Top 30 Cotton Opener Interview Questions and Answers [Updated 2025]
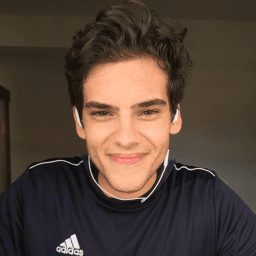
Andre Mendes
•
March 30, 2025
Preparing for an interview as a Cotton Opener? Our latest post is your go-to resource for the most common questions you might encounter. We provide insightful example answers and practical tips to help you respond with confidence and clarity. Whether you're new to the field or a seasoned professional, this guide is designed to help you ace your interview and secure that coveted position.
Download Cotton Opener Interview Questions in PDF
To make your preparation even more convenient, we've compiled all these top Cotton Openerinterview questions and answers into a handy PDF.
Click the button below to download the PDF and have easy access to these essential questions anytime, anywhere:
List of Cotton Opener Interview Questions
Behavioral Interview Questions
Can you describe a time when you had to work closely with your team to ensure the quality of cotton processing?
How to Answer
- 1
Choose a specific project or time when teamwork was essential.
- 2
Highlight your role and contributions to the team effort.
- 3
Discuss communication methods used within the team.
- 4
Mention the outcome, focusing on the quality improvement achieved.
- 5
Reflect on what you learned from the experience.
Example Answers
In my previous role, we had a project to improve cotton cleaning processes. I collaborated closely with the team, helping to ensure everyone understood the new protocols. We held daily check-ins to monitor progress and quality. As a result, we reduced impurities by 15%. I learned the value of clear communication in achieving our goals.
Tell me about a significant challenge you faced while operating cotton opening machinery and how you overcame it.
How to Answer
- 1
Identify a specific challenge related to cotton opening machinery.
- 2
Explain the impact this challenge had on your work performance.
- 3
Describe the steps you took to overcome the challenge.
- 4
Highlight any improvements or lessons learned from the experience.
- 5
Keep your answer concise and focused on your actions and outcomes.
Example Answers
During my time operating cotton opening machinery, I faced the challenge of frequent jams due to inconsistent cotton quality. I analyzed the problem and realized that adjusting the feed parameters could help. After implementing a new feeding technique, the jams significantly reduced, improving our throughput by 25%.
Don't Just Read Cotton Opener Questions - Practice Answering Them!
Reading helps, but actual practice is what gets you hired. Our AI feedback system helps you improve your Cotton Opener interview answers in real-time.
Personalized feedback
Unlimited practice
Used by hundreds of successful candidates
Give an example of when you noticed a process inefficiency in cotton opening and took action to improve it.
How to Answer
- 1
Identify a specific inefficiency you noticed during cotton opening.
- 2
Describe the impact of this inefficiency on productivity or quality.
- 3
Explain the steps you took to address the issue.
- 4
Highlight the outcome of your actions and any metrics that show improvement.
- 5
Keep your answer focused on your contribution and the results achieved.
Example Answers
In my last role, I observed that the cotton fibers were often tangled during the opening process, slowing down production. I researched methods to improve the feeding mechanism and proposed a new setup that reduced tangling. After implementing this change, we saw a 20% increase in throughput.
Describe a situation where you had to communicate a safety concern regarding machinery to your supervisor.
How to Answer
- 1
Be specific about the machinery involved.
- 2
Describe the safety concern clearly and objectively.
- 3
Explain how you communicated the issue to your supervisor.
- 4
Mention any actions taken after reporting the concern.
- 5
Highlight the importance of safety culture in the workplace.
Example Answers
During a routine check on the cotton opener, I noticed that the safety guards were missing on one of the belts. I immediately reported this to my supervisor by stating the specific issue and the potential risks. As a result, the machine was shut down until the guards were replaced.
Can you describe a time when you had to lead a team in a challenging situation during cotton processing?
How to Answer
- 1
Identify a specific challenge related to cotton processing.
- 2
Describe your role in leading the team during this challenge.
- 3
Highlight your problem-solving skills and decision-making process.
- 4
Mention the outcome and any learned lessons.
- 5
Keep your response focused and relevant to cotton processing.
Example Answers
In one instance, our cotton processing line faced a machinery breakdown during peak season. I quickly assessed the situation, organized a team meeting to delegate responsibilities, and we worked together to troubleshoot the issue. As a result, we minimized downtime and caught up on our production schedule by the end of the week.
Tell me about a time you trained or onboarded a new employee on cotton opener equipment.
How to Answer
- 1
Begin with a specific situation that highlights your experience.
- 2
Describe the training methods you used, such as hands-on training or instructional materials.
- 3
Emphasize the outcome of the training and how it benefited the team or company.
- 4
Share feedback from the new employee to showcase the effectiveness of your training.
- 5
Conclude with what you learned from the experience that could improve future onboarding.
Example Answers
In my previous role, I trained a new technician on the cotton opener equipment by first walking them through the machinery and its components. We then moved to hands-on training where they operated the machine under my guidance. This led to them quickly becoming proficient and reducing downtime by 20%. They mentioned feeling confident in their abilities due to my structured approach.
What has been the most challenging aspect of being a cotton opener in your previous experience?
How to Answer
- 1
Identify a real challenge you faced in previous roles.
- 2
Explain how it affected your work or the team.
- 3
Discuss the steps you took to overcome this challenge.
- 4
Highlight what you learned from the experience.
- 5
Connect the challenge to skills relevant to the position.
Example Answers
One of the most challenging aspects was managing the cotton's moisture levels. During peak season, fluctuations made it hard to maintain quality. I implemented a better monitoring system, which improved quality consistency and taught me the importance of adaptability in production.
Provide an example of how you improved the efficiency of your work in a previous job related to cotton processing.
How to Answer
- 1
Identify a specific task where you found inefficiencies
- 2
Explain the actions you took to improve the process
- 3
Quantify the results of your improvements if possible
- 4
Use clear and specific language
- 5
Focus on your role and contributions in the process
Example Answers
In my previous role at a cotton processing plant, I noticed that the manual sorting of cotton fibers slowed down production. I proposed an automated sorting system that reduced sorting time by 30%. As a result, we increased overall output without additional labor costs.
Describe a time when you received constructive feedback about your work. How did you respond?
How to Answer
- 1
Choose a specific instance where feedback was given.
- 2
Explain the feedback you received and who it came from.
- 3
Describe your initial reaction to the feedback.
- 4
Outline the steps you took to implement the feedback.
- 5
Share the positive outcome or what you learned from the experience.
Example Answers
In my previous role, my supervisor pointed out that I needed to improve my time management skills after missing some deadlines. Initially, I felt disappointed, but I took this feedback seriously. I started using a project management tool to better track my tasks and deadlines. As a result, my timely submissions improved, and I received positive feedback on my enhanced productivity.
Don't Just Read Cotton Opener Questions - Practice Answering Them!
Reading helps, but actual practice is what gets you hired. Our AI feedback system helps you improve your Cotton Opener interview answers in real-time.
Personalized feedback
Unlimited practice
Used by hundreds of successful candidates
Technical Interview Questions
What types of cotton opener machines have you operated, and what are the key features of each?
How to Answer
- 1
Identify the specific cotton opener machines you have experience with.
- 2
Explain the operation process and key features of each machine clearly.
- 3
Highlight any unique aspects or advantages of the machines you mention.
- 4
Mention your level of proficiency with each machine and any relevant achievements.
- 5
Be prepared to discuss any challenges encountered and how you resolved them.
Example Answers
I have operated the Ginning Cotton Opener, which features a high throughput capacity and efficient seed removal, enhancing the quality of cotton. My proficiency in adjusting the settings improved the output significantly.
How do you ensure the cotton quality during the opening process?
How to Answer
- 1
Monitor humidity and temperature regularly in the facility
- 2
Use calibrated equipment for precise measurement
- 3
Conduct visual inspections of cotton to identify any contamination
- 4
Implement a quality control checklist for each batch opened
- 5
Train staff on best practices for handling cotton
Example Answers
I ensure cotton quality by regularly monitoring the humidity and temperature in the opening area to maintain optimal conditions. Additionally, I conduct visual inspections for contamination and utilize calibrated equipment for accurate measurements.
Don't Just Read Cotton Opener Questions - Practice Answering Them!
Reading helps, but actual practice is what gets you hired. Our AI feedback system helps you improve your Cotton Opener interview answers in real-time.
Personalized feedback
Unlimited practice
Used by hundreds of successful candidates
What safety protocols do you follow while operating cotton opening machines?
How to Answer
- 1
Always wear appropriate personal protective equipment like gloves and safety goggles.
- 2
Conduct pre-operation checks to ensure the machine is in safe working order.
- 3
Keep the work area clean and free from clutter to prevent accidents.
- 4
Be aware of emergency shut-off procedures in case of malfunction.
- 5
Maintain a safe distance from moving parts while operating the machine.
Example Answers
I always wear gloves and goggles to protect myself while operating the cotton opening machine. Additionally, I ensure that the machine is thoroughly checked before I start to make sure everything is functioning properly.
Can you explain how you use data to monitor the efficiency and performance of opening machines?
How to Answer
- 1
Identify key performance metrics relevant to opening machines.
- 2
Explain how you collect and analyze data regularly.
- 3
Discuss how data influences operational decisions.
- 4
Provide an example where data led to performance improvement.
- 5
Mention any software or tools you use for data analysis.
Example Answers
I monitor the efficiency of opening machines by tracking metrics like throughput and downtime. I collect this data using machine sensors and analyze it weekly. For instance, I noticed our downtime increased due to a specific maintenance delay, and I adjusted our schedule to prevent this issue.
What do you know about the differing fiber properties of cotton types and how they affect the opening process?
How to Answer
- 1
Identify common types of cotton such as Upland, Pima, and Egyptian.
- 2
Describe key fiber properties like length, strength, and fineness.
- 3
Explain how fiber properties influence the efficiency of the opening process.
- 4
Mention the impact of moisture content on cotton fiber during opening.
- 5
Connect your knowledge to practical implications in a cotton opener's work.
Example Answers
I know that Upland cotton is shorter and coarser compared to Pima, which is longer and stronger. These properties mean that Upland cotton may require more energy to open, whereas Pima can be opened more efficiently.
How do you calibrate or adjust cotton opening machines for different batches of cotton?
How to Answer
- 1
Identify key cotton characteristics such as moisture, color, and fiber length.
- 2
Adjust opening speed based on the batch's fiber quality to avoid damage.
- 3
Calibrate blend ratios to ensure consistent output with mixed cotton types.
- 4
Regularly monitor and record machine settings for optimal performance.
- 5
Conduct tests with small sample batches before full production runs.
Example Answers
I start by assessing the specific characteristics of the cotton batch, like moisture content and fiber length. Based on that, I adjust the opening speed to prevent fiber breakage and set the blend ratios if using multiple types.
How do you prepare raw cotton for the opening process?
How to Answer
- 1
Inspect cotton bales for moisture and quality before processing
- 2
Ensure cotton is free of contaminants like leaves and trash
- 3
Loosen bales using appropriate equipment to separate fibers
- 4
Feed the cotton into the opening machine evenly to prevent jams
- 5
Monitor the opening process to maintain a consistent flow of fiber
Example Answers
I start by inspecting the cotton bales for any moisture issues and contaminants. Then I loosen the bales carefully to separate the fibers before feeding them into the opening machine evenly.
How familiar are you with modern technologies used in cotton processing?
How to Answer
- 1
Research current technologies in cotton processing such as Ginning, HVI testing, and automation.
- 2
Mention any specific equipment or software you have experience with or knowledge of.
- 3
Highlight the importance of efficiency and sustainability in modern processing technology.
- 4
Show enthusiasm for new advancements in the field.
- 5
Relate your experience or education to these technologies to illustrate familiarity.
Example Answers
I am quite familiar with modern cotton processing technologies, especially HVI testing for fiber quality. I have worked with automated ginning systems that increase efficiency and reduce waste.
What steps do you take to troubleshoot when a cotton opener machine is not performing as expected?
How to Answer
- 1
Check the machine settings for compliance with operational standards
- 2
Inspect for any visible blockages or maintenance needed in the feeding area
- 3
Review and analyze any error messages or indicators from the control panel
- 4
Clean or replace any worn or damaged parts affecting performance
- 5
Run a test cycle after adjustments to ensure the issue has been resolved
Example Answers
First, I check the machine settings to ensure they match operational requirements. Then, I inspect the feeding area for any blockages. If there are any error messages, I review those next. I also make sure to clean any components that may need it, and finally, I run a test cycle to confirm everything is working well.
What routine maintenance procedures do you follow for cotton opening machinery?
How to Answer
- 1
Identify key components that need regular checks such as blades, belts, and rollers.
- 2
Schedule daily, weekly, and monthly maintenance tasks to ensure consistent performance.
- 3
Always clean machinery after use to prevent buildup of cotton and debris.
- 4
Use the manufacturer's guidelines for lubrication points and intervals.
- 5
Document maintenance activities to track issues and improvements over time.
Example Answers
I ensure that I check the blades and belts daily for wear and tear. I also clean the machinery thoroughly after every shift to avoid any buildup.
Don't Just Read Cotton Opener Questions - Practice Answering Them!
Reading helps, but actual practice is what gets you hired. Our AI feedback system helps you improve your Cotton Opener interview answers in real-time.
Personalized feedback
Unlimited practice
Used by hundreds of successful candidates
Situational Interview Questions
If you notice a colleague not following safety procedures while operating cotton machinery, how would you handle the situation?
How to Answer
- 1
Address the issue immediately but calmly
- 2
Use 'I' statements to express concern
- 3
Suggest a safer alternative if possible
- 4
Encourage them to follow safety procedures for their own protection
- 5
If necessary, report the behavior to a supervisor
Example Answers
I would approach my colleague and say, 'I noticed you weren't wearing your safety gear while operating the cotton machine. I'm concerned for your safety. Can we make sure to follow all procedures together?'
What steps would you take if you discovered that the opened cotton did not meet the quality standards?
How to Answer
- 1
Immediately assess the extent of the quality issue.
- 2
Document the findings clearly before taking further actions.
- 3
Inform the relevant supervisors and quality control team.
- 4
Implement corrective measures to the faulty batch.
- 5
Re-evaluate quality checks to prevent future occurrences.
Example Answers
I would first assess how severe the quality issue is and document the specific problems. Then, I would notify my supervisor and the quality control team. Next, I'd work on corrective measures for the batch and review our quality checks to ensure we avoid this in the future.
Don't Just Read Cotton Opener Questions - Practice Answering Them!
Reading helps, but actual practice is what gets you hired. Our AI feedback system helps you improve your Cotton Opener interview answers in real-time.
Personalized feedback
Unlimited practice
Used by hundreds of successful candidates
How would you respond if a critical piece of opening equipment failed during peak operation hours?
How to Answer
- 1
Stay calm and assess the situation quickly
- 2
Communicate the issue to your team immediately
- 3
Implement contingency plans or backup procedures
- 4
Prioritize safety for all personnel
- 5
Document the incident for future reference
Example Answers
If a critical piece of equipment failed, I would first assess the severity and impact on operations. Then, I would inform my team to ensure everyone is aware of the situation. I'd activate our contingency plan to minimize downtime, while keeping safety a priority. After stabilizing the situation, I'd document the issue for review.
Imagine you have a disagreement with a team member about the best way to open cotton. How would you resolve this conflict?
How to Answer
- 1
Listen actively to your team member's perspective without interrupting
- 2
Share your viewpoint clearly and calmly, focusing on facts
- 3
Identify common goals and interests to find shared ground
- 4
Consider proposing a trial of both methods to see which works better
- 5
Follow up after resolving the disagreement to ensure ongoing collaboration
Example Answers
I would listen carefully to my team member's approach on how to open cotton, ensuring I understand their reasoning. Then, I would share my method, highlighting any advantages. Together, we could assess our goals and possibly try both methods to see which one yields better results.
If you were asked to improve the efficiency of the cotton opening process, what steps would you take?
How to Answer
- 1
Analyze current process workflows to identify bottlenecks
- 2
Research and implement new technology such as automated opening machines
- 3
Train staff on best practices for operating equipment
- 4
Regularly review and adjust procedures based on performance data
- 5
Collaborate with suppliers for better raw cotton quality
Example Answers
I would start by mapping out the current workflow to pinpoint delays or inefficiencies. Then, I would explore automated cotton opening machines that can increase speed and reduce labor costs. Training the team on best practices would also be crucial to ensure everyone is skilled in using the equipment effectively.
What would you do if there was an emergency due to a machinery malfunction during cotton processing?
How to Answer
- 1
Stay calm and assess the situation quickly
- 2
Initiate emergency shut down procedures if safe
- 3
Communicate with team members immediately
- 4
Follow safety protocols and check for injuries
- 5
Inform the maintenance team and document the incident
Example Answers
In an emergency due to machinery malfunction, I would stay calm and quickly assess the situation to determine if I need to initiate emergency shut down procedures. I would communicate the issue to my team and ensure everyone's safety, following established safety protocols, and then inform the maintenance team to address the malfunction.
If you have to choose between maintaining quality and increasing output, how would you prioritize?
How to Answer
- 1
Evaluate the impact of both quality and output on the overall production goals.
- 2
Consider scenarios where quality impacts customer satisfaction or product returns.
- 3
Discuss your approach to finding a balance rather than a strict choice.
- 4
Mention the importance of teamwork and communication in executing either priority.
- 5
Share a relevant experience where you had to make a similar decision.
Example Answers
I believe maintaining quality should be the priority because poor quality can lead to customer dissatisfaction and increased costs in the long run. However, I would explore ways to optimize processes that could allow both quality and output to improve together.
If your team is falling behind schedule, what actions would you take to help get back on track?
How to Answer
- 1
Assess the current status of the project and identify specific bottlenecks.
- 2
Communicate with the team to gather input on challenges they are facing.
- 3
Prioritize tasks based on urgency and importance to realign the schedule.
- 4
Consider reallocating resources or adjusting timelines if necessary.
- 5
Keep stakeholders informed of changes and progress to maintain transparency.
Example Answers
First, I would assess the current project status to identify where we are falling behind. I'd then communicate with the team to understand the challenges and barriers they are facing. Once I gather this information, I would prioritize tasks to ensure that we focus on the most critical issues and may reallocate resources if needed. Finally, I would update stakeholders on our progress and any adjustments we are making to the timeline.
How would you handle a situation where customer requirements for cotton quality are higher than the current output levels?
How to Answer
- 1
Assess the current quality levels and identify gaps to understand customer expectations
- 2
Communicate openly with the customer about the current capabilities and timeline for improvement
- 3
Develop an action plan to enhance the quality, which could include training staff or investing in better equipment
- 4
Set realistic goals and timelines to meet customer requirements, keeping them informed throughout the process
- 5
Seek feedback from the customer post-implementation to ensure that their requirements are being met and to build trust.
Example Answers
I would start by reviewing the current cotton quality and comparing it with the customer's standards. Then, I would discuss openly with them about what is achievable and create a plan to enhance our processes to meet their needs over time. This way, we can manage expectations while working towards improvement.
How would you plan your day to ensure all tasks related to cotton opening are completed on time?
How to Answer
- 1
Start the day with a clear checklist of tasks related to cotton opening.
- 2
Prioritize tasks based on their deadlines and importance.
- 3
Allocate specific time slots for each task within the working hours.
- 4
Regularly check progress throughout the day to stay on track.
- 5
Communicate with team members if assistance or adjustments are needed.
Example Answers
I would begin my day by creating a checklist of all cotton opening tasks. I would prioritize tasks that need to be completed first. Then, I would set specific time allocations for each task, like dedicating the first hour to sorting and the next two hours for cleaning equipment. I would check my progress midday and adjust if needed.
Don't Just Read Cotton Opener Questions - Practice Answering Them!
Reading helps, but actual practice is what gets you hired. Our AI feedback system helps you improve your Cotton Opener interview answers in real-time.
Personalized feedback
Unlimited practice
Used by hundreds of successful candidates
Cotton Opener Position Details
Related Positions
- Cloth Baler
- Cloth Spreader
- Textile Machine Operator
- Wool Carder
- Wool Cleaner
- Rope Maker
- Folding Machine Operator
- Wool Scourer
- Textile Worker
- Button Puncher
Similar positions you might be interested in.
Ace Your Next Interview!
Practice with AI feedback & get hired faster
Personalized feedback
Used by hundreds of successful candidates
Ace Your Next Interview!
Practice with AI feedback & get hired faster
Personalized feedback
Used by hundreds of successful candidates