Top 32 Blower Interview Questions and Answers [Updated 2025]
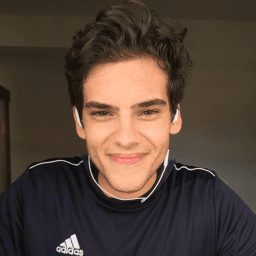
Andre Mendes
•
March 30, 2025
Preparing for a blower role interview can be daunting, but we've got you covered! In this blog post, we'll delve into the most common interview questions you might encounter, complete with example answers and valuable tips to help you respond confidently and effectively. Whether you're a seasoned professional or a newcomer, this guide will equip you with the insights needed to excel in your interview.
Download Blower Interview Questions in PDF
To make your preparation even more convenient, we've compiled all these top Blowerinterview questions and answers into a handy PDF.
Click the button below to download the PDF and have easy access to these essential questions anytime, anywhere:
List of Blower Interview Questions
Behavioral Interview Questions
Can you describe a time when you identified a safety hazard while operating equipment? What steps did you take to address it?
How to Answer
- 1
Start with a specific situation where you spotted a hazard.
- 2
Explain the nature of the hazard clearly.
- 3
Detail the immediate actions you took to mitigate the risk.
- 4
Mention any follow-up actions to ensure ongoing safety.
- 5
Emphasize the importance of safety and teamwork.
Example Answers
While operating a blower, I noticed a loose guard cover that could potentially get caught in the blades. I immediately powered down the equipment and secured the cover. After that, I reported the issue to my supervisor to have it properly fixed and ensured all team members were aware to prevent accidents.
Tell me about a time when you had to work closely with other team members to complete a project. What was your role and how did you contribute?
How to Answer
- 1
Select a specific project example from your experience
- 2
Clearly define your role within the team
- 3
Highlight your contributions and skills utilized
- 4
Discuss the outcome and team dynamic
- 5
Reflect on what you learned from the collaboration
Example Answers
In my last job, we worked on a project to improve our production line efficiency. I was the team lead and coordinated between engineers and production staff. I facilitated daily meetings to share progress and address any issues, which increased our productivity by 20%. The team's collaboration was key to our success, and I learned the importance of effective communication.
Don't Just Read Blower Questions - Practice Answering Them!
Reading helps, but actual practice is what gets you hired. Our AI feedback system helps you improve your Blower interview answers in real-time.
Personalized feedback
Unlimited practice
Used by hundreds of successful candidates
Describe a challenging situation you encountered while managing blower operations. How did you resolve it?
How to Answer
- 1
Identify a specific challenge with blower operations.
- 2
Explain the impact the challenge had on operations.
- 3
Describe the steps you took to analyze and resolve the issue.
- 4
Highlight any teamwork or communication involved.
- 5
Conclude with the results and what you learned.
Example Answers
I faced a situation where our main blower failed during peak hours, causing a halt in production. I immediately assessed the situation and organized a team to troubleshoot the blower. After identifying a power supply issue, we coordinated with maintenance to fix it promptly. As a result, we minimized downtime by 30%. I learned the importance of quick decision-making and teamwork.
Have you ever had to lead a team during a critical operation? How did you ensure everyone was aligned and on task?
How to Answer
- 1
Describe the situation briefly and clearly.
- 2
Highlight your leadership role and specific actions taken.
- 3
Mention how you communicated with the team.
- 4
Explain how you kept everyone focused and accountable.
- 5
Share the outcome and any lessons learned.
Example Answers
During a major outage, I led a team of six engineers to restore service. I organized a quick meeting to assess the situation, assigned clear roles based on expertise, and set up regular check-ins to track progress. We used a shared dashboard for real-time updates, ensuring everyone stayed aligned. We restored service within three hours, and I learned the importance of clear communication under pressure.
Can you provide an example of how you trained a new employee on blower operations? What challenges did you face?
How to Answer
- 1
Start with a clear overview of the training process.
- 2
Mention specific tools or materials used during training.
- 3
Identify any initial challenges faced during training.
- 4
Highlight how you adapted to overcome those challenges.
- 5
Conclude with the outcome or improvement seen after training.
Example Answers
I trained a new employee by providing them a hands-on demonstration of the blower operations using the manual and videos. One challenge was their difficulty in understanding the safety protocols, so I organized a workshop to reinforce those points. As a result, they became more confident and completed their certification successfully.
Describe a time when you received critical feedback on your work regarding blower operations. How did you respond?
How to Answer
- 1
Focus on a specific instance where you received feedback.
- 2
Explain the feedback clearly and objectively.
- 3
Describe your immediate reaction and how you processed it.
- 4
Discuss the actions you took to improve based on the feedback.
- 5
Conclude with the positive outcome resulting from your response.
Example Answers
In my previous role, I received feedback on my blower maintenance schedule being too infrequent. I took it seriously and reviewed the operational data. I then adjusted the schedule to a more regular maintenance cycle, which improved efficiency and reduced downtime. The result was a noticeable decrease in blower failures.
What accomplishment are you most proud of in your career related to blower operations?
How to Answer
- 1
Choose a specific accomplishment that showcases your skills in blower operations.
- 2
Quantify your achievement with metrics if possible to emphasize impact.
- 3
Explain the challenges you faced and how you overcame them.
- 4
Highlight the skills or techniques you used in achieving this success.
- 5
Connect your accomplishment to the value it brought to the company or team.
Example Answers
I am proud of successfully leading a project to optimize our blower system, which resulted in a 20% increase in efficiency and reduced energy costs by $15,000 annually. The challenge was dealing with outdated equipment, but by implementing a new maintenance schedule and training the team on best practices, we achieved these results.
Have you ever suggested a new technique or technology in your blower operations? What was it and what was the outcome?
How to Answer
- 1
Think of a specific instance where you proposed a change
- 2
Describe the technique or technology you suggested clearly
- 3
Explain the reasoning behind your suggestion and its projected benefits
- 4
Include the outcome, focusing on tangible improvements
- 5
Mention any feedback from your team or management regarding your suggestion
Example Answers
In my previous role, I suggested using variable frequency drives for our blowers. This allowed us to adjust the speed of the blowers based on demand, which improved energy efficiency. After implementation, we reduced energy costs by 20% and received positive feedback from management on the operational efficiency.
Describe a situation where you had to manage risks related to equipment operation. What strategies did you employ?
How to Answer
- 1
Identify a specific incident related to equipment risks you handled.
- 2
Highlight your assessment of potential risks in that situation.
- 3
Discuss the specific strategies you implemented to mitigate those risks.
- 4
Emphasize the outcome of your actions and any improvements made.
- 5
Consider including teamwork or collaboration with others in your approach.
Example Answers
In a previous role, we faced a potential failure in a blower due to excessive dust accumulation. I assessed the risks and implemented a new filter maintenance schedule to ensure optimal airflow. This reduced equipment failure by 30%.
Don't Just Read Blower Questions - Practice Answering Them!
Reading helps, but actual practice is what gets you hired. Our AI feedback system helps you improve your Blower interview answers in real-time.
Personalized feedback
Unlimited practice
Used by hundreds of successful candidates
How do you align your work practices with the safety culture in a manufacturing environment?
How to Answer
- 1
Understand and adhere to safety protocols and guidelines provided by the company.
- 2
Communicate openly with colleagues about safety concerns and practices.
- 3
Participate in safety training and workshops regularly.
- 4
Report any unsafe conditions or practices immediately to management.
- 5
Set an example by following safety measures consistently and encouraging others to do the same.
Example Answers
I always make sure to follow the safety protocols outlined by our company and discuss any concerns with my team. I believe regular communication ensures we all stay aligned with the safety culture.
Technical Interview Questions
What are the key components of a centrifugal blower and how do they function together?
How to Answer
- 1
Identify and name the main components such as the impeller, casing, and motor.
- 2
Explain the role of each component in generating airflow.
- 3
Discuss how the components interact to increase pressure and move air.
- 4
Use simple terms to ensure clarity for the interviewer.
- 5
Be prepared for follow-up questions on specific components or applications.
Example Answers
A centrifugal blower mainly consists of an impeller, casing, and motor. The impeller rotates and adds kinetic energy to the air, while the casing directs the airflow and increases pressure. Together, they move air efficiently in a system.
How do you measure the performance of a blower system? What parameters do you monitor?
How to Answer
- 1
Identify key performance indicators such as flow rate, pressure, and power consumption.
- 2
Discuss the importance of monitoring efficiency and specific energy usage.
- 3
Explain the role of vibration and temperature measurements in assessing blower health.
- 4
Mention the significance of regular maintenance checks and system inspections.
- 5
Include how data logging can help in tracking performance over time.
Example Answers
To measure blower system performance, I focus on flow rate and pressure differential, which indicate how effectively the blower is moving air. I also monitor power consumption to ensure it's running efficiently, and I keep an eye on vibration levels to catch any mechanical issues early.
Don't Just Read Blower Questions - Practice Answering Them!
Reading helps, but actual practice is what gets you hired. Our AI feedback system helps you improve your Blower interview answers in real-time.
Personalized feedback
Unlimited practice
Used by hundreds of successful candidates
What are the best practices for maintaining a blower to ensure optimal performance?
How to Answer
- 1
Regularly check and clean air filters to prevent clogs.
- 2
Inspect and tighten all mechanical connections to avoid air leaks.
- 3
Lubricate bearings and other moving parts according to the manufacturer's schedule.
- 4
Monitor and record operating temperatures and pressures to detect abnormalities.
- 5
Schedule periodic professional inspections for wear and integrity.
Example Answers
One best practice is to regularly check and clean the air filters to prevent clogs, which can reduce efficiency.
Can you explain how you would troubleshoot a blower that is producing abnormal noises?
How to Answer
- 1
Start by identifying the type of noise: is it a rattling, grinding, or humming sound?
- 2
Check for loose components or debris around the blower that may be causing noise.
- 3
Examine the blower's motor and bearings for wear or damage.
- 4
Ensure that the blower is properly mounted and aligned to prevent vibrations.
- 5
Test the blower at different speeds to locate when the noise occurs.
Example Answers
First, I would listen closely to identify the type of noise. If it's a rattling sound, I would check for any loose bolts or debris. For a grinding noise, I'd inspect the motor and bearings for wear.
How do you integrate blower systems with other machinery in a production line?
How to Answer
- 1
Identify specific machinery that requires airflow assistance.
- 2
Ensure proper sizing and capacity of blowers for equipment.
- 3
Utilize control systems to synchronize blower operation with machine cycles.
- 4
Install safety and monitoring systems to prevent failures during integration.
- 5
Collaborate with mechanical and electrical engineers for optimal layout.
Example Answers
To integrate blower systems, I first assess which machines need additional airflow, ensuring that the blower capacity matches the airflow demands. Then, I synchronize the blower's operation with those machines, using control systems to maintain efficiency.
What safety regulations are particularly relevant to operating industrial blowers?
How to Answer
- 1
Familiarize yourself with OSHA regulations relevant to blowers.
- 2
Mention the importance of proper training for operators.
- 3
Highlight the significance of regular maintenance and inspections.
- 4
Discuss the need for personal protective equipment (PPE).
- 5
Reference any industry-specific standards that apply to blowers.
Example Answers
OSHA regulations focus on ensuring that blowers are operated safely, emphasizing the need for operator training and awareness of hazards. Maintenance schedules should be strictly followed to avoid accidents, and PPE like gloves and goggles must be used.
Explain the principle of fluid dynamics as it relates to the operation of blowers.
How to Answer
- 1
Define fluid dynamics briefly to set context.
- 2
Explain how pressure differences lead to airflow.
- 3
Discuss Bernoulli's principle and its relevance to blowers.
- 4
Mention the impact of impeller design on airflow.
- 5
Relate fluid dynamics to energy efficiency in blower operation.
Example Answers
Fluid dynamics is the study of how fluids move. In blowers, we create pressure differences that push air. According to Bernoulli's principle, as air speeds up, its pressure drops, which helps in creating suction or airflow. The design of the impeller is crucial as it determines how efficiently air is moved through the blower. Understanding these principles helps design blowers that operate efficiently.
What emergency procedures should be followed in case of a blower malfunction?
How to Answer
- 1
Immediately stop the blower to prevent further damage or hazards.
- 2
Notify supervisor or team leader about the malfunction.
- 3
Follow the site-specific emergency protocols for equipment failure.
- 4
Ensure all personnel are at a safe distance from the blower.
- 5
Document the malfunction details for future analysis.
Example Answers
In case of a blower malfunction, the first step is to stop the blower to prevent additional hazards. Then, I would inform my supervisor and follow our emergency protocols to maintain safety.
How do you ensure that the blower systems operate with maximum energy efficiency?
How to Answer
- 1
Perform regular maintenance to keep the blower systems in optimal condition
- 2
Monitor airflow and pressure to adjust settings for maximum efficiency
- 3
Implement variable speed drives to match blower output to demand
- 4
Conduct efficiency audits to identify and correct energy waste
- 5
Train staff on best practices to operate blowers efficiently
Example Answers
I ensure maximum energy efficiency by implementing regular maintenance schedules and using variable speed drives to adjust blower output based on real-time demand.
What considerations must be made when designing a blower system for a specific application?
How to Answer
- 1
Identify the required airflow and pressure for the application
- 2
Select the blower type based on the application needs
- 3
Consider the system's operating environment and conditions
- 4
Evaluate noise levels and regulatory requirements
- 5
Plan for maintenance and serviceability of the blower system
Example Answers
When designing a blower system, first determine the airflow and pressure required for optimal performance in the application. Next, choose between positive displacement or centrifugal blowers based on these needs. Don't forget to assess the operating environment, ensuring the blower materials can withstand the conditions.
Don't Just Read Blower Questions - Practice Answering Them!
Reading helps, but actual practice is what gets you hired. Our AI feedback system helps you improve your Blower interview answers in real-time.
Personalized feedback
Unlimited practice
Used by hundreds of successful candidates
What are the key technical specifications to consider when selecting a blower for an application?
How to Answer
- 1
Identify the required airflow rate in CFM or m³/h.
- 2
Consider the pressure requirements, knowing whether the application needs positive or negative pressure.
- 3
Check the blower's efficiency rating to ensure energy savings.
- 4
Assess the ambient conditions like temperature and humidity that can affect performance.
- 5
Look at the blower design type (centrifugal, positive displacement, etc.) that suits the application.],
- 6
sampleAnswers
Example Answers
When selecting a blower, I consider the required airflow in CFM to match the application needs, the necessary pressure for the system, and the efficiency to minimize energy costs. I also choose the blower type based on the application, such as centrifugal for high volume or positive displacement for consistent pressure.
Situational Interview Questions
Imagine you notice that a colleague is not following standard operating procedures when using the blower. How would you approach this situation?
How to Answer
- 1
Observe the colleague discreetly to ensure you understand the situation completely.
- 2
Approach the colleague privately to avoid embarrassing them in front of others.
- 3
Express concern for safety and efficiency rather than simply pointing out the mistake.
- 4
Offer to review the standard operating procedures together to clarify any misunderstandings.
- 5
Suggest additional training if necessary, emphasizing the importance of following procedures.
Example Answers
I would first observe to confirm that they are indeed not following the procedures. Then, I would approach them privately, expressing my concern for safety and suggesting we review the standard operating procedures together.
If you are faced with a sudden equipment failure during a critical time, what steps would you take to minimize downtime?
How to Answer
- 1
Stay calm and assess the situation quickly.
- 2
Identify the root cause of the failure and gather necessary tools.
- 3
Implement temporary fixes if possible to keep production going.
- 4
Communicate the issue to your team and supervisors promptly.
- 5
Document the incident for future reference and improvement.
Example Answers
I would first remain calm and assess the equipment to understand the issue. Then, I would gather the necessary tools to either temporarily fix it or implement a workaround. It's important to keep communication open with my team while we handle the situation, and I would document everything for future learning.
Don't Just Read Blower Questions - Practice Answering Them!
Reading helps, but actual practice is what gets you hired. Our AI feedback system helps you improve your Blower interview answers in real-time.
Personalized feedback
Unlimited practice
Used by hundreds of successful candidates
You observe that the ventilation in the work area has decreased significantly. What immediate actions would you take to ensure safety?
How to Answer
- 1
Assess the immediate area for any signs of danger related to reduced ventilation
- 2
Communicate the issue to the team and supervisors urgently
- 3
Shut down any equipment that may pose a risk due to poor air quality
- 4
Evacuate the area if conditions seem unsafe for continued work
- 5
Implement temporary ventilation solutions if possible
Example Answers
First, I would assess the area for any immediate hazards, then notify my supervisor and the team about the ventilation issue. If the air quality is compromised, I would shut down equipment to prevent fumes from accumulating and, if necessary, evacuate the area before implementing any temporary ventilation measures.
How would you handle a scenario where two team members disagree on the best way to operate a blower?
How to Answer
- 1
Listen to both team members' perspectives carefully
- 2
Encourage them to discuss their reasoning logically
- 3
Facilitate a small meeting to address the disagreement
- 4
Suggest a trial run for both methods and evaluate results
- 5
Aim to reach a consensus based on operational efficiency
Example Answers
I would first listen to both team members to understand their viewpoints. Then, I'd encourage them to share their reasoning and work together to explore both methods. If the disagreement persists, I would suggest running a trial of each method to see which one performs better and decide from there.
If a product being processed with a blower does not meet quality standards, what steps would you take to investigate and resolve the issue?
How to Answer
- 1
Identify the specific quality standards that were not met.
- 2
Check the blower settings and operation to ensure they are correct.
- 3
Examine the materials used for any defects or inconsistencies.
- 4
Conduct a thorough inspection of the processing environment for any issues.
- 5
Document your findings and implement corrective actions to prevent recurrence.
Example Answers
I would first determine which specific quality standards were not met. Then, I'd inspect the blower settings to ensure they are appropriate. After that, I'd check the raw materials for quality and any defects. Lastly, I'd document everything and take steps to correct any issues found.
If you were tasked with improving the efficiency of a blower system, what steps would you take?
How to Answer
- 1
Conduct an initial assessment of the current blower system performance and inefficiencies.
- 2
Identify key parameters and operating conditions affecting performance, such as pressure, flow rate, and energy consumption.
- 3
Explore possible upgrades or replacements for blower components like impellers or motors.
- 4
Implement monitoring tools to track performance metrics and identify ongoing issues.
- 5
Consider potential modifications to the system design to optimize airflow and reduce losses.
Example Answers
First, I would assess the blower system to identify inefficiencies related to pressure and flow rate. Then, I would explore replacing inefficient components, such as upgrading to a more efficient motor or impeller. Finally, I'd implement a monitoring system to track improvements and further optimize performance.
If you were running low on spare parts for a blower repair, how would you prioritize which repairs to conduct?
How to Answer
- 1
Identify critical repairs that impact safety or operation.
- 2
Assess the urgency of each repair based on customer needs.
- 3
Consider the cost-effectiveness of repairing certain units.
- 4
Evaluate which repairs can be completed with available parts.
- 5
Communicate transparently with customers about delays.
Example Answers
I would first prioritize repairs that are essential for safety or functionality, such as equipment that is crucial for emergency use. Then I'd look at customer urgency and schedule those repairs soonest.
If a client reported issues with the blower systems you've installed, how would you handle the communication and resolution process?
How to Answer
- 1
Acknowledge the client's concerns promptly and professionally
- 2
Gather all relevant details about the issue before responding
- 3
Communicate clearly about the steps you will take to address the problem
- 4
Provide a timeline for resolution and keep the client updated
- 5
Follow up after resolution to ensure the client is satisfied
Example Answers
I would first acknowledge the client's concern and thank them for bringing it to my attention. Then, I would ask detailed questions to understand the specific issues they're facing with the blower system. After gathering sufficient information, I would communicate the steps I plan to take to resolve the problem and provide them with an estimated timeline. Lastly, I would ensure to follow up after the issue has been resolved to confirm everything is working well.
If your team is struggling with too many projects at once, how would you help prioritize the workload?
How to Answer
- 1
Assess the urgency and importance of each project using a matrix.
- 2
Involve the team in discussing priorities to gain their input and buy-in.
- 3
Set clear deadlines for each project to manage expectations.
- 4
Identify any dependencies between projects to ensure smooth workflows.
- 5
Regularly review and adjust priorities as needed based on progress.
Example Answers
I would start by using an urgency-importance matrix to categorize projects. Then, I'd hold a team meeting to discuss and gather their insights when determining what to prioritize.
In the event of a power failure affecting blower operations, what steps would you take to safely bring the system back online?
How to Answer
- 1
Assess the situation and confirm the power failure.
- 2
Check for any safety hazards before approaching the blower system.
- 3
Reset any circuit breakers or emergency stop functions.
- 4
Confirm that all systems are clear and ready for restart.
- 5
Gradually restore power and monitor blower performance closely.
Example Answers
First, I would verify that a power failure has occurred and check for safety hazards around the blower. Then, I'd reset any tripped circuit breakers and ensure that all components are ready before restoring power. Finally, I would bring the system back online gradually and monitor its performance.
Don't Just Read Blower Questions - Practice Answering Them!
Reading helps, but actual practice is what gets you hired. Our AI feedback system helps you improve your Blower interview answers in real-time.
Personalized feedback
Unlimited practice
Used by hundreds of successful candidates
Blower Position Details
Related Positions
- Dry Roller
- Breaker
- Soap Boiler
- Button Puncher
- Battery Loader
- Battery Hand
- Flyer
- Throwster
- Spot Cleaner
- Flyer Builder
Similar positions you might be interested in.
Ace Your Next Interview!
Practice with AI feedback & get hired faster
Personalized feedback
Used by hundreds of successful candidates
Ace Your Next Interview!
Practice with AI feedback & get hired faster
Personalized feedback
Used by hundreds of successful candidates