Top 31 Laundry Machine Mechanic Interview Questions and Answers [Updated 2025]
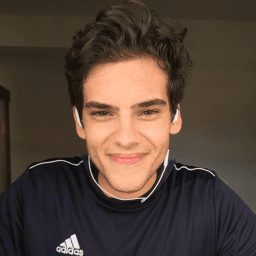
Andre Mendes
•
March 30, 2025
Preparing for a Laundry Machine Mechanic interview can be daunting, but we've got you covered with the most common questions you'll face. In this post, you'll find insightful example answers and practical tips to help you respond effectively and confidently. Whether you're a seasoned professional or new to the field, these insights will hone your skills and prepare you for success in landing the job.
Download Laundry Machine Mechanic Interview Questions in PDF
To make your preparation even more convenient, we've compiled all these top Laundry Machine Mechanicinterview questions and answers into a handy PDF.
Click the button below to download the PDF and have easy access to these essential questions anytime, anywhere:
List of Laundry Machine Mechanic Interview Questions
Behavioral Interview Questions
Can you describe a time when you worked as part of a team to repair a laundry machine?
How to Answer
- 1
Share a specific problem you encountered with the machine.
- 2
Explain your role in the team and what actions you took.
- 3
Describe how you communicated and collaborated with team members.
- 4
Highlight the results of your teamwork and what you learned.
- 5
Be concise and focused on the collaboration aspect.
Example Answers
In my last job, our team faced a situation where a commercial laundry machine was leaking water. I identified the source of the leak while collaborating with three other mechanics. We divided tasks; I handled the disconnecting of hoses while others inspected the pump. We communicated constantly to ensure we weren't duplicating efforts and successfully fixed the leak in under two hours, preventing downtime.
Tell me about a particularly challenging repair you faced and how you resolved it.
How to Answer
- 1
Choose a specific repair that had significant complications.
- 2
Explain what diagnostic steps you took to identify the issue.
- 3
Describe the repair steps you implemented and any tools used.
- 4
Discuss any challenges faced during the repair process.
- 5
Highlight the outcome and what you learned from the experience.
Example Answers
I once worked on a commercial laundry machine that kept overheating. I first ran a full diagnostic and discovered a faulty thermostat. I replaced the thermostat using a multimeter to ensure proper connection. The challenge was reassembling a tight space, but I succeeded. In the end, the machine worked flawlessly, and I learned the importance of careful diagnostics.
Don't Just Read Laundry Machine Mechanic Questions - Practice Answering Them!
Reading helps, but actual practice is what gets you hired. Our AI feedback system helps you improve your Laundry Machine Mechanic interview answers in real-time.
Personalized feedback
Unlimited practice
Used by hundreds of successful candidates
Describe a situation where you had to quickly learn a new type of laundry equipment. How did you handle it?
How to Answer
- 1
Focus on a specific instance where you learned quickly.
- 2
Explain the steps you took to familiarize yourself with the equipment.
- 3
Mention resources you used, such as manuals or training.
- 4
Highlight any challenges you faced and how you overcame them.
- 5
Conclude with the outcome of your quick learning.
Example Answers
At my previous job, we acquired new commercial washers. I quickly read the manual and watched tutorial videos online. I practiced by observing a couple of colleagues and then tried operating the machines myself. One challenge was understanding the control panel, but I asked questions, which helped me master it. As a result, I became the go-to person for that equipment.
Can you give an example of how you caught a mistake in your work that could have led to a bigger issue?
How to Answer
- 1
Think of a specific time when you identified a potential problem.
- 2
Explain how you noticed the mistake, whether through inspection or routine checks.
- 3
Describe the steps you took to correct the mistake.
- 4
Mention the outcome and how it prevented further issues.
- 5
Keep it concise and focused on your actions.
Example Answers
During a routine maintenance check on a commercial washer, I noticed unusual vibrations. I investigated further and found that a belt was misaligned. I corrected the alignment and completed maintenance without any equipment downtime.
Describe a time when you went above and beyond for a customer.
How to Answer
- 1
Pick a specific instance where you helped a customer.
- 2
Focus on your actions and the impact on the customer.
- 3
Mention any skills or tools you used to resolve the issue.
- 4
Emphasize customer satisfaction and feedback.
- 5
Keep it concise and relevant to the mechanic role.
Example Answers
Once, a customer needed a laundry machine repair urgently due to a big event. I stayed late to ensure I completed the repair that same day. The customer was incredibly grateful and mentioned how it saved their event.
How have you kept your skills updated with the latest laundry technology?
How to Answer
- 1
Mention specific training or certifications you've completed related to laundry technology.
- 2
Discuss any workshops or webinars you've attended that focus on industry advancements.
- 3
Highlight any professional organizations you belong to that provide resources for staying updated.
- 4
Share examples of new technologies or techniques you've learned about and implemented in your work.
- 5
Talk about online resources, forums, or communities where you engage with other professionals on laundry technology.
Example Answers
I've completed a certification course on commercial laundry equipment, which included the latest energy-efficient washer models. I also attend workshops at industry trade shows regularly.
Can you provide an example of how you have used feedback from a supervisor to improve your work?
How to Answer
- 1
Think of a specific situation where you received feedback.
- 2
Explain the feedback clearly and the context in which it was given.
- 3
Describe the action you took based on the feedback.
- 4
Share the results or improvements that occurred after your changes.
- 5
Keep your response focused and relevant to the job.
Example Answers
In my previous job, my supervisor noted that my wiring of the control panels was sometimes messy. I took this feedback seriously and researched best practices to improve my organization. After consolidating wires and labeling them more clearly, my efficiency increased, and I received positive recognition from my team.
What motivates you to do your best work as a laundry machine mechanic?
How to Answer
- 1
Think about personal satisfaction in solving mechanical problems
- 2
Consider the importance of quality work for customer satisfaction
- 3
Reflect on how teamwork and collaboration motivate you
- 4
Identify any pride in maintaining equipment that ensures hygiene and cleanliness
- 5
Mention the challenge and satisfaction of continual learning in your field
Example Answers
I am motivated by the challenge of diagnosing and repairing complex issues in laundry machines. There’s a deep satisfaction in knowing my work directly impacts the efficiency of the machines, helping customers maintain their operations smoothly.
Have you ever proposed a new procedure or solution to your team? What was it, and what was the outcome?
How to Answer
- 1
Think of a specific instance where you identified a problem.
- 2
Describe the procedure or solution you proposed clearly.
- 3
Explain how you communicated this proposal to your team.
- 4
Share the outcome: did it improve efficiency, save time, or reduce errors?
- 5
Conclude with what you learned from this experience and if you would do anything differently.
Example Answers
In my previous role, I noticed that our maintenance logs were often incomplete. I proposed a standardized form for logging maintenance activities to improve accuracy. After implementing it, we saw a 30% increase in log completion rates, which helped us schedule preventative maintenance more effectively. I learned the importance of clear communication and follow-up.
Don't Just Read Laundry Machine Mechanic Questions - Practice Answering Them!
Reading helps, but actual practice is what gets you hired. Our AI feedback system helps you improve your Laundry Machine Mechanic interview answers in real-time.
Personalized feedback
Unlimited practice
Used by hundreds of successful candidates
Technical Interview Questions
What are the main components of a commercial washing machine, and how do they function together?
How to Answer
- 1
Identify key components such as the drum, motor, water pump, control panel, and detergent dispenser.
- 2
Explain the role of each component in the washing process.
- 3
Discuss how these components interact to perform a wash cycle effectively.
- 4
Use technical terminology appropriately, but keep it simple and clear.
- 5
Provide examples of how issues with these components could affect machine performance.
Example Answers
A commercial washing machine consists of several key components: the drum holds the laundry, the motor drives the drum, the water pump circulates water, the control panel sets the washing cycle, and the detergent dispenser releases detergent. Together, these parts work to efficiently clean clothes by agitating them in water while ensuring proper temperature and detergent concentration.
How do you diagnose electrical issues in laundry machines?
How to Answer
- 1
Start by conducting a visual inspection of the machine for any obvious signs of damage.
- 2
Use a multimeter to check for continuity in electrical components like switches and motors.
- 3
Examine the wiring for any fraying or disconnections that could cause issues.
- 4
Refer to wiring diagrams to understand the circuit layout and locate problem areas.
- 5
Test individual components to identify the faulty part before replacing any parts.
Example Answers
I begin by doing a visual inspection to look for any damaged wires or burnt components. Then, I use a multimeter to test continuity across the switches and motor. If I find any anomalies, I consult the wiring diagram to pinpoint the issue.
Don't Just Read Laundry Machine Mechanic Questions - Practice Answering Them!
Reading helps, but actual practice is what gets you hired. Our AI feedback system helps you improve your Laundry Machine Mechanic interview answers in real-time.
Personalized feedback
Unlimited practice
Used by hundreds of successful candidates
What steps do you follow when troubleshooting a washer that won't drain?
How to Answer
- 1
Check for any obvious clogs in the drain hose and remove them.
- 2
Inspect the pump for blockages or damage and ensure it is functioning properly.
- 3
Examine the lid switch to confirm it is engaging when closed.
- 4
Assess the control board for faults that might prevent draining.
- 5
Test the drain pump motor to see if it is receiving power.
Example Answers
First, I check the drain hose for clogs and clear them if necessary. Then, I inspect the pump for any blockages and ensure it's operating properly. After that, I verify that the lid switch is engaging correctly. If everything looks good, I check the control board and finally test the drain pump motor for power.
Can you explain the procedure for replacing a water pump in a laundry machine?
How to Answer
- 1
Start by unplugging the machine and turning off the water supply.
- 2
Remove any panels or covers to access the water pump.
- 3
Disconnect the hoses and electrical connections from the old pump.
- 4
Install the new pump by reversing the disconnection steps.
- 5
Reassemble the machine and run a test cycle to check for leaks.
Example Answers
To replace a water pump, I first make sure the machine is unplugged and the water supply is off. Then I remove the front panel to access the pump. I disconnect the hoses and the electrical connections. After that, I install the new pump, reattach everything, and finally run a test to ensure it's working properly.
What safety precautions do you take when servicing laundry machines?
How to Answer
- 1
Always unplug the machine before starting any repairs.
- 2
Wear appropriate personal protective equipment like gloves and safety glasses.
- 3
Ensure the area is dry and free of any water spillage before working.
- 4
Use tools that are insulated and rated for electrical work.
- 5
Follow the manufacturer's safety guidelines and use lockout/tagout procedures.
Example Answers
I always unplug the machine before performing any servicing to prevent electrical shock.
What tools and methods do you use for diagnosing mechanical issues in laundry machines?
How to Answer
- 1
Mention specific diagnostic tools you regularly use.
- 2
Describe a systematic approach to troubleshooting.
- 3
Include examples of common issues and how you diagnose them.
- 4
Highlight your experience with both electrical and mechanical aspects.
- 5
Reference any relevant technology or software that aids diagnosis.
Example Answers
I use a multimeter and diagnostic software to check electrical components, starting with the power supply and then testing the motor. For mechanical issues, I inspect the belt and pulleys visually. I've often found worn belts to be a common problem.
What routine maintenance tasks do you recommend performing on laundry machines?
How to Answer
- 1
Check and clean the lint filter after each use
- 2
Inspect hoses for wear or leaks monthly
- 3
Calibrate and check the machine's level and vibration every six months
- 4
Perform a deep clean on the drum and seals every three months
- 5
Ensure the water supply and drainage lines are functioning properly
Example Answers
I recommend cleaning the lint filter after every load, checking the hoses monthly for any signs of wear, and deep cleaning the drum every three months to maintain efficiency.
Are you familiar with any diagnostic software used in modern laundry machines?
How to Answer
- 1
Mention specific software or tools you have used.
- 2
Explain how you have used the software for diagnostics.
- 3
Highlight any troubleshooting successes using the software.
- 4
Discuss your ability to learn new software quickly.
- 5
Relate your experience to the specific machines used by the company.
Example Answers
Yes, I have experience with the Electrolux Diagnostic Tool. I used it to identify issues like an overloaded drum and successfully reset the system and cleared error codes.
What is the process for installing a new commercial laundry machine?
How to Answer
- 1
Begin with preparation steps, such as reviewing the installation manual.
- 2
Ensure the installation area is clean and meets electrical and plumbing requirements.
- 3
Connect water and drainage hoses securely before moving the machine into place.
- 4
Level the machine and adjust feet if necessary for stability.
- 5
Test the machine by running a test cycle to check for leaks and ensure proper functioning.
Example Answers
First, I would review the installation manual and ensure the area is prepared with the right electrical and plumbing setups. Then, I would connect the water and drainage hoses properly, place the machine in position, and level it. Finally, I would run a test cycle to make sure everything works correctly.
How do you differentiate between OEM and aftermarket parts, and what is your preference?
How to Answer
- 1
Understand that OEM parts are made by the original manufacturer, while aftermarket parts are made by third-party companies.
- 2
Consider the quality, warranty, and performance of both types of parts.
- 3
Explain your preference based on reliability and the specific needs of the machine you are working on.
- 4
Be prepared to cite examples from past experiences to support your preference.
- 5
Discuss situations where you might choose one over the other.
Example Answers
I differentiate OEM parts as those made by the original manufacturer, ensuring perfect compatibility and reliability. Aftermarket parts can be good alternatives, often at a lower cost, but I prefer OEM for critical components due to their guarantee of quality.
Don't Just Read Laundry Machine Mechanic Questions - Practice Answering Them!
Reading helps, but actual practice is what gets you hired. Our AI feedback system helps you improve your Laundry Machine Mechanic interview answers in real-time.
Personalized feedback
Unlimited practice
Used by hundreds of successful candidates
How do hydraulic systems work in industrial laundry machines?
How to Answer
- 1
Explain the basic components of hydraulic systems like pumps, actuators, and fluid.
- 2
Describe how the system uses pressurized fluid to perform work.
- 3
Mention the advantages of hydraulics in laundry machines such as efficiency and control.
- 4
Provide an example of a specific function in the laundry machine that uses hydraulics.
- 5
Keep the explanation clear and avoid overly technical jargon.
Example Answers
Hydraulic systems in industrial laundry machines use a pump to move fluid under pressure through hoses to actuators, which perform tasks like opening and closing doors or agitating the wash drum. This allows for precise control and efficient operation.
Explain the purpose of control systems in modern laundry machines.
How to Answer
- 1
Start with a brief definition of control systems.
- 2
Highlight their role in automating machine functions.
- 3
Mention examples of functions they control like washing, rinsing, and drying.
- 4
Emphasize energy efficiency and water conservation.
- 5
Conclude with how they enhance user experience.
Example Answers
Control systems in laundry machines automate the washing, rinsing, and drying processes. They ensure that each cycle operates efficiently, using the right amount of water and energy. This not only saves resources but also improves the washing results, making laundry easier for the user.
Situational Interview Questions
If a customer is upset about a machine malfunction shortly after it was repaired, how would you handle the situation?
How to Answer
- 1
Listen actively to the customer's concerns without interrupting.
- 2
Empathize with their frustration and acknowledge the inconvenience.
- 3
Apologize for the situation and take responsibility for the repair.
- 4
Offer a solution, such as a priority follow-up or additional repair at no cost.
- 5
Ensure the customer feels heard and valued before ending the conversation.
Example Answers
I would first listen to the customer carefully to understand their issue. I would empathize with their frustration, express my apologies for the inconvenience, and assure them that I take their concerns seriously. Then, I would offer to schedule a priority inspection and repair of the machine at no extra charge, ensuring they feel taken care of.
You encounter a machine that has multiple possible faults. How do you decide which fault to address first?
How to Answer
- 1
Assess the symptoms to prioritize the most critical issue impacting operation.
- 2
Check for common faults that could cause multiple symptoms.
- 3
Use a process of elimination by testing each potential fault.
- 4
Consult maintenance logs or previous repair history for recurring issues.
- 5
Focus on the fault that poses the highest safety risk or operational downtime.
Example Answers
First, I look at the symptoms and see which fault is causing the most disruption. For example, if the machine is not spinning at all, I would investigate the motor or belt issues first, as those would prevent operation completely.
Don't Just Read Laundry Machine Mechanic Questions - Practice Answering Them!
Reading helps, but actual practice is what gets you hired. Our AI feedback system helps you improve your Laundry Machine Mechanic interview answers in real-time.
Personalized feedback
Unlimited practice
Used by hundreds of successful candidates
If you have multiple service calls at the same time, how do you prioritize your workload?
How to Answer
- 1
Assess the urgency of each service call based on client needs.
- 2
Evaluate the complexity of the job and allocate time accordingly.
- 3
Consider geographical location to minimize travel time.
- 4
Communicate with clients to set realistic expectations.
- 5
Document everything to keep track of your priorities.
Example Answers
I prioritize service calls by first assessing the urgency, dealing with clients who have urgent issues or downtime first. Then, I look at the complexity of the repairs to allocate my time effectively. Finally, I try to schedule calls that are geographically close together to save on travel time.
Imagine you are behind schedule on repairs due to an unexpected complication. How do you manage your time?
How to Answer
- 1
Identify the complication and assess its impact on your schedule.
- 2
Prioritize the repairs based on urgency and importance.
- 3
Communicate with your team or supervisor about the delay.
- 4
Consider breaking tasks into smaller steps to tackle them efficiently.
- 5
Stay focused on the current task to avoid further delays.
Example Answers
I would first determine the specific issue causing the delay and evaluate what repairs are most critical. Then, I'd prioritize those repairs to minimize downtime. I'd communicate with my supervisor about the delay and make sure everyone is aligned on the new schedule. Finally, I'd break the remaining tasks into manageable steps to ensure I stay on track.
What would you do if you notice a repeated issue with a machine that you previously repaired?
How to Answer
- 1
Assess the machine to confirm the issue is consistent.
- 2
Review the repair history to identify any patterns or overlooked factors.
- 3
Consult the manufacturer's guidelines for troubleshooting the specific issue.
- 4
Consider whether additional training or resources are needed for proper repair.
- 5
Document the issue and the steps taken for future reference and to inform your team.
Example Answers
If I notice a repeated issue, I would first assess the machine to ensure the problem is the same. Then, I would review my previous repair notes to see if something was overlooked. I would also look at the manufacturer’s troubleshooting guide for similar cases.
If a machine is leaking water and causing a flood, what is your immediate response?
How to Answer
- 1
First, turn off the power to the machine to ensure safety.
- 2
Identify the source of the leak quickly to prevent further damage.
- 3
Use absorbent materials to contain and soak up the water immediately.
- 4
Notify your supervisor or maintenance team about the situation.
- 5
Document the issue and what actions were taken for future reference.
Example Answers
My first action would be to cut the power to the machine to ensure safety. Then I would quickly locate the source of the leak and use towels or a mop to contain the water. After that, I would inform my supervisor about the situation and follow up by documenting everything.
How would you address a situation where a team member disagrees with your approach to a repair?
How to Answer
- 1
Listen to their concerns and ask for their input on the repair approach
- 2
Explain your reasoning clearly and provide evidence if available
- 3
Look for common ground and find a solution that incorporates both views
- 4
Remain professional and collaborative throughout the discussion
- 5
Keep an open mind and be willing to adjust your approach if necessary
Example Answers
I would first listen to my colleague's concerns to understand their perspective. Then I would explain my approach, highlighting the rationale behind it. If we find common ground, we can agree on a method that works for both of us.
How would you handle a situation where you do not have the necessary parts to complete a repair?
How to Answer
- 1
Assess the situation and the urgency of the repair
- 2
Communicate clearly with the customer about the delay
- 3
Check for alternative solutions or temporary fixes
- 4
Order the necessary parts promptly
- 5
Follow up with the customer once parts arrive and keep them updated
Example Answers
If I find that I don't have the necessary parts for a repair, I first assess how critical the repair is. Then I inform the customer about the situation, let them know I’ll find a solution, and check if a temporary fix is possible. I order the parts immediately and keep the customer updated on the progress.
If you were tasked to fix a machine with no service manual available, how would you proceed?
How to Answer
- 1
Start by inspecting the machine closely for visible issues or signs of wear.
- 2
Utilize your previous experience and knowledge of similar machines to guide your troubleshooting.
- 3
Check for any common failure points or components that typically cause issues.
- 4
Use online resources or forums to search for similar problems and solutions.
- 5
Document your process and findings to create a reference for future repairs.
Example Answers
I would first inspect the machine for any obvious damages or leaks. Then, I would rely on my experience with similar machines to identify common issues. Checking online forums can also provide insights from others who faced similar problems.
Laundry Machine Mechanic Position Details
Recommended Job Boards
ZipRecruiter
www.ziprecruiter.com/Jobs/Laundry-MechanicThese job boards are ranked by relevance for this position.
Related Positions
- Sewing Machine Mechanic
- Appliance Mechanic
- Machine Fixer
- Industrial Mechanic
- Production Mechanic
- Appliance Fixer
- Machine Repairer
- Tool Mechanic
- Pump Mechanic
- Conveyor Mechanic
Similar positions you might be interested in.
Ace Your Next Interview!
Practice with AI feedback & get hired faster
Personalized feedback
Used by hundreds of successful candidates
Ace Your Next Interview!
Practice with AI feedback & get hired faster
Personalized feedback
Used by hundreds of successful candidates