Top 31 Cartridge Loader Interview Questions and Answers [Updated 2025]
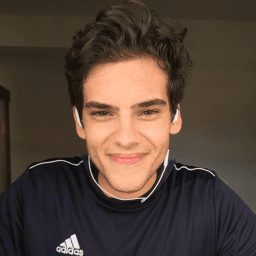
Andre Mendes
•
March 30, 2025
Preparing for a Cartridge Loader interview? This blog post is your ultimate guide to acing it! We've compiled the most common interview questions for the Cartridge Loader role, offering insightful example answers and practical tips to help you respond effectively. Whether you're a seasoned professional or a newcomer to the field, this resource is designed to boost your confidence and readiness for the big day. Dive in and start preparing!
Download Cartridge Loader Interview Questions in PDF
To make your preparation even more convenient, we've compiled all these top Cartridge Loaderinterview questions and answers into a handy PDF.
Click the button below to download the PDF and have easy access to these essential questions anytime, anywhere:
List of Cartridge Loader Interview Questions
Technical Interview Questions
What steps do you take to troubleshoot a malfunctioning cartridge loading machine?
How to Answer
- 1
Start by checking the power supply and ensuring the machine is properly plugged in.
- 2
Inspect all mechanical components for blockages or wear that could affect operation.
- 3
Review error codes or messages from the machine's control panel.
- 4
Test each part of the loading sequence step by step to identify where the failure occurs.
- 5
Consult the machine's manual for troubleshooting tips specific to the model.
Example Answers
First, I check the power supply and ensure the machine is functioning properly. Then, I look at the mechanical components for any blockages or signs of wear. Next, I review any error codes displayed and troubleshoot according to the control panel. Finally, I follow the loading sequence step by step to pinpoint where the issue arises.
What types of machines and equipment have you used in cartridge loading, and what are their key functions?
How to Answer
- 1
Identify specific machines used in cartridge loading, like presses or loaders
- 2
Explain the key functions of each machine briefly
- 3
Mention any experience with calibration or maintenance of these machines
- 4
Highlight the importance of safety and efficiency during operation
- 5
Relate your experience to the requirements of the position you're applying for
Example Answers
I have worked extensively with automatic cartridge loaders, which are essential for efficiently filling and sealing cartridges. I also used pneumatic presses that ensure precise assembly. Additionally, I have experience calibrating these machines to maintain quality control.
Don't Just Read Cartridge Loader Questions - Practice Answering Them!
Reading helps, but actual practice is what gets you hired. Our AI feedback system helps you improve your Cartridge Loader interview answers in real-time.
Personalized feedback
Unlimited practice
Used by hundreds of successful candidates
Can you explain the process of loading cartridges step by step?
How to Answer
- 1
Start with the components of a cartridge: casing, primer, powder, and bullet.
- 2
Describe the preparation: cleaning and inspecting the casing.
- 3
Explain the process of inserting the primer into the casing.
- 4
Detail the filling of the casing with powder and seating the bullet.
- 5
Conclude with a mention of safety checks and final inspections.
Example Answers
First, I gather all the components: the casing, primer, powder, and bullet. Next, I clean and inspect the casing to ensure it's ready. Then, I insert the primer into the casing securely. After that, I fill the casing with the appropriate amount of powder and carefully seat the bullet on top. Finally, I perform safety checks to ensure everything is in order before using the cartridges.
How do you ensure that the loaded cartridges meet quality standards?
How to Answer
- 1
Start with understanding the specifications for quality standards.
- 2
Detail the inspection process you follow for loaded cartridges.
- 3
Mention any tools or equipment you use during the quality checks.
- 4
Highlight the importance of following safety protocols.
- 5
Explain how you document your quality assurance processes.
Example Answers
I ensure quality by closely following the specified standards for each type of cartridge. I inspect every batch visually and use calipers for measurements, documenting any deviations for further action.
What safety protocols do you follow when operating loading machinery?
How to Answer
- 1
Always conduct a pre-operation inspection of the machinery to identify any hazards.
- 2
Wear appropriate personal protective equipment including gloves, goggles, and hearing protection.
- 3
Follow the manufacturer's guidelines for loading procedures and machine operation.
- 4
Maintain a clean and organized work area to prevent accidents.
- 5
Be aware of your surroundings and communicate with teammates to ensure everyone's safety.
Example Answers
I always start by inspecting the loading machinery for any potential hazards, and I ensure I wear my gloves and goggles as required. Following the manufacturer's instructions is crucial for safe operation.
What factors do you consider when selecting the cartridges for loading?
How to Answer
- 1
Consider the specific requirements of the firearm being used
- 2
Evaluate the intended use of the cartridges, such as target shooting or hunting
- 3
Check the compatibility of the cartridges with existing equipment
- 4
Assess the performance characteristics needed, like velocity and energy
- 5
Look into regulatory and safety standards that apply to ammunition selection
Example Answers
I focus on the firearm’s specifications, ensuring the cartridges I select match its chambering for safety and performance. Additionally, I consider the intended use, such as target practice or hunting, to choose appropriate bullet types and loadings.
How often do you perform maintenance on loading equipment, and what does that entail?
How to Answer
- 1
State your maintenance schedule clearly.
- 2
Mention specific tasks you perform during maintenance.
- 3
Emphasize adherence to safety protocols.
- 4
Provide examples of past experiences with equipment maintenance.
- 5
Connect your maintenance practices to efficiency and productivity.
Example Answers
I perform maintenance on loading equipment weekly. This includes checking for wear and tear, lubricating moving parts, and ensuring all safety features are operational. I always follow the manufacturer’s guidelines and have prevented several potential issues by staying on schedule.
What regulations and standards do you keep in mind while loading cartridges?
How to Answer
- 1
Familiarize yourself with ATF regulations related to firearm ammunition.
- 2
Understand industry standards like SAAMI for cartridge specifications.
- 3
Always prioritize safety protocols to prevent accidents.
- 4
Keep updated with local and federal laws regarding ammunition handling.
- 5
Document your processes for accountability and compliance.
Example Answers
I ensure to follow ATF regulations closely, adhere to SAAMI standards for cartridge specs, and prioritize safety in every step of loading.
How do you track and document loading results and discrepancies?
How to Answer
- 1
Use a structured log to record each loading session including date, time, and batch number
- 2
Document any discrepancies immediately with detailed observations
- 3
Utilize software tools or spreadsheets for real-time tracking and analysis
- 4
Regularly review documented results to identify patterns and improvements
- 5
Share your findings with the team for transparency and collective learning
Example Answers
I maintain a detailed log for each loading session that includes the date, batch number, and specific results. If I encounter a discrepancy, I note it down with all relevant details right away to facilitate further analysis.
What methods do you use to detect loading errors before they become larger issues?
How to Answer
- 1
Explain the importance of routine checks and preventive maintenance.
- 2
Mention the use of quality control measures like visual inspections.
- 3
Discuss any tools or technology you use for error detection.
- 4
Include examples of past experiences with error detection.
- 5
Emphasize your attention to detail and proactive approach.
Example Answers
I conduct routine checks of the loading machinery to ensure everything is working properly, and I implement visual inspections to catch any issues before they escalate. Additionally, I use diagnostic tools to monitor performance and detect irregularities.
Don't Just Read Cartridge Loader Questions - Practice Answering Them!
Reading helps, but actual practice is what gets you hired. Our AI feedback system helps you improve your Cartridge Loader interview answers in real-time.
Personalized feedback
Unlimited practice
Used by hundreds of successful candidates
Behavioral Interview Questions
Can you describe a time when you worked as part of a team to meet a deadline in cartridge loading?
How to Answer
- 1
Choose a specific project where you collaborated with others.
- 2
Highlight your role and contributions clearly.
- 3
Emphasize effective communication and teamwork.
- 4
Discuss the strategies used to meet the deadline.
- 5
Conclude with the outcome and what you learned.
Example Answers
During my time at ABC Company, we had a tight deadline to load cartridges for a major event. I coordinated with my team to ensure everyone was aware of their tasks. We held daily check-ins to monitor progress and addressed any issues promptly. As a result, we completed the loading two days ahead of schedule, which boosted team morale and taught me the importance of clear communication.
Tell me about a challenging loading process you encountered and how you resolved it.
How to Answer
- 1
Identify a specific loading process that had issues.
- 2
Explain the nature of the challenge clearly and briefly.
- 3
Describe the steps you took to resolve the issue.
- 4
Highlight any tools or techniques you utilized.
- 5
Conclude with what you learned from the experience.
Example Answers
In a recent project, we faced significant delays due to inconsistent cartridge weights during loading. I analyzed the weighing system and discovered it was miscalibrated. After recalibrating, I implemented a regular maintenance schedule, which improved accuracy and efficiency. This experience taught me the importance of regular equipment checks.
Don't Just Read Cartridge Loader Questions - Practice Answering Them!
Reading helps, but actual practice is what gets you hired. Our AI feedback system helps you improve your Cartridge Loader interview answers in real-time.
Personalized feedback
Unlimited practice
Used by hundreds of successful candidates
Give an example of a situation where your attention to detail prevented a mistake in the loading process.
How to Answer
- 1
Identify a specific instance in your experience.
- 2
Focus on the details you noticed that others might have missed.
- 3
Explain the actions you took to prevent the error.
- 4
Highlight the outcome of your attention to detail.
- 5
Connect the example to your role as a Cartridge Loader.
Example Answers
In my previous job at the ammunition factory, I noticed that one batch of cartridges had inconsistent powder levels. I double-checked the measurements and found that a calibration issue was affecting the loader. I adjusted the machine, which prevented misfires in the production run.
Describe a time when you had to adjust to changes in loading procedures or equipment.
How to Answer
- 1
Think of a specific instance where you faced a change.
- 2
Explain the nature of the change and why it was necessary.
- 3
Detail your immediate reaction and the steps you took to adapt.
- 4
Highlight any teamwork or communication involved in the adjustment.
- 5
Conclude with the positive outcome or what you learned from the experience.
Example Answers
In my previous role, the loading system was upgraded to a new automated process. I initially felt overwhelmed but quickly sought guidance from my supervisor. I then organized a training session with my team to ensure everyone understood the new procedures. We successfully adapted within a week, improving our loading efficiency by 15%.
How have you effectively communicated complex loading instructions to new team members?
How to Answer
- 1
Use clear and simple language when explaining procedures
- 2
Provide written handouts or guides for reference
- 3
Demonstrate the loading process step-by-step in person
- 4
Encourage questions and clarify any doubts immediately
- 5
Follow up with team members to ensure understanding and retention
Example Answers
In my previous job, I created a simple step-by-step guide that outlined the loading process. During training, I demonstrated each step and encouraged my team to ask questions, which helped clarify complex points.
Tell me about a time you managed your time effectively during a high-pressure loading task.
How to Answer
- 1
Use the STAR method: Situation, Task, Action, Result.
- 2
Focus on a specific instance that highlights time management.
- 3
Mention the tools or techniques you used to organize your work.
- 4
Emphasize the outcome and how it benefited the team or operation.
- 5
Keep it concise and relevant to loading tasks.
Example Answers
During a busy holiday season, I was tasked with loading a high volume of cartridges with a tight deadline. I prioritized the loading schedule by breaking it down into hourly goals. Using a timer, I stayed accountable to these checkpoints, which allowed me to complete the loading 10% ahead of schedule, ensuring all products were shipped on time.
Can you describe a time when you received constructive criticism about your loading process? How did you respond?
How to Answer
- 1
Choose a specific instance where you received constructive criticism.
- 2
Explain what the feedback was and who gave it.
- 3
Describe how you implemented changes based on the feedback.
- 4
Mention any positive outcomes that resulted from your adjustments.
- 5
Reflect on how this experience helped you grow as a loader.
Example Answers
In my previous role, my supervisor pointed out that my loading speed could be improved. I took this feedback seriously and worked on my technique by observing high performers and practicing their methods. As a result, my loading time improved by 20%, which helped increase overall productivity.
Have you ever taken the initiative to improve a cartridge loading process? What changes did you implement?
How to Answer
- 1
Think of a specific example where you identified a problem in the loading process.
- 2
Describe the steps you took to analyze and improve the process.
- 3
Mention any tools or techniques you used to make the changes.
- 4
Highlight the outcome of your actions, such as improved efficiency or safety.
- 5
Keep your answer concise and focused on the impact of your initiative.
Example Answers
In my previous role, I noticed that our cartridge loading was taking longer than necessary due to manual handling. I proposed implementing a conveyor system that would automate part of the loading. After the changes, we reduced loading time by 30% and increased overall production efficiency.
Don't Just Read Cartridge Loader Questions - Practice Answering Them!
Reading helps, but actual practice is what gets you hired. Our AI feedback system helps you improve your Cartridge Loader interview answers in real-time.
Personalized feedback
Unlimited practice
Used by hundreds of successful candidates
Describe a project where you demonstrated a strong work ethic in cartridge loading.
How to Answer
- 1
Choose a specific project that highlights your dedication to quality.
- 2
Focus on challenges you faced and how you overcame them through hard work.
- 3
Emphasize teamwork and your role in maintaining high standards.
- 4
Include metrics or results to demonstrate the impact of your efforts.
- 5
Conclude with a reflection on what you learned and how it shapes your work ethic.
Example Answers
In my last role, I was involved in a project to load cartridges for a high-volume production run. I noticed inconsistencies in the loading process, so I took the initiative to develop a quality checklist. My diligence led to a 20% reduction in errors during loading, and the project was completed ahead of schedule.
Situational Interview Questions
If you notice that a batch of cartridges has been improperly loaded, what immediate actions would you take?
How to Answer
- 1
Identify the scope of the issue by inspecting the batch thoroughly.
- 2
Isolate the affected batch to prevent further use until resolved.
- 3
Notify your supervisor immediately about the situation.
- 4
Document your findings and the steps taken for accountability.
- 5
Follow standard operating procedures to investigate and rectify the issue.
Example Answers
Firstly, I would inspect the batch to determine how many cartridges are affected. Then, I would isolate the batch to prevent further usage and inform my supervisor about the problem. I would document everything and follow our procedures to rectify the issue.
What would you do if a colleague ignored safety guidelines while loading cartridges?
How to Answer
- 1
Remain calm and approach the colleague privately.
- 2
Politely remind them of the safety guidelines that are in place.
- 3
Emphasize the importance of safety for everyone's well-being.
- 4
If they do not comply, report the situation to a supervisor.
- 5
Document the incident for follow-up if necessary.
Example Answers
I would first talk to my colleague privately and remind them about the safety guidelines. It's crucial we all follow safety to ensure everyone's well-being. If they continue to ignore it, I would escalate the matter to a supervisor.
Don't Just Read Cartridge Loader Questions - Practice Answering Them!
Reading helps, but actual practice is what gets you hired. Our AI feedback system helps you improve your Cartridge Loader interview answers in real-time.
Personalized feedback
Unlimited practice
Used by hundreds of successful candidates
How would you handle a situation where two team members are arguing about the loading process?
How to Answer
- 1
Stay calm and listen to both sides without interrupting.
- 2
Acknowledge their concerns and validate their feelings.
- 3
Encourage them to present their facts and viewpoints clearly.
- 4
Steer the conversation towards a collaborative solution.
- 5
If necessary, involve a supervisor for a final decision.
Example Answers
I would first listen to both team members to understand their points of view. Acknowledging their concerns, I would ask them to share their perspectives clearly. Then, I would encourage them to work together on finding a solution, possibly suggesting a compromise that incorporates elements from both sides.
If you are facing a tight deadline, how would you prioritize the loading tasks?
How to Answer
- 1
Identify the most critical tasks that must be completed first
- 2
Assess the impact of each task on the overall deadline
- 3
Communicate with team members to understand their capacity and current workload
- 4
Allocate resources effectively to tasks based on urgency
- 5
Stay adaptable and be ready to shift priorities as needed
Example Answers
I would first identify the tasks that are critical for meeting the deadline, focusing on those that directly affect production. I would then communicate with my team to ensure we are all aligned and address any potential bottlenecks. After that, I would prioritize tasks that can be completed quickly to ensure progress and adapt as needed based on our situation.
What would you do if the loading machine broke down in the middle of a critical load?
How to Answer
- 1
Stay calm and assess the situation immediately.
- 2
Check for any obvious issues or error messages on the machine.
- 3
Notify your supervisor and the maintenance team as soon as possible.
- 4
Implement any safety procedures required during a breakdown.
- 5
Plan for alternative loading options to minimize downtime.
Example Answers
If the loading machine breaks down, I would first remain calm and assess the issue to see if there are any quick fixes. If not, I would immediately notify my supervisor and the maintenance team to get assistance. Meanwhile, I would ensure safety protocols are followed and consider any alternative loading methods available.
How would you ensure a smooth transition between shifts in the loading operation?
How to Answer
- 1
Establish a handover checklist to cover key points for the incoming shift.
- 2
Communicate any ongoing issues or updates verbally before leaving.
- 3
Document all relevant information in a shift log for reference.
- 4
Ensure that equipment and workspace are clean and ready for the next team.
- 5
Encourage a brief meeting between outgoing and incoming staff to discuss important details.
Example Answers
I would create a handover checklist that covers all critical tasks and issues for the incoming team. This way, they have a clear overview and can easily pick up where we left off.
If you received unclear loading instructions, how would you go about clarifying them?
How to Answer
- 1
Review the instructions carefully to identify specific unclear areas.
- 2
Consult with a supervisor or team leader for clarification.
- 3
Ask the person who provided the instructions for further details.
- 4
Utilize available documentation or guidelines related to the loading process.
- 5
Take notes on the clarification to ensure understanding and avoid future confusion.
Example Answers
I would first reread the loading instructions to pinpoint where they are unclear. Then, I would ask my supervisor for clarification on those specific points to ensure I fully understand what is required.
How would you manage a situation where you are assigned more loading tasks than usual?
How to Answer
- 1
Prioritize tasks based on deadlines and importance
- 2
Communicate with your supervisor about workload concerns
- 3
Break tasks into smaller steps to manage them more easily
- 4
Use a checklist to keep track of completed tasks
- 5
Remain flexible and adaptable to changes in priorities
Example Answers
I would start by prioritizing the tasks based on their deadlines and importance. If I notice I'm overloaded, I would communicate this to my supervisor to seek assistance or adjust priorities. Then, I would break down the tasks into smaller steps and use a checklist to keep organized.
How would you handle multiple loading orders coming in at once?
How to Answer
- 1
Prioritize orders based on deadlines and importance
- 2
Communicate with the team to distribute the workload
- 3
Use a checklist to track each order's progress
- 4
Stay organized and maintain clear records of each loading
- 5
Remain calm and focused to ensure efficiency and accuracy
Example Answers
I would first assess the urgency of each order and prioritize them accordingly. Then, I would communicate with my team to delegate tasks effectively and ensure everyone is on the same page regarding responsibilities. Keeping a checklist would help track the progress of each order without missing any details.
What would you do if you received negative feedback from a customer regarding the cartridges loaded?
How to Answer
- 1
Listen carefully to the customer's feedback without interrupting.
- 2
Acknowledge their concerns and show empathy for their experience.
- 3
Ask clarifying questions to understand the issue fully.
- 4
Discuss possible solutions or corrective actions you can take.
- 5
Follow up with the customer to ensure their issues are resolved and they are satisfied.
Example Answers
I would listen to the customer carefully and acknowledge their feedback. I would then ask questions to fully understand their concerns and ensure that I know the specific issues with the cartridges. After assessing the situation, I would discuss potential solutions with them, such as providing a replacement or refund if necessary. Lastly, I would follow up to confirm the issue was resolved to their satisfaction.
Don't Just Read Cartridge Loader Questions - Practice Answering Them!
Reading helps, but actual practice is what gets you hired. Our AI feedback system helps you improve your Cartridge Loader interview answers in real-time.
Personalized feedback
Unlimited practice
Used by hundreds of successful candidates
Cartridge Loader Position Details
Related Positions
- Conveyor Loader
- Bolt Loader
- Bobbin Carrier
- Gun Stocker
- Carton Liner
- Charger
- Carbon Printer
- Card Maker
- Gas Charger
- Bottle Carrier
Similar positions you might be interested in.
Ace Your Next Interview!
Practice with AI feedback & get hired faster
Personalized feedback
Used by hundreds of successful candidates
Ace Your Next Interview!
Practice with AI feedback & get hired faster
Personalized feedback
Used by hundreds of successful candidates