Top 30 Materials Technician Interview Questions and Answers [Updated 2025]
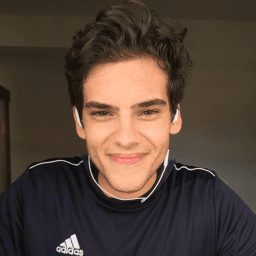
Andre Mendes
•
March 30, 2025
Preparing for a Materials Technician interview? This post is your ultimate guide to acing it! We've compiled the most common interview questions for the role, complete with example answers and tips to help you respond confidently and effectively. Whether you're a seasoned professional or a fresh entrant to the field, our insights will equip you with the knowledge and skills to impress your interviewers.
Download Materials Technician Interview Questions in PDF
To make your preparation even more convenient, we've compiled all these top Materials Technicianinterview questions and answers into a handy PDF.
Click the button below to download the PDF and have easy access to these essential questions anytime, anywhere:
List of Materials Technician Interview Questions
Behavioral Interview Questions
Can you describe a time when you had to solve a difficult materials-related problem? What was the challenge and how did you address it?
How to Answer
- 1
Use the STAR method: Situation, Task, Action, Result.
- 2
Choose a specific example related to materials testing or selection.
- 3
Explain the challenge clearly and how it impacted the project.
- 4
Detail the steps you took to solve the problem and why you chose those actions.
- 5
Conclude with the positive outcome and what you learned from the experience.
Example Answers
In my previous role, we faced a significant issue with a batch of composite materials that did not meet strength specifications. The task was to identify the source of the failure quickly. I led a team to conduct a thorough analysis of the materials and processes, discovering that improper mixing ratios were used. We adjusted the mixing process and retested the materials, resulting in a successful outcome that met the required standards. This experience taught me the importance of precise process control.
Give an example of a time when your attention to detail prevented a mistake in a project.
How to Answer
- 1
Think of a specific project where detail was crucial.
- 2
Describe the situation clearly and the mistake that could have happened.
- 3
Explain how your attention to detail helped in identifying and fixing the issue.
- 4
Conclude with the positive outcome due to your actions.
- 5
Use the STAR method: Situation, Task, Action, Result.
Example Answers
During my internship, I was responsible for testing material samples. I noticed a discrepancy in the dimensions of a sample compared to our standards. By double-checking the measurements, I identified an error in the preparation process. Correcting this ensured that we presented accurate results and avoided costly delays in production.
Don't Just Read Materials Technician Questions - Practice Answering Them!
Reading helps, but actual practice is what gets you hired. Our AI feedback system helps you improve your Materials Technician interview answers in real-time.
Personalized feedback
Unlimited practice
Used by hundreds of successful candidates
Describe a successful team project you were involved in. What was your role and contribution?
How to Answer
- 1
Choose a specific project that had a clear outcome
- 2
Highlight your role and specific contributions
- 3
Emphasize teamwork and collaboration aspects
- 4
Discuss any challenges faced and how you overcame them
- 5
Conclude with the impact of the project on your team or organization
Example Answers
In my last job, I worked on a project to develop a new composite material for automotive parts. My role was a materials tester, and I conducted various strength tests on prototypes. The team collaborated closely, and I shared test results which helped us refine our designs. This project increased material efficiency by 15%.
Tell me about a time when you improved a process or method in a technical setting. What was the outcome?
How to Answer
- 1
Choose a specific example from your experience.
- 2
Describe the initial problem with the process.
- 3
Explain the steps you took to improve it clearly.
- 4
Highlight the measurable outcomes of the improvement.
- 5
Connect the experience to how it makes you a good fit for the role.
Example Answers
In my previous job, I noticed that the material testing process took too long. I proposed implementing a new software tool that automated data collection. After the change, we reduced testing time by 30% and improved accuracy.
Describe a situation where you had a conflict with a coworker. How did you resolve it?
How to Answer
- 1
Choose a specific example where the conflict was clear
- 2
Explain the cause of the conflict briefly
- 3
Focus on your actions and communication
- 4
Emphasize the resolution and what you learned
- 5
Show how it improved your working relationship or the team dynamics
Example Answers
In my previous role, I had a disagreement with a coworker about the best approach to a project. We both had different ideas and it led to some tension. I suggested we sit down and discuss our viewpoints openly. By listening to each other's concerns and finding common ground, we were able to combine our ideas into a solid plan. This not only resolved the conflict but also strengthened our collaboration.
Provide an example of how you adapted to a significant change at work.
How to Answer
- 1
Think of a specific change you faced, such as new technology or procedures.
- 2
Explain the situation briefly and what prompted the change.
- 3
Describe the steps you took to adapt, highlighting your proactive approach.
- 4
Share the positive outcome or benefits that resulted from your adaptation.
- 5
Keep it relevant to the materials technician role, focusing on skills that apply.
Example Answers
At my previous job, we switched to a new materials tracking software. I took the initiative to attend extra training sessions and helped my team adapt by sharing tips and creating a guide. This led to improved efficiency in our inventory management process.
How do you prioritize your tasks when working on multiple projects simultaneously?
How to Answer
- 1
Identify deadlines for each project and create a timeline.
- 2
Assess the impact of each task on project goals.
- 3
Use a task management tool to organize and track progress.
- 4
Communicate with team members about progress and challenges.
- 5
Be flexible and ready to adjust priorities as needed.
Example Answers
I start by listing all projects and their deadlines. Then, I evaluate which tasks have the biggest impact. I use a project management tool to visualize my workflow and constantly communicate with my team about our priorities.
Describe a time when you took initiative to solve a problem in the workplace.
How to Answer
- 1
Identify a specific problem you faced that required immediate attention.
- 2
Explain the steps you took to address the issue proactively.
- 3
Highlight the positive outcome as a result of your initiative.
- 4
Use the STAR method: Situation, Task, Action, Result for clarity.
- 5
Keep your answer focused and relevant to materials technician duties.
Example Answers
At my previous job, we faced a critical shortage of a specific material which was delaying production. I took the initiative to contact multiple suppliers and sourced an alternative material that met our specifications. This action not only resolved the immediate shortage but also established a new relationship with a reliable supplier, improving our supply chain.
Give an example of a time when you managed your time efficiently under a tight deadline.
How to Answer
- 1
Choose a specific project or task with a deadline.
- 2
Explain the steps you took to prioritize tasks.
- 3
Highlight the tools or techniques you used to stay on track.
- 4
Mention the outcome and what you learned from the experience.
- 5
Keep your answer focused and to the point.
Example Answers
In my last role, we had a product launch that was delayed, and I had only three days to analyze materials and prepare a report. I created a checklist of essential tasks and prioritized them based on impact. I used project management software to track my progress and ensured I stayed focused by eliminating distractions. As a result, I submitted the report one day early, which helped the team make important decisions ahead of schedule.
Don't Just Read Materials Technician Questions - Practice Answering Them!
Reading helps, but actual practice is what gets you hired. Our AI feedback system helps you improve your Materials Technician interview answers in real-time.
Personalized feedback
Unlimited practice
Used by hundreds of successful candidates
Technical Interview Questions
How do you analyze and interpret data from material tests?
How to Answer
- 1
Start by explaining the importance of accurate data collection.
- 2
Discuss specific analytical methods you use, such as statistical analysis or software tools.
- 3
Mention how you ensure data validity and reliability.
- 4
Describe how you interpret the results in the context of material properties.
- 5
Provide an example of how data influenced a decision or a project.
Example Answers
I ensure accurate data collection by following standardized testing procedures. I frequently use statistical analysis tools like R or Excel to interpret the results, checking for validity using control standards. For example, in a recent project, the tensile strength data informed our choice of materials, leading to better performance.
What are the different methods used for material testing, and how do you determine which method to use?
How to Answer
- 1
List common material testing methods such as tensile, compression, and hardness tests.
- 2
Explain the purpose of each method briefly.
- 3
Discuss factors influencing the choice of method like material type and testing standards.
- 4
Mention the importance of accuracy and reproducibility in testing.
- 5
Share a real-life example of selecting a testing method for a specific material.
Example Answers
There are several methods for material testing including tensile testing, which measures the strength of materials under tension, compression testing for materials under pressure, and hardness testing to assess the hardness of a material. The choice of method depends on the material type, its intended application, and relevant industry standards like ASTM or ISO.
Don't Just Read Materials Technician Questions - Practice Answering Them!
Reading helps, but actual practice is what gets you hired. Our AI feedback system helps you improve your Materials Technician interview answers in real-time.
Personalized feedback
Unlimited practice
Used by hundreds of successful candidates
What safety protocols are essential when working with hazardous materials?
How to Answer
- 1
Identify common safety protocols relevant to hazardous materials.
- 2
Mention the use of personal protective equipment (PPE).
- 3
Explain the importance of proper labeling and storage.
- 4
Discuss the need for training and emergency response plans.
- 5
Highlight the role of safety data sheets (SDS).
Example Answers
It is essential to always wear appropriate PPE, such as gloves and goggles, when handling hazardous materials. Proper labeling and storage are critical to avoid accidents, and we must have emergency response plans in place in case of spills or exposure. Additionally, safety data sheets must be reviewed regularly to stay informed about the materials we are working with.
What are the most important properties to consider when selecting a material for a specific application?
How to Answer
- 1
Identify the application requirements clearly before choosing a material
- 2
Consider mechanical properties like strength, ductility, and hardness
- 3
Evaluate environmental factors such as temperature and corrosion resistance
- 4
Think about cost-effectiveness and availability of materials
- 5
Discuss the impact of weight and ease of fabrication on material selection
Example Answers
When selecting a material, it's essential to first understand the application requirements. Key properties to consider are strength and ductility for load-bearing applications, as well as temperature resistance if it’s going to be exposed to high heat.
Explain the process of selecting materials for a new product design.
How to Answer
- 1
Identify the product requirements such as functionality, weight, and cost.
- 2
Evaluate material properties including strength, durability, and conductivity.
- 3
Consider manufacturing processes and how materials will be shaped or formed.
- 4
Assess environmental impact and sustainability of material choices.
- 5
Test and prototype with selected materials to validate their performance.
Example Answers
To select materials for a new product design, I first gather the product requirements, such as the need for lightweight yet durable materials. Then, I evaluate various materials based on their properties like tensile strength and thermal resistance. I consider how materials can be processed to meet design requirements and also check for environmental considerations. Finally, I prototype using the chosen materials to ensure they perform as expected.
What regulations and standards are important for material technicians to be aware of?
How to Answer
- 1
Identify key regulations such as ASTM, ISO, and ASME relevant to materials testing.
- 2
Mention safety standards like OSHA that impact materials handling and testing.
- 3
Discuss any industry-specific standards that apply to your field, like AASHTO for civil materials.
- 4
Emphasize understanding of local and state regulations that affect material usage.
- 5
Be ready to explain how these standards influence your daily work and decision-making.
Example Answers
As a materials technician, I stay updated on critical standards such as ASTM for testing procedures, ISO for quality management, and OSHA regulations for workplace safety. Each of these guides my process and ensures compliance.
What are the uses of microscopy in material analysis, and what types do you typically use?
How to Answer
- 1
Start by explaining the general role of microscopy in material analysis.
- 2
Mention specific applications such as examining surface structures and defects.
- 3
Discuss the types of microscopy you are familiar with, like optical, electron, or scanning probe.
- 4
Provide examples of materials or projects where microscopy was crucial.
- 5
Be prepared to explain the benefits of each microscopy type you mention.
Example Answers
Microscopy plays a crucial role in material analysis by allowing us to examine the microstructure of materials, identify defects, and assess surface features. I typically use optical microscopy for general observations and electron microscopy for high-resolution imaging of nanoparticle structures.
What techniques do you use to conduct failure analysis in materials?
How to Answer
- 1
Begin with identifying the type of failure observed.
- 2
Use systematic approaches like visual inspection and non-destructive testing.
- 3
Apply materials characterization techniques such as microscopy or spectroscopy.
- 4
Document all findings and compare with standards for similar materials.
- 5
Conclude with recommendations based on the analysis and findings.
Example Answers
I start by identifying the failure type, then conduct a visual inspection followed by non-destructive testing. For deeper analysis, I utilize microscopy to examine microstructural features and compare them with relevant material standards.
How do you ensure competency with the latest material testing standards and procedures?
How to Answer
- 1
Regularly attend workshops and training sessions on material testing.
- 2
Subscribe to industry journals and online resources for updates.
- 3
Participate in professional organizations related to materials science.
- 4
Engage with peers to discuss new standards and share best practices.
- 5
Stay hands-on with testing equipment to maintain practical skills.
Example Answers
I ensure my competency by regularly attending workshops and training sessions on the latest material testing standards. I also subscribe to industry journals to keep myself updated with new developments.
Why is instrument calibration important in material testing, and how is it performed?
How to Answer
- 1
Explain importance of accuracy in test results for material quality.
- 2
Mention compliance with industry standards and regulations.
- 3
Describe the steps involved in the calibration process.
- 4
Emphasize routine calibration checks and maintenance.
- 5
Highlight consequences of uncalibrated instruments.
Example Answers
Instrument calibration is crucial in material testing to ensure that we obtain accurate and reliable test results. Accurate measurements guarantee the quality and safety of materials, which is vital in industries like construction and manufacturing. Typically, calibration involves comparing the instrument reading to a known standard and making adjustments as necessary, following a routine schedule to maintain accuracy.
Don't Just Read Materials Technician Questions - Practice Answering Them!
Reading helps, but actual practice is what gets you hired. Our AI feedback system helps you improve your Materials Technician interview answers in real-time.
Personalized feedback
Unlimited practice
Used by hundreds of successful candidates
Situational Interview Questions
You discover a batch of materials that seems to be out of spec. How would you handle this situation?
How to Answer
- 1
Assess the extent of the issue and verify the out-of-spec data.
- 2
Document all findings and communicate them to your supervisor immediately.
- 3
Investigate the root cause of the deviation by reviewing the production process.
- 4
Determine if the materials can be reworked or if they need to be discarded.
- 5
Ensure that all relevant personnel are informed and involved in the resolution process.
Example Answers
I would first confirm the out-of-spec condition by double-checking the measurements. After that, I would document everything and notify my supervisor. Then, I would investigate the cause, perhaps checking the production logs for anomalies. Depending on my findings, I would decide on reworking the materials or discarding them.
Imagine a critical piece of equipment malfunctions during an important test. What steps would you take to resolve this issue?
How to Answer
- 1
Assess the situation quickly to understand the malfunction.
- 2
Check the equipment manual for troubleshooting steps.
- 3
Communicate with team members about the issue.
- 4
Take immediate action to rectify the issue or implement a workaround.
- 5
Document the incident for future reference and prevent recurrence.
Example Answers
I would first assess the situation to identify what specifically malfunctioned. Then, I would refer to the equipment manual for troubleshooting guidelines. I would inform my team to keep everyone in the loop and implement any immediate fixes or adjustments. Finally, I would document the incident to help with future prevention.
Don't Just Read Materials Technician Questions - Practice Answering Them!
Reading helps, but actual practice is what gets you hired. Our AI feedback system helps you improve your Materials Technician interview answers in real-time.
Personalized feedback
Unlimited practice
Used by hundreds of successful candidates
You are behind schedule on a project due to a setback. How do you plan to meet the deadline?
How to Answer
- 1
Assess the reasons for the delay quickly and identify the most critical issues.
- 2
Prioritize the remaining tasks based on urgency and impact on the project.
- 3
Communicate with the team and stakeholders about the delay and your plan.
- 4
Consider reallocating resources or adjusting workflows to speed up progress.
- 5
Set short-term goals to track progress and ensure accountability.
Example Answers
I would first assess what caused the delay and focus on the main issues. I would then prioritize tasks that are critical to meeting the deadline. Next, I would communicate these priorities to my team and ensure everyone is aligned. If needed, I would look into reallocating resources to the critical tasks to speed up the process.
A client is unhappy with the quality of materials provided. How would you address their concerns?
How to Answer
- 1
Listen carefully to the client's concerns and acknowledge their feelings.
- 2
Ask for specific examples of the quality issues they are facing.
- 3
Explain how you plan to investigate the problem and ensure quality.
- 4
Offer a solution or alternative materials that meet their standards.
- 5
Follow up with the client after the resolution to ensure satisfaction.
Example Answers
I would first listen to the client's concerns and ask them to share specific examples of the quality issues. Then, I would investigate the problem and work with my team to find a solution or alternative materials that meet their expectations.
Resources are limited, and multiple tasks are competing for priority. How do you decide which task to address first?
How to Answer
- 1
Assess the urgency of each task and their deadlines
- 2
Evaluate the impact of each task on overall project goals
- 3
Consider dependencies—what tasks rely on the completion of others
- 4
Communicate with team members for input on priorities
- 5
Make a list to visually prioritize tasks based on criteria
Example Answers
I first assess deadlines and urgency, focusing on tasks that are due soonest. Then, I look at how each task impacts project goals, prioritizing those with greater significance.
You receive unexpected results during a test. How would you proceed to ensure accuracy?
How to Answer
- 1
Review the test procedure and confirm it was followed correctly
- 2
Double-check your equipment and calibration to rule out malfunctions
- 3
Repeat the test to see if you can replicate the results
- 4
Analyze the data for any anomalies or outliers that could explain discrepancies
- 5
Consult with a colleague or supervisor for a second opinion on the results
Example Answers
I would first review the test procedure to ensure I followed it correctly. Next, I would check the calibration of my equipment. After that, I would repeat the test to see if I get the same unexpected result.
You notice inventory levels are inaccurate. What steps would you take to correct and prevent this issue?
How to Answer
- 1
Conduct a physical inventory audit immediately to verify current stock levels
- 2
Identify discrepancies between actual counts and system records
- 3
Implement a regular inventory review schedule to monitor accuracy
- 4
Train staff on proper inventory management practices
- 5
Consider using inventory management software for real-time tracking
Example Answers
First, I would perform a full physical count of the inventory to compare against our records. Then, I would analyze where the discrepancies are occurring and adjust the records accordingly. Next, I would set up a regular audit schedule and ensure my team receives training on accurate inventory management to minimize future errors.
A superior asks you to overlook a minor safety violation to meet a deadline. How do you handle the situation?
How to Answer
- 1
Acknowledge the request and express understanding of the importance of deadlines.
- 2
Emphasize the importance of safety and how violations can lead to bigger problems.
- 3
Politely explain your concerns about overlooking safety and propose alternatives.
- 4
Offer to discuss possible solutions that can meet both safety and deadline requirements.
- 5
Stay calm and assertive, ensuring you maintain professionalism throughout.
Example Answers
I understand the pressure to meet deadlines, but safety is critical. Overlooking this violation could lead to serious consequences. I suggest we look for a solution that ensures safety while trying to meet the deadline.
You need to present complex technical information to a non-technical audience. How do you approach this?
How to Answer
- 1
Understand your audience's background and needs
- 2
Break down complex information into simple concepts
- 3
Use analogies or relatable examples to explain technical terms
- 4
Visualize data with charts or diagrams to enhance understanding
- 5
Encourage questions and be prepared to clarify points
Example Answers
I first assess the audience's familiarity with the topic, then I distill the technical concepts into 2-3 core ideas. For instance, if explaining a new material's properties, I might relate it to everyday items they are familiar with. Additionally, I use charts to show comparisons visually and always invite questions to ensure clarity.
You are asked to take on an additional project while already fully occupied. How do you handle this situation?
How to Answer
- 1
Assess your current workload and priorities clearly.
- 2
Communicate openly with your supervisor about your capacity.
- 3
Consider possible adjustments to your current tasks.
- 4
Evaluate the importance and urgency of the new project.
- 5
Suggest alternatives or take on the new project with a plan.
Example Answers
I would first review my current tasks and deadlines then discuss my workload with my supervisor to see if we can adjust priorities or timelines, ensuring I can still contribute effectively.
Don't Just Read Materials Technician Questions - Practice Answering Them!
Reading helps, but actual practice is what gets you hired. Our AI feedback system helps you improve your Materials Technician interview answers in real-time.
Personalized feedback
Unlimited practice
Used by hundreds of successful candidates
Materials Technician Position Details
Salary Information
Recommended Job Boards
CareerBuilder
www.careerbuilder.com/jobs-materials-technicianZipRecruiter
www.ziprecruiter.com/Jobs/Materials-TechnicianThese job boards are ranked by relevance for this position.
Related Positions
Ace Your Next Interview!
Practice with AI feedback & get hired faster
Personalized feedback
Used by hundreds of successful candidates
Ace Your Next Interview!
Practice with AI feedback & get hired faster
Personalized feedback
Used by hundreds of successful candidates