Top 32 Cloth Baler Interview Questions and Answers [Updated 2025]
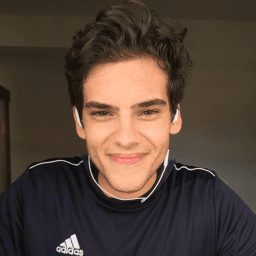
Andre Mendes
•
March 30, 2025
Preparing for a Cloth Baler interview can be daunting, but with the right guidance, you can confidently tackle any question that comes your way. In this post, we dive into the most common interview questions for the Cloth Baler role, providing you with example answers and practical tips to help you respond effectively. Whether you're a seasoned professional or new to the industry, these insights will set you on the path to success.
Download Cloth Baler Interview Questions in PDF
To make your preparation even more convenient, we've compiled all these top Cloth Balerinterview questions and answers into a handy PDF.
Click the button below to download the PDF and have easy access to these essential questions anytime, anywhere:
List of Cloth Baler Interview Questions
Behavioral Interview Questions
Can you give an example that highlights your work ethic in a challenging environment?
How to Answer
- 1
Choose a specific situation where you faced difficulties.
- 2
Highlight your actions and decisions during this challenge.
- 3
Emphasize your commitment to completing the task.
- 4
Mention any positive outcomes or lessons learned.
- 5
Keep the focus on your work ethic and resilience.
Example Answers
In my previous job at a recycling plant, we faced a situation where a machine broke down during peak processing hours. I stayed late to help troubleshoot and fix the issue, ensuring that we met our daily production goal.
Don't Just Read Cloth Baler Questions - Practice Answering Them!
Reading helps, but actual practice is what gets you hired. Our AI feedback system helps you improve your Cloth Baler interview answers in real-time.
Personalized feedback
Unlimited practice
Used by hundreds of successful candidates
Describe a time when you were under significant stress at work. What strategies did you use to cope?
How to Answer
- 1
Select a specific stressful situation relevant to the job.
- 2
Explain the context and what caused the stress.
- 3
Detail the strategies you used to cope, focusing on practical actions.
- 4
Emphasize the positive outcome or what you learned.
- 5
Keep it concise and focused on your response.
Example Answers
In my previous role, I faced significant stress during a machinery breakdown. The pressure was on to meet production deadlines. To cope, I prioritized tasks, communicated effectively with my team, and took short breaks to maintain focus. As a result, we managed to minimize downtime and completed the shift on time, learning the importance of teamwork under pressure.
Tell me about a time you received constructive criticism. How did you respond?
How to Answer
- 1
Choose a specific instance where you received feedback.
- 2
Explain the context and the nature of the criticism.
- 3
Describe your initial reaction honestly.
- 4
Detail the steps you took to address the feedback.
- 5
Share the positive outcome or lesson learned.
Example Answers
At my previous job, my supervisor told me that I needed to improve my pacing during production. At first, I felt defensive, but then I realized it was valuable feedback. I started to monitor my speed and practiced to find a better balance. As a result, my efficiency increased, which helped the team meet our targets.
Can you describe a time when you worked successfully as part of a team in a manufacturing environment?
How to Answer
- 1
Choose a specific project or task you were involved in.
- 2
Highlight your role and contributions clearly.
- 3
Emphasize teamwork and communication within the group.
- 4
Mention any challenges the team faced and how they were overcome.
- 5
Conclude with the outcome and what you learned from the experience.
Example Answers
In my last position, our team was tasked with optimizing the baling process to increase efficiency. I took on the role of coordinating communications between the shift teams and monitoring output. We faced a challenge when there was a malfunction in the equipment, but through teamwork, we quickly shared our insights and implemented a temporary fix. As a result, we increased our output by 15% and learned to rely on each other’s strengths.
Tell me about a situation where you faced a challenge while operating heavy machinery. How did you handle it?
How to Answer
- 1
Identify a specific challenge you faced while operating machinery
- 2
Explain your thought process at the time of the challenge
- 3
Describe the actions you took to address the problem
- 4
Share the outcome and what you learned from the experience
- 5
Emphasize safety and responsibility in your actions
Example Answers
During my last job, I was operating a baler when the machine jammed due to a large load that was improperly packed. I immediately stopped the machine to ensure safety. I assessed the situation, cleared the jam, and adjusted the loading technique to prevent it from happening again. This not only solved the issue but also improved our packing process going forward.
Describe a time when you had to adapt to a sudden change in your work environment. What was the outcome?
How to Answer
- 1
Identify a specific situation where a sudden change occurred
- 2
Explain how you assessed the new circumstances quickly
- 3
Describe the steps you took to adapt to the change
- 4
Highlight the outcome of your actions and any positive results
- 5
Keep it concise and focus on your personal contribution
Example Answers
In my previous job at the recycling facility, we had an unexpected shortage of baler operators. I quickly stepped up to learn the role, assisted in training new hires, and ensured production goals were met. This led to minimal downtime and improved team efficiency.
Give an example of when you identified a mistake in your work process that others had overlooked.
How to Answer
- 1
Think of a specific instance in your past work experience.
- 2
Describe the situation clearly and concisely.
- 3
Explain the mistake and its impact on the process or results.
- 4
Detail how you identified the mistake and what steps you took to correct it.
- 5
Highlight what you learned and how it improved future processes.
Example Answers
In my previous role as a cloth baler, I noticed that the baling machine was consistently underfilled, which led to inefficiencies. I reviewed the loading procedures and realized the team was skipping a crucial step. I documented the process correctly and trained the team on the new method, improving our output by 20%.
Describe a time when clear communication helped prevent a problem in your previous workplace.
How to Answer
- 1
Think of a specific situation where miscommunication could have led to a problem.
- 2
Explain how you communicated clearly, including the methods used (e.g., meetings, emails).
- 3
Describe the outcome of your clear communication and how it prevented issues.
- 4
Use a STAR format: Situation, Task, Action, Result.
- 5
Keep it brief but detailed enough to show your communication skills.
Example Answers
In my previous role as a warehouse associate, I noticed that we were running low on specific materials. I scheduled a meeting with the team to discuss inventory levels and clearly communicated the urgency. This led to a prompt order that arrived before we ran out, preventing delays in production.
Don't Just Read Cloth Baler Questions - Practice Answering Them!
Reading helps, but actual practice is what gets you hired. Our AI feedback system helps you improve your Cloth Baler interview answers in real-time.
Personalized feedback
Unlimited practice
Used by hundreds of successful candidates
Situational Interview Questions
How would you prioritize your tasks if faced with an unexpectedly high volume of materials to be processed?
How to Answer
- 1
Assess the urgency of the materials based on deadlines
- 2
Evaluate the resources available and their capabilities
- 3
Sort materials by type and processing requirements
- 4
Communicate with the team to delegate tasks effectively
- 5
Monitor progress and adjust priorities as needed
Example Answers
I would first assess which materials have the closest deadlines and tackle those first. Then, I'd organize the materials by type and process them according to their requirements while ensuring the team knows their roles.
What would you do if you noticed that the bales being produced are consistently below the desired weight?
How to Answer
- 1
Analyze the scale calibration to ensure it's accurate.
- 2
Check the input materials for any inconsistencies in quality.
- 3
Inspect the baler settings and operation to ensure they align with specifications.
- 4
Communicate findings with the team to address potential issues.
- 5
Document the problem and develop a plan for corrective action.
Example Answers
I would first check the scale to ensure it is properly calibrated. If it is accurate, I would review the input materials to confirm they meet the required standards and inspect the baler settings to ensure everything is set correctly.
Don't Just Read Cloth Baler Questions - Practice Answering Them!
Reading helps, but actual practice is what gets you hired. Our AI feedback system helps you improve your Cloth Baler interview answers in real-time.
Personalized feedback
Unlimited practice
Used by hundreds of successful candidates
If you find that a specific baling technique is preventing you from meeting production targets, how would you address this?
How to Answer
- 1
Evaluate the current baling technique and identify specific issues.
- 2
Discuss potential adjustments with team members for their input.
- 3
Test new methods or adjustments on a smaller scale before full implementation.
- 4
Monitor the results of changes closely to ensure they improve productivity.
- 5
Communicate improvements and training to the team effectively.
Example Answers
First, I would analyze the technique to pinpoint the exact problem. Then, I would bring my findings to my team and brainstorm possible adjustments. After testing one or two alternatives, I would monitor the outcomes and implement the best solution.
If you observe a colleague not wearing protective equipment, how do you handle the situation?
How to Answer
- 1
Approach the colleague privately to discuss the importance of safety.
- 2
Express concern for their well-being without being confrontational.
- 3
Suggest they wear the appropriate equipment for their safety.
- 4
If they refuse, report the situation to a supervisor to ensure safety protocols are followed.
- 5
Always prioritize safety and compliance with company policies.
Example Answers
I would privately approach my colleague and express my concern for their safety, reminding them that wearing protective equipment is crucial in our environment. If they still choose not to wear it, I would inform a supervisor.
How would you handle a situation where a new employee is struggling with the baling machine?
How to Answer
- 1
Keep calm and approach the employee with a supportive attitude.
- 2
Ask them specific questions to understand what they are struggling with.
- 3
Offer to demonstrate how to use the baling machine effectively.
- 4
Encourage them to practice under supervision until they feel more confident.
- 5
Follow up later to see if they need any more help or guidance.
Example Answers
I would first approach the new employee calmly and ask what specific issues they are having with the baling machine. Then, I would demonstrate how to operate the machine and suggest they try it while I supervise to ensure they're comfortable.
How would you manage your workspace to ensure optimal productivity and safety?
How to Answer
- 1
Keep the workspace organized with designated areas for each task.
- 2
Regularly inspect and maintain equipment to prevent hazards.
- 3
Ensure all safety protocols are clearly posted and followed.
- 4
Use proper storage solutions for materials to avoid clutter.
- 5
Implement a routine for cleaning and tidying up at the end of each shift.
Example Answers
I would organize my workspace by having specific areas for loading, baling, and material storage. This helps keep things clear and efficient. I would also check equipment daily and follow all safety guidelines posted around the area.
How would you encourage teamwork among new and experienced staff in a baling operation?
How to Answer
- 1
Foster an inclusive environment where everyone's ideas are valued
- 2
Organize mentorship programs pairing new and experienced staff
- 3
Create team goals that require collaboration to achieve
- 4
Encourage regular team meetings for open communication
- 5
Recognize and reward teamwork and collaboration efforts
Example Answers
I would pair new staff with experienced colleagues in mentorship roles, allowing the former to learn while fostering a supportive team dynamic.
If a client complains about the quality of the bales, how would you address their concerns?
How to Answer
- 1
Listen actively to the client's concerns without interrupting.
- 2
Acknowledge the issue and express understanding of their frustration.
- 3
Ask specific questions to clarify the client's experience with the bales.
- 4
Propose a solution or improvement plan, and set a timeframe for follow-up.
- 5
Thank the client for their feedback and assure them of your commitment to quality.
Example Answers
I would first listen carefully to the client's specific issues regarding the bales. Then, I would acknowledge their concerns and clarify the details before suggesting an inspection or possible improvements.
If you see a way to reduce waste in your process, what steps would you take to implement your idea?
How to Answer
- 1
Identify specific areas where waste occurs
- 2
Gather data and assess the impact of the waste
- 3
Propose a clear, actionable plan to reduce waste
- 4
Communicate your idea to the team
- 5
Monitor the results and adjust as necessary
Example Answers
I would first observe the entire baling process to pinpoint where waste happens. Then I would collect data to understand the volume of waste produced. Next, I’d suggest a modification to the packing process to minimize leftover material. After presenting this to my team and getting their input, I’d implement it and measure the results to ensure effectiveness.
If you disagree with a team member about how to organize a work shift, how would you address this issue?
How to Answer
- 1
Listen actively to the team member's perspective.
- 2
Express your concerns clearly and respectfully.
- 3
Suggest a collaborative discussion to find a compromise.
- 4
Refer to past successful strategies or data when suitable.
- 5
Focus on the team's goal and how your solution meets it.
Example Answers
I would start by listening to my team member's point of view to understand their reasoning. Then, I would share my concerns and suggest we discuss both our ideas together to find a solution that works for everyone. Ultimately, I believe it's important to keep our team's objectives in mind.
Don't Just Read Cloth Baler Questions - Practice Answering Them!
Reading helps, but actual practice is what gets you hired. Our AI feedback system helps you improve your Cloth Baler interview answers in real-time.
Personalized feedback
Unlimited practice
Used by hundreds of successful candidates
If a baling machine stops working mid-operation, what steps would you take to troubleshoot the issue?
How to Answer
- 1
Check for error messages or indicators on the control panel
- 2
Inspect the power supply and connections for any issues
- 3
Look for physical blockages in the machine or jams in the material
- 4
Examine the main components such as cylinders or belts for wear or damage
- 5
Refer to the machine's manual for specific troubleshooting steps
Example Answers
First, I would check the control panel for any error messages or alerts. Then, I would inspect the power supply and connections to ensure everything is functioning. Next, I'd look for any blockages in the baling area that could be causing the issue.
Technical Interview Questions
How have you used data or metrics to improve the production or efficiency of your previous work?
How to Answer
- 1
Identify specific metrics or data points you regularly monitored.
- 2
Describe a particular situation where data analysis led to a change.
- 3
Explain the actions you took based on the data and the results achieved.
- 4
Be clear about your role in the process of using data.
- 5
Keep your answer focused on measurable improvements.
Example Answers
In my previous role, I tracked the downtime of machines weekly. By analyzing this data, I identified that machine XYZ had the most downtime due to maintenance issues. I proposed a new preventive maintenance schedule, which led to a 20% increase in production efficiency over three months.
Don't Just Read Cloth Baler Questions - Practice Answering Them!
Reading helps, but actual practice is what gets you hired. Our AI feedback system helps you improve your Cloth Baler interview answers in real-time.
Personalized feedback
Unlimited practice
Used by hundreds of successful candidates
What is your experience with diagnosing mechanical failures in baling equipment?
How to Answer
- 1
Start with your background in mechanical systems related to baling.
- 2
Mention specific types of balers you have worked on.
- 3
Describe a particular incident where you diagnosed a failure.
- 4
Highlight the tools and methods you used for diagnosis.
- 5
Emphasize your ability to troubleshoot and resolve issues quickly.
Example Answers
I have 5 years of experience working with both vertical and horizontal balers. Once, I noticed a baler was jamming frequently. I used a vibration analysis tool to pinpoint the misalignment in the press mechanism and adjusted it, which solved the problem.
What specific characteristics do you believe are crucial for creating high-quality bales?
How to Answer
- 1
Focus on material selection and its impact on quality
- 2
Emphasize the importance of moisture control
- 3
Mention the role of proper compression techniques
- 4
Discuss the need for consistent bale size and weight
- 5
Highlight the significance of proper packaging for storage
Example Answers
High-quality bales mainly rely on selecting clean, dry materials, as excess moisture can lead to mold. Proper compression ensures tight bales that are easier to store and transport effectively.
What types of baling methods are you familiar with? Which do you prefer and why?
How to Answer
- 1
Identify specific baling methods you have experience with, such as hydraulic or mechanical balers.
- 2
Explain your preferred method and provide reasoning based on efficiency, ease of use, and material type.
- 3
Mention any unique features of your preferred method that make it advantageous.
- 4
Stay concise but include examples from your experience if relevant.
- 5
Conclude with how your choice impacts productivity or workplace safety positively.
Example Answers
I am familiar with hydraulic and mechanical baling methods. I prefer hydraulic balers because they are more efficient for compacting larger volumes of materials, especially in textile recycling. Their integration with conveyor systems also enhances workflow and reduces manual labor.
What types of machines have you operated in a baling or recycling operation?
How to Answer
- 1
List specific machines you have experience with
- 2
Mention the types of materials handled by those machines
- 3
Highlight your familiarity with safety procedures
- 4
Discuss any maintenance or troubleshooting experience
- 5
Emphasize your ability to adapt to new machinery
Example Answers
I have operated hydraulic balers and cardboard balers, primarily handling cardboard and plastics. I also have experience in ensuring safety checks before operation.
Can you explain the different types of materials that can be baled and how their properties affect the baling process?
How to Answer
- 1
Identify key materials commonly baled such as textiles, paper, plastics, and metals.
- 2
Describe the properties of each material, focusing on density, moisture content, and elasticity.
- 3
Mention how these properties influence the choice of baling equipment and techniques.
- 4
Explain the significance of proper material sorting before baling.
- 5
Conclude with the importance of understanding material properties for maximizing efficiency.
Example Answers
There are several types of materials that can be baled, including textiles, paper, plastics, and metals. Textiles are often lighter and may need moisture control to prevent mold. Paper is generally denser and compresses well. Plastics have different properties based on type, affecting how tightly they can be baled. Metals are heavy and rigid, requiring strong machinery. Understanding these properties helps in selecting the right equipment for efficient baling.
What routine maintenance tasks do you think are essential for ensuring baling equipment operates efficiently?
How to Answer
- 1
Emphasize cleaning and removing debris from the baler regularly
- 2
Check and adjust tension on belts and chains as needed
- 3
Inspect hydraulic fluid levels and replace filters periodically
- 4
Lubricate moving parts to minimize wear and improve efficiency
- 5
Conduct regular inspections for wear and tear on components
Example Answers
I believe essential tasks include regularly cleaning the baler to prevent jams, adjusting the tension on the belts, and checking the hydraulic fluid levels to ensure smooth operation.
What safety measures do you take when working with hydraulic balers?
How to Answer
- 1
Always wear appropriate personal protective equipment such as gloves and safety glasses.
- 2
Make sure to understand and follow the manufacturer's safety instructions before operating the baler.
- 3
Check the hydraulic system for any leaks or malfunctions before use.
- 4
Never attempt to clear a jam while the baler is in operation.
- 5
Keep the area around the baler clean and free of obstructions.
Example Answers
I always wear my gloves and safety glasses when operating the baler. I also ensure I read the safety manual beforehand and check for any leaks in the hydraulic system.
How do you determine the optimal size and weight for a finished bale?
How to Answer
- 1
Understand the specifications required by the processing facility.
- 2
Consider the type of materials being baled and their density.
- 3
Ensure the size and weight allow for easy handling and transport.
- 4
Evaluate the baling machine's capacity and settings.
- 5
Adjust based on feedback from shipping and storage conditions.
Example Answers
I first check the receiving specifications from our facility to understand the required size and weight. Then, I analyze the density of the materials being baled and adjust the press settings to achieve the optimal weight that fits our transportation capabilities.
Don't Just Read Cloth Baler Questions - Practice Answering Them!
Reading helps, but actual practice is what gets you hired. Our AI feedback system helps you improve your Cloth Baler interview answers in real-time.
Personalized feedback
Unlimited practice
Used by hundreds of successful candidates
What steps do you take to ensure the quality of the bales produced meets industry standards?
How to Answer
- 1
Start with regular inspections of raw materials before processing
- 2
Implement consistent compression techniques to achieve uniform density
- 3
Conduct quality checks on finished bales for size, weight, and integrity
- 4
Maintain proper maintenance of baler equipment to avoid malfunctions
- 5
Document all quality control procedures for traceability and compliance
Example Answers
I begin by inspecting the raw materials to ensure they are clean and suitable for baling. During the baling process, I apply consistent compression techniques to maintain uniformity. After bales are produced, I conduct weight and size checks to confirm they meet specifications.
Cloth Baler Position Details
Related Positions
- Cloth Spreader
- Clothier
- Wool Carder
- Textile Machine Operator
- Textile Worker
- Cloth Hand
- Wool Cleaner
- Cotton Opener
- Wool Scourer
- Folding Machine Operator
Similar positions you might be interested in.
Ace Your Next Interview!
Practice with AI feedback & get hired faster
Personalized feedback
Used by hundreds of successful candidates
Ace Your Next Interview!
Practice with AI feedback & get hired faster
Personalized feedback
Used by hundreds of successful candidates