Top 30 Drum Printer Interview Questions and Answers [Updated 2025]
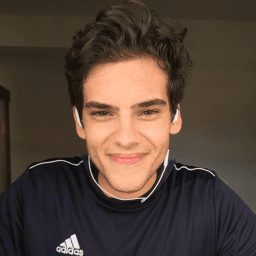
Andre Mendes
•
March 30, 2025
Preparing for a Drum Printer role can be challenging, but we've got you covered! This blog post compiles the most common interview questions for this position, providing you with example answers and effective tips to tackle them confidently. Whether you're a seasoned professional or a newcomer, our insights will help you stand out and ace your interview. Dive in to boost your preparation and secure your next job!
Download Drum Printer Interview Questions in PDF
To make your preparation even more convenient, we've compiled all these top Drum Printerinterview questions and answers into a handy PDF.
Click the button below to download the PDF and have easy access to these essential questions anytime, anywhere:
List of Drum Printer Interview Questions
Behavioral Interview Questions
Can you describe a challenging printing project you worked on and how you overcame the difficulties?
How to Answer
- 1
Identify a specific project that had significant challenges
- 2
Explain the nature of the challenge clearly
- 3
Describe the steps you took to address the challenge
- 4
Highlight any collaboration with team members or departments
- 5
Conclude with the positive outcome or what you learned from the experience
Example Answers
In a recent project, we faced a tight timeline for printing promotional materials for a major event. The challenge was coordinating with suppliers who delayed their deliveries. I communicated with them daily to expedite the process and adjusted our printing schedule to accommodate. We completed the project on time, and the event was a success, which strengthened our client relationship.
Tell me about a time when you had to work closely with a team to complete a drum printing project.
How to Answer
- 1
Choose a specific project that highlights teamwork.
- 2
Describe your role and contributions clearly.
- 3
Mention challenges encountered and how the team overcame them.
- 4
Include the outcome and what you learned from the experience.
- 5
Keep it concise and focused on teamwork dynamics.
Example Answers
In my previous job, we worked on a large drum printing project for a client. I coordinated with the design team to ensure our specifications met their expectations. We faced a tight deadline, so we held daily briefings to stay on track. In the end, we delivered the project on time, and the client praised our collaboration. I learned the importance of communication in a team.
Don't Just Read Drum Printer Questions - Practice Answering Them!
Reading helps, but actual practice is what gets you hired. Our AI feedback system helps you improve your Drum Printer interview answers in real-time.
Personalized feedback
Unlimited practice
Used by hundreds of successful candidates
How have you adapted to changes in printing technology or processes in your previous work?
How to Answer
- 1
Identify specific technologies you have worked with.
- 2
Explain the challenges posed by new technologies.
- 3
Describe a situation where you learned quickly.
- 4
Mention any training or resources you utilized.
- 5
Discuss the positive outcomes of your adaptability.
Example Answers
In my previous role, when our department transitioned to digital printing, I quickly enrolled in a training workshop. I learned how to operate the new printers effectively and helped train my colleagues, which improved our overall productivity.
Give an example of a time when attention to detail made a significant difference in your printing results.
How to Answer
- 1
Choose a specific instance that highlights your attention to detail.
- 2
Explain the context and your role in the situation.
- 3
Describe the actions you took to ensure accuracy and quality.
- 4
Emphasize the positive outcome resulting from your focus on details.
- 5
Keep it relevant to printing processes or quality control.
Example Answers
In my previous job, we were preparing for a large print run of marketing materials. I noticed some discrepancies in the color profiles for the images. By meticulously checking each file against our standards, I ensured consistent color output. This attention to detail not only saved us from potential reprints but also received praise from the client for the final results.
Describe a situation where you led a team to achieve a specific goal in your printing work.
How to Answer
- 1
Choose a specific project with a clear objective.
- 2
Detail your role and the team's structure.
- 3
Explain the challenges faced and how you addressed them.
- 4
Highlight the results and the goal achieved.
- 5
Include any learning experiences or improvements made.
Example Answers
In my previous job, I led a team to reduce print waste by 20% in six months. We implemented a new recycling process and trained staff on efficient printing techniques. This initiative not only achieved our waste reduction goal but also saved the company money.
Describe a time when you disagreed with a colleague regarding a printing process. How did you resolve it?
How to Answer
- 1
Choose a specific disagreement related to printing.
- 2
Focus on the resolution process and collaboration.
- 3
Highlight communication skills and willingness to compromise.
- 4
Mention the outcome and what you learned.
- 5
Keep it concise and relevant to printing.
Example Answers
In a previous job, my colleague wanted to use a different ink for a large print job. I explained my concerns about color fastness. We decided to run tests together to compare results. Ultimately, we found a compromise and used my suggested ink but adjusted the formulation based on his input. The project was a success and we both learned the value of testing.
Have you ever taken the initiative to implement a new technique or process in your printing work? Describe that experience.
How to Answer
- 1
Identify a specific technique or process you improved.
- 2
Emphasize the results and benefits of the change.
- 3
Share any challenges you faced during implementation.
- 4
Mention how you communicated this change to your team.
- 5
Show how it increased efficiency or quality in printing.
Example Answers
In my previous role, I introduced a new color calibration technique that reduced ink waste. The result was a 15% savings on ink costs and improved color consistency across prints. I communicated the new process through a team workshop and supported others in its implementation.
How have you responded to feedback on your printing work in the past?
How to Answer
- 1
Reflect on specific feedback you received
- 2
Highlight how you implemented changes
- 3
Emphasize positive outcomes from adjustments
- 4
Show your willingness to learn and adapt
- 5
Keep your answer focused and concise
Example Answers
I once received feedback about color inconsistencies in my prints. I took that constructively and worked on calibrating the printer settings accordingly, which resulted in improved color accuracy for subsequent projects.
Can you discuss an instance where you had to manage a complex printing project from start to finish?
How to Answer
- 1
Identify a specific project that illustrates your skills.
- 2
Describe your role and responsibilities clearly.
- 3
Highlight any challenges faced and how you overcame them.
- 4
Mention collaboration with team members or clients during the project.
- 5
Conclude with the outcome and what you learned from the experience.
Example Answers
In my previous job, I managed a project for a large marketing print campaign. My role involved coordinating with both the design team and the print facility to ensure quality. We encountered delays due to file issues, but I organized extra review sessions that helped us fix the problems quickly. The campaign was delivered on time, and we received positive feedback from the client.
Don't Just Read Drum Printer Questions - Practice Answering Them!
Reading helps, but actual practice is what gets you hired. Our AI feedback system helps you improve your Drum Printer interview answers in real-time.
Personalized feedback
Unlimited practice
Used by hundreds of successful candidates
Technical Interview Questions
What types of drum printing equipment have you worked with, and what are the main differences between them?
How to Answer
- 1
Identify specific drum printing technologies you have experience with
- 2
Explain key features that differentiate each type
- 3
Include examples of applications for each type of drum printer
- 4
Discuss any relevant maintenance or operational differences
- 5
Be prepared to talk about your comfort level with each type
Example Answers
I have worked with both flexographic and gravure drum printers. Flexographic printers are great for high-speed tasks on various materials, while gravure printers offer higher print quality for longer runs, especially on packaging. Each has its unique setup and maintenance requirements.
Can you explain the drum printing process, including key steps from setup to quality checks?
How to Answer
- 1
Start with an overview of the drum printing system.
- 2
Outline the main setup steps including loading the ink and configuring the drum.
- 3
Describe the printing process highlighting how the image transfers.
- 4
Mention the cooling and drying phase after printing.
- 5
Conclude with the importance of quality checks and adjustments.
Example Answers
The drum printing process begins by setting up the system, where I load the correct inks and configure the drum for the desired print. Once set, the image is transferred from the drum to the substrate through the pressure rollers. After printing, the prints are cooled and dried. Finally, I perform quality checks to ensure consistency and accuracy in color and alignment.
Don't Just Read Drum Printer Questions - Practice Answering Them!
Reading helps, but actual practice is what gets you hired. Our AI feedback system helps you improve your Drum Printer interview answers in real-time.
Personalized feedback
Unlimited practice
Used by hundreds of successful candidates
How do you troubleshoot common issues that arise during the drum printing process?
How to Answer
- 1
Identify common issues such as color misalignment and ink smudging.
- 2
Check the drum and print heads for wear or damage.
- 3
Ensure proper calibration and alignment of the printing components.
- 4
Clean the printer regularly to avoid build-up that can affect quality.
- 5
Document previous issues and their solutions for future reference.
Example Answers
If I notice color misalignment, I first check the calibration settings and adjust them as needed. Then, I inspect the drum for any wear and clean the print heads to ensure clear ink application.
What software tools do you use for design and setup in drum printing?
How to Answer
- 1
Mention specific software you are proficient in
- 2
Explain how you've used each tool in drum printing
- 3
Focus on tools relevant to the role
- 4
Highlight any experience with color management and workflow
- 5
Discuss how you ensure precision and quality in your designs
Example Answers
I primarily use Adobe Illustrator and FlexiSign for design and setup, ensuring that my artwork is print-ready and meets specifications. I've also utilized RIP software like Wasatch to manage color and maintain quality output.
Can you discuss the various types of inks used in drum printing and their applications?
How to Answer
- 1
Identify the main types of inks commonly used in drum printing.
- 2
Briefly explain the properties of each ink type.
- 3
Mention specific applications or industries for each ink.
- 4
Highlight any advantages or limitations of the inks.
- 5
Use examples from your experience if possible.
Example Answers
In drum printing, we commonly use oil-based, water-based, and UV-curable inks. Oil-based inks offer rich colors and durability, making them suitable for packaging. Water-based inks are more environmentally friendly and used in printing on paper products. UV-curable inks dry quickly and are ideal for glossy finishes.
What routine maintenance procedures do you follow for drum printing machines?
How to Answer
- 1
Identify specific routine checks such as ink levels and print quality
- 2
Describe cleaning procedures for the drum and ink supply
- 3
Mention any lubrication requirements for moving parts
- 4
Discuss monitoring and replacing worn parts timely
- 5
Emphasize the importance of maintaining the print settings and calibration
Example Answers
I routinely check the ink levels and replace them as needed to ensure consistent quality. I also clean the drum and the ink supply system to prevent clogs and maintain print clarity.
What safety protocols do you observe in a drum printing environment?
How to Answer
- 1
Identify specific safety equipment used, like gloves and goggles.
- 2
Mention the importance of proper machine handling procedures.
- 3
Emphasize the need for regular maintenance checks on equipment.
- 4
Discuss the significance of keeping work areas clean and organized.
- 5
Highlight the importance of training and following established safety guidelines.
Example Answers
In a drum printing environment, I always wear protective gear such as gloves and goggles. I strictly follow machine handling procedures to avoid accidents, and I ensure that regular maintenance checks are conducted on the equipment to keep everything in safe working order.
What metrics do you use to assess the quality of printed materials?
How to Answer
- 1
Focus on specific metrics relevant to printing processes.
- 2
Mention common industry standards like color accuracy and registration.
- 3
Include both qualitative and quantitative measures.
- 4
Emphasize the importance of customer satisfaction feedback.
- 5
Share examples of how these metrics have improved quality in your past work.
Example Answers
I use metrics like color accuracy, print density, and registration precision. Monitoring these helps ensure the prints meet client specifications consistently.
How do you ensure color consistency across different runs of drum printing?
How to Answer
- 1
Calibrate color profiles regularly for accuracy.
- 2
Use standardized ink formulations to maintain color integrity.
- 3
Implement regular quality checks for each print run.
- 4
Maintain consistent environmental conditions in the printing area.
- 5
Document color settings and adjustments for future reference.
Example Answers
I ensure color consistency by regularly calibrating our color profiles and using standardized ink formulations. This helps maintain the integrity across different runs.
What recent trends in the printing industry do you find most impactful for drum printing?
How to Answer
- 1
Identify key technological advancements like digital printing integration.
- 2
Discuss sustainability trends influencing material choices.
- 3
Mention shifts in consumer demand for customization and short runs.
- 4
Highlight the impact of automation on production efficiency.
- 5
Consider the role of smart technology and IoT in drum printing.
Example Answers
One significant trend is the integration of digital technologies with drum printing, allowing for quicker setup and flexibility in short-run projects.
Don't Just Read Drum Printer Questions - Practice Answering Them!
Reading helps, but actual practice is what gets you hired. Our AI feedback system helps you improve your Drum Printer interview answers in real-time.
Personalized feedback
Unlimited practice
Used by hundreds of successful candidates
Situational Interview Questions
If you notice that printed materials are not meeting quality standards, what steps would you take to address the issue?
How to Answer
- 1
Identify the specific quality issues in the printed materials.
- 2
Check the printer settings and ensure they are configured correctly.
- 3
Perform routine maintenance on the equipment to prevent further issues.
- 4
Consult with team members to gather insights and possible solutions.
- 5
Implement corrective actions and monitor results for improvement.
Example Answers
I would start by identifying the specific quality issues, such as color discrepancies or misalignments. Then, I would check the printer settings and perform any necessary maintenance to ensure the machinery is functioning properly.
You have multiple printing deadlines approaching. How would you prioritize your tasks?
How to Answer
- 1
Identify the deadlines and their importance
- 2
Evaluate the complexity of each printing task
- 3
Consider any dependencies between tasks
- 4
Communicate with stakeholders about priorities
- 5
Allocate time effectively based on urgency
Example Answers
I would start by listing all the printing tasks and their deadlines. Then, I would prioritize based on which tasks are most urgent and complex, ensuring to communicate any potential delays to the team.
Don't Just Read Drum Printer Questions - Practice Answering Them!
Reading helps, but actual practice is what gets you hired. Our AI feedback system helps you improve your Drum Printer interview answers in real-time.
Personalized feedback
Unlimited practice
Used by hundreds of successful candidates
A client is unhappy with the final printed product. How would you handle the situation?
How to Answer
- 1
Listen carefully to the client's concerns to understand the issue
- 2
Acknowledge the client's feelings and apologize for any inconvenience
- 3
Investigate the specific problem by reviewing production details
- 4
Offer solutions or alternatives to meet the client's expectations
- 5
Follow up after resolution to ensure client satisfaction
Example Answers
I would first listen to the client's feedback to understand their specific concerns. Acknowledging their feelings, I would apologize for the inconvenience caused and investigate the issue. I would then discuss possible solutions with them, such as reprinting the product or offering a discount, and follow up to ensure they are satisfied with the resolution.
If you were required to reduce costs in a printing project without compromising quality, how would you approach that?
How to Answer
- 1
Analyze the current expenses and identify the highest cost areas.
- 2
Negotiate with suppliers for better pricing on materials.
- 3
Optimize the printing process to reduce waste and increase efficiency.
- 4
Consider alternative materials that maintain quality but lower costs.
- 5
Implement a quality control system to catch issues early and avoid reprints.
Example Answers
I would first analyze the project budget to find where the most significant expenses are. Then, I would negotiate with our suppliers to see if we can get better rates on inks and papers. Additionally, I'd look for ways to streamline the printing process to minimize waste.
Imagine you could improve one aspect of the drum printing process. What would it be and why?
How to Answer
- 1
Focus on a specific aspect of the drum printing process such as efficiency, color consistency, or waste reduction.
- 2
Consider technological advancements that could enhance the current process.
- 3
Think about practical solutions that can be implemented without requiring a complete overhaul.
- 4
Use metrics or examples to support your suggested improvement.
- 5
Explain the impact of your improvement on overall production and quality.
Example Answers
I would improve the ink delivery system in the drum printing process to reduce waste and improve color consistency. By implementing a more precise ink dispensing mechanism, we can ensure that only the necessary amount of ink is used, which would save costs and reduce environmental impact.
If a printing job is delayed due to machinery failure, what steps would you take to resolve the issue?
How to Answer
- 1
Identify the specific machinery causing the delay
- 2
Communicate the issue to your team and management immediately
- 3
Assess if the failure can be fixed quickly or if a backup printer is available
- 4
Implement the solution and monitor the job progress closely
- 5
Document the incident and discuss preventive measures for the future
Example Answers
First, I would identify which machine failed and assess the issue. Then, I would inform my supervisor and team about the delay. If we have a backup printer available, I would switch to that. I would ensure the job is completed with minimal impact and report any maintenance needs for future prevention.
You’ve been assigned a new project with limited resources. How do you plan to proceed?
How to Answer
- 1
Identify the project's key objectives and focus on them.
- 2
Assess the available resources and prioritize their usage.
- 3
Break the project into smaller, manageable tasks to avoid overwhelm.
- 4
Engage team members to gather insights and delegate tasks.
- 5
Establish a timeline and milestones to monitor progress.
Example Answers
First, I would clarify the project's main objectives to ensure we stay focused. Then, I would analyze what resources we do have, such as time and personnel, and determine which tasks are essential. By breaking the project down into smaller tasks, I can manage them more effectively and involve the team in their areas of expertise. Finally, I would set clear milestones to track our progress.
Describe a time when you had to produce a large volume of prints under tight deadlines and how you managed the pressure.
How to Answer
- 1
Recall a specific project where the deadline was tight.
- 2
Explain the steps you took to prioritize tasks and manage time.
- 3
Mention any tools or strategies you used to streamline the printing process.
- 4
Discuss how you communicated with your team or stakeholders.
- 5
Reflect on what you learned from the experience.
Example Answers
In my previous job, we received a last-minute order for 5,000 prints needed within 48 hours. I immediately assessed my available resources and divided the workload among my team. We used our editing software to batch process the files, which saved us a lot of time. I kept in close contact with our production manager to ensure we were on track and made sure to maintain quality throughout. We delivered ahead of schedule, and I learned the importance of effective teamwork under pressure.
If you discover a mistake in a job after delivering to a client, what steps would you take to rectify the situation?
How to Answer
- 1
Immediately assess the nature and impact of the mistake
- 2
Communicate transparently with the client about the issue
- 3
Provide a solution or corrective action plan
- 4
Take responsibility for the mistake and apologize sincerely
- 5
Follow up to ensure the client is satisfied with the resolution
Example Answers
If I discover a mistake, I would first evaluate how it affects the client. Then, I'd promptly inform the client, explain the situation, and present a clear plan to fix the issue. I would also apologize for the inconvenience and ensure they are happy with the final result.
If you encounter a technical issue that you cannot resolve, what is your approach to seeking help?
How to Answer
- 1
Identify the specific issue and gather relevant information before asking for help
- 2
Choose the right person or resource to seek assistance from, such as a senior technician or documentation
- 3
Be clear and concise when explaining the problem to others
- 4
Show willingness to learn by asking questions and understanding the solutions offered
- 5
Follow up on the resolution to ensure the issue is resolved and learn for future reference
Example Answers
If I encounter a technical issue, I first try to pinpoint the problem and gather all relevant details. Then I reach out to a more experienced team member or consult the technical manuals available. I make sure to explain the issue clearly and ask specific questions to gain a better understanding of the solution.
Don't Just Read Drum Printer Questions - Practice Answering Them!
Reading helps, but actual practice is what gets you hired. Our AI feedback system helps you improve your Drum Printer interview answers in real-time.
Personalized feedback
Unlimited practice
Used by hundreds of successful candidates
Drum Printer Position Details
Related Positions
- Drummer
- Button Puncher
- Roller Painter
- Roller Machine Operator
- Dry Roller
- Battery Hand
- Cloth Baler
- Textile Machine Operator
- Dumper Operator
- Roller Operator
Similar positions you might be interested in.
Ace Your Next Interview!
Practice with AI feedback & get hired faster
Personalized feedback
Used by hundreds of successful candidates
Ace Your Next Interview!
Practice with AI feedback & get hired faster
Personalized feedback
Used by hundreds of successful candidates