Top 33 Conveyor Worker Interview Questions and Answers [Updated 2025]
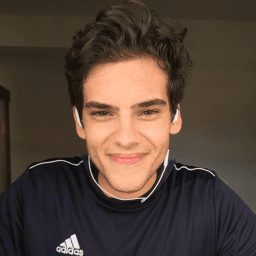
Andre Mendes
•
March 30, 2025
Navigating the interview process for a conveyor worker position can be daunting, but preparation is key to success. In this post, we've compiled the most common interview questions for this role, providing you with not only example answers but also practical tips on how to respond effectively. Dive in to enhance your interview skills and boost your confidence, setting you on the path to landing the job.
Download Conveyor Worker Interview Questions in PDF
To make your preparation even more convenient, we've compiled all these top Conveyor Workerinterview questions and answers into a handy PDF.
Click the button below to download the PDF and have easy access to these essential questions anytime, anywhere:
List of Conveyor Worker Interview Questions
Behavioral Interview Questions
Describe a time when you had to work closely with others on a conveyor system. What was your role and how did you contribute to the team?
How to Answer
- 1
Think of a specific project or shift where teamwork was essential.
- 2
Clearly define your role and responsibilities within the team.
- 3
Mention how you communicated and collaborated with others.
- 4
Include a specific outcome or result that shows success.
- 5
Reflect on what you learned from the experience.
Example Answers
During a busy shipping season, our team needed to ensure the conveyor system was running smoothly. I was tasked with monitoring the flow of packages and coordinating with my teammates on any blockages. I communicated any issues immediately and helped troubleshoot jams. As a result, we met our shipping deadlines and improved efficiency.
Don't Just Read Conveyor Worker Questions - Practice Answering Them!
Reading helps, but actual practice is what gets you hired. Our AI feedback system helps you improve your Conveyor Worker interview answers in real-time.
Personalized feedback
Unlimited practice
Used by hundreds of successful candidates
Tell me about a time when you identified a safety hazard in your work environment. What actions did you take?
How to Answer
- 1
Choose a specific incident to discuss.
- 2
Describe the hazard clearly and its potential impact.
- 3
Explain the steps you took to address the hazard.
- 4
Include any collaboration with coworkers or supervisors.
- 5
Mention the outcome and any preventive measures implemented.
Example Answers
In my previous job, I noticed a spill of oil near the conveyor belt that could lead to slips. I immediately marked the area with warning cones and notified my supervisor. We cleaned the spill promptly, and I suggested a regular check to prevent future spills.
Describe a situation where you had to adapt to a change in your workplace, particularly regarding conveyor operations.
How to Answer
- 1
Identify the specific change in conveyor operations you faced.
- 2
Explain your immediate reaction and how you assessed the situation.
- 3
Discuss any steps you took to learn about the new process or equipment.
- 4
Share the outcome of your adaptation and how it benefited the team.
- 5
Highlight any skills you used or developed during this transition.
Example Answers
In my last job, the conveyor speed was increased to improve efficiency. I quickly adjusted by closely monitoring the product flow and making necessary adjustments to my work pace. This helped minimize errors and maintain productivity during the transition.
Have you ever taken a lead role in resolving a conveyor malfunction? What steps did you take?
How to Answer
- 1
Describe the situation clearly and briefly.
- 2
Explain your role and why you took the lead.
- 3
Outline the specific steps you took to diagnose the issue.
- 4
Discuss how you communicated with your team during the process.
- 5
Share the outcome and any lessons learned.
Example Answers
In my previous job, our conveyor system stopped working during a shipment. I led a small team to investigate the issue. First, we checked the power supply and safety switches. I assigned tasks to my teammates and communicated updates to the supervisors. We identified a loose connection, fixed it, and got the conveyor running again in under an hour.
Give an example of how you effectively communicated with your team about a change in conveyor operation procedures.
How to Answer
- 1
Describe the specific change in procedure clearly.
- 2
Explain how you informed your team (e.g., meeting, email).
- 3
Mention the importance of the change and its impact.
- 4
Discuss how you ensured everyone understood the new procedures.
- 5
Share any feedback or follow-up you conducted after the communication.
Example Answers
In my previous job, we changed the conveyor speed settings for safety reasons. I held a team meeting to explain the new settings, emphasizing the importance of safety. I shared a handout with detailed instructions and made sure to answer questions to ensure clarity. After the change, I followed up to see if anyone was still confused.
Describe a time when you went above and beyond to ensure conveyor operations ran smoothly.
How to Answer
- 1
Think of a specific scenario where you took extra steps to solve a problem.
- 2
Use the STAR method: Situation, Task, Action, Result.
- 3
Highlight teamwork or communication if applicable.
- 4
Quantify your impact if possible, such as time saved or issues resolved.
- 5
End with what you learned or how it improved your work.
Example Answers
During a night shift, I noticed the conveyor was making unusual noises. I stayed late to inspect the belts and found a buildup of debris. I quickly cleared it out and lubricated the moving parts, which prevented a potential breakdown and ensured we met our morning production targets.
Tell me about a time when you faced a challenging situation while working with conveyors. How did you overcome it?
How to Answer
- 1
Identify a specific problem you encountered with the conveyor system.
- 2
Explain how you assessed the situation and what steps you took.
- 3
Describe the solution you implemented and its outcome.
- 4
Highlight any teamwork or collaboration that helped you succeed.
- 5
Conclude with what you learned from the experience.
Example Answers
In my previous role, the conveyor belt jammed frequently during peak hours. I quickly assessed that the issue was due to improper alignment. I gathered a small team, communicated the problem, and together we realigned the belt. This reduced downtime significantly and improved our efficiency.
What motivates you to perform well in your role as a conveyor worker?
How to Answer
- 1
Identify specific aspects of the job you enjoy
- 2
Mention the importance of teamwork and contributing to the company's goals
- 3
Discuss personal satisfaction from completing tasks efficiently
- 4
Highlight a commitment to safety and quality in work
- 5
Reference career growth and skill development opportunities.
Example Answers
I am motivated by the satisfaction of ensuring smooth operations on the conveyor line, and I take pride in working efficiently to meet targets. I also enjoy being part of a team that supports each other to achieve common goals.
Don't Just Read Conveyor Worker Questions - Practice Answering Them!
Reading helps, but actual practice is what gets you hired. Our AI feedback system helps you improve your Conveyor Worker interview answers in real-time.
Personalized feedback
Unlimited practice
Used by hundreds of successful candidates
Technical Interview Questions
What types of conveyor systems are you familiar with, and what are the key components involved in their operation?
How to Answer
- 1
Identify different types of conveyor systems like belt, roller, and chain conveyors.
- 2
Mention key components such as motors, pulleys, idlers, and control systems.
- 3
Explain how these components work together to facilitate the movement of materials.
- 4
Provide examples of industries or processes where you have seen these systems used.
- 5
Be clear and concise, showing your familiarity without overwhelming with jargon.
Example Answers
I am familiar with several types of conveyor systems including belt conveyors, roller conveyors, and chain conveyors. Key components include the motor for power, pulleys to guide the belt, and idlers to support it. For instance, I have worked with belt conveyors in food processing where hygiene is critical.
What routine maintenance tasks do you perform on conveyor systems to ensure their efficiency?
How to Answer
- 1
List specific tasks you perform regularly.
- 2
Mention any tools or diagnostic equipment you use.
- 3
Explain how you identify issues before they become major problems.
- 4
Emphasize the importance of keeping the conveyor clean.
- 5
Discuss any safety procedures you follow during maintenance.
Example Answers
I regularly inspect the conveyor belts for wear and tear and replace them as needed. I also check the alignment and tension of the belts to ensure smooth operation.
Don't Just Read Conveyor Worker Questions - Practice Answering Them!
Reading helps, but actual practice is what gets you hired. Our AI feedback system helps you improve your Conveyor Worker interview answers in real-time.
Personalized feedback
Unlimited practice
Used by hundreds of successful candidates
How do you troubleshoot issues with conveyor systems? Can you describe your process?
How to Answer
- 1
Start by observing the conveyor system to identify obvious signs of malfunction.
- 2
Check for common issues like blockages or power supply problems.
- 3
Use diagnostic tools to measure performance and pinpoint issues.
- 4
Consult the conveyor system manual for troubleshooting guidelines.
- 5
Document the issue and the steps taken to resolve it for future reference.
Example Answers
I begin by closely observing the conveyor to see if there are any visible issues like jams. Then I check the power connections and look for obstructions. If the problem isn't obvious, I use diagnostic tools to test the system's performance against its specifications.
What role do sensors play in conveyor systems, and how do you handle sensor malfunctions?
How to Answer
- 1
Explain how sensors detect and monitor the operation of the conveyor system.
- 2
Discuss the types of sensors commonly used, like proximity and photoelectric sensors.
- 3
Emphasize the importance of sensor accuracy for efficient operation.
- 4
Describe a step-by-step process you follow when a sensor malfunction occurs.
- 5
Mention preventative maintenance to reduce sensor issues.
Example Answers
Sensors are crucial in conveyor systems as they monitor the flow and detect jams. Common types are proximity and photoelectric sensors that ensure items are properly aligned. When a sensor malfunctions, I first check the connections, then perform diagnostics. I document the issue and recommend regular maintenance to prevent future problems.
How do you assess the load limits of a conveyor system and ensure they are not exceeded?
How to Answer
- 1
Familiarize yourself with the conveyor system's specifications and load limits provided by the manufacturer.
- 2
Regularly inspect the conveyor for wear and load-bearing components to ensure they are in good condition.
- 3
Use a scale or weight measurement device to check the actual load being placed on the conveyor.
- 4
Follow a system of checks to document and monitor loads used on the conveyor regularly.
- 5
Report and adjust practices if loads continuously approach or exceed safe limits.
Example Answers
I always check the manufacturer's specifications for load limits before operating the conveyor, and I keep a record of the loads I transport to ensure we stay within those limits.
Are you familiar with any conveyor control software? If so, how have you used it in your previous roles?
How to Answer
- 1
Identify specific conveyor control software you have used.
- 2
Be clear about your role in using the software and its impact.
- 3
Share an example that demonstrates your proficiency and problem-solving skills.
- 4
Mention any training or certifications related to the software.
- 5
Highlight the importance of the software in ensuring efficiency and safety.
Example Answers
I have used FlexiLink conveyor control software in my previous job. I was responsible for troubleshooting issues, which helped reduce downtime by 20%.
What skills do you possess that help you perform repairs on conveyor systems?
How to Answer
- 1
Highlight your mechanical skills and understanding of conveyor parts.
- 2
Mention experience with troubleshooting and diagnosing issues.
- 3
Discuss your familiarity with tools used in repairs and maintenance.
- 4
Emphasize your ability to follow safety protocols during repairs.
- 5
Share any relevant certifications or training that enhance your skills.
Example Answers
I have strong mechanical skills and understand the key components of conveyor systems. I am experienced in troubleshooting issues, which helps me quickly identify problems. I also know how to use the necessary tools for repairs and always follow safety protocols to ensure a safe working environment.
What safety standards do you follow when operating or maintaining conveyor systems?
How to Answer
- 1
Emphasize personal protective equipment like gloves and helmets.
- 2
Mention regular inspections and maintenance procedures.
- 3
Discuss specific safety protocols for loading and unloading materials.
- 4
Include awareness of emergency stop mechanisms.
- 5
Highlight the importance of following manufacturer guidelines.
Example Answers
I always wear proper PPE, including gloves and a hard hat. I conduct daily inspections to ensure everything is functioning properly and check emergency stops before starting the conveyor.
Can you explain the function of different conveyor components, such as rollers and belts?
How to Answer
- 1
Start with a brief overview of what conveyors do.
- 2
Explain the role of the belt in moving materials.
- 3
Describe the function of rollers in supporting and guiding the belt.
- 4
Mention other components like pulleys and motors if relevant.
- 5
Keep your explanation concise and focused on the components.
Example Answers
Conveyors are used to transport materials efficiently. The belt moves products along the conveyor line, while rollers support the belt and help it rotate smoothly. This combination ensures materials are conveyed quickly and effectively.
What measures have you taken in the past to improve the efficiency of conveyor operations?
How to Answer
- 1
Identify specific improvements you initiated or suggested in previous roles
- 2
Mention any tools or technologies you used to analyze performance
- 3
Highlight collaboration with team members to implement changes
- 4
Use quantifiable outcomes to show the impact of your efforts
- 5
Briefly explain the monitoring process you established to maintain efficiency
Example Answers
In my previous position, I analyzed the conveyor speed and noticed bottlenecks during peak hours. I suggested increasing the speed during those times, which improved throughput by 15%.
Don't Just Read Conveyor Worker Questions - Practice Answering Them!
Reading helps, but actual practice is what gets you hired. Our AI feedback system helps you improve your Conveyor Worker interview answers in real-time.
Personalized feedback
Unlimited practice
Used by hundreds of successful candidates
What is your experience with installing new conveyor systems? Can you describe the process?
How to Answer
- 1
Begin with your relevant experience in installing conveyor systems
- 2
Describe specific tasks you performed during the installation process
- 3
Mention any tools or equipment you used
- 4
Highlight your problem-solving skills during installations
- 5
Conclude with a successful outcome or a key lesson learned
Example Answers
I have three years of experience installing conveyor systems in a manufacturing environment. I started by reviewing the installation plans, then I assembled the conveyor sections using appropriate tools like wrenches and levels. During one installation, we faced a spacing issue, but I adjusted the layout to ensure smooth operation. The system was up and running ahead of schedule, which pleased the management.
Situational Interview Questions
If a conveyor system suddenly stops due to a fault, what immediate steps would you take to assess and address the situation?
How to Answer
- 1
Ensure safety by stopping any related machinery.
- 2
Check for visible signs of issues like jams or obstructions.
- 3
Refer to operator manuals or troubleshooting guides.
- 4
Communicate the situation to supervisors or team members.
- 5
Document the incident and any actions taken for future reference.
Example Answers
First, I would stop any related machinery to ensure no one is at risk. Then, I would inspect the conveyor for any visible jams or issues that could be the cause. I would consult the operator manual for troubleshooting steps and notify my supervisor about the situation.
Imagine you're working with a team, and the conveyor speed is too fast for workers to process items. How would you address this issue with your supervisor?
How to Answer
- 1
Observe the workflow and note specific problems caused by the speed
- 2
Speak with your team to gather their feedback and experiences
- 3
Request a private meeting with your supervisor to discuss the issue
- 4
Present the collected information clearly and professionally
- 5
Suggest possible solutions, such as adjusting the speed or adding breaks
Example Answers
I would first observe how the fast speed affects the workflow and note any specific issues. Then, I'd talk to my team to understand their challenges. I would request a meeting with my supervisor, present our feedback, and suggest we slow down the conveyor speed to allow for smooth operations.
Don't Just Read Conveyor Worker Questions - Practice Answering Them!
Reading helps, but actual practice is what gets you hired. Our AI feedback system helps you improve your Conveyor Worker interview answers in real-time.
Personalized feedback
Unlimited practice
Used by hundreds of successful candidates
If you notice a colleague improperly handling packages on the conveyor, how would you approach them?
How to Answer
- 1
Stay calm and approach the colleague privately.
- 2
Use 'I' statements to express concern without blaming.
- 3
Suggest safer handling techniques rather than criticizing.
- 4
Offer to help them if they are unsure about the proper method.
- 5
If necessary, inform a supervisor if the issue persists.
Example Answers
I would approach my colleague privately and say, 'I noticed that the way you handled that package may lead to damage. Can I show you a better technique?'
You have two conveyor lines running simultaneously, and one starts to jam while the other is operating normally. How do you prioritize your actions?
How to Answer
- 1
Assess which conveyor line has the more immediate impact on workflow.
- 2
Quickly check for safety hazards before taking action.
- 3
Prioritize clearing the jammed line while monitoring the operational line.
- 4
Communicate with team members about the status and receive assistance if needed.
- 5
Document the incident for future analysis and prevent recurrence.
Example Answers
I would first determine which conveyor line affects our output more significantly. Next, I would ensure there are no safety hazards and then focus on clearing the jam. I would keep an eye on the other line to ensure it continues running smoothly while getting assistance if necessary.
If you are notified of a recurring technical problem with a specific conveyor, what steps would you take to address it long-term?
How to Answer
- 1
Investigate the root cause of the problem by reviewing maintenance logs.
- 2
Consult with team members and supervisors to gather input and observations.
- 3
Establish a plan for resolving the issue, including necessary repairs or part replacements.
- 4
Implement the solution and monitor the conveyor performance closely for improvements.
- 5
Document the changes made and develop preventive maintenance protocols.
Example Answers
First, I would review the maintenance logs to identify any patterns in the recurring issue. Then, I would talk to my team to gather insights. After identifying the root cause, I'd create a plan to repair it and put a monitoring system in place to ensure the problem doesn’t return. Finally, I would document the solution and propose preventive maintenance steps.
Imagine you disagree with a team member about how to resolve a conveyor issue, how would you handle this disagreement?
How to Answer
- 1
Listen actively to the team member's perspective
- 2
Ask questions to understand their reasoning
- 3
Share your viewpoint clearly and calmly
- 4
Suggest finding a compromise or a middle ground
- 5
Involve a supervisor if the disagreement persists
Example Answers
I would first listen to my teammate's ideas to understand their perspective. Then, I'd explain my view calmly and suggest we brainstorm together to find the best solution.
If your supervisor asked you to train a new conveyor worker but you also have your regular tasks, how would you manage your time?
How to Answer
- 1
Prioritize tasks based on deadlines and importance
- 2
Allocate specific time slots for training the new worker
- 3
Communicate with your supervisor about workload
- 4
Break down training into manageable segments
- 5
Use downtime from regular tasks to assist with training
Example Answers
I would first assess my current tasks and prioritize them. Then, I would schedule specific times during the day to train the new worker, ensuring it doesn't interfere with critical deadlines. I'd also communicate with my supervisor if I feel overwhelmed and ask for support if needed.
If you were faced with a conveyor breakdown during peak hours, what immediate actions would you take?
How to Answer
- 1
Quickly assess the situation to identify the nature of the breakdown
- 2
Notify the supervisor or team leader about the issue
- 3
Switch to a contingency plan, such as rerouting materials or using backup equipment
- 4
Check for any safety hazards before proceeding with repairs
- 5
Document the incident for future reference and analysis
Example Answers
First, I would assess the conveyor to determine the cause of the breakdown. Then, I’d inform my supervisor to keep them in the loop. Next, I would implement our contingency plan, perhaps rerouting products to another conveyor. After ensuring safety protocols are followed, I would start the troubleshooting process while keeping the area clear for maintenance. Finally, I’d document the breakdown for our records.
How would you approach teaching a new employee the proper safety protocols when working with conveyors?
How to Answer
- 1
Start with explaining the importance of safety protocols
- 2
Use hands-on demonstrations with the conveyor system
- 3
Provide a written safety manual or checklist for reference
- 4
Encourage questions to ensure understanding
- 5
Conduct a practical assessment to verify competency
Example Answers
I would first explain why safety is critical when working with conveyors, then give a live demonstration of the safety protocols in action. After that, I'd provide them with a safety manual to refer back to and encourage them to ask questions until they feel comfortable. Finally, I would have them demonstrate their understanding of the protocols in a practical setting.
If you notice a design flaw in the conveyor setup that could lead to inefficiency, what steps would you take to address it?
How to Answer
- 1
Identify the specific design flaw and its impact on efficiency.
- 2
Communicate the issue to your supervisor and relevant team members.
- 3
Suggest possible solutions or improvements based on best practices.
- 4
Document the flaw and your proposed solutions for future reference.
- 5
Follow up to ensure that the suggestions are considered and acted upon.
Example Answers
I would first analyze the flaw and assess how it affects workflow. Then, I would report it to my supervisor, ensuring they understand the urgency. I could suggest ways to redesign the setup or adjust processes to mitigate the issue. Lastly, I would keep track of the follow-up to see if changes were implemented.
Don't Just Read Conveyor Worker Questions - Practice Answering Them!
Reading helps, but actual practice is what gets you hired. Our AI feedback system helps you improve your Conveyor Worker interview answers in real-time.
Personalized feedback
Unlimited practice
Used by hundreds of successful candidates
You have multiple conveyor lines to monitor and one of them starts malfunctioning. How do you prioritize your tasks?
How to Answer
- 1
Assess the urgency of the malfunction and its impact on production.
- 2
Communicate the issue to your team and relevant supervisors promptly.
- 3
Determine if the malfunction can be addressed quickly or if it requires more time.
- 4
Prioritize attending to the malfunctioning line before monitoring others.
- 5
Keep a log of any issues for future reference and continuous improvement.
Example Answers
I would first evaluate how serious the malfunction is and its effect on overall production. Then I would inform my supervisors about the situation. If it's a quick fix, I would prioritize that over the other lines. If it requires more time, I’d ensure the other lines continue to run smoothly while focusing on fixing the issue.
Conveyor Worker Position Details
Related Positions
- Conveyor Loader
- Track Worker
- Factory Worker
- Door Worker
- Piece Worker
- Work Distributor
- Factory Laborer
- Wireworker
- Tool Worker
- Shop Worker
Similar positions you might be interested in.
Ace Your Next Interview!
Practice with AI feedback & get hired faster
Personalized feedback
Used by hundreds of successful candidates
Ace Your Next Interview!
Practice with AI feedback & get hired faster
Personalized feedback
Used by hundreds of successful candidates