Top 32 Product Assembler Interview Questions and Answers [Updated 2025]
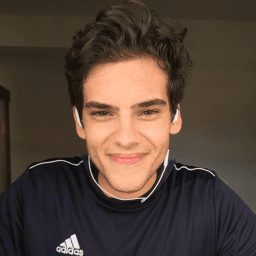
Andre Mendes
•
March 30, 2025
Navigating the interview process for a Product Assembler role can be daunting, but preparation is key to success. In this post, we delve into the most common interview questions candidates might encounter, offering insightful example answers and effective strategies to tackle them. Whether you're a seasoned professional or entering the field, these tips will help you confidently showcase your skills and land the job.
Download Product Assembler Interview Questions in PDF
To make your preparation even more convenient, we've compiled all these top Product Assemblerinterview questions and answers into a handy PDF.
Click the button below to download the PDF and have easy access to these essential questions anytime, anywhere:
List of Product Assembler Interview Questions
Behavioral Interview Questions
Describe a time when you worked as part of a team to complete an assembly project. What was your role?
How to Answer
- 1
Identify a specific project where teamwork was crucial
- 2
Mention your specific role and responsibilities
- 3
Highlight your contributions and the outcome
- 4
Emphasize communication and collaboration
- 5
Make sure to reflect on what you learned from the experience
Example Answers
I worked on assembling a batch of electronic devices with a team of four. My role was to ensure that all components were correctly placed and tested after assembly. I communicated closely with my teammates to identify problems and resolve them quickly, which helped us meet our delivery deadline.
Don't Just Read Product Assembler Questions - Practice Answering Them!
Reading helps, but actual practice is what gets you hired. Our AI feedback system helps you improve your Product Assembler interview answers in real-time.
Personalized feedback
Unlimited practice
Used by hundreds of successful candidates
Tell me about a time when you made a mistake during assembly. What steps did you take to correct it?
How to Answer
- 1
Identify a specific mistake you've made in the assembly process.
- 2
Explain the impact of the mistake on the product and the team.
- 3
Describe the steps you took to correct the mistake and any tools or processes used.
- 4
Highlight what you learned from the experience and any changes you made to avoid future errors.
- 5
Keep the focus on positive outcomes and your problem-solving skills.
Example Answers
In my previous job, I accidentally used the wrong size screws while assembling a unit, which caused instability. I noticed the issue during final checks and immediately disassembled the parts. I replaced the screws with the correct size and tested the assembly for stability. This experience taught me to double-check parts before starting assembly, and I've since developed a checklist to help with that.
Give an example of a time when you had to adapt to a change in assembly instructions or processes. How did you handle it?
How to Answer
- 1
Think of a specific example from your past work experience
- 2
Describe the change in instructions or processes clearly
- 3
Explain your initial reaction and how you sought clarification
- 4
Discuss the steps you took to adapt to the new instructions
- 5
Highlight the outcome and what you learned from the experience
Example Answers
In my last job, the assembly line changed the configuration of parts mid-production. I first reviewed the new instructions and asked a supervisor for clarification on the changes. I then made a checklist of the new steps and adjusted my workflow. As a result, I kept my productivity high and avoided mistakes.
Describe a situation where you had to communicate important assembly details to your team. How did you ensure everyone understood?
How to Answer
- 1
Identify a specific situation that required clear communication.
- 2
Mention the method you used to share the information (e.g., meeting, email).
- 3
Explain how you checked for understanding, such as asking questions or providing visuals.
- 4
Describe the outcome and any feedback from your team.
- 5
Keep the focus on your role in facilitating the communication.
Example Answers
In a recent project, I noticed some assembly instructions were confusing for my team. I called a quick team meeting where I presented the details using a visual aid, and I encouraged questions afterwards. By doing so, I ensured everyone understood their tasks, which led to a successful assembly completion ahead of schedule.
Can you discuss an occasion when you had to meet a tight deadline in your assembly work? What strategies did you use?
How to Answer
- 1
Identify a specific instance from your experience
- 2
Focus on the deadline and challenges faced
- 3
Explain the steps you took to meet the deadline
- 4
Highlight teamwork and communication if applicable
- 5
Conclude with the outcome and any lessons learned
Example Answers
In my previous role, we had a shipment due within 48 hours after a machine breakdown. I prioritized the assembly tasks by focusing on the most critical components first and coordinated with my team to work overtime. This team effort allowed us to complete the assembly ahead of time, and we met the deadline successfully.
What is your experience with quality control in assembly? Can you provide an example of how you ensured product quality?
How to Answer
- 1
Describe any relevant quality control processes you followed
- 2
Mention specific tools or techniques you used for quality checks
- 3
Share a situation where you identified a quality issue and resolved it
- 4
Quantify improvements or results when possible
- 5
Show your commitment to maintaining high standards in your work
Example Answers
In my previous role as a product assembler, I followed a strict checklist to ensure each part met quality standards. For instance, I used calipers to measure components before assembly, which helped reduce errors by 30%.
Can you give an example of a time when you learned a new assembly technique? How did you apply it?
How to Answer
- 1
Think of a specific instance where you had to learn a technique on the job.
- 2
Describe the situation clearly and briefly.
- 3
Explain how you learned the new technique, mention any resources or training.
- 4
Discuss how you applied the technique in your work.
- 5
Conclude with the impact of your application on your team or productivity.
Example Answers
At my previous job, we introduced a new automated assembly machine. I attended a training session provided by the equipment vendor to learn how to operate it. I practiced using the machine under supervision and then started using it independently. This allowed us to increase our production speed by 20% without sacrificing quality.
Describe a time when you took the lead on an assembly project. What challenges did you face?
How to Answer
- 1
Think of a specific assembly project you led.
- 2
Focus on your leadership role and actions taken.
- 3
Identify at least one challenge you encountered.
- 4
Explain how you overcame that challenge.
- 5
Conclude with the outcome of the project.
Example Answers
In my previous role, I led a project to assemble a new product line. The challenge was coordinating a team with different skill levels. I organized training sessions to upskill everyone, which improved teamwork and efficiency. We completed the assembly ahead of schedule and met quality standards.
What motivates you to deliver quality work in product assembly?
How to Answer
- 1
Focus on personal pride in craftsmanship and precision.
- 2
Mention the importance of teamwork and collaboration.
- 3
Discuss the impact of quality work on customer satisfaction.
- 4
Highlight your goal to minimize errors and waste.
- 5
Express your commitment to continuous improvement and learning.
Example Answers
I take personal pride in my craftsmanship, ensuring that every product I assemble meets high standards. Knowing that my work contributes to customer satisfaction motivates me to deliver quality consistently.
Don't Just Read Product Assembler Questions - Practice Answering Them!
Reading helps, but actual practice is what gets you hired. Our AI feedback system helps you improve your Product Assembler interview answers in real-time.
Personalized feedback
Unlimited practice
Used by hundreds of successful candidates
Can you discuss a time when your work ethic positively impacted your team’s performance?
How to Answer
- 1
Choose a specific example that showcases your work ethic.
- 2
Focus on how your actions helped the team achieve a goal.
- 3
Highlight any challenges you faced and how you overcame them.
- 4
Explain the outcome and the positive impact on your team.
- 5
Keep the answer structured: situation, action, result.
Example Answers
In my previous job as a Product Assembler, we were on a tight deadline for a major project. I took the initiative to stay late to finish my tasks and encouraged my teammates to join me. By collaborating closely, we met our deadline, and our team received commendations for our hard work.
Describe a time when you took the initiative on a project related to assembly.
How to Answer
- 1
Identify a specific project where you improved or led the assembly process.
- 2
Focus on your role and actions taken to enhance efficiency or quality.
- 3
Highlight the positive outcome that resulted from your initiative.
- 4
Use quantifiable results if possible, such as time saved or errors reduced.
- 5
Keep your answer structured: situation, action, result.
Example Answers
In my previous role at XYZ Manufacturing, I noticed that assembly line delays were caused by a lack of organized tools. I took the initiative to design and implement a tool organization system. As a result, we reduced assembly time by 15%, and team productivity increased significantly.
Technical Interview Questions
What tools and equipment do you commonly use in product assembly? How proficient are you with them?
How to Answer
- 1
List specific tools and equipment you are familiar with
- 2
Mention your level of proficiency with each tool
- 3
Include any relevant experience or context
- 4
Highlight your ability to learn new tools quickly
- 5
Be honest about your skills while showing willingness to improve
Example Answers
I commonly use power drills, screwdrivers, and measuring tools in product assembly. I am proficient with power drills and have over two years of experience using them effectively. I also have used screwdrivers extensively in my previous job and can adapt to new tools quickly.
Explain how you read and interpret assembly blueprints or technical drawings.
How to Answer
- 1
Familiarize yourself with common blueprint symbols and notations
- 2
Describe your step-by-step approach to analyzing the drawing
- 3
Highlight your attention to detail in measurements and instructions
- 4
Mention any tools or resources you use to aid interpretation
- 5
Share an example of a past experience where you successfully interpreted a blueprint
Example Answers
I start by identifying key symbols and dimensions on the blueprint. I carefully cross-reference these with assembly instructions to ensure accuracy. For instance, in my last job, I followed a technical drawing to assemble a component that required precise measurements, which I double-checked throughout the assembly process.
Don't Just Read Product Assembler Questions - Practice Answering Them!
Reading helps, but actual practice is what gets you hired. Our AI feedback system helps you improve your Product Assembler interview answers in real-time.
Personalized feedback
Unlimited practice
Used by hundreds of successful candidates
What safety protocols do you follow while assembling products? Can you give an example?
How to Answer
- 1
Identify specific safety protocols relevant to assembly, such as wearing protective gear.
- 2
Mention equipment checks to ensure tools are safe to use.
- 3
Discuss keeping workstations organized to prevent hazards.
- 4
Give a concrete example of a situation where you followed safety protocols.
- 5
Emphasize the importance of following company safety guidelines.
Example Answers
I always wear safety goggles and gloves while assembling products. For example, when working with sharp components, I make sure to check that my gloves are intact, and I maintain a clear workspace to avoid accidents.
Can you describe common assembly methods you've used, such as manual vs. automated assembly?
How to Answer
- 1
Mention specific assembly methods you've worked with.
- 2
Explain the advantages and disadvantages of each method briefly.
- 3
Provide examples of products you assembled using both methods.
- 4
Discuss your personal preference and why it matters for efficiency.
- 5
Highlight any relevant experience with tools or machinery.
Example Answers
I have experience with both manual and automated assembly. For manual assembly, I assembled small electronic devices, which allowed for greater precision with hand tools. Automated assembly was used for mass production of components, which increased speed, although it required regular maintenance. I prefer manual assembly for complex items requiring detail.
How do you troubleshoot an assembly that doesn't meet specifications? What steps do you take?
How to Answer
- 1
Identify the specific issue with the assembly
- 2
Consult the specifications and assembly guidelines
- 3
Examine components and tools used for any faults
- 4
Test the assembly process to locate the error
- 5
Document your findings and adjustments made
Example Answers
First, I identify the issue by checking which specifications are not met. Then, I refer to the assembly guidelines and review each step I took. I inspect the components to see if there are any defects or if any tools malfunctioned. I repeat the assembly process to isolate where things went wrong and ensure everything is working correctly. Finally, I document the issue and how I resolved it for future reference.
What types of materials have you worked with in product assembly, and how do they affect the assembly process?
How to Answer
- 1
Identify specific materials you have hands-on experience with.
- 2
Explain how each material influences the tools or methods you use.
- 3
Discuss any challenges you've faced with different materials.
- 4
Mention how certain materials require specific safety precautions.
- 5
Use examples that demonstrate your problem-solving skills.
Example Answers
I have worked with plastics, metals, and wood in product assembly. For example, plastics require heat sealing, which needs careful temperature control to avoid melting, while metals often require drilling and fastening, which can affect assembly speed.
What experience do you have with repairing or maintaining assembly equipment?
How to Answer
- 1
Highlight specific tools or equipment you are familiar with
- 2
Mention any formal training or certifications
- 3
Discuss any hands-on experience you’ve had
- 4
Provide examples of problems you've solved
- 5
Show your understanding of maintenance best practices
Example Answers
I have worked with pneumatic and electric assembly tools in my previous role and have repaired equipment by replacing faulty parts and performing routine maintenance checks.
How do you continuously improve your assembly efficiency? Can you share an example?
How to Answer
- 1
Identify specific bottlenecks in your assembly process
- 2
Implement small changes and measure their impact
- 3
Seek feedback from team members to find improvement areas
- 4
Use tools and techniques like 5S or Kaizen for organization and efficiency
- 5
Document changes and results to build best practices
Example Answers
In my last role, I noticed that my team spent a lot of time searching for tools. I set up a tool organization system based on 5S principles, which streamlined our workflow and saved us about 15 minutes per shift.
What experience do you have working on an assembly line, and what were your key contributions?
How to Answer
- 1
Describe specific roles you have held on the assembly line.
- 2
Highlight any improvements you made to the process.
- 3
Mention teamwork and collaboration experiences.
- 4
Include any tools or equipment you are familiar with.
- 5
Be ready to discuss metrics or outcomes from your contributions.
Example Answers
I worked on an automotive assembly line for two years where I was responsible for assembling engine components. I implemented a new organization system for parts that reduced assembly time by 15%. Collaborating closely with my team helped us maintain a high output rate.
What assembly processes have you implemented to make workflows more efficient?
How to Answer
- 1
Identify specific processes you have improved.
- 2
Use metrics or examples to show efficiency gains.
- 3
Mention collaboration with team members for improvements.
- 4
Emphasize continuous improvement and feedback loops.
- 5
Highlight how changes benefited production speed or quality.
Example Answers
In my previous role, I streamlined the soldering process by organizing tools and materials closer to the workstations, resulting in a 15% reduction in assembly time.
Don't Just Read Product Assembler Questions - Practice Answering Them!
Reading helps, but actual practice is what gets you hired. Our AI feedback system helps you improve your Product Assembler interview answers in real-time.
Personalized feedback
Unlimited practice
Used by hundreds of successful candidates
Situational Interview Questions
If you discovered that a crucial part is missing while you were assembling a product, what would you do?
How to Answer
- 1
Assess the impact of the missing part on the assembly process.
- 2
Check the assembly instructions for possible alternatives or workarounds.
- 3
Notify your supervisor or team leader immediately about the missing part.
- 4
Look for the part in the inventory or warehouse.
- 5
Document the issue for future reference and to prevent it from happening again.
Example Answers
I would first assess how critical the missing part is and if it affects the assembly process significantly. Then, I'd check the inventory to see if we have any replacements available. If not, I would promptly inform my supervisor and document the incident for future improvements.
Imagine you are working on a team project and a teammate is not contributing effectively. How would you handle this situation?
How to Answer
- 1
Address the issue directly with the teammate in a private conversation
- 2
Express your concern and seek to understand their perspective
- 3
Suggest ways they can contribute more effectively
- 4
Involve a team leader only if the problem persists
- 5
Focus on solutions and maintaining team cohesion
Example Answers
I would start by having a private conversation with my teammate to express my concerns about their lack of contribution. I would ask if there’s anything preventing them from participating and offer my support to help them get back on track.
Don't Just Read Product Assembler Questions - Practice Answering Them!
Reading helps, but actual practice is what gets you hired. Our AI feedback system helps you improve your Product Assembler interview answers in real-time.
Personalized feedback
Unlimited practice
Used by hundreds of successful candidates
If you had multiple assembly tasks to complete in a short time frame, how would you prioritize your work?
How to Answer
- 1
Assess the urgency of each task based on deadlines or production schedules
- 2
Evaluate the complexity and time required for each task
- 3
Identify tasks that can be completed quickly for immediate progress
- 4
Consider the impact of each task on the overall assembly process
- 5
Communicate with team members if prioritized tasks affect others
Example Answers
I would first look at the deadlines for each task to ensure that the most urgent ones are done first. Then, I would choose tasks that I can complete quickly to build momentum.
If you noticed a batch of products you assembled had quality issues, what steps would you take to address it?
How to Answer
- 1
Identify the specific quality issues observed
- 2
Document the problems clearly with examples
- 3
Notify your supervisor about the issues immediately
- 4
Stop the assembly line if necessary to prevent further errors
- 5
Suggest corrective actions or improvements based on your observations
Example Answers
I would first examine the specific quality issues to understand what went wrong. Next, I would document these issues and inform my supervisor right away. If the problems are serious enough, I would stop the assembly line to prevent more defective products from being assembled. Finally, I would propose any potential solutions I could think of based on my experience to avoid these issues in the future.
You receive new assembly instructions that you find confusing. What do you do to clarify them?
How to Answer
- 1
Read through the instructions carefully and highlight key areas of confusion
- 2
Consult with a colleague who may have experience with similar instructions
- 3
Use visual aids or diagrams available to help understand the process better
- 4
Reach out to your supervisor for clarification on specific points
- 5
Take notes on the clarification process to reference in the future
Example Answers
First, I would read through the instructions and note down the parts I find confusing. Then, I would ask a colleague for their input, as they might have faced similar issues before. If needed, I would also speak to my supervisor to get a better understanding.
How would you handle a disagreement with a colleague about the best way to assemble a product?
How to Answer
- 1
Stay calm and listen to the colleague's perspective carefully
- 2
Clarify your own viewpoint with specific reasons and evidence
- 3
Suggest reaching a compromise or a testing phase to evaluate both methods
- 4
Focus on the common goal: assembling the product correctly and efficiently
- 5
Keep the discussion professional and constructive, avoiding personal conflicts
Example Answers
I would first listen to my colleague's reasoning to understand their perspective. Then, I would explain my approach and the benefits it has based on past experience. If we still disagree, I might suggest we try both methods on a small scale to see which one yields better results.
If your supervisor provided critical feedback on your assembly work, how would you respond?
How to Answer
- 1
Listen carefully to the feedback without interrupting.
- 2
Acknowledge the feedback and express appreciation for it.
- 3
Ask clarifying questions if necessary to understand better.
- 4
Share what steps you will take to improve based on the feedback.
- 5
Follow up with your supervisor after implementing changes to show progress.
Example Answers
I appreciate the feedback and will make sure to address the concerns. I'll review the specific areas pointed out and practice those techniques to ensure my work meets the standards.
What would you do if a machine malfunctioned in the middle of your assembly work?
How to Answer
- 1
Stay calm and assess the situation quickly
- 2
Refer to the machine's manual or troubleshooting guide if available
- 3
Notify your supervisor or maintenance team immediately
- 4
If safe, isolate the machine to prevent further issues
- 5
Document the malfunction for future reference and follow up after resolution.
Example Answers
I would first ensure my safety and the safety of those around me, then I would check the machine for visible issues. If I couldn't resolve it quickly, I'd notify my supervisor right away.
Imagine you're assembling products while under significant pressure to meet a deadline. How would you manage?
How to Answer
- 1
Prioritize tasks based on urgency and importance
- 2
Stay organized with your workspace and materials
- 3
Maintain clear communication with your team or supervisor
- 4
Take short breaks when needed to stay focused
- 5
Check your work frequently to avoid mistakes
Example Answers
I would start by prioritizing tasks that are critical for meeting the deadline. I'd keep my workspace organized to ensure I have everything at hand. Communication with my supervisor would be key to adjust priorities if needed.
If you were assembling products that had to meet specific customer requirements, how would you ensure those were met?
How to Answer
- 1
Review detailed product specifications and customer requirements thoroughly
- 2
Create a checklist based on the requirements to follow during assembly
- 3
Conduct quality checks after completing each assembly to confirm adherence to standards
- 4
Communicate with team members to share insights about any discrepancies or issues
- 5
Gather feedback from customers post-assembly for continuous improvement
Example Answers
I would start by carefully reviewing the product specifications to understand the customer requirements. Then I would create a checklist to follow during the assembly process to ensure nothing is overlooked. After assembling, I would perform quality checks to confirm everything meets the standards before final inspection.
Don't Just Read Product Assembler Questions - Practice Answering Them!
Reading helps, but actual practice is what gets you hired. Our AI feedback system helps you improve your Product Assembler interview answers in real-time.
Personalized feedback
Unlimited practice
Used by hundreds of successful candidates
Product Assembler Position Details
Salary Information
Recommended Job Boards
ZipRecruiter
www.ziprecruiter.com/Jobs/Product-AssemblerThese job boards are ranked by relevance for this position.
Related Positions
- Pallet Assembler
- Hardware Assembler
- Puzzle Assembler
- Assembly Operator
- Cabinet Assembler
- Part Maker
- Lock Assembler
- Production Line
- Assembly Loader
- Manufacturing Assistant
Similar positions you might be interested in.
Ace Your Next Interview!
Practice with AI feedback & get hired faster
Personalized feedback
Used by hundreds of successful candidates
Ace Your Next Interview!
Practice with AI feedback & get hired faster
Personalized feedback
Used by hundreds of successful candidates