Top 32 Bolt Loader Interview Questions and Answers [Updated 2025]
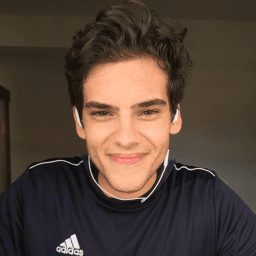
Andre Mendes
•
March 30, 2025
Preparing for a Bolt Loader interview can be daunting, but we've got you covered with the most common questions and expert-crafted example answers to help you succeed. This post is designed to equip you with insightful tips and strategies to answer effectively, boosting your confidence and readiness. Dive in to discover how to make a lasting impression and secure your dream role as a Bolt Loader.
Download Bolt Loader Interview Questions in PDF
To make your preparation even more convenient, we've compiled all these top Bolt Loaderinterview questions and answers into a handy PDF.
Click the button below to download the PDF and have easy access to these essential questions anytime, anywhere:
List of Bolt Loader Interview Questions
Behavioral Interview Questions
Can you describe a time when you worked in a team to load materials efficiently?
How to Answer
- 1
Choose a specific example from your past experiences
- 2
Highlight your role in the team
- 3
Emphasize teamwork and communication
- 4
Mention any techniques or tools used
- 5
Discuss the outcome and what you learned
Example Answers
In my previous job at a construction site, our team needed to load materials for a large project. I coordinated with my colleagues to assign specific tasks based on strengths, ensuring everyone knew what to do. We used a system to track what was loaded, which reduced confusion and increased speed. As a result, we completed the loading one hour early, which impressed our supervisor.
Tell me about a specific instance where you identified a safety hazard while loading bolts. What action did you take?
How to Answer
- 1
Choose a specific example from your experience.
- 2
Explain the hazard you identified clearly.
- 3
Describe the immediate actions you took to mitigate the risk.
- 4
Mention any follow-up actions you implemented.
- 5
Highlight the positive outcome of your actions.
Example Answers
Once, I noticed that the loading area for bolts had oil spilled on the floor, creating a slipping hazard. I immediately reported it to my supervisor and placed caution signs around the area. We cleaned up the spill and implemented a routine check for spills in the future, ensuring the safety of the team.
Don't Just Read Bolt Loader Questions - Practice Answering Them!
Reading helps, but actual practice is what gets you hired. Our AI feedback system helps you improve your Bolt Loader interview answers in real-time.
Personalized feedback
Unlimited practice
Used by hundreds of successful candidates
Describe a situation where you faced a difficult loading problem. How did you solve it?
How to Answer
- 1
Identify a specific loading challenge you've faced in the past.
- 2
Explain the steps you took to analyze the problem.
- 3
Describe the solution you implemented and why it was effective.
- 4
Mention any tools or equipment you used during the process.
- 5
Highlight the outcome and what you learned from the experience.
Example Answers
In my previous job, we had a shipment scheduled that was too heavy for our standard loader. I assessed the weight distribution and determined that we could use a different loader equipped with higher capacity. I coordinated with the equipment manager and we successfully loaded the shipment on time. This taught me the importance of knowing our equipment's limits.
Can you give an example of when you had to adapt quickly to a last-minute change in loading procedures?
How to Answer
- 1
Identify a specific situation you faced.
- 2
Explain the change that occurred and the reason for it.
- 3
Describe your thought process in responding to the change.
- 4
Highlight the steps you took to adapt quickly.
- 5
Conclude with the positive outcome that resulted from your adaptability.
Example Answers
In my previous job, we had a last-minute request to change loading sequences due to an equipment failure. I quickly assessed the new load order and communicated with the team to ensure everyone was aware of their tasks. I re-prioritized the loading schedule, and we successfully completed the load without delay.
Describe a time when you took the initiative to improve the loading process. What was the outcome?
How to Answer
- 1
Think of a specific situation where you noticed inefficiencies.
- 2
Explain what actions you took to address those inefficiencies.
- 3
Include measurable results or improvements from your actions.
- 4
Make sure to highlight your problem-solving and teamwork skills.
- 5
Keep your response structured: situation, action, result.
Example Answers
At my previous job, I noticed that the loading times during peak hours were significantly slower. I suggested a new loading sequence that prioritized certain products. By implementing this change, we reduced loading times by 20% and improved overall efficiency.
Have you ever been in charge of a loading team? What strategies did you use to lead effectively?
How to Answer
- 1
Highlight your leadership experience with clear examples.
- 2
Discuss specific strategies such as communication and delegation.
- 3
Mention how you motivated your team to meet goals.
- 4
Include any challenges faced and how you overcame them.
- 5
Emphasize the importance of safety and efficiency in your leadership.
Example Answers
Yes, I led a loading team during a peak season. I held daily briefings to communicate goals and expectations clearly. I delegated tasks based on each member’s strengths, which improved efficiency. One challenge was a last-minute shipment delay, but I reorganized our schedule and kept everyone informed to adapt quickly, ensuring we met our deadline.
Tell me about a time when you had to work under a lot of pressure during a loading operation. How did you cope?
How to Answer
- 1
Identify a specific incident and describe it briefly
- 2
Highlight the pressure factors involved
- 3
Explain the steps you took to manage the situation
- 4
Emphasize teamwork or communication if applicable
- 5
Conclude with the outcome and what you learned
Example Answers
During a busy shipping week, our team was under pressure to load 5 trucks in under 3 hours. I organized the team by assigning roles based on each person's strengths, which helped us be more efficient. We communicated constantly to ensure everyone was aware of their tasks and deadlines. In the end, we finished on time, which boosted everyone's morale.
Can you describe a time when you had to train someone on loading processes? What approach did you take?
How to Answer
- 1
Use a specific example from your experience.
- 2
Outline the training method you used, such as hands-on or demonstrations.
- 3
Mention any challenges faced during the training and how you overcame them.
- 4
Highlight the outcome of the training and the trainee's progress.
- 5
Keep your answer focused on your role in the training process.
Example Answers
In my previous job, I trained a new loader on the loading processes. I created a step-by-step guide and demonstrated the loading techniques first. The trainee struggled with the equipment initially, so I provided extra one-on-one sessions to address their specific difficulties. As a result, they became proficient and were able to independently handle loads within a week.
What do you consider your greatest achievement while working as a bolt loader?
How to Answer
- 1
Identify a specific achievement related to bolt loading.
- 2
Quantify the achievement with numbers or metrics if possible.
- 3
Explain the steps you took to achieve this success.
- 4
Highlight any teamwork or collaboration involved.
- 5
Connect the achievement to skills valuable for the position.
Example Answers
My greatest achievement as a bolt loader was increasing the loading efficiency by 20% over six months by implementing better organization strategies and collaborating with my team to streamline our workflow.
Don't Just Read Bolt Loader Questions - Practice Answering Them!
Reading helps, but actual practice is what gets you hired. Our AI feedback system helps you improve your Bolt Loader interview answers in real-time.
Personalized feedback
Unlimited practice
Used by hundreds of successful candidates
Technical Interview Questions
What types of equipment have you operated in the loading process, and what maintenance practices are essential?
How to Answer
- 1
List specific types of loading equipment you've used, such as forklifts or bolt loaders.
- 2
Mention your experience with each type and any relevant certifications.
- 3
Describe regular maintenance practices you performed, like daily inspections or lubricating parts.
- 4
Highlight the importance of safety checks and operational efficiency in maintenance.
- 5
Be prepared to give examples of how maintenance practices helped prevent issues in your experience.
Example Answers
I have operated bolt loaders and forklifts during my time at the warehouse. I always conducted daily checks on fluid levels and tire conditions to ensure safety.
How do you ensure that the correct quantity of bolts is loaded? What measurement techniques do you use?
How to Answer
- 1
Always double-check the order specifications for the bolt quantity.
- 2
Use a scale to weigh the bulk bolts before loading to verify the quantity.
- 3
Implement visual counting methods, like using bins marked for specific quantities.
- 4
Keep a log or checklist to track the number of bolts loaded during the process.
- 5
Confirm the total after loading by recounting or verifying weights against the expected total.
Example Answers
To ensure the correct quantity of bolts is loaded, I start by checking the order specifications. Then, I weigh the bulk bolts to verify they match the quantity needed. I also use marked bins for visual counting and keep a log during the process.
Don't Just Read Bolt Loader Questions - Practice Answering Them!
Reading helps, but actual practice is what gets you hired. Our AI feedback system helps you improve your Bolt Loader interview answers in real-time.
Personalized feedback
Unlimited practice
Used by hundreds of successful candidates
Explain the process you follow to perform an inventory check of bolts before loading.
How to Answer
- 1
Start by gathering all necessary tools and materials.
- 2
Check the inventory list for types and quantities of bolts needed.
- 3
Physically count each type of bolt and verify against the inventory list.
- 4
Inspect bolts for quality and any signs of damage.
- 5
Document any discrepancies and report them to the supervisor.
Example Answers
I begin by collecting the inventory list and ensuring I have tools like calipers. I check the list for types of bolts, then I count each type physically and confirm quantities. I also look for any damaged bolts, and I record any differences I find to inform my supervisor immediately.
What are the safety protocols you follow while operating loading equipment?
How to Answer
- 1
Always conduct a pre-operation inspection of the equipment
- 2
Wear personal protective equipment (PPE) such as hard hats and gloves
- 3
Follow the manufacturer's instructions and operational guidelines
- 4
Communicate clearly with team members using hand signals or radios
- 5
Maintain a safe distance from hazards and ensure the area is clear before operating.
Example Answers
I always conduct a pre-operation safety check to ensure everything is functioning correctly. I also make sure to wear my PPE and communicate with my team to ensure everyone's safety before starting operations.
What common loading issues have you encountered and how did you troubleshoot them?
How to Answer
- 1
Identify specific loading issues you've faced such as misalignment, excessive weight, or equipment malfunction.
- 2
Describe the steps you took to diagnose the problem and assess its impact on operations.
- 3
Highlight tools or techniques you used to resolve the issue, like load tests or safety checks.
- 4
Mention any communication with team members or supervisors during the troubleshooting process.
- 5
Conclude with what you learned and how you applied it to prevent future issues.
Example Answers
In my previous role, I encountered misalignment of the load on the forklift. I first stopped the operation to assess the load's position, then adjusted it using the lift’s controls to correct the alignment. This ensured safety and efficiency before continuing.
How do you ensure that the load is balanced correctly during the loading process?
How to Answer
- 1
Inspect the load before loading to identify weight distribution
- 2
Use markings or guidelines on the loading area to help position the load
- 3
Regularly check balance after adding each part to the load
- 4
Adjust the load as needed based on the balance observations
- 5
Communicate with team members to ensure everyone is aware of the loading process
Example Answers
I always begin by inspecting the load to identify how weight is distributed. I use guidelines on the loading area to position it correctly and make sure to check the balance after adding each item.
What loading techniques are you most proficient in, and how did you learn them?
How to Answer
- 1
Identify key techniques like stack loading, bulk loading, or container loading.
- 2
Explain your experience briefly, focusing on specific situations.
- 3
Mention any formal training or certifications if applicable.
- 4
Include safety practices that are important in loading.
- 5
Conclude with how these techniques have improved your efficiency or team productivity.
Example Answers
I am most proficient in stack loading and bulk loading. I learned these techniques during my time at XYZ Logistics, where I received hands-on training. Additionally, I completed a safety certification which emphasized proper loading methods, ensuring we maximize space while maintaining safety.
What operational rules do you always adhere to while working as a bolt loader?
How to Answer
- 1
Prioritize safety protocols to protect yourself and others.
- 2
Ensure you perform pre-operation checks on equipment.
- 3
Adhere to weight limits and load distribution guidelines.
- 4
Communicate clearly with your team during loading operations.
- 5
Maintain accurate records of loads and any incidents.
Example Answers
I always follow safety protocols, conduct pre-operation checks, and ensure that loads are within safe weight limits to prevent accidents.
What specific gear do you use for safety while loading heavy materials?
How to Answer
- 1
Mention essential personal protective equipment like hard hats and gloves
- 2
Include safety footwear and its importance in preventing injuries
- 3
Discuss the use of back support belts for lifting heavy loads
- 4
Talk about harnesses or fall protection when working at heights
- 5
Emphasize regular checks and maintenance of safety equipment
Example Answers
I always use a hard hat and safety gloves to protect my head and hands. Good safety footwear is essential to prevent slips or foot injuries while loading materials. I also utilize back support belts to help with heavy lifting.
Describe your familiarity with loading procedures and how they affect efficiency.
How to Answer
- 1
Explain specific loading procedures you have used.
- 2
Discuss how these procedures streamline the process.
- 3
Mention any tools or systems you are familiar with that aid in loading.
- 4
Provide examples of how proper loading maximizes productivity.
- 5
Highlight any challenges faced and how you overcame them.
Example Answers
In my previous role, I followed strict loading procedures such as checking weight limits and load stability before transport. These practices minimized delays and reduced accidents, enhancing overall efficiency.
Don't Just Read Bolt Loader Questions - Practice Answering Them!
Reading helps, but actual practice is what gets you hired. Our AI feedback system helps you improve your Bolt Loader interview answers in real-time.
Personalized feedback
Unlimited practice
Used by hundreds of successful candidates
Situational Interview Questions
If you noticed a co-worker not following safety protocols while loading, what would you do?
How to Answer
- 1
Prioritize safety and your own responsibility to ensure a safe workplace.
- 2
Approach the co-worker privately to discuss the observed behavior.
- 3
Refer to company policies on safety protocols for guidance.
- 4
If the behavior continues, report it to a supervisor for further action.
- 5
Maintain a professional and supportive attitude throughout the process.
Example Answers
I would first speak to my co-worker privately and respectfully point out the safety protocol they were overlooking. I would remind them of the importance of safety for everyone involved.
You have multiple loading tasks to complete, and your manager wants one done urgently. How do you prioritize?
How to Answer
- 1
Assess the urgency and importance of each task
- 2
Communicate with your manager to clarify priorities
- 3
Consider deadlines and potential impact on operations
- 4
Use a systematic approach like the Eisenhower Matrix if needed
- 5
Stay flexible and be ready to adjust as new information comes in
Example Answers
I would first assess which task is the most urgent and important. I'd communicate with my manager to confirm that I'm prioritizing the right loading task. Then, I would proceed with that task while keeping an eye on timelines for the others.
Don't Just Read Bolt Loader Questions - Practice Answering Them!
Reading helps, but actual practice is what gets you hired. Our AI feedback system helps you improve your Bolt Loader interview answers in real-time.
Personalized feedback
Unlimited practice
Used by hundreds of successful candidates
If a piece of loading equipment malfunctioned while you were using it, how would you respond?
How to Answer
- 1
Assess the situation calmly to ensure safety first.
- 2
Immediately stop using the equipment to prevent further damage or injury.
- 3
Notify your supervisor or the maintenance team about the malfunction.
- 4
Document the issue, including any error codes or unusual behaviors.
- 5
Follow safety protocols and procedures for handling equipment malfunctions.
Example Answers
If I encountered a malfunction, I would stop using the equipment right away to ensure safety. Then, I would notify my supervisor and provide details about the issue to facilitate a quick resolution.
Imagine you must decide between two loading methods that affect efficiency. How would you choose?
How to Answer
- 1
Identify the key performance metrics for both methods.
- 2
Consider the impact on overall workflow and team productivity.
- 3
Evaluate the cost-effectiveness of each method.
- 4
Engage with team members for their insight and expertise.
- 5
Test each method in a small-scale scenario before full implementation.
Example Answers
I would start by comparing the loading speed and accuracy of both methods. Then, I’d assess how each method fits into our current processes to minimize disruptions. Finally, I’d gather feedback from my team on their experiences with both methods before making a decision.
If a supervisor criticizes your loading technique, how would you take their feedback?
How to Answer
- 1
Stay calm and listen carefully to the supervisor's feedback
- 2
Ask clarifying questions if you don't understand their concerns
- 3
Acknowledge the criticism and express your willingness to improve
- 4
Reflect on the feedback and consider how to implement it in future tasks
- 5
Maintain a positive attitude and show appreciation for their guidance
Example Answers
I would listen closely to their feedback without getting defensive. I might ask questions to ensure I fully understand their concerns, and I would thank them for their input, promising to work on improving my technique.
If you run out of bolts during a loading operation, how would you handle the situation?
How to Answer
- 1
Stay calm and assess the situation quickly.
- 2
Communicate immediately with your supervisor or team.
- 3
Identify an alternative source for bolts on site or nearby.
- 4
Ensure safety and compliance with procedures while addressing the issue.
- 5
Document the incident for future reference and improve processes.
Example Answers
I would first stay calm and quickly inform my supervisor about the shortage. Then, I would check if there are any spare bolts available on site or if I can source them from a nearby location. Meanwhile, I would ensure that all operations are safe and that my team is informed.
If a customer complained about the quality of loaded bolts, what steps would you take to address the issue?
How to Answer
- 1
Acknowledge the customer's complaint and express understanding of their concerns
- 2
Ask specific questions to gather more details about the issue with the bolts
- 3
Investigate the loading process to identify any potential errors or quality concerns
- 4
Communicate findings and proposed solutions to the customer promptly
- 5
Implement changes to prevent recurrence and follow up with the customer to ensure satisfaction
Example Answers
I would first acknowledge the customer's complaint and show empathy. Then I would ask for specific details on what quality issues they observed with the loaded bolts to understand the problem better. After that, I would review our loading process to see if any errors occurred. I'd keep the customer informed about what I find and propose a solution while ensuring to implement preventive measures for the future. Finally, I would follow up with the customer to confirm they are satisfied with the resolution.
If you were given a tight schedule for loading bolts, how would you manage your time?
How to Answer
- 1
Prioritize tasks based on urgency and importance
- 2
Break down the loading process into smaller manageable steps
- 3
Use a timer to keep track of each step to stay on schedule
- 4
Communicate with the team to delegate tasks as needed
- 5
Prepare tools and materials in advance to minimize delays
Example Answers
I would start by prioritizing the tasks by identifying which bolts need to be loaded first based on urgency. Then, I would break down the loading process into smaller steps, setting a timer for each. I would also communicate with my team to delegate any tasks that can be handled simultaneously.
How would you handle a situation where team members disagreed on the loading method to use?
How to Answer
- 1
Encourage open communication among team members.
- 2
Facilitate a discussion to explore each method's pros and cons.
- 3
Suggest a trial of both methods if time and safety allow.
- 4
Make a decision based on team consensus or supervisor input.
- 5
Document the agreed method for future reference.
Example Answers
I would first bring the team together to discuss each loading method and encourage everyone to share their thoughts. Then, we could weigh the pros and cons as a group.
If new safety protocols were introduced, how would you adapt your loading practices?
How to Answer
- 1
Review the new safety protocols thoroughly to understand the changes.
- 2
Communicate with your team about the new protocols and ensure everyone is aware.
- 3
Implement training sessions to practice the new loading techniques safely.
- 4
Make adjustments to your loading processes to comply with the safety protocols.
- 5
Continuously monitor adherence to the protocols and provide feedback to the team.
Example Answers
I would start by reviewing the new safety protocols to get a clear understanding. Then, I would discuss them with my team to ensure we are all on the same page. Next, I would set up a training session to practice the new procedures and adapt our loading practices accordingly.
Don't Just Read Bolt Loader Questions - Practice Answering Them!
Reading helps, but actual practice is what gets you hired. Our AI feedback system helps you improve your Bolt Loader interview answers in real-time.
Personalized feedback
Unlimited practice
Used by hundreds of successful candidates
Working as a bolt loader can have tedious tasks. How would you maintain patience and focus?
How to Answer
- 1
Break tasks into smaller steps to make them more manageable.
- 2
Set short-term goals and celebrate their completion.
- 3
Use a timer to create work intervals, followed by short breaks.
- 4
Stay organized and keep your workstation tidy to reduce distractions.
- 5
Stay positive and remind yourself of the importance of the task.
Example Answers
I would break the loading tasks into smaller steps, setting goals for each. This way, I can focus on one task at a time and celebrate completing each step.
Bolt Loader Position Details
Related Positions
- Bolter
- Cartridge Loader
- Conveyor Loader
- Bundler
- Assembly Loader
- Bobbin Carrier
- Charger
- Basket Filler
- Battery Stacker
- Belt Maker
Similar positions you might be interested in.
Ace Your Next Interview!
Practice with AI feedback & get hired faster
Personalized feedback
Used by hundreds of successful candidates
Ace Your Next Interview!
Practice with AI feedback & get hired faster
Personalized feedback
Used by hundreds of successful candidates