Top 30 Material Technician Interview Questions and Answers [Updated 2025]
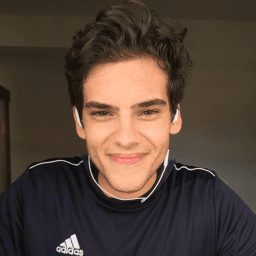
Andre Mendes
•
March 30, 2025
If you're preparing for a Material Technician interview, you've come to the right place. This post compiles the most common questions you might face, providing example answers and valuable tips to help you respond confidently and effectively. Whether you're a seasoned professional or new to the field, these insights will equip you with the knowledge to ace your interview and stand out from the competition.
Download Material Technician Interview Questions in PDF
To make your preparation even more convenient, we've compiled all these top Material Technicianinterview questions and answers into a handy PDF.
Click the button below to download the PDF and have easy access to these essential questions anytime, anywhere:
List of Material Technician Interview Questions
Situational Interview Questions
In an emergency situation requiring immediate material delivery, how would you ensure prompt handling and communication?
How to Answer
- 1
Assess the situation quickly to determine urgent material needs
- 2
Contact suppliers or vendors directly to expedite delivery
- 3
Use clear and concise communication with team members
- 4
Establish a priority list for materials required
- 5
Document all steps taken for accountability and future reference
Example Answers
In a situation like this, I would first assess the specific materials needed and then contact our suppliers directly to request expedited delivery. I would keep my team informed throughout the process to ensure everyone knows what's happening.
If you receive two urgent requests for different materials at the same time, how would you decide which one to fulfill first?
How to Answer
- 1
Assess the urgency and impact of each request on ongoing projects
- 2
Communicate with both requesters to gather more context
- 3
Determine if one request is time-sensitive with deadlines approaching
- 4
Consider the availability and readiness of materials for each request
- 5
Make a decision based on data and inform both parties promptly
Example Answers
I would first evaluate both requests to see which materials are critical to ongoing tasks. If one material is needed for a project with a tight deadline, I would prioritize that. I would also communicate with both requesters to ensure I make the best decision.
Don't Just Read Material Technician Questions - Practice Answering Them!
Reading helps, but actual practice is what gets you hired. Our AI feedback system helps you improve your Material Technician interview answers in real-time.
Personalized feedback
Unlimited practice
Used by hundreds of successful candidates
You notice an unexpected discrepancy in the inventory count. How would you investigate and address it?
How to Answer
- 1
Review the inventory records to identify where the discrepancies occurred
- 2
Check for any recent changes in stock management procedures or staff responsibilities
- 3
Communicate with team members to gather insights about the discrepancy
- 4
Conduct a physical count to confirm the accurate number of items in stock
- 5
Document the findings and adjust inventory records as necessary
Example Answers
I would start by reviewing the inventory records to pinpoint the discrepancy. Next, I would check for any recent changes in stock procedures and talk to team members about their knowledge of the situation. Finally, I would conduct a physical inventory count to verify and document the outcomes.
If a key supplier is unable to deliver materials on time, what actions would you take to minimize impact on production?
How to Answer
- 1
Assess the situation and gather information about the delay
- 2
Communicate with the supplier to understand the cause and possible alternatives
- 3
Explore alternative suppliers or materials that can be used temporarily
- 4
Prioritize production plans to focus on available materials
- 5
Inform stakeholders and keep them updated on the situation
Example Answers
I would first assess the situation by contacting the supplier to learn the specifics of the delay. If it seems prolonged, I would start looking for alternative suppliers or materials to ensure production continues. I'd also prioritize our production schedule based on what materials we currently have.
If you were tasked with implementing a new inventory procedure, how would you ensure successful adoption by the team?
How to Answer
- 1
Initiate communication with the team to explain the reasons for the change.
- 2
Involve team members in the development of the new procedure for their input.
- 3
Provide adequate training sessions to familiarize the team with the new system.
- 4
Set clear expectations and define the benefits of the new procedure.
- 5
Solicit feedback during and after the implementation to make adjustments as needed.
Example Answers
I would start by communicating the need for the new inventory procedure to the team, explaining how it can improve our efficiency. I would involve the team in discussions to gather their insights and make them feel included. Training would be crucial, so I would organize workshops to ensure everyone knows how to use the new system. Lastly, I would continuously seek feedback and be ready to adapt the procedure based on their experiences.
How would you handle a situation where the equipment used for material handling breaks down unexpectedly?
How to Answer
- 1
Stay calm and assess the situation quickly.
- 2
Notify your supervisor or the maintenance team immediately.
- 3
Evaluate alternative methods to continue operations if possible.
- 4
Document the breakdown details for future reference.
- 5
Communicate openly with your team about the situation.
Example Answers
In case of equipment failure, I would first remain calm and assess the situation. Then, I would notify my supervisor and the maintenance team about the issue. If feasible, I would look for alternative equipment or methods to keep our operations running smoothly while waiting for repairs.
If two departments need materials at the same time but have conflicting deadlines, how do you manage to prioritize?
How to Answer
- 1
Evaluate the urgency of each department's needs.
- 2
Communicate with both departments to understand their priorities.
- 3
Consider the impact on operations and project timelines.
- 4
Prioritize tasks based on deadlines and resource availability.
- 5
Document your decision to ensure transparency and accountability.
Example Answers
I would first assess which department's deadline is more critical to the overall project. Then, I would reach out to both departments to discuss their needs and explain the situation. After evaluating the urgency, I would prioritize the department that has a more significant impact and ensure that I provide them with the necessary materials first while trying to find a quick solution for the other department.
How would you approach training a new employee in your department to ensure they understand material handling procedures?
How to Answer
- 1
Start with an orientation to introduce the employee to the team and the workplace.
- 2
Provide a detailed overview of material handling procedures, including safety protocols.
- 3
Utilize hands-on demonstrations to show practical application of each procedure.
- 4
Assign a mentor or buddy who can provide ongoing support and answer questions.
- 5
Encourage feedback and ensure there are opportunities for the new employee to ask questions.
Example Answers
I would start with an orientation to welcome the new employee and introduce them to the team. Then, I would explain the material handling procedures in detail, focusing on safety. Next, I’d demonstrate the procedures in action and have the new employee practice under supervision. I would also assign them a mentor for further guidance.
What would you do if there was an unexpected surge in demand for a specific material?
How to Answer
- 1
Assess current inventory levels immediately to understand available stock.
- 2
Communicate with suppliers to check on the possibility of increasing orders.
- 3
Evaluate the production schedule and adjust priorities as needed.
- 4
Consider alternative materials if the surge is prolonged and demand is critical.
- 5
Keep stakeholders informed about the situation and any changes in supply timelines.
Example Answers
First, I would check our current inventory to see how much of the material we have on hand. Then, I would reach out to our suppliers to see if they can fulfill a larger order quickly. Meanwhile, I would adjust our production schedule to prioritize products that require this material. If the demand continues, I would look into alternative materials to keep production going.
How would you go about identifying opportunities to reduce costs in material procurement and usage?
How to Answer
- 1
Analyze historical data on material usage and costs to identify trends.
- 2
Engage with suppliers to explore bulk purchasing discounts or alternative materials.
- 3
Implement a just-in-time inventory system to minimize excess stock and storage costs.
- 4
Coordinate with the production team to align material specifications with actual needs.
- 5
Conduct regular reviews and audits of material consumption to identify wastage.
Example Answers
I would start by analyzing the historical data to identify patterns in material usage. Then, I would discuss with suppliers about potential bulk discounts. Additionally, I would evaluate our inventory practices to implement just-in-time strategies that could lower storage costs.
Don't Just Read Material Technician Questions - Practice Answering Them!
Reading helps, but actual practice is what gets you hired. Our AI feedback system helps you improve your Material Technician interview answers in real-time.
Personalized feedback
Unlimited practice
Used by hundreds of successful candidates
Behavioral Interview Questions
Can you describe a time when you identified a problem with inventory materials and how you resolved it?
How to Answer
- 1
Use the STAR method: Situation, Task, Action, Result.
- 2
Focus on a specific inventory issue you faced.
- 3
Explain the steps you took to identify the problem.
- 4
Detail the solution you implemented and its outcome.
- 5
Show how your actions improved the situation or process.
Example Answers
In my previous role, I noticed discrepancies in our inventory counts during our monthly audit (Situation). I was responsible for overseeing the inventory and realized we had excess materials that didn't match our records (Task). I conducted a thorough investigation and found that incorrect data entry was causing the issues (Action). I implemented a double-check system for data entry, which reduced errors by 30% in the following months (Result).
Tell me about a time when you worked as part of a team to complete a materials-related project. What was your role?
How to Answer
- 1
Choose a specific project that highlights teamwork in materials handling.
- 2
Clearly state your role and responsibilities in the project.
- 3
Mention specific outcomes and what the team accomplished.
- 4
Highlight any challenges faced and how you overcame them as a team.
- 5
Use the STAR method: Situation, Task, Action, Result.
Example Answers
In my last job, we were tasked with developing a new composite material for a construction project. My role was to coordinate material testing and analyze the results. Our teamwork led to a composite that met all strength requirements. We faced challenges in consistency, but regular meetings helped us troubleshoot effectively, resulting in a successful material launch.
Don't Just Read Material Technician Questions - Practice Answering Them!
Reading helps, but actual practice is what gets you hired. Our AI feedback system helps you improve your Material Technician interview answers in real-time.
Personalized feedback
Unlimited practice
Used by hundreds of successful candidates
Give an example of how your attention to detail has helped prevent a mistake in materials management.
How to Answer
- 1
Choose a specific incident where attention to detail was crucial.
- 2
Describe how you identified the potential mistake.
- 3
Explain the action you took to address the issue.
- 4
Include the positive outcome that resulted from your actions.
- 5
Keep your response focused and clear.
Example Answers
In my previous role, I was responsible for inventory audits. During one audit, I noticed a discrepancy in the stock levels reported versus what was physically present. I double-checked the counts and discovered an error in the data entry. I corrected the mistake before it led to a supply shortage, ensuring that production lines did not experience delays.
Describe a situation where you had to communicate a materials issue to colleagues or management. How did you ensure clarity?
How to Answer
- 1
Identify a specific materials issue you encountered.
- 2
Explain how you prepared for the communication, considering the audience.
- 3
Use clear and straightforward language to describe the issue and impact.
- 4
Provide a solution or recommendation along with the problem.
- 5
Encourage questions to clarify any misunderstandings.
Example Answers
In my previous role, we faced a shortage of a critical material which delayed production. I gathered all relevant data and prepared a brief report outlining the issue and its impact on our timelines. During the meeting, I presented the facts using clear visuals and encouraged questions to ensure everyone understood the situation.
Can you provide an example of how you adapted to a change in materials management processes?
How to Answer
- 1
Think of a specific situation where processes changed.
- 2
Describe the initial challenge and your response.
- 3
Highlight any skills or tools you used to adjust.
- 4
Mention the outcome or impact of your adaptation.
- 5
Keep your answer structured: situation, action, result.
Example Answers
In my previous role, we switched to a new inventory tracking software. Initially, it was difficult to navigate, but I organized training sessions for our team and learned the software on my own. This led to a smoother transition, and we improved our inventory accuracy by 20%.
Tell me about a time you took initiative to improve a process in your material technician role.
How to Answer
- 1
Think of a specific example where you saw a problem.
- 2
Explain how you identified the process that needed improvement.
- 3
Describe the steps you took to implement the change.
- 4
Share the results or impact of your initiative.
- 5
Make it clear how this benefited the team or organization.
Example Answers
In my previous role, I noticed that our inventory tracking system was causing delays. I proposed shifting to a digital tracking system. I researched options, convinced my supervisor to invest, and led the training. As a result, we reduced errors by 30% and saved two hours of work each week.
Describe a time when you had a disagreement with a coworker about material management and how you handled it.
How to Answer
- 1
Choose a specific disagreement that highlights a material management issue.
- 2
Explain your perspective clearly and rationally without placing blame.
- 3
Discuss how you listened to your coworker's viewpoint and sought common ground.
- 4
Share how you reached a resolution or compromise that benefited the team.
- 5
Reflect on what you learned from the experience to improve future collaborations.
Example Answers
I had a disagreement with a coworker about the appropriate type of concrete to use for a project. I believed a different mix would yield better durability. I presented my research and data to support my argument. After discussing, we reviewed samples and decided to test both options. Ultimately, the team chose my suggestion, but I valued the input I received from my coworker.
Provide an example of how you managed multiple competing tasks in your role as a material technician.
How to Answer
- 1
Identify key tasks and their deadlines
- 2
Prioritize based on urgency and importance
- 3
Communicate with team members about workload
- 4
Use organizational tools or software to track progress
- 5
Be flexible and ready to adjust plans as needed
Example Answers
In my last role, we faced a tight deadline on a project while also preparing for an audit. I prioritized the project tasks, communicated with my team to delegate some audit preparations, and used a project management tool to keep everything on track. This allowed us to meet both deadlines successfully.
Describe a process improvement you made that increased efficiency in managing materials.
How to Answer
- 1
Identify a specific process you improved.
- 2
Explain the problem you were facing.
- 3
Describe your solution and how you implemented it.
- 4
Highlight the measurable outcome or benefit.
- 5
Keep your answer concise and to the point.
Example Answers
In my previous role, the manual inventory tracking process often led to discrepancies. I developed an automated system using Excel macros that reduced errors in tracking by 30%. This change saved us hours each week in manual checks.
Don't Just Read Material Technician Questions - Practice Answering Them!
Reading helps, but actual practice is what gets you hired. Our AI feedback system helps you improve your Material Technician interview answers in real-time.
Personalized feedback
Unlimited practice
Used by hundreds of successful candidates
Technical Interview Questions
What tools or software have you used to manage and track inventory levels?
How to Answer
- 1
Mention specific tools or software you've used like ERP systems or spreadsheets
- 2
Explain how you utilized these tools in your previous roles
- 3
Include any relevant experience with inventory management processes
- 4
Highlight any efficiency improvements achieved through these tools
- 5
Be prepared to discuss your comfort level with technology and learning new systems
Example Answers
I have used Microsoft Excel extensively for tracking inventory levels with formulas and pivot tables to analyze stock data. This helped us identify slow-moving items and reduce overstock by 20%.
What are the OSHA guidelines for safe material handling practices, and how do you apply them in your work?
How to Answer
- 1
Familiarize yourself with OSHA’s general guidelines for material handling.
- 2
Discuss specific practices such as proper lifting techniques or use of personal protective equipment.
- 3
Mention the importance of training and ensuring coworkers are aware of safety protocols.
- 4
Provide examples of how you've implemented these guidelines in past work experiences.
- 5
Emphasize the role of documentation and reporting in maintaining safety standards.
Example Answers
OSHA guidelines state to follow proper lifting techniques, such as keeping your back straight and lifting with your legs. In my previous job, I ensured we had lifting workshops that reinforced these practices and improved safety.
Don't Just Read Material Technician Questions - Practice Answering Them!
Reading helps, but actual practice is what gets you hired. Our AI feedback system helps you improve your Material Technician interview answers in real-time.
Personalized feedback
Unlimited practice
Used by hundreds of successful candidates
How do you analyze inventory data to make procurement decisions?
How to Answer
- 1
Review historical usage data to identify trends and patterns.
- 2
Use inventory turnover rates to assess product performance.
- 3
Consider lead times and supplier reliability in your analysis.
- 4
Implement inventory management software for real-time insights.
- 5
Collaborate with sales and production teams for aligned forecasts.
Example Answers
I analyze historical usage data to find trends, then check inventory turnover rates to see how quickly products sell. I also take lead times into account to ensure we don’t run out of key materials.
What steps do you take to ensure safety when handling hazardous materials?
How to Answer
- 1
Always wear appropriate personal protective equipment such as gloves, goggles, and masks.
- 2
Follow all safety data sheets (SDS) for the materials you are handling.
- 3
Label and store hazardous materials properly to avoid spills or accidents.
- 4
Maintain a clean and organized workspace to reduce hazards.
- 5
Regularly participate in safety training and drills to stay updated on best practices.
Example Answers
I always ensure to wear the correct PPE like gloves and masks, and I strictly follow the safety data sheets for any material I handle.
Explain how you document material usage and why proper documentation is important.
How to Answer
- 1
Start by describing the methods you use for documentation such as logs or software.
- 2
Mention the types of materials you track and the units of measurement.
- 3
Explain the importance of accuracy in documentation for inventory control.
- 4
Emphasize compliance with regulatory requirements and safety standards.
- 5
Conclude with how proper documentation helps in project planning and budgeting.
Example Answers
I document material usage by maintaining a detailed log where I record the type, quantity, and date of materials used. This helps me keep track of inventory levels and ensures we always have the materials we need for projects.
What methods do you use to ensure the quality of materials before they are used in production?
How to Answer
- 1
Describe specific quality control procedures you follow.
- 2
Mention the use of inspection tools or equipment.
- 3
Explain how you document and track material quality.
- 4
Include any standards or regulations you adhere to.
- 5
Discuss your collaboration with suppliers for quality assurance.
Example Answers
I perform regular inspections on incoming materials using calipers and spectrometers to ensure they meet specifications, and I document these checks in our quality control log.
How do you work with production schedules to ensure materials are available when needed?
How to Answer
- 1
Review production schedules regularly to anticipate material needs
- 2
Communicate with production teams to understand their requirements
- 3
Coordinate with suppliers for timely delivery of materials
- 4
Utilize inventory management systems to track stock levels
- 5
Plan for contingencies to handle unexpected changes in production
Example Answers
I consistently review production schedules on a weekly basis to anticipate material needs. I also maintain open communication with production teams to adapt to any changes in their requirements, ensuring we order materials in advance.
How do you determine the compatibility of different materials for a specific job?
How to Answer
- 1
Assess the properties of each material like strength, flexibility, and durability
- 2
Consider environmental factors such as temperature and exposure to chemicals
- 3
Evaluate the intended use and load requirements of the application
- 4
Check compatibility through testing and industry standards
- 5
Consult relevant literature and collaborate with experienced colleagues for insights
Example Answers
I start by analyzing the mechanical properties of the materials and how they apply to the specific job requirements. Then, I look into environmental conditions, ensuring the materials can withstand them, and finally, I may run compatibility tests if needed.
What are some strategies you use to optimize space in material storage areas?
How to Answer
- 1
Implement vertical storage solutions to maximize height.
- 2
Use shelving units that can be adjusted for different material sizes.
- 3
Organize materials by frequency of use to allow easy access.
- 4
Utilize inventory management software to track space utilization.
- 5
Regularly assess and purge obsolete materials to free up space.
Example Answers
I focus on vertical storage by installing high shelving units, which allows us to use the height of the area efficiently. Additionally, I organize materials on shelves by how often they're used, keeping frequently used items at eye level for quick access.
Explain how you assess suppliers to ensure the quality and reliability of materials.
How to Answer
- 1
Research supplier background and reputation before engagement.
- 2
Request and evaluate samples or trial orders for quality assessment.
- 3
Establish clear quality standards and specifications for materials.
- 4
Conduct regular audits and inspections of supplier facilities.
- 5
Maintain communication with suppliers for continuous improvement.
Example Answers
I research suppliers by checking their industry reputation and reviews. I request samples to ensure they meet our quality standards. Regular audits keep us informed about their production practices.
Don't Just Read Material Technician Questions - Practice Answering Them!
Reading helps, but actual practice is what gets you hired. Our AI feedback system helps you improve your Material Technician interview answers in real-time.
Personalized feedback
Unlimited practice
Used by hundreds of successful candidates
Material Technician Position Details
Salary Information
Recommended Job Boards
CareerBuilder
www.careerbuilder.com/jobs/materials-technicianZipRecruiter
www.ziprecruiter.com/Jobs/Materials-TechnicianThese job boards are ranked by relevance for this position.
Related Positions
Ace Your Next Interview!
Practice with AI feedback & get hired faster
Personalized feedback
Used by hundreds of successful candidates
Ace Your Next Interview!
Practice with AI feedback & get hired faster
Personalized feedback
Used by hundreds of successful candidates