Top 30 Folding Machine Operator Interview Questions and Answers [Updated 2025]
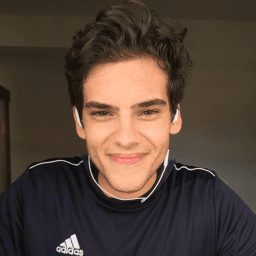
Andre Mendes
•
March 30, 2025
Preparing for a folding machine operator interview? This blog post is your ultimate guide, featuring the most common questions you might encounter for this role. Dive into expertly crafted example answers and insightful tips on how to respond effectively, ensuring you stand out as a top candidate. Get ready to enhance your interview skills and boost your confidence with our comprehensive resource.
Download Folding Machine Operator Interview Questions in PDF
To make your preparation even more convenient, we've compiled all these top Folding Machine Operatorinterview questions and answers into a handy PDF.
Click the button below to download the PDF and have easy access to these essential questions anytime, anywhere:
List of Folding Machine Operator Interview Questions
Behavioral Interview Questions
Can you describe a time when you identified a safety hazard in the workplace? What actions did you take?
How to Answer
- 1
Think of a specific incident where you spotted a safety issue.
- 2
Describe the hazard clearly and its potential risks.
- 3
Detail the steps you took to address the hazard immediately.
- 4
Mention any communication with supervisors or colleagues regarding the issue.
- 5
Conclude with the outcome or improvements made after your actions.
Example Answers
In my previous job, I noticed that a conveyor belt was not fully covered, exposing employees to moving parts. I immediately reported it to my supervisor and we placed barriers to prevent access. After the barriers were installed, we conducted a team meeting to reiterate safety measures. The area has been safe since then.
Tell me about a time you worked on a team to meet production goals. What was your role, and how did you contribute?
How to Answer
- 1
Choose a specific team project you were part of.
- 2
Clearly state your role in the team and your responsibilities.
- 3
Highlight specific contributions you made that helped meet the goals.
- 4
Mention any challenges faced and how the team overcame them.
- 5
Conclude with the outcome and what you learned from the experience.
Example Answers
In my previous job at XYZ Manufacturing, I was part of a team responsible for increasing the output of our folding machines. As the lead operator, I streamlined the workflow by organizing the machine setup and training new team members. We faced a challenge with equipment downtime, but I suggested a preventive maintenance schedule that reduced delays significantly. As a result, we exceeded our production target by 15% that quarter and I learned the importance of proactive communication and collaboration.
Don't Just Read Folding Machine Operator Questions - Practice Answering Them!
Reading helps, but actual practice is what gets you hired. Our AI feedback system helps you improve your Folding Machine Operator interview answers in real-time.
Personalized feedback
Unlimited practice
Used by hundreds of successful candidates
Describe a situation where you encountered a mechanical issue with a folding machine. How did you troubleshoot it?
How to Answer
- 1
Start with a clear description of the mechanical issue.
- 2
Explain the steps you took to diagnose the problem.
- 3
Mention any tools or resources you used in troubleshooting.
- 4
Talk about how you resolved the issue and any adjustments made.
- 5
Conclude with the outcome and what you learned from the experience.
Example Answers
During a production run, I noticed the folding machine was not folding correctly. I first stopped the machine and observed the mechanism, identifying that a guide was misaligned. I used a wrench to adjust the guide back into position, tested the machine with scrap paper, and confirmed it was working properly. The issue was resolved, and I learned the importance of regular checks.
Can you give an example of a time when you had to adjust to a change in production processes? How did you handle it?
How to Answer
- 1
Reflect on a specific situation where a process changed
- 2
Explain the change clearly and how it affected your work
- 3
Describe your thought process and steps taken to adapt
- 4
Highlight any support or resources you used to adjust
- 5
Conclude with the positive outcome of your adjustment
Example Answers
In my previous job, the company switched from manual folding to an automated folding machine. I took the initiative to learn the new machine by attending a training session and watching instructional videos. I also collaborated with colleagues to share knowledge. This adaptation led to increased production efficiency and reduced errors.
How do you prioritize tasks when facing multiple deadlines on the production line?
How to Answer
- 1
Assess the urgency of each task based on deadlines and production needs
- 2
Communicate with team members about workload and priorities
- 3
Use a checklist to track progress on each task
- 4
Stay flexible and be ready to adjust priorities as situations change
- 5
Focus on completing critical tasks that impact production flow first
Example Answers
I prioritize tasks by first assessing their deadlines and production impact. I make a checklist to track my progress and talk with my team to ensure we're aligned on what needs to be done first. This way, I can focus on critical tasks that keep the production line moving smoothly.
Can you talk about a time when you had to learn to operate a new machine? What was your approach?
How to Answer
- 1
Identify a specific machine and situation you faced.
- 2
Describe the steps you took to learn the machine.
- 3
Mention any resources you used, such as manuals or training sessions.
- 4
Explain any challenges you encountered and how you overcame them.
- 5
Conclude with the outcome and what you learned from the experience.
Example Answers
At my previous job, I was assigned to operate a new packaging machine. I first reviewed the operation manual thoroughly before attempting to use it. I then shadowed a seasoned operator for a few hours to observe best practices. After a day of practice, I faced challenges with the machine jamming, but I quickly consulted troubleshooting guides and resolved the issue, which improved my confidence and efficiency.
Describe an instance where you improved the efficiency of the folding process. What changes did you implement?
How to Answer
- 1
Identify a specific situation where you noticed inefficiency.
- 2
Explain the analysis you conducted to understand the problem.
- 3
Describe the solution you implemented in detail.
- 4
Share the measurable results or improvements from your changes.
- 5
Keep it concise and focus on your role in the process.
Example Answers
In my previous job, I noticed the folding machine often jammed, slowing down production. I analyzed the process and found that improper loading was the cause. I trained the team on correct loading techniques and adjusted the machine settings. As a result, we reduced downtime by 30%.
Tell me about a time when you had to communicate complex instructions to your team. How did you ensure clarity?
How to Answer
- 1
Focus on a specific instance where communication was key.
- 2
Explain how you broke down the complex instructions into simpler parts.
- 3
Highlight the methods you used to verify understanding, like asking questions.
- 4
Mention the outcome and how it benefited the team.
- 5
Conclude with any feedback you received that affirmed your communication skills.
Example Answers
In my previous job, I had to train new employees on a complicated folding machine. I divided the instructions into steps, used visual aids, and demonstrated each step. After explaining, I asked each team member to repeat the step back to me, ensuring they understood. This approach led to fewer mistakes and increased productivity.
Have you ever received constructive feedback on your machine operation skills? How did you respond to it?
How to Answer
- 1
Think of a specific instance where you received feedback
- 2
Explain the feedback clearly and objectively
- 3
Describe how you implemented changes based on that feedback
- 4
Share any positive outcomes or improvements that resulted
- 5
Be honest and show a willingness to learn and grow
Example Answers
In my previous job, my supervisor pointed out that I was not maximizing the efficiency of the folding machine. I took that feedback seriously, made adjustments to my workflow, and started monitoring my speed and accuracy more closely. As a result, my output improved by 15%.
What motivates you as a Folding Machine Operator? Can you share an experience that exemplifies this?
How to Answer
- 1
Identify specific aspects of the job that excite you, like precision and efficiency.
- 2
Think of a past experience where your motivation led to a successful outcome.
- 3
Emphasize teamwork if you enjoyed collaborating with others.
- 4
Mention any personal goals, like mastering a new skill related to folding.
- 5
Keep your response concise, focusing on motivations relevant to the role.
Example Answers
I am motivated by the challenge of maintaining high precision in my work as a Folding Machine Operator. For example, at my previous job, I led a team project where we streamlined the folding process, which resulted in a 20% increase in efficiency.
Don't Just Read Folding Machine Operator Questions - Practice Answering Them!
Reading helps, but actual practice is what gets you hired. Our AI feedback system helps you improve your Folding Machine Operator interview answers in real-time.
Personalized feedback
Unlimited practice
Used by hundreds of successful candidates
Technical Interview Questions
What types of folding machines have you operated, and what are their specific functions?
How to Answer
- 1
Identify specific types of folding machines you have experience with.
- 2
Explain the primary functions and features of each machine.
- 3
Mention any relevant technical details like model numbers or brands if applicable.
- 4
Share examples of tasks you completed with these machines.
- 5
Highlight any training or certifications related to operating these machines.
Example Answers
I have operated a Folder 8000 which is used for folding brochures. It can handle paper from 20 lb to 100 lb and has adjustable speed settings. I used it to produce thousands of brochures for a marketing campaign.
What routine maintenance tasks do you perform on a folding machine, and why are they important?
How to Answer
- 1
List specific tasks you perform regularly, such as cleaning or lubrication.
- 2
Explain the purpose of each maintenance task clearly.
- 3
Mention how these tasks contribute to machine longevity and performance.
- 4
Discuss safety aspects related to maintenance procedures.
- 5
Relate maintenance to preventing costly breakdowns or production delays.
Example Answers
I regularly clean the folding machine by removing dust and debris to prevent buildup that can cause malfunctions. Lubrication of moving parts ensures smooth operation and reduces wear and tear, which is crucial for extending the machine's life.
Don't Just Read Folding Machine Operator Questions - Practice Answering Them!
Reading helps, but actual practice is what gets you hired. Our AI feedback system helps you improve your Folding Machine Operator interview answers in real-time.
Personalized feedback
Unlimited practice
Used by hundreds of successful candidates
How do you adjust the settings on a folding machine for different materials and folds?
How to Answer
- 1
Identify the material type and thickness before adjusting settings.
- 2
Consult machine manual for specific recommendations on dial settings.
- 3
Adjust folding guides to match the desired fold type accurately.
- 4
Test different settings with sample materials to ensure quality.
- 5
Monitor output and make final adjustments for precision and consistency.
Example Answers
First, I determine the type and thickness of the material I am using. Then, I refer to the machine manual for recommended settings. After that, I carefully adjust the folding guides to ensure they match the specific fold type required.
What steps do you take to ensure the quality of the folded products?
How to Answer
- 1
Inspect materials before use for defects or inconsistencies
- 2
Calibrate the folding machine regularly to maintain precision
- 3
Implement a quality control checklist for each production run
- 4
Conduct random sampling of finished products to check folds and dimensions
- 5
Document and analyze any defects to improve the process
Example Answers
I start by inspecting all materials to ensure they are of high quality and free from defects. I regularly calibrate the folding machine to guarantee precise folds and use a quality control checklist to track each production run. Additionally, I perform random sampling of the finished products to confirm they meet our specifications.
What are common issues that can occur with folding machines, and how do you resolve them?
How to Answer
- 1
Identify typical problems such as jams, misalignments, or inconsistent folding.
- 2
Explain a specific troubleshooting technique for each issue mentioned.
- 3
Mention the importance of regular maintenance and inspections.
- 4
Provide examples of how you have solved similar issues in past experiences.
- 5
Discuss safety precautions while resolving issues.
Example Answers
Common issues include paper jams, which I resolve by checking for obstructions and adjusting the feeder. Misalignments can occur, and I ensure proper alignment by following calibration procedures. Regular maintenance helps prevent these issues.
What safety protocols do you follow when operating folding machines?
How to Answer
- 1
Always wear appropriate personal protective equipment such as gloves and safety glasses
- 2
Ensure the machine is properly locked out during maintenance or cleaning
- 3
Inspect the machine for any defects or hazards before starting operation
- 4
Follow the manufacturer's instructions for safe operation and emergency procedures
- 5
Keep the work area clean and free of obstructions to maintain mobility and safety
Example Answers
I always wear gloves and safety glasses to protect myself. Before starting the machine, I check for any defects and ensure it's clean and safe to operate.
Can you explain the types of materials you have experience folding and any specific difficulties they present?
How to Answer
- 1
Identify specific materials you have worked with, such as paper, cardboard, or plastic.
- 2
Discuss the characteristics of each material that influence folding, like thickness or texture.
- 3
Mention any challenges you faced, such as precision or consistency in folds.
- 4
Explain how you overcame these challenges, for example, adjusting machine settings.
- 5
Relate your experience to the specific needs of the employer if possible.
Example Answers
I have experience folding lightweight paper and thick cardboard. Thicker materials like cardboard present challenges with precision, but I adjusted the machine's pressure settings to ensure consistent folds.
What do you consider before determining if a folding machine needs repair or if it can be fixed on the spot?
How to Answer
- 1
Assess the machine's symptoms and performance issues carefully.
- 2
Check for obvious signs of damage or wear, such as broken parts.
- 3
Evaluate if the problem is minor and can be handled quickly.
- 4
Consult the machine's manual for troubleshooting guidelines.
- 5
Determine if additional tools or parts are needed for a proper fix.
Example Answers
I first look at the specific issues the machine is exhibiting, checking for any unusual noises or performance drops. If I notice something minor, like a misalignment, I try to adjust it immediately. Otherwise, I check for visible damage or consult the machine's manual.
What is your process for calibrating a folding machine for different production requirements?
How to Answer
- 1
Evaluate the specifications of the job order.
- 2
Adjust the folding die and settings based on material type.
- 3
Test the calibration with sample material before full production.
- 4
Monitor the output for quality and consistency during the run.
- 5
Make adjustments as needed based on feedback.
Example Answers
For each job, I first review the specifications to understand the required folds and material. Then, I adjust the folding die and settings accordingly. I always run a test using sample sheets to ensure everything is calibrated well before starting the full production run.
Have you worked with any software systems to track the operation of folding machines? If so, which ones?
How to Answer
- 1
Mention specific software names you have experience with
- 2
Explain how you used the software in your previous roles
- 3
Highlight any results or improvements due to the software
- 4
If you haven't used specific software, mention your ability to learn new systems quickly
- 5
Be confident in discussing your technical skills
Example Answers
In my previous job, I used the Folders Pro software to monitor and adjust the operation of our folding machines, which enhanced production efficiency by about 15%.
Don't Just Read Folding Machine Operator Questions - Practice Answering Them!
Reading helps, but actual practice is what gets you hired. Our AI feedback system helps you improve your Folding Machine Operator interview answers in real-time.
Personalized feedback
Unlimited practice
Used by hundreds of successful candidates
Situational Interview Questions
If you noticed a colleague consistently making errors with their folding machine operation, how would you address the situation?
How to Answer
- 1
Observe the colleague's operation closely to confirm the errors.
- 2
Choose a private and respectful setting for the discussion.
- 3
Express your observations without sounding accusatory.
- 4
Offer assistance or share useful tips based on your experience.
- 5
Encourage them to ask questions and seek help when needed.
Example Answers
I would first observe my colleague to ensure I understand the errors they are making. Then, I would talk to them privately, describing what I noticed and asking if they need help. I might share some techniques that work for me and encourage them to reach out when they're unsure.
Imagine you are behind on production targets for the day. What strategies would you implement to catch up?
How to Answer
- 1
Assess current production status quickly to identify the gap.
- 2
Communicate with the team to gather input and ideas for improvement.
- 3
Prioritize tasks that will have the highest impact on output.
- 4
Increase efficiency by optimizing machine speed and reducing downtime.
- 5
Consider extending working hours or shifts if necessary and justifiable.
Example Answers
First, I would assess where we are behind and how much we need to catch up. I would then gather the team for a quick meeting to brainstorm solutions. I would focus on prioritizing the most critical tasks and see if we can run the machine at higher speeds without compromising quality.
Don't Just Read Folding Machine Operator Questions - Practice Answering Them!
Reading helps, but actual practice is what gets you hired. Our AI feedback system helps you improve your Folding Machine Operator interview answers in real-time.
Personalized feedback
Unlimited practice
Used by hundreds of successful candidates
What would you do if a folding machine suddenly stopped working during peak production hours?
How to Answer
- 1
Stay calm and assess the situation quickly
- 2
Check the machine for any visible issues such as jams or error messages
- 3
Communicate with your supervisor and the team about the issue
- 4
Attempt basic troubleshooting, but don't risk safety
- 5
If necessary, follow the established protocol to escalate the repair request
Example Answers
I would remain calm and first check if there is a visible jam in the machine. If I don't see any obvious issue, I would notify my supervisor and the team so we can start troubleshooting together.
How would you handle a situation where another operator was struggling with their machine?
How to Answer
- 1
Assess the situation calmly and understand their specific issue.
- 2
Offer to help troubleshoot the problem directly with them.
- 3
Share your own experiences with similar issues to relate.
- 4
Encourage them to take a break if they are frustrated for better focus.
- 5
Suggest asking a supervisor if the problem persists beyond your help.
Example Answers
I would first approach the operator and ask what specifically is causing the struggle. I’d then offer my assistance to troubleshoot together, sharing any similar experiences I have had to help guide them.
If you discover that a batch of folded products does not meet quality standards, what steps would you take?
How to Answer
- 1
Inspect the batch to determine the specific quality issues.
- 2
Isolate the affected products to prevent further processing.
- 3
Document the findings and the nature of the quality failure.
- 4
Report the issue to the supervisor and suggest potential solutions.
- 5
Review the folding process to identify the root cause of the problem.
Example Answers
I would first inspect the batch to identify the specific defects. Next, I'd isolate the non-conforming products and document the issues. Then, I would report it to my supervisor and suggest we check the machine settings.
How would you manage your work if you faced unexpected equipment failures right before a deadline?
How to Answer
- 1
Stay calm and assess the situation quickly
- 2
Identify the specific issue with the equipment
- 3
Communicate with your supervisor and team immediately
- 4
Explore alternative solutions or temporary fixes
- 5
Prioritize tasks and adjust the workflow to meet the deadline
Example Answers
If I faced unexpected equipment failures, I would first remain calm and assess the issue to understand what's wrong. Then, I would inform my supervisor about the situation and discuss potential temporary fixes or alternative solutions. I would also prioritize my remaining tasks to ensure we still meet the deadline as best as possible.
If there is an injury in your working area, what immediate actions would you take?
How to Answer
- 1
Assess the situation quickly and ensure your safety first.
- 2
Call for medical help or alert the supervisor immediately if needed.
- 3
Provide basic first aid if you are trained and it's safe to do so.
- 4
Evacuate the area if necessary to prevent further injuries.
- 5
Document the incident afterward for reporting purposes.
Example Answers
I would first make sure the area is safe for myself and others, then call for medical help while assessing the injury.
You notice that the supplies for your folding machine are running low during your shift. What steps do you take?
How to Answer
- 1
Assess the current supply levels to confirm they are low
- 2
Notify your supervisor about the low supplies immediately
- 3
Check if there are backup supplies stored nearby
- 4
Continue operating the machine if possible, while waiting for a replacement
- 5
Document the incident for future supply planning
Example Answers
First, I would check the supply level to confirm they are running low. Then, I would notify my supervisor right away. If there are backup materials available, I would fetch them to keep the machine running without delays. I would also make sure to document this incident for future reference.
If you realize you have made a mistake in the folding settings after starting production, how would you proceed?
How to Answer
- 1
Stay calm and assess the situation quickly
- 2
Pause the machine to prevent further errors
- 3
Check the settings and identify the mistake
- 4
Adjust the settings correctly based on production requirements
- 5
Communicate the issue to your supervisor and document the change
Example Answers
I would first pause the machine to stop any defective folds. Then I would check the folding settings to confirm the mistake, make the necessary adjustments, and resume production. Finally, I would inform my supervisor of the change and document what happened to ensure clarity.
If you were asked to lead a training session for new operators on best practices, what key points would you cover?
How to Answer
- 1
Start with safety protocols specific to folding machine operations.
- 2
Demonstrate the correct machine setup and maintenance procedures.
- 3
Discuss material handling best practices to ensure quality output.
- 4
Highlight troubleshooting techniques for common issues.
- 5
Emphasize the importance of consistent monitoring during operation.
Example Answers
I would begin by emphasizing the safety protocols, like wearing protective gear and ensuring the area is clear. Then, I'd show them how to set up the machine properly and explain routine maintenance. Next, I would cover how to handle materials to avoid jams and ensure quality. I'd also teach them how to troubleshoot common issues and stress the need to monitor the machine regularly for optimal performance.
Don't Just Read Folding Machine Operator Questions - Practice Answering Them!
Reading helps, but actual practice is what gets you hired. Our AI feedback system helps you improve your Folding Machine Operator interview answers in real-time.
Personalized feedback
Unlimited practice
Used by hundreds of successful candidates
Folding Machine Operator Position Details
Recommended Job Boards
These job boards are ranked by relevance for this position.
Related Positions
- Textile Machine Operator
- Roller Machine Operator
- Towel Folder
- Cloth Baler
- Textile Worker
- Folder Operator
- Cloth Hand
- Roller Operator
- Cloth Spreader
- Flyer Maker
Similar positions you might be interested in.
Ace Your Next Interview!
Practice with AI feedback & get hired faster
Personalized feedback
Used by hundreds of successful candidates
Ace Your Next Interview!
Practice with AI feedback & get hired faster
Personalized feedback
Used by hundreds of successful candidates