Top 29 Equipment Technician Interview Questions and Answers [Updated 2025]
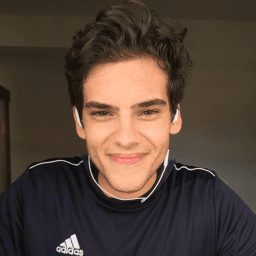
Andre Mendes
•
March 30, 2025
Preparing for an Equipment Technician interview can be daunting, but we're here to help you succeed. In this post, we delve into the most common interview questions for this vital role, providing you with example answers and expert tips to help you respond confidently and effectively. Whether you're a seasoned professional or just starting out, this guide will equip you with the insights you need to impress your potential employer.
Download Equipment Technician Interview Questions in PDF
To make your preparation even more convenient, we've compiled all these top Equipment Technicianinterview questions and answers into a handy PDF.
Click the button below to download the PDF and have easy access to these essential questions anytime, anywhere:
List of Equipment Technician Interview Questions
Behavioral Interview Questions
Can you describe a time when you solved a complex equipment issue? What steps did you take?
How to Answer
- 1
Identify the specific equipment issue and its impact
- 2
Explain the diagnostic process and tools used
- 3
Detail the solution implemented and why it was chosen
- 4
Mention any collaboration with team members or departments
- 5
Highlight the results and what you learned from the experience
Example Answers
At my previous job, the conveyor system frequently jammed. I used diagnostic tools to determine it was a sensor issue. I recalibrated the sensors and tested the system, collaborating with the maintenance team. This reduced downtime by 30%, teaching me the value of accurate diagnostics.
Tell me about a time you worked closely with other technicians or engineers. What was your role in the project?
How to Answer
- 1
Choose a specific project where teamwork was essential.
- 2
Highlight your specific contributions and responsibilities.
- 3
Mention tools or technologies used in collaboration.
- 4
Discuss the outcome or success of the project.
- 5
Reflect on what you learned from the experience.
Example Answers
In a recent project to upgrade our facility's HVAC system, I collaborated closely with two other technicians and an HVAC engineer. My role involved conducting initial inspections and assessing equipment needs. We used diagnostic software to identify issues and coordinated to ensure our schedules aligned for timely repairs. The project resulted in reduced downtime and improved system efficiency by 20%. I learned the importance of communication in a team setting.
Don't Just Read Equipment Technician Questions - Practice Answering Them!
Reading helps, but actual practice is what gets you hired. Our AI feedback system helps you improve your Equipment Technician interview answers in real-time.
Personalized feedback
Unlimited practice
Used by hundreds of successful candidates
Describe a situation where you had to adapt quickly to a new piece of equipment. How did you handle it?
How to Answer
- 1
Choose a specific equipment example that you used.
- 2
Briefly describe the context and why adaptation was necessary.
- 3
Highlight the actions you took to learn about the equipment quickly.
- 4
Mention any challenges you faced and how you overcame them.
- 5
Conclude with the positive outcome or what you learned from the experience.
Example Answers
When I started at my previous job, we implemented a new CNC machine. I made it a priority to read the manual and watch instructional videos. I also asked a senior technician for tips. Despite initial confusion, I got the hang of it in a few days and was able to operate it efficiently. This experience taught me the importance of proactive learning.
Have you ever led a team during a maintenance project? What challenges did you face, and how did you overcome them?
How to Answer
- 1
Choose a specific project to discuss
- 2
Highlight your leadership role clearly
- 3
Identify one or two key challenges faced
- 4
Describe specific actions you took to overcome those challenges
- 5
Mention the positive outcomes of your leadership
Example Answers
In a recent project, I led a team of four during the overhaul of a conveyor system. One challenge was a tight deadline, so I prioritized tasks and organized daily check-ins to keep everyone on track. As a result, we completed the project two days ahead of schedule, improving overall productivity.
Give an example of a time when you had to explain a technical issue to a non-technical person. How did you ensure they understood?
How to Answer
- 1
Identify a specific technical issue you faced.
- 2
Choose a non-technical audience relevant to your experience.
- 3
Break down complex terms into simple language.
- 4
Use analogies or visual aids to clarify points.
- 5
Ask questions to confirm their understanding.
Example Answers
In my previous role, I had to explain a malfunctioning conveyor belt to our warehouse manager. I simplified the issue by comparing it to a car's engine, saying it needed a tune-up. I used a diagram to show where the problem was and asked if they had any questions, which helped them grasp the solution better.
Describe a situation where you disagreed with a colleague regarding a technical approach. How was the conflict resolved?
How to Answer
- 1
Identify a specific disagreement you had with a colleague.
- 2
Explain the different technical approaches each of you proposed.
- 3
Highlight how you communicated your perspective respectfully.
- 4
Describe the resolution process, including any compromises made.
- 5
Focus on the outcome, including any positive impact on the project.
Example Answers
In a project to install new machinery, I disagreed with a colleague who wanted to use a different software for diagnostics. I explained my reasons for advocating the original software based on past success. We discussed our viewpoints and decided to test both options before making a final decision, leading to improved efficiency in the installation process.
Tell me about a time when you had to complete a project under a tight deadline. How did you manage your time?
How to Answer
- 1
Choose a specific project that had a clear deadline.
- 2
Explain the steps you took to prioritize tasks.
- 3
Mention tools or methods you used for time management.
- 4
Highlight any challenges faced and how you overcame them.
- 5
Conclude with the successful outcome and what you learned.
Example Answers
In my last position, we had a tight deadline to complete equipment maintenance. I made a prioritized checklist of tasks, focused on high-impact repairs first, and used scheduling software to track progress. Despite a few unexpected issues, I delegated tasks effectively and completed the project on time, improving our equipment uptime.
Describe a time when attention to detail made a significant difference in your work.
How to Answer
- 1
Select a specific incident that highlights your attention to detail.
- 2
Explain the mistake or challenge that arose without attention to detail.
- 3
Describe the actions you took to address the issue.
- 4
Highlight the positive outcome resulting from your attention to detail.
- 5
Connect the experience to how it will benefit the role you're applying for.
Example Answers
In my previous job, I noticed the calibration settings on a piece of equipment were incorrect. I double-checked the specifications against the manufacturer's guidelines, found discrepancies, and corrected them. This prevented a costly error during production and increased equipment efficiency by 15%. It reinforced the importance of precision in my work.
Don't Just Read Equipment Technician Questions - Practice Answering Them!
Reading helps, but actual practice is what gets you hired. Our AI feedback system helps you improve your Equipment Technician interview answers in real-time.
Personalized feedback
Unlimited practice
Used by hundreds of successful candidates
Technical Interview Questions
What methods do you use to troubleshoot malfunctioning equipment? Can you provide an example?
How to Answer
- 1
Begin with a clear thought process for troubleshooting.
- 2
Mention specific tools or techniques you use.
- 3
Provide a concise, relevant example from past experience.
- 4
Highlight the outcome of your troubleshooting.
- 5
Emphasize teamwork or communication in your approach.
Example Answers
I start by identifying the symptoms and gathering data on the equipment's performance. For instance, when a conveyor motor stopped working, I used a multimeter to check the power supply and found a blown fuse. After replacing it, the motor functioned normally.
What is your experience with preventive maintenance programs? How do you implement them?
How to Answer
- 1
Describe specific programs you have developed or managed
- 2
Highlight tools or software you used for tracking maintenance schedules
- 3
Explain how you trained team members on these programs
- 4
Provide examples of the outcomes or improvements from the programs
- 5
Discuss how you adjust plans based on equipment performance or feedback
Example Answers
In my previous role, I developed a preventive maintenance program using CMMS software to schedule regular checks. This included training technicians on the system, which improved our on-time maintenance by 30%.
Don't Just Read Equipment Technician Questions - Practice Answering Them!
Reading helps, but actual practice is what gets you hired. Our AI feedback system helps you improve your Equipment Technician interview answers in real-time.
Personalized feedback
Unlimited practice
Used by hundreds of successful candidates
Can you explain the safety protocols you follow when working with heavy machinery?
How to Answer
- 1
Always conduct a thorough pre-operation inspection of the machinery.
- 2
Wear appropriate personal protective equipment (PPE) at all times.
- 3
Follow lockout/tagout procedures to ensure machinery is safe to work on.
- 4
Maintain clear communication with team members when operating heavy equipment.
- 5
Stay trained on the specific safety procedures for each type of machinery.
Example Answers
I conduct a full inspection of the machinery before use, check all safety features, and always wear my PPE, including hard hats and safety glasses. I follow lockout/tagout procedures and ensure clear communication with my team.
What diagnostic tools and software are you familiar with? How do you use them in your role?
How to Answer
- 1
List specific diagnostic tools and software you have experience with
- 2
Explain how you utilize each tool in your daily tasks
- 3
Highlight any relevant certifications or training on the tools
- 4
Mention any troubleshooting examples where tools played a key role
- 5
Tailor your examples to the equipment and industry relevant to the position
Example Answers
I have experience with tools like Multimeters, Oscilloscopes, and Fluke diagnostic software. I use Multimeters for voltage measurements during routine maintenance and Oscilloscopes for analyzing waveforms when troubleshooting circuit issues.
Describe a complex repair job you completed. What challenges did you encounter, and how did you address them?
How to Answer
- 1
Choose a specific repair job that showcases your skills and experience.
- 2
Outline the steps you took to diagnose the problem clearly.
- 3
Describe at least two specific challenges you faced during the repair.
- 4
Explain how you resolved these challenges effectively.
- 5
Include the outcome of the repair and any lessons learned.
Example Answers
I repaired a faulty hydraulic lift in a manufacturing plant. The main challenge was identifying a hidden leak that wasn't visible. I used a pressure test to isolate the issue, ensuring I didn't overlook any components. After fixing the leak, I conducted thorough tests to confirm it was working. The lift is now operating efficiently, which improved production speed.
What experience do you have working with electrical systems in equipment? Can you provide specific examples?
How to Answer
- 1
Outline relevant work experience specifically related to electrical systems.
- 2
Mention specific types of equipment you have interacted with.
- 3
Include any troubleshooting or repair tasks you performed.
- 4
Highlight any relevant certifications or training in electrical systems.
- 5
Discuss how your experience improved equipment performance or safety.
Example Answers
In my previous role as a maintenance technician, I worked with industrial robotics and performed routine electrical system checks. For example, I diagnosed a fault in a robotic arm's wiring, replaced the damaged components, and restored it to full operation, increasing productivity by 20%.
What types of software or computerized maintenance management systems (CMMS) have you worked with?
How to Answer
- 1
List the specific CMMS you've used and your role with them
- 2
Highlight your experience with each system's key features
- 3
Mention any successes or improvements achieved using these systems
- 4
Be prepared to discuss how you adapted to new systems
- 5
Express willingness to learn new software quickly
Example Answers
I have worked with MPulse and MAXIMO. In my previous role, I used MPulse for tracking maintenance schedules and inventory. This helped reduce equipment downtime by 20%.
How do you approach the use of technical manuals and schematics when repairing equipment?
How to Answer
- 1
Start by thoroughly reading the relevant sections of the manual.
- 2
Use schematics to understand the layout and connections of the equipment.
- 3
Follow troubleshooting guides step-by-step for systematic diagnosis.
- 4
Compare actual equipment conditions with schematics to identify discrepancies.
- 5
Document findings and solutions for future reference and improvements.
Example Answers
I always begin by reading the manual to familiarize myself with the equipment. Next, I use schematics to visualize the components and connections, which helps me identify possible issues quickly. I follow troubleshooting steps closely to ensure that I don’t miss anything.
What is your experience with mechanical systems in equipment, and how do you maintain them?
How to Answer
- 1
Describe specific mechanical systems you have worked on
- 2
Include types of equipment you've maintained or repaired
- 3
Mention any relevant tools or technologies you use
- 4
Explain your systematic approach to maintenance procedures
- 5
Highlight any successful outcomes or improvements you've achieved
Example Answers
I have worked extensively with hydraulic systems in industrial machinery, maintaining equipment by performing regular inspections and replacing worn components. I use diagnostic tools to pinpoint issues early, ensuring optimal performance.
What specific experience do you have with hydraulic systems, and what challenges have you faced?
How to Answer
- 1
Highlight your hands-on experience with hydraulic systems.
- 2
Mention specific tools or technologies you have used.
- 3
Discuss a challenge you faced and how you overcame it.
- 4
Emphasize your problem-solving skills.
- 5
Relate your experiences to the job you're applying for.
Example Answers
I have worked on hydraulic systems for heavy machinery for over 5 years. I regularly used pressure testers and hydraulic fluid analysis tools. A challenge I faced was diagnosing a leak in a hydraulic line, which I traced to a loose fitting and resolved by tightening it and replacing O-rings.
Don't Just Read Equipment Technician Questions - Practice Answering Them!
Reading helps, but actual practice is what gets you hired. Our AI feedback system helps you improve your Equipment Technician interview answers in real-time.
Personalized feedback
Unlimited practice
Used by hundreds of successful candidates
What methods do you use to track and manage equipment parts and inventory?
How to Answer
- 1
Discuss specific software or systems you are familiar with for inventory management.
- 2
Mention methods for categorizing parts to ensure easy access and tracking.
- 3
Explain how you maintain accurate records of equipment usage and parts replacement.
- 4
Highlight any experience with audits or regular inventory checks.
- 5
Include your approach to forecasting inventory needs based on equipment usage.
Example Answers
I use inventory management software like SAP to track parts. I categorize items based on equipment type and usage frequency. I keep detailed logs of all parts used and conduct monthly audits to ensure accuracy.
Situational Interview Questions
Imagine you are on-site, and you notice an equipment failure that could halt production. What immediate actions would you take?
How to Answer
- 1
Assess the situation to understand the extent of the failure
- 2
Notify your supervisor and relevant team members immediately
- 3
Implement safety measures to prevent accidents or injuries
- 4
Isolate or shutdown the affected equipment if necessary
- 5
Document the issue for future reference and troubleshooting
Example Answers
I would first evaluate the equipment to determine how severe the failure is. Then, I would inform my supervisor and the team about the situation. If it's critical, I would ensure the area is secure to prevent any safety hazards.
If you had multiple maintenance requests at the same time, how would you prioritize them?
How to Answer
- 1
Assess the urgency of each request based on equipment impact.
- 2
Consider safety implications for personnel and operations.
- 3
Evaluate downtime costs associated with each piece of equipment.
- 4
Check if any request is tied to scheduled operational needs.
- 5
Communicate priorities to the team and set clear expectations.
Example Answers
I prioritize maintenance requests by first assessing any that impact safety or pose immediate risks, followed by those affecting production. I also factor in the potential loss in downtime costs and communicate my plan to the team for alignment.
Don't Just Read Equipment Technician Questions - Practice Answering Them!
Reading helps, but actual practice is what gets you hired. Our AI feedback system helps you improve your Equipment Technician interview answers in real-time.
Personalized feedback
Unlimited practice
Used by hundreds of successful candidates
Suppose you are tasked with improving the efficiency of an existing maintenance process. What steps would you take?
How to Answer
- 1
Analyze current maintenance process to identify bottlenecks
- 2
Engage with the team to gather feedback on issues
- 3
Research best practices and technology upgrades applicable
- 4
Implement small-scale changes and monitor impacts
- 5
Train staff on new processes and ensure proper support
Example Answers
First, I would analyze the current maintenance process to find any bottlenecks. Then, I’d gather feedback from the team to understand their challenges. Based on the insights, I would research best practices and consider using new technology. After that, I’d implement small changes and monitor the results. Finally, I’d provide training to ensure everyone is comfortable with the updates.
If given a limited budget for equipment repairs, how would you decide which repairs to prioritize?
How to Answer
- 1
Assess the impact of equipment failure on operations.
- 2
Evaluate the frequency and severity of issues with each piece of equipment.
- 3
Consider safety implications of each repair.
- 4
Examine the cost versus benefit of repairs.
- 5
Consult with team members for insights on operational needs.
Example Answers
I would first identify which equipment has the highest impact on production. If a piece of equipment is critical and frequently breaks down, I would prioritize its repair even if it means delaying less crucial repairs.
You are responsible for training new technicians on equipment handling. How would you structure the training?
How to Answer
- 1
Start with an overview of equipment safety protocols.
- 2
Introduce each piece of equipment with hands-on demonstrations.
- 3
Encourage new technicians to shadow experienced staff during initial handling.
- 4
Implement quizzes or checkpoints to assess understanding.
- 5
Provide ongoing support and schedule regular feedback sessions.
Example Answers
I would begin by teaching safety protocols, followed by hands-on demonstrations for each equipment type. New technicians would then shadow experienced staff to see best practices in action and take quizzes to ensure they understand key points.
If you find a problem that requires input from other departments, how would you approach collaboration?
How to Answer
- 1
Identify key stakeholders in the relevant departments
- 2
Clearly define the problem and your specific needs for input
- 3
Initiate a conversation through an email or meeting request
- 4
Be open to ideas and suggestions from others
- 5
Follow up to ensure alignment and communicate solutions
Example Answers
I would first identify the key stakeholders in the departments involved. Then, I would clearly outline the problem and what specific input I need from them, followed by reaching out to schedule a meeting to discuss it.
If you encounter a recurring issue with equipment despite repairs, what steps would you take to report and address it?
How to Answer
- 1
Document the specific issue with details on frequency and impact.
- 2
Analyze trends in the issue to identify possible root causes.
- 3
Communicate findings to the appropriate team members or supervisor.
- 4
Suggest possible solutions based on your analysis.
- 5
Follow up on the implemented solutions to ensure effectiveness.
Example Answers
I would start by documenting the issue, noting when and how often it occurs. Then, I would analyze the data to see if there's a pattern or root cause. After that, I would report my findings to my supervisor and suggest solutions that might work.
How would you handle a situation where you discovered that an equipment component did not meet quality standards?
How to Answer
- 1
Identify the issue clearly and specify how you noticed the quality problem.
- 2
Communicate the issue to your supervisor or team immediately.
- 3
Document the findings and ensure there is a record of the quality concern.
- 4
Propose a solution or corrective action to address the issue.
- 5
Follow up to confirm that the issue has been resolved and it doesn’t happen again.
Example Answers
I found a component that was out of tolerance during my routine checks. I immediately reported it to my supervisor and documented the issue for future reference. I suggested a redesign of that component and worked with the team to implement the change.
Equipment Technician Position Details
Salary Information
Recommended Job Boards
CareerBuilder
www.careerbuilder.com/jobs/equipment-technicianZipRecruiter
www.ziprecruiter.com/Jobs/Equipment-TechnicianThese job boards are ranked by relevance for this position.
Related Positions
Ace Your Next Interview!
Practice with AI feedback & get hired faster
Personalized feedback
Used by hundreds of successful candidates
Ace Your Next Interview!
Practice with AI feedback & get hired faster
Personalized feedback
Used by hundreds of successful candidates