Top 32 Sewing Machine Mechanic Interview Questions and Answers [Updated 2025]
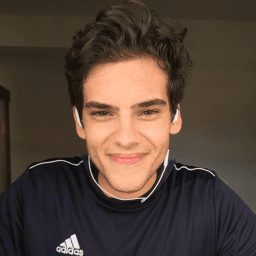
Andre Mendes
•
March 30, 2025
Preparing for a sewing machine mechanic interview can be daunting, but with the right preparation, you can confidently tackle any question thrown your way. In this blog post, we compile the most common interview questions for the sewing machine mechanic role, complete with example answers and effective tips to help you stand out. Whether you're a seasoned professional or new to the field, this guide will equip you with the insights needed to impress your interviewers.
Download Sewing Machine Mechanic Interview Questions in PDF
To make your preparation even more convenient, we've compiled all these top Sewing Machine Mechanicinterview questions and answers into a handy PDF.
Click the button below to download the PDF and have easy access to these essential questions anytime, anywhere:
List of Sewing Machine Mechanic Interview Questions
Behavioral Interview Questions
Can you describe a time when you diagnosed a complex issue with a sewing machine?
How to Answer
- 1
Start by briefly describing the sewing machine model and the problem.
- 2
Explain the steps you took to diagnose the issue methodically.
- 3
Mention any tools or techniques you used during the diagnosis.
- 4
Share the outcome and how the solution benefited the user.
- 5
Conclude with what you learned from the experience.
Example Answers
I worked on a Brother sewing machine that was skipping stitches. I started by checking the needle, then examined the tension settings. I used a tension gauge and found it was too tight. After adjusting, the machine worked perfectly. The customer was very satisfied, and I learned the importance of checking tension early in the process.
Tell me about a time you had to work closely with a team to repair sewing machines under a tight deadline.
How to Answer
- 1
Describe a specific instance with clear details.
- 2
Emphasize communication and teamwork skills.
- 3
Mention the roles of different team members.
- 4
Highlight how you contributed to meeting the deadline.
- 5
Include the outcome and what you learned from the experience.
Example Answers
In a recent project, our team had to repair 50 sewing machines for a client within a week. I coordinated communication between the mechanics, ensuring everyone knew their tasks. I focused on troubleshooting the machines and shared my findings with the team daily, which helped us finish two days early. We received positive feedback from the client, which was motivating.
Don't Just Read Sewing Machine Mechanic Questions - Practice Answering Them!
Reading helps, but actual practice is what gets you hired. Our AI feedback system helps you improve your Sewing Machine Mechanic interview answers in real-time.
Personalized feedback
Unlimited practice
Used by hundreds of successful candidates
When was the last time you faced an unexpected breakdown during a job? How did you handle it?
How to Answer
- 1
Describe a specific incident with context.
- 2
Explain the steps you took to diagnose the problem.
- 3
Mention any tools or techniques used for the repair.
- 4
Highlight the outcome and what you learned.
- 5
Keep it relevant to sewing machines or mechanical work.
Example Answers
In my previous job, a customer's sewing machine suddenly stopped working during a busy day. I quickly assessed the issue by checking the power supply and foot pedal. I used my multimeter to test the electrical components and found a blown fuse. I replaced the fuse, tested the machine, and it was up and running again. This experience reinforced the importance of being prepared for unexpected issues.
Describe an experience where you had to explain a technical issue to a customer who was upset.
How to Answer
- 1
Stay calm and listen to the customer's concerns fully.
- 2
Use simple language to explain the technical issue without jargon.
- 3
Acknowledge the customer's frustration and show empathy.
- 4
Provide a clear solution or next steps to resolve their issue.
- 5
Follow up to ensure the customer is satisfied with the resolution.
Example Answers
I once had a customer who was upset because their sewing machine would not turn on. I listened carefully to their frustrations. I gently explained that it was likely a power issue, avoiding technical jargon, and suggested checking the power cord and outlet. I assured them that I could walk them through it step by step. After they followed my guidance, the machine worked perfectly, and I followed up later to confirm their satisfaction.
Have you ever trained someone else in sewing machine maintenance? What approach did you take?
How to Answer
- 1
Start with a brief overview of the training experience.
- 2
Explain the methods you used, such as hands-on demonstrations.
- 3
Highlight any materials or resources you provided.
- 4
Mention how you assessed their understanding.
- 5
Share the outcome of the training or any feedback received.
Example Answers
Yes, I trained a new technician on sewing machine maintenance. I used hands-on demonstrations for each task and provided a detailed manual. After each session, I had them show me the steps to ensure they understood. They felt confident after our training, and their first performance review was very positive.
Describe a time when you improved the process of sewing machine maintenance or repairs.
How to Answer
- 1
Think of a specific instance when you identified a problem.
- 2
Explain the changes you made to improve the maintenance or repair process.
- 3
Include measurable outcomes or benefits from your changes.
- 4
Be clear about your role in the process.
- 5
Use the STAR method: Situation, Task, Action, Result.
Example Answers
In my last job, we often faced delays due to outdated maintenance schedules. I analyzed the repair logs and proposed a new schedule based on machine usage. This reduced downtime by 20%, improving overall efficiency.
Can you provide an example of taking ownership of a difficult repair task?
How to Answer
- 1
Select a specific repair that was challenging.
- 2
Describe the steps you took to diagnose the issue.
- 3
Explain how you researched or sought help if needed.
- 4
Share the outcome and what you learned from the experience.
- 5
Highlight your responsibility and problem-solving skills.
Example Answers
At a local shop, I repaired a sewing machine that had a faulty tension mechanism. I diagnosed the issue by carefully testing the stitch quality and checking the tension settings. I researched the manual for troubleshooting steps and discovered a common issue with the tension spring. After replacing the spring, the machine worked flawlessly and the owner was very satisfied.
What do you consider your biggest success in your career as a sewing machine mechanic?
How to Answer
- 1
Think of a specific project you completed successfully.
- 2
Focus on quantifiable results, if possible.
- 3
Consider a challenging repair job that led to satisfaction for the customer.
- 4
Highlight any skills or techniques you used that are unique.
- 5
Reflect on how this success contributes to your professional growth.
Example Answers
One of my biggest successes was when I fully restored a vintage sewing machine that no one else could repair. The client was thrilled as it was a family heirloom, and I was able to use my specialized skills to ensure it worked perfectly again.
What interests you the most about working as a sewing machine mechanic?
How to Answer
- 1
Focus on your passion for sewing and machinery.
- 2
Mention problem-solving as a key interest.
- 3
Highlight your desire to help others through repairs.
- 4
Express enthusiasm for continuous learning in the field.
- 5
Relate your experience or skills to the job.
Example Answers
I have always been passionate about sewing and find great satisfaction in fixing machines that help others create. I love troubleshooting issues and learning new techniques to improve my skills.
Don't Just Read Sewing Machine Mechanic Questions - Practice Answering Them!
Reading helps, but actual practice is what gets you hired. Our AI feedback system helps you improve your Sewing Machine Mechanic interview answers in real-time.
Personalized feedback
Unlimited practice
Used by hundreds of successful candidates
Technical Interview Questions
How do you approach diagnosing electrical issues in sewing machines?
How to Answer
- 1
Start by visually inspecting the machine for any obvious signs of damage or wear.
- 2
Check the power source and ensure the machine is properly plugged in and switched on.
- 3
Use a multimeter to test electrical connections and components for continuity.
- 4
Look for any blown fuses or tripped circuit breakers that may indicate electrical issues.
- 5
Consult the sewing machine's manual for specific electrical troubleshooting tips.
Example Answers
I begin by visually checking the machine for obvious issues, like frayed wires or burned components. Then, I ensure it's plugged in and powered properly. If everything looks good, I use a multimeter to check for power in the machine's circuits.
What tools do you consider essential for repairing sewing machines?
How to Answer
- 1
List specific hand tools like screwdrivers and pliers.
- 2
Mention diagnostic tools such as multimeters or stitch analyzers.
- 3
Include cleaning tools such as brushes and oilers.
- 4
Highlight safety equipment like goggles and gloves.
- 5
Discuss the importance of a workbench with good lighting.
Example Answers
I believe essential tools for sewing machine repair include both screwdrivers and pliers for disassembly, a multimeter for electrical diagnostics, and brushes for cleaning out lint and debris.
Don't Just Read Sewing Machine Mechanic Questions - Practice Answering Them!
Reading helps, but actual practice is what gets you hired. Our AI feedback system helps you improve your Sewing Machine Mechanic interview answers in real-time.
Personalized feedback
Unlimited practice
Used by hundreds of successful candidates
Can you explain the function of the tension mechanism in a sewing machine?
How to Answer
- 1
Understand that the tension mechanism controls the tightness of the thread during sewing.
- 2
Explain that it affects both the upper and lower threads to create balanced stitches.
- 3
Mention that too much tension can cause thread breakage and too little can lead to loose stitches.
- 4
Use terminology like 'tension dial' or 'adjustment' when discussing the mechanism.
- 5
Provide an example of how adjusting the tension can improve stitch quality.
Example Answers
The tension mechanism in a sewing machine is responsible for controlling how tightly the thread is pulled as it sews. It can be adjusted using a tension dial to ensure that both the upper and lower threads are balanced for effective stitching. If the tension is too tight, the thread may break; if it’s too loose, stitches can come undone. For instance, if I'm sewing a lightweight fabric, I might lower the tension to avoid puckering.
What steps would you take if a sewing machine repeatedly skips stitches?
How to Answer
- 1
Check and replace the needle if it's bent or dull.
- 2
Ensure the needle is properly installed and suitable for the fabric.
- 3
Adjust the thread tension to the appropriate level for the fabric thickness.
- 4
Clean the machine and ensure there is no lint or thread blocking the feed dogs.
- 5
Test the machine on sample fabric after making adjustments.
Example Answers
If a sewing machine skips stitches, I would first check the needle to see if it needs replacing or if it's the right type for the fabric. Then, I would adjust the thread tension to ensure it's appropriate for the material. Finally, I would clean the machine to remove any lint that might be causing the issue.
What experience do you have with the electrical systems in automated sewing machines?
How to Answer
- 1
Discuss any formal training or certifications you have in electrical systems.
- 2
Mention specific models or types of automated sewing machines you have worked on.
- 3
Highlight relevant troubleshooting or repair experiences.
- 4
Include any preventative maintenance tasks you've performed on electrical systems.
- 5
Emphasize your ability to read electrical schematics or manuals.
Example Answers
I completed a technical training program focused on sewing machine technology, which included comprehensive modules on electrical systems. I've worked on various models, including Juki and Brother machines, where I diagnosed and repaired electrical faults.
What are common symptoms of a sewing machine that is not threading correctly?
How to Answer
- 1
Identify visible signs of thread misalignment or jamming.
- 2
Explain the types of stitching issues that arise, like skipped stitches.
- 3
Mention how bobbin issues contribute to threading problems.
- 4
Refer to potential tension problems affecting stitching.
- 5
Discuss the importance of checking the threading path for correctness.
Example Answers
Common symptoms include visible jamming of thread near the needle or bobbin, inconsistent stitch quality, skipped stitches, or loose threads. I would check the threading path and ensure the tension settings are correctly adjusted.
Are you familiar with any software used in modern sewing machines for diagnostic purposes?
How to Answer
- 1
Research commonly used software in sewing machines like Bernina's BERNINA Toolbox or Brother's PE-Design.
- 2
Mention specific diagnostic features of these software like stitch analysis or error reports.
- 3
Explain any experience you have using such software during maintenance or troubleshooting.
- 4
Highlight your ability to adapt to new software for sewing machine diagnostics.
- 5
Show enthusiasm for learning about the latest technology in sewing machines.
Example Answers
Yes, I am familiar with BERNINA Toolbox, which provides diagnostic tools for error reporting and stitch analysis, and I have used it during machine maintenance.
How long have you been working with industrial sewing machines, and what brands are you most familiar with?
How to Answer
- 1
State your total years of experience clearly.
- 2
Mention specific brands you have worked with, highlighting your expertise.
- 3
Include any relevant training or certifications related to sewing machines.
- 4
If possible, share a brief example of your work with a particular machine.
- 5
Be honest about your experience level while focusing on strengths.
Example Answers
I have been working with industrial sewing machines for over 5 years. I'm most familiar with brands like Juki, Brother, and Consew. I have worked extensively on Juki machines in a factory setting, performing routine maintenance and troubleshooting.
How do you manage parts inventory when working as a sewing machine mechanic?
How to Answer
- 1
Keep a detailed log of parts used for each job to track consumption.
- 2
Regularly assess inventory levels to anticipate reordering needs.
- 3
Use an organized storage system for easy access to frequently used parts.
- 4
Establish relationships with suppliers for quick restocking.
- 5
Implement a first-in, first-out system to reduce obsolescence.
Example Answers
I maintain a detailed parts log for each job, which helps me track what I use and forecast reorders. I regularly check inventory to ensure I have essential parts in stock.
What advanced features of modern sewing machines do you think require special knowledge to repair?
How to Answer
- 1
Identify specific advanced features like computerized systems or automatic tension adjustment.
- 2
Mention the importance of understanding software for machines with programmable settings.
- 3
Discuss the significance of needle and thread compatibility with machine functions.
- 4
Emphasize skills in diagnosing electronic issues versus mechanical ones.
- 5
Highlight the need for proper training or certification for advanced repairs.
Example Answers
Modern sewing machines have features like computerized settings and automatic tension. Repairing these requires knowledge of both electronics and software, as well as the correct thread and needle combinations to ensure optimal performance.
Don't Just Read Sewing Machine Mechanic Questions - Practice Answering Them!
Reading helps, but actual practice is what gets you hired. Our AI feedback system helps you improve your Sewing Machine Mechanic interview answers in real-time.
Personalized feedback
Unlimited practice
Used by hundreds of successful candidates
What are the primary components of a sewing machine that you regularly service?
How to Answer
- 1
Identify key components such as the needle, feed dogs, and bobbin case.
- 2
Explain the specific issues you address with each component.
- 3
Mention the importance of regular maintenance for optimal performance.
- 4
Include your experience in troubleshooting common problems.
- 5
Highlight any specialized tools or techniques you use.
Example Answers
I regularly service the needle for dullness, the feed dogs for proper movement, and the bobbin case to prevent jams, ensuring smooth operation.
What routine maintenance tasks do you perform on sewing machines to ensure they operate efficiently?
How to Answer
- 1
Highlight the importance of cleaning the machine regularly to prevent dust and lint buildup
- 2
Mention lubricating moving parts according to the manufacturer's specifications
- 3
Discuss inspecting and replacing worn parts such as needles and tension discs
- 4
Emphasize the significance of checking thread tension and alignment
- 5
Include testing the machine after maintenance to ensure it functions properly
Example Answers
I regularly clean the machine to remove lint and dust, lubricate moving parts as per the manual, and check for any worn components like needles and tension discs to ensure smooth operation.
Situational Interview Questions
If you are tasked with repairing several sewing machines in a day but encounter a particularly challenging repair, how would you prioritize your tasks?
How to Answer
- 1
Assess the urgency of each repair based on customer needs
- 2
Identify which machines are quick fixes to save time
- 3
Consider your skill level with the challenging repair
- 4
Communicate with the team if you need assistance or a second opinion
- 5
Plan your day by creating a timeline for repairs, starting with the easiest tasks
Example Answers
I would start by evaluating each machine's repair needs and prioritize based on urgency and customer requests. Quick repairs would go first, then I would set aside specific time slots to tackle the challenging repair later in the day when I could focus completely on it.
Imagine a customer complains that their machine is making strange noises. How would you handle the situation during the service call?
How to Answer
- 1
Listen carefully to the customer’s description of the noises
- 2
Ask clarifying questions to understand the context of the issue
- 3
Perform a visual inspection of the sewing machine
- 4
Test the machine to replicate the noise if possible
- 5
Explain to the customer what you find and the steps you will take to fix it
Example Answers
I would start by listening to the customer's description of the noise and asking specific questions about when it occurs. Then, I would inspect the machine visually to check for any obvious issues like loose parts. If I can replicate the noise, I'll test it and diagnose the problem from there. Finally, I would explain what I've found and propose a solution to fix it.
Don't Just Read Sewing Machine Mechanic Questions - Practice Answering Them!
Reading helps, but actual practice is what gets you hired. Our AI feedback system helps you improve your Sewing Machine Mechanic interview answers in real-time.
Personalized feedback
Unlimited practice
Used by hundreds of successful candidates
How would you handle a disagreement with a team member about the best approach to fix a sewing machine?
How to Answer
- 1
Listen carefully to their viewpoint to understand their reasoning.
- 2
Share your perspective politely and explain your approach.
- 3
Suggest a collaborative solution like testing both methods.
- 4
Focus on the goal of fixing the machine effectively together.
- 5
Stay professional and avoid personal conflicts in your discussion.
Example Answers
I would first listen to my team member's approach to understand their reasoning. Then I’d share my perspective and suggest that we could test both methods to see which one works best.
You are out of a critical part needed for repairs. What strategies would you employ to ensure the job gets done?
How to Answer
- 1
Check local suppliers and distributors for immediate availability
- 2
Reach out to colleagues or contacts in the industry for spare parts or alternatives
- 3
Consider using temporary fixes or substitutes until the part is obtained
- 4
Communicate with customers about the delay and manage their expectations
- 5
Plan ahead to avoid running out of critical parts in the future by keeping an inventory
Example Answers
I would first check with local suppliers or distributors to see if they have the part in stock. If not available, I would contact colleagues in the industry to borrow or source the needed part temporarily.
If you notice a safety hazard in the workshop while repairing machines, what steps would you take?
How to Answer
- 1
Identify the specific safety hazard clearly.
- 2
Inform your supervisor or the safety officer immediately.
- 3
Ensure the area is clear and mark it to prevent others from approaching.
- 4
Assess if you can safely mitigate the hazard temporarily.
- 5
Follow up to ensure the issue is resolved and the area is safe.
Example Answers
If I noticed a safety hazard, I would first identify what the hazard is and then inform my supervisor immediately. I would also mark the area to keep others away until it's addressed.
If a customer insists on a specific repair method that you believe is not appropriate, how would you address it?
How to Answer
- 1
Listen to the customer's concerns and understand their reasoning.
- 2
Acknowledge their request respectfully to show you value their input.
- 3
Explain your professional expertise and the reasons for your recommended repair method.
- 4
Offer alternative solutions that align with their needs and your professional judgment.
- 5
Seek to find common ground and assure them of the quality of the service.
Example Answers
I would first listen carefully to the customer's reasoning for their preferred method. Then, I would explain why I believe that method may not be appropriate, sharing my expertise on the subject. Lastly, I'd suggest an alternative that ensures the best outcome for their machine.
How would you handle repairing a sewing machine that is critical for production if you are running out of time?
How to Answer
- 1
Assess the most common issues first to save time.
- 2
Communicate with your team about the urgency.
- 3
Prioritize repairs that will get the machine back in operation quickly.
- 4
Focus on temporary fixes that allow production to continue.
- 5
Plan to do a thorough inspection after urgent production needs are met.
Example Answers
I would quickly assess common issues like thread jams or needle problems first, as these can often be fixed quickly. I would inform my team about the situation so we can coordinate production while I work on the machine. If necessary, I would implement a temporary fix to keep the production line running.
If a customer provided you feedback that your repairs were not effective, how would you react?
How to Answer
- 1
Listen carefully to the customer's feedback without interrupting.
- 2
Acknowledge their feelings and express understanding of their frustration.
- 3
Ask specific questions to understand the issue and clarify the details.
- 4
Offer a solution, such as a re-evaluation or additional repairs at no cost.
- 5
Follow up to ensure the customer is satisfied after the resolution.
Example Answers
I would first listen to the customer's concerns fully and acknowledge their frustration. Then, I would ask specific questions to pinpoint what issues they are experiencing. I would offer to review the machine again and repair any unresolved problems at no extra charge.
If you need help from a colleague on a complex repair but they are busy, how would you handle the situation?
How to Answer
- 1
Assess the urgency of the repair and if it can wait.
- 2
Consider if you can solve the problem independently with available resources.
- 3
Communicate with the colleague about the issue briefly and ask for a convenient time to discuss.
- 4
Seek assistance from other team members if available and knowledgeable.
- 5
Document your observations and attempts to fix the problem for future reference.
Example Answers
I would first evaluate whether the repair can wait until my colleague is available. If it’s not urgent, I’d note down the details and approach them later. If it's urgent, I’d try to troubleshoot the problem using the manuals or resources I have and, if necessary, I would ask another team member for help.
You have been asked to work on a model of sewing machine you have never seen before. What would you do?
How to Answer
- 1
Research the specific model online to gather information and manuals.
- 2
Consult with colleagues or experienced technicians for insights.
- 3
Examine the machine carefully to understand its components and functions.
- 4
Test the machine functions step-by-step to identify issues.
- 5
Document any unique findings for future reference.
Example Answers
I would start by searching for the model online to find any manuals or resources available. Then, I would reach out to team members who might have experience with that model to get their insights. Once I get familiar with the basics, I would examine the machine closely and run tests to pinpoint any problems.
Don't Just Read Sewing Machine Mechanic Questions - Practice Answering Them!
Reading helps, but actual practice is what gets you hired. Our AI feedback system helps you improve your Sewing Machine Mechanic interview answers in real-time.
Personalized feedback
Unlimited practice
Used by hundreds of successful candidates
Sewing Machine Mechanic Position Details
Salary Information
Average Salary
$23,440
Source: Talent.com
Recommended Job Boards
These job boards are ranked by relevance for this position.
Related Positions
Ace Your Next Interview!
Practice with AI feedback & get hired faster
Personalized feedback
Used by hundreds of successful candidates
Ace Your Next Interview!
Practice with AI feedback & get hired faster
Personalized feedback
Used by hundreds of successful candidates