Top 30 Materials Specialist Interview Questions and Answers [Updated 2025]
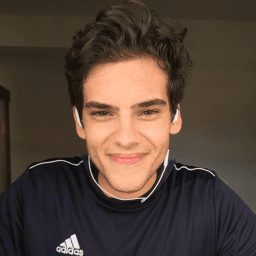
Andre Mendes
•
March 30, 2025
Navigating a Materials Specialist interview can be challenging without the right preparation. In this blog post, we delve into the most common interview questions for this pivotal role, offering example answers and insightful tips to help you respond with confidence and finesse. Whether you're a seasoned professional or new to the field, this guide is designed to equip you with the strategies needed to excel and make a lasting impression.
Download Materials Specialist Interview Questions in PDF
To make your preparation even more convenient, we've compiled all these top Materials Specialistinterview questions and answers into a handy PDF.
Click the button below to download the PDF and have easy access to these essential questions anytime, anywhere:
List of Materials Specialist Interview Questions
Technical Interview Questions
Explain the importance of compliance standards in materials selection.
How to Answer
- 1
Define compliance standards relevant to materials in your industry.
- 2
Discuss how compliance ensures safety and functionality.
- 3
Explain the role of standards in maintaining product quality and consistency.
- 4
Mention legal implications and potential penalties for non-compliance.
- 5
Highlight the importance of sustainability and ethical sourcing in compliance.
Example Answers
Compliance standards are crucial as they define the safety and performance benchmarks for materials. They ensure that the materials used meet specific safety and quality requirements, reducing the risk of product failures.
What analytical methods do you use to evaluate material performance?
How to Answer
- 1
Identify specific analytical methods you have experience with
- 2
Connect methods to real-world applications or projects
- 3
Emphasize both qualitative and quantitative evaluation techniques
- 4
Mention any software or tools you're proficient with
- 5
Discuss how these methods help inform material selection or improvement
Example Answers
I regularly use tensile testing and scanning electron microscopy to evaluate mechanical properties and failure modes in materials, which helps in selecting appropriate materials for engineering applications.
Don't Just Read Materials Specialist Questions - Practice Answering Them!
Reading helps, but actual practice is what gets you hired. Our AI feedback system helps you improve your Materials Specialist interview answers in real-time.
Personalized feedback
Unlimited practice
Used by hundreds of successful candidates
What criteria do you use to evaluate and select material suppliers?
How to Answer
- 1
Identify key factors such as quality, cost, and delivery time.
- 2
Consider the supplier's reputation and reliability in the industry.
- 3
Evaluate compliance with industry standards and certifications.
- 4
Assess the supplier's ability to scale and support your needs over time.
- 5
Look for strong communication and customer service from the supplier.
Example Answers
I evaluate suppliers based on their quality certifications, historical performance on delivery times, and ability to meet our budget. Reputation in the industry also plays a critical role.
What software tools are you familiar with for materials planning and inventory management?
How to Answer
- 1
Identify specific software tools you have used.
- 2
Mention your experience level with each tool.
- 3
Explain how you used these tools in previous roles.
- 4
Highlight any relevant certifications or training.
- 5
Be prepared to discuss improvements you made using these tools.
Example Answers
I am familiar with SAP for materials planning and have used it extensively to manage inventory levels and forecast demand in my last job, where I streamlined operations.
What types of material testing have you conducted, and what were the key parameters?
How to Answer
- 1
Identify specific tests you have performed, such as tensile, compression, or fatigue tests.
- 2
Mention the key parameters that are critical to each test, like strength, elongation, or hardness.
- 3
Use metrics and standards relevant to your industry to demonstrate knowledge.
- 4
Provide examples of how testing results influenced decision-making.
- 5
Be prepared to discuss any testing equipment or methodologies you are familiar with.
Example Answers
In my previous role, I conducted tensile testing on various polymers. Key parameters included tensile strength, yield point, and elongation at break, which helped us select the right material for product durability.
How do you perform a cost analysis for materials to ensure cost-effectiveness?
How to Answer
- 1
Identify all material costs including direct and indirect costs
- 2
Compare prices from multiple suppliers to find competitive rates
- 3
Evaluate the total cost of ownership, not just the purchase price
- 4
Consider the quality and performance of materials in relation to their costs
- 5
Use cost-benefit analysis to justify material choices for projects
Example Answers
To perform a cost analysis, I first list all costs associated with materials, including shipping and handling. Then, I gather quotes from several suppliers to ensure I'm getting the best price. I also assess the total cost of ownership by considering durability and maintenance, which helps justify the best option in terms of long-term value.
Can you explain how different material properties can affect product performance?
How to Answer
- 1
Identify key material properties like strength, flexibility, and thermal conductivity
- 2
Discuss how each property impacts specific product functions and applications
- 3
Use examples from past experiences or well-known products to illustrate points
- 4
Mention trade-offs between different material properties and their implications
- 5
Conclude with the importance of selecting the right material for intended performance
Example Answers
Material properties such as strength and flexibility greatly impact product performance. For instance, in the automotive industry, high strength materials improve safety by preventing structural failure, while flexibility is important in components that need to withstand vibrations.
What considerations do you take into account for sustainability in materials selection?
How to Answer
- 1
Think about the lifecycle of materials from extraction to disposal.
- 2
Consider the energy consumption in producing and transporting materials.
- 3
Evaluate the recyclability and biodegradability of materials.
- 4
Assess the availability of sustainable alternatives and local sourcing.
- 5
Incorporate any certifications or standards relevant to sustainability.
Example Answers
I focus on the lifecycle impact of materials, ensuring that they are energy-efficient to produce and transport. I also prioritize materials that are recyclable or biodegradable, like natural fibers or recycled plastics.
Explain your understanding of the material lifecycle and its impact on procurement.
How to Answer
- 1
Define the stages of the material lifecycle: sourcing, manufacturing, usage, and disposal.
- 2
Highlight the importance of considering the entire lifecycle in procurement decisions.
- 3
Discuss how lifecycle awareness can lead to cost savings and sustainability.
- 4
Mention the role of supplier collaboration throughout the lifecycle.
- 5
Provide examples of how lifecycle management can influence procurement strategies.
Example Answers
The material lifecycle includes sourcing, manufacturing, usage, and disposal. Understanding each phase helps us make informed procurement decisions that optimize costs and support sustainability. For example, sourcing materials from suppliers who prioritize sustainability can reduce waste and improve our overall impact.
What strategies do you use to ensure timely delivery of materials?
How to Answer
- 1
Establish strong relationships with suppliers and vendors
- 2
Utilize inventory management systems for real-time tracking
- 3
Implement a proactive communication plan for updates
- 4
Forecast demand accurately to prevent delays
- 5
Create contingency plans for potential disruptions
Example Answers
I maintain strong relationships with suppliers to ensure they understand our timelines and expectations, which helps in achieving timely deliveries.
Don't Just Read Materials Specialist Questions - Practice Answering Them!
Reading helps, but actual practice is what gets you hired. Our AI feedback system helps you improve your Materials Specialist interview answers in real-time.
Personalized feedback
Unlimited practice
Used by hundreds of successful candidates
Situational Interview Questions
What would you do if you had to stay within a strict budget while sourcing high-quality materials?
How to Answer
- 1
Research multiple suppliers to compare prices and quality.
- 2
Negotiate with suppliers for better rates or bulk discounts.
- 3
Prioritize the most critical materials and allocate funds accordingly.
- 4
Consider alternative materials that offer similar quality but at a lower cost.
- 5
Build strong relationships with suppliers for long-term benefits and better deals.
Example Answers
I would compare multiple suppliers to find the best quality at the lowest price, and I would negotiate bulk discounts to stay within budget.
How would you handle a request from management for urgent material usage reports?
How to Answer
- 1
Acknowledge the urgency and importance of the request
- 2
Prioritize gathering the most critical data first
- 3
Use existing templates or systems to streamline the report generation
- 4
Communicate a timeline for when the report will be ready
- 5
Follow up with management to confirm receipt and any additional needs
Example Answers
I would first acknowledge the request and its urgency, then I would quickly gather the most critical data, using existing templates to speed up the process. I would communicate that I can provide the report within 24 hours and confirm with management if there are any specific details they need.
Don't Just Read Materials Specialist Questions - Practice Answering Them!
Reading helps, but actual practice is what gets you hired. Our AI feedback system helps you improve your Materials Specialist interview answers in real-time.
Personalized feedback
Unlimited practice
Used by hundreds of successful candidates
If a key supplier informs you of a material shortage, how would you handle this situation?
How to Answer
- 1
Assess the impact of the shortage on your operations
- 2
Communicate with the supplier to understand the details and timeline
- 3
Explore alternative sources for the material if necessary
- 4
Inform internal stakeholders about the situation and potential delays
- 5
Develop a plan to mitigate the effects of the shortage
Example Answers
First, I would evaluate how the shortage affects our production timelines and identify which projects are at risk. Then, I would contact the supplier to gather more details on the duration of the shortage and potential resolutions. If needed, I would reach out to alternative suppliers to secure the materials to minimize disruption.
What steps would you take if a critical material failed quality assurance tests just before a product launch?
How to Answer
- 1
Immediately inform the project team and relevant stakeholders.
- 2
Analyze the failure to identify root causes and potential solutions.
- 3
Consult with suppliers for alternative materials or expedited replacements.
- 4
Assess the impact on the project timeline and communicate this to stakeholders.
- 5
Implement a contingency plan to minimize delay and risk.
Example Answers
I would first notify the project team and key stakeholders about the material failure. Then, I would investigate the root cause of the failure and explore options for alternative materials with our suppliers. I'd also evaluate how this impacts our launch timeline and discuss any necessary adjustments with the team.
How would you handle a situation where your engineering team disagrees with your material recommendations?
How to Answer
- 1
Listen actively to the team's concerns and rationale
- 2
Present data and research to support your recommendations
- 3
Encourage an open discussion to explore all viewpoints
- 4
Look for compromises or alternative materials if necessary
- 5
Ensure decisions align with project goals and performance criteria
Example Answers
I would first listen to my team's concerns and try to understand their perspective. After that, I would present my recommendations backed by data and research. I believe an open discussion helps everyone feel heard and could lead us to a better solution together.
Imagine you notice that your inventory levels are running low on a crucial material. How would you address this?
How to Answer
- 1
Assess the current inventory levels and determine how critical the shortage is.
- 2
Check with suppliers for availability and lead times of the material.
- 3
Communicate with stakeholders about the potential impact of the shortage.
- 4
Implement a short-term solution such as expediting an order or finding alternatives.
- 5
Review inventory management processes to prevent future shortages.
Example Answers
First, I would check the current inventory levels against our usage rates to assess the urgency. Then, I'd immediately contact our suppliers to inquire about stock availability and estimated delivery times. I'd inform relevant teams about the situation and potential impact. Next, I'd look into expediting the order or consider alternative materials if necessary. Finally, I'd review our inventory practices to identify how we can avoid such shortages in the future.
How would you respond if a material you sourced falls under new regulatory scrutiny?
How to Answer
- 1
Stay calm and assess the situation quickly
- 2
Review the specifics of the new regulations immediately
- 3
Communicate with relevant stakeholders about potential impacts
- 4
Evaluate options for compliance or alternatives
- 5
Document your response and decisions for future reference
Example Answers
I would first assess the new regulations to understand their implications. Then, I would inform my team and any relevant stakeholders about the issue. Together, we would explore compliance options and potential alternatives to ensure we meet regulatory standards.
If a team member is resistant to a new material specification, how would you address their concerns?
How to Answer
- 1
Listen actively to their concerns without interrupting.
- 2
Ask open-ended questions to understand their perspective.
- 3
Provide clear information about the benefits of the new specification.
- 4
Suggest a collaborative approach to address their concerns.
- 5
Follow up to ensure they feel supported and valued.
Example Answers
I would start by listening carefully to their concerns, making sure they feel heard. Then, I'd ask what specific aspects of the new specification they find challenging and explain how it aligns with our project goals.
Imagine you are tasked with reducing material costs without sacrificing quality. What would be your approach?
How to Answer
- 1
Analyze current material usage and identify areas of waste.
- 2
Negotiate with suppliers for better pricing or bulk deals.
- 3
Research alternative materials that could maintain quality but at lower costs.
- 4
Implement just-in-time inventory to reduce holding costs.
- 5
Collaborate with the R&D team to improve material efficiency in designs.
Example Answers
First, I would conduct a thorough analysis of our current material usage to spot any areas where we are wasting materials or over-ordering. Then, I'd reach out to our suppliers to negotiate better pricing, especially if we can commit to larger orders. Additionally, I would explore alternative materials that maintain our standards but are more cost-effective.
Behavioral Interview Questions
Describe a time when you worked as part of a team to resolve a materials issue.
How to Answer
- 1
Choose a specific situation with clear roles and outcomes
- 2
Use the STAR method: Situation, Task, Action, Result
- 3
Highlight collaboration and communication with team members
- 4
Focus on your contributions and learnings
- 5
Conclude with the positive impact on materials management
Example Answers
In my previous job, we faced a shortage of a critical material that delayed production. I coordinated with the procurement team to analyze the issue. We held a brainstorming session to identify alternative materials. I suggested a substitute that met quality standards, and we tested it successfully, which allowed us to resume production on time. This experience taught me the importance of quick thinking and teamwork in resolving materials challenges.
Don't Just Read Materials Specialist Questions - Practice Answering Them!
Reading helps, but actual practice is what gets you hired. Our AI feedback system helps you improve your Materials Specialist interview answers in real-time.
Personalized feedback
Unlimited practice
Used by hundreds of successful candidates
Describe a situation where you took the lead on a project involving material selection.
How to Answer
- 1
Choose a specific project with clear objectives.
- 2
Highlight your role in leading the team or decision-making.
- 3
Describe the criteria you used for material selection.
- 4
Mention any challenges faced and how you overcame them.
- 5
Include the positive outcomes from your leadership or decisions.
Example Answers
In my previous role, I led a team to select materials for a new product line. We aimed for durability and cost-effectiveness. I organized brainstorming sessions and collaborated with engineering to evaluate options based on strength and weight. We faced a challenge when initial choices exceeded budget, but I facilitated a re-evaluation and we found a suitable alternative that saved us 15% in costs while maintaining quality.
Give an example of how you adapted to a significant change in your materials sourcing process.
How to Answer
- 1
Identify a specific change in your sourcing process.
- 2
Explain the reason for the change.
- 3
Describe the steps you took to adapt.
- 4
Highlight any tools or methods you used to facilitate the adaptation.
- 5
Mention the positive outcomes from your adaptation.
Example Answers
In my previous role, we switched suppliers due to rising costs. I researched alternative suppliers and negotiated improved contracts, which led to a 10% cost reduction while maintaining quality.
Have you ever missed a critical detail in material specifications? What was the outcome?
How to Answer
- 1
Acknowledge a real error without being overly negative
- 2
Emphasize learning and corrective actions taken after the incident
- 3
Highlight how the experience improved your attention to detail or processes
- 4
Mention any proactive measures implemented to prevent future issues
- 5
Keep the focus on a constructive outcome rather than just the mistake
Example Answers
During a project, I overlooked a detail in the aluminum grade specified for a component. This resulted in a delay as we had to replace the materials after finding the mismatch. I took responsibility, revised our review processes, and now I double-check material specs with a checklist, ensuring higher accuracy in future projects.
Describe a time when you had to work under pressure to meet a materials deadline.
How to Answer
- 1
Identify a specific project or situation with a tight deadline.
- 2
Explain the actions you took to manage your time and resources.
- 3
Highlight any teamwork or communication that was crucial in meeting the deadline.
- 4
Discuss the outcome and any positive results from your efforts.
- 5
Reflect on what you learned from the experience and how it helped you grow.
Example Answers
In my previous role, we had a major product launch that was ahead of schedule, and we needed materials delivered one week earlier than planned. I coordinated with our suppliers, prioritized the most critical components, and held daily meetings with the team to ensure everyone was aligned. We successfully met the deadline and the launch went smoothly, exceeding sales expectations.
Tell me about a time when you introduced a new material or process that improved efficiency.
How to Answer
- 1
Choose a specific example with clear details.
- 2
Explain the problem you faced and your reasoning for the change.
- 3
Describe the new material or process you introduced.
- 4
Share measurable results or improvements after the change.
- 5
Conclude with what you learned from the experience.
Example Answers
At my last job, we faced delays due to traditional packaging materials. I researched biodegradable options and introduced a new material that reduced packaging time by 30%. The switch improved our workflow and received positive feedback from the team.
Provide an example of how you have used feedback to improve your materials process.
How to Answer
- 1
Choose a specific feedback instance that had a clear impact.
- 2
Describe the situation and the feedback received.
- 3
Explain the steps you took to implement changes based on the feedback.
- 4
Highlight the results or improvements that followed.
- 5
Make sure to focus on your role in the process.
Example Answers
In my last role, I received feedback that our material inventory tracking was causing delays. I initiated a weekly review process for inventory and updated our tracking software. This reduced the average material retrieval time by 30%.
Describe how you have communicated complex materials data to a non-technical audience.
How to Answer
- 1
Identify the key points or data you want to convey.
- 2
Use analogies or relatable examples to simplify concepts.
- 3
Focus on visual aids like charts or graphs to illustrate data.
- 4
Refrain from using technical jargon; keep the language simple.
- 5
Engage the audience with questions to ensure understanding.
Example Answers
In my previous role, I presented the properties of a new composite material to our marketing team. I highlighted key benefits using everyday analogies, comparing the material to lightweight yet strong bicycle frames. I used charts to show performance metrics, ensuring everyone grasped the advantages effectively.
Don't Just Read Materials Specialist Questions - Practice Answering Them!
Reading helps, but actual practice is what gets you hired. Our AI feedback system helps you improve your Materials Specialist interview answers in real-time.
Personalized feedback
Unlimited practice
Used by hundreds of successful candidates
Can you discuss a time when you learned something new that improved your work as a Materials Specialist?
How to Answer
- 1
Select a specific example where you actively sought out knowledge or training.
- 2
Explain how the new learning helped solve a problem or improved a process.
- 3
Quantify the results if possible, such as time saved or costs reduced.
- 4
Be honest about both the challenge and the outcome.
- 5
Keep it concise, focusing on your initiative and the benefits.
Example Answers
In my previous role, I took a course on advanced inventory management systems. This helped me optimize our stock levels, reducing excess inventory by 20% and saving the company significant carrying costs.
Materials Specialist Position Details
Salary Information
Recommended Job Boards
CareerBuilder
www.careerbuilder.com/jobs-materials-specialistZipRecruiter
www.ziprecruiter.com/Jobs/Materials-SpecialistThese job boards are ranked by relevance for this position.
Related Positions
Ace Your Next Interview!
Practice with AI feedback & get hired faster
Personalized feedback
Used by hundreds of successful candidates
Ace Your Next Interview!
Practice with AI feedback & get hired faster
Personalized feedback
Used by hundreds of successful candidates