Top 30 Continuous Improvement Specialist Interview Questions and Answers [Updated 2025]
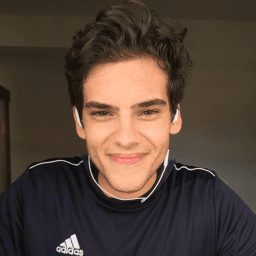
Andre Mendes
•
March 30, 2025
Embarking on a career as a Continuous Improvement Specialist requires a deep understanding of processes and a knack for driving efficiency. In this blog post, we delve into the most common interview questions you might encounter for this role, providing insightful example answers and practical tips to help you respond with confidence and clarity. Prepare to enhance your interview skills and make a lasting impression.
Download Continuous Improvement Specialist Interview Questions in PDF
To make your preparation even more convenient, we've compiled all these top Continuous Improvement Specialistinterview questions and answers into a handy PDF.
Click the button below to download the PDF and have easy access to these essential questions anytime, anywhere:
List of Continuous Improvement Specialist Interview Questions
Situational Interview Questions
You are tasked with improving a process that several departments are involved in. How would you engage stakeholders from these departments?
How to Answer
- 1
Identify key stakeholders from each department early in the process.
- 2
Schedule an initial meeting to discuss goals and expectations.
- 3
Encourage open communication to gather input and concerns.
- 4
Use collaborative tools for feedback and tracking progress.
- 5
Regularly update stakeholders on improvements and solicit their feedback.
Example Answers
I would start by identifying the key stakeholders from each department involved in the process. Then, I'd organize a kickoff meeting to align our goals and set expectations. During this meeting, I would emphasize the importance of their input and establish a feedback loop using shared tools like a project management software.
If a current process seems highly efficient, but a team member suggests an untested improvement, how would you handle the situation?
How to Answer
- 1
Acknowledge the team member's suggestion to create a positive atmosphere
- 2
Assess the current process metrics and performance data to confirm efficiency
- 3
Encourage a pilot test of the suggested improvement on a small scale
- 4
Involve the team member in planning the test to ensure buy-in
- 5
Evaluate the results and decide collaboratively on implementation
Example Answers
I would first acknowledge the team member's suggestion and encourage their innovative thinking. Then, I would review our current metrics to ensure the process is indeed efficient. If everything checks out, I'd propose a small pilot test of their idea to see if it yields positive results, involving them in the planning to foster teamwork.
Don't Just Read Continuous Improvement Specialist Questions - Practice Answering Them!
Reading helps, but actual practice is what gets you hired. Our AI feedback system helps you improve your Continuous Improvement Specialist interview answers in real-time.
Personalized feedback
Unlimited practice
Used by hundreds of successful candidates
If halfway through a process improvement project, it becomes clear that your approach isn't working, what would you do?
How to Answer
- 1
Acknowledge the issue and remain open to change.
- 2
Gather data and feedback from stakeholders about the current approach.
- 3
Conduct a root cause analysis to understand why the approach is failing.
- 4
Propose an alternative strategy based on the findings.
- 5
Communicate the changes and the rationale to all team members.
Example Answers
I would first acknowledge that the current approach isn't yielding results. Then, I would gather feedback from the team and stakeholders to identify specific pain points. After analyzing the data, I would suggest a new strategy that addresses the identified issues and ensure everyone is on board with this change.
How would you handle a situation where an improvement initiative could potentially disrupt business operations?
How to Answer
- 1
Assess the potential impact of the initiative on current operations and identify critical areas.
- 2
Engage stakeholders early to gather their input and concerns regarding the initiative.
- 3
Develop a phased implementation plan to minimize disruption, including pilot testing if possible.
- 4
Communicate clearly about the initiative's benefits and how to mitigate risks during implementation.
- 5
Monitor the process closely and be prepared to adapt based on feedback and operational needs.
Example Answers
I would first evaluate the potential impact on operations and engage with key stakeholders to address their concerns. By creating a phased implementation plan, I would test the initiative in a controlled environment before a full rollout. This ensures we minimize disruptions and collect valuable feedback to improve the process.
You're given multiple process improvement requests. How would you prioritize them?
How to Answer
- 1
Assess the impact of each request on business outcomes.
- 2
Evaluate the resources required for implementation.
- 3
Consider the urgency of each improvement request.
- 4
Consult with stakeholders to understand their perspectives.
- 5
Utilize a scoring system for a structured approach.
Example Answers
I would start by assessing each request's potential impact on overall business goals. Then, I'd look at the resources needed and identify any that require immediate attention due to urgency. Finally, I would consult with involved stakeholders to ensure alignment and apply a scoring system to prioritize effectively.
Suppose you have limited resources for an improvement project. How would you allocate them effectively?
How to Answer
- 1
Identify the key areas that will have the highest impact on performance.
- 2
Prioritize tasks based on urgency and potential ROI.
- 3
Leverage cross-functional skills within your team to maximize resource efficiency.
- 4
Establish metrics to evaluate effectiveness and make adjustments as needed.
- 5
Consider low-cost quick wins that can deliver immediate benefits.
Example Answers
I would start by analyzing the project goals and determining which tasks align most closely with achieving significant improvements. Then, I would prioritize those tasks, focusing on quick wins that require minimal resources but offer high impact. Throughout the project, I would monitor outcomes and adjust allocations based on the effectiveness of each initiative.
How would you go about measuring the success of an improvement initiative you implemented?
How to Answer
- 1
Define specific KPIs related to the initiative's goals
- 2
Establish a baseline measurement before implementation
- 3
Track progress regularly against set KPIs
- 4
Gather feedback from stakeholders involved
- 5
Analyze the outcomes against the baseline to identify improvements
Example Answers
I would start by identifying KPIs such as efficiency gains or cost reductions. Before implementing the initiative, I would measure the current performance to establish a baseline. After implementation, I'd track these KPIs regularly to see the impact. I'd also collect feedback from team members to understand qualitative improvements.
How would you lead a team through the implementation of a new process that eliminates an entire department's tasks?
How to Answer
- 1
Start by communicating the vision clearly to the team.
- 2
Engage the team in discussions about the new process and encourage feedback.
- 3
Provide training and resources to ensure everyone is comfortable with the new process.
- 4
Establish metrics to measure the success of the implementation.
- 5
Acknowledge and address any concerns or resistance from the team.
Example Answers
I would begin by holding a meeting to explain the rationale behind the new process, making sure everyone understands the benefits. Then, I would involve the team in open discussions to gather their insights and address concerns. Training sessions would follow to equip them with the necessary skills, and I would set clear metrics to track our progress throughout the implementation.
After implementing a new process, how would you ensure all employees are trained adequately to use it effectively?
How to Answer
- 1
Conduct a needs assessment to identify knowledge gaps.
- 2
Develop clear, step-by-step training materials.
- 3
Organize training sessions, both hands-on and virtual.
- 4
Assign mentors or champions who can provide support.
- 5
Gather feedback and adjust training methods as needed.
Example Answers
I would first assess the current skill levels of the employees to tailor the training accordingly. Next, I would create comprehensive training materials and conduct interactive workshops to engage the employees. I would also ensure that there are experienced mentors available for ongoing support.
Imagine a situation where you have two potential solutions to improve a process. How do you decide which one to implement?
How to Answer
- 1
Evaluate each solution based on impact and feasibility
- 2
Consider data and metrics to support your decision
- 3
Involve stakeholders to gather diverse perspectives
- 4
Run a pilot test if possible to validate effectiveness
- 5
Choose the solution that aligns best with the organization's goals
Example Answers
I would analyze the pros and cons of each solution by assessing their potential impact on efficiency and cost. After gathering data from past performance, I'd consult with key stakeholders to gauge their insights before making a decision.
Don't Just Read Continuous Improvement Specialist Questions - Practice Answering Them!
Reading helps, but actual practice is what gets you hired. Our AI feedback system helps you improve your Continuous Improvement Specialist interview answers in real-time.
Personalized feedback
Unlimited practice
Used by hundreds of successful candidates
Behavioral Interview Questions
Tell me about a time when you had to work with a team to implement a continuous improvement project. What was your role, and what was the outcome?
How to Answer
- 1
Choose a specific project that shows teamwork and improvement.
- 2
Clearly define your role and contributions to the project.
- 3
Highlight the results achieved and any measurable improvements.
- 4
Use the STAR method: Situation, Task, Action, Result.
- 5
Reflect on what you learned and how it impacted your approach.
Example Answers
In my previous role at Company X, our team aimed to reduce production downtime. I was the team lead, coordinating weekly meetings and analyzing downtime data. By implementing a new logging system and training staff, we reduced downtime by 30% within three months, significantly increasing throughput.
Can you describe a time when you identified a process inefficiency and successfully improved it?
How to Answer
- 1
Select a specific process you improved; clarity is key
- 2
Quantify the inefficiency; use data or metrics if possible
- 3
Explain your approach; detail the steps you took for improvement
- 4
Highlight the outcome; focus on results and impact
- 5
Relate it to continuous improvement principles; show how it aligns with best practices
Example Answers
In my previous role, I noticed that our order processing time was taking an average of 48 hours. I analyzed the process and identified bottlenecks in data entry. I proposed digitizing our order forms, which cut processing time down to 24 hours, improving customer satisfaction and reducing errors.
Don't Just Read Continuous Improvement Specialist Questions - Practice Answering Them!
Reading helps, but actual practice is what gets you hired. Our AI feedback system helps you improve your Continuous Improvement Specialist interview answers in real-time.
Personalized feedback
Unlimited practice
Used by hundreds of successful candidates
Describe an instance where you led a team through a significant change process. How did you handle resistance?
How to Answer
- 1
Start with a specific example of a change process you led.
- 2
Explain the rationale for the change and your role in it.
- 3
Discuss the resistance you encountered and the concerns raised.
- 4
Describe the strategies you used to address the resistance.
- 5
Conclude with the outcome and any lessons learned.
Example Answers
At my previous job, I led the implementation of a new project management software. The team was resistant due to fear of change. I organized a series of training sessions to demonstrate the software's benefits and held Q&A sessions to address concerns. This approach helped alleviate fears and increased buy-in, leading to a successful transition.
Have you ever had a conflict arise while working on a process improvement project? How did you handle it?
How to Answer
- 1
Describe the conflict briefly and contextually.
- 2
Explain the stakeholders involved and their perspectives.
- 3
Detail the steps you took to address the issue.
- 4
Highlight the outcome and what you learned.
- 5
Emphasize your communication and collaborative skills.
Example Answers
During a recent project to streamline our reporting process, I encountered a conflict with the finance team who were concerned about changes affecting their workflow. I organized a meeting to listen to their concerns, clarified the benefits of the changes, and proposed a pilot to address their issues. Ultimately, we reached a compromise that improved efficiency while satisfying their needs.
Can you give an example of when you had to persuade others to adopt a new process?
How to Answer
- 1
Start with a brief context of the situation.
- 2
Explain what the new process was and why it was needed.
- 3
Describe the objections or resistance you faced.
- 4
Outline your strategy for persuasion and communication.
- 5
Conclude with the outcome and any metrics that demonstrate success.
Example Answers
In my previous role, we needed to implement a new inventory tracking system to reduce errors. Some team members were skeptical about the change. I organized a meeting to explain the benefits and shared data showing previous issues. By involving them in training, they felt empowered and adopted the system quickly, leading to a 30% reduction in discrepancies within three months.
Describe a situation where an improvement initiative you worked on did not go as planned. What did you do?
How to Answer
- 1
Choose a specific initiative and clearly describe what went wrong.
- 2
Explain the reasons behind the failure without placing blame.
- 3
Highlight your role in addressing the issue and any corrective actions taken.
- 4
Show what you learned from the experience and how it influenced future initiatives.
- 5
Express your ability to adapt and keep a positive outlook despite setbacks.
Example Answers
In a previous role, I led a project to streamline our reporting process using new software. However, we faced significant resistance from users who were accustomed to the old method. I organized meetings to understand their concerns and provided additional training. Ultimately, I adapted the implementation plan based on their feedback, and the project was successful in the long run.
Can you tell me about a time when you proactively identified a continuous improvement opportunity that was not immediately apparent to others?
How to Answer
- 1
Choose a specific instance from your experience.
- 2
Explain the context and your observation that led to the identification.
- 3
Describe the actions you took to address the opportunity.
- 4
Highlight the impact or results of your actions.
- 5
Conclude with what you learned or how it influenced your work.
Example Answers
In my previous role, I noticed that our team was spending excessive time on manual data entry. I proposed automating the process using a software tool, which significantly reduced our workload by 30%. This allowed the team to focus more on strategic tasks, and I learned the value of using technology to improve efficiency.
How have you used data to drive improvement decisions in the past?
How to Answer
- 1
Identify specific data sources you have used for analysis.
- 2
Describe the analytical methods you applied to interpret the data.
- 3
Provide a clear example of how the data led to a decision or action.
- 4
Mention the results or improvements that occurred as a result.
- 5
Be concise and focused on your role in the process.
Example Answers
In my previous role, I analyzed customer feedback data from surveys to identify recurring issues. I used statistical analysis to pinpoint critical pain points and proposed changes to our service protocols. This led to a 20% reduction in customer complaints over six months.
Give an example of how you improved a process that directly impacted customer satisfaction.
How to Answer
- 1
Identify a specific process you improved.
- 2
Explain the problem with the original process.
- 3
Describe the solution you implemented.
- 4
Quantify the impact on customer satisfaction.
- 5
Use a clear structure: Situation, Task, Action, Result.
Example Answers
At my previous job, I noticed that our order processing time was slowing down customer deliveries. We were taking up to 3 days to process orders. I implemented an automated system that reduced processing time to just 1 day. As a result, customer satisfaction scores increased by 30%.
Tell me about a project where you significantly reduced process waste or cycle time.
How to Answer
- 1
Use the STAR method: Situation, Task, Action, Result.
- 2
Clearly define the waste or cycle time issue before your intervention.
- 3
Quantify the impact of your actions with metrics or percentages.
- 4
Explain the tools or methodologies you used for improvement.
- 5
Describe how you engaged the team or stakeholders in the process.
Example Answers
In my last role, we faced excessive wait times in our assembly line. I led a Kaizen event where we mapped out the entire process and identified bottlenecks. By reorganizing the layout and training staff on new procedures, we reduced cycle time by 30% within three months.
Don't Just Read Continuous Improvement Specialist Questions - Practice Answering Them!
Reading helps, but actual practice is what gets you hired. Our AI feedback system helps you improve your Continuous Improvement Specialist interview answers in real-time.
Personalized feedback
Unlimited practice
Used by hundreds of successful candidates
Technical Interview Questions
Explain the key principles of Lean methodology and how you have applied them in your work.
How to Answer
- 1
Start by defining Lean methodology in simple terms.
- 2
List the key principles such as value, waste reduction, continuous improvement, and flow.
- 3
Share a specific example of a project where you applied Lean principles.
- 4
Discuss measurable outcomes or improvements from your example.
- 5
Conclude with how these principles can be beneficial in future projects.
Example Answers
Lean methodology focuses on maximizing value by minimizing waste. Key principles include identifying value, eliminating waste, and continuous improvement. In my previous role, I led a project to streamline our order processing by mapping the workflow, identifying bottlenecks, and reducing processing time by 30%. This not only improved efficiency but also enhanced customer satisfaction.
What are the key differences between Lean and Six Sigma approaches to process improvement?
How to Answer
- 1
Focus on the goals of each approach, Lean aims to eliminate waste, Six Sigma aims to reduce variability.
- 2
Highlight the methodologies used in each approach, Lean uses tools like value stream mapping, Six Sigma uses DMAIC.
- 3
Discuss the role of data, Six Sigma is data-driven while Lean is more about process flow.
- 4
Mention the cultural impact, Lean fosters a culture of continuous improvement, Six Sigma focuses on quality control.
- 5
Be ready to use examples from experience that illustrate your understanding of both methodologies.
Example Answers
Lean primarily focuses on eliminating waste and improving efficiency by streamlining processes, while Six Sigma aims to reduce variability and defects through data-driven methodologies like DMAIC.
Don't Just Read Continuous Improvement Specialist Questions - Practice Answering Them!
Reading helps, but actual practice is what gets you hired. Our AI feedback system helps you improve your Continuous Improvement Specialist interview answers in real-time.
Personalized feedback
Unlimited practice
Used by hundreds of successful candidates
Describe how you would conduct a root cause analysis on a recurring process failure.
How to Answer
- 1
Define the process failure and gather data on failures.
- 2
Utilize tools like the 5 Whys or Fishbone diagram to identify root causes.
- 3
Involve cross-functional teams for diverse perspectives and insights.
- 4
Develop an action plan to address root causes and prevent recurrence.
- 5
Establish metrics to monitor the effectiveness of implemented solutions.
Example Answers
I would start by clearly defining the recurring process failure and collecting relevant data, such as frequency and impact. Then, I would apply the 5 Whys technique to drill down to the root cause, involving team members to gain different insights. After identifying the root causes, I would create a plan with specific actions to mitigate these issues and track the results.
What techniques do you use for process mapping, and why are they effective?
How to Answer
- 1
Start by mentioning specific process mapping techniques such as SIPOC, flowcharts, or value stream mapping.
- 2
Explain the strengths of each technique in terms of clarity and visualization of processes.
- 3
Include examples of situations where each technique has been successfully applied.
- 4
Discuss how these techniques help in identifying inefficiencies and opportunities for improvement.
- 5
Conclude with how these mapping techniques facilitate team discussions and stakeholder engagement.
Example Answers
I often use flowcharts for process mapping because they clearly illustrate the steps in a process. For example, in my last project, creating a flowchart helped our team quickly identify bottlenecks, leading to a 20% reduction in processing time.
What are the most important factors to consider when managing change during an improvement initiative?
How to Answer
- 1
Identify stakeholders and understand their perspectives
- 2
Communicate the vision and benefits clearly
- 3
Provide training and resources to support the change
- 4
Establish feedback mechanisms to gauge progress
- 5
Monitor the change process and adjust as necessary
Example Answers
In managing change during an improvement initiative, I believe it's crucial to first identify key stakeholders and understand their concerns. Clear communication about the vision and benefits helps to gain buy-in, and providing adequate training ensures everyone feels equipped to adapt.
How do you develop Key Performance Indicators (KPIs) to measure process improvement?
How to Answer
- 1
Identify the critical objectives of the process
- 2
Select measurable outcomes that reflect those objectives
- 3
Ensure that the KPIs are relevant to stakeholders
- 4
Use historical data to set benchmarks
- 5
Monitor and adjust KPIs based on performance feedback
Example Answers
I start by clarifying the primary goals of the process, then I select specific outcomes that we can measure, like cycle time or defect rate. I ensure these KPIs align with what stakeholders need, and I use past performance data to establish realistic benchmarks. Finally, I regularly review the KPIs to ensure they remain relevant and adjust them as needed.
Can you explain what value stream mapping is and how it can benefit process improvement?
How to Answer
- 1
Define value stream mapping simply as a visual tool
- 2
Highlight its purpose in identifying waste and inefficiencies
- 3
Mention the steps involved in creating a value stream map
- 4
Discuss how it aids in aligning processes with customer value
- 5
Emphasize collaboration among team members in the mapping process
Example Answers
Value stream mapping is a technique used to visualize the flow of materials and information through a process. It helps identify waste, bottlenecks, and areas for improvement. By mapping out the current state, teams can work collaboratively to redesign processes that maximize value for the customer.
What are some tools you frequently use for continuous improvement, and how do they help?
How to Answer
- 1
Identify specific tools you know well
- 2
Explain how each tool contributes to improvement
- 3
Use examples from past experiences
- 4
Mention the impact of these tools on outcomes
- 5
Be concise and focused in your response
Example Answers
I frequently use Lean methodologies like 5S, which helps in organizing and standardizing the workspace to reduce waste. For example, in my last project, implementing 5S led to a 20% increase in productivity.
How do you plan and manage continuous improvement projects to ensure they are completed on time and within budget?
How to Answer
- 1
Define clear project goals and objectives at the start.
- 2
Create a detailed project plan, including timelines and budget estimates.
- 3
Use metrics to track progress and identify issues early.
- 4
Involve stakeholders throughout the project for feedback and support.
- 5
Regularly review and adjust the plan as needed to stay on track.
Example Answers
I start by defining the project's goals and objectives clearly. Then, I create a detailed project plan that outlines the tasks, timelines, and budget. I track progress using specific metrics, ensuring I can catch any issues early. I also keep stakeholders involved for their input. Regular reviews help me adapt the plan as needed.
How do you ensure quality is maintained during and after process improvement implementations?
How to Answer
- 1
Establish clear quality metrics before starting the implementation.
- 2
Involve team members in quality checks throughout the process.
- 3
Conduct regular reviews to monitor quality outcomes during implementation.
- 4
Implement a feedback loop for continuous improvement after changes are made.
- 5
Document lessons learned for future process enhancements.
Example Answers
I ensure quality by establishing clear metrics at the start, involving the team in quality checks, and conducting regular reviews during the implementation to monitor our progress.
Don't Just Read Continuous Improvement Specialist Questions - Practice Answering Them!
Reading helps, but actual practice is what gets you hired. Our AI feedback system helps you improve your Continuous Improvement Specialist interview answers in real-time.
Personalized feedback
Unlimited practice
Used by hundreds of successful candidates
Continuous Improvement Specialist Position Details
Salary Information
Recommended Job Boards
These job boards are ranked by relevance for this position.
Related Positions
Ace Your Next Interview!
Practice with AI feedback & get hired faster
Personalized feedback
Used by hundreds of successful candidates
Ace Your Next Interview!
Practice with AI feedback & get hired faster
Personalized feedback
Used by hundreds of successful candidates