Top 29 Conveyor Loader Interview Questions and Answers [Updated 2025]
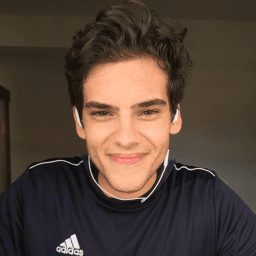
Andre Mendes
•
March 30, 2025
Preparing for a Conveyor Loader interview can be daunting, but our latest blog post is here to help you stand out. Dive into the most common questions asked in these interviews, complete with example answers and expert tips on how to respond effectively. Whether you're a seasoned professional or new to the field, this guide will equip you with the insights needed to impress any hiring manager.
Download Conveyor Loader Interview Questions in PDF
To make your preparation even more convenient, we've compiled all these top Conveyor Loaderinterview questions and answers into a handy PDF.
Click the button below to download the PDF and have easy access to these essential questions anytime, anywhere:
List of Conveyor Loader Interview Questions
Behavioral Interview Questions
Can you describe a time when you worked as part of a team to load a large shipment? What was your role?
How to Answer
- 1
Choose a specific instance where teamwork was essential
- 2
Highlight your specific responsibilities in the loading process
- 3
Mention challenges the team faced and how you contributed to overcoming them
- 4
Discuss the outcome of the shipment and team performance
- 5
Keep the example relevant to the Conveyor Loader position
Example Answers
In my previous job at a logistics company, we had a large shipment of machinery to load in one day. I was responsible for coordinating with my team to ensure all equipment was properly secured. We faced tight deadlines, but I organized a rotation system to keep everyone energized. The shipment was loaded successfully, and we received praise from management for our efficiency.
Tell me about a situation where you had to deal with a malfunctioning conveyor system while loading. How did you handle it?
How to Answer
- 1
Start with a specific incident where the conveyor malfunctioned.
- 2
Explain the nature of the malfunction clearly and concisely.
- 3
Describe the immediate steps you took to address the issue.
- 4
Highlight any collaboration with your team or maintenance staff.
- 5
Conclude with the outcome and what you learned from the experience.
Example Answers
In my last job, the conveyor belt suddenly stopped working during a peak loading time. I quickly checked the system and discovered a power issue. I communicated with my supervisor and we coordinated with the maintenance team to resolve it. We managed to get the system back online in about 20 minutes, which minimized delays.
Don't Just Read Conveyor Loader Questions - Practice Answering Them!
Reading helps, but actual practice is what gets you hired. Our AI feedback system helps you improve your Conveyor Loader interview answers in real-time.
Personalized feedback
Unlimited practice
Used by hundreds of successful candidates
Describe an experience where you identified a safety hazard while loading materials. What actions did you take?
How to Answer
- 1
Think of a specific incident where you noticed a safety issue.
- 2
Be clear about the hazard and why it was hazardous.
- 3
Describe the steps you took to address the hazard immediately.
- 4
Mention any communication with coworkers or management.
- 5
Highlight the outcome and any changes made to improve safety.
Example Answers
While loading materials, I noticed that a load was not secured properly, which posed a risk of it falling. I immediately stopped the loading process, secured the load correctly, and informed my supervisor about the hazard to prevent any accidents.
Give an example of how you've effectively communicated with your team during a busy loading shift.
How to Answer
- 1
Use clear, direct language to relay instructions.
- 2
Emphasize teamwork by encouraging input from others.
- 3
Highlight specific tools or methods used for communication, like radios or hand signals.
- 4
Mention how you adapted based on the flow of the shift or challenges faced.
- 5
Provide a specific outcome that improved efficiency or safety.
Example Answers
During a busy loading shift, I used two-way radios to quickly relay updates and coordinate with my teammates. I encouraged everyone to share their input on any bottlenecks, which helped us adjust our loading process on the fly, resulting in a smoother shift and meeting our targets.
Describe a time when you took the initiative to improve a loading process. What was the outcome?
How to Answer
- 1
Think of a specific incident where you noticed an inefficiency.
- 2
Explain what steps you took to address the issue.
- 3
Highlight any teamwork involved and how you communicated your ideas.
- 4
Discuss the outcome and any measurable improvements achieved.
- 5
Keep it clear and focused on your role in the initiative.
Example Answers
In my previous job, I noticed that the loading times were consistently slow. I suggested a new layout for the loading area and organized a team meeting to implement the changes. As a result, we reduced loading times by 20%.
How do you keep yourself motivated during repetitive loading tasks?
How to Answer
- 1
Set small goals for each loading session to create a sense of achievement.
- 2
Focus on maintaining high-quality standards for each load.
- 3
Use music or podcasts to make the work environment more enjoyable.
- 4
Take scheduled short breaks to recharge and maintain energy levels.
- 5
Visualize the end result of your work and how it contributes to the bigger picture.
Example Answers
I keep myself motivated by setting small goals during each loading session, like completing a certain number of loads in a specific timeframe. This gives me a sense of achievement and keeps me focused.
Can you tell me about a time when you had to learn a new skill quickly for your job? How did you approach it?
How to Answer
- 1
Choose a specific example that clearly illustrates the situation.
- 2
Describe the skill you needed to learn and why it was important.
- 3
Explain your learning process and the resources you used.
- 4
Share the outcome and how it impacted your work or the team.
- 5
Demonstrate your ability to adapt and be proactive.
Example Answers
At my previous job, I had to quickly learn how to operate a new conveyor loader system because the regular operator was out sick. I studied the manual, watched training videos provided by the company, and practiced under supervision. Within a day, I was able to operate the loader efficiently, and it helped us keep our production schedule on track.
Describe a time when you found a way to enhance efficiency in a loading operation.
How to Answer
- 1
Think of a specific situation where you made a process better.
- 2
Describe the problem you encountered and what actions you took.
- 3
Focus on the measurable outcomes of your improvements.
- 4
Use clear and direct language to explain your thought process.
- 5
Emphasize teamwork or how collaboration helped enhance efficiency.
Example Answers
In my previous job, we faced delays due to loading miscommunications. I implemented a checklist system for loaders to follow before operations. This reduced errors by 30% and speeded up our loading time significantly.
Have you ever been responsible for training new employees in loading procedures? What approach did you take?
How to Answer
- 1
Share specific experiences you have in training others
- 2
Explain your method clearly, such as hands-on demonstrations
- 3
Emphasize the importance of safety and efficiency in training
- 4
Mention how you assess understanding and provide feedback
- 5
Include any materials or resources you used during training
Example Answers
Yes, I have trained new employees on loading procedures. I used hands-on demonstrations to show the correct techniques, emphasizing safety protocols very clearly. After training, I would check their understanding by observing their loading practices and providing constructive feedback.
Don't Just Read Conveyor Loader Questions - Practice Answering Them!
Reading helps, but actual practice is what gets you hired. Our AI feedback system helps you improve your Conveyor Loader interview answers in real-time.
Personalized feedback
Unlimited practice
Used by hundreds of successful candidates
Technical Interview Questions
What types of conveyor systems are you familiar with and what maintenance do they require?
How to Answer
- 1
Identify the main types of conveyor systems you have used, such as belt, roller, and screw conveyors.
- 2
Explain specific maintenance tasks for each type, like cleaning, lubrication, and checking for wear.
- 3
Mention any experience with troubleshooting common issues in conveyor systems.
- 4
Be prepared to discuss how often maintenance should be performed for optimal operation.
- 5
Use technical terminology appropriately to demonstrate familiarity with the systems.
Example Answers
I have experience with belt conveyors, particularly in material handling. Regular maintenance involves checking the tension and alignment of the belt, lubricating the drive components, and inspecting for any wear or damage.
Explain the process you follow for loading items onto a conveyor system. What steps are critical to ensure efficiency?
How to Answer
- 1
Identify the items and check for any packaging issues
- 2
Ensure the conveyor system is operational and clear of obstructions
- 3
Load items in an organized manner to prevent jams
- 4
Maintain a steady pace to match the conveyor speed
- 5
Communicate with team members to coordinate the loading process
Example Answers
I start by inspecting the items to ensure they’re properly packaged. Then I check the conveyor for any obstructions and ensure it’s running smoothly. I load the items carefully in a way that keeps them organized, and I maintain a steady loading pace to avoid disruptions. Lastly, I keep in constant communication with my coworkers to ensure we are synced up during the loading process.
Don't Just Read Conveyor Loader Questions - Practice Answering Them!
Reading helps, but actual practice is what gets you hired. Our AI feedback system helps you improve your Conveyor Loader interview answers in real-time.
Personalized feedback
Unlimited practice
Used by hundreds of successful candidates
How do you determine the weight limits for items being loaded on a conveyor system?
How to Answer
- 1
Understand the manufacturer's specifications for the conveyor system
- 2
Consider the type of materials being loaded and their properties
- 3
Account for the load distribution across the conveyor
- 4
Check safety regulations and standards regarding weight limits
- 5
Regularly inspect the conveyor system for wear and tear that could affect weight capacity
Example Answers
I determine the weight limits by referring to the manufacturer's specifications and ensuring the load is evenly distributed across the conveyor to prevent strain.
What common issues might arise with conveyor loader operations, and how do you troubleshoot them?
How to Answer
- 1
Identify typical problems like belt misalignment, material jams, and power issues.
- 2
Explain your systematic approach to troubleshooting, starting from observation to diagnosis.
- 3
Mention the importance of regular maintenance checks to prevent issues.
- 4
Highlight the need for clear communication with team members during operations.
- 5
Provide examples of past experiences where you successfully resolved conveyor loader issues.
Example Answers
A common issue is belt misalignment. I would first observe the belt during operation to identify the misalignment, then adjust the tracking system to correct it. Regular maintenance helps prevent this.
What safety regulations must be followed when operating conveyor loaders?
How to Answer
- 1
Know and understand OSHA regulations relevant to conveyor operations
- 2
Wear appropriate personal protective equipment (PPE) like gloves and hard hats
- 3
Ensure all safety guards on conveyor loaders are in place and functioning
- 4
Conduct regular inspections and maintenance of the equipment
- 5
Be trained in emergency response procedures operating the machinery.
Example Answers
It is essential to follow OSHA regulations, use appropriate PPE, and ensure that all safety guards on the conveyor loader are properly functioning before operation.
How do you ensure even load distribution when loading items onto a conveyor?
How to Answer
- 1
Assess the weight and size of items before loading
- 2
Distribute heavier items evenly across the conveyor
- 3
Stack items in a stable manner to prevent shifting
- 4
Use guides or barriers to maintain alignment on the conveyor
- 5
Check the load visually and adjust as necessary during the process
Example Answers
I check the weights of items and place heavier ones in the middle for balance, ensuring lighter items are on the sides.
What techniques do you use to keep track of inventory levels while loading?
How to Answer
- 1
Utilize a standardized inventory checklist to verify items before loading.
- 2
Implement a barcode scanning system to quickly track quantities.
- 3
Regularly update inventory management software in real-time during loading.
- 4
Conduct periodic visual inspections of inventory levels as loading progresses.
- 5
Communicate with team members to confirm inventory counts and resolve discrepancies.
Example Answers
I use a standardized checklist to verify the items loaded against our inventory records, ensuring accuracy.
What considerations do you take into account when loading items on different types of conveyors?
How to Answer
- 1
Know the weight capacity of the conveyor to prevent overloads.
- 2
Use appropriate packing and securing methods for different item shapes.
- 3
Consider conveyor speed and its effect on item movement stability.
- 4
Be aware of conveyor type (roller, belt, etc.) and how it affects loading techniques.
- 5
Ensure proper alignment of items for efficient loading and minimal jams.
Example Answers
I always check the weight capacity of the conveyor first to avoid overloading it. Then, I secure items properly based on their shape and size to ensure they unload smoothly.
How does the role of a conveyor loader fit into the larger supply chain?
How to Answer
- 1
Explain how conveyor loaders enable efficient material handling.
- 2
Discuss the importance of accuracy in loading for inventory management.
- 3
Mention the role of conveyor loaders in reducing transit times.
- 4
Connect the efficiency of conveyor loaders to customer satisfaction.
- 5
Highlight how conveyor loaders support other supply chain functions.
Example Answers
The role of a conveyor loader is essential in the supply chain as it streamlines the transfer of goods, improving efficiency in material handling. By ensuring accurate loading, we maintain precise inventory levels, which helps in inventory management and order fulfillment, ultimately enhancing customer satisfaction.
What maintenance tasks do you perform on conveyor loaders to ensure they run smoothly?
How to Answer
- 1
Begin with routine cleaning of the conveyor surfaces to prevent build-up.
- 2
Check and replace worn or damaged belts regularly to avoid breakdowns.
- 3
Lubricate moving parts according to the manufacturer's recommendations.
- 4
Inspect electrical connections and sensors to ensure proper function.
- 5
Keep a maintenance log for tracking tasks and issues.
Example Answers
I regularly clean the conveyor surfaces to prevent any material build-up. I also check the belts for any wear and replace them as needed to keep everything running smoothly.
Don't Just Read Conveyor Loader Questions - Practice Answering Them!
Reading helps, but actual practice is what gets you hired. Our AI feedback system helps you improve your Conveyor Loader interview answers in real-time.
Personalized feedback
Unlimited practice
Used by hundreds of successful candidates
Situational Interview Questions
If you notice an employee not following safety protocols while loading, what would you do?
How to Answer
- 1
Observe the situation carefully before acting
- 2
Approach the employee calmly and respectfully
- 3
Address the specific safety issue they are overlooking
- 4
Remind them of the importance of safety protocols
- 5
Report the incident to a supervisor if it persists
Example Answers
I would first observe what the employee is doing and assess the situation. Then, I would calmly approach them and discuss the safety protocol they are not following, emphasizing its importance for their safety and that of others. If they continue to disregard safety, I would inform a supervisor to ensure the issue is addressed appropriately.
You have a tight deadline and the loading process is slower than expected. How do you improve the situation?
How to Answer
- 1
Assess the current loading process and identify bottlenecks.
- 2
Communicate with the team to increase coordination and efficiency.
- 3
Prioritize the most critical loads and streamline their handling.
- 4
Consider reallocating resources or manpower to speed up the process.
- 5
Monitor progress closely and adapt as needed.
Example Answers
I would first assess where the bottlenecks are in the loading process. After identifying the issues, I would communicate with the team to improve coordination and implement any needed changes immediately.
Don't Just Read Conveyor Loader Questions - Practice Answering Them!
Reading helps, but actual practice is what gets you hired. Our AI feedback system helps you improve your Conveyor Loader interview answers in real-time.
Personalized feedback
Unlimited practice
Used by hundreds of successful candidates
How would you address a conflict between two teammates during a loading operation?
How to Answer
- 1
Stay calm and listen to both sides without judgement.
- 2
Encourage open communication between the teammates.
- 3
Identify the root cause of the conflict specifically related to loading operations.
- 4
Suggest a fair resolution and how to prevent it in future operations.
- 5
Follow up with both teammates to ensure the issue is fully resolved.
Example Answers
I would first listen to both teammates to understand their perspectives. Then, I would facilitate a discussion where they can openly express their concerns. After identifying the main issue, I would work with them to find a solution that works for both, ensuring we all agree on a plan going forward.
Imagine the conveyor suddenly stops functioning during a critical loading task. What steps would you take?
How to Answer
- 1
Immediately stop all operations to prevent accidents.
- 2
Check for visible issues like jams or obstructions.
- 3
Notify your supervisor about the situation promptly.
- 4
Follow the emergency procedures for equipment failure.
- 5
Document the issue and corrective actions taken.
Example Answers
I would first stop all loading operations to ensure safety. Then I'd check the conveyor for any visible jams or issues. I'd inform my supervisor and follow the necessary emergency procedures, documenting everything for further review.
You are directed to change the loading procedures on short notice. How would you ensure the team adapts?
How to Answer
- 1
Communicate the changes clearly and promptly to the team
- 2
Provide a brief training or demonstration on the new procedures
- 3
Encourage team members to ask questions for clarification
- 4
Assign roles to ensure each member knows their responsibilities
- 5
Monitor the team's progress and offer support as needed
Example Answers
I would start by holding a quick team meeting to explain the new loading procedures, ensuring everyone understands the changes. Then, I'd provide a brief demonstration to show the correct method. I would encourage my team to ask questions and clarify any doubts. Assigning specific roles to team members would help streamline the process, and I'd monitor the situation closely to provide assistance if needed.
If a customer is waiting for their shipment to be processed and the loading is delayed, how would you handle the situation?
How to Answer
- 1
Acknowledge the delay and apologize sincerely.
- 2
Inform the customer about the reason for the delay briefly but clearly.
- 3
Provide an estimated time of resolution if possible.
- 4
Assure the customer that you are working to resolve the issue quickly.
- 5
Follow up with updates as the situation changes.
Example Answers
I would first apologize to the customer for the delay and explain that we're experiencing a hold-up due to equipment maintenance. I would then provide an estimated time for when loading is expected to resume and let them know I will keep them updated on any changes.
How would you prioritize loading tasks when faced with multiple shipments arriving at once?
How to Answer
- 1
Assess the urgency of each shipment based on delivery deadlines.
- 2
Consider the size and weight of shipments to optimize loading efficiency.
- 3
Coordinate with team members to ensure clear communication and support.
- 4
Check for any special handling requirements for certain shipments.
- 5
Use a systematic approach, like FIFO (First In, First Out), when applicable.
Example Answers
I would first identify which shipments have the tightest deadlines and prioritize those. Then, I would assess the sizes to arrange loading for maximum efficiency. Communication with my team would be key to avoid any overlap.
If you were asked to lead a team in a busy loading operation, how would you coordinate the efforts?
How to Answer
- 1
Assess the workload and set clear priorities for the team
- 2
Communicate effectively with team members about their roles
- 3
Monitor progress and adjust strategies as needed
- 4
Ensure safety protocols are followed during operations
- 5
Encourage teamwork and support to maintain morale
Example Answers
I would first evaluate the load requirements and prioritize tasks. Then, I'd assign roles based on each member's strengths and ensure everyone knows their responsibilities. I would regularly check in on progress and remain flexible to make changes if necessary, all while enforcing safety precautions.
How would you handle a situation where the loading software is not functioning properly?
How to Answer
- 1
Stay calm and assess the problem clearly
- 2
Check for common issues like internet connectivity or power supply
- 3
Contact technical support or IT department if necessary
- 4
Communicate with your team about the issue and any delays it may cause
- 5
Look for manual loading procedures to keep operations running
Example Answers
I would first remain calm and assess the issue. I would check if it's a connectivity problem or something else. If I can't resolve it, I would reach out to the IT team for assistance and inform my supervisor about the situation to manage expectations.
Conveyor Loader Position Details
Recommended Job Boards
ZipRecruiter
www.ziprecruiter.com/Jobs/ConveyorThese job boards are ranked by relevance for this position.
Related Positions
- Conveyor Worker
- Cartridge Loader
- Bolt Loader
- Production Line
- Belt Maker
- Pallet Assembler
- Extruder Operator
- Bag Machine Operator
- Factory Laborer
- Bobbin Carrier
Similar positions you might be interested in.
Ace Your Next Interview!
Practice with AI feedback & get hired faster
Personalized feedback
Used by hundreds of successful candidates
Ace Your Next Interview!
Practice with AI feedback & get hired faster
Personalized feedback
Used by hundreds of successful candidates