Top 30 Medical Equipment Repairer Interview Questions and Answers [Updated 2025]
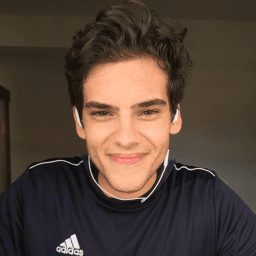
Andre Mendes
•
March 30, 2025
Navigating the intricate world of medical equipment repair requires not just technical expertise but also excellent problem-solving skills. In this blog post, we delve into the most common interview questions for the 'Medical Equipment Repairer' role, offering insightful example answers and practical tips to help you respond effectively. Prepare to enhance your interview readiness and confidently showcase your qualifications to potential employers.
Download Medical Equipment Repairer Interview Questions in PDF
To make your preparation even more convenient, we've compiled all these top Medical Equipment Repairerinterview questions and answers into a handy PDF.
Click the button below to download the PDF and have easy access to these essential questions anytime, anywhere:
List of Medical Equipment Repairer Interview Questions
Behavioral Interview Questions
Can you describe a time when you diagnosed a complex issue with a medical device? What steps did you take to resolve it?
How to Answer
- 1
Start with a specific situation involving a medical device.
- 2
Clearly outline the symptoms you observed or were reported.
- 3
Describe the diagnostic process you followed step by step.
- 4
Include the tools or techniques you used in the diagnosis.
- 5
Explain the resolution and any follow-up actions taken.
Example Answers
In my previous role, I encountered a ventilator that was not delivering the correct volume. I first reviewed the logs to check for error messages. Then, I inspected the tubing and connections for leaks. I used a flow meter to measure the output and confirmed it was significantly below expected levels. I replaced a faulty pressure sensor, which resolved the issue.
Describe an experience where you had to work closely with a healthcare team to repair a critical piece of medical equipment.
How to Answer
- 1
Identify a specific piece of equipment and its significance to patient care.
- 2
Explain your role and how you collaborated with the healthcare team.
- 3
Discuss any challenges faced during the repair process and how you resolved them.
- 4
Highlight any outcomes or improvements resulting from the repair.
- 5
Emphasize the importance of communication and teamwork in successful equipment maintenance.
Example Answers
In my previous role, I worked on a faulty MRI machine that was crucial for patient diagnostics. I collaborated with radiologists and nurses to understand the issues, and conducted thorough troubleshooting. We found a malfunctioning component that needed replacement, which I coordinated with the supplier to expedite. After the repair, we were able to resume scanning patients within hours, minimizing downtime.
Don't Just Read Medical Equipment Repairer Questions - Practice Answering Them!
Reading helps, but actual practice is what gets you hired. Our AI feedback system helps you improve your Medical Equipment Repairer interview answers in real-time.
Personalized feedback
Unlimited practice
Used by hundreds of successful candidates
Tell me about a time when you faced a tight deadline for repairing equipment. How did you manage the pressure?
How to Answer
- 1
Briefly describe the situation and the urgency of the repair.
- 2
Explain the steps you took to prioritize the tasks.
- 3
Mention any tools or methods used to manage your time effectively.
- 4
Describe how you maintained focus under pressure, including any teamwork involved.
- 5
Conclude with the outcome and what you learned from the experience.
Example Answers
In my previous role, we had a critical piece of medical imaging equipment fail just days before a scheduled patient screening. I quickly assessed the issue and prioritized the repair by gathering necessary tools and components. I focused on isolating the problem and consulted with a technician for additional support. We completed the repair in time for the screening, and I learned the importance of clear communication under pressure.
Describe a situation where you had to learn a new technology or equipment quickly. How did you handle it?
How to Answer
- 1
Identify a specific technology or equipment you learned.
- 2
Explain the context and why it was important to learn quickly.
- 3
Describe the steps you took to learn it, like online courses or hands-on practice.
- 4
Highlight any challenges you faced and how you overcame them.
- 5
Conclude with the results of your learning and its impact.
Example Answers
In my previous job, I had to quickly learn how to repair a new type of ultrasound machine. The hospital had just upgraded, and I was tasked with maintaining it. I enrolled in a quick online course and scheduled extra hours to practice with a technician. Despite initial difficulties in understanding the software, I used manuals and consulted with experienced colleagues. As a result, I became the go-to person for that machine within a few weeks.
Can you give an example of a time when you had to explain a technical issue to a non-technical member of staff?
How to Answer
- 1
Choose a specific incident from your past experience.
- 2
Describe the technical issue in simple terms.
- 3
Highlight your approach to communication, such as using analogies.
- 4
Mention the outcome and the impact of your explanation.
- 5
Keep it focused on how you helped the non-technical staff member understand.
Example Answers
In my previous role, I had to explain a software glitch in our medical imaging system to a nurse. I described it as if it were like a blurry picture on a camera, and once I explained how to reset the system, she was able to apply that every time it happened. This helped streamline our imaging process and maintain efficiency.
Have you ever led a project involving multiple repairs or installations? What was your approach?
How to Answer
- 1
Identify a specific project you led and explain its scope.
- 2
Outline the steps you took to organize the repair or installation.
- 3
Mention how you prioritized tasks and managed time effectively.
- 4
Discuss how you communicated with your team and stakeholders.
- 5
Highlight any challenges you faced and how you overcame them.
Example Answers
In my last role, I led a project to install new diagnostic machines in three clinics. I started by outlining the timeline and assigning tasks based on team strengths. We had weekly check-ins to monitor progress, and when issues arose with equipment delivery, I coordinated with suppliers for urgent solutions, ensuring we stayed on schedule.
Describe a conflict you had with a coworker regarding repair methods. How did you resolve it?
How to Answer
- 1
Identify the specific conflict and the differing viewpoints.
- 2
Explain your approach to communication and understanding the other person's perspective.
- 3
Describe the steps you took to resolve the conflict, focusing on collaboration.
- 4
Highlight any compromises made or final agreement reached.
- 5
Conclude with the outcome and what you learned from the experience.
Example Answers
In a previous role, a coworker and I disagreed on the best method to recalibrate a defibrillator. I listened to his approach and shared my concerns. We discussed both methods and agreed to conduct a side-by-side test to determine which was more effective. The test helped us find a better method that combined elements from both approaches, enhancing our repair process.
Give an example of a time when your attention to detail prevented a potential problem during a repair.
How to Answer
- 1
Choose a specific repair incident you handled.
- 2
Describe the details you noticed that led to preventing the problem.
- 3
Explain the potential problem that was avoided due to your actions.
- 4
Highlight the positive outcome of your attention to detail.
- 5
Keep it concise and focused on your role in the situation.
Example Answers
During a routine maintenance check on a defibrillator, I noticed that the battery connectors were slightly corroded. Instead of proceeding with the task, I replaced the connectors, preventing potential power failure during its next use.
Tell me about a time when you prepared for a difficult repair task. What precautions did you take?
How to Answer
- 1
Identify a specific challenging repair you faced in the past.
- 2
Explain how you researched or gathered information before the task.
- 3
Describe the tools or techniques you prepared to ensure success.
- 4
Mention any safety precautions you took during the repair.
- 5
Conclude with the outcome of the repair and what you learned.
Example Answers
In my previous job, I had to repair a complex MRI machine that had a malfunction. I first studied the technical manual thoroughly and watched online tutorials. I prepared my toolkit with specialized tools and kept safety gear handy. During the repair, I made sure to follow electrical safety protocols. The repair was successful, and the MRI machine was back in service within a few hours.
Technical Interview Questions
What are the key steps you take when performing routine maintenance on a life-supporting medical device?
How to Answer
- 1
Always review the manufacturer's maintenance schedule and guidelines before beginning.
- 2
Ensure the device is powered off and disconnected from any power source before inspection.
- 3
Perform a visual inspection for any obvious damage or wear on components.
- 4
Calibrate the device according to the manufacturer's specifications after maintenance checks.
- 5
Document all maintenance work performed, including any adjustments or repairs made.
Example Answers
I start by reviewing the manufacturer's guidelines for maintenance, and then I ensure the device is powered off and unplugged. Next, I inspect the device visually for any damage and follow up with calibration to ensure it meets specifications. Finally, I document all steps taken in the maintenance log.
What diagnostic tools do you typically use for troubleshooting issues with medical imaging equipment?
How to Answer
- 1
Identify common tools specific to medical imaging equipment like multimeters and oscilloscopes.
- 2
Mention any software used for diagnostics in imaging systems.
- 3
Discuss your experience with any brand-specific tools or manufacturer software.
- 4
Highlight the importance of safety in using diagnostic tools.
- 5
Demonstrate your approach to systematic troubleshooting with examples.
Example Answers
I commonly use multimeters and oscilloscopes for troubleshooting imaging equipment. I also utilize manufacturer-specific software to diagnose issues efficiently.
Don't Just Read Medical Equipment Repairer Questions - Practice Answering Them!
Reading helps, but actual practice is what gets you hired. Our AI feedback system helps you improve your Medical Equipment Repairer interview answers in real-time.
Personalized feedback
Unlimited practice
Used by hundreds of successful candidates
Explain how you would approach repairing a malfunctioning infusion pump.
How to Answer
- 1
Identify the specific malfunction symptoms
- 2
Review the service manual for troubleshooting procedures
- 3
Perform a visual inspection for obvious issues
- 4
Test electrical components and connections using a multimeter
- 5
Replace or repair faulty components as needed
Example Answers
I would start by identifying the symptoms of the malfunction, such as alarms or error messages. Then, I'd refer to the service manual for troubleshooting steps and perform a visual inspection for any obvious damage. After that, I would test the electrical components with a multimeter to find any faulty connections before replacing or repairing any defective parts.
What safety and regulatory standards are critical when working on medical devices?
How to Answer
- 1
Mention specific regulations such as ISO 13485 and FDA standards.
- 2
Emphasize the importance of following manufacturer guidelines for repairs.
- 3
Discuss the relevance of ensuring proper infection control and safety protocols.
- 4
Highlight the component of documentation for compliance and tracking.
- 5
Show awareness of the importance of training and certification in the field.
Example Answers
When working on medical devices, it's crucial to adhere to standards like ISO 13485 and FDA regulations. I always follow the manufacturer's repair guidelines to ensure safety and effectiveness. Additionally, infection control measures are vital during repairs, and I prioritize thorough documentation for compliance.
How do you handle software issues in medical devices, and what experience do you have with firmware updates?
How to Answer
- 1
Identify the types of software issues you have encountered.
- 2
Explain your troubleshooting process step-by-step.
- 3
Mention specific medical devices you've worked with and their software.
- 4
Highlight your experience with firmware updates and how you performed them.
- 5
Discuss any collaboration with software engineers or teams for unresolved issues.
Example Answers
In my previous role, I handled software issues by first identifying the problem, such as system crashes or slow performance. I used diagnostic tools and logs to pinpoint errors. For instance, I updated the firmware on infusion pumps, ensuring compliance with manufacturer guidelines to enhance performance.
Can you explain the principles of troubleshooting electrical faults in medical equipment?
How to Answer
- 1
Start with safety: ensure equipment is powered down and follow safety protocols
- 2
Use a systematic approach: follow a step-by-step method to identify the issue
- 3
Check power supply: verify the equipment is receiving power and fuses are intact
- 4
Utilize diagnostic tools: employ multimeters or oscilloscopes to test circuits
- 5
Refer to manuals: consult technical documentation for specific troubleshooting procedures
Example Answers
To troubleshoot electrical faults in medical equipment, I first prioritize safety by ensuring the device is powered down. I then use a systematic method, starting from the power supply to confirm it's functioning properly. If the power is on, I'll use a multimeter to test the circuits for continuity or shorts following the manual's guidelines.
What is your process for calibrating medical equipment, and why is it important?
How to Answer
- 1
Start by explaining your understanding of calibration in the medical field.
- 2
Describe the specific steps you take to calibrate equipment accurately.
- 3
Emphasize the importance of following manufacturer's guidelines and regulatory standards.
- 4
Discuss how calibration affects patient safety and equipment performance.
- 5
Mention any tools or technologies you use during the calibration process.
Example Answers
My process for calibrating medical equipment involves first reviewing the manufacturer's instructions, then using appropriate calibration tools like multimeters or oscilloscopes. I check the equipment against known standards to ensure accuracy. Calibration is critical to ensure patient safety and the reliability of the equipment's readings.
What experience do you have with repairing electromechanical systems found in medical devices?
How to Answer
- 1
Speak specifically about previous roles where you worked on medical devices.
- 2
Highlight your knowledge of electromechanical principles and troubleshooting methods.
- 3
Mention any relevant certifications or training in medical equipment repair.
- 4
Provide examples of installations or repairs you've completed successfully.
- 5
Discuss teamwork and communication with other medical staff during repairs.
Example Answers
In my previous role at XYZ Medical, I repaired infusion pumps and ventilators, specifically focusing on their electromechanical components. I have hands-on experience diagnosing faults and replacing faulty parts, ensuring minimal downtime for patient care.
What types of medical devices do you have the most experience repairing, and what makes them unique?
How to Answer
- 1
Identify specific medical devices you have worked on.
- 2
Describe your unique experience with each type.
- 3
Mention any certifications or training related to those devices.
- 4
Highlight challenges faced in repairs and how you resolved them.
- 5
Talk about the importance of these devices in patient care.
Example Answers
I have the most experience repairing MRI machines. They are unique due to their complex magnetic systems and require special calibration after repairs. I completed a certification course specifically for MRI maintenance, which helped me solve a critical issue with image clarity.
How do you approach diagnosing intermittent faults in complex medical equipment?
How to Answer
- 1
Start by gathering all relevant information from users about the issues they experience.
- 2
Use a systematic approach, testing components individually to isolate the fault.
- 3
Observe equipment during operation to detect conditions that may lead to faults.
- 4
Utilize diagnostic tools and software when available to streamline the process.
- 5
Document findings and steps taken for future reference and knowledge sharing.
Example Answers
I begin by talking to the users to understand the issue in detail, noting when it occurs. Next, I test different components under various scenarios to identify any faults. I also keep a close eye on the equipment during operation to see if I can replicate the issue, all while using diagnostic tools as necessary.
Don't Just Read Medical Equipment Repairer Questions - Practice Answering Them!
Reading helps, but actual practice is what gets you hired. Our AI feedback system helps you improve your Medical Equipment Repairer interview answers in real-time.
Personalized feedback
Unlimited practice
Used by hundreds of successful candidates
How do you utilize technical manuals or guides when repairing equipment, and can you give an example of a time they were crucial?
How to Answer
- 1
Explain the process of how you reference manuals during repairs.
- 2
Mention the importance of understanding wiring diagrams and troubleshooting sections.
- 3
Provide a specific example where a manual helped you solve a complex issue.
- 4
Highlight how manuals aid in ensuring compliance and safety standards.
- 5
Conclude with how you keep manuals updated for your future reference.
Example Answers
I always keep technical manuals at hand when repairing equipment. For instance, last month I worked on a defibrillator that wasn't charging. By referring to the troubleshooting section, I identified a faulty capacitor. This manual helped me follow the correct procedures and confirm the repair was safe before returning the equipment to service.
Situational Interview Questions
Imagine you are on-site during a medical emergency, and a critical device fails. What actions would you take?
How to Answer
- 1
Remain calm and assess the situation quickly.
- 2
Identify the critical device and confirm the failure.
- 3
Communicate with medical staff about the failure and potential risks.
- 4
Use your training to attempt a prompt repair if possible.
- 5
If unable to repair, direct staff to an alternative solution or device.
Example Answers
In a medical emergency, I would first remain calm and assess the situation. Then, I would quickly identify which device has failed and confirm the nature of the failure. I'd inform the medical staff immediately to ensure they are aware of the issue and its implications. If it's something I can fix quickly, I would attempt to do so; otherwise, I'd guide them to alternative equipment that can be used without delay.
If you discovered that a piece of essential equipment had a recurring problem, how would you proceed to investigate the root cause?
How to Answer
- 1
Start by reviewing the equipment's service history for past issues.
- 2
Examine recent maintenance logs to identify any patterns or changes.
- 3
Conduct tests to replicate the problem under controlled conditions.
- 4
Collaborate with colleagues to gather insights on the equipment's usage.
- 5
Document all findings and form a hypothesis about the root cause.
Example Answers
I would begin by checking the service history of the equipment to see if this issue has been documented before. Then, I would look at the maintenance logs for any recent repairs that might relate to the recurring problem.
Don't Just Read Medical Equipment Repairer Questions - Practice Answering Them!
Reading helps, but actual practice is what gets you hired. Our AI feedback system helps you improve your Medical Equipment Repairer interview answers in real-time.
Personalized feedback
Unlimited practice
Used by hundreds of successful candidates
You face a situation where a medical piece of equipment needs urgent repair, but it might take too long to fix. How do you handle this?
How to Answer
- 1
Assess the urgency and impact on patient care
- 2
Communicate with the medical staff about the issue
- 3
Identify potential temporary solutions or alternatives
- 4
Prioritize safety and compliance with regulations
- 5
Document the process and steps taken for transparency
Example Answers
First, I would evaluate the urgency of the repair compared to the needs of patient care. Then, I'd inform the medical staff about the issue and discuss any immediate alternatives we could use. If necessary, I'd work with the team to prioritize safety and ensure all regulations are followed as I complete the repair.
How would you prioritize multiple repair requests that come in at the same time, especially for critical equipment?
How to Answer
- 1
Assess the type and urgency of each repair request.
- 2
Identify equipment critical to patient care and prioritize those.
- 3
Communicate with healthcare staff to understand the impact of each equipment failure.
- 4
Organize repairs based on the severity and time sensitivity.
- 5
Keep a checklist to track ongoing repairs and ensure timely updates.
Example Answers
I would first assess all incoming requests and identify which equipment is crucial for patient care. For example, if a ventilator is down, I would prioritize that repair over other non-critical equipment. I’d communicate with the staff to understand the urgency and estimated downtime, ensuring that the most critical needs are addressed first.
If you were tasked with training new staff on the importance of proper equipment maintenance, what key points would you emphasize?
How to Answer
- 1
Highlight the role of equipment maintenance in patient safety and care quality.
- 2
Discuss the cost implications of neglecting maintenance, including repairs and replacements.
- 3
Explain how regular maintenance can extend the lifecycle of the equipment.
- 4
Incorporate real-life examples of equipment failure due to poor maintenance.
- 5
Emphasize the need for adherence to manufacturer guidelines and protocols.
Example Answers
I would emphasize how proper equipment maintenance is crucial for patient safety, as malfunctioning equipment can lead to severe consequences. I'd also cover the cost savings from extending equipment life through regular maintenance.
You have a healthcare provider who is frustrated with delays in equipment repair. How would you address their concerns?
How to Answer
- 1
Listen actively to the provider's concerns and acknowledge their frustration
- 2
Explain the reasons for the delays clearly and respectfully
- 3
Provide a realistic timeline for repairs and improvement
- 4
Offer to keep them updated on the status of their equipment
- 5
Suggest alternative solutions or loaner equipment if feasible
Example Answers
I would first listen to the provider's concerns and acknowledge their frustration. Then, I would explain the reasons for the delays, ensuring they understand we're working hard to address the issues. I would provide them with a realistic timeline and offer regular updates on the repair process.
How would you handle a situation in which a supervisor disagrees with your repair method on a medical device?
How to Answer
- 1
Acknowledge your supervisor's expertise and experience.
- 2
Listen actively to their concerns and reasoning.
- 3
Provide clear rationale for your repair method.
- 4
Be open to discussing alternative solutions together.
- 5
Aim for a collaborative approach to find common ground.
Example Answers
I would first listen carefully to my supervisor's concerns and understand their perspective. Then I would explain my repair method and the reasons behind it. Together, we could explore the best approach to ensure the medical device is repaired effectively.
Imagine you forgot to document an important repair step. How would you rectify that situation?
How to Answer
- 1
Acknowledge the mistake clearly and take responsibility for it.
- 2
Immediately review what steps were missed and gather any information you need.
- 3
Communicate with your team or supervisor about the oversight transparently.
- 4
Document the missed step as soon as possible to maintain accurate records.
- 5
Implement a system or checklist to prevent similar mistakes in the future.
Example Answers
I would first acknowledge my oversight and take full responsibility. Then, I would revisit the repair process to identify the missed step and document it right away. I would inform my supervisor and ensure that this rectification is noted in our records. Finally, I would create a checklist for future repairs to help avoid this kind of mistake.
If you identified a way to improve the repair process for a specific device, how would you present your idea to management?
How to Answer
- 1
Start with data on the current repair process and its limitations.
- 2
Clearly outline your proposed improvement with specific benefits.
- 3
Prepare to explain how this change can save time or reduce costs.
- 4
Consider potential objections and prepare responses.
- 5
Visual aids or a demonstration can help communicate your idea effectively.
Example Answers
I've analyzed our repair process for the XYZ device and noticed that we spend excessive time on calibrating settings. I propose a new calibration tool that could reduce this time by 30%. This improvement could enhance efficiency and lower our labor costs. I can show a prototype or a flow diagram to visualize this.
If a team member is not following proper equipment handling procedures, how do you address this with them?
How to Answer
- 1
Observe the team member's actions discreetly and gather facts.
- 2
Initiate a private conversation to avoid public embarrassment.
- 3
Express your concern clearly and focus on the importance of safety and procedure.
- 4
Listen to their perspective and understand any challenges they may have.
- 5
Offer assistance or additional training if needed to help them improve.
Example Answers
I would first discreetly observe the team member to ensure I have the correct understanding of the situation. Then, I would approach them privately to address my concerns about the handling procedures and emphasize how safety is crucial. I would listen to their side and see if they need more training on the equipment.
Don't Just Read Medical Equipment Repairer Questions - Practice Answering Them!
Reading helps, but actual practice is what gets you hired. Our AI feedback system helps you improve your Medical Equipment Repairer interview answers in real-time.
Personalized feedback
Unlimited practice
Used by hundreds of successful candidates
Medical Equipment Repairer Position Details
Salary Information
Recommended Job Boards
My Next Move
www.mynextmove.org/profile/summary/49-9062.00These job boards are ranked by relevance for this position.
Related Positions
Ace Your Next Interview!
Practice with AI feedback & get hired faster
Personalized feedback
Used by hundreds of successful candidates
Ace Your Next Interview!
Practice with AI feedback & get hired faster
Personalized feedback
Used by hundreds of successful candidates