Top 31 Machine Fixer Interview Questions and Answers [Updated 2025]
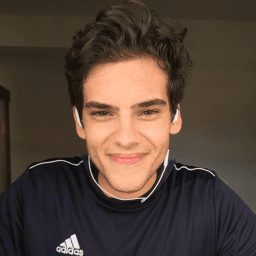
Andre Mendes
•
March 30, 2025
Preparing for a 'Machine Fixer' interview can be daunting, but this blog post is here to help you succeed. We've compiled the most common interview questions for this vital role, offering example answers and expert tips on how to respond effectively. Whether you're a seasoned professional or new to the field, this guide will equip you with the insights needed to impress your interviewers and secure the job.
Download Machine Fixer Interview Questions in PDF
To make your preparation even more convenient, we've compiled all these top Machine Fixerinterview questions and answers into a handy PDF.
Click the button below to download the PDF and have easy access to these essential questions anytime, anywhere:
List of Machine Fixer Interview Questions
Situational Interview Questions
Imagine you are working on a machine that suddenly breaks down during production. What steps would you take to address the situation?
How to Answer
- 1
Stay calm and assess the machine's condition quickly
- 2
Identify the immediate cause of the breakdown
- 3
Inform your supervisor and relevant colleagues about the issue
- 4
Implement a basic troubleshooting process if possible
- 5
Document the incident and the steps taken for future reference
Example Answers
I would first stay calm and check for any obvious signs of failure. Then, I would identify what caused the breakdown and inform my supervisor about it. If it's safe to do so, I would perform basic troubleshooting to see if I can fix it quickly, and finally, I would document what happened.
If you are unable to fix a machine with the tools on hand, what would your next steps be?
How to Answer
- 1
Assess the problem to ensure you understand the issue thoroughly.
- 2
Check for any additional tools or resources available nearby before seeking help.
- 3
Document the steps you have taken so far for clarity.
- 4
Reach out to a colleague or supervisor for assistance if necessary.
- 5
Consider whether the machine can be temporarily shut down or if there are safety concerns.
Example Answers
I would first assess the issue to confirm what is wrong with the machine. Then, I'd check if there are any additional tools or resources I could use. If I still can't fix it, I would document everything I've done and consult a colleague or supervisor for their insight.
Don't Just Read Machine Fixer Questions - Practice Answering Them!
Reading helps, but actual practice is what gets you hired. Our AI feedback system helps you improve your Machine Fixer interview answers in real-time.
Personalized feedback
Unlimited practice
Used by hundreds of successful candidates
How would you handle a situation where you identify a safety hazard while repairing a machine?
How to Answer
- 1
Identify the hazard and assess the risk it poses.
- 2
Immediately stop all work and inform your supervisor.
- 3
Implement safety measures to secure the area around the hazard.
- 4
Document the hazard and actions taken in your maintenance log.
- 5
Ensure that the hazard is corrected before resuming repairs.
Example Answers
If I identify a safety hazard while repairing a machine, I would first assess the risk and then stop all work immediately. I would notify my supervisor about the issue and make sure the area is secured. I’d document the hazard thoroughly and ensure it is fixed before continuing.
Suppose there is a recurring problem with a machine despite previous repairs. How would you address this issue?
How to Answer
- 1
Investigate the root cause of the problem through thorough analysis
- 2
Review previous repair logs to understand what was attempted
- 3
Consult with colleagues or specialists for insights on persistent issues
- 4
Develop a comprehensive repair plan that addresses underlying issues
- 5
Implement monitoring to track the machine's performance after repairs
Example Answers
I would start by analyzing the machine's previous repair records to identify patterns. Then, I would investigate the root cause, possibly by disassembling parts of the machine to inspect for underlying issues. Consulting with colleagues for different perspectives can also be valuable before finalizing a comprehensive repair plan.
How would you approach working with an engineer to solve a machine problem that requires both mechanical and software knowledge?
How to Answer
- 1
Establish clear communication with the engineer.
- 2
Identify the specific mechanical and software issues separately.
- 3
Propose a collaborative approach to troubleshooting.
- 4
Utilize diagrams or flowcharts to visualize the problem.
- 5
Document the process and findings for future reference.
Example Answers
I would start by setting up a meeting with the engineer to discuss the problem in detail, separating the mechanical and software aspects. Then, we could work together, perhaps creating a flowchart to visualize the issue and develop a step-by-step troubleshooting plan.
How would you prioritize your work if multiple machines broke down at the same time?
How to Answer
- 1
Identify which machines impact production the most.
- 2
Assess the complexity of each issue to estimate repair time.
- 3
Communicate with your supervisor to confirm priorities.
- 4
Work on machines that can be repaired quickly to minimize downtime.
- 5
Document the breakdowns for future reference and troubleshooting.
Example Answers
I would first determine which machine's breakdown affects production the most, like the assembly line. Then, I would check the severity of each issue and quickly repair the simplest ones to reduce downtime, all while keeping my supervisor informed about my actions.
How would you handle a situation where a client is unhappy with the repairs performed on their machinery?
How to Answer
- 1
Listen carefully to the client's concerns without interrupting.
- 2
Apologize sincerely for any inconvenience caused by the repairs.
- 3
Assess the situation to understand the cause of the issue.
- 4
Offer a solution, such as a follow-up visit or free repair if warranted.
- 5
Ensure the client feels valued by keeping communication open throughout the process.
Example Answers
I would start by listening closely to the client's concerns. I'd apologize for any inconvenience and then ask clarifying questions to understand their issue. After identifying the problem, I'd explain how I plan to resolve it and schedule a follow-up visit if necessary.
If you were tasked with overhauling an old machine, what factors would you consider in your planning process?
How to Answer
- 1
Assess the current condition and performance of the machine
- 2
Identify the specific goals of the overhaul
- 3
Consider the availability of parts and technical support
- 4
Evaluate the cost implications and budget
- 5
Plan for safety and compliance with regulations
Example Answers
I would first assess the machine's current condition to understand what components need replacement or repair. Next, I would identify the goals of the overhaul, like improving efficiency or reliability. Then, I would check for available parts and technical support to ensure feasibility. I would also look at the budget to keep costs under control, and finally, I would ensure that all safety regulations are being followed throughout the process.
If you had to work with a difficult colleague while fixing a machine, how would you manage the relationship to ensure project success?
How to Answer
- 1
Stay calm and focus on the task at hand.
- 2
Listen actively to understand their perspective.
- 3
Communicate clearly and respectfully to avoid misunderstandings.
- 4
Find common ground to foster collaboration.
- 5
Suggest regular check-ins to align on progress and issues.
Example Answers
I would listen to my colleague's concerns first, showing that I value their input. Then, I would communicate openly about the project goals and suggest check-ins to make sure we're both on the same page.
Behavioral Interview Questions
Can you describe a time when you had to troubleshoot a complex machine issue? What was the problem and how did you resolve it?
How to Answer
- 1
Choose a specific example from your previous experience
- 2
Explain the symptoms of the machine issue clearly
- 3
Describe the steps you took to diagnose the problem
- 4
Highlight the resolution and what you learned from the experience
- 5
Mention any tools or methods used during troubleshooting
Example Answers
In my last job, the assembly line machine was frequently stopping. I noticed the sensors were not responding. I checked wiring and found a loose connection, reattached it, and the machine worked flawlessly afterwards.
Tell me about a time you worked with a team to fix a machine. What role did you play and what was the outcome?
How to Answer
- 1
Choose a specific incident where teamwork was essential.
- 2
Clearly define your role and contributions within the team.
- 3
Highlight the problem with the machine and how it impacted operations.
- 4
Describe the steps taken as a team to resolve the issue.
- 5
Conclude with the positive outcome and what you learned from the experience.
Example Answers
In my previous job, we faced a breakdown in a critical packaging machine. I was assigned as the lead technician. I organized a meeting to assess the issue and delegated tasks based on our strengths. We identified a faulty conveyor belt, replaced it, and tested the machine. The result was a successful operation with no further downtime.
Don't Just Read Machine Fixer Questions - Practice Answering Them!
Reading helps, but actual practice is what gets you hired. Our AI feedback system helps you improve your Machine Fixer interview answers in real-time.
Personalized feedback
Unlimited practice
Used by hundreds of successful candidates
Describe a situation where you disagreed with a colleague about the best approach to fix a machine. How was the situation resolved?
How to Answer
- 1
Choose a relevant example from your experience
- 2
Clearly explain the disagreement and your perspective
- 3
Highlight how you respected the colleague's opinion
- 4
Describe how you collaboratively reached a solution
- 5
Conclude with the outcome and what you learned
Example Answers
In a previous role, I disagreed with a colleague on how to tackle a recurring issue in our CNC machine. I believed a software update was necessary, while they thought it was a hardware issue. We discussed our viewpoints in a meeting, and I suggested we first gather data to analyze the problem. After evaluating, we found the software update fixed the issue, which improved our production efficiency. This taught me the importance of data in decision-making.
Give an example of a time you had to learn a new technology or method quickly in order to fix a machine. How did you handle it?
How to Answer
- 1
Identify a specific experience where you learned quickly under pressure.
- 2
Highlight the new technology or method you learned.
- 3
Explain your approach to learning it, such as using manuals, online resources, or asking colleagues.
- 4
Describe the outcome of the situation and how it helped in fixing the machine.
- 5
Convey what you learned from the experience and how it applies in the future.
Example Answers
In my previous job, a critical machine broke down unexpectedly, and I had to learn how to operate a new diagnostic tool. I quickly read the user manual and watched tutorial videos online for a few hours. Then, I performed the diagnostics, identified the issue, and successfully fixed the machine. This experience taught me the importance of being adaptable and efficient in learning new techniques.
Have you ever led a project to repair or maintain machinery? How did you ensure everyone was on track?
How to Answer
- 1
Start with a brief overview of the project and your role.
- 2
Mention specific tasks assigned to team members.
- 3
Describe how you tracked progress, such as meetings or checklists.
- 4
Highlight any challenges faced and how you overcame them.
- 5
Conclude with the successful outcome of the project.
Example Answers
In my previous role, I led a project to repair an outdated conveyor system. I assigned tasks based on expertise and created a timeline for each one. Weekly check-in meetings ensured everyone was on track. We faced delays due to parts availability, but we resolved this by sourcing from alternative suppliers. The project was completed ahead of schedule and improved our production flow significantly.
Describe a time when you had to explain a complex machine issue to a non-technical team member. How did you ensure they understood?
How to Answer
- 1
Identify the machine issue clearly and avoid jargon.
- 2
Break down the explanation into simple steps.
- 3
Use analogies or examples that relate to their experience.
- 4
Encourage questions to ensure understanding.
- 5
Check their comprehension by asking them to summarize.
Example Answers
When our assembly line jammed, I explained to the marketing team that it was like a traffic jam. I outlined the cause step-by-step and then checked if they had any questions. After I explained, I asked them to describe what they understood, and they did so accurately.
Can you give an example of a time you implemented a new solution or method when fixing a machine that improved efficiency?
How to Answer
- 1
Start with a specific situation where you identified a problem.
- 2
Describe the solution or method you implemented clearly.
- 3
Quantify the improvement in efficiency, if possible.
- 4
Highlight any collaboration with team members or other departments.
- 5
Conclude with the impact of the solution on overall operations.
Example Answers
In my previous role at a manufacturing plant, we faced frequent downtime with a conveyor belt system. I analyzed the mechanical components and noticed that the lubrication frequency was insufficient. I proposed a schedule for more frequent lubrication and installed an automatic lubrication system. This reduced our downtime by 30% and improved the overall efficiency of the production line.
Describe a time when you took the initiative to improve a machine or repair process.
How to Answer
- 1
Identify a specific machine or process issue you noticed.
- 2
Explain what steps you took to address the issue.
- 3
Highlight any teamwork involved if applicable.
- 4
Mention the outcome or improvement resulting from your initiative.
- 5
Use metrics or data to show the impact of your actions if possible.
Example Answers
At my last job, I noticed that the assembly line machine frequently jammed, causing delays. I investigated and found the root cause was outdated software. I suggested updating the software, coordinated with the IT team, and reduced downtime by 30%.
Tell me about a time when you had to be particularly patient while troubleshooting a machine issue.
How to Answer
- 1
Identify a specific machine issue you encountered.
- 2
Explain the steps you took to diagnose the problem methodically.
- 3
Highlight the duration and challenges you faced to emphasize patience.
- 4
Conclude with the resolution and what you learned from the experience.
- 5
Keep the focus on your problem-solving approach and resilience.
Example Answers
In my last role, I worked on a printing machine that kept jamming. I took time to investigate the feed mechanism carefully, which involved removing various parts and testing them individually. It took several hours to narrow down the issue to a single worn-out rubber roller. My patience paid off as it helped ensure the overall quality of our prints and reduced future jams.
Can you describe how you stay updated with the latest technology and methods in machine repair?
How to Answer
- 1
Attend industry workshops and training sessions regularly
- 2
Follow reputable online forums and communities dedicated to machine repair
- 3
Subscribe to industry magazines and newsletters for updates
- 4
Take online courses to learn about new technologies in machinery
- 5
Network with other professionals to share knowledge and experiences
Example Answers
I stay updated by attending workshops and training sessions whenever they are available, which allows me to learn hands-on about the latest technologies. I also follow several online forums where experts discuss new methods in machine repair.
Don't Just Read Machine Fixer Questions - Practice Answering Them!
Reading helps, but actual practice is what gets you hired. Our AI feedback system helps you improve your Machine Fixer interview answers in real-time.
Personalized feedback
Unlimited practice
Used by hundreds of successful candidates
Technical Interview Questions
What are the essential tools you typically use for machine repairs? Can you explain their purposes?
How to Answer
- 1
List the most common tools you use in machine repairs.
- 2
Explain the purpose of each tool clearly and concisely.
- 3
Mention any specific tools related to the types of machines you repair.
- 4
Emphasize your familiarity and expertise with these tools.
- 5
Consider giving a brief anecdote about a time you used one of these tools.
Example Answers
I typically use a socket set for loosening or tightening bolts, a multimeter for checking electrical circuits, and wrenches for adjusting parts. For instance, I used a multimeter recently to diagnose a faulty sensor on a conveyor machine, which saved us a lot of time.
How do you approach diagnosing mechanical failures? Describe your step-by-step process.
How to Answer
- 1
Start with visual inspection of the equipment for obvious signs of damage.
- 2
Consult equipment documentation and error codes to gather initial data.
- 3
Isolate the problem by testing individual components systematically.
- 4
Use diagnostic tools such as multimeters or pressure gauges to measure performance.
- 5
Document findings and note potential solutions or repairs needed.
Example Answers
I begin by visually inspecting the equipment for any obvious signs of wear or damage. Next, I check the error codes or messages on the control panel, which gives me initial clues. I then isolate the suspect components, performing tests on them individually before using tools like multimeters to measure their performance. Finally, I document everything and propose a plan for repair based on my findings.
Don't Just Read Machine Fixer Questions - Practice Answering Them!
Reading helps, but actual practice is what gets you hired. Our AI feedback system helps you improve your Machine Fixer interview answers in real-time.
Personalized feedback
Unlimited practice
Used by hundreds of successful candidates
What safety precautions do you follow when repairing machines?
How to Answer
- 1
Always wear appropriate personal protective equipment such as gloves and goggles
- 2
Ensure machines are powered down and locked out before starting repairs
- 3
Follow proper lifting techniques when handling heavy components
- 4
Keep the workspace clean and organized to avoid accidents
- 5
Be aware of potential hazards like sharp edges or moving parts during repairs
Example Answers
I wear gloves and goggles when repairing to protect myself from sharp edges and flying debris. I also ensure that the machine is powered down and locked out to prevent accidental startup.
What is preventative maintenance, and how do you implement it in machine fixing?
How to Answer
- 1
Define preventative maintenance clearly and concisely.
- 2
Mention specific tasks involved in preventative maintenance.
- 3
Provide examples of how it helps reduce machine downtime.
- 4
Discuss the importance of regular inspections and schedules.
- 5
Emphasize record-keeping and follow-up actions.
Example Answers
Preventative maintenance is the practice of regularly inspecting and servicing machines to prevent unexpected failures. I implement it by performing scheduled checks, lubricating moving parts, and replacing worn components before they cause breakdowns. This approach helps keep machines running smoothly and minimizes downtime.
Explain the differences between a caliper and a micrometer. In what scenarios would you use each?
How to Answer
- 1
Identify the main function of each tool.
- 2
Mention the typical measurement ranges for calipers and micrometers.
- 3
Discuss the precision level of each measurement tool.
- 4
Provide practical examples of when to use them.
- 5
Keep the explanation clear and concise.
Example Answers
A caliper measures outside, inside, and depth dimensions, usually up to 6 inches or more, with a precision of about 0.01 inches. I would use a caliper for general measurements, such as checking the size of a screw.
What is the difference between AC and DC motors? How do you troubleshoot issues with each?
How to Answer
- 1
Define AC and DC motors clearly and concisely.
- 2
Mention key differences such as power supply, construction, and applications.
- 3
Explain the primary troubleshooting steps for both motor types.
- 4
Discuss common issues encountered with AC and DC motors.
- 5
Highlight the tools used for troubleshooting.
Example Answers
AC motors run on alternating current and are often used in industrial applications, while DC motors use direct current and are common in smaller devices. To troubleshoot AC motors, check the power supply and connections first, and look for tripped circuit breakers. For DC motors, ensure the brushes are making proper contact and check the supply voltage.
Can you explain how hydraulic systems work? What common issues do you encounter?
How to Answer
- 1
Start with a clear definition of hydraulic systems focusing on fluid pressure.
- 2
Explain the main components: pump, cylinder, and valves.
- 3
Mention basic principles like Pascal's law regarding pressure transmission.
- 4
Discuss common issues such as leaks, air in the system, and pump failure.
- 5
Provide a brief example or scenario to illustrate a problem and solution.
Example Answers
Hydraulic systems use fluid under pressure to transmit power. They consist of a pump, which pushes fluid through pipes to a cylinder. Common issues include leaks, which can lead to pressure loss, and air bubbles in the fluid that can cause erratic movement.
What steps do you take during a routine inspection of machinery?
How to Answer
- 1
Start by checking for obvious visible issues like leaks or wear and tear
- 2
Inspect all safety guards and emergency stops to ensure they are functional
- 3
Listen for unusual sounds while the machine operates to detect potential problems
- 4
Review the machine's maintenance logs for any past issues or needed repairs
- 5
Test all control systems to confirm they respond correctly and safely
Example Answers
During a routine inspection, I first look for any visible leaks or damaged parts. Then, I make sure that all safety guards are in place and functional. Next, I listen for any unusual sounds while the machine is running, and I check the maintenance logs for any recent issues.
How do you measure the performance of a machine post-repair to ensure it operates correctly?
How to Answer
- 1
Inspect machine functionality to check for smooth operation.
- 2
Run diagnostic tests or software to evaluate performance metrics.
- 3
Observe the machine under load to see if it maintains efficiency.
- 4
Compare performance against specifications to ensure it meets standards.
- 5
Document results and any discrepancies for future reference.
Example Answers
I first perform a visual inspection to ensure all components are functioning smoothly. Then, I run diagnostic tests to check performance metrics. After that, I operate the machine under load to verify it meets the specified efficiency standards.
What types of welding techniques are you familiar with, and when do you use them in machine repair?
How to Answer
- 1
List specific welding techniques you know, like MIG, TIG, or Stick welding.
- 2
Explain the context of each technique: material type, thickness, and repair situations.
- 3
Mention your experience with each technique, including any projects or repairs you've completed.
- 4
Highlight safety practices you follow during welding.
- 5
Stay concise and focused on how your skills relate to the job requirements.
Example Answers
I am familiar with MIG welding, which I use for repairing thin metals and structures due to its speed and ease. For tougher materials like stainless steel, I opt for TIG welding, which offers precision. I've successfully repaired several machine parts using both techniques on various projects.
Don't Just Read Machine Fixer Questions - Practice Answering Them!
Reading helps, but actual practice is what gets you hired. Our AI feedback system helps you improve your Machine Fixer interview answers in real-time.
Personalized feedback
Unlimited practice
Used by hundreds of successful candidates
How do you use software tools in conjunction with mechanical repairs? Can you give an example?
How to Answer
- 1
Identify specific software tools you have used in mechanical repairs
- 2
Explain how these tools assist in diagnosis or repair processes
- 3
Give a concrete example where you successfully integrated software with mechanical work
- 4
Mention any metrics or outcomes that improved due to using software
- 5
Keep the explanation clear and concise, focusing on the benefit
Example Answers
I regularly use diagnostic software like AutoCAD or SolidWorks to analyze mechanical systems. For example, when I was repairing a conveyor belt system, I used CAD software to visualize the components and identify wear points before physically inspecting them. This approach saved time and helped prevent further damage.
What is the function of a spindle in a machine tool?
How to Answer
- 1
Define what a spindle is in the context of machine tools.
- 2
Explain the primary role of a spindle in operations like drilling or milling.
- 3
Mention the types of spindles and their relevance to different tasks.
- 4
Discuss how spindles affect precision and efficiency in machining.
- 5
Provide examples of spindles used in specific machine tools.
Example Answers
A spindle is a rotating component of a machine tool that holds and drives the cutting tool. Its main function is to facilitate the cutting process by providing the necessary rotational motion for tasks like drilling or milling, ensuring precision and effectiveness in machining operations.
Machine Fixer Position Details
Related Positions
- Machine Repairer
- Tool Mechanic
- Appliance Fixer
- Fixer
- Laundry Machine Mechanic
- Machine Tool Rebuilder
- Production Mechanic
- Sewing Machine Mechanic
- Maintenance Repairman
- Frame Fixer
Similar positions you might be interested in.
Ace Your Next Interview!
Practice with AI feedback & get hired faster
Personalized feedback
Used by hundreds of successful candidates
Ace Your Next Interview!
Practice with AI feedback & get hired faster
Personalized feedback
Used by hundreds of successful candidates