Top 32 Production Line Interview Questions and Answers [Updated 2025]
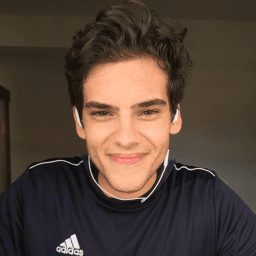
Andre Mendes
•
March 30, 2025
Navigating a job interview for a production line role can be daunting, but preparation is key to success. In this blog post, we delve into the most common interview questions you might encounter in this field. Alongside example answers, we offer practical tips to help you respond confidently and effectively, setting you up for a successful interview. Dive in and enhance your readiness for your next career opportunity!
Download Production Line Interview Questions in PDF
To make your preparation even more convenient, we've compiled all these top Production Lineinterview questions and answers into a handy PDF.
Click the button below to download the PDF and have easy access to these essential questions anytime, anywhere:
List of Production Line Interview Questions
Behavioral Interview Questions
Can you describe a time when you successfully worked as part of a production team?
How to Answer
- 1
Choose a specific project or task you worked on
- 2
Highlight your role and contributions
- 3
Focus on teamwork and communication aspects
- 4
Mention any challenges faced and how you overcame them
- 5
Conclude with the results and lessons learned
Example Answers
In my previous role at Manufacturing Co., I was part of a team assembling electronic devices. My responsibility was to ensure quality control. During a busy period, we faced a supply delay, and I suggested a redivision of tasks to keep production moving. We communicated regularly and increased output by 20% during that time.
Tell me about a challenging issue you faced on the production line and how you resolved it.
How to Answer
- 1
Describe the issue clearly and briefly
- 2
Explain the impact of the issue on production
- 3
Detail the steps you took to address the challenge
- 4
Emphasize teamwork or collaboration if applicable
- 5
Conclude with the positive outcome or lessons learned
Example Answers
In my previous job, we faced a frequent machine breakdown that delayed production. I coordinated with maintenance and we developed a preventive maintenance schedule, reducing breakdowns by 30%.
Don't Just Read Production Line Questions - Practice Answering Them!
Reading helps, but actual practice is what gets you hired. Our AI feedback system helps you improve your Production Line interview answers in real-time.
Personalized feedback
Unlimited practice
Used by hundreds of successful candidates
Have you ever had to lead a team during a busy production period? How did you handle it?
How to Answer
- 1
Describe a specific busy period you led your team.
- 2
Explain the strategies you used to manage the workload.
- 3
Highlight any communication or delegation techniques you employed.
- 4
Share a positive outcome that resulted from your leadership.
- 5
Emphasize teamwork and morale boosting during high pressure.
Example Answers
During a holiday peak season, I led my team as we faced a significant increase in orders. I organized a daily morning briefing to distribute tasks based on each member's strengths and kept open lines for feedback. By fostering a supportive environment, we increased output by 30% and met our deadlines.
Describe a situation where you had to adapt quickly to changes on the production line. What did you do?
How to Answer
- 1
Focus on a specific example from your experience
- 2
Describe the changes that occurred on the production line
- 3
Explain your immediate response and actions taken
- 4
Highlight any positive outcomes or lessons learned
- 5
Keep your answer concise and relevant to the role
Example Answers
During a busy shift, we suddenly lost a key machine. I quickly communicated with my team, reassigned tasks, and we adapted by using manual methods to keep production going. We minimized downtime and ensured our targets were met, reinforcing our ability to work under pressure.
Can you provide an example of how you effectively communicated with your team during a production issue?
How to Answer
- 1
Describe the production issue clearly.
- 2
Explain the steps you took to communicate with your team.
- 3
Mention any tools or methods used for communication.
- 4
Highlight the outcome of your communication.
- 5
Reflect on what you learned from the experience.
Example Answers
During a machinery breakdown, I quickly called an emergency team meeting and used our team chat app to keep everyone updated. We collaborated on a solution, and within an hour, we had a repair plan in place, which minimized downtime.
Describe a situation where you had to manage your time effectively on the production line.
How to Answer
- 1
Identify a specific production task you were involved in.
- 2
Explain the challenges that required time management.
- 3
Describe your strategies for prioritizing tasks.
- 4
Highlight the outcome and how it benefited the team or process.
- 5
Show how you learned from the experience to improve future time management.
Example Answers
In my previous job, we faced a high demand during the holiday season. I prioritized tasks by focusing on the most time-sensitive orders first, which improved our output by 20%. I used a checklist to track progress and ensured that all team members were aware of their responsibilities, which kept us on schedule.
Can you talk about a time you faced significant pressure at work and how you coped?
How to Answer
- 1
Choose a specific situation where you faced pressure.
- 2
Explain the context and what made it stressful.
- 3
Describe the actions you took to manage the pressure.
- 4
Highlight any positive outcomes or lessons learned.
- 5
Keep it focused on your personal experience.
Example Answers
In my previous job as a production assistant, we had a sudden surge in orders. The tight deadline put me under pressure. I organized a team meeting to prioritize tasks and delegated responsibilities effectively. We met the deadline and I learned the importance of teamwork under pressure.
Give an example of how you have accepted constructive criticism in your work.
How to Answer
- 1
Choose a specific instance where you received feedback.
- 2
Explain the context and the nature of the criticism.
- 3
Describe how you reacted to the feedback positively.
- 4
Share what actions you took to improve based on the feedback.
- 5
Highlight the positive outcomes from incorporating the suggestions.
Example Answers
In my previous job, my supervisor pointed out that my packaging processes were slower than my peers. I took this feedback seriously and asked for tips on efficiency. I then implemented new techniques, which helped my speed improve by 20%.
Describe a time when your attention to detail helped avoid a significant mistake.
How to Answer
- 1
Think of a specific situation in your previous job or study.
- 2
Explain the mistake that was avoided and why it was significant.
- 3
Describe the actions you took that demonstrated your attention to detail.
- 4
Highlight the positive outcome as a result of your actions.
- 5
Keep it concise and focused on your personal contribution.
Example Answers
In my previous job at the manufacturing plant, I noticed a discrepancy in the measurements of a batch of components. By double-checking the specs, I flagged the issue before production started, preventing a costly rework later on. This attention to detail saved the company time and resources.
What has motivated you in your past production roles, and how did you maintain that motivation?
How to Answer
- 1
Identify specific aspects of production work that energize you, like teamwork or problem-solving.
- 2
Share a personal anecdote that illustrates your motivation in action.
- 3
Mention strategies you used to stay motivated during challenging times.
- 4
Relate your motivation to achieving team goals or improving processes.
- 5
Finish with how this motivation translates to success in the role you're applying for.
Example Answers
I've always been motivated by the teamwork found on the production line. For example, during a tight deadline, I organized daily briefings to keep everyone informed and focused, which really lifted morale. When the team met our targets, it was a fantastic achievement, and I strive to bring that same energy to your team.
Don't Just Read Production Line Questions - Practice Answering Them!
Reading helps, but actual practice is what gets you hired. Our AI feedback system helps you improve your Production Line interview answers in real-time.
Personalized feedback
Unlimited practice
Used by hundreds of successful candidates
Have you experienced a conflict with a coworker on the production line? How was it resolved?
How to Answer
- 1
Explain the conflict clearly and simply.
- 2
Focus on your role in resolving it.
- 3
Highlight communication and teamwork.
- 4
Mention the positive outcome of the resolution.
- 5
Keep it professional, avoiding personal details.
Example Answers
I had a disagreement with a coworker about the best way to operate a machine. I suggested we take a break and discuss our views calmly. After talking, we both agreed on a compromise that worked well for both of us, and it improved our workflow.
Technical Interview Questions
What types of production line machinery are you familiar with, and what maintenance tasks have you performed?
How to Answer
- 1
List specific types of machinery you have worked with.
- 2
Mention the maintenance tasks you received training for or performed regularly.
- 3
Describe any troubleshooting experience you have with machinery.
- 4
Focus on your hands-on experience rather than theory.
- 5
Be prepared to discuss any relevant safety protocols you followed.
Example Answers
I have experience with conveyor belts and packaging machines. I performed regular cleaning and lubrication, and I also troubleshot minor issues like jams or misalignments.
Explain how you ensure product quality on the production line.
How to Answer
- 1
Use standardized procedures to gain consistency.
- 2
Perform regular quality checks at each stage of production.
- 3
Train team members on quality control practices.
- 4
Document and address any defects or issues immediately.
- 5
Communicate with the team to foster a culture of quality.
Example Answers
I ensure product quality by following strict procedures, conducting quality checks at every stage, and training my team to recognize and report defects.
Don't Just Read Production Line Questions - Practice Answering Them!
Reading helps, but actual practice is what gets you hired. Our AI feedback system helps you improve your Production Line interview answers in real-time.
Personalized feedback
Unlimited practice
Used by hundreds of successful candidates
What methods do you know for optimizing production line efficiency?
How to Answer
- 1
Identify bottlenecks in the current process
- 2
Consider lean manufacturing principles
- 3
Implement automation where feasible
- 4
Utilize data analytics for performance tracking
- 5
Train staff on best practices and efficient workflows
Example Answers
To optimize production line efficiency, I focus on identifying bottlenecks and applying lean principles to reduce waste. For example, I analyze the flow of materials and adjust the layout or process to eliminate delays.
What safety regulations must be followed on a production line?
How to Answer
- 1
Identify key safety regulations specific to the production industry.
- 2
Mention the importance of personal protective equipment (PPE).
- 3
Discuss the need for regular safety training for all employees.
- 4
Highlight compliance with OSHA or relevant safety standards.
- 5
Emphasize the role of reporting hazards and near-misses.
Example Answers
On a production line, we must follow OSHA regulations, ensure all employees wear proper PPE like gloves and goggles, and conduct regular safety training to keep everyone informed about hazards.
How do you utilize production data to improve processes?
How to Answer
- 1
Identify key performance indicators relevant to production efficiency.
- 2
Gather and analyze data from various stages of the production line.
- 3
Look for patterns or trends that indicate bottlenecks or inefficiencies.
- 4
Implement changes based on data insights and monitor their impact.
- 5
Continuously review data to adapt and optimize processes over time.
Example Answers
I track key metrics like cycle time and defect rates, analyze them weekly, and identify bottlenecks, leading to a 15% increase in efficiency after adjustments.
What steps do you follow for troubleshooting a malfunctioning machine?
How to Answer
- 1
Identify the symptoms of the malfunction clearly.
- 2
Check the machine's manual for troubleshooting guidelines.
- 3
Inspect for visible issues like loose wires or misalignments.
- 4
Run diagnostic tests if available to isolate the problem.
- 5
Document each step taken to track the troubleshooting process.
Example Answers
I first identify the symptoms, such as abnormal noises or performance issues. Then I refer to the machine's manual to find specific troubleshooting steps. Next, I visually inspect the machine for any obvious problems.
How do you track and manage inventory on the production line?
How to Answer
- 1
Use a clear inventory tracking system, like barcode scanning or software.
- 2
Regularly update inventory records to reflect real-time counts.
- 3
Implement a labeling system for easy identification of materials.
- 4
Monitor stock levels to predict shortages and adjust orders accordingly.
- 5
Communicate with team members about inventory needs daily.
Example Answers
I use a barcode scanning system to track inventory as it moves through the production line. This allows for real-time updates and minimizes mistakes.
Which key performance indicators do you think are essential for measuring production line success?
How to Answer
- 1
Identify specific KPIs relevant to production lines like efficiency, defect rates, and output rate.
- 2
Explain why these KPIs are important in the context of production quality and efficiency.
- 3
Be prepared to discuss how you would monitor and improve these KPIs.
- 4
Use examples from past experience if possible to demonstrate your knowledge.
- 5
Tailor your response to the company's specific production goals and industry.
Example Answers
I believe essential KPIs for production line success include overall equipment effectiveness, defect rates, and production output. These indicators help us understand efficiency and quality, which are crucial for meeting production targets.
What kinds of preventive maintenance practices do you followed to keep the production line running smoothly?
How to Answer
- 1
Identify specific preventive maintenance tasks you perform regularly
- 2
Mention any scheduling systems you use to track maintenance
- 3
Discuss the importance of keeping machinery clean and lubricated
- 4
Include how you monitor equipment performance for early signs of issues
- 5
Share examples of teamwork to address maintenance needs proactively
Example Answers
I follow a strict weekly maintenance schedule that includes cleaning and lubricating all moving parts. I also check for wear and tear on equipment to prevent breakdowns.
What experience do you have with automated production processes?
How to Answer
- 1
Briefly describe your hands-on experience with automation equipment.
- 2
Mention specific tools or technologies you have worked with.
- 3
Highlight any relevant training or certifications in automation.
- 4
Share measurable results or improvements achieved through automation.
- 5
Emphasize teamwork or collaboration on automation projects.
Example Answers
In my previous job, I operated a robotic assembly line where I programmed and maintained the automated systems. I also completed a certification in PLC programming, which helped optimize our production efficiency by 20%.
Don't Just Read Production Line Questions - Practice Answering Them!
Reading helps, but actual practice is what gets you hired. Our AI feedback system helps you improve your Production Line interview answers in real-time.
Personalized feedback
Unlimited practice
Used by hundreds of successful candidates
Situational Interview Questions
If there was a sudden delay in production due to equipment failure, how would you manage the situation?
How to Answer
- 1
Assess the situation and identify the cause of the equipment failure.
- 2
Communicate with the team and management about the delay and next steps.
- 3
Implement troubleshooting steps or coordinate with maintenance for repairs.
- 4
Prioritize tasks to minimize downtime and keep other areas of production moving.
- 5
Document the incident to inform future preventive measures.
Example Answers
First, I would assess the equipment to determine the cause of the failure. Then, I would communicate with my supervisor and the team about the delay. I would start immediate troubleshooting steps while coordinating with maintenance for repairs. Meanwhile, I would ensure that other production tasks can continue as much as possible to minimize overall downtime.
How would you handle a situation where demand exceeds the production capacity?
How to Answer
- 1
Assess the production processes to identify bottlenecks
- 2
Communicate with management and sales about capacity limits
- 3
Consider overtime or additional shifts to increase output
- 4
Implement a prioritization system for orders based on deadlines
- 5
Explore options for temporary staff or subcontracting to meet demand
Example Answers
I would first analyze our current processes to find any inefficiencies. Then, I would communicate with management and sales to ensure everyone is aware of our capacity constraints. If feasible, I would suggest increasing our workforce temporarily to keep up with demand.
Don't Just Read Production Line Questions - Practice Answering Them!
Reading helps, but actual practice is what gets you hired. Our AI feedback system helps you improve your Production Line interview answers in real-time.
Personalized feedback
Unlimited practice
Used by hundreds of successful candidates
If you discover a batch of products that do not meet quality standards, what steps would you take?
How to Answer
- 1
Immediately isolate the affected batch to prevent further processing.
- 2
Notify your supervisor about the quality issue without delay.
- 3
Document the specifics of the quality failure for investigation.
- 4
Assess the cause of the issue, if possible, to prevent recurrence.
- 5
Follow the company's established procedures for addressing quality issues.
Example Answers
First, I would isolate the batch to avoid further issues. Then, I would inform my supervisor about the quality concern. I would document the exact nature of the problem and any potential reasons I could identify. Finally, I would follow our established procedures to ensure the issue is addressed properly.
Imagine a team member is consistently underperforming on the line. How would you address this?
How to Answer
- 1
Observe the team member's performance discreetly to identify specific issues.
- 2
Have a private conversation to discuss their challenges and listen actively.
- 3
Offer support and resources such as training or mentorship.
- 4
Set clear expectations and goals for improvement.
- 5
Follow up regularly to monitor progress and provide feedback.
Example Answers
I would first observe the team member to understand their specific challenges. Then, I'd have a one-on-one conversation with them to talk about these issues, listen to their side, and offer any needed support. Together, we would set clear goals for improvement and I would check in regularly to ensure they are making progress.
What would you do if your supervisor asked you to implement a new production process that you're not familiar with?
How to Answer
- 1
Ask questions to clarify the new process
- 2
Research the process to gain understanding
- 3
Seek guidance from colleagues with experience
- 4
Develop a step-by-step plan for implementation
- 5
Communicate progress and ask for feedback regularly
Example Answers
I would first ask my supervisor for more details about the new process to understand the expectations. Then, I would research the process to familiarize myself with it. If needed, I would reach out to colleagues who have worked with it before for advice. I would create a clear plan for implementation and keep my supervisor updated on my progress.
You are under a tight schedule for a production run. How do you prioritize tasks?
How to Answer
- 1
Identify critical tasks that directly impact production output.
- 2
Assess resource availability to ensure you have what you need.
- 3
Use a priority matrix to categorize tasks by urgency and importance.
- 4
Communicate with your team to delegate effectively.
- 5
Monitor progress and be ready to adjust priorities as needed.
Example Answers
I would first identify the tasks that are critical to meeting our production deadline, such as machine setup and initial quality checks. Then, I would check if all necessary materials are available and delegate any non-critical tasks to my team so we can focus on the essentials.
In case of an emergency on the production line, what immediate actions would you take?
How to Answer
- 1
Assess the situation quickly to understand the nature of the emergency
- 2
Prioritize safety by alerting your team and stopping the line if needed
- 3
Follow established emergency protocols or procedures in place
- 4
Communicate clearly and calmly with your supervisor and team members
- 5
Ensure that any necessary support services, like first aid or emergency services, are contacted if required
Example Answers
First, I would assess the situation to determine what kind of emergency we're dealing with. Then, I would immediately alert my team and stop the production line to ensure everyone's safety. Next, I would follow the company's emergency protocols to address the issue effectively. If needed, I would communicate to my supervisor and call for any necessary assistance.
If you're tasked with training a new employee on the production line, how would you approach it?
How to Answer
- 1
Start with a safety briefing to ensure a safe work environment
- 2
Provide a hands-on demonstration of each task they will perform
- 3
Encourage questions during the training to clarify their understanding
- 4
Introduce them to the team to foster a supportive environment
- 5
Follow up with periodic check-ins to assess their progress
Example Answers
I would begin the training by conducting a safety briefing, then I would demonstrate each task on the production line. I would encourage the new employee to ask questions throughout the process to ensure they understand. Additionally, I would introduce them to the team so they feel welcomed and supported, and I would schedule check-ins after a few days to see how they are adjusting.
What would you do if there was a conflicting schedule affecting the production line workflow?
How to Answer
- 1
Identify the specific conflict and its impact on production.
- 2
Communicate with team members and supervisors to clarify the situation.
- 3
Prioritize tasks or adjust staffing to minimize disruption.
- 4
Consider alternative solutions like rescheduling or reallocating resources.
- 5
Document the resolution process for future reference.
Example Answers
I would first assess the nature of the scheduling conflict and evaluate its impact on the workflow. Then, I would discuss with team members and supervisors to see if we can adjust priorities. If necessary, I might recommend rescheduling certain tasks to keep production on track.
How would you ensure a smooth transition during a shift change on the production line?
How to Answer
- 1
Communicate with the incoming team about ongoing tasks
- 2
Ensure that all equipment is properly maintained and checked
- 3
Use a checklist to verify completion of key tasks before handover
- 4
Document any issues or updates in a shared log
- 5
Conduct a brief meeting to align on priorities and responsibilities
Example Answers
To ensure a smooth transition, I would communicate directly with the incoming team about the status of ongoing tasks. I would make sure all equipment is checked and ready for use, and I would use a checklist to verify that everything is completed before handing over. Finally, I’d document any important notes in a shared log so everyone is informed.
Don't Just Read Production Line Questions - Practice Answering Them!
Reading helps, but actual practice is what gets you hired. Our AI feedback system helps you improve your Production Line interview answers in real-time.
Personalized feedback
Unlimited practice
Used by hundreds of successful candidates
If the entire team is underperforming, what steps would you take to boost morale and productivity?
How to Answer
- 1
Identify specific issues causing underperformance through open discussions
- 2
Encourage teamwork by organizing team-building activities
- 3
Set clear, achievable goals to create a sense of direction
- 4
Recognize and celebrate small wins to build confidence
- 5
Provide support and resources for skill development and training
Example Answers
I would start by holding a team meeting to openly discuss what challenges we're facing. This would help us identify the root causes of underperformance. Then, I would initiate some team-building exercises to strengthen our collaboration and encourage a positive atmosphere.
Production Line Position Details
Recommended Job Boards
ManufacturingJobs.com
www.manufacturingjobs.com/jobs/production-line-workerCareerBuilder
www.careerbuilder.com/jobs/production-line-workerZipRecruiter
www.ziprecruiter.com/Jobs/Production-Line-WorkerThese job boards are ranked by relevance for this position.
Related Positions
- Factory Worker
- Factory Laborer
- Product Assembler
- Conveyor Worker
- Conveyor Loader
- Tube Maker
- Manufacturing Assistant
- Bag Machine Operator
- Turning Machine Operator
- Machine Hand
Similar positions you might be interested in.
Ace Your Next Interview!
Practice with AI feedback & get hired faster
Personalized feedback
Used by hundreds of successful candidates
Ace Your Next Interview!
Practice with AI feedback & get hired faster
Personalized feedback
Used by hundreds of successful candidates