Top 33 Manufacturing Technician Interview Questions and Answers [Updated 2025]
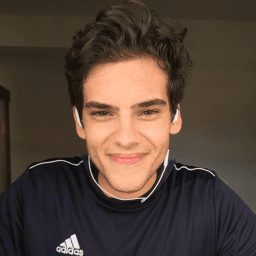
Andre Mendes
•
March 30, 2025
Navigating the interview process for a Manufacturing Technician role can be daunting, but preparation is key to success. In this blog post, we've compiled the most common interview questions you might face, complete with example answers and insightful tips to help you respond confidently. Whether you're a seasoned professional or just starting out, this guide will equip you with the strategies needed to impress potential employers.
Download Manufacturing Technician Interview Questions in PDF
To make your preparation even more convenient, we've compiled all these top Manufacturing Technicianinterview questions and answers into a handy PDF.
Click the button below to download the PDF and have easy access to these essential questions anytime, anywhere:
List of Manufacturing Technician Interview Questions
Technical Interview Questions
Explain the quality control processes you have used in past manufacturing roles.
How to Answer
- 1
Identify specific QC processes you have implemented or followed.
- 2
Mention any tools or software you used for quality control.
- 3
Provide examples of how you identified and resolved quality issues.
- 4
Highlight any relevant metrics or statistics that demonstrate success.
- 5
Connect your experience to the company's focus on quality.
Example Answers
In my previous role, I utilized statistical process control to monitor production quality. By analyzing data trends, I was able to identify defects early, resulting in a 15% reduction in scrap rate over six months.
How do you approach troubleshooting an equipment malfunction?
How to Answer
- 1
Identify the symptoms of the malfunction clearly
- 2
Check the equipment manual for troubleshooting guidelines
- 3
Inspect the equipment physically for obvious issues
- 4
Test components systematically to isolate the problem
- 5
Document your findings and steps taken for future reference
Example Answers
I begin by identifying the specific symptoms of the malfunction, then I refer to the equipment manual for troubleshooting tips. After that, I conduct a physical inspection to spot any obvious issues before systematically testing components to find the exact problem.
Don't Just Read Manufacturing Technician Questions - Practice Answering Them!
Reading helps, but actual practice is what gets you hired. Our AI feedback system helps you improve your Manufacturing Technician interview answers in real-time.
Personalized feedback
Unlimited practice
Used by hundreds of successful candidates
What types of machinery are you familiar with in a manufacturing setting?
How to Answer
- 1
List specific machines you have operated such as CNC machines, lathes, and milling machines.
- 2
Mention your experience level with each type of machinery.
- 3
Include any relevant certifications or training you have.
- 4
Relate your experience to the specific equipment used at the company if you know.
- 5
Be prepared to discuss any troubleshooting or maintenance tasks you have performed.
Example Answers
I have experience operating CNC machines, lathes, and assembly line equipment. I have worked extensively with CNC lathes and have a certification in CNC programming.
What tools do you use to measure and ensure product specifications?
How to Answer
- 1
Identify specific tools you have used, such as calipers or micrometers
- 2
Mention techniques for verifying measurements, like statistical process control
- 3
Highlight your experience with quality assurance software if applicable
- 4
Discuss the importance of calibration and tool maintenance
- 5
Emphasize teamwork in checking specifications with colleagues or supervisors
Example Answers
I regularly use digital calipers and micrometers to ensure precise measurements on parts. I also implement statistical process control to monitor production quality continuously.
What safety or quality standards are you well-versed in?
How to Answer
- 1
Identify key safety and quality standards relevant to manufacturing such as ISO 9001, OSHA regulations or Lean Six Sigma.
- 2
Mention any specific training or certifications you have received in these standards.
- 3
Share examples of how you've implemented these standards in your previous work experiences.
- 4
Highlight the impact of these standards on product quality and workplace safety.
- 5
Be confident and clear about your knowledge and experience with these standards.
Example Answers
I am well-versed in ISO 9001 and have completed a training course on quality management systems. In my previous job, I implemented these standards which led to a 15% reduction in defects over six months.
Describe a technical method you've used to optimize a manufacturing process.
How to Answer
- 1
Identify a specific method you used such as lean manufacturing, Six Sigma, or process automation.
- 2
Quantify the impact of your method with metrics like time saved, cost reduced, or quality improved.
- 3
Provide context about the manufacturing process you were optimizing and the challenges faced.
- 4
Briefly describe your role in implementing the method and any collaboration with the team.
- 5
Conclude with what you learned from the experience and how it can apply to future situations.
Example Answers
In a previous role, I implemented a Six Sigma methodology to reduce defects in our assembly line. By analyzing the data, I identified that a significant number of defects were arising from a specific step in the process. I worked with the team to streamline that step, which decreased defects by 25% and improved throughput by 15%. This experience taught me the value of data-driven decision making.
Do you have experience with CNC programming? Can you describe how you've applied it?
How to Answer
- 1
Be specific about your CNC programming experience
- 2
Mention any software you are proficient in
- 3
Describe a project where you successfully programmed a CNC machine
- 4
Highlight any challenges you faced and how you overcame them
- 5
Keep your answer concise and relevant to the job
Example Answers
I have over two years of experience in CNC programming using Mastercam. In my previous job, I programmed a CNC milling machine for a large batch of parts, reducing production time by 15%. I faced a challenge with tool changes, but I optimized the setup for efficiency.
What experience do you have with data analysis in manufacturing processes?
How to Answer
- 1
Identify specific tools or software you've used for data analysis
- 2
Mention particular metrics or KPIs you monitored
- 3
Discuss a project where your analysis led to actionable insights
- 4
Highlight any collaboration with engineering or quality teams
- 5
Emphasize improvements resulting from your data analysis
Example Answers
In my previous role, I used Excel to analyze production line efficiency metrics, which helped identify bottlenecks. This led to a 15% increase in throughput over three months.
Can you explain the principles of lean manufacturing and how you've applied them?
How to Answer
- 1
Define lean manufacturing and its key principles.
- 2
Provide specific examples from your past experience.
- 3
Focus on results achieved through lean practices.
- 4
Mention tools used, such as 5S, Kaizen, or value stream mapping.
- 5
Be concise and keep it relevant to the role.
Example Answers
Lean manufacturing focuses on minimizing waste while maximizing productivity. In my previous role, I implemented 5S by reorganizing the workspace, which reduced waste by 30% and improved efficiency.
What type of preventive maintenance have you been responsible for in previous roles?
How to Answer
- 1
Identify specific equipment or systems you maintained.
- 2
Explain the preventive maintenance tasks you performed regularly.
- 3
Mention any maintenance schedules you followed.
- 4
Highlight any improvements or results from your maintenance work.
- 5
Use technical terms relevant to the role clearly.
Example Answers
In my previous role, I was responsible for performing monthly maintenance on CNC machines, which included checking and replacing filters, lubricating moving parts, and ensuring that safety systems were functional. This proactive approach resulted in a 15% reduction in machine downtime.
Don't Just Read Manufacturing Technician Questions - Practice Answering Them!
Reading helps, but actual practice is what gets you hired. Our AI feedback system helps you improve your Manufacturing Technician interview answers in real-time.
Personalized feedback
Unlimited practice
Used by hundreds of successful candidates
Why is documentation important in manufacturing, and what forms have you used?
How to Answer
- 1
Emphasize accuracy and consistency in processes through proper documentation
- 2
Mention compliance with safety and regulatory standards
- 3
Highlight the role of documentation in training and onboarding new employees
- 4
Discuss how it aids in troubleshooting and quality control
- 5
Provide specific examples of documentation forms used, like SOPs or work instructions
Example Answers
Documentation is crucial in manufacturing because it ensures processes are followed accurately and consistently. I have used Standard Operating Procedures (SOPs) to guide operations and help train new staff effectively.
How do you ensure you are following the correct product specifications during manufacturing?
How to Answer
- 1
Familiarize yourself with the product specifications document.
- 2
Keep a checklist of key specifications for quick reference.
- 3
Double-check measurements and settings before starting production.
- 4
Communicate with team members about any uncertainties.
- 5
Document any deviations or errors and report them immediately.
Example Answers
I always start by reviewing the product specifications document thoroughly. I also create a checklist of key items to verify before production begins, ensuring I double-check each measurement and setting.
Behavioral Interview Questions
Can you describe a time when you identified a production issue and resolved it?
How to Answer
- 1
Think of a specific incident in your experience.
- 2
Explain how you identified the issue clearly.
- 3
Describe the steps you took to resolve it.
- 4
Mention any teamwork involved or tools you used.
- 5
Finish with the positive outcome of your actions.
Example Answers
In my previous role, we were facing delays due to a machine frequently breaking down. I noticed the problem was occurring after maintenance schedules. I proposed a new checklist for maintenance protocols and worked with the team to implement it. This reduced machine downtime by 30%, improving our production flow significantly.
Give an example of how you worked with a team to improve a manufacturing process.
How to Answer
- 1
Identify a specific project where team collaboration was key.
- 2
Explain your role and contribution clearly.
- 3
Highlight the problem you were solving together.
- 4
Show the positive outcome or results of the process improvement.
- 5
Mention any tools or methods used in collaboration.
Example Answers
In my previous job, our team noticed high waste in the assembly line. I suggested using a Lean approach. We mapped out the process, identified bottlenecks, and implemented changes that reduced waste by 20%. My role was to gather data and facilitate team meetings.
Don't Just Read Manufacturing Technician Questions - Practice Answering Them!
Reading helps, but actual practice is what gets you hired. Our AI feedback system helps you improve your Manufacturing Technician interview answers in real-time.
Personalized feedback
Unlimited practice
Used by hundreds of successful candidates
Tell me about a time you had to adapt to a major change in a manufacturing process.
How to Answer
- 1
Select a specific example where a process changed significantly.
- 2
Explain the nature of the change and why it was necessary.
- 3
Describe your immediate reactions and how you processed the information.
- 4
Highlight the steps you took to adapt and any challenges you faced.
- 5
Conclude with the positive outcomes of your adaptation.
Example Answers
At my last job, we switched from manual to automated assembly lines. The change was necessary to increase production speed. I quickly learned the new machinery, attended training sessions, and helped train others. Despite initial challenges in troubleshooting, we improved efficiency by 30% within a month.
Describe a situation where you had to explain a technical concept to a non-technical colleague.
How to Answer
- 1
Choose a relevant technical concept from your experience.
- 2
Explain the context and why the explanation was necessary.
- 3
Use simple language and relatable analogies.
- 4
Highlight the outcome of the explanation and any positive feedback.
- 5
Keep it concise and focused on the key points.
Example Answers
In my previous job, I needed to explain the process of quality control inspections to a new warehouse associate. I compared the process to checking a recipe when baking a cake, emphasizing the importance of each step. As a result, they understood their role better and were able to assist in maintaining quality standards.
Can you provide an example of how you contributed to a safe working environment?
How to Answer
- 1
Think of a specific situation where you took action to improve safety.
- 2
Focus on your role and what steps you took.
- 3
Mention any safety protocols or training you implemented.
- 4
Include the positive outcomes of your actions.
- 5
Use metrics or feedback if possible to illustrate success.
Example Answers
At my previous job, I noticed that several colleagues were not using proper PPE. I organized a brief training session on the importance of PPE, resulting in 100% compliance and a safer work area.
Describe a time when your attention to detail prevented a serious issue in production.
How to Answer
- 1
Think of a specific incident where your careful observation made a difference.
- 2
Highlight the problem you identified and its potential impact.
- 3
Explain the actions you took to address the problem.
- 4
Emphasize the results of your actions and how they benefited production.
- 5
Showcase your commitment to quality and safety in your answer.
Example Answers
In my previous role, I noticed that a batch of components had inconsistent measurements. I double-checked the specifications and found they were out of tolerance. I reported it to my supervisor and we halted the production line, preventing defective products from being shipped. This saved the company from potential recalls and increased customer satisfaction.
Give an example of a time when you took initiative to improve efficiency in your work area.
How to Answer
- 1
Choose a specific project or task where you saw a need for improvement.
- 2
Explain the initiative you took and the actions you implemented.
- 3
Include measurable results to demonstrate the impact of your initiative.
- 4
Use the STAR method: Situation, Task, Action, Result for structure.
- 5
Highlight collaboration with team members if applicable.
Example Answers
In my previous role, I noticed that our machine setup time was taking longer than necessary. I initiated a project to standardize the setup process by creating a checklist and training my colleagues. As a result, we reduced setup time by 20%, allowing us to increase our production output.
Tell me about a time you learned a new skill on the job. How did you go about it?
How to Answer
- 1
Identify a specific skill you learned that is relevant to manufacturing.
- 2
Explain the context and why learning that skill was important.
- 3
Describe the steps you took to learn the skill, including any resources you used.
- 4
Mention any challenges you faced and how you overcame them.
- 5
Share the outcome of applying that skill in your work.
Example Answers
In my previous role, I needed to learn how to operate a CNC machine for a new project. I first shadowed an experienced operator to understand the basics. Then, I took an online course to deepen my knowledge. Despite initially struggling with the controls, I practiced consistently and asked for feedback. Eventually, I became proficient and was able to manage my own projects.
Situational Interview Questions
What would you do if you encountered a safety incident while working on the production floor?
How to Answer
- 1
Stay calm and assess the situation quickly to determine the severity.
- 2
Ensure your own safety and the safety of others first.
- 3
Follow established safety protocols, like reporting the incident to a supervisor.
- 4
Provide help if you are trained to do so, such as administering first aid.
- 5
Document the incident clearly for future reference and review.
Example Answers
If I encountered a safety incident, I would first assess the situation to ensure everyone is safe. Then I would notify my supervisor immediately and follow any emergency procedures in place.
If you noticed that a batch of products did not meet quality standards, what steps would you take?
How to Answer
- 1
Immediately stop the production line to prevent further issues.
- 2
Document the findings with specific details about the quality failures.
- 3
Notify the supervisor or quality control team without delay.
- 4
Conduct an investigation to identify the root cause of the problem.
- 5
Implement corrective actions and monitor closely to ensure compliance.
Example Answers
I would halt production immediately to prevent any further defective products. Then, I would document the specific quality issues and notify my supervisor right away. Next, I would investigate what caused the problem, so we can address it, and finally, I would implement corrective measures to ensure it doesn’t happen again.
Don't Just Read Manufacturing Technician Questions - Practice Answering Them!
Reading helps, but actual practice is what gets you hired. Our AI feedback system helps you improve your Manufacturing Technician interview answers in real-time.
Personalized feedback
Unlimited practice
Used by hundreds of successful candidates
How would you manage your workload if you were given a tight deadline to meet production targets?
How to Answer
- 1
Prioritize tasks based on urgency and importance
- 2
Break down the workload into smaller, manageable steps
- 3
Communicate with the team to ensure alignment and support
- 4
Utilize any available tools or technology to improve efficiency
- 5
Monitor progress regularly and adjust plans as needed
Example Answers
I would prioritize tasks based on their deadlines and impact on production. Then, I would break down the workload into smaller steps and set mini-deadlines. I would check in with my team to share updates and ensure we're all on track.
What would your immediate actions be if a critical piece of equipment broke down during a busy shift?
How to Answer
- 1
Stay calm and assess the situation quickly.
- 2
Immediately inform your supervisor and the maintenance team.
- 3
Identify if there are safety risks and address them.
- 4
Communicate with the team to redistribute tasks.
- 5
Document the incident for future reference.
Example Answers
First, I would assess the situation to understand the extent of the breakdown. Then, I would notify my supervisor and the maintenance team right away. If there are any safety risks, I would ensure those are managed first before discussing with the team how we can redistribute tasks to maintain production.
How would you handle a situation where two team members disagree on the best way to proceed with a task?
How to Answer
- 1
Listen to both team members' viewpoints carefully.
- 2
Encourage open communication to understand the reasons behind their opinions.
- 3
Seek to find common ground or a compromise between their approaches.
- 4
If necessary, involve a supervisor for a final decision.
- 5
Maintain a positive team dynamic by ensuring everyone feels heard.
Example Answers
I would first listen to both team members to understand their perspectives. Then, I'd encourage them to discuss their ideas openly. I would aim to find a compromise that incorporates the best parts of both suggestions. If they cannot agree, I would involve a supervisor to help make the final decision.
If a new technology is introduced in your workplace, how would you go about learning to use it?
How to Answer
- 1
Research the technology to understand its purpose and functionality
- 2
Utilize manuals and resources provided by the company for training
- 3
Seek out training sessions or workshops to gain hands-on experience
- 4
Collaborate with colleagues who are familiar with the technology
- 5
Practice using the technology regularly to build confidence and proficiency
Example Answers
I would start by researching the new technology to understand its features. Then, I would read any manuals provided and attend training sessions to get hands-on experience. I’d also ask colleagues for tips and practice regularly to become proficient.
How would you respond to a customer complaint about a defective product that was produced?
How to Answer
- 1
Acknowledge the customer's concern promptly and professionally
- 2
Gather specific details about the complaint and the product
- 3
Apologize for the inconvenience caused to the customer
- 4
Explain the steps you will take to resolve the issue
- 5
Follow up with the customer to ensure satisfaction after the resolution
Example Answers
I would start by listening carefully to the customer's complaint and acknowledging their frustration. Then I would gather details about the defect and the specific product. I would apologize for the inconvenience and assure them I would investigate. Finally, I would explain our process for handling such issues and follow up afterward to ensure they are satisfied with the solution.
If you're asked to set personal development goals for the year, what would you focus on?
How to Answer
- 1
Identify skills relevant to the manufacturing technician role
- 2
Consider both technical and soft skills for balance
- 3
Set measurable objectives with timelines
- 4
Include opportunities for hands-on experience or training
- 5
Align goals with the company’s objectives or values
Example Answers
This year, I would focus on improving my understanding of automation systems and aim to complete a certification course in robotics, along with enhancing my communication skills through team workshops.
If you're tasked with improving production efficiency by 10%, where would you start?
How to Answer
- 1
Analyze the current production process to identify bottlenecks.
- 2
Engage with team members for input on inefficiencies.
- 3
Implement lean manufacturing principles to streamline workflows.
- 4
Explore automation opportunities for repetitive tasks.
- 5
Set clear, measurable goals and monitor progress regularly.
Example Answers
I would start by mapping the entire production process to identify any bottlenecks. Then, I would consult with my team to gather their insights on where they see inefficiencies, and focus on implementing lean principles to eliminate waste.
How would you handle a situation where a product recall was initiated due to safety concerns?
How to Answer
- 1
Acknowledge the seriousness of the situation
- 2
Emphasize the importance of safety and compliance
- 3
Discuss steps taken to communicate with relevant stakeholders
- 4
Mention the need for thorough investigation and analysis
- 5
Highlight the importance of taking proactive measures to prevent future recalls
Example Answers
If a product recall was initiated, I would immediately support the recall process by ensuring all safety protocols are followed. I would communicate with the team and management to coordinate our response and reassure stakeholders that safety is our top priority. Then, I would analyze the root cause to prevent future issues.
Don't Just Read Manufacturing Technician Questions - Practice Answering Them!
Reading helps, but actual practice is what gets you hired. Our AI feedback system helps you improve your Manufacturing Technician interview answers in real-time.
Personalized feedback
Unlimited practice
Used by hundreds of successful candidates
How would you prioritize your tasks if unexpected issues arose during your shift?
How to Answer
- 1
Assess the urgency and impact of the issue
- 2
Communicate with your team and supervisor immediately
- 3
Identify critical tasks that must be handled first
- 4
Stay organized by making a quick list of priorities
- 5
Remain flexible and ready to adapt as needed
Example Answers
If an unexpected machine breakdown occurs, I would first assess the situation to determine its impact on production. I would communicate with my supervisor and then prioritize getting the machine back online if it affects other tasks. Meanwhile, I would check other equipment to ensure the rest of production can continue smoothly.
How would you approach a project that requires coordination with multiple departments?
How to Answer
- 1
Identify key stakeholders in each department
- 2
Establish clear communication channels from the start
- 3
Set common goals and objectives for the project
- 4
Schedule regular check-ins to track progress
- 5
Be open to feedback and adapt as necessary
Example Answers
I would first identify the stakeholders involved in each department and establish clear communication channels. I would set common goals to ensure everyone is aligned, and schedule regular check-ins to monitor progress and gather feedback.
Manufacturing Technician Position Details
Salary Information
Recommended Job Boards
CareerBuilder
www.careerbuilder.com/jobs-manufacturing-technicianThese job boards are ranked by relevance for this position.
Related Positions
Ace Your Next Interview!
Practice with AI feedback & get hired faster
Personalized feedback
Used by hundreds of successful candidates
Ace Your Next Interview!
Practice with AI feedback & get hired faster
Personalized feedback
Used by hundreds of successful candidates