Top 30 Mobile Equipment Mechanic Interview Questions and Answers [Updated 2025]
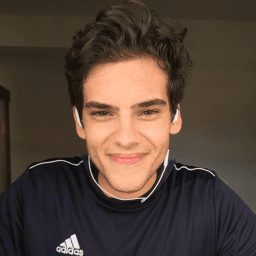
Andre Mendes
•
March 30, 2025
Are you gearing up for a Mobile Equipment Mechanic interview and looking to stand out from the competition? This blog post is your ultimate guide, featuring the most common interview questions for this pivotal role. Dive into expertly crafted sample answers and insightful tips that will help you respond confidently and effectively, ensuring you're well-prepared to impress potential employers. Read on to boost your interview prowess!
Download Mobile Equipment Mechanic Interview Questions in PDF
To make your preparation even more convenient, we've compiled all these top Mobile Equipment Mechanicinterview questions and answers into a handy PDF.
Click the button below to download the PDF and have easy access to these essential questions anytime, anywhere:
List of Mobile Equipment Mechanic Interview Questions
Behavioral Interview Questions
Describe a time when you worked as part of a team to repair a piece of mobile equipment. What was your role?
How to Answer
- 1
Think of a specific project or repair task you completed as a team.
- 2
Outline your specific responsibilities and contributions clearly.
- 3
Mention any challenges you faced and how the team overcame them.
- 4
Highlight the importance of communication and collaboration in the repair.
- 5
End with a positive outcome, like successful repairs or improved equipment performance.
Example Answers
In my last job, we had a downtime incident with a bulldozer. I was assigned as the lead mechanic. I coordinated with my team to assess the hydraulic system. I guided them in replacing worn hoses and ensured we adhered to safety standards. Our teamwork helped us complete the repair in record time, and the bulldozer was back in operation the next day.
Can you give an example of a challenging repair you faced and how you resolved it?
How to Answer
- 1
Choose a specific repair that had significant difficulties
- 2
Explain the problem clearly and the steps you took to diagnose it
- 3
Highlight any tools or techniques that were essential in your repair
- 4
Discuss the outcome and what you learned from the experience
- 5
Emphasize teamwork or communication if applicable
Example Answers
I once dealt with a catastrophic failure in a hydraulic system on a loader. After noticing irregular pressure readings, I conducted a thorough inspection and pinpointed a damaged control valve. Using specialized diagnostic tools, I replaced the valve and re-tested the system. This resolved the issue, and I learned the importance of precision in diagnostics.
Don't Just Read Mobile Equipment Mechanic Questions - Practice Answering Them!
Reading helps, but actual practice is what gets you hired. Our AI feedback system helps you improve your Mobile Equipment Mechanic interview answers in real-time.
Personalized feedback
Unlimited practice
Used by hundreds of successful candidates
Tell me about a time when you had to adapt to a sudden change in a project or task. What steps did you take?
How to Answer
- 1
Choose a specific example from your experience.
- 2
Explain the change clearly and its impact on the task.
- 3
Describe the steps you took to adapt effectively.
- 4
Highlight the outcome and what you learned from the experience.
- 5
Keep your answer focused and concise.
Example Answers
During a routine maintenance project, we discovered a critical part was backordered. I quickly coordinated with the team to adjust our work schedule, prioritized other tasks, and sourced temporary solutions from local suppliers. We completed the project on time, and I learned the importance of flexibility.
Describe a situation where you had to explain a technical issue to someone without a technical background. How did you ensure they understood?
How to Answer
- 1
Choose a specific example from your experience.
- 2
Break down the technical issue into simple terms.
- 3
Use analogies or everyday examples to clarify your points.
- 4
Ask questions to confirm understanding during your explanation.
- 5
Summarize the key points at the end to reinforce what you've explained.
Example Answers
In my previous job, I had to explain a hydraulic issue to a warehouse manager who had no technical background. I simplified the problem by comparing the hydraulic system to a water hose. I asked questions like 'Do you understand how water pressure works?' and confirmed their understanding. At the end, I summarized that maintaining proper pressure is crucial for the equipment's operation.
Have you ever been in charge of a project or a team? What challenges did you face in leading the team?
How to Answer
- 1
Choose a specific project where you were in charge.
- 2
Mention the number of team members and their roles.
- 3
Describe a specific challenge you faced and how you resolved it.
- 4
Highlight the outcome or success of the project.
- 5
Reflect on what you learned from the experience.
Example Answers
I led a team of four mechanics in overhauling a fleet of vehicles. The main challenge was coordinating schedules and ensuring everyone was on the same page. I implemented daily briefings to address issues as they arose, and we completed the project ahead of schedule. I learned the importance of communication in teamwork.
Can you describe a time when your attention to detail prevented a major mistake in a repair job?
How to Answer
- 1
Think of a specific repair job where you spotted an error.
- 2
Explain how you noticed the detail and what it was.
- 3
Describe the action you took to address the issue.
- 4
Mention the outcome and how it helped the project or customer.
- 5
Keep it concise and focus on your role.
Example Answers
During a routine maintenance on a backhoe, I noticed a small crack in the hydraulic hose that could have led to a failure. I immediately replaced it before starting the job. This attention to detail prevented a potential hydraulic failure during operation.
Tell me about a time you suggested improvements to a maintenance process. What impact did it have?
How to Answer
- 1
Select a specific example from your experience.
- 2
Describe the situation and the maintenance process you improved.
- 3
Explain your suggestion clearly and why it was needed.
- 4
Share the outcome and the positive impact your suggestion had.
- 5
Use metrics or data if available to quantify the improvement.
Example Answers
In my previous role, I noticed that our fluid change intervals were inconsistent. I suggested we implement a standardized checklist for every service. This not only reduced fluid change errors but also cut our maintenance time by 20%.
Describe a situation when you had to work longer hours to complete a job. What motivated you?
How to Answer
- 1
Share a specific example from your past experience
- 2
Explain the task or project that required longer hours
- 3
Emphasize your motivation and dedication
- 4
Highlight the positive outcome of your effort
- 5
Conclude with what you learned from the experience
Example Answers
In my previous job as a mechanic, I worked on a critical repair for a client’s equipment. The job required extra hours due to parts delays. I was motivated by the need to ensure the equipment was operational before the weekend so the client could use it. Ultimately, my efforts paid off, and we completed the repair ahead of schedule, leading to a grateful client and additional referrals.
Tell me about a time when you had to manage your time effectively to meet a deadline.
How to Answer
- 1
Think of a specific project or task with a clear deadline.
- 2
Describe the steps you took to prioritize tasks.
- 3
Explain how you monitored your progress.
- 4
Mention any tools or methods you used to stay organized.
- 5
Conclude with the outcome and what you learned from the experience.
Example Answers
When I was assigned to complete a maintenance check on a fleet of 10 vehicles before a major event, I created a schedule breaking down each vehicle into specific tasks. I prioritized by the vehicle needing the most work first and checked off tasks as I completed them. This allowed me to finish a day early, ensuring everything was ready for the event.
Describe a conflict you experienced with a colleague and how you resolved it.
How to Answer
- 1
Choose a specific example that demonstrates your conflict resolution skills.
- 2
Explain the context of the conflict clearly and briefly.
- 3
Focus on your role in the resolution and the steps you took.
- 4
Highlight the outcome and what you learned from the experience.
- 5
Stay positive and professional, avoiding negativity about the co-worker.
Example Answers
In a previous job, a colleague and I disagreed on how to repair a piece of equipment. I suggested we meet to discuss our viewpoints. By listening to each other, we found common ground and combined our ideas, which led to a successful repair. This experience taught me the importance of communication.
Don't Just Read Mobile Equipment Mechanic Questions - Practice Answering Them!
Reading helps, but actual practice is what gets you hired. Our AI feedback system helps you improve your Mobile Equipment Mechanic interview answers in real-time.
Personalized feedback
Unlimited practice
Used by hundreds of successful candidates
Technical Interview Questions
What are the common causes of hydraulic system failures in mobile equipment, and how do you diagnose them?
How to Answer
- 1
Identify key causes like leaks, air in the system, and component wear
- 2
Explain how to check fluid levels and condition
- 3
Discuss the importance of inspecting hoses and connections
- 4
Mention the use of diagnostic tools like pressure gauges and flow meters
- 5
Emphasize the need for systematic troubleshooting steps
Example Answers
Common causes of hydraulic failures include leaks in hoses, air in the system, and wear on seals. To diagnose issues, I first check fluid levels and inspect for leaks. Then, I use pressure gauges to measure system pressure and look for inconsistencies that indicate blockages or component wear.
Explain the steps you would take to troubleshoot a diesel engine that won’t start.
How to Answer
- 1
Check the fuel system for proper supply and quality of diesel fuel.
- 2
Inspect the battery and electrical connections for charge and corrosion.
- 3
Examine the starter motor and ignition system for functionality.
- 4
Look for any error codes or indicators on the engine’s diagnostic system.
- 5
Review the air intake and exhaust systems for blockages or restrictions.
Example Answers
First, I would check if there is adequate fuel in the tank and ensure the fuel lines are free of blockages.
Don't Just Read Mobile Equipment Mechanic Questions - Practice Answering Them!
Reading helps, but actual practice is what gets you hired. Our AI feedback system helps you improve your Mobile Equipment Mechanic interview answers in real-time.
Personalized feedback
Unlimited practice
Used by hundreds of successful candidates
What preventive maintenance practices do you follow to ensure equipment reliability?
How to Answer
- 1
Discuss routine inspection schedules
- 2
Mention specific tasks like fluid changes or filter replacements
- 3
Highlight the importance of tracking equipment usage
- 4
Include the benefits of keeping a maintenance log
- 5
Talk about teamwork and communication with operators
Example Answers
I follow a routine inspection schedule every 250 hours of operation, focusing on fluid levels and filter replacements. I also keep detailed maintenance logs to track any issues over time.
How do you diagnose electrical issues in mobile equipment? Can you describe the tools you use?
How to Answer
- 1
Start by explaining your systematic approach to diagnosing electrical issues.
- 2
Mention specific tools like multimeters, oscilloscopes, and diagnostic software.
- 3
Include steps such as checking battery voltage, inspecting wiring, and using a multimeter.
- 4
Emphasize problem-solving and troubleshooting skills.
- 5
Provide an example of a past experience where you successfully diagnosed an issue.
Example Answers
I diagnose electrical issues by first checking the battery and ensuring there is adequate voltage. I then use a multimeter to test circuits for continuity and to check for shorts. Additionally, I might use an oscilloscope to analyze signals. For example, I once diagnosed a faulty starter on a mobile crane using these tools, which involved tracing back from the starter to the battery.
What safety protocols do you always follow when working on mobile equipment?
How to Answer
- 1
Always wear appropriate personal protective equipment such as gloves and safety glasses.
- 2
Conduct a pre-job safety inspection of the equipment to check for hazards.
- 3
Follow lockout/tagout procedures to ensure equipment is powered down before servicing.
- 4
Use fall protection equipment when working at heights or in elevated positions.
- 5
Maintain a clean and organized workspace to reduce the risk of accidents.
Example Answers
I prioritize safety by wearing the required PPE, conducting inspections, and following lockout/tagout procedures before starting any work.
What are the key components of a mobile crane, and how do they function together?
How to Answer
- 1
Identify major components like the boom, counterweight, and chassis.
- 2
Explain the function of each component clearly.
- 3
Discuss how the components interact for safe operation.
- 4
Use specific examples of cranes or scenarios.
- 5
Practice a structured response to stay concise.
Example Answers
A mobile crane typically includes components like the boom, which extends to lift loads; the chassis, which provides mobility; and the counterweight, which stabilizes the crane during operation. Together, they allow for lifting heavy objects safely and efficiently while maintaining balance.
How would you interpret the results of an oil sample from an engine? What indicators would you look for?
How to Answer
- 1
Check for metal particles to identify wear in engine components.
- 2
Look for signs of contamination such as water or coolant in the oil.
- 3
Assess viscosity to ensure proper lubrication performance.
- 4
Evaluate the oil's oxidation level to determine its lifespan.
- 5
Analyze additive levels to understand oil effectiveness and maintenance needs.
Example Answers
I would analyze the oil sample for metal particles which indicate wear. High numbers of metal particles could signal issues like bearing wear. Additionally, I'd check for contamination as it can affect engine performance.
What types of welding techniques are commonly used in mobile equipment repairs, and when would you use each?
How to Answer
- 1
Identify common welding techniques like MIG, TIG, and Stick welding.
- 2
Explain the strengths and weaknesses of each technique.
- 3
Use specific examples of mobile equipment repairs for context.
- 4
Mention the materials that are best suited for each welding method.
- 5
Discuss when you would choose one method over another based on the repair requirements.
Example Answers
In mobile equipment repairs, MIG welding is commonly used for its speed and versatility. I would use it for repairing aluminum parts because it allows for a clean weld without much distortion. For heavier steel components, Stick welding is preferred due to its strength and ability to penetrate thick materials in outdoor settings.
Walk me through the troubleshooting process you follow for a mobile equipment braking system.
How to Answer
- 1
Start with a visual inspection of the braking system components.
- 2
Check for any error codes or warning lights on the dashboard.
- 3
Test the brake fluid level and condition.
- 4
Inspect the brake pads and rotors for wear and damage.
- 5
Conduct a road test to evaluate the performance of the braking system.
Example Answers
I begin by visually inspecting the braking system for any obvious issues like leaks or worn parts. Then, I check the dashboard for any warning lights or codes. Next, I assess the brake fluid level and its condition. After that, I inspect the brake pads and rotors for wear, followed by a road test to see if the brakes engage properly.
What diagnostic tools and software are you familiar with for mobile equipment maintenance?
How to Answer
- 1
List specific tools you have used
- 2
Mention relevant software and their functions
- 3
Include examples of how you used each
- 4
Talk about experience with both mechanical and electronic diagnostics
- 5
Highlight any certifications related to the tools or software
Example Answers
I have extensive experience with Diagnostic Scan Tools such as CAT ET and John Deere Service Advisor, which I used for troubleshooting engine issues and performing software updates.
Don't Just Read Mobile Equipment Mechanic Questions - Practice Answering Them!
Reading helps, but actual practice is what gets you hired. Our AI feedback system helps you improve your Mobile Equipment Mechanic interview answers in real-time.
Personalized feedback
Unlimited practice
Used by hundreds of successful candidates
Situational Interview Questions
Imagine you are on-site and a piece of equipment breaks down unexpectedly. What steps would you take to address the situation?
How to Answer
- 1
Assess the situation quickly and determine the extent of the breakdown.
- 2
Isolate the equipment to ensure safety for yourself and others.
- 3
Communicate with your team and supervisor about the issue.
- 4
Conduct a preliminary inspection to identify potential causes.
- 5
Plan and execute repairs or next steps, documenting the process.
Example Answers
First, I would assess the equipment to understand the failure. Then, I would ensure that the area is safe and isolate the broken equipment. I would immediately inform my supervisor and the team about the breakdown. After that, I would inspect the equipment for visible issues and plan the necessary repairs or call for additional support.
If you have multiple repairs to complete at once, how would you prioritize your tasks?
How to Answer
- 1
Assess which repairs are urgent based on safety and operational needs
- 2
Consider the complexity of each repair and the time required
- 3
Evaluate the availability of parts and tools for each task
- 4
Communicate with the team to understand any dependencies
- 5
Keep a checklist to track completed repairs and pending tasks
Example Answers
I would first identify any repair that impacts safety or functionality and prioritize those. Then, I'd look at the tasks that require immediate attention and have the tools ready to address them effectively.
Don't Just Read Mobile Equipment Mechanic Questions - Practice Answering Them!
Reading helps, but actual practice is what gets you hired. Our AI feedback system helps you improve your Mobile Equipment Mechanic interview answers in real-time.
Personalized feedback
Unlimited practice
Used by hundreds of successful candidates
You receive a call from a client who is upset because their equipment is malfunctioning. How would you handle the situation?
How to Answer
- 1
Listen carefully to the client's concerns without interrupting.
- 2
Acknowledge their frustration and show empathy.
- 3
Ask clear questions to understand the issue thoroughly.
- 4
Explain the steps you will take to resolve the problem.
- 5
Follow up after the issue is resolved to ensure satisfaction.
Example Answers
I would first listen to the client's concerns and allow them to express their frustration. I would empathize by saying I understand how disruptive equipment issues can be. Then, I'd ask specific questions about the malfunction to gather details. After that, I would explain how I plan to address their equipment's problems and provide a timeline for resolution.
If you are working with a team on a large piece of equipment and there is a disagreement on repair techniques, how would you resolve it?
How to Answer
- 1
Listen to all team members' perspectives on the repair techniques.
- 2
Encourage open discussion to understand the reasoning behind each technique.
- 3
Suggest a collaborative approach, combining the best ideas from each perspective.
- 4
Refer to technical documents or past experiences to support the discussion.
- 5
If necessary, consult a supervisor or expert for a final decision.
Example Answers
I would first listen to everyone's views on the repair techniques. Then, I would facilitate a discussion to understand the reasoning behind each option. After weighing the pros and cons, I might suggest a combined approach that incorporates the best elements from each side.
You encounter a problem you haven’t dealt with before. How would you proceed to find a solution?
How to Answer
- 1
Stay calm and assess the situation carefully.
- 2
Gather any relevant information or documentation.
- 3
Consult with colleagues or mentors who may have experience.
- 4
Use online resources or manuals specific to the equipment.
- 5
Test potential solutions in a controlled and safe manner.
Example Answers
If I encounter an unfamiliar problem, I would first take a moment to assess the situation and gather any available documentation related to the equipment. Then, I would consult with a more experienced colleague for advice and review any relevant online resources or manuals to find potential solutions.
If you were at a remote job site and lacked a specific tool needed for a repair, what would you do?
How to Answer
- 1
Assess the situation and identify the exact tool needed.
- 2
Check if any alternative tools can achieve the same result.
- 3
Consider improvising a tool using available materials.
- 4
Communicate with the team or supervisor for possible solutions.
- 5
Document the tool shortage for future reference and restock.
Example Answers
I would first determine what specific tool I need and then see if I can use an alternative tool to complete the repair. If not, I would communicate with my supervisor to find a solution or look for materials to improvise a tool.
You receive critical feedback from a supervisor about your work. How would you respond and improve?
How to Answer
- 1
Listen carefully to the feedback without becoming defensive.
- 2
Ask clarifying questions to fully understand the concerns.
- 3
Acknowledge any valid points and express gratitude for the feedback.
- 4
Create a plan to address the issues and improve your skills.
- 5
Follow up with your supervisor on your progress and any changes made.
Example Answers
I appreciate the feedback and will take time to reflect on it. I plan to ask clarifying questions during our next meeting to ensure I fully understand the issues. Then, I'll develop a plan to improve my skills accordingly.
How would you handle a situation where multiple pieces of equipment fail at the same time?
How to Answer
- 1
Assess the situation quickly to understand the extent of the failures.
- 2
Prioritize the equipment based on urgency and impact on operations.
- 3
Communicate clearly with your team about the situation.
- 4
Implement a plan to address the most critical problems first.
- 5
Document the issue and repairs made for future reference.
Example Answers
I would first assess which pieces of equipment are critical and categorize them by urgency. Then, I would communicate with my team about our priorities and tackle the most urgent repair first, ensuring minimal downtime.
Imagine you find that a common part is out of stock just when you need it. What actions do you take?
How to Answer
- 1
Check the inventory management system for the stock status of the part
- 2
Identify alternative parts that can be used in place of the original
- 3
Contact suppliers to find out the estimated restock date
- 4
Communicate with your supervisor or team about the issue and your plan
- 5
Document the incident to help improve inventory processes in the future
Example Answers
I would first check our inventory system to confirm that the part is indeed out of stock. Then, I would look for possible alternatives that could serve the same function. I would also reach out to our suppliers to see when the part might be back in stock. I believe it's important to keep my team updated on the situation, so I would inform them and discuss the best way to proceed. Lastly, I would record this issue to review our inventory management practices later.
If you were tasked with training a new mechanic, what key concepts would you emphasize?
How to Answer
- 1
Focus on safety protocols and practices as the top priority.
- 2
Teach fundamental mechanical knowledge, including systems and components.
- 3
Emphasize the importance of diagnostics and troubleshooting techniques.
- 4
Instill the value of effective communication and teamwork.
- 5
Encourage ongoing learning and adaptation to new technologies.
Example Answers
I would start with safety protocols, ensuring the new mechanic understands the importance of personal protective equipment. Next, I’d cover the essential mechanical knowledge, focusing on understanding different systems like hydraulic and electrical systems. I’d also highlight diagnostic skills, teaching them how to troubleshoot effectively. Teamwork is crucial, so I’d emphasize communication with colleagues. Lastly, I’d encourage them to stay updated on new technologies in the field.
Don't Just Read Mobile Equipment Mechanic Questions - Practice Answering Them!
Reading helps, but actual practice is what gets you hired. Our AI feedback system helps you improve your Mobile Equipment Mechanic interview answers in real-time.
Personalized feedback
Unlimited practice
Used by hundreds of successful candidates
Mobile Equipment Mechanic Position Details
Recommended Job Boards
CareerBuilder
www.careerbuilder.com/jobs/mobile-equipment-mechanicThese job boards are ranked by relevance for this position.
Related Positions
Ace Your Next Interview!
Practice with AI feedback & get hired faster
Personalized feedback
Used by hundreds of successful candidates
Ace Your Next Interview!
Practice with AI feedback & get hired faster
Personalized feedback
Used by hundreds of successful candidates