Top 28 Plastic Finisher Interview Questions and Answers [Updated 2025]
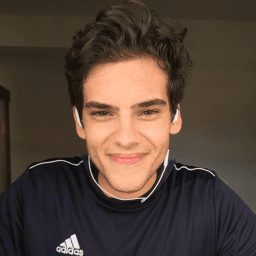
Andre Mendes
•
March 30, 2025
Preparing for a Plastic Finisher interview can be daunting, but we're here to help you shine. In this post, you'll find a curated list of the most common interview questions for the Plastic Finisher role, complete with example answers and insightful tips on how to respond effectively. Whether you're a seasoned professional or just starting out, this guide will boost your confidence and enhance your interview performance.
Download Plastic Finisher Interview Questions in PDF
To make your preparation even more convenient, we've compiled all these top Plastic Finisherinterview questions and answers into a handy PDF.
Click the button below to download the PDF and have easy access to these essential questions anytime, anywhere:
List of Plastic Finisher Interview Questions
Behavioral Interview Questions
Can you describe a time when you had to troubleshoot a defect in a plastic finishing process?
How to Answer
- 1
Start by briefly explaining the context of the defect you encountered.
- 2
Describe the specific symptoms of the defect and how you identified it.
- 3
Outline the steps you took to analyze and fix the issue.
- 4
Mention any relevant tools or techniques you used in your troubleshooting.
- 5
Conclude with the positive outcome of your efforts and what you learned.
Example Answers
In my previous role, we noticed inconsistent texture on finished parts. I investigated and found that a specific batch of material was causing the issue. I adjusted the temperature settings during the finishing process and switched to a different additive. After making these changes, the texture normalized, leading to improved product quality.
Tell me about a situation where you worked closely with a team to meet a tight deadline.
How to Answer
- 1
Focus on a specific project or task.
- 2
Describe your role and contributions clearly.
- 3
Emphasize collaboration and communication within the team.
- 4
Highlight how you overcame challenges to meet the deadline.
- 5
Conclude with the positive outcome or learning experience.
Example Answers
In my previous role at XYZ Corp, we had a project that involved finishing plastic components for a product launch. As the lead finisher, I coordinated with my team to streamline our workflow. We held daily check-ins to align on progress and tackle bottlenecks. Despite the tight deadline, we all communicated well and finished on time, resulting in a successful launch.
Don't Just Read Plastic Finisher Questions - Practice Answering Them!
Reading helps, but actual practice is what gets you hired. Our AI feedback system helps you improve your Plastic Finisher interview answers in real-time.
Personalized feedback
Unlimited practice
Used by hundreds of successful candidates
Describe an instance where you improved an existing finishing technique and the impact it had.
How to Answer
- 1
Identify a specific technique you improved.
- 2
Explain the original process and its limitations.
- 3
Describe the changes you implemented clearly.
- 4
Quantify the improvements if possible, such as time saved or quality enhanced.
- 5
Highlight the positive feedback from team members or customers.
Example Answers
In my previous role, I noticed the polishing process for our plastic parts caused uneven finishes. I researched and introduced a new polishing compound that provided a smoother finish. As a result, we reduced polishing time by 30% and received positive feedback from clients about the improved look of our products.
Give me an example of a time when your attention to detail significantly impacted the quality of a finished product.
How to Answer
- 1
Describe a specific situation or project
- 2
Explain what details you focused on
- 3
Discuss how your attention to detail made a difference
- 4
Share the outcome or results of your actions
- 5
Consider using the STAR method (Situation, Task, Action, Result)
Example Answers
In my previous role, we had a project where we were finishing custom parts for a client. I noticed some minor imperfections in the surface finish. I worked meticulously to sand and polish these areas, ensuring they met the client’s high standards. As a result, the client was very pleased and gave us repeat business.
Describe a time when you had to lead a project or initiative in your finishing work.
How to Answer
- 1
Think of a specific project you led in finishing work.
- 2
Outline your role and responsibilities in that project.
- 3
Explain the challenges you faced and how you overcame them.
- 4
Highlight the results or improvements achieved through your leadership.
- 5
Emphasize any teamwork and communication skills you demonstrated.
Example Answers
In my previous job, I led a team to improve the finishing process for a new line of plastic parts. I organized daily meetings to track progress and address any issues. We faced a challenge with surface quality, which I solved by implementing a new polishing technique. As a result, we reduced defects by 30%
Can you recall a time when you received constructive criticism and how you responded to it?
How to Answer
- 1
Choose a specific example where criticism helped you improve.
- 2
Briefly explain the situation and what the criticism was.
- 3
Describe how you reacted at first and what steps you took afterward.
- 4
Highlight the outcome and what you learned from the experience.
- 5
Keep the tone positive, showing growth and appreciation for feedback.
Example Answers
In my last role as a plastic finisher, my supervisor pointed out that my sanding technique was not consistent, which affected the final finish. At first, I felt defensive, but I took the feedback seriously. I spent extra time practicing my technique and asked for additional tips from colleagues. This resulted in a noticeable improvement in my work quality, and I became a go-to person for sanding tasks.
What motivates you to perform well in your role as a plastic finisher?
How to Answer
- 1
Identify specific aspects of your job that excite you.
- 2
Connect your motivation to quality and craftsmanship.
- 3
Mention the satisfaction from seeing a final product.
- 4
Discuss the importance of teamwork and collaboration.
- 5
Include personal goals for improvement and mastery.
Example Answers
I'm motivated by the satisfaction of seeing a polished piece come together. The quality of my work reflects my commitment to craft.
Tell me about a successful collaboration you had with another department related to plastic finishing.
How to Answer
- 1
Identify a specific project involving another department.
- 2
Highlight your role and contributions in the collaboration.
- 3
Emphasize the positive outcomes of the joint efforts.
- 4
Share any challenges faced and how they were overcome.
- 5
Mention the impact on plastic finishing quality or efficiency.
Example Answers
In a project to improve the surface finish of a new product, I collaborated with the design team to refine the specifications for texture. My input on finishing techniques led to a 20% improvement in the final product aesthetics.
Technical Interview Questions
What types of plastic finishing techniques are you familiar with and which do you prefer to use?
How to Answer
- 1
List specific techniques you have experience with, such as sanding, polishing, or coating.
- 2
Explain the purpose and benefits of each technique briefly.
- 3
Share a preference for a technique and justify why you prefer it.
- 4
Relate your experience to manufacturing or project examples.
- 5
Show enthusiasm for mastering different finishing techniques.
Example Answers
I am familiar with sanding, polishing, and applying spray finishes. I prefer polishing because it enhances the aesthetic quality and provides a smooth finish that customers appreciate. In my last project, using polishing made the product visually appealing, which led to positive feedback.
What experience do you have with the different machinery used in plastic finishing?
How to Answer
- 1
List specific machinery you have operated.
- 2
Mention any relevant training or certifications.
- 3
Discuss the context of your experience, such as projects or tasks.
- 4
Highlight any troubleshooting or maintenance you performed.
- 5
Connect your skills to how they can benefit the role.
Example Answers
I have extensive experience operating CNC machines, sanders, and buffing equipment for plastic finishing. In my previous role, I completed a certification program on CNC operations and handled a project that involved custom plastic parts, ensuring they met quality standards.
Don't Just Read Plastic Finisher Questions - Practice Answering Them!
Reading helps, but actual practice is what gets you hired. Our AI feedback system helps you improve your Plastic Finisher interview answers in real-time.
Personalized feedback
Unlimited practice
Used by hundreds of successful candidates
How do you determine which type of finish or coating to use for a specific type of plastic?
How to Answer
- 1
Identify the purpose of the finish or coating, such as protection or aesthetics.
- 2
Evaluate the properties of the plastic, like flexibility, heat resistance and chemical exposure.
- 3
Consider environmental factors, including UV exposure and moisture levels.
- 4
Research industry standards for finishes on specific plastic types.
- 5
Consult with suppliers for recommendations on compatible finishes.
Example Answers
I start by determining the finish's purpose; if it's for protection, I choose durable coatings. Then, I assess the plastic's properties to ensure compatibility.
What safety precautions do you take when working with finishing chemicals and machinery?
How to Answer
- 1
Always wear appropriate personal protective equipment including gloves, goggles, and masks.
- 2
Ensure proper ventilation in the workspace to avoid inhaling harmful fumes.
- 3
Follow Material Safety Data Sheets (MSDS) for all chemicals to understand their hazards.
- 4
Keep a well-stocked first aid kit accessible and be trained in its use.
- 5
Regularly inspect and maintain machinery to ensure safe operation.
Example Answers
I always wear gloves, goggles, and an appropriate mask when working with chemicals to protect my skin, eyes, and respiratory system. I also ensure the workspace is well-ventilated.
How do you perform quality checks on your finished plastic products?
How to Answer
- 1
Inspect each product visually for surface defects or inconsistencies.
- 2
Use measuring tools to verify dimensions against specifications.
- 3
Conduct stress tests on select samples to ensure durability.
- 4
Check for proper finishing techniques, like sanding or polishing.
- 5
Document any defects and track trends over time to improve processes.
Example Answers
I visually inspect each product for any surface flaws and use calipers to measure dimensions to ensure they match the specifications. I also conduct stress tests to confirm their durability.
What steps do you follow when a finishing process does not yield the expected results?
How to Answer
- 1
Analyze the finished product for defects or inconsistencies.
- 2
Review the process parameters used during finishing.
- 3
Identify potential sources of error, such as material or equipment issues.
- 4
Make necessary adjustments based on findings.
- 5
Re-test the process to ensure improvements.
Example Answers
When I notice unexpected results, I first inspect the product to identify specific defects. Then, I check the finishing process parameters, like temperature and pressure, to see if they were within specifications. If something seems off, I troubleshoot equipment for potential issues and adjust accordingly. After adjustments, I run tests again to ensure the quality is improved.
What are the most common defects you encounter in the finishing process, and how do you address them?
How to Answer
- 1
Identify specific defects such as scratches, uneven coating, or discoloration.
- 2
Describe the root causes of these defects based on your experience.
- 3
Explain methods you use to fix or prevent these defects.
- 4
Mention any tools or techniques that help in the finishing process.
- 5
Show a proactive attitude towards quality control and continuous improvement.
Example Answers
One common defect I encounter is scratches. I address this by ensuring proper handling of the materials during transport and using soft cloths during the finishing process. Additionally, I inspect surfaces before finishing to minimize scratches.
How do you select the appropriate sanding or polishing technique for different types of plastics?
How to Answer
- 1
Identify the type of plastic you are working with, such as acrylic, polycarbonate, or PVC.
- 2
Consider the surface finish required; high gloss may require finer grits.
- 3
Start with a coarser grit to remove defects, then progress to finer grits for a smooth finish.
- 4
Use appropriate tools for each technique, such as rotary tools for polishing or hand sanding for precision.
- 5
Always test your technique on a scrap piece first to ensure desired results.
Example Answers
I start by determining the plastic type, such as acrylic or polycarbonate. For a glossy finish, I use finer grits after starting with a coarser one to handle imperfections. I also test on a scrap piece to gauge the right technique.
What types of painting or coating materials have you worked with in your finishing processes?
How to Answer
- 1
List specific types of coatings you have experience with, such as powders or liquids.
- 2
Mention any techniques you've used like spray painting or dipping.
- 3
Include brands or products if relevant for credibility.
- 4
Discuss your familiarity with surface preparation and post-application processes.
- 5
Highlight any safety protocols you followed when handling materials.
Example Answers
I have worked with epoxy and polyurethane coatings primarily, using spray painting techniques. I am familiar with brands like DuPont and PPG. I also ensure proper surface preparation before application.
How do you manage waste and ensure environmental compliance in your finishing processes?
How to Answer
- 1
Explain your understanding of waste management practices.
- 2
Discuss specific methods you use to minimize waste.
- 3
Mention any compliance training or certifications you have.
- 4
Give examples of how you have improved processes for environmental compliance.
- 5
Highlight your commitment to sustainability in the workplace.
Example Answers
I follow strict waste management protocols, such as recycling materials whenever possible and properly disposing of hazardous waste according to regulations. I also ensure that my team is trained in these practices.
Don't Just Read Plastic Finisher Questions - Practice Answering Them!
Reading helps, but actual practice is what gets you hired. Our AI feedback system helps you improve your Plastic Finisher interview answers in real-time.
Personalized feedback
Unlimited practice
Used by hundreds of successful candidates
Situational Interview Questions
If a colleague disagrees with your approach to a finishing task, how would you handle the situation?
How to Answer
- 1
Listen to their concerns carefully and acknowledge their perspective.
- 2
Ask questions to understand their reasoning and specific issues with your approach.
- 3
Explain your rationale clearly, focusing on the benefits of your method.
- 4
Suggest a compromise or a trial of both methods to evaluate results.
- 5
Maintain a respectful tone throughout to foster collaboration.
Example Answers
I would first listen to my colleague's concerns and ask questions to fully understand their viewpoint. Then, I would share my reasons for my approach, highlighting how it leads to better quality or efficiency. If needed, I would propose trying both methods on a small scale to see which works best.
Imagine you discover a defect after the finishing process is complete; what steps would you take?
How to Answer
- 1
Identify the defect and document it clearly.
- 2
Assess the extent of the defect and determine its cause.
- 3
Communicate the issue to the relevant team members promptly.
- 4
Evaluate potential solutions or corrective measures.
- 5
Implement the chosen solution and monitor the outcome.
Example Answers
Upon discovering a defect, I would first document the defect thoroughly. Then, I would analyze the process to determine how it occurred. After that, I would inform my supervisor and the team about the issue to gather input on corrective actions. Finally, I'd implement the solution and keep track of the results to ensure it doesn't reoccur.
Don't Just Read Plastic Finisher Questions - Practice Answering Them!
Reading helps, but actual practice is what gets you hired. Our AI feedback system helps you improve your Plastic Finisher interview answers in real-time.
Personalized feedback
Unlimited practice
Used by hundreds of successful candidates
If you are falling behind on a project due to equipment failure, how would you prioritize your tasks?
How to Answer
- 1
Assess the impact of the equipment failure on project timelines
- 2
Identify critical tasks that can be completed without the equipment
- 3
Communicate with the team and stakeholders about the situation
- 4
Plan for equipment repair or alternative solutions quickly
- 5
Adjust your project timeline based on the current situation
Example Answers
I would first evaluate how the equipment failure affects our deadlines. Then, I would focus on tasks that don't require the faulty equipment, like preparing materials or coordinating with team members. I would also inform my supervisor and team about delays and explore options to repair the equipment or use alternative tools efficiently.
How would you approach a situation where you need to implement a new finishing technology that you're unfamiliar with?
How to Answer
- 1
Research the new technology thoroughly to understand its principles and benefits
- 2
Seek out training resources or workshops for hands-on experience
- 3
Consult with colleagues or experts who have used the technology before
- 4
Start with small-scale tests to evaluate the technology in your environment
- 5
Document the process and results to refine your approach and improve future implementations
Example Answers
I would begin by researching the new finishing technology to understand its features and advantages. Then, I would look for training or workshops to gain hands-on experience. Consulting with colleagues who have used it would also be essential for insights. After that, I'd implement it on a small scale to see how it fits into our processes and document everything for future reference.
How would you respond if a client is dissatisfied with the finish on their product?
How to Answer
- 1
Acknowledge the client's concerns immediately.
- 2
Ask for specific details about their dissatisfaction.
- 3
Offer a solution or corrective action.
- 4
Express commitment to quality and client satisfaction.
- 5
Follow up to ensure the resolution meets their expectations.
Example Answers
I would start by acknowledging the client's concerns and thank them for bringing it to my attention. I would ask them to specify what they are dissatisfied with and then offer to redo the finish to their specifications, ensuring we meet their expectations.
What would you do if you experienced a safety incident while operating finishing equipment?
How to Answer
- 1
Immediately stop the equipment and ensure the area is safe.
- 2
Assess the situation and determine if anyone is injured and needs assistance.
- 3
Report the incident to a supervisor or safety officer as per protocol.
- 4
Document the incident as required, noting details and any observed hazards.
- 5
Participate in any follow-up investigations to improve safety procedures.
Example Answers
If I experienced a safety incident, I would stop the machine immediately and ensure everyone is safe. I would check if anyone is injured, then report to my supervisor right away. After that, I would document the incident and help with any safety review.
If you notice a recurring issue in the quality of the finish, what steps would you take to analyze and resolve it?
How to Answer
- 1
Observe the finish closely for patterns in defects.
- 2
Review the production process and identify any variables that could affect quality.
- 3
Consult with team members for their insights or experiences related to the issue.
- 4
Test different approaches or adjustments to the finish process to see if improvements occur.
- 5
Document the findings and implement standard procedures if a solution is found.
Example Answers
I would first examine the finish to identify any consistent defects, then I’d look into the production steps to pinpoint if anything has changed. After gathering data, I would discuss the issue with my coworkers for additional perspectives and finally, I would test adjustments to see what improves the quality.
How would you handle a situation where you need to train a new employee on finishing techniques?
How to Answer
- 1
Start with a clear explanation of the finishing techniques.
- 2
Demonstrate the techniques hands-on for better understanding.
- 3
Encourage questions during and after the demonstration.
- 4
Provide written materials or resources for reference.
- 5
Set up practice sessions to allow the new employee to gain confidence.
Example Answers
I would begin by explaining the key finishing techniques in detail. Then, I'd demonstrate each technique, ensuring they understand the process. I'd encourage questions and provide a manual for reference. Finally, I'd schedule practice sessions to help them apply what they've learned.
What would you do if a significant order needed a different finish than what your process is set up for?
How to Answer
- 1
Assess the requirements of the new finish.
- 2
Communicate with the team about the change needed.
- 3
Evaluate possible adjustments to the existing process or equipment.
- 4
Consider alternative finishing methods that could meet the order's needs.
- 5
Be proactive in proposing solutions or timelines to the customer.
Example Answers
First, I would carefully review the specifications for the desired finish. Then, I would discuss with my team whether we can adjust our current process or if we need to explore alternative finishing techniques. It's important to keep the customer informed and provide them with an estimated timeline for the change.
Plastic Finisher Position Details
Related Positions
- Plastic Worker
- Plastic Machine Operator
- Tool Dresser
- Wire Bender
- Stapler
- Nail Maker
- Metal Worker
- Electrolytic Etcher
- Sheeter Operator
- Cable Swager
Similar positions you might be interested in.
Ace Your Next Interview!
Practice with AI feedback & get hired faster
Personalized feedback
Used by hundreds of successful candidates
Ace Your Next Interview!
Practice with AI feedback & get hired faster
Personalized feedback
Used by hundreds of successful candidates