Top 31 Packaging Technician Interview Questions and Answers [Updated 2025]
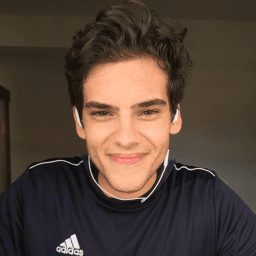
Andre Mendes
•
March 30, 2025
Navigating a Packaging Technician interview can be a daunting task, but we're here to help you succeed. This blog post is designed to equip you with the most common interview questions for this crucial role, alongside example answers and practical tips for crafting effective responses. Whether you're a seasoned professional or new to the field, our guide will prepare you to tackle interviews with confidence and poise.
Download Packaging Technician Interview Questions in PDF
To make your preparation even more convenient, we've compiled all these top Packaging Technicianinterview questions and answers into a handy PDF.
Click the button below to download the PDF and have easy access to these essential questions anytime, anywhere:
List of Packaging Technician Interview Questions
Behavioral Interview Questions
Can you describe a time when you successfully worked as part of a team to complete a packaging project?
How to Answer
- 1
Choose a specific project where teamwork was essential.
- 2
Describe your role and contribution to the team.
- 3
Highlight how communication and collaboration led to success.
- 4
Mention any challenges faced and how the team overcame them.
- 5
End with the positive outcome or impact of the project.
Example Answers
In my previous job, our team worked on launching a new product. I was responsible for ensuring the packaging met safety standards. We had daily meetings to discuss progress, and when there was an issue with the materials, we quickly brainstormed alternatives. My suggestions helped the team find a solution, and we completed the project on time with excellent feedback from management.
Tell me about a time you faced a significant challenge during a packaging process. How did you handle it?
How to Answer
- 1
Choose a specific challenge related to packaging.
- 2
Describe the situation clearly and concisely.
- 3
Explain the steps you took to resolve the issue.
- 4
Highlight any positive outcomes from your actions.
- 5
Mention any skills or knowledge that helped you.
Example Answers
In my previous job, we had a sudden shortage of packaging materials. I quickly assessed our inventory and contacted multiple suppliers. I prioritized orders and managed to keep production on track without delays. This experience taught me the importance of supplier relationships and proactive planning.
Don't Just Read Packaging Technician Questions - Practice Answering Them!
Reading helps, but actual practice is what gets you hired. Our AI feedback system helps you improve your Packaging Technician interview answers in real-time.
Personalized feedback
Unlimited practice
Used by hundreds of successful candidates
Describe an instance where your attention to detail made a difference in your packaging work.
How to Answer
- 1
Think of a specific project where details were crucial.
- 2
Explain what your role was and how you ensured accuracy.
- 3
Mention the outcome that resulted from your attention to detail.
- 4
Use numbers or specific results if possible.
- 5
Keep it concise and focus on your contribution.
Example Answers
In my previous role, I noticed a recurring issue with packaging labels not matching product specifications. I double-checked each label against the order sheet, which prevented a major shipping error and saved the company from potential returns. As a result, shipping accuracy improved by 15%.
Have you ever had to adapt to a sudden change in packaging specifications? How did you manage it?
How to Answer
- 1
Stay calm and assess the new specifications promptly
- 2
Communicate with your team about the changes
- 3
Implement the changes step by step to avoid confusion
- 4
Test the new packaging process for quality assurance
- 5
Reflect on the experience to learn and prepare for future changes
Example Answers
Yes, I faced a sudden change when the client requested a new eco-friendly material for packaging. I reviewed the specifications immediately, discussed the implications with my team, and we quickly developed a plan to adapt our machinery. We conducted tests to ensure everything met quality standards and managed to deliver on time.
Explain a situation where you had to communicate an issue to your supervisor. What was the outcome?
How to Answer
- 1
Choose a specific issue where communication was key.
- 2
Use the STAR method: Situation, Task, Action, Result.
- 3
Focus on clarity and the importance of communication.
- 4
Highlight the positive outcome or learning experience.
- 5
Keep it relevant to the packaging environment.
Example Answers
In a previous role, I noticed that our packing machine was malfunctioning. I immediately informed my supervisor about the issue. I explained the symptoms and its potential impact on production. As a result, we had a technician come in to fix it promptly, minimizing downtime.
Describe a moment when you took the lead in a packaging project. What steps did you take?
How to Answer
- 1
Think of a specific project where you were in charge.
- 2
Outline your role and responsibilities clearly.
- 3
Describe the steps you took to lead the team.
- 4
Highlight the outcome or success of the project.
- 5
Mention any challenges you faced and how you overcame them.
Example Answers
In my previous role, I led a project to redesign our packaging to reduce costs. I organized a team meeting to brainstorm ideas, assigned tasks based on strengths, and set a timeline. We collaborated closely and I monitored progress weekly. The new design reduced material costs by 20% and improved shelf appeal.
Can you give an example of receiving critical feedback about your packaging work? How did you respond?
How to Answer
- 1
Select a specific situation where you received feedback
- 2
Describe the feedback clearly and accurately
- 3
Explain your immediate emotional response, if applicable
- 4
Discuss the steps you took to improve based on the feedback
- 5
Highlight any positive outcomes from implementing the feedback
Example Answers
In my previous role, my supervisor pointed out that my packaging designs were too bulky, which increased shipping costs. I felt initially defensive but realized they were right. I reviewed the design process, sought advice from colleagues, and improved my designs for better efficiency. This resulted in a 15% reduction in shipping costs and positive feedback from management.
Can you describe a work ethic that you live by when handling packaging tasks?
How to Answer
- 1
Focus on quality and attention to detail in every task.
- 2
Emphasize the importance of teamwork and communication.
- 3
Highlight the value of safety and following protocols.
- 4
Mention time management and meeting deadlines.
- 5
Show a proactive attitude in problem-solving.
Example Answers
I believe in maintaining a strict focus on quality; ensuring every package is secure and meets standards is essential. I also prioritize clear communication with my team to make sure we are all aligned and working efficiently together.
Technical Interview Questions
What types of packaging materials are you most experienced with, and what factors do you consider when selecting them?
How to Answer
- 1
Identify specific packaging materials you have worked with like cardboard, plastic, or glass.
- 2
Discuss the specific features of each material that suit different products.
- 3
Mention factors like cost, durability, sustainability, and product protection.
- 4
Highlight any relevant experience in choosing or testing materials.
- 5
Be prepared to give examples of how your choices improved packaging efficiency or reduced waste.
Example Answers
I have experience with cardboard and plastic packaging. When choosing materials, I consider their cost-effectiveness, durability for shipping, and sustainability, as I aim to reduce waste. For instance, I switched to recycled cardboard which reduced costs by 15% and improved our environmental footprint.
What types of packaging machinery have you operated, and what maintenance practices do you follow?
How to Answer
- 1
List specific types of machinery you have experience with.
- 2
Briefly describe the tasks you performed on each machine.
- 3
Mention any certifications or training related to machinery operation.
- 4
Explain regular maintenance practices you follow, such as cleaning and inspections.
- 5
Highlight any troubleshooting skills and experiences with machinery repairs.
Example Answers
I have operated shrink wrap machines and labelers. I ensure regular cleaning and calibration of the shrink wrap machine weekly, and I check for any wear on parts during shifts.
Don't Just Read Packaging Technician Questions - Practice Answering Them!
Reading helps, but actual practice is what gets you hired. Our AI feedback system helps you improve your Packaging Technician interview answers in real-time.
Personalized feedback
Unlimited practice
Used by hundreds of successful candidates
How do you ensure quality control during the packaging process?
How to Answer
- 1
Review packaging specifications before starting work
- 2
Perform visual inspections of packaging materials
- 3
Conduct random checks of packed products for defects
- 4
Keep accurate records of quality control checks
- 5
Communicate any issues immediately to the supervisor
Example Answers
I ensure quality control by reviewing the packaging specifications at the start of each shift, then I perform visual inspections of materials to catch any defects early.
What industry standards do you follow when it comes to packaging safety and compliance?
How to Answer
- 1
Identify key industry standards related to packaging, such as ISO 22000 or FDA regulations
- 2
Discuss your experience with safety protocols and compliance checks
- 3
Mention any training or certifications you have related to packaging safety
- 4
Explain how you stay updated on changes in regulations and standards
- 5
Provide examples of how you have implemented these standards in past roles
Example Answers
I follow ISO 22000 standards for food safety packaging, and I ensure that all our packing processes comply with FDA regulations. In my previous job, I was responsible for conducting regular compliance checks and updating our procedures accordingly.
How do you troubleshoot issues with packaging machinery during production?
How to Answer
- 1
Assess the situation to understand the specific issue with the machinery.
- 2
Consult the machine's manual for troubleshooting tips related to common problems.
- 3
Check for any obvious mechanical issues like jams or misalignments.
- 4
Test the machine in manual mode to identify if the issue persists without automation.
- 5
Document the problem and the steps taken for future reference.
Example Answers
I usually start by assessing the machinery to identify any immediate issues, like jams. Then I refer to the manual for troubleshooting guidelines. If I can't find the issue, I run the machine in manual mode to see if the problem is with the automation.
What methods do you use to optimize the packaging process for efficiency?
How to Answer
- 1
Analyze current packaging workflows to identify bottlenecks.
- 2
Implement automation tools where feasible to speed up processes.
- 3
Regularly review material usage to reduce waste and cost.
- 4
Train team members on best practices for packing techniques.
- 5
Gather feedback from the team to continuously improve processes.
Example Answers
I analyze current workflows to spot any bottlenecks, then implement automation for tasks like sealing and labeling to increase speed.
Describe your experience with designing packaging solutions. What software or tools do you use?
How to Answer
- 1
Start with a specific project where you designed packaging.
- 2
Mention the materials you worked with and their properties.
- 3
Include software you used, like CAD or Adobe Creative Suite.
- 4
Discuss how you ensured the design met product requirements.
- 5
Highlight any feedback you received from stakeholders.
Example Answers
In my last role, I designed packaging for a new line of organic snacks. I used Adobe Illustrator to create the dielines and CAD software for structural design. The focus was on sustainable materials, and I ensured that the packaging was easy to open while protecting the product. Feedback from both the marketing team and customers was very positive.
Describe your experience working on an assembly line focused on packaging. What were your key responsibilities?
How to Answer
- 1
Start with the types of packaging materials you worked with.
- 2
Mention specific tasks you performed on the assembly line.
- 3
Highlight your attention to quality control.
- 4
Include any teamwork or collaboration experiences.
- 5
End with any improvements you suggested or implemented.
Example Answers
In my previous role, I operated machinery for packing consumer goods. My key responsibilities included sealing boxes, labeling products, and ensuring they were correctly packed for shipping. I worked closely with a team and always checked for quality issues before the final shipment.
What are some key properties of packaging materials that you always consider when designing a package?
How to Answer
- 1
Identify the material's durability and strength to protect contents.
- 2
Consider the weight of the material for shipping efficiency.
- 3
Evaluate the barrier properties for freshness and shelf-life.
- 4
Assess the material's cost and environmental impact.
- 5
Think about aesthetics and branding to attract customers.
Example Answers
When designing packages, I first look at the material's durability to ensure it protects the product during transport. Weight is also crucial, as lighter packaging can reduce shipping costs. Barrier properties are vital for items like food, ensuring they stay fresh longer. Additionally, I always consider the cost and seek sustainable options, as consumers are becoming more eco-conscious. Finally, I think about how the package represents the brand to attract these customers.
How do you measure and report on packaging efficiency metrics?
How to Answer
- 1
Identify key metrics such as packaging speed and waste percentage.
- 2
Explain how to gather data using production logs and automated systems.
- 3
Discuss the importance of analyzing data regularly to improve processes.
- 4
Mention how you report findings to stakeholders clearly and concisely.
- 5
Provide an example of how you used metrics to implement a change.
Example Answers
I measure packaging efficiency by tracking metrics like speed, accuracy, and waste. I collect data from production logs and real-time monitoring systems. Regular analysis helps identify trends, and I report my findings in concise presentations to management, highlighting areas for improvement.
Don't Just Read Packaging Technician Questions - Practice Answering Them!
Reading helps, but actual practice is what gets you hired. Our AI feedback system helps you improve your Packaging Technician interview answers in real-time.
Personalized feedback
Unlimited practice
Used by hundreds of successful candidates
What trends do you see in sustainable packaging, and how have you incorporated them into your work?
How to Answer
- 1
Research recent innovations in sustainable packaging materials like bioplastics and recycled fibers
- 2
Mention specific projects where you used sustainable practices
- 3
Express understanding of consumer demand for eco-friendly products
- 4
Highlight any collaboration with suppliers for sustainable sourcing
- 5
Discuss any metrics or outcomes from your sustainable packaging efforts
Example Answers
I see a trend towards using biodegradable materials, and in my last role, I implemented a switch to compostable packaging for our food products, which decreased our waste footprint by 30%.
Situational Interview Questions
Imagine you have multiple packaging orders due soon. How would you prioritize your tasks?
How to Answer
- 1
Identify deadlines for each order to understand urgency.
- 2
Evaluate the size and complexity of each packaging task.
- 3
Consider product priority or customer significance.
- 4
Coordinate with team members for any dependencies.
- 5
Communicate with your supervisor if unclear or need adjustments.
Example Answers
I would first check the deadlines for each order and prioritize those due soonest. Then, I would assess which tasks are larger or more complex, as they might take more time. If any orders involve key customers or high-priority products, I would ensure those are at the top of my list. Lastly, I would confirm with my team to coordinate any overlapping tasks.
You are informed of a change in packaging regulations. How would you approach integrating these changes into your work?
How to Answer
- 1
Stay updated on the latest packaging regulations
- 2
Assess how the changes impact current processes
- 3
Communicate with team members about the updates
- 4
Provide training if necessary for compliance
- 5
Document the changes and update procedures accordingly
Example Answers
I would first review the new packaging regulations thoroughly. Then, I would analyze how these changes affect our current packaging processes and notify my team. If needed, I would organize a training session to ensure everyone understands the new requirements and document all changes in our processes.
Don't Just Read Packaging Technician Questions - Practice Answering Them!
Reading helps, but actual practice is what gets you hired. Our AI feedback system helps you improve your Packaging Technician interview answers in real-time.
Personalized feedback
Unlimited practice
Used by hundreds of successful candidates
If you witnessed a conflict between team members over packaging processes, how would you address it?
How to Answer
- 1
Listen to both sides of the conflict to understand their perspectives.
- 2
Encourage open communication among team members to express their concerns.
- 3
Identify common goals, such as improving efficiency or quality in packaging.
- 4
Suggest a collaborative approach to find a compromise or solution.
- 5
Follow up to ensure the resolution is implemented effectively.
Example Answers
I would first listen to what both team members have to say to understand their viewpoints. Then, I'd facilitate a discussion to help them communicate directly, focusing on our shared goal of improving packaging efficiency.
What would you do if a key piece of machinery failed during a critical production run?
How to Answer
- 1
Assess the situation quickly to understand the extent of the failure.
- 2
Notify your supervisor and relevant team members immediately.
- 3
Check for troubleshooting guides or manuals available for the machinery.
- 4
Consider alternative solutions, like using backup equipment if available.
- 5
Document the incident and your response for future reference.
Example Answers
I would first assess the machine to identify the issue quickly and then inform my supervisor about the failure. While waiting for further instruction, I would consult the troubleshooting manual to see if I could resolve the issue myself. If the failure affects our timeline, I would explore if any backup machinery is available to maintain production.
A client requests a special packaging feature that is outside your current capabilities. How would you handle this?
How to Answer
- 1
Acknowledge the request positively and thank the client
- 2
Assess the specific requirements and understand the client's needs
- 3
Communicate current limitations honestly and clearly
- 4
Explore potential alternatives or solutions within existing capabilities
- 5
If necessary, propose a timeline for evaluating the request further
Example Answers
Thank you for your request. I understand the importance of this feature. I will review your needs, and while we currently lack this specific capability, I can suggest several alternatives that might meet your requirements.
You realize a safety protocol is not being followed during the packaging process. What steps would you take?
How to Answer
- 1
Identify the specific safety protocol that is being ignored.
- 2
Assess the potential risks or hazards resulting from this oversight.
- 3
Communicate the issue to your supervisor immediately.
- 4
Suggest immediate corrective actions to ensure safety.
- 5
Document the incident as per company policies.
Example Answers
I would first identify which safety protocol is not being followed and evaluate the risks involved. Then, I would inform my supervisor right away so they can take action. I would suggest stopping the process until we correct the protocol and ensure everyone is safe.
You have limited resources for a packaging project but tight deadlines. How would you approach this situation?
How to Answer
- 1
Assess the most critical requirements for the project
- 2
Prioritize tasks that provide the highest impact
- 3
Communicate clearly with the team about limitations
- 4
Seek input for creative solutions from team members
- 5
Focus on efficiency and streamline processes
Example Answers
I would first determine the non-negotiable requirements of the packaging project. Then, I would prioritize tasks that yield the best results within our limitations, ensuring to communicate these priorities with the team.
How would you conduct a final inspection of packaged goods before they are shipped?
How to Answer
- 1
Examine packaging for any visible damage or defects.
- 2
Verify that labels are correctly placed and legible.
- 3
Check for proper sealing and closure of packages.
- 4
Ensure that quantity and products match the shipping documents.
- 5
Conduct a random sampling of packages for quality assurance.
Example Answers
I would start by checking the exterior of each package for any physical damage, then ensure that all labels are correctly applied and easy to read. After that, I'd verify that each package is sealed properly and assess them against the shipping list to confirm the quantities are correct.
If you receive negative feedback from a customer about the packaging of your product, how would you respond?
How to Answer
- 1
Acknowledge the feedback sincerely and thank the customer for sharing their thoughts.
- 2
Gather specific details about the complaint to understand the issue better.
- 3
Stay calm and professional; avoid being defensive or dismissive.
- 4
Explain the steps you will take to address the feedback, including communication with your team.
- 5
Follow up with the customer if possible to inform them of improvements made.
Example Answers
I appreciate the feedback and will look into the specifics of the packaging issue. I'll discuss this with my team to find a solution and ensure it doesn't happen again.
How do you maintain performance when packing under tight deadlines?
How to Answer
- 1
Prioritize tasks based on urgency and importance
- 2
Stay organized with packing materials and tools readily accessible
- 3
Use efficient techniques, such as batching similar items together
- 4
Minimize distractions to stay focused on the task
- 5
Communicate effectively with team members to coordinate workflow
Example Answers
I prioritize my tasks by identifying which items need to be packed first based on deadlines. I keep my packing materials organized and within reach to save time. When possible, I batch similar items together to streamline the packing process.
Don't Just Read Packaging Technician Questions - Practice Answering Them!
Reading helps, but actual practice is what gets you hired. Our AI feedback system helps you improve your Packaging Technician interview answers in real-time.
Personalized feedback
Unlimited practice
Used by hundreds of successful candidates
If you notice a defect in a batch of packaged goods, what would be your immediate course of action?
How to Answer
- 1
Immediately stop the packaging line to prevent further defects.
- 2
Identify the nature of the defect and document it.
- 3
Inform your supervisor or quality control team about the issue.
- 4
Isolate the defective batch from the good products.
- 5
Conduct a root cause analysis to determine how the defect occurred.
Example Answers
I would stop the line to prevent any more defective items from being packaged. Then, I would document the defect and notify my supervisor. Next, I would isolate the defective batch and work with the team to find out how the defect happened.
Packaging Technician Position Details
Salary Information
Recommended Job Boards
ZipRecruiter
www.ziprecruiter.com/Jobs/Packaging-TechnicianThese job boards are ranked by relevance for this position.
Related Positions
- Manufacturing Technician
- Bag Machine Operator
- Manufacturing Assistant
- Factory Laborer
- Bindery Worker
- Flexographic Press Operator
- Shop Worker
- Pallet Assembler
- Factory Worker
- Carton Liner
Similar positions you might be interested in.
Ace Your Next Interview!
Practice with AI feedback & get hired faster
Personalized feedback
Used by hundreds of successful candidates
Ace Your Next Interview!
Practice with AI feedback & get hired faster
Personalized feedback
Used by hundreds of successful candidates