Top 30 Master Mechanic Interview Questions and Answers [Updated 2025]
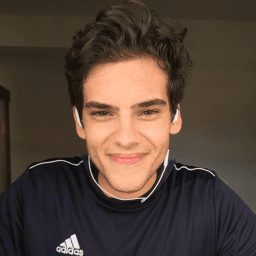
Andre Mendes
•
March 30, 2025
Preparing for a Master Mechanic interview can be daunting, but our latest blog post simplifies the process by presenting the most common questions you'll encounter. Dive into expertly crafted example answers and gain insights into answering effectively, ensuring you leave a lasting impression. Whether you're a seasoned professional or a budding mechanic, this guide is your key to acing that pivotal interview.
Download Master Mechanic Interview Questions in PDF
To make your preparation even more convenient, we've compiled all these top Master Mechanicinterview questions and answers into a handy PDF.
Click the button below to download the PDF and have easy access to these essential questions anytime, anywhere:
List of Master Mechanic Interview Questions
Behavioral Interview Questions
Can you describe a time when you diagnosed a complex mechanical issue? What was your approach?
How to Answer
- 1
Select a specific instance that showcases your diagnostic skills
- 2
Explain the steps you took to investigate the issue
- 3
Highlight any tools or techniques you used for diagnosis
- 4
Discuss the outcome and how it impacted the team or customer
- 5
Emphasize what you learned from the experience
Example Answers
I once diagnosed a malfunctioning hydraulic system on a construction vehicle. I started by checking the hydraulic fluid levels, then used pressure gauges to identify leaks. After isolating the faulty valve, I replaced it and tested the system. This reduced downtime by 30%, which pleased the client. I learned the importance of thorough initial checks.
Tell me about a time you worked closely with other mechanics to solve a difficult problem.
How to Answer
- 1
Select a specific example that highlights teamwork.
- 2
Describe the problem clearly and what made it difficult.
- 3
Explain each mechanic's role and contribution.
- 4
Detail the solution and how it benefited the team.
- 5
Conclude with what you learned from the experience.
Example Answers
At my last job, we faced a major engine failure on a customer's truck. Our team of three mechanics collaborated closely; I diagnosed the issue while my colleague sourced the parts. The third mechanic led the installation. Together, we managed to fix it ahead of schedule, which improved our customer satisfaction ratings.
Don't Just Read Master Mechanic Questions - Practice Answering Them!
Reading helps, but actual practice is what gets you hired. Our AI feedback system helps you improve your Master Mechanic interview answers in real-time.
Personalized feedback
Unlimited practice
Used by hundreds of successful candidates
Have you ever trained or mentored a junior mechanic? How did you approach this role?
How to Answer
- 1
Reflect on a specific experience you had mentoring a junior mechanic.
- 2
Describe your teaching style and how you tailored it to their learning needs.
- 3
Highlight the skills or knowledge you shared that were most beneficial.
- 4
Mention any positive outcomes from the mentorship for both the junior mechanic and yourself.
- 5
Conclude with what you learned from the experience as a mentor.
Example Answers
Yes, I mentored a junior mechanic last summer. I took a hands-on approach, demonstrating repairs while explaining the reasoning behind each step. I noticed he struggled with brake systems, so I focused on that area. By the end of the summer, he had confidently handled brake jobs on his own and even improved our turnaround time.
Describe a time when you had to learn a new technology or repair method quickly.
How to Answer
- 1
Choose a specific example that highlights urgency.
- 2
Focus on how you approached the learning process.
- 3
Explain the outcome and its impact on your work.
- 4
Mention any resources or tools you used to learn.
- 5
Highlight skills that helped you adapt quickly.
Example Answers
During a long shift, our diagnostic machine broke down. I had to quickly learn a new diagnostic software within a couple of hours. I referenced the online manual and asked a colleague for tips. By the end of the shift, I had successfully diagnosed the issue, which saved the team time and kept us on schedule.
Describe a situation where you had a disagreement with a colleague regarding a repair method. How did you resolve it?
How to Answer
- 1
Describe the context of the repair situation clearly
- 2
Explain your colleague's perspective and your reasoning
- 3
Emphasize communication and teamwork in resolving the disagreement
- 4
Highlight the final outcome and what you learned
- 5
Keep the focus on professionalism and respect
Example Answers
In a recent engine repair, my colleague insisted on using a quick fix method while I believed a thorough inspection was necessary. We discussed our viewpoints calmly, comparing potential risks. Ultimately, we decided to inspect the engine together and found the underlying issue. This collaborative approach strengthened our working relationship and improved our repair process.
Give an example of a time when you had to adapt to new technology or procedures in your work.
How to Answer
- 1
Choose a specific technology or procedure you adapted to.
- 2
Explain the challenge you faced with the change.
- 3
Describe the steps you took to learn and implement the new system.
- 4
Highlight the positive outcome from your adaptation.
- 5
Reflect on what you learned from the experience.
Example Answers
In my previous job, we adopted a new diagnostic software that improved efficiency. I took the initiative to enroll in a training session, practiced using the software during my off hours, and soon became the go-to person for my team. Our repair times improved by 30% as a result.
What drives you to excel as a mechanic, and how do you stay updated on industry trends?
How to Answer
- 1
Identify your passion for mechanics and problem-solving.
- 2
Mention specific areas of expertise and achievements.
- 3
Discuss your methods for continuing education, like courses or certifications.
- 4
Share how you engage with the community, such as forums or trade shows.
- 5
Highlight any mentors or resources that inspire your growth.
Example Answers
I thrive on the challenge of diagnosing complex issues and the satisfaction of fixing them. I constantly read industry publications and attend local workshops to stay updated.
What has been your most challenging project as a mechanic, and what did you learn from it?
How to Answer
- 1
Choose a project that had significant difficulties.
- 2
Describe the specific challenges you faced.
- 3
Explain how you addressed those challenges.
- 4
Highlight the skills and lessons you gained.
- 5
Keep your answer focused and relevant to the Master Mechanic role.
Example Answers
One of my most challenging projects was overhauling a vintage engine where I encountered numerous mechanical failures. I had to troubleshoot various issues like old wiring and parts that were hard to find. I learned the importance of patience and thorough research to find the right components, which enhanced my problem-solving skills.
How do you ensure that you maintain high quality and efficiency in your repairs?
How to Answer
- 1
Prioritize thorough inspections before starting any repair to identify all issues.
- 2
Keep detailed records of past repairs for reference and learning.
- 3
Use high-quality parts and tools to avoid repeated repairs.
- 4
Follow a systematic repair process to ensure no steps are skipped.
- 5
Continuously update your skills through training and certifications.
Example Answers
I begin each repair with a detailed inspection to spot all potential issues. I document my previous repairs to learn from them and always prioritize using quality parts. This systematic approach helps me maintain both quality and efficiency.
Don't Just Read Master Mechanic Questions - Practice Answering Them!
Reading helps, but actual practice is what gets you hired. Our AI feedback system helps you improve your Master Mechanic interview answers in real-time.
Personalized feedback
Unlimited practice
Used by hundreds of successful candidates
Technical Interview Questions
What steps do you follow when diagnosing an engine performance issue?
How to Answer
- 1
Start with a thorough assessment of the symptoms reported by the vehicle owner.
- 2
Perform a visual inspection of the engine components and check for any obvious issues.
- 3
Utilize diagnostic tools such as OBD-II scanners to retrieve trouble codes.
- 4
Conduct tests such as fuel pressure, compression, and spark checks to pinpoint the issue.
- 5
Review and analyze the vehicle's repair history for patterns or recurring problems.
Example Answers
I first listen to the owner's observations about the performance issues. Then, I visually inspect the engine for leaks or loose connections. After that, I use an OBD-II scanner to check for any error codes, followed by conducting compression tests to get a clear picture of the engine's health.
Can you explain how the fuel injection system works and common issues associated with it?
How to Answer
- 1
Start by defining what a fuel injection system is.
- 2
Explain the main components involved in the fuel injection system.
- 3
Describe the process of fuel delivery and injection timing.
- 4
Mention common problems like injector clogs or fuel pump issues.
- 5
Conclude with how these issues can affect engine performance.
Example Answers
A fuel injection system delivers the right amount of fuel to the engine. It includes components like fuel injectors, a fuel pump, and an ECU. Fuel is injected into the combustion chamber at precise times for optimal performance. Common issues are clogged injectors that can cause misfires and a faulty fuel pump that can lead to poor acceleration.
Don't Just Read Master Mechanic Questions - Practice Answering Them!
Reading helps, but actual practice is what gets you hired. Our AI feedback system helps you improve your Master Mechanic interview answers in real-time.
Personalized feedback
Unlimited practice
Used by hundreds of successful candidates
What experience do you have with electrical systems in vehicles? Can you provide an example?
How to Answer
- 1
Highlight specific electrical systems you've worked on
- 2
Mention any certifications or training in automotive electrical systems
- 3
Provide a concrete example of a problem you solved
- 4
Discuss the tools and techniques you used
- 5
Emphasize the results of your work, such as improved vehicle performance
Example Answers
In my previous role, I worked on diagnosing and repairing the electrical systems of various vehicles, including troubleshooting wiring issues. For example, I identified a short circuit in a customer's SUV, used a multimeter to trace the issue, and fixed it, restoring the vehicle's function. This saved the customer both time and repair costs.
What safety precautions do you take when working on heavy machinery?
How to Answer
- 1
Always wear appropriate personal protective equipment such as gloves, goggles, and hard hats.
- 2
Ensure that all machinery is properly maintained and inspected before use.
- 3
Follow lockout/tagout procedures to ensure that machinery cannot be accidentally started.
- 4
Make sure the work area is clear of hazards and that safety barriers are in place.
- 5
Stay vigilant and aware of your surroundings, especially when working near other team members.
Example Answers
I always wear my protective gear and ensure the machinery is inspected and maintained. I also follow lockout/tagout procedures.
What are your favorite tools for automotive repair, and why?
How to Answer
- 1
Mention specific tools you use regularly
- 2
Explain why each tool is important to your work
- 3
Include personal experiences with the tools
- 4
Highlight tools that showcase your skills and expertise
- 5
Connect tools to the types of repairs you specialize in
Example Answers
I really prefer using a torque wrench because it ensures accurate tightening, which is crucial for engine assembly. I once prevented a major engine failure by double-checking torque specs with it.
How do you approach routine maintenance schedules for different vehicle types?
How to Answer
- 1
Review manufacturer maintenance guidelines for each vehicle type
- 2
Create a checklist for common tasks like oil changes and tire rotations
- 3
Use a digital or physical calendar to track schedules
- 4
Consider the vehicle's age, mileage, and previous service history
- 5
Communicate with the vehicle owner to prioritize their needs
Example Answers
I start by reviewing the manufacturer's guidelines, as they detail essential maintenance for each vehicle. Then, I create a checklist of tasks like oil changes and tire rotations. I use a digital calendar to keep track of when services are due and adjust based on each vehicle's specifics and owner preferences.
What is your process for troubleshooting a malfunctioning transmission?
How to Answer
- 1
Gather information from the vehicle owner about symptoms and recent history.
- 2
Perform a visual inspection of the transmission and surrounding components.
- 3
Use diagnostic tools to check for error codes and perform a fluid check.
- 4
Test drive the vehicle to observe the transmission behavior under various conditions.
- 5
Follow a systematic approach to isolate the issue, checking for common faults step by step.
Example Answers
First, I ask the owner about the symptoms they've noticed and any recent work done. Then, I visually inspect the transmission and check for leaks. Next, I connect my diagnostic scanner to look for error codes and check the fluid levels. After that, I take the vehicle for a test drive to see how the transmission behaves. Finally, I methodically check components like solenoids and sensors to narrow down the problem.
How would you assess the performance of a vehicle's brake system?
How to Answer
- 1
Begin with a visual inspection of the brake components.
- 2
Check the brake fluid level and condition.
- 3
Test the brake response while driving in a safe environment.
- 4
Listen for unusual noises when applying brakes.
- 5
Use a diagnostic tool to check for brake system errors if applicable.
Example Answers
I would start by visually inspecting the brake pads and rotors for wear and damage. Next, I would check the brake fluid for level and clarity. After that, I would take the vehicle for a short test drive to assess the brake response and feel.
What is the role of the onboard diagnostic system (OBD) in modern vehicles?
How to Answer
- 1
Explain what OBD stands for and its purpose
- 2
Mention how OBD monitors vehicle systems
- 3
Discuss how OBD helps in diagnosing problems
- 4
Include the role of OBD in emissions control
- 5
Highlight the importance of OBD for maintenance and repairs
Example Answers
The OBD stands for onboard diagnostics. Its primary role is to monitor various vehicle systems for performance and emissions issues. This allows mechanics to diagnose problems effectively and ensure that vehicles meet regulatory emissions standards.
Can you explain how hydraulic systems in vehicles operate and common problems that may arise?
How to Answer
- 1
Start by defining hydraulic systems and their purpose in vehicles.
- 2
Explain how hydraulic pressure is generated and transmitted through fluids.
- 3
Mention common components like pumps, hoses, and cylinders.
- 4
Identify typical issues such as leaks, contamination, and pump failure.
- 5
Conclude with how these problems can affect vehicle performance.
Example Answers
Hydraulic systems in vehicles use fluid pressure to operate various components, like brakes and steering. A pump generates pressure, which is transmitted through hoses to cylinders that perform work. Common problems include leaks from hoses, fluid contamination, or pump failures which can lead to brake failure or difficulty steering.
Don't Just Read Master Mechanic Questions - Practice Answering Them!
Reading helps, but actual practice is what gets you hired. Our AI feedback system helps you improve your Master Mechanic interview answers in real-time.
Personalized feedback
Unlimited practice
Used by hundreds of successful candidates
Situational Interview Questions
If you received a vehicle that the owner claimed would not start, what would be your systematic approach to diagnosing the problem?
How to Answer
- 1
Start by asking the owner detailed questions about the symptoms.
- 2
Check for visible issues like battery connections or leaks under the hood.
- 3
Use diagnostic tools to check for error codes if applicable.
- 4
Test the battery, starter, and ignition system methodically.
- 5
Verify fuel delivery and check fuses related to starting system.
Example Answers
First, I would ask the owner about any indicators like dashboard lights or sounds when trying to start. Then, I’d visually inspect the battery and connections before using a multimeter to test voltage at the battery and starter.
Imagine you have multiple cars to repair with tight deadlines. How would you prioritize your work?
How to Answer
- 1
Assess the severity of each issue and prioritize critical repairs first.
- 2
Consider customer deadlines and communicate with them if needed.
- 3
Evaluate which repairs can be done quickly for immediate needs.
- 4
Group similar repairs together to save time and increase efficiency.
- 5
Stay organized and create a clear schedule to track progress.
Example Answers
I would first identify the critical repairs that are essential for vehicle safety and prioritize those. Then, I would align my work based on each vehicle's deadline, communicating with customers to manage expectations.
Don't Just Read Master Mechanic Questions - Practice Answering Them!
Reading helps, but actual practice is what gets you hired. Our AI feedback system helps you improve your Master Mechanic interview answers in real-time.
Personalized feedback
Unlimited practice
Used by hundreds of successful candidates
If a customer is unhappy with the service they received, how would you handle the situation?
How to Answer
- 1
Listen to the customer without interrupting
- 2
Acknowledge their feelings and apologize sincerely
- 3
Ask questions to understand the issue clearly
- 4
Offer a solution or compromise where possible
- 5
Follow up to ensure satisfaction after resolving the issue
Example Answers
I would first listen to the customer fully to understand their concerns. Then, I would acknowledge their feelings and apologize for any inconvenience caused. After that, I would ask clarifying questions to pinpoint the issue and then discuss potential solutions with them.
You discover a critical safety issue while repairing a vehicle that was scheduled for a quick turnaround. What would you do?
How to Answer
- 1
Immediately assess the severity of the safety issue
- 2
Communicate the issue to your supervisor and the team
- 3
Prioritize safety over time constraints
- 4
Document the issue and follow company protocols for repairs
- 5
Inform the customer about the delay and safety concerns
Example Answers
I would first assess the situation to understand the safety issue's severity. Then, I would inform my supervisor about the problem immediately. Safety is my top priority, so I would halt any further work until the issue is resolved. I would document everything and follow the necessary repair protocols, and finally, I would communicate clearly with the customer regarding the delay due to safety concerns.
If you identify a recurring problem with a particular vehicle model, how would you propose a long-term fix?
How to Answer
- 1
Analyze the root cause of the recurring problem thoroughly.
- 2
Gather data and feedback from technicians and customers about the issue.
- 3
Develop a comprehensive repair procedure or fix that addresses the cause.
- 4
Collaborate with the manufacturer for possible recalls or service bulletins.
- 5
Implement training for staff to ensure proper handling of the issue.
Example Answers
First, I would conduct a detailed analysis to understand the root cause of the recurring issue. Then, I would gather data from my team and testimonials from customers. After confirming the root cause, I would draft a comprehensive repair plan and discuss it with our manufacturer for any necessary updates in service procedures.
How would you handle a situation where a team member is consistently making mistakes?
How to Answer
- 1
Identify the specific mistakes and their impacts on the team.
- 2
Approach the team member privately and express your concerns.
- 3
Ask if there are underlying issues affecting their performance.
- 4
Offer assistance or resources to help them improve.
- 5
Follow up regularly to track progress and provide feedback.
Example Answers
I would first identify the specific mistakes they're making and how those affect the team's workflow. Then, I would have a private conversation to discuss my concerns and understand if there are any underlying issues. Depending on the situation, I would offer my help or suggest resources for improvement.
If you need to explain a technical problem to a customer who has little mechanical knowledge, how would you do it?
How to Answer
- 1
Start with a simple analogy related to everyday life
- 2
Break down the problem into basic parts
- 3
Use clear and non-technical language
- 4
Encourage questions to clarify understanding
- 5
Summarize the main points at the end
Example Answers
I would say that the issue is like a car running out of gas. I would explain that the engine needs energy to run, just like a car needs fuel.
If a vehicle comes in with an unexpected failure right before a customer is set to pick it up, how would you handle it?
How to Answer
- 1
Stay calm and assess the situation quickly.
- 2
Communicate transparently with the customer about the issue.
- 3
Offer a solution or alternative, such as a rental or reschedule.
- 4
Document the issue for future reference.
- 5
Follow up with the customer after the repair is completed.
Example Answers
I would quickly check the vehicle to understand the failure and inform the customer immediately, explaining the problem and estimating the time needed for repairs.
How would you decide whether to repair or replace a faulty engine component?
How to Answer
- 1
Assess the cost of repair versus replacement.
- 2
Evaluate the component's overall condition and lifespan.
- 3
Consider the vehicle's age and value before making a decision.
- 4
Consult repair manuals and OEM specifications for guidance.
- 5
Think about the impact on vehicle performance and reliability.
Example Answers
If the repair costs are significantly lower than replacement and the component has good longevity left, I would choose to repair it.
You're short on parts needed for several repairs; what steps would you take to manage this situation?
How to Answer
- 1
Assess the urgency of each repair and prioritize accordingly.
- 2
Communicate with customers about potential delays and alternatives.
- 3
Reach out to suppliers for expedited shipping or alternative parts.
- 4
Consider temporary solutions or workarounds to keep operations moving.
- 5
Keep an inventory log to track which parts are missing and re-order promptly.
Example Answers
First, I would evaluate which repairs are most urgent and prioritize them. I'd then inform customers about the situation and offer alternative solutions if possible. Next, I would contact suppliers to find out if they have faster shipping options or similar parts that could be used.
Don't Just Read Master Mechanic Questions - Practice Answering Them!
Reading helps, but actual practice is what gets you hired. Our AI feedback system helps you improve your Master Mechanic interview answers in real-time.
Personalized feedback
Unlimited practice
Used by hundreds of successful candidates
Master Mechanic Position Details
Recommended Job Boards
CareerBuilder
www.careerbuilder.com/jobs-master-mechanicZipRecruiter
www.ziprecruiter.com/Jobs/-Master-MechanicThese job boards are ranked by relevance for this position.
Related Positions
Ace Your Next Interview!
Practice with AI feedback & get hired faster
Personalized feedback
Used by hundreds of successful candidates
Ace Your Next Interview!
Practice with AI feedback & get hired faster
Personalized feedback
Used by hundreds of successful candidates