Top 30 Sheeter Operator Interview Questions and Answers [Updated 2025]
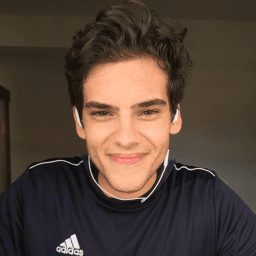
Andre Mendes
•
March 30, 2025
Preparing for a Sheeter Operator interview can be daunting, but this comprehensive guide is here to help you succeed. Dive into the most common questions asked in Sheeter Operator interviews and discover insightful example answers and expert tips on how to respond effectively. Whether you're a seasoned operator or a newcomer, this post will equip you with the knowledge and confidence to excel in your next interview.
Download Sheeter Operator Interview Questions in PDF
To make your preparation even more convenient, we've compiled all these top Sheeter Operatorinterview questions and answers into a handy PDF.
Click the button below to download the PDF and have easy access to these essential questions anytime, anywhere:
List of Sheeter Operator Interview Questions
Behavioral Interview Questions
Can you describe a time when you worked as part of a team to achieve a production goal? What was your role?
How to Answer
- 1
Identify a specific project you worked on with a team.
- 2
Clearly state your role and responsibilities within the team.
- 3
Describe the goal you aimed to achieve and any challenges faced.
- 4
Highlight how teamwork contributed to overcoming these challenges.
- 5
Conclude with the positive outcome and what you learned from the experience.
Example Answers
In my previous job at a manufacturing plant, our team was tasked with increasing production output by 20%. I was the lead operator, coordinating with my team to streamline our process. We identified bottlenecks in the workflow, implemented a new scheduling system, and by working together, we not only met but exceeded the goal by achieving a 25% increase in output. This taught me the importance of communication and collaboration.
Tell me about a situation where you encountered a problem with the sheeting machine. How did you resolve it?
How to Answer
- 1
Describe the specific problem clearly and concisely.
- 2
Explain the steps you took to diagnose the issue.
- 3
Highlight any tools or techniques you used to fix it.
- 4
Mention the outcome and what you learned from the experience.
- 5
Keep it focused on your role and contributions.
Example Answers
Once, the sheeting machine jammed during a run. I quickly stopped the machine and assessed the feed area, discovering a misaligned roll. I realigned the roll and adjusted the tension settings. After restarting, the machine ran smoothly, and production was back on track without delays. I learned the importance of regular checks on machine alignment.
Good Candidates Answer Questions. Great Ones Win Offers.
Reading sample answers isn't enough. Top candidates practice speaking with confidence and clarity. Get real feedback, improve faster, and walk into your next interview ready to stand out.
Master your interview answers under pressure
Boost your confidence with real-time practice
Speak clearly and impress hiring managers
Get hired faster with focused preparation
Used by hundreds of successful candidates
Describe a time when you identified a safety hazard in the workplace. What actions did you take?
How to Answer
- 1
Think of a specific incident where you noticed a safety risk.
- 2
Explain how you assessed the situation before taking action.
- 3
Describe the steps you took to mitigate the hazard.
- 4
Mention any communication with coworkers or supervisors regarding the hazard.
- 5
Highlight any positive outcomes from your actions.
Example Answers
While working as a technician, I noticed that a machine's safety guard was missing. I immediately reported it to my supervisor and stopped anyone from using the machine. We quickly put a replacement guard on, and I suggested regular safety checks to prevent future issues.
How have you managed your time in a fast-paced production environment? Provide an example.
How to Answer
- 1
Prioritize tasks by urgency and importance.
- 2
Use a checklist to keep track of daily goals.
- 3
Communicate with team members for clarity on responsibilities.
- 4
Regularly review progress to adjust plans as needed.
- 5
Stay organized to minimize downtime and distractions.
Example Answers
In my previous role, I prioritized tasks by understanding production schedules. For example, I created a checklist each morning, which helped me stay focused on critical tasks like machine setup and maintenance, reducing our downtime by 15%.
Can you give an example of how you ensured quality standards were met during your previous work?
How to Answer
- 1
Choose a specific example from your experience.
- 2
Describe the quality standards relevant to the situation.
- 3
Explain the actions you took to meet those standards.
- 4
Mention any tools or processes you used.
- 5
Conclude with the positive outcome or feedback received.
Example Answers
At my previous job, we had strict quality standards for our product dimensions. I conducted regular measurements using calipers throughout the shift and adjusted the machine settings as needed. This helped maintain our quality rates above 98%, and I received recognition from my supervisor for my efforts.
Describe a time when you had to adapt to changes in production processes. How did you handle it?
How to Answer
- 1
Identify a specific change in the production process you faced.
- 2
Explain your initial reaction and thoughts upon learning the change.
- 3
Describe the steps you took to adjust to the new process.
- 4
Highlight any teamwork or communication involved.
- 5
Conclude with the positive outcome or what you learned.
Example Answers
In my previous role, we switched to a new sheet material that required different handling. Initially, I felt uncertain, but I took the initiative to read the guidelines and asked questions. I worked closely with the training team to understand the new process better. As a result, our production efficiency improved, and I gained a deeper understanding of material properties.
Have you ever had to lead a team in the absence of a supervisor? How did you ensure tasks were completed successfully?
How to Answer
- 1
Identify a specific instance where you stepped up to lead.
- 2
Explain your approach to delegating tasks among team members.
- 3
Discuss how you maintained communication with the team.
- 4
Highlight any challenges faced and how you overcame them.
- 5
Mention the positive outcomes of your leadership during that time.
Example Answers
Once, during a shift when my supervisor was unavailable, I took the initiative to organize the workflow. I assigned tasks based on each member's strengths, maintained regular check-ins to monitor progress, and addressed any issues immediately. We completed our targets ahead of schedule, which impressed management.
Describe how you prioritize your tasks during a busy shift as a Sheeter Operator.
How to Answer
- 1
Identify urgent tasks first, like machine setups and adjustments
- 2
Assess production goals to align your priorities with team objectives
- 3
Communicate with teammates to coordinate responsibilities and avoid overlap
- 4
Keep a checklist of tasks to track progress and stay organized
- 5
Stay flexible and adjust priorities as new challenges arise
Example Answers
During a busy shift, I first focus on urgent tasks like machine setups to ensure we hit our production goals. I communicate with my team to delegate effectively and avoid overlap in our tasks, and I keep a checklist to monitor my progress throughout the shift.
Describe a situation where effective communication with your team made a significant difference in achieving a goal.
How to Answer
- 1
Think of a specific project or task where communication was key.
- 2
Use the STAR method: Situation, Task, Action, Result.
- 3
Focus on how you communicated and why it was effective.
- 4
Highlight the impact on the team's performance or outcome.
- 5
Keep it concise and relevant to the role of a Sheeter Operator.
Example Answers
In my previous job, we had a tight deadline for a large production run. During our weekly meeting, I clearly outlined each person's role and what was needed to meet our goal. By maintaining open lines of communication via daily check-ins, we identified issues early. As a result, we completed the project two days ahead of schedule, exceeding our client's expectations.
Can you provide an example of a time when you took initiative on the job?
How to Answer
- 1
Think of a specific situation where your actions led to a positive outcome.
- 2
Describe what the problem was and what steps you took to address it.
- 3
Highlight how your initiative improved efficiency, safety, or teamwork.
- 4
Use the STAR method: Situation, Task, Action, Result.
- 5
Be clear about the impact of your actions on the team or project.
Example Answers
In my previous job, we were facing consistent delays in our printing process due to machine maintenance. I took the initiative to create a maintenance schedule that outlined regular checks and training for all operators. This reduced downtime by 30%, improving overall productivity.
Good Candidates Answer Questions. Great Ones Win Offers.
Reading sample answers isn't enough. Top candidates practice speaking with confidence and clarity. Get real feedback, improve faster, and walk into your next interview ready to stand out.
Master your interview answers under pressure
Boost your confidence with real-time practice
Speak clearly and impress hiring managers
Get hired faster with focused preparation
Used by hundreds of successful candidates
Technical Interview Questions
What experience do you have operating sheet cutting or sheeting machinery?
How to Answer
- 1
Highlight specific machinery you have operated.
- 2
Mention the types of materials you have worked with.
- 3
Discuss your understanding of safety procedures in operation.
- 4
Include any maintenance or troubleshooting experience you possess.
- 5
Quantify your experience by mentioning years or volume of production.
Example Answers
I have operated a guillotine cutter for over 3 years, primarily working with paper and cardstock. I am familiar with the setup and adjustments necessary for different thicknesses.
What routine maintenance tasks are important for sheeting machines?
How to Answer
- 1
Regularly check and replace worn blades for clean cuts
- 2
Lubricate moving parts to reduce friction and prevent wear
- 3
Inspect belts and rollers for signs of damage or wear
- 4
Clean the machine daily to prevent dust buildup affecting performance
- 5
Perform alignment checks on the machine regularly to ensure precision
Example Answers
Routine maintenance for sheeting machines includes checking and replacing worn blades, lubricating moving parts to prevent wear, and cleaning the machine to avoid dust buildup.
Good Candidates Answer Questions. Great Ones Win Offers.
Reading sample answers isn't enough. Top candidates practice speaking with confidence and clarity. Get real feedback, improve faster, and walk into your next interview ready to stand out.
Master your interview answers under pressure
Boost your confidence with real-time practice
Speak clearly and impress hiring managers
Get hired faster with focused preparation
Used by hundreds of successful candidates
What types of materials have you worked with as a Sheeter Operator, and how do they affect the sheeting process?
How to Answer
- 1
Identify the types of materials you've worked with such as paper, cardboard, or plastics
- 2
Discuss specific properties of these materials that impact sheeting, like thickness or texture
- 3
Mention how you adjusted the sheeting process based on material characteristics
- 4
Provide examples of challenges faced with different materials and how you overcame them
- 5
Keep your answer focused and relevant to the sheeting process
Example Answers
I have primarily worked with paper and cardboard. For instance, thinner paper requires faster speeds to avoid jams, while thicker cardboard needs more pressure to ensure clean sheets without tearing.
How do you adjust the sheeting machine settings for different material thicknesses?
How to Answer
- 1
Identify the thickness of the material you will use.
- 2
Adjust the roller gap based on thickness; wider for thicker materials.
- 3
Modify the feed rate to ensure consistent sheet production.
- 4
Check and adjust the cutting blades for optimal thickness.
- 5
Run test sheets and monitor for quality before full production.
Example Answers
For different material thicknesses, I first check the thickness and adjust the roller gap accordingly to avoid crushing the material. Then, I set the feed rate lower for thicker material to maintain tension and quality. Finally, I run a test sheet to confirm the settings.
Can you explain how you would calibrate a sheeting machine prior to a production run?
How to Answer
- 1
Start by checking the machine's manual for specific calibration instructions.
- 2
Inspect and clean all rollers and components to ensure smooth operation.
- 3
Set the desired sheet size and adjust the machine settings accordingly.
- 4
Run a test sheet to verify dimensions and quality before full production.
- 5
Make final adjustments based on the test results to achieve optimal performance.
Example Answers
To calibrate a sheeting machine, I would first consult the manual for guidance. After that, I would clean all rollers and components thoroughly. Then, I would set the required sheet size and adjust the controls accordingly. I'd run a test sheet to check the dimensions and quality, making any necessary adjustments based on the results.
What steps do you take when the sheeting machine is not producing sheets correctly?
How to Answer
- 1
Check the machine settings for accuracy
- 2
Inspect the paper feed and alignment
- 3
Look for any jams or blockages
- 4
Clean the machine parts that may be affecting performance
- 5
Run a test to diagnose specific issues
Example Answers
I first check the machine settings to make sure they are correct for the job. Then, I inspect the paper feed for any misalignments or jams that might be causing issues.
What industry standards and regulations are relevant to sheeting operations?
How to Answer
- 1
Mention relevant OSHA safety regulations that apply to manufacturing.
- 2
Discuss ISO standards that may pertain to quality management in sheeting.
- 3
Address any specific industry guidelines for handling materials and machinery.
- 4
Highlight any local environmental regulations impacting operations.
- 5
Demonstrate understanding of industry best practices in maintaining safety and quality.
Example Answers
In sheeting operations, OSHA regulations ensure worker safety by addressing machinery safety standards and personal protective equipment requirements. Additionally, ISO 9001 provides a framework for quality management to ensure consistent product quality.
What recent advancements in sheeting technology or processes are you aware of?
How to Answer
- 1
Research the latest technologies in sheeter equipment and processes
- 2
Be prepared to discuss how these advancements improve efficiency and quality
- 3
Mention any relevant experiences you have with new technology
- 4
Stay updated with industry news and journals
- 5
Highlight specific examples of technology that interests you
Example Answers
I recently read about the improvements in automated sheeting systems, which can adjust the cutting speed based on the paper type, enhancing efficiency and reducing waste.
What types of reports or documentation do you typically complete in your role?
How to Answer
- 1
Identify key reports relevant to your previous roles as a Sheeter Operator
- 2
Mention any specific metrics or production documentation you track
- 3
Highlight safety and quality-related documentation you complete
- 4
Discuss any communication logs with team members or supervisors
- 5
Tailor your answer to reflect industry standards and practices
Example Answers
In my previous role, I regularly completed production reports that detailed our output and machine performance metrics. I also maintained safety checklists and quality control documentation to ensure compliance with standards.
How do you prepare the sheeting machine for a new type of material?
How to Answer
- 1
Review the specifications for the new material including thickness and properties
- 2
Clean the machine to remove any residual material or contaminants
- 3
Adjust the machine settings such as speed and temperature according to the new material's requirements
- 4
Perform a test run with the new material to ensure proper feed and output
- 5
Document any adjustments made for future reference
Example Answers
First, I check the specifications of the new material for its thickness and composition. Then, I thoroughly clean the machine to eliminate any leftover material. After that, I adjust the machine settings like the speed and temperature based on the new material's guidelines. Finally, I run a few test sheets to confirm everything is working correctly before starting full production.
Good Candidates Answer Questions. Great Ones Win Offers.
Reading sample answers isn't enough. Top candidates practice speaking with confidence and clarity. Get real feedback, improve faster, and walk into your next interview ready to stand out.
Master your interview answers under pressure
Boost your confidence with real-time practice
Speak clearly and impress hiring managers
Get hired faster with focused preparation
Used by hundreds of successful candidates
What software, if any, do you use to track production metrics related to sheeting?
How to Answer
- 1
Mention specific software you are familiar with, such as ERP systems, MES software, or spreadsheets.
- 2
Explain how you use the software to track key metrics like production speed, waste, and downtime.
- 3
Share any experience with entering data or generating reports using the software.
- 4
If you have used custom software, describe how it was tailored to sheeting processes.
- 5
Emphasize your ability to adapt to new software if necessary.
Example Answers
I have used SAP ERP to track production metrics in sheeting. I input data on production speed and material usage, which helps us identify areas for improvement.
Situational Interview Questions
If you and a co-worker disagreed on how to operate the sheeting machine, how would you resolve the disagreement?
How to Answer
- 1
Acknowledge the disagreement calmly without confrontation.
- 2
Listen to your co-worker's perspective fully before responding.
- 3
Discuss the reasons behind each method and weigh pros and cons.
- 4
Suggest a test run to compare both methods in practice.
- 5
Remain open to compromise and find a solution that works for both.
Example Answers
I would start by discussing our differing views to understand my co-worker's approach. Then, I would suggest we run a small test to see which method yields the best results, allowing us to make an informed decision together.
What would you do if you were falling behind on a production schedule? What steps would you take?
How to Answer
- 1
Assess the current production status and identify the bottlenecks
- 2
Prioritize tasks that will have the largest impact on output
- 3
Communicate with the team to address issues and gather suggestions
- 4
Implement short-term solutions to increase efficiency
- 5
Consider adjusting schedules or shifts if necessary to recover time
Example Answers
I would first analyze the workflow to pinpoint where delays are occurring. Then, I would prioritize key tasks that can help us catch up and collaborate with the team to tackle any challenges effectively.
Good Candidates Answer Questions. Great Ones Win Offers.
Reading sample answers isn't enough. Top candidates practice speaking with confidence and clarity. Get real feedback, improve faster, and walk into your next interview ready to stand out.
Master your interview answers under pressure
Boost your confidence with real-time practice
Speak clearly and impress hiring managers
Get hired faster with focused preparation
Used by hundreds of successful candidates
How would you respond if you noticed a co-worker not following safety protocols while operating the sheeting machine?
How to Answer
- 1
Stay calm and assess the situation before reacting.
- 2
Communicate directly with the co-worker about the safety issue.
- 3
Explain the possible consequences of not following safety protocols.
- 4
Encourage the co-worker to correct their actions immediately.
- 5
If necessary, report the situation to a supervisor for further action.
Example Answers
I would first approach my co-worker calmly and let them know I noticed they weren’t following the safety protocols. I would explain the importance of safety and the risks involved, and encourage them to correct their behavior.
What steps would you take if you noticed that the sheets coming off the machine did not meet quality standards?
How to Answer
- 1
Inspect the sheets immediately to identify specific quality issues.
- 2
Stop the machine to prevent further production of defective sheets.
- 3
Check the machine settings and calibration to ensure they are correct.
- 4
Document the findings and the actions taken for reference.
- 5
Report the issue to the supervisor and collaborate on a solution.
Example Answers
I would first inspect the sheets to determine the exact quality issue. Then, I would stop the machine to prevent any more defective production. After that, I would check the machine settings and make sure everything is calibrated correctly. Finally, I would document the problem and inform my supervisor so we can find a solution together.
If an emergency situation occurred while you are operating the machine, what would be your first course of action?
How to Answer
- 1
Stay calm and assess the situation quickly
- 2
Shut down the machine immediately if it's safe to do so
- 3
Notify your supervisor or team about the emergency immediately
- 4
Follow the company's emergency protocol
- 5
Ensure the safety of yourself and others around you
Example Answers
In an emergency, I would first stay calm and assess the situation. If it is safe, I would shut down the machine to prevent further issues, then I would notify my supervisor immediately and follow our emergency procedures.
Imagine the machine malfunctions during a critical production run; how would you handle the situation?
How to Answer
- 1
Stay calm and assess the situation immediately
- 2
Communicate the issue to your supervisor and team
- 3
Follow the safety protocols before attempting fixes
- 4
Identify the cause of the malfunction if possible
- 5
Document the issue and any steps taken to resolve it
Example Answers
I would first assess the malfunction and ensure safety is prioritized. Then, I would inform my supervisor and the team about the situation. After that, I would check if I can correct the issue while following the safety protocols, and if not, I would assist in implementing the backup plan.
If a new colleague is struggling to learn the sheeting process, how would you assist them?
How to Answer
- 1
Ask them to explain which part they find most challenging to identify specific issues.
- 2
Offer to demonstrate the sheeting process step by step while they observe.
- 3
Encourage hands-on practice by guiding them through the process directly.
- 4
Provide constructive feedback on their attempts and address any mistakes positively.
- 5
Check in with them regularly to ensure they are comfortable and answer any questions.
Example Answers
I would first ask my colleague which part of the sheeting process is challenging for them. Once I understand, I would demonstrate that section step by step, then allow them to try while I guide them. Afterward, I'd give them feedback and check in regularly.
How would you maintain focus and productivity if you were working under tight deadlines?
How to Answer
- 1
Prioritize tasks by urgency and importance.
- 2
Break down larger tasks into manageable steps.
- 3
Limit distractions by creating a focused workspace.
- 4
Take short, regular breaks to recharge.
- 5
Communicate with the team to manage workload effectively.
Example Answers
To maintain focus under tight deadlines, I prioritize tasks based on urgency. I break projects into smaller steps to avoid feeling overwhelmed, and I make sure to limit distractions by keeping my workspace clear. Regular short breaks help me stay refreshed and sharp.
Sheeter Operator Position Details
Salary Information
Average Salary
$37,502
Source: Talent.com
Recommended Job Boards
CareerBuilder
www.careerbuilder.com/jobs/sheeter-operatorZipRecruiter
www.ziprecruiter.com/Jobs/-Sheeter-OperatorThese job boards are ranked by relevance for this position.
Related Positions
- Plastic Machine Operator
- Press Operator
- Metal Worker
- Spring Machine Operator
- Key Cutter
- Tool Dresser
- Steel Checker
- Nail-Making Machine Tender
- Wire Bender
- Plastic Finisher
Similar positions you might be interested in.
Good Candidates Answer Questions. Great Ones Win Offers.
Master your interview answers under pressure
Boost your confidence with real-time practice
Speak clearly and impress hiring managers
Get hired faster with focused preparation
Used by hundreds of successful candidates
Good Candidates Answer Questions. Great Ones Win Offers.
Master your interview answers under pressure
Boost your confidence with real-time practice
Speak clearly and impress hiring managers
Get hired faster with focused preparation
Used by hundreds of successful candidates