Top 31 Maintenance Helper Interview Questions and Answers [Updated 2025]
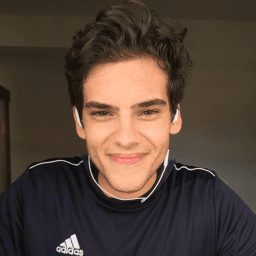
Andre Mendes
•
March 30, 2025
Preparing for a Maintenance Helper interview? This blog post is your ultimate guide, featuring the most common interview questions tailored for the role. Dive into expertly crafted example answers and gain valuable tips on how to respond effectively, ensuring you stand out to potential employers. Whether you're a novice or seasoned professional, these insights will help you confidently tackle any interview challenge.
Download Maintenance Helper Interview Questions in PDF
To make your preparation even more convenient, we've compiled all these top Maintenance Helperinterview questions and answers into a handy PDF.
Click the button below to download the PDF and have easy access to these essential questions anytime, anywhere:
List of Maintenance Helper Interview Questions
Behavioral Interview Questions
Can you describe a time when you worked as part of a team to solve a maintenance issue?
How to Answer
- 1
Think of a specific example from past experiences.
- 2
Highlight your role in the team and your contributions.
- 3
Explain the problem clearly and how the team tackled it together.
- 4
Mention any tools or skills that were essential in resolving the issue.
- 5
Conclude with the positive outcome and what you learned.
Example Answers
In my last job, our team faced a critical HVAC failure in the facility. I was responsible for coordinating with the HVAC technician and documenting all issues. We collaborated to identify the root cause and I assisted by sourcing replacement parts quickly. As a result, we restored comfort in the building within hours and improved our response time for future issues.
Tell me about a challenging maintenance task you faced and how you resolved it.
How to Answer
- 1
Think of a specific task that was difficult.
- 2
Explain the steps you took to address the challenge.
- 3
Mention any tools or skills you used.
- 4
Discuss the outcome and what you learned.
- 5
Keep it concise and focused on your role.
Example Answers
I once had to repair a broken HVAC unit in the middle of summer. I first diagnosed the issue, finding a blown capacitor. I ordered the part and replaced it while ensuring the system was safe to work on. The unit was back up and running quickly, keeping the building cool. I learned the importance of troubleshooting.
Don't Just Read Maintenance Helper Questions - Practice Answering Them!
Reading helps, but actual practice is what gets you hired. Our AI feedback system helps you improve your Maintenance Helper interview answers in real-time.
Personalized feedback
Unlimited practice
Used by hundreds of successful candidates
Have you ever had to quickly adapt to a new situation while performing maintenance? What did you do?
How to Answer
- 1
Describe a specific situation where you had to adapt quickly.
- 2
Focus on the challenges you faced in that situation.
- 3
Explain the steps you took to address the challenge.
- 4
Highlight any positive outcomes or what you learned.
- 5
Keep your response concise and relevant to maintenance work.
Example Answers
Once, while repairing an HVAC unit, I discovered the original part was unavailable. I quickly checked local suppliers, found a compatible part, and completed the repairs ahead of schedule.
Describe a time when you had to communicate maintenance issues to a supervisor. How did you approach it?
How to Answer
- 1
Be specific about the maintenance issue you identified.
- 2
Explain how you communicated the issue clearly.
- 3
Include the actions you suggested to resolve it.
- 4
Mention any follow-up to ensure the issue was addressed.
- 5
Keep your response focused on your role in the situation.
Example Answers
In my previous job, I noticed a leaky faucet in the break room. I approached my supervisor during a shift change and explained the situation clearly, stating the potential water waste. I suggested calling a plumber or checking our maintenance schedules. After a week, I followed up to see if it was fixed, and it was addressed quickly.
Can you give an example of a time you went above and beyond in your maintenance duties?
How to Answer
- 1
Think of a specific incident where you exceeded expectations
- 2
Focus on the impact of your actions on the team or facilities
- 3
Use the STAR method: Situation, Task, Action, Result
- 4
Quantify the results if possible
- 5
Keep it concise and relevant to the job
Example Answers
At my last job, we had a sudden plumbing issue that affected multiple units. I stayed late to not only fix the leak but also to ensure every affected tenant had running water again. This prevented further complaints and improved tenant satisfaction.
Tell me about a time you took initiative in a maintenance project without being asked.
How to Answer
- 1
Identify a specific situation where you saw a problem or opportunity.
- 2
Explain the actions you took and why you felt it was important to act.
- 3
Highlight any positive outcomes from your initiative, such as improvements or efficiencies.
- 4
Use specific details to make your example memorable.
- 5
Keep the focus on your problem-solving and proactive approach.
Example Answers
At my previous job, I noticed that the break room was often messy and uninviting. I took the initiative to organize a cleaning schedule and even created a checklist for maintenance tasks. As a result, the break room became a much more pleasant space, and team morale improved.
Can you provide an example of how you manage multiple maintenance tasks effectively?
How to Answer
- 1
Prioritize tasks based on urgency and impact.
- 2
Create a checklist to keep track of tasks.
- 3
Communicate with team members for assistance if necessary.
- 4
Set a timeframe for each task.
- 5
Review completed tasks and adjust plans as needed.
Example Answers
In my previous role, I managed multiple tasks by first prioritizing them based on urgency. I made a checklist to ensure I didn't overlook anything and set time limits for each task to stay on schedule. For instance, I completed a plumbing issue first before addressing routine inspections.
Describe a situation where you had to work under pressure. How did you manage it?
How to Answer
- 1
Identify a specific situation where you faced pressure.
- 2
Explain the context and the challenge clearly.
- 3
Describe the steps you took to manage the pressure.
- 4
Highlight the outcome and what you learned.
- 5
Keep it brief and focused on your actions.
Example Answers
In my previous job, we faced a sudden work order that required immediate attention. I assessed the tasks, prioritized the most urgent repairs, and communicated with my team to delegate responsibilities efficiently. We completed the tasks under tight deadlines and received positive feedback from the supervisor, which proved our ability to handle pressure.
Don't Just Read Maintenance Helper Questions - Practice Answering Them!
Reading helps, but actual practice is what gets you hired. Our AI feedback system helps you improve your Maintenance Helper interview answers in real-time.
Personalized feedback
Unlimited practice
Used by hundreds of successful candidates
Technical Interview Questions
What types of maintenance tools and equipment are you familiar with?
How to Answer
- 1
List specific hand tools like wrenches, screwdrivers, and pliers you have used.
- 2
Include any power tools such as drills, saws, or sanders you are comfortable operating.
- 3
Mention any specialized equipment relevant to the job, like HVAC tools or plumbing equipment.
- 4
Discuss your experience with safety equipment and your awareness of safety protocols.
- 5
Emphasize any relevant certifications or training for tools you're familiar with.
Example Answers
I am familiar with basic hand tools like wrenches, screwdrivers, and pliers, as well as power tools like drills and saws. I have also used HVAC equipment for routine maintenance and repairs.
What safety protocols do you follow when performing maintenance tasks?
How to Answer
- 1
Always assess the work area for hazards before starting any task.
- 2
Wear appropriate personal protective equipment (PPE) such as gloves, goggles, and helmets.
- 3
Utilize lockout/tagout procedures to ensure machinery is safely shut off.
- 4
Follow all safety guidelines provided by your employer and the equipment manufacturer.
- 5
Keep an emergency kit and first aid supplies accessible at all times.
Example Answers
I always start by assessing the work area for any potential hazards like wet surfaces or moving equipment. I wear gloves and goggles as necessary, and I make sure to use lockout/tagout on machinery to prevent accidents.
Don't Just Read Maintenance Helper Questions - Practice Answering Them!
Reading helps, but actual practice is what gets you hired. Our AI feedback system helps you improve your Maintenance Helper interview answers in real-time.
Personalized feedback
Unlimited practice
Used by hundreds of successful candidates
How would you troubleshoot a malfunctioning piece of equipment?
How to Answer
- 1
Identify the symptoms of the malfunction
- 2
Check if the equipment is receiving power and connections
- 3
Refer to the equipment manual for troubleshooting tips
- 4
Inspect for any visible damage or obstructions
- 5
Test individual components if feasible to isolate the issue
Example Answers
First, I would identify the symptoms of what’s wrong, like unusual noises or error codes. Then, I’d check the power supply and connections to ensure everything is plugged in correctly. If that’s fine, I would consult the equipment manual for specific troubleshooting steps and inspect for any visible wear or damage. Finally, I’d test components one by one if necessary to determine which part is malfunctioning.
What are the steps you would take to perform routine maintenance on a HVAC system?
How to Answer
- 1
Start with a visual inspection of the HVAC system.
- 2
Check and replace air filters as necessary.
- 3
Clean the condenser and evaporator coils.
- 4
Inspect and clean the drain lines and pans.
- 5
Test the system for proper operation and check refrigerant levels.
Example Answers
To perform routine maintenance on an HVAC system, I would begin with a visual inspection to check for any obvious issues. Then, I would replace the air filters to ensure clean airflow. Next, I would clean both the condenser and evaporator coils to improve efficiency, followed by cleaning the drain lines and pans to prevent water damage. Finally, I would test the system to ensure it operates correctly and check the refrigerant levels.
Can you explain the basic methods for dealing with pest infestations in a facility?
How to Answer
- 1
Identify the type of pest to tailor the response.
- 2
Limit food and water sources to deter pests.
- 3
Seal entry points to prevent infestations.
- 4
Consider traps or baits as non-chemical control methods.
- 5
Consult or hire a professional pest control service for severe issues.
Example Answers
First, it's important to identify the type of pest, like rodents or insects. Then, I would eliminate food and water sources, seal any gaps, and use traps as a first line of defense. If the problem persists, I would recommend calling a professional pest control service.
What experience do you have with installing and maintaining electrical systems?
How to Answer
- 1
Mention relevant educational background or certifications in electrical work.
- 2
Highlight specific hands-on experience with electrical installations or repairs.
- 3
Include examples of maintenance tasks you've performed on electrical systems.
- 4
Discuss any safety protocols you follow while working with electrical systems.
- 5
Be prepared to explain your problem-solving approach when dealing with electrical issues.
Example Answers
I completed a vocational course in electrical systems, where I learned installation techniques. I have helped install lighting fixtures and outlets in residential buildings, and I've also performed routine maintenance checks on electric panels.
How would you approach fixing a leaking pipe?
How to Answer
- 1
Identify the source of the leak before taking any action
- 2
Shut off the water supply to prevent further flooding
- 3
Use appropriate tools like a wrench and pipe tape for repairs
- 4
Assess if the pipe needs a patch or full replacement
- 5
Test the repair by turning the water supply back on slowly
Example Answers
First, I would locate the leak and turn off the water supply to avoid any water damage. Then, I would inspect the pipe to determine if it needs a simple patch or if it requires replacement. Using a wrench, I would tighten any loose fittings or replace damaged sections, then seal with pipe tape and test for leaks after turning the water back on.
What knowledge do you have regarding the maintenance of landscaped areas?
How to Answer
- 1
Mention specific tasks such as mowing, pruning, and weeding.
- 2
Highlight importance of seasonal care and pest control.
- 3
Discuss knowledge of different plants and their needs.
- 4
Include experience with tools and equipment used in landscaping.
- 5
Emphasize ability to follow safety guidelines while working.
Example Answers
I have experience with mowing lawns regularly, as well as pruning shrubs to promote healthy growth. I understand that seasonal changes require different care, such as mulching in winter and weeding in spring.
What is your approach to creating a maintenance schedule?
How to Answer
- 1
Identify critical equipment and systems that require regular maintenance.
- 2
Determine the frequency of maintenance based on manufacturer recommendations and past performance data.
- 3
Use a calendar or maintenance management software to track and schedule tasks.
- 4
Involve team members to input on needed maintenance based on their experience.
- 5
Review and adjust the schedule regularly based on efficiency and equipment status.
Example Answers
I start by listing all critical equipment and assess their maintenance needs. Then, I set up a weekly and monthly calendar using maintenance software to ensure all tasks are assigned and tracked efficiently.
What methods do you use for cleaning and maintaining workshop tools?
How to Answer
- 1
Always inspect tools before and after use to ensure they are clean and functional
- 2
Use appropriate cleaning solutions and tools specific to the type of equipment
- 3
Regularly lubricate moving parts to prevent rust and ensure efficiency
- 4
Keep tools organized and store them in designated areas to avoid damage
- 5
Create a scheduled maintenance checklist to track cleaning and servicing tasks
Example Answers
I inspect all tools for dirt and damage before and after use, then clean them with appropriate solutions. I also lubricate any moving parts to prevent rust.
Don't Just Read Maintenance Helper Questions - Practice Answering Them!
Reading helps, but actual practice is what gets you hired. Our AI feedback system helps you improve your Maintenance Helper interview answers in real-time.
Personalized feedback
Unlimited practice
Used by hundreds of successful candidates
How would you implement a preventive maintenance program?
How to Answer
- 1
Identify critical equipment and systems that require regular maintenance
- 2
Establish a maintenance schedule based on manufacturers' recommendations and usage patterns
- 3
Train staff on preventive maintenance procedures and the importance of documentation
- 4
Use a checklist to ensure all tasks are completed and track maintenance activities
- 5
Continuously review and adjust the program based on performance data and feedback
Example Answers
To implement a preventive maintenance program, I would start by identifying all critical machinery and creating a clear maintenance schedule based on their specific needs. I would then train the team to follow this schedule and ensure that all maintenance tasks are documented properly to maintain a record of upkeep.
Situational Interview Questions
If you noticed a coworker not following safety procedures, how would you handle the situation?
How to Answer
- 1
Stay calm and assess the situation without confrontation.
- 2
Approach the coworker privately and express your concerns.
- 3
Encourage them to follow safety procedures for everyone's well-being.
- 4
If necessary, report the issue to a supervisor.
- 5
Always prioritize safety and take action if the behavior continues.
Example Answers
I would first make sure I understood the situation clearly and then I would talk to my coworker in private. I would explain my concerns and why it's important to follow safety procedures. If they continued to ignore the safety rules, I would report it to a supervisor to ensure everyone's safety.
What would you do if you were assigned multiple urgent maintenance requests at the same time?
How to Answer
- 1
Assess the urgency and impact of each request
- 2
Communicate with team members or supervisors for insights
- 3
Prioritize tasks that ensure safety and operational continuity
- 4
Document each request to track progress and ensure completion
- 5
Handle the most critical issues first, delegating when possible
Example Answers
I would first assess each request to determine which one poses the greatest risk or has the most significant impact on operations. After prioritizing them, I would communicate with my team to see if resources can be allocated more efficiently. Then, I would address the most critical issue promptly while keeping track of others to ensure they are completed afterward.
Don't Just Read Maintenance Helper Questions - Practice Answering Them!
Reading helps, but actual practice is what gets you hired. Our AI feedback system helps you improve your Maintenance Helper interview answers in real-time.
Personalized feedback
Unlimited practice
Used by hundreds of successful candidates
How would you handle a situation where two team members disagreed on how to fix an issue?
How to Answer
- 1
Listen to both team members' viewpoints without interrupting
- 2
Encourage a collaborative discussion to find common ground
- 3
Suggest evaluating the pros and cons of each proposed solution
- 4
If needed, involve a supervisor for additional input and guidance
- 5
Remain neutral and focus on the best solution for the task at hand
Example Answers
I would listen to both team members to understand their perspectives. Then, I would facilitate a discussion to highlight the pros and cons of each solution. If they still couldn't agree, I would suggest we consult a supervisor for their expertise.
If you were running low on maintenance supplies, what steps would you take?
How to Answer
- 1
Assess current inventory to determine exact shortages
- 2
Prioritize which supplies are most critical for ongoing tasks
- 3
Communicate with your supervisor about the shortages
- 4
Research suppliers or vendors for quick reordering options
- 5
Establish a restocking schedule to prevent future shortages
Example Answers
First, I would check our inventory and identify which supplies are low. Then, I'd notify my supervisor to discuss the most crucial items that need restocking. Finally, I would reach out to our suppliers to place an order for those items promptly.
Imagine you recognize a critical issue with a piece of machinery that needs immediate attention. What are your next steps?
How to Answer
- 1
Assess the situation to understand the severity of the issue.
- 2
Immediately inform your supervisor or the responsible team member.
- 3
Take steps to ensure the safety of yourself and others around the machinery.
- 4
Document the issue clearly for future reference.
- 5
Follow up to ensure the issue is resolved and the machinery is safe to use.
Example Answers
First, I would assess the situation to determine the severity of the issue with the machinery. Then, I would notify my supervisor to make them aware of the critical situation. Safety is my top priority, so I would ensure the area is clear of personnel before further actions. I would document everything and follow up on the repair process to ensure the machinery is safe.
If you have repeatedly encountered delays in your work due to unforeseen circumstances, how would you adjust your time management strategies?
How to Answer
- 1
Identify key areas where delays occur and learn from them.
- 2
Prioritize tasks based on urgency and impact.
- 3
Create buffer times in your schedule for unexpected issues.
- 4
Stay flexible and be ready to adapt your plans as needed.
- 5
Use tools like checklists or apps to track progress and adjust timelines.
Example Answers
I would start by analyzing the causes of the delays to understand them better. Then I would prioritize my tasks and include buffer times in my schedule to accommodate any unexpected issues.
If you are asked to perform a maintenance task you have never done before, what will you do?
How to Answer
- 1
Stay calm and assess the task requirements carefully.
- 2
Seek guidance from a more experienced colleague or supervisor.
- 3
Research the task online for tutorials or instructions.
- 4
Break the task down into manageable steps.
- 5
Test your knowledge by practicing basic skills related to the task.
Example Answers
First, I would read through the task details to understand what is needed. Then, I would ask a coworker who has experience with this task for advice. Finally, I would look up any resources online to familiarize myself before starting.
How would you approach learning about a new type of equipment you are unfamiliar with?
How to Answer
- 1
Research the equipment online using manuals and specifications.
- 2
Ask experienced coworkers for insights and tips.
- 3
Observe the operation of the equipment in a real-world setting.
- 4
Take notes and create a checklist of key features and maintenance tasks.
- 5
Practice using the equipment under supervision to gain hands-on experience.
Example Answers
I would start by researching the equipment online, looking for manuals and how-to videos. Then, I would ask my coworkers who have experience with it for advice. Observing them as they work would also help me understand its functionality before I try it myself.
What would you do if you discovered a safety hazard in your work area?
How to Answer
- 1
Immediately assess the situation to understand the nature of the hazard.
- 2
Inform your supervisor or safety officer about the hazard right away.
- 3
If safe, take steps to mitigate the hazard until help arrives.
- 4
Follow company protocols for reporting safety issues.
- 5
Encourage coworkers to stay clear of the hazard until it is resolved.
Example Answers
If I found a safety hazard, I would first assess if it's safe to handle. Then, I would inform my supervisor immediately and ensure the area is marked off to prevent anyone from getting too close until it’s cleared.
How would you prioritize maintenance tasks if you have limited time available?
How to Answer
- 1
Assess the safety risks associated with each task.
- 2
Identify tasks that are urgent and affect operations.
- 3
Consider the impact on equipment and facility functionality.
- 4
Look for quick fixes that can offer immediate relief.
- 5
Communicate with your team to align priorities.
Example Answers
I would first look at tasks that pose safety risks, as those need immediate attention. Next, I'd evaluate which tasks are impacting our operations the most and tackle those priority-wise. Quick fixes that can be done in a short time would also be prioritized to clear minor issues.
Don't Just Read Maintenance Helper Questions - Practice Answering Them!
Reading helps, but actual practice is what gets you hired. Our AI feedback system helps you improve your Maintenance Helper interview answers in real-time.
Personalized feedback
Unlimited practice
Used by hundreds of successful candidates
Maintenance Helper Position Details
Salary Information
Recommended Job Boards
CareerBuilder
www.careerbuilder.com/jobs/maintenance-helperZipRecruiter
www.ziprecruiter.com/Jobs/Maintenance-HelperThese job boards are ranked by relevance for this position.
Related Positions
- Cleaning Helper
- Maintenance Assistant
- Maintenance Janitor
- Maintenance Worker
- General Cleaner
- Night Cleaner
- Window Cleaner
- Pool Cleaner
- Cleaner
- Hospital Cleaner
Similar positions you might be interested in.
Ace Your Next Interview!
Practice with AI feedback & get hired faster
Personalized feedback
Used by hundreds of successful candidates
Ace Your Next Interview!
Practice with AI feedback & get hired faster
Personalized feedback
Used by hundreds of successful candidates