Top 30 Materials Management Technician Interview Questions and Answers [Updated 2025]
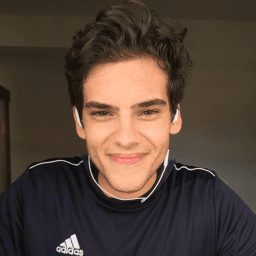
Andre Mendes
•
March 30, 2025
Embarking on a career as a Materials Management Technician requires not only technical expertise but also a readiness to tackle challenging interview questions. In this post, we delve into the most common questions asked in interviews for this role, providing insightful example answers and tips on how to respond effectively. Whether you're preparing for an interview or seeking to refine your skills, this guide is designed to help you succeed.
Download Materials Management Technician Interview Questions in PDF
To make your preparation even more convenient, we've compiled all these top Materials Management Technicianinterview questions and answers into a handy PDF.
Click the button below to download the PDF and have easy access to these essential questions anytime, anywhere:
List of Materials Management Technician Interview Questions
Behavioral Interview Questions
Tell me about a time you successfully managed a fluctuating inventory level in a previous role.
How to Answer
- 1
Choose a specific example with a clear context.
- 2
Describe the challenges posed by the fluctuating inventory levels.
- 3
Explain the strategies you implemented to manage the fluctuations.
- 4
Highlight the outcomes and how they benefited the organization.
- 5
Use metrics or results to quantify your success.
Example Answers
In my last role, we experienced a sudden spike in demand for a key product. I analyzed past inventory data and predicted requirements, coordinated with suppliers for faster deliveries, and implemented a just-in-time strategy. As a result, we reduced stockouts by 30% and improved customer satisfaction.
Describe a situation where you had to communicate complex inventory data to a non-technical team. How did you ensure clarity?
How to Answer
- 1
Simplify the data using visuals like charts or graphs.
- 2
Use everyday language and avoid technical jargon.
- 3
Focus on key insights rather than all the details.
- 4
Engage the audience with questions to check their understanding.
- 5
Provide a summary of main points at the end of your explanation.
Example Answers
In my last role, I presented inventory turnover rates to the sales team. I created a simple bar chart showing the turnover ratios over the past year. I explained the key points in plain language, highlighting how these rates impacted their sales targets. I asked if they had any questions to clarify and summarized the main insights at the end.
Don't Just Read Materials Management Technician Questions - Practice Answering Them!
Reading helps, but actual practice is what gets you hired. Our AI feedback system helps you improve your Materials Management Technician interview answers in real-time.
Personalized feedback
Unlimited practice
Used by hundreds of successful candidates
Can you provide an example of a problem you faced in materials management and how you solved it?
How to Answer
- 1
Identify a specific materials management problem you encountered.
- 2
Describe the impact of the problem on operations or costs.
- 3
Explain the steps you took to analyze and address the issue.
- 4
Highlight any tools or techniques you used to implement the solution.
- 5
Conclude with the positive outcome or lesson learned from the experience.
Example Answers
In my previous role, we faced a shortage of critical materials that halted production. I analyzed inventory levels and identified the supplier issue. I negotiated with a backup supplier to expedite delivery, which resolved the issue and minimized downtime.
Describe a time you worked as part of a team to improve a supply chain process.
How to Answer
- 1
Think of a specific project or task involving a team.
- 2
Identify the problem in the supply chain you aimed to improve.
- 3
Describe your role and contributions to the team effort.
- 4
Explain the outcome and how it benefited the supply chain.
- 5
Keep it concise and focus on measurable improvements.
Example Answers
In my previous job, our team faced delays in inventory delivery. I suggested we implement a new tracking system. I worked with IT to set it up, and we trained staff. As a result, our delivery times improved by 20%.
Have you ever disagreed with a supervisor or colleague about how to manage materials? How did you handle it?
How to Answer
- 1
Describe the situation clearly and briefly.
- 2
Focus on the disagreement and the reasoning behind your perspective.
- 3
Emphasize your communication skills and ability to listen.
- 4
Highlight any positive outcome or compromise you reached.
- 5
Show how the experience improved your teamwork or processes.
Example Answers
In a previous role, I disagreed with my supervisor about the ordering frequency of materials. I felt we were overstocking. I presented data showing our consumption rates and discussed potential waste. We adjusted the order schedule, resulting in a 15% reduction in costs.
Tell me about a time when a change in company policy affected your materials management process.
How to Answer
- 1
Identify a specific policy change you experienced.
- 2
Describe how it impacted your daily operations or processes.
- 3
Explain the actions you took to adapt to the change.
- 4
Highlight any positive outcomes or lessons learned.
- 5
Keep it concise and focus on your role in the situation.
Example Answers
When our company implemented a new policy on vendor selection, I had to adjust our inventory procurement process. I researched new vendors compatible with our requirements, and after testing their materials, I streamlined our ordering process, which improved lead times by 20%.
Give an example of how you have effectively managed your time to meet multiple deadlines in materials management.
How to Answer
- 1
Identify specific tasks you prioritized based on urgency and importance.
- 2
Describe a situation where you used tools or software for tracking deadlines.
- 3
Mention how you communicated with team members to coordinate efforts.
- 4
Include an example of adjusting your schedule to accommodate unexpected changes.
- 5
Conclude with the positive outcome that resulted from your time management.
Example Answers
In my previous role, I had to manage the inventory for multiple projects. I prioritized tasks by deadlines and used a project management tool to track progress. I communicated regularly with my team to ensure we were all aligned. When an unexpected shipment delay occurred, I adjusted my schedule to focus on sourcing alternative materials swiftly. This proactive approach ensured we met all project deadlines.
Tell me about a time you had to prioritize tasks in a high-pressure situation. What criteria did you use?
How to Answer
- 1
Choose a specific past experience to discuss.
- 2
Identify the high-pressure context clearly.
- 3
Explain the criteria you used for prioritizing tasks.
- 4
Describe the outcome of your prioritization.
- 5
Highlight any skills or tools that helped you manage the situation.
Example Answers
In my previous role at the warehouse, we had a shipment due on a tight deadline while equipment malfunctioned. I prioritized tasks by assessing which shipments were most time-sensitive. I coordinated with team members to focus on packing those first, leading to successful on-time delivery.
Describe a time when you implemented a creative solution in your materials management role.
How to Answer
- 1
Think of a specific challenge you faced in materials management.
- 2
Describe the creative solution you came up with in detail.
- 3
Explain the impact of your solution on efficiency or cost savings.
- 4
Emphasize any collaboration with team members or departments.
- 5
Use the STAR method: Situation, Task, Action, Result.
Example Answers
In my previous role, we faced frequent stockouts of critical materials. I developed a color-coded inventory dashboard that identified low stock items in real-time. This allowed the team to reorder materials proactively, reducing stockouts by 30%.
Technical Interview Questions
What are the key components of an effective supply chain you must consider in materials management?
How to Answer
- 1
Identify the main components like sourcing, inventory, production, and logistics.
- 2
Discuss the importance of supplier relationships for quality and reliability.
- 3
Emphasize the role of inventory management in reducing costs.
- 4
Mention the significance of technology in tracking and optimizing processes.
- 5
Stress the impact of demand forecasting on supply chain efficiency.
Example Answers
An effective supply chain includes sourcing, where strong supplier relationships are essential for quality materials. Inventory management is crucial to minimize holding costs, while technology plays a key role in tracking supplies and optimizing logistics.
What ERP systems have you used in managing inventory, and how proficient are you with them?
How to Answer
- 1
List specific ERP systems you've used, such as SAP, Oracle, or Microsoft Dynamics.
- 2
Discuss your level of proficiency, using terms like beginner, intermediate, or advanced.
- 3
Provide examples of tasks or functions you performed using these systems.
- 4
Mention any relevant certifications or training related to the ERP systems.
- 5
Convey how your experience with these systems has benefited your previous roles.
Example Answers
I have experience with SAP and Oracle. I would rate my proficiency as advanced with SAP, where I managed inventory tracking and reporting, and intermediate with Oracle, focusing on procurement and order management.
Don't Just Read Materials Management Technician Questions - Practice Answering Them!
Reading helps, but actual practice is what gets you hired. Our AI feedback system helps you improve your Materials Management Technician interview answers in real-time.
Personalized feedback
Unlimited practice
Used by hundreds of successful candidates
How do you approach demand forecasting for materials? What tools or methods do you use?
How to Answer
- 1
Discuss your experience with historical data analysis.
- 2
Mention specific forecasting tools like Excel, SAP, or specialized software.
- 3
Explain how you collaborate with other departments to gather insights.
- 4
Talk about the importance of adjusting forecasts based on market trends.
- 5
Highlight any experiences with inventory management systems.
Example Answers
I start by analyzing historical data to identify trends in material usage. I often use Excel for this, applying statistical methods to create more accurate forecasts. I also collaborate with sales and production teams to gather insights on upcoming projects that may affect demand.
Explain how you would use data analysis to optimize inventory levels.
How to Answer
- 1
Identify key metrics for inventory management such as turnover rate and lead time.
- 2
Use historical sales data to predict future inventory needs.
- 3
Analyze supplier performance and reliability to adjust reorder points.
- 4
Implement inventory tracking tools that provide real-time data insights.
- 5
Regularly review and adjust inventory policies based on data findings.
Example Answers
I would start by analyzing historical sales data to forecast future demand, which helps in setting optimal stock levels. Additionally, I'd track key metrics like inventory turnover to identify slow-moving items and ensure we don't overstock. I would also adjust reorder points based on supplier lead times and reliability.
Can you walk me through the procurement process as you've experienced it in your previous roles?
How to Answer
- 1
Start by defining procurement and its importance in materials management.
- 2
Outline the steps you followed in the procurement process, such as identifying needs and suppliers.
- 3
Mention any relevant software or tools you used to facilitate procurement.
- 4
Share a specific example to illustrate your experience in procurement.
- 5
Highlight how you ensured compliance and quality in the procurement process.
Example Answers
In my previous role, procurement began with identifying the materials needed based on production forecasts. I would then research suppliers, request quotes, and compare prices. We used SAP software to track orders. For instance, when sourcing steel for a project, I found a new supplier that reduced costs by 15% while maintaining quality standards.
What safety standards should be considered when handling materials and inventory?
How to Answer
- 1
Understand OSHA regulations related to material handling.
- 2
Follow proper lifting techniques to prevent injuries.
- 3
Use personal protective equipment (PPE) appropriate for the materials.
- 4
Implement safe storage practices to prevent hazards.
- 5
Be aware of chemical safety guidelines if applicable.
Example Answers
When handling materials, I ensure compliance with OSHA standards, use PPE like gloves and safety glasses, and follow safe lifting practices to avoid injury.
How do you ensure the quality of materials when they are received in the warehouse?
How to Answer
- 1
Conduct a visual inspection of all received materials for damage or defects
- 2
Compare received materials against the purchase order for correct quantity and specifications
- 3
Perform quality checks or tests as necessary based on the material type
- 4
Document any discrepancies and communicate with suppliers promptly
- 5
Establish a systematic process for receiving that includes quality control checkpoints
Example Answers
I always start by visually inspecting the materials for any damage and checking them against the purchase order to ensure we received the right quantities and specifications.
What inventory management software are you familiar with, and how have you used it in past positions?
How to Answer
- 1
Identify specific inventory management software you've used.
- 2
Describe your role and responsibilities while using the software.
- 3
Mention specific tasks or features you utilized (e.g., tracking, reporting).
- 4
Share any improvements or efficiencies you achieved with the software.
- 5
Be honest about your familiarity and willingness to learn new systems.
Example Answers
I have extensive experience with SAP Inventory Management. In my last role, I used it to track inventory levels and automate reordering processes, which reduced stockouts by 20%.
Describe your understanding of logistics in relation to materials management.
How to Answer
- 1
Define logistics and its key components in materials management.
- 2
Explain how logistics impacts inventory control and supply chain efficiency.
- 3
Mention the importance of timing and accuracy in logistics for materials management.
- 4
Discuss the role of technology in optimizing logistics processes.
- 5
Highlight collaboration with suppliers and vendors in logistics.
Example Answers
Logistics refers to the processes that moving and storing materials effectively, which is critical in materials management. It ensures timely delivery and optimal inventory levels, directly impacting supply chain efficiency.
How can lean principles be applied in materials management to improve efficiency?
How to Answer
- 1
Identify waste in inventory processes and eliminate it.
- 2
Implement just-in-time inventory to reduce holding costs.
- 3
Standardize processes to ensure consistency in material flow.
- 4
Use visual management tools to track stock levels and order needs.
- 5
Encourage team involvement in problem-solving to optimize workflows.
Example Answers
Lean principles can be applied by using just-in-time inventory systems to reduce waste and holding costs. By only ordering materials as they are needed, we can streamline operations.
Don't Just Read Materials Management Technician Questions - Practice Answering Them!
Reading helps, but actual practice is what gets you hired. Our AI feedback system helps you improve your Materials Management Technician interview answers in real-time.
Personalized feedback
Unlimited practice
Used by hundreds of successful candidates
Situational Interview Questions
Suppose you suddenly receive an unexpected demand for a material that is in low stock. What steps would you take to handle the situation?
How to Answer
- 1
Quickly assess current inventory levels and confirm the stock on hand.
- 2
Communicate with suppliers to check availability and lead times for restocking.
- 3
Prioritize and consider alternatives or substitutes for the requested material.
- 4
Inform relevant stakeholders about the situation and any potential impact.
- 5
Implement a plan to manage the order while awaiting restock.
Example Answers
First, I would check our inventory system to confirm the exact quantity of the material available. Then, I would reach out to our suppliers to see if we can expedite an order for more stock. If that’s not feasible, I would explore any suitable substitutes we could use to fulfill the demand. Finally, I would update my team and management about the situation to keep everyone informed.
Imagine there is a disruption in your supply chain. How would you manage the situation to minimize impact?
How to Answer
- 1
Identify the source and impact of the disruption quickly.
- 2
Communicate with suppliers and logistics partners to assess alternatives.
- 3
Prioritize critical materials and adjust inventory levels if needed.
- 4
Implement short-term solutions while planning for long-term fixes.
- 5
Document the process to improve future response strategies.
Example Answers
I would first assess the disruption's impact by contacting suppliers to understand the issue. I'd prioritize obtaining critical materials and adjust our inventory strategy to buffer against the disruption. Meanwhile, I'd explore alternative suppliers or routes to minimize delays.
Don't Just Read Materials Management Technician Questions - Practice Answering Them!
Reading helps, but actual practice is what gets you hired. Our AI feedback system helps you improve your Materials Management Technician interview answers in real-time.
Personalized feedback
Unlimited practice
Used by hundreds of successful candidates
You are asked to find cost reduction solutions in the materials management process. How would you approach this task?
How to Answer
- 1
Analyze current inventory levels and turnover rates to identify excess stock.
- 2
Engage suppliers for bulk pricing or discounts to lower procurement costs.
- 3
Implement just-in-time inventory practices to reduce holding costs.
- 4
Evaluate and streamline the logistics and transportation processes for efficiency.
- 5
Monitor and review usage patterns to minimize waste and optimize order quantities.
Example Answers
I would start by analyzing our current inventory levels and turnover rates to pinpoint any excess stock that could be reduced. Then, I would discuss with suppliers to negotiate better bulk pricing, leading to lower costs.
How would you handle a situation where a vendor is unable to fulfill your order on time?
How to Answer
- 1
Stay calm and assess the situation professionally
- 2
Contact the vendor immediately to get an update on the issue
- 3
Discuss possible solutions or alternatives to meet deadlines
- 4
Communicate with your team about the situation and any adjustments needed
- 5
Document the incident for future reference or similar cases
Example Answers
I would quickly reach out to the vendor to understand the cause of the delay. Then, I would explore options like partial shipments or finding alternative vendors. Finally, I would keep my team informed so we can adjust our plans accordingly.
What would be your first steps when integrating a new inventory management software?
How to Answer
- 1
Assess current inventory processes and identify pain points.
- 2
Involve key stakeholders for their input and feedback.
- 3
Choose a pilot group and test the software with them.
- 4
Develop a training plan for all users before full rollout.
- 5
Monitor the integration closely and gather feedback for adjustments.
Example Answers
First, I would assess our current inventory processes to pinpoint any issues. Then, I'd engage key stakeholders to understand their needs. Next, I'd conduct a pilot test with a small team and gather their feedback. Following that, I'd create a comprehensive training plan for everyone. Finally, I'd ensure continuous monitoring throughout the integration.
You discover a discrepancy during an inventory count. How would you resolve this issue?
How to Answer
- 1
Verify the counts against the inventory records.
- 2
Check for possible human errors in the count.
- 3
Conduct a recount to confirm the discrepancy.
- 4
Investigate the potential causes for the discrepancy.
- 5
Document findings and report to the management.
Example Answers
I would first double-check the initial counts against the inventory records to ensure accuracy. If the discrepancy persists, I would recount the items to verify. If unresolved, I would investigate the causes, such as mislabeling or data entry errors, and then report my findings to management.
You receive an urgent request from production for materials that are unavailable. How do you prioritize and resolve this?
How to Answer
- 1
Assess the urgency and impact on production schedule
- 2
Check current inventory and potential alternatives
- 3
Communicate with production for clarification on needs
- 4
Collaborate with suppliers for expedited delivery options
- 5
Document the decision-making process for future reference
Example Answers
I assess the urgency of the request and its impact on production. Then, I check inventory for any alternatives. If nothing is available, I contact suppliers for expedited delivery and keep production informed throughout the process.
How would you approach training a new employee on your materials management process?
How to Answer
- 1
Start with an overview of the materials management process to provide context.
- 2
Identify key tools and systems used in the process and demonstrate their use.
- 3
Use hands-on training to allow the new employee to practice under supervision.
- 4
Set clear expectations and goals for the training period.
- 5
Encourage questions and provide ongoing support throughout the training.
Example Answers
I would begin by explaining the overall materials management process, highlighting how it fits into the larger organization. Then, I'd show them the inventory management system we use, allowing them to see how to input orders and check stock levels. I think hands-on practice is essential, so I would let them shadow me for a few days and gradually let them handle tasks themselves.
A shipment arrives with potentially hazardous materials not previously accounted for. What steps do you take to ensure safety and compliance?
How to Answer
- 1
Identify and assess the nature of the hazardous materials.
- 2
Communicate with your supervisor and the safety officer immediately.
- 3
Isolate the shipment from other materials and secure the area.
- 4
Follow the proper protocols for handling hazardous materials.
- 5
Document all actions taken for compliance and safety records.
Example Answers
First, I would assess the materials to determine their hazards and then inform my supervisor and the safety officer right away. I would ensure the area is isolated and secured, and follow established procedures for dealing with such materials. Finally, I'd document every step to maintain compliance.
You've identified a bottleneck in the materials handling process. How would you go about resolving it?
How to Answer
- 1
Analyze the current process to identify the root cause of the bottleneck
- 2
Gather data to understand the extent of the bottleneck's impact on operations
- 3
Brainstorm potential solutions or alternative approaches with the team
- 4
Implement a pilot solution to test its effectiveness before full rollout
- 5
Monitor the results and adjust the solution as necessary based on feedback
Example Answers
First, I would analyze the materials handling process to pinpoint the exact cause of the bottleneck. Then, I'd collect data on how it affects workflow and productivity. After understanding the issue, I would involve my team in brainstorming solutions, and we could test a new layout or process adjustment. Finally, I would monitor the changes to ensure they resolve the issue effectively.
Don't Just Read Materials Management Technician Questions - Practice Answering Them!
Reading helps, but actual practice is what gets you hired. Our AI feedback system helps you improve your Materials Management Technician interview answers in real-time.
Personalized feedback
Unlimited practice
Used by hundreds of successful candidates
Suppose a communication breakdown with a vendor occurs and impacts your supply chain. How would you address it?
How to Answer
- 1
Stay calm and assess the situation to understand the root cause of the breakdown.
- 2
Reach out to the vendor directly to clarify the issues and gather necessary information.
- 3
Document the communication for future reference and accountability.
- 4
Develop a contingency plan to mitigate the impact on your supply chain.
- 5
Communicate with your team about the situation and necessary adjustments.
Example Answers
I would first assess the situation to understand what caused the breakdown. Then, I'd contact the vendor to clarify the issues and get necessary updates. I would document our communication and develop a backup plan to ensure continued supply. Finally, I'd inform my team so we can manage any adjustments needed in our operations.
Materials Management Technician Position Details
Salary Information
Recommended Job Boards
These job boards are ranked by relevance for this position.
Related Positions
Ace Your Next Interview!
Practice with AI feedback & get hired faster
Personalized feedback
Used by hundreds of successful candidates
Ace Your Next Interview!
Practice with AI feedback & get hired faster
Personalized feedback
Used by hundreds of successful candidates