust strategies based on new data insights
Example Answers
I start by defining the KPIs that reflect our operational goals. I then gather data and leverage tools like Tableau to visualize trends. If I identify inefficiencies, I conduct a root cause analysis and implement solutions, monitoring their impact over time.
What manufacturing or operational software are you proficient in?
How to Answer
- 1
Identify key software used in manufacturing such as ERP or MES systems.
- 2
Mention specific tools like SAP, Oracle, or Lean manufacturing software.
- 3
Describe your hands-on experience and specific tasks you performed.
- 4
Highlight any certifications related to the software.
- 5
Be honest about your skill level and willingness to learn.
Example Answers
I am proficient in SAP ERP, where I managed inventory control and production scheduling. I also worked with MES to track real-time production data.
Can you describe your approach to troubleshooting equipment failures?
How to Answer
- 1
Start with identifying the symptoms of the failure
- 2
Gather information by consulting logs and data
- 3
Use a systematic approach to isolate the problem
- 4
Test potential fixes one at a time to verify solutions
- 5
Document the process and outcome for future reference
Example Answers
When troubleshooting equipment failures, I first identify the symptoms to understand what isn't working properly. Then, I gather relevant data and logs related to the failure. Following that, I systematically isolate the issue by testing components step by step. I prefer to test one potential fix at a time to see if it resolves the problem. Finally, I document what steps were taken in case the issue arises again.
What quality control measures do you think are essential for operators?
How to Answer
- 1
Identify key quality control measures like inspections and testing protocols
- 2
Emphasize the importance of adhering to standard operating procedures
- 3
Discuss continuous monitoring and real-time feedback systems
- 4
Mention training and development for operators on quality standards
- 5
Highlight the role of documentation in quality control
Example Answers
I believe essential quality control measures for operators include regular inspections and integrating real-time monitoring systems. Adhering to SOPs helps maintain standards, and continuous training ensures everyone is up to date with quality expectations.
How do you ensure that you adhere to technical documentation when operating equipment?
How to Answer
- 1
Familiarize yourself with the documentation before operation
- 2
Highlight critical procedures or safety points
- 3
Use checklists derived from the documentation
- 4
Keep the documentation accessible during operation
- 5
Report any discrepancies in the documentation immediately
Example Answers
I make sure to read the technical documentation thoroughly before starting any operation. I highlight safety procedures and keep a printed copy nearby for easy reference.
What steps do you take to ensure the machinery is functioning correctly before starting a shift?
How to Answer
- 1
Conduct a visual inspection for any signs of damage or wear
- 2
Check fluid levels and refill if necessary
- 3
Test all emergency stop buttons and safety features
- 4
Calibrate settings according to operational requirements
- 5
Review previous shift logs for noted issues or maintenance actions
Example Answers
Before starting my shift, I perform a visual inspection for any obvious damage and check all fluid levels. Then, I test the emergency stops to ensure they work properly, calibrate any equipment needed, and review the previous shift logs to address any noted issues.
How do you measure and improve operational efficiency in your work?
How to Answer
- 1
Identify key performance indicators (KPIs) relevant to operations.
- 2
Analyze workflows to spot bottlenecks and inefficiencies.
- 3
Implement technology or tools to automate tasks.
- 4
Regularly review and adjust processes based on data insights.
- 5
Engage with team feedback to uncover improvement areas.
Example Answers
I measure operational efficiency by tracking KPIs such as cycle time and throughput rates. I regularly analyze workflows and identify bottlenecks, then implement tools that automate repetitive tasks to enhance speed and accuracy.
Don't Just Read Water Pump Operator Questions - Practice Answering Them!
Reading helps, but actual practice is what gets you hired. Our AI feedback system helps you improve your Water Pump Operator interview answers in real-time.
Personalized feedback
Unlimited practice
Used by hundreds of successful candidates
How do you ensure compliance with both internal and external regulations in your work?
How to Answer
- 1
Familiarize yourself with all relevant regulations and policies.
- 2
Implement a checklist to monitor compliance regularly.
- 3
Document all compliance-related activities and findings.
- 4
Engage in ongoing training to stay updated on regulatory changes.
- 5
Communicate with team members to ensure everyone understands the regulations.
Example Answers
I stay informed about both internal policies and external regulations by reviewing them quarterly. I use a compliance checklist to ensure I meet all requirements and document everything for future reference.
Situational Interview Questions
Imagine you are operating machinery and notice a fault. What steps would you take to handle the situation?
How to Answer
- 1
Immediately stop the machinery to prevent further damage or danger.
- 2
Follow safety protocols and ensure the area is safe for you and others.
- 3
Assess the nature of the fault if safe to do so.
- 4
Notify your supervisor or maintenance team about the issue.
- 5
Document the fault according to company procedures.
Example Answers
First, I would stop the machinery right away to avoid any accidents. Then, I would check the area for safety before assessing the fault. After that, I would report the issue to my supervisor and document the incident as required.
If you are faced with multiple urgent tasks at once, how would you prioritize them?
How to Answer
- 1
Identify deadlines for each task
- 2
Assess the impact of each task on overall operations
- 3
Consider resources and personnel availability
- 4
Communicate with team members about the priorities
- 5
Be flexible and ready to adjust as needs change
Example Answers
I would first list all tasks along with their deadlines and impacts. Then, I'd communicate with my team to ensure we're aligned on priorities before starting the most urgent task.
Don't Just Read Water Pump Operator Questions - Practice Answering Them!
Reading helps, but actual practice is what gets you hired. Our AI feedback system helps you improve your Water Pump Operator interview answers in real-time.
Personalized feedback
Unlimited practice
Used by hundreds of successful candidates
If you disagreed with a coworker about operational procedures, how would you handle the situation?
How to Answer
- 1
Listen to your coworker's perspective without interrupting.
- 2
Express your viewpoint calmly and clearly.
- 3
Focus on the facts and data supporting your stance.
- 4
Seek a collaborative solution rather than confrontation.
- 5
If needed, involve a third party for mediation.
Example Answers
I would first listen to my coworker to understand their perspective. Then, I would share my viewpoint with data that supports my position. We could then discuss ways to find a common ground or a solution that works for both of us.
Suppose you identify an inefficient process in your work area. What would you do to address it?
How to Answer
- 1
Clearly define the inefficiency and its impact on the team.
- 2
Gather data to support your observations and identify the root cause.
- 3
Propose a specific solution to improve the process.
- 4
Communicate your findings with your supervisor and team.
- 5
Offer to lead a trial or pilot of the new process.
Example Answers
I noticed that our inventory tracking takes too long, which delays order fulfillment. I analyzed the system and found that manual entries were causing errors. I proposed switching to automated software. I shared this with my supervisor and organized a trial to test the new system, which reduced processing time by 30%.
What actions would you take if an emergency alarm sounded while you were operating machinery?
How to Answer
- 1
Immediately stop the machinery to prevent accidents
- 2
Assess the situation to understand the nature of the alarm
- 3
Follow the established emergency protocols for your workplace
- 4
Notify your supervisor or the emergency response team
- 5
Document the incident after ensuring safety and compliance
Example Answers
I would stop the machinery at once and check the alarm details to assess the situation. Then, I would follow the emergency procedures by alerting my supervisor and ensuring everyone is safe.
How would you handle a situation where a team member is not pulling their weight?
How to Answer
- 1
Address the issue directly and privately with the team member.
- 2
Ask open-ended questions to understand their perspective.
- 3
Discuss how their performance affects the team and project.
- 4
Work together to come up with a plan to improve their contribution.
- 5
Follow up to ensure the plan is being implemented and offer support.
Example Answers
I would first talk to the team member privately to understand if there are any issues affecting their performance. I would express how their contributions are important for the team's success and work with them to create a plan that helps them get back on track.
If you are consistently finding it hard to meet deadlines, what steps would you take to improve?
How to Answer
- 1
Identify specific reasons for missing deadlines
- 2
Prioritize tasks using a simple ranking system
- 3
Break down large tasks into smaller, manageable steps
- 4
Set realistic deadlines and adjust schedules as needed
- 5
Communicate proactively with team members if delays arise
Example Answers
I would first identify why I'm missing deadlines, whether it's poor time management or unexpected challenges. Then, I'd prioritize tasks based on urgency, break them down into smaller actions, and set clearer deadlines for myself. Lastly, I'd keep my team informed if I anticipate any issues.
How would you handle the stress of a high-pressure situation while ensuring operational safety?
How to Answer
- 1
Stay calm and take a deep breath before responding.
- 2
Prioritize tasks by assessing the situation quickly.
- 3
Communicate clearly with team members to coordinate actions.
- 4
Focus on safety protocols and procedures to guide your actions.
- 5
Reflect on past high-pressure experiences to inform your decision-making.
Example Answers
In a high-pressure situation, I would first take a moment to assess the urgency and prioritize tasks. I would communicate clearly with my team, ensuring everyone understands their roles and safety protocols to mitigate risks.
If resources are limited, how would you handle task assignments among your team?
How to Answer
- 1
Assess the skills and strengths of each team member.
- 2
Prioritize tasks based on urgency and impact.
- 3
Communicate clearly with the team about constraints.
- 4
Consider cross-training team members for flexibility.
- 5
Regularly review the workload and adjust assignments as necessary.
Example Answers
I would first evaluate the skills of my team to match tasks to the right individuals. Then, I would prioritize tasks that deliver the most value and keep the team informed about our resource limitations. This way, we stay aligned and can adapt quickly if needed.
What would you do if you realized there was a lack of coordination among team members during operations?
How to Answer
- 1
Identify the specific areas of miscommunication or lack of clarity.
- 2
Initiate a team meeting to address the issues directly.
- 3
Encourage open dialogue to understand team members' perspectives.
- 4
Establish clearer roles and responsibilities to prevent future issues.
- 5
Implement regular check-ins to monitor coordination and progress.
Example Answers
I would first identify the key areas where coordination is lacking. Then, I would organize a team meeting to discuss these challenges and encourage everyone to share their thoughts. This way, we can clarify roles and establish a plan for better communication moving forward.
Don't Just Read Water Pump Operator Questions - Practice Answering Them!
Reading helps, but actual practice is what gets you hired. Our AI feedback system helps you improve your Water Pump Operator interview answers in real-time.
Personalized feedback
Unlimited practice
Used by hundreds of successful candidates
If you noticed a decline in product quality, what steps would you take to investigate the issue?
How to Answer
- 1
Gather data on quality metrics to identify trends.
- 2
Interview team members involved in production for insights.
- 3
Review recent changes in processes or materials used.
- 4
Conduct tests or inspections on the affected products.
- 5
Collaborate with quality assurance to understand their findings.
Example Answers
I would first review our quality metrics to pinpoint when the decline started. Then, I would talk to the production team to see if they noticed anything unusual. Next, I'd check if any new materials or processes were introduced.
Water Pump Operator Position Details
Recommended Job Boards
ZipRecruiter
www.ziprecruiter.com/Jobs/Water-Pump-OperatorThese job boards are ranked by relevance for this position.
Related Positions
- Water Pumper
- Steam Plant Operator
- Tank Farm Operator
- Steam Engineer
- Boiler Operator
- Stationary Steam Engineer
- Air Compressor Engineer
- Turbine Operator
- Watch Engineer
- Compressor Operator
Similar positions you might be interested in.
Ace Your Next Interview!
Practice with AI feedback & get hired faster
Personalized feedback
Used by hundreds of successful candidates
Ace Your Next Interview!
Practice with AI feedback & get hired faster
Personalized feedback
Used by hundreds of successful candidates