Top 31 Mobile Mechanic Interview Questions and Answers [Updated 2025]
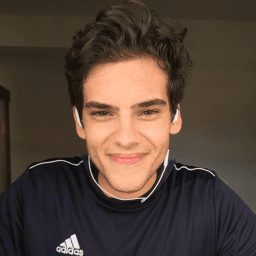
Andre Mendes
•
March 30, 2025
Navigating the complexities of a job interview can be daunting, especially for aspiring mobile mechanics. This blog post offers a comprehensive guide to the most common interview questions for this role. Packed with example answers and expert tips, it equips you with the tools to respond confidently and effectively, setting you on the path to success in your mobile mechanic career.
Download Mobile Mechanic Interview Questions in PDF
To make your preparation even more convenient, we've compiled all these top Mobile Mechanicinterview questions and answers into a handy PDF.
Click the button below to download the PDF and have easy access to these essential questions anytime, anywhere:
List of Mobile Mechanic Interview Questions
Behavioral Interview Questions
Can you describe a time when you encountered a major mechanical issue on-site? How did you resolve it?
How to Answer
- 1
Start with a specific situation you faced on-site.
- 2
Outline the mechanical problem clearly and concisely.
- 3
Explain the steps you took to diagnose the issue.
- 4
Detail any tools or techniques you used to fix the problem.
- 5
Conclude with the outcome and what you learned from the experience.
Example Answers
I was called to fix a truck that wouldn't start due to a suspected fuel issue. I performed a quick check of the fuel filter and lines, discovered a clog, and used my tools to replace the filter on site. The truck started immediately afterward, and the driver was able to continue his route without delay.
Tell me about a time when you dealt with a difficult customer. How did you handle the situation?
How to Answer
- 1
Start with a clear description of the situation.
- 2
Explain the customer's concerns in their context.
- 3
Describe the specific steps you took to address their issues.
- 4
Emphasize positive outcomes and what you learned.
- 5
Keep it concise and focus on your communication skills.
Example Answers
A customer was upset about a delay in their vehicle repair. I listened patiently, acknowledged their frustration, and explained the reason for the delay. I arranged for a discount as compensation, and they appreciated my transparency and the vehicle was completed soon after.
Don't Just Read Mobile Mechanic Questions - Practice Answering Them!
Reading helps, but actual practice is what gets you hired. Our AI feedback system helps you improve your Mobile Mechanic interview answers in real-time.
Personalized feedback
Unlimited practice
Used by hundreds of successful candidates
Describe an experience where you had to work as part of a team to complete a job. What was your role?
How to Answer
- 1
Choose a specific team experience, preferably related to mechanics.
- 2
Clearly state your role and responsibilities in the team.
- 3
Highlight any challenges faced and how you overcame them as a team.
- 4
Mention the outcome of the project and what you learned from it.
- 5
Connect the experience to how it makes you a good fit for the mobile mechanic role.
Example Answers
In my last job, I worked on a car repair project with three other mechanics. I was responsible for diagnosing electrical issues while others focused on the engine and suspension. We communicated regularly to ensure our repairs aligned. We completed the job efficiently, and the client was very satisfied with our teamwork. This experience improved my collaboration skills, which I believe are essential for a mobile mechanic.
Give an example of how you adapted to a sudden change in your work environment or job responsibilities.
How to Answer
- 1
Think of a specific instance where you faced a sudden change.
- 2
Describe the context clearly and what the change was.
- 3
Explain how you adjusted your approach or methods to accommodate the change.
- 4
Mention any positive outcomes from your adaptability.
- 5
Keep your answer focused on your actions and results.
Example Answers
At my last job, we suddenly had a new piece of equipment that I had never worked with before. I took the initiative to quickly learn its operation by watching online tutorials and consulting with my colleagues. Within a week, I was able to use it effectively and even helped train others, improving our efficiency.
Have you ever had to prioritize safety over speed in your work? What was the situation?
How to Answer
- 1
Choose a specific example where safety was a concern.
- 2
Explain the context and what you had to decide.
- 3
Describe the actions you took to ensure safety.
- 4
Mention the positive outcome of prioritizing safety.
- 5
Reflect on what you learned from the experience.
Example Answers
Once, I was working on a car with a malfunctioning brake system. I noticed the brakes were not up to standard and decided to take my time to properly fix them instead of rushing. I communicated with the customer about the delay, emphasizing that their safety was my priority. In the end, the customer appreciated the extra attention and felt safe driving their vehicle.
Describe a time when you had to learn a new skill or technology on the job. How did you approach it?
How to Answer
- 1
Identify a specific technology or skill you learned.
- 2
Explain the context or reason why you needed to learn it.
- 3
Describe the steps you took to learn it, such as resources or tools used.
- 4
Mention how you applied the new skill in your job.
- 5
Reflect on the outcome and what you gained from the experience.
Example Answers
At my previous job, we adopted a new diagnostic software for cars. I recognized its importance for troubleshooting while working on vehicles. I spent time watching tutorial videos and practicing using the software on test vehicles. I was able to implement it in my daily work, which ultimately improved my efficiency in diagnosing issues by 30%.
Have you ever had to lead a team of mechanics? What did you do to ensure the work was done effectively?
How to Answer
- 1
Start with a brief overview of your experience leading a team.
- 2
Highlight specific actions you took to manage and organize the workflow.
- 3
Mention any tools or methods you used for communication among the team.
- 4
Discuss how you dealt with challenges and kept the team motivated.
- 5
Conclude with the outcome of your leadership and its impact on the project.
Example Answers
In my previous job, I led a team of three mechanics for a major project. I organized daily briefings to assign tasks and keep everyone on the same page. We used a checklist to track our progress and communicate any issues, which kept us on schedule despite some unexpected repairs. The project was completed ahead of time and with high customer satisfaction.
What motivates you to perform well in your job as a mobile mechanic?
How to Answer
- 1
Reflect on your passion for problem-solving and helping others with their vehicle issues
- 2
Mention specific rewards from fixing cars and getting positive feedback from clients
- 3
Include your desire for continuous learning and staying updated with new automotive technologies
- 4
Talk about the satisfaction of being independent and working in diverse environments
- 5
Share your aim to build long-term relationships with clients through reliable service
Example Answers
I am motivated by my passion for problem-solving; every vehicle I work on challenges me and allows me to learn something new. Plus, receiving positive feedback from clients makes me feel proud of the work I do.
Can you provide an example of a creative solution you've implemented in your work as a mechanic?
How to Answer
- 1
Think of a specific problem you faced and how you solved it.
- 2
Focus on an innovative or resourceful approach, not just a standard fix.
- 3
Explain the context briefly to set the stage for your solution.
- 4
Describe the outcome and why it was effective.
- 5
Use clear, straightforward language to convey your idea.
Example Answers
Once, I had a client with a vehicle that wouldn’t start due to a faulty starter. After diagnosing, I realized I could use a portable jump starter and guide them to safely start their vehicle without needing a tow, which saved them both time and money.
Don't Just Read Mobile Mechanic Questions - Practice Answering Them!
Reading helps, but actual practice is what gets you hired. Our AI feedback system helps you improve your Mobile Mechanic interview answers in real-time.
Personalized feedback
Unlimited practice
Used by hundreds of successful candidates
Technical Interview Questions
What diagnostic tools do you prefer to use when troubleshooting vehicle issues, and why?
How to Answer
- 1
Identify the essential diagnostic tools you use regularly.
- 2
Explain why you prefer each tool based on its effectiveness or features.
- 3
Mention any brand names or specific models that you find reliable.
- 4
Provide examples of situations where these tools helped solve a problem.
- 5
Keep your answer concise and focused on your practical experience.
Example Answers
I prefer using the Autel MaxiCOM diagnostic scanner because it provides comprehensive data and has excellent user support. For example, it helped me identify a faulty sensor in a vehicle that was experiencing intermittent stalling.
Can you explain the steps you take when performing an engine oil change?
How to Answer
- 1
Start by gathering all necessary tools and materials like oil, filter, wrench, and drain pan.
- 2
Warm up the engine for a few minutes to thin the oil for easier draining.
- 3
Lift the vehicle safely using jack stands to access the oil pan.
- 4
Drain old oil completely, replace the oil filter, and refill with new oil as per manufacturer's specifications.
- 5
Check for leaks and ensure the oil level is correct using the dipstick.
Example Answers
First, I gather tools like an oil filter wrench, drain pan, and the new oil. Then, I warm up the engine slightly so the oil flows out easier. After raising the vehicle securely, I drain the old oil and swap out the oil filter. Once that’s done, I refill it with new oil to the appropriate level and check for any leaks.
Don't Just Read Mobile Mechanic Questions - Practice Answering Them!
Reading helps, but actual practice is what gets you hired. Our AI feedback system helps you improve your Mobile Mechanic interview answers in real-time.
Personalized feedback
Unlimited practice
Used by hundreds of successful candidates
How do you approach diagnosing electrical problems in vehicles?
How to Answer
- 1
Start with gathering information from the owner about the symptoms.
- 2
Use a multimeter to check battery voltage and ground connections.
- 3
Inspect fuses and relays to identify obvious faults.
- 4
Utilize wiring diagrams to trace circuits relevant to the issue.
- 5
Perform systematic testing of components to isolate the problem.
Example Answers
I begin by talking to the vehicle owner to understand the symptoms they’ve experienced. Then, I check the battery voltage with a multimeter and inspect connections for corrosion. I look at fuses and relays next, and follow wiring diagrams to trace any faulty circuits.
What are the key components of a vehicle's braking system, and how do you test them?
How to Answer
- 1
Identify main components like brake pads, rotors, calipers, brake lines, and master cylinder.
- 2
Explain how to visually inspect components for wear and leaks.
- 3
Describe testing methods such as measuring rotor thickness and checking brake fluid level.
- 4
Mention performance tests like applying brakes at various speeds to assess effectiveness.
- 5
Highlight the importance of listening for unusual sounds during braking.
Example Answers
A vehicle's braking system includes brake pads, rotors, calipers, brake lines, and the master cylinder. I would visually inspect these components for wear, check the brake fluid level, and measure rotor thickness. To test the system, I would perform a brake application test at low and high speeds to ensure proper functioning.
What are some common issues you encounter with automatic transmissions and how do you resolve them?
How to Answer
- 1
Identify frequent problems like slipping, hard shifting, and fluid leaks.
- 2
Explain how to diagnose the issue using tools and tests.
- 3
Discuss common solutions like replacing seals or adjusting the transmission fluid level.
- 4
Mention the importance of regular maintenance to prevent transmission issues.
- 5
Share a specific example from your experience addressing a transmission problem.
Example Answers
I often encounter slipping in automatic transmissions due to low fluid levels. I first check the transmission fluid and look for any leaks. If the fluid is low, I top it up and monitor for leaks, which usually resolves the issue.
What routine maintenance tasks do you think are most important for vehicle longevity?
How to Answer
- 1
Mention the importance of regular oil changes to keep the engine running smoothly
- 2
Emphasize checking and replacing air filters for better engine performance
- 3
Discuss the significance of maintaining proper tire pressure and regular rotations
- 4
Include coolant system checks to prevent overheating issues
- 5
Highlight the necessity of regular brake inspections for safety and longevity
Example Answers
I believe regular oil changes are crucial for engine longevity, as dirty oil can lead to wear and tear. Additionally, checking and replacing air filters helps the engine breathe better and improves fuel efficiency.
What are some common problems associated with fuel systems, and how do you troubleshoot them?
How to Answer
- 1
Identify common fuel system issues like clogging, leaks, and fuel pump failure
- 2
Explain how to diagnose each issue step by step
- 3
Mention tools used for troubleshooting such as pressure gauges
- 4
Discuss visual inspections and testing fuel flow
- 5
Highlight the importance of checking for error codes in modern vehicles
Example Answers
Common problems in fuel systems include clogging in fuel filters and failing fuel pumps. To troubleshoot, I start by checking the fuel pressure using a gauge. If it's low, I inspect the fuel filter for blockages. I also look for leaks in the fuel lines and test the fuel pump operation.
Can you explain how to inspect and service a vehicle's suspension system?
How to Answer
- 1
Start with a visual inspection of the suspension components for wear and damage.
- 2
Check the shock absorbers and struts for leaks and proper function.
- 3
Inspect the bushings, ball joints, and control arms for play or deterioration.
- 4
Test drive the vehicle to identify any unusual noises or handling issues.
- 5
Perform a wheel alignment if necessary and replace any worn components.
Example Answers
To inspect a vehicle's suspension system, I begin with a visual check for any signs of damage to parts like the control arms and struts. Then, I check the shock absorbers for leaks and perform a test drive to listen for noises.
What steps do you take to assess tire conditions and when do you recommend replacement?
How to Answer
- 1
Check tread depth using the penny test or tread depth gauge
- 2
Inspect for visible damage like cuts, bulges, or cracks
- 3
Evaluate tire pressure and look for uneven wear patterns
- 4
Consider the age of the tires; replace if over 6 years
- 5
Recommend replacement if tread depth is below 2/32 inches or if damage is severe
Example Answers
I check the tread depth using the penny test. If the tread is below 2/32 inches, I recommend replacement. I also inspect for any visible damage and check tire pressure regularly.
How do you check and maintain the proper fluid levels in various systems of a vehicle?
How to Answer
- 1
Identify each fluid type: oil, coolant, brake fluid, transmission fluid, etc.
- 2
Check levels using dipsticks or reservoir markings.
- 3
Look for leaks or discoloration as indicators of potential issues.
- 4
Regularly top off fluids as needed based on manufacturer recommendations.
- 5
Keep a log of fluid checks and changes for maintenance records.
Example Answers
I first identify the different fluids in the vehicle, like oil and coolant. I check oil levels with a dipstick and coolant in the reservoir. I also look for signs of leaks or any discoloration that could indicate problems. I keep track of when I last checked and filled the fluids to ensure everything is maintained properly.
Don't Just Read Mobile Mechanic Questions - Practice Answering Them!
Reading helps, but actual practice is what gets you hired. Our AI feedback system helps you improve your Mobile Mechanic interview answers in real-time.
Personalized feedback
Unlimited practice
Used by hundreds of successful candidates
What experience do you have with modern diagnostic equipment and software?
How to Answer
- 1
Mention specific diagnostic tools you have used like scanners or multimeters
- 2
Describe your experience with automotive software, such as OBD-II or specialized manufacturer software
- 3
Share how you stay updated on new technologies in the automotive field
- 4
Provide an example of a problem you solved using diagnostic equipment
- 5
Highlight any training or certifications you have related to diagnostic tools
Example Answers
I have experience using several OBD-II scanners and coding tools to troubleshoot issues. Last month, I used a diagnostic tool to pinpoint an issue in a Ford F-150 which turned out to be a faulty sensor.
What is your approach to preventative maintenance and how do you educate customers about its importance?
How to Answer
- 1
Explain the benefits of preventative maintenance, including cost savings and safety.
- 2
Share specific preventative maintenance tasks you recommend for vehicles.
- 3
Discuss how you communicate effectively with customers about maintenance schedules.
- 4
Highlight any resources or materials you provide to customers for their education.
- 5
Use examples or anecdotes to illustrate the impact of preventative maintenance.
Example Answers
I emphasize that preventative maintenance helps avoid costly repairs and keeps vehicles safe. I recommend regular oil changes, fluid checks, and tire rotations. I explain these tasks to customers and provide them with a schedule based on their mileage.
Situational Interview Questions
If you arrive at a job and the vehicle won't start, what steps would you take to diagnose the issue?
How to Answer
- 1
Check the battery and connections for issues or corrosion.
- 2
Test for fuel getting to the engine by checking the fuel pump and fuel lines.
- 3
Scan for error codes using a diagnostic scanner if available.
- 4
Inspect fuses and relays that may affect the starting system.
- 5
Perform a visual inspection of the engine components for any obvious issues.
Example Answers
First, I would check the battery to see if it's charged and if the terminals are clean and tight. If the battery seems fine, I would then inspect the fuel system to ensure fuel is reaching the engine.
Imagine a customer is unhappy with the service provided. How would you address their concerns?
How to Answer
- 1
Listen carefully to the customer's complaints without interrupting
- 2
Acknowledge their feelings and express empathy for their situation
- 3
Apologize for any inconvenience caused and take responsibility
- 4
Investigate the issue to understand what went wrong and gather facts
- 5
Offer a solution or compansation that addresses their concerns
Example Answers
I would listen to the customer's concerns without interrupting, acknowledging their feelings. I'd apologize for the inconvenience and assure them that I will investigate the issue to find a resolution as quickly as possible.
Don't Just Read Mobile Mechanic Questions - Practice Answering Them!
Reading helps, but actual practice is what gets you hired. Our AI feedback system helps you improve your Mobile Mechanic interview answers in real-time.
Personalized feedback
Unlimited practice
Used by hundreds of successful candidates
If you notice unsafe conditions while performing repairs at a customer's location, what actions would you take?
How to Answer
- 1
Assess the severity of the unsafe condition immediately.
- 2
Communicate the issue to the customer clearly and professionally.
- 3
Determine if it's safe to continue working or if repairs need to be halted.
- 4
Suggest alternative solutions or locations if required.
- 5
Document the unsafe condition and any actions taken for future reference.
Example Answers
I would first assess how serious the unsafe condition is. If it’s severe, I would inform the customer about the risks and suggest pausing the repair. I’d then discuss alternative solutions, such as moving the vehicle to a safer location if possible.
What would you do if you were called to a roadside emergency involving a vehicle accident?
How to Answer
- 1
Assess the situation for safety before approaching the vehicle.
- 2
Call for emergency services if anyone is injured or if the accident is severe.
- 3
Use safety cones or warning triangles to protect the scene if necessary.
- 4
Check the vehicle to diagnose immediate mechanical issues and ensure safe operation.
- 5
Communicate clearly with the vehicle occupants and other responders about the situation.
Example Answers
I would first assess if it's safe to approach the accident site, then I'd call emergency services if there are injuries. After that, I'd set up warning triangles and check for any mechanical issues to help the driver.
If a tool breaks while you're working on a vehicle, how would you manage the situation?
How to Answer
- 1
Stay calm and assess the situation immediately.
- 2
Determine if the job can continue without the broken tool.
- 3
Identify an alternative tool or method to proceed.
- 4
Communicate with the customer if delays occur.
- 5
Report the broken tool for repair or replacement after the job.
Example Answers
If a tool breaks, I would first assess whether I can continue the work without it. If not, I'd look for a suitable replacement tool in my kit or nearby. I'd also inform the customer if it would cause a delay.
You have multiple service calls scheduled for the day, and one of the vehicles has a complex issue that is taking longer than expected. How do you handle this?
How to Answer
- 1
Prioritize communication with customers about delays
- 2
Assess the situation to determine if you can delegate other tasks
- 3
Keep track of time spent on the complex issue to manage your schedule
- 4
Consider rescheduling less urgent calls if necessary
- 5
Maintain a calm and professional demeanor throughout
Example Answers
I would first inform the customer about the delay and provide them with an estimated time of completion. Then, I would assess if I can tackle any simpler jobs in the meantime or if I need to reschedule later appointments.
If a customer insists on a repair that you believe is unnecessary, how do you communicate your professional opinion?
How to Answer
- 1
Acknowledge the customer's concerns and listen actively.
- 2
Explain your reasoning with clear, technical details.
- 3
Offer alternative solutions or recommendations.
- 4
Be respectful and patient in your communication.
- 5
Provide documentation or visual evidence to support your opinion.
Example Answers
I understand your concerns about the repair. I believe it's unnecessary because our diagnostics show everything is functioning well. I can suggest monitoring the issue instead.
If faced with a tight deadline and unexpected mechanical issues, how would you prioritize the tasks?
How to Answer
- 1
Assess the severity of each mechanical issue immediately
- 2
Identify which tasks are critical for meeting the deadline
- 3
Communicate with the customer about any changes in the plan
- 4
Break tasks into smaller manageable steps to stay organized
- 5
Utilize any available resources or tools to speed up the process
Example Answers
First, I would quickly assess the mechanical issues to determine which ones are the most serious and might impact safety. Then, I'd focus on the critical tasks that must be completed to meet the deadline while keeping the customer informed of my progress.
How would you handle the situation if you arrived at a job and discovered you did not have the necessary parts?
How to Answer
- 1
Stay calm and assess the situation clearly.
- 2
Communicate with the customer about the issue honestly.
- 3
Check if there are nearby suppliers where you can obtain the parts quickly.
- 4
Discuss alternative solutions or temporary fixes with the customer.
- 5
Document the incident and any agreed-upon follow-up actions.
Example Answers
If I arrive and don't have the necessary parts, I would first reassure the customer and explain the situation. I would then check for local suppliers to see if I can get the parts quickly, and if not, I would suggest a safe temporary solution until I can return with the right parts.
Mobile Mechanic Position Details
Recommended Job Boards
CareerBuilder
www.careerbuilder.com/jobs-mobile-mechanicZipRecruiter
www.ziprecruiter.com/Jobs/Mobile-Mechanic/These job boards are ranked by relevance for this position.
Related Positions
Ace Your Next Interview!
Practice with AI feedback & get hired faster
Personalized feedback
Used by hundreds of successful candidates
Ace Your Next Interview!
Practice with AI feedback & get hired faster
Personalized feedback
Used by hundreds of successful candidates