Top 33 Cloth Spreader Interview Questions and Answers [Updated 2025]
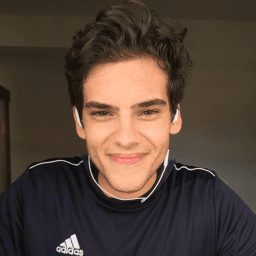
Andre Mendes
•
March 30, 2025
Preparing for a Cloth Spreader interview can be daunting, but we've got you covered with a comprehensive guide to the most common interview questions for this specialized role. In this post, you'll find example answers and insightful tips on how to respond effectively, helping you to stand out as a skilled and confident candidate. Dive in to enhance your interview skills and boost your chances of success!
Download Cloth Spreader Interview Questions in PDF
To make your preparation even more convenient, we've compiled all these top Cloth Spreaderinterview questions and answers into a handy PDF.
Click the button below to download the PDF and have easy access to these essential questions anytime, anywhere:
List of Cloth Spreader Interview Questions
Behavioral Interview Questions
Can you describe a time when you worked closely with a team to accomplish a task related to spreading materials? What was your role?
How to Answer
- 1
Think of a specific project where you collaborated with others to spread materials.
- 2
Mention your specific responsibilities in the team setting.
- 3
Highlight any challenges faced and how the team overcame them.
- 4
Emphasize the outcome of the project and what you learned from the teamwork.
- 5
Be concise and focus on your role rather than the team's overall success.
Example Answers
In my previous role, we worked as a team to spread insulation material in a large warehouse. I was responsible for coordinating with the team to ensure we maintained even coverage. We faced a challenge when we had to adapt to a tight schedule, but by communicating effectively and strategizing, we completed the task two days ahead of time, which taught me the importance of teamwork and adaptability.
Tell me about a challenge you faced while spreading fabric. How did you handle it?
How to Answer
- 1
Identify a specific challenge related to fabric spreading.
- 2
Explain the impact of the challenge on the task at hand.
- 3
Describe the steps you took to resolve the issue.
- 4
Highlight any skills or techniques you utilized.
- 5
Conclude with the positive outcome and what you learned.
Example Answers
Once, I struggled with uneven fabric due to incorrect tension when spreading. I realized the fabric was pulling on one side, impacting the layout. I adjusted the tension and repositioned the fabric, checking it multiple times as I spread it. This ensured an even layout and improved my attention to detail in future tasks.
Don't Just Read Cloth Spreader Questions - Practice Answering Them!
Reading helps, but actual practice is what gets you hired. Our AI feedback system helps you improve your Cloth Spreader interview answers in real-time.
Personalized feedback
Unlimited practice
Used by hundreds of successful candidates
Give an example of a situation where your attention to detail made a significant difference in the quality of your work.
How to Answer
- 1
Think of a specific project or task where precision was crucial.
- 2
Describe the problem you faced and how attention to detail helped solve it.
- 3
Include the result or positive outcome that was achieved due to your attention to detail.
- 4
Use the STAR method: Situation, Task, Action, Result.
- 5
Keep it concise and focus on the impact of your actions.
Example Answers
In my previous job as a textile technician, I was responsible for setting up the cloth spreading machine. During one project, I noticed that the fabric alignment was slightly off. I took the time to adjust the tension and alignment, ensuring the fabric was perfectly straight. This attention to detail resulted in fewer fabric defects and saved the company from additional costs due to waste.
Describe a time when there was a disagreement with a colleague while performing your tasks. How did you resolve it?
How to Answer
- 1
Identify the disagreement clearly and contextually.
- 2
Explain your feelings and perspective on the issue.
- 3
Describe the steps you took to address the disagreement.
- 4
Highlight the resolution and any compromise you reached.
- 5
Emphasize the teamwork and communication skills you used.
Example Answers
In a previous role, a colleague and I disagreed on the speed settings for the cloth spreading machine. I believed a slower speed would result in better quality. I expressed my concerns and we decided to test both settings. After comparing the results, we found a middle speed that worked best for both quality and efficiency, and I learned the value of collaboration.
Tell me about a time you learned a new technique in fabric spreading. How did you implement it?
How to Answer
- 1
Identify a specific technique you learned recently.
- 2
Describe the context and reason for learning it.
- 3
Explain how you implemented the technique in your work.
- 4
Share the outcome or results from using the new technique.
- 5
Reflect on what you gained from this experience.
Example Answers
I recently learned about the pinning technique to prevent shifting during spreading. I practiced it on a batch of silk fabric and found it significantly reduced wrinkles. This led to more efficient cutting and improved fabric utilization.
Give an example of how you've used feedback from supervisors or colleagues to improve your work as a cloth spreader.
How to Answer
- 1
Choose a specific instance of feedback you received.
- 2
Explain how you implemented the feedback into your work.
- 3
Detail the outcome after applying the feedback.
- 4
Keep the example relevant to your role as a cloth spreader.
- 5
Be honest and show how the feedback made a positive impact.
Example Answers
In my last job, my supervisor noticed I was not aligning the fabric pattern correctly. I took their advice and started checking alignment more carefully before cutting. As a result, my accuracy improved significantly, and we reduced fabric waste.
Describe a time when you took initiative to improve the fabric spreading process. What was the outcome?
How to Answer
- 1
Think of a specific instance when you noticed a flaw or inefficiency in the process
- 2
Explain the steps you took to address the issue, demonstrating your problem-solving skills
- 3
Focus on the impact of your initiative: how it benefited the team or the quality of the work
- 4
Use metrics or qualitative results to illustrate the outcome if possible
- 5
Keep your answer structured: Situation, Action, Result (SAR)
Example Answers
In my previous position, I saw that the fabric spreading process was taking too long due to manual measurements. I proposed and implemented a standard measuring guide, which cut the spreading time by 20%, improving overall workflow efficiency.
Can you provide an example of a time when your strong work ethic helped you meet a tight deadline?
How to Answer
- 1
Choose a specific instance from your past work experience.
- 2
Describe the situation and the deadline clearly.
- 3
Explain the steps you took to ensure you met the deadline.
- 4
Highlight how your work ethic played a critical role in your success.
- 5
Conclude with the positive outcome or what you learned.
Example Answers
In my previous job as a production assistant, we had a last-minute order from a major client that needed to be completed within 48 hours. Recognizing the urgency, I organized the team, prioritized tasks, and worked extra hours alongside my colleagues. My strong commitment to quality helped us deliver the order on time, and the client praised our effort, leading to repeat business.
What achievement in your career as a cloth spreader are you most proud of, and why?
How to Answer
- 1
Identify a specific project or instance where you excelled as a cloth spreader.
- 2
Explain the challenges you faced and how you overcame them.
- 3
Highlight the skills you used and how they contributed to your success.
- 4
Discuss the positive impact of your achievement on the team or project.
- 5
Keep your answer focused and concise, ideally within 2-3 minutes.
Example Answers
I am most proud of improving the efficiency of our fabric spreading process during a major project. We had tight deadlines, and I implemented a new technique to reduce the setup time. This not only saved us 15% in labor costs but also helped the team meet our delivery schedule on time, boosting morale.
Don't Just Read Cloth Spreader Questions - Practice Answering Them!
Reading helps, but actual practice is what gets you hired. Our AI feedback system helps you improve your Cloth Spreader interview answers in real-time.
Personalized feedback
Unlimited practice
Used by hundreds of successful candidates
Technical Interview Questions
What types of equipment have you used in your experience as a cloth spreader, and what were your responsibilities concerning them?
How to Answer
- 1
Identify specific equipment you've used, such as spreading machines or cutting tables.
- 2
Mention your role in operating, maintaining, or troubleshooting the equipment.
- 3
Explain how you've ensured quality and efficiency in your work with the equipment.
- 4
Highlight any safety protocols you followed when using the equipment.
- 5
Be prepared to discuss how your experience with this equipment contributes to the overall production process.
Example Answers
In my previous role, I frequently used automatic cloth spreading machines, which I operated and calibrated to ensure precision. My responsibilities included setting the tension and feeding the fabric correctly, as well as performing routine maintenance to keep the machines running efficiently.
What different types of fabrics have you worked with, and how does each one require a different approach to spreading?
How to Answer
- 1
Identify at least three types of fabrics you've handled.
- 2
Explain how the characteristics of each fabric affect spreading technique.
- 3
Discuss any specific tools or methods used for different fabrics.
- 4
Mention any challenges faced with certain fabrics and how you overcame them.
- 5
Conclude with the importance of adapting your approach based on fabric type.
Example Answers
I have worked with cotton, polyester, and silk fabrics. Cotton is sturdy and spreads easily, so I use a standard spreading technique. Polyester is slippery, so I use weights to keep it in place. Silk is delicate, requiring a gentle touch and less heat during the process to avoid damage.
Don't Just Read Cloth Spreader Questions - Practice Answering Them!
Reading helps, but actual practice is what gets you hired. Our AI feedback system helps you improve your Cloth Spreader interview answers in real-time.
Personalized feedback
Unlimited practice
Used by hundreds of successful candidates
What safety protocols do you follow while operating machinery for fabric spreading?
How to Answer
- 1
Always wear personal protective equipment like gloves and goggles.
- 2
Ensure that the machine is properly maintained and inspected before use.
- 3
Make sure to follow the manufacturer's operating instructions strictly.
- 4
Be aware of your surroundings and keep the workspace clear of obstacles.
- 5
Report any safety concerns or malfunctions immediately.
Example Answers
I always wear gloves and goggles when operating the fabric spreader to protect myself. I also check the machine for any issues before starting it.
Describe the techniques you use for spreading fabric evenly to prevent wrinkles and damage.
How to Answer
- 1
Always start by laying the fabric flat on a clean, smooth surface.
- 2
Use your hands to gently pull the fabric from the center outwards to avoid uneven tension.
- 3
Check for any folds or creases and smooth them out carefully with your hands.
- 4
If the fabric is especially wrinkled, use a steamer or iron on a low setting to remove wrinkles before spreading.
- 5
Ensure even weight distribution by adjusting the fabric in all corners before starting any further processing.
Example Answers
I start by laying the fabric flat on a smooth surface, then gently pull from the center to eliminate any tension. I always check for creases and smooth them out with my hands.
How do you assess the quality of the fabric spread after the process is complete?
How to Answer
- 1
Check for evenness across the entire fabric spread
- 2
Look for any folds or creases that could affect cutting
- 3
Inspect the fabric alignment with the cutting markers
- 4
Ensure there are no defects in the fabric like stains or tears
- 5
Confirm the total fabric width matches specifications
Example Answers
I assess the fabric spread by first ensuring it is even and free of creases. Then, I check the alignment with cutting markers and inspect for any defects like stains. Lastly, I confirm the width matches the specifications.
What do you know about the characteristics of different fabrics, and how do they affect the spreading process?
How to Answer
- 1
Understand the basic properties of fabrics like weight, stretch, and fiber content.
- 2
Discuss how these properties influence the ease of spreading.
- 3
Mention specific fabric types like cotton, polyester, or silk and their unique characteristics.
- 4
Explain the impact of fabric finish and texture on the spreading process.
- 5
Relate your knowledge to potential challenges in spreading different fabrics.
Example Answers
Different fabrics have unique characteristics that affect spreading. For example, heavier fabrics like canvas may require more tension and careful handling, while lighter fabrics like chiffon can easily bunch up if not spread properly.
Explain how you would troubleshoot issues with uneven spreading during the process.
How to Answer
- 1
Check the calibration settings of the spreader for accuracy.
- 2
Inspect the material flow to ensure it is consistent and unobstructed.
- 3
Look for any mechanical issues, such as worn parts or clogs.
- 4
Test different spreader speeds to find the optimal setting.
- 5
Perform visual checks during operation to identify patterns of unevenness.
Example Answers
I would begin by checking the spreader’s calibration to ensure it is set correctly for the material. Then I would examine the flow of the spreading material for any blockages. If those are fine, I would inspect for mechanical issues like worn or damaged parts.
How do you ensure that the spreading equipment you use remains in good working condition?
How to Answer
- 1
Perform regular maintenance checks according to the manufacturer's guidelines.
- 2
Keep the equipment clean and free from debris after each use.
- 3
Report any malfunctions or issues immediately to the supervisor.
- 4
Use the equipment only as intended and follow operational protocols.
- 5
Train and remind team members on proper handling and care of the equipment.
Example Answers
I ensure the spreading equipment remains in good condition by performing regular maintenance checks and cleaning it after each use to prevent buildup.
What metrics do you track to ensure effective performance in fabric spreading?
How to Answer
- 1
Identify key performance indicators related to efficiency, such as spread width accuracy.
- 2
Consider tracking fabric waste percentage to measure material optimization.
- 3
Monitor production speed to ensure timely completion of tasks.
- 4
Evaluate consistency and quality of spread to maintain high standards.
- 5
Keep records of machine downtime to identify areas for improvement.
Example Answers
I track spread width accuracy to ensure the fabric is spread evenly and consistently across the designated area, minimizing waste. I also monitor the waste percentage to optimize material usage and production speed to keep up with our timelines.
How do you handle different thicknesses and weights of fabric during the spreading process?
How to Answer
- 1
Assess the fabric’s thickness and weight beforehand to select the right spreading technique.
- 2
Use appropriate tools, like weights or clamps, to secure heavier fabrics while spreading.
- 3
For thicker fabrics, ensure that the spreading surface is clean and smooth to avoid snags.
- 4
Adjust the tension and speed of spreading based on the fabric’s properties to prevent damage.
- 5
Test a small section first if you're unsure about how the fabric will behave.
Example Answers
I always begin by assessing the fabric's thickness and weight. For heavier materials, I apply more tension and use clamps to hold the fabric in place, ensuring it spreads evenly without slipping.
Don't Just Read Cloth Spreader Questions - Practice Answering Them!
Reading helps, but actual practice is what gets you hired. Our AI feedback system helps you improve your Cloth Spreader interview answers in real-time.
Personalized feedback
Unlimited practice
Used by hundreds of successful candidates
What practices do you employ to minimize waste during the fabric spreading process?
How to Answer
- 1
Carefully measure fabric lengths before spreading to prevent excess cut-offs
- 2
Utilize optimized lay plans to maximize fabric usage
- 3
Regularly inspect fabric for defects before spreading
- 4
Train team members on efficient spreading techniques
- 5
Implement a feedback loop to continuously improve waste reduction practices
Example Answers
I always measure the fabric lengths accurately before I start to minimize waste. I also make sure to use optimized lay plans that maximize the amount of fabric used with minimal cut-offs.
Situational Interview Questions
Imagine you have multiple rolls of fabric to spread in a limited time. How would you prioritize your tasks?
How to Answer
- 1
Assess the fabric types and requirements for each roll.
- 2
Estimate the time needed to spread each roll based on complexity.
- 3
Prioritize rolls with upcoming deadlines or production schedules.
- 4
Organize your workspace for efficient movement between rolls.
- 5
Communicate with team members to delegate tasks if necessary.
Example Answers
I would first assess the types of fabric and their specific requirements, then estimate how long each roll will take. I'd prioritize those with the nearest deadlines and organize my workspace to minimize movement.
If you notice a tear in the fabric while spreading, what immediate actions would you take?
How to Answer
- 1
Stop spreading immediately to prevent further damage.
- 2
Assess the size and location of the tear to determine severity.
- 3
Notify a supervisor or manager about the situation promptly.
- 4
Mark the tear to ensure it is easily visible to others.
- 5
Document the incident if required by company protocols.
Example Answers
I would stop the spreading process to avoid causing more damage. Then, I would assess the tear's size and notify my supervisor immediately while marking the area for visibility.
Don't Just Read Cloth Spreader Questions - Practice Answering Them!
Reading helps, but actual practice is what gets you hired. Our AI feedback system helps you improve your Cloth Spreader interview answers in real-time.
Personalized feedback
Unlimited practice
Used by hundreds of successful candidates
You overhear a colleague saying that they found an issue with the fabric you've spread. How would you handle the situation?
How to Answer
- 1
Stay calm and don't take it personally.
- 2
Approach the colleague to understand the issue better.
- 3
Ask for specific details about the problem with the fabric.
- 4
Collaborate on a solution and determine the next steps together.
- 5
Communicate with your supervisor about any findings or remedies.
Example Answers
I would first approach my colleague and ask them to explain the issue they found with the fabric. It's important to understand the problem clearly. Together, we could assess the fabric and come up with a solution. I would also inform my supervisor about the situation to ensure everyone is on the same page.
If the machinery you are using suddenly stops functioning, what steps would you take to address the issue?
How to Answer
- 1
Stay calm and assess the situation before taking action.
- 2
Check the machine for any visible signs of trouble or error messages.
- 3
Ensure the machine is safely turned off before inspecting it further.
- 4
Refer to the machine's manual for troubleshooting guidance.
- 5
If the issue cannot be resolved quickly, report it to a supervisor.
Example Answers
I would first remain calm and try to quickly assess the issue by looking for any error messages or unusual sounds. Then, I would safely turn off the machine and check for any obvious problems. If I couldn't fix it, I would consult the manual for troubleshooting steps or report it to my supervisor.
How would you handle the spread of a particularly delicate fabric that requires special care?
How to Answer
- 1
Identify the fabric type and its specific care requirements
- 2
Use appropriate tools to avoid damaging the fabric
- 3
Work in a controlled environment to prevent accidents
- 4
Spread the fabric gently and ensure it lies flat without tension
- 5
Regularly check for any signs of distress during the handling process
Example Answers
I would first understand the fabric's specific care requirements, such as the need for low tension. Then, I would use a soft spreader that minimizes pressure to gently lay out the fabric in a controlled environment, avoiding any potential snags. Finally, I would continuously check the fabric for any signs of damage.
You are working within a team, and one member is not using the spreading equipment correctly. How would you approach this situation?
How to Answer
- 1
Observe the team member and identify the specific issue with the equipment use.
- 2
Approach the team member privately to discuss your concerns without embarrassment.
- 3
Use a positive and constructive tone to explain the correct usage of the equipment.
- 4
Offer to demonstrate the proper technique or suggest a short training session.
- 5
Encourage teamwork by reinforcing that everyone can learn from each other.
Example Answers
I would first observe the team member to understand what they are doing incorrectly. Then, I would approach them privately and explain the correct method of using the spreading equipment in a supportive way. I might offer to show them how to do it properly and suggest we review best practices together as a team.
In the event of a fabric spill while spreading, what actions would you take?
How to Answer
- 1
Calmly assess the situation without panic.
- 2
Stop the spreading machine immediately to prevent further spread of the fabric.
- 3
Quickly gather the spilled fabric and remove it from the working area.
- 4
Inform your supervisor or team about the incident as needed.
- 5
Clean the area to ensure safety and prepare for the next task.
Example Answers
If there is a fabric spill, I would first stop the spreading machine to avoid further issues. Then, I'd carefully collect the spilled fabric and remove it from the area while making sure to keep the workspace clean. After that, I would inform my supervisor about the spill.
You have received a batch of fabric that seems inconsistent in quality. How would you proceed with spreading it?
How to Answer
- 1
Inspect the fabric thoroughly for defects before spreading.
- 2
Categorize the fabric pieces based on quality and consistency.
- 3
Adjust the spreading technique based on the quality of each category.
- 4
Communicate any findings to the team and suggest solutions.
- 5
Document the quality issues for future reference.
Example Answers
First, I would inspect the entire batch for defects and categorize the fabric into 'high quality' and 'low quality'. For high quality pieces, I would spread them using standard techniques, and for low quality pieces, I would adjust my approach to ensure a smooth finish while noting any areas that require special attention.
When you are under pressure to meet a deadline, how do you maintain the quality of your work?
How to Answer
- 1
Prioritize tasks to focus on the most impactful aspects of the work.
- 2
Break down the project into smaller, manageable steps to avoid feeling overwhelmed.
- 3
Set specific mini-deadlines for each task to ensure steady progress.
- 4
Communicate with team members to delegate appropriately and ensure clarity.
- 5
Review and edit your work regularly to catch any potential errors before final submission.
Example Answers
When under pressure, I prioritize my tasks to focus on the most critical aspects of the project. I break my work into smaller steps, setting mini-deadlines for each. This helps me manage my time and maintain quality.
If you were to start a new project that involved spreading multiple types of fabric, how would you collaborate with the design team?
How to Answer
- 1
Initiate discussions to understand the design vision and fabric needs
- 2
Share knowledge about different fabric handling techniques with the team
- 3
Integrate feedback loops to ensure quality throughout the process
- 4
Schedule regular check-ins to align on project progress and address issues
- 5
Prepare visual samples to illustrate spreading techniques for different fabrics
Example Answers
I would start by meeting with the design team to gain insight into their vision for each fabric type. Then, I would discuss the best spreading techniques to achieve their goals, ensuring we collaborate at each stage to incorporate their feedback.
Don't Just Read Cloth Spreader Questions - Practice Answering Them!
Reading helps, but actual practice is what gets you hired. Our AI feedback system helps you improve your Cloth Spreader interview answers in real-time.
Personalized feedback
Unlimited practice
Used by hundreds of successful candidates
How would you handle a situation where the job requirements were unclear regarding fabric specifications?
How to Answer
- 1
Clarify the requirements by communicating directly with your supervisor or team.
- 2
Look for any documentation or resources that might explain the fabric specifications.
- 3
Ask colleagues who may have dealt with similar fabrics for their insights.
- 4
Conduct a test with a sample fabric if feasible to see how it performs.
- 5
Document your findings and any clarifications for future reference.
Example Answers
I would start by asking my supervisor for clarification on the fabric specifications. If there is documentation available, I would review it to ensure I understand the expectations. Additionally, I would consult with colleagues who might have more experience with the fabric in question.
Cloth Spreader Position Details
Recommended Job Boards
These job boards are ranked by relevance for this position.
Related Positions
- Cloth Baler
- Cloth Hand
- Clothier
- Textile Machine Operator
- Towel Folder
- Textile Worker
- Dry Roller
- Cotton Opener
- Wool Scourer
- Folding Machine Operator
Similar positions you might be interested in.
Ace Your Next Interview!
Practice with AI feedback & get hired faster
Personalized feedback
Used by hundreds of successful candidates
Ace Your Next Interview!
Practice with AI feedback & get hired faster
Personalized feedback
Used by hundreds of successful candidates