Top 30 Quality Assurance Specialist Interview Questions and Answers [Updated 2025]
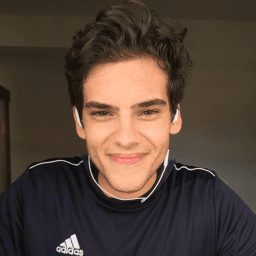
Andre Mendes
•
March 30, 2025
Navigating a Quality Assurance Specialist interview can be daunting, but preparation is key. In this blog post, we've compiled the most common interview questions for this role, complete with example answers and insightful tips to help you respond effectively. Whether you're a seasoned professional or new to the field, these strategies will enhance your confidence and readiness, setting you on the path to success.
Download Quality Assurance Specialist Interview Questions in PDF
To make your preparation even more convenient, we've compiled all these top Quality Assurance Specialistinterview questions and answers into a handy PDF.
Click the button below to download the PDF and have easy access to these essential questions anytime, anywhere:
List of Quality Assurance Specialist Interview Questions
Behavioral Interview Questions
Give an example of a time when you proposed a quality improvement initiative. What was the outcome?
How to Answer
- 1
Select a specific initiative you proposed in your previous role.
- 2
Describe the issue that prompted your proposal clearly.
- 3
Explain the steps you took to implement your initiative.
- 4
Discuss the measurable outcome or results of your initiative.
- 5
Reflect on what you learned from the experience.
Example Answers
In my last job, I noticed that our defect rate was higher than acceptable. I proposed implementing a peer review system for inspections. After implementing this system for three months, we reduced defects by 25% and improved overall team collaboration.
Describe a time when you caught an error in a product or process that others had missed. What was the impact of your discovery?
How to Answer
- 1
Use the STAR method: Situation, Task, Action, Result.
- 2
Clearly explain the context of the error you found.
- 3
Describe your specific role in identifying the error.
- 4
Quantify the impact of your discovery when possible.
- 5
Highlight any improvements made as a result of your action.
Example Answers
In my previous role, I reviewed a batch of components before shipment and found a defect in the soldering that others had missed. This error could have led to product failures in the field. After reporting it, we were able to rework the batch before delivery, preventing costly returns and ensuring customer satisfaction.
Don't Just Read Quality Assurance Specialist Questions - Practice Answering Them!
Reading helps, but actual practice is what gets you hired. Our AI feedback system helps you improve your Quality Assurance Specialist interview answers in real-time.
Personalized feedback
Unlimited practice
Used by hundreds of successful candidates
Can you provide an example where you worked closely with a production team to implement quality standards? How did you ensure collaboration was effective?
How to Answer
- 1
Choose a specific project or production run.
- 2
Describe your role in the team and the quality standards discussed.
- 3
Highlight tools or methods you used for collaboration, like meetings or quality reports.
- 4
Mention challenges faced and how you resolved them with team input.
- 5
End with the positive outcome for quality improvement.
Example Answers
In my previous role, we were launching a new product line. I led weekly meetings with the production team to discuss and implement quality standards. We used a quality checklist during production and addressed non-conformities immediately. This collaboration helped reduce defects by 30% by getting team feedback quickly.
Tell me about a challenging quality issue you encountered and how you resolved it.
How to Answer
- 1
Select a specific issue that had a significant impact
- 2
Outline the steps you took to analyze the problem
- 3
Describe your solution clearly and its implementation
- 4
Include the outcome or results after resolution
- 5
Reflect on what you learned from the experience
Example Answers
In my previous role, we encountered a high defect rate in a key product line. I led a root cause analysis with the team, identifying that a supplier change had impacted material quality. We worked closely with the supplier to set new quality standards and performed additional testing. The defect rate dropped by 50% in the following production cycle, and we established stronger supplier oversight processes. This taught me the importance of collaboration with suppliers.
Tell us about a time you helped improve a quality assurance process. What changes did you implement?
How to Answer
- 1
Choose a specific process you worked on and describe it clearly.
- 2
Explain the problem with the original process that needed improvement.
- 3
Detail the changes you implemented and how you did it.
- 4
Discuss the outcome and benefits of the changes made.
- 5
Use specific metrics or feedback to support your success.
Example Answers
In my last job, I noticed our inspection process was taking too long due to redundant steps. I mapped out the process and identified two inspection stages that could be combined. After implementing this change, we reduced inspection time by 25%, allowing for faster production and improved morale.
Describe a situation where you had to lead a team through a quality inspection process.
How to Answer
- 1
Identify a specific inspection process you led.
- 2
Explain your role in planning and organizing the inspection.
- 3
Discuss how you motivated and communicated with your team.
- 4
Highlight any challenges faced and how you overcame them.
- 5
Conclude with the outcome of the inspection and any improvements made.
Example Answers
In my previous role, I led a quality inspection of a new production line. I organized the team schedule, ensuring everyone understood their roles. When we encountered a recurring defect, I held a meeting to brainstorm solutions. Our efforts led to a 30% reduction in defects in the following weeks.
Explain a scenario where your communication skills helped resolve a quality assurance issue.
How to Answer
- 1
Think of a specific example where communication was key.
- 2
Focus on the problem, your role, and the outcome.
- 3
Highlight how you communicated with different team members.
- 4
Emphasize the impact of your communication on the quality issue.
- 5
Keep your answer concise and structured.
Example Answers
In my previous job, we found a recurring defect in a product. I organized a meeting with the production team to discuss the issue. By clearly explaining the defect and its impact, we collaborated on a corrective action plan, which ultimately reduced the defect rate by 20%.
Discuss a time where you had to quickly adjust to a change in quality standards or regulations.
How to Answer
- 1
Identify a specific situation where a change occurred.
- 2
Explain your initial response to the change.
- 3
Describe the steps you took to adapt to the new standards.
- 4
Highlight the outcome or impact of your actions.
- 5
Reflect on what you learned from the experience.
Example Answers
In my previous role, the company introduced new safety regulations unexpectedly. I quickly gathered the team to review the changes, created a checklist for compliance, and ensured all inspections met the new requirements. As a result, we maintained our certification without any downtime.
Don't Just Read Quality Assurance Specialist Questions - Practice Answering Them!
Reading helps, but actual practice is what gets you hired. Our AI feedback system helps you improve your Quality Assurance Specialist interview answers in real-time.
Personalized feedback
Unlimited practice
Used by hundreds of successful candidates
Technical Interview Questions
What quality assurance standards are you most familiar with, and how have you applied them in previous roles?
How to Answer
- 1
Identify key QA standards relevant to your field like ISO 9001, Six Sigma, or Agile.
- 2
Prepare specific examples where you implemented these standards in your work.
- 3
Highlight measurable outcomes or improvements achieved through your application of these standards.
- 4
Clarify your role in adhering to or promoting these standards within teams or projects.
- 5
Express your commitment to ongoing learning about QA standards and practices.
Example Answers
I am most familiar with ISO 9001, which I applied in my last role by revamping our documentation process. This led to a 20% reduction in defects during production.
What steps do you take to ensure compliance with industry regulations during quality inspections?
How to Answer
- 1
Familiarize yourself with relevant industry standards and regulations.
- 2
Create a checklist based on those regulations to guide your inspections.
- 3
Document findings meticulously and keep records for accountability.
- 4
Collaborate with other departments to align on compliance requirements.
- 5
Stay updated on any changes to regulations and adjust processes accordingly.
Example Answers
I start by reviewing the industry standards relevant to our products to ensure I understand what is required. Then, I create a checklist that reflects these regulations, which I use during inspections. I document every finding thoroughly and maintain a record to track compliance over time.
Don't Just Read Quality Assurance Specialist Questions - Practice Answering Them!
Reading helps, but actual practice is what gets you hired. Our AI feedback system helps you improve your Quality Assurance Specialist interview answers in real-time.
Personalized feedback
Unlimited practice
Used by hundreds of successful candidates
What types of inspection tools and techniques are you proficient with? Can you give examples of how you have used them?
How to Answer
- 1
Identify specific inspection tools you have used in previous roles.
- 2
Mention techniques such as visual inspection, ultrasonic testing, or statistical process control.
- 3
Provide a brief example involving how you used each tool or technique effectively.
- 4
Highlight any relevant certifications or training with these tools.
- 5
Emphasize the outcome of your inspections, such as improvements in quality or compliance.
Example Answers
I am proficient with calipers and micrometers for dimensional inspections. In my previous job, I used calipers to measure component thickness and identified a discrepancy that resulted in adjusting the manufacturing process, improving product accuracy.
Describe your experience with defect tracking systems. Which tools have you used, and how do you document and report defects?
How to Answer
- 1
Identify specific defect tracking tools you have experience with, such as JIRA or Bugzilla.
- 2
Explain how you log defects, including fields you fill out like severity, status, and description.
- 3
Discuss your process for assigning defects to developers or team members.
- 4
Mention any reporting tools or dashboards you have used to communicate defect status.
- 5
Highlight your experience with following up on defect resolution and retesting.
Example Answers
I have used JIRA extensively for defect tracking. When I find a defect, I document it by filling out all necessary fields, including a detailed description, steps to reproduce, and categorizing its severity. I also assign it to the responsible developer and use JIRA's dashboards to track the progress until resolution.
How do you conduct a risk assessment during the quality inspection process?
How to Answer
- 1
Identify potential risks at each stage of the inspection process.
- 2
Evaluate the likelihood and impact of each identified risk.
- 3
Develop a checklist that includes critical quality indicators to monitor.
- 4
Implement control measures to mitigate high-risk issues.
- 5
Document findings and adjust inspection protocols based on the assessment.
Example Answers
I start by identifying potential risks in the materials and processes, then I assess how likely each risk is to occur and what impact it could have. I use a checklist tailored to key quality indicators to ensure nothing is missed, and I take action to mitigate risks where necessary, such as increasing inspections on high-risk items.
What experience do you have with ISO standards related to quality management?
How to Answer
- 1
Identify specific ISO standards you are familiar with, like ISO 9001.
- 2
Share any relevant certifications you have related to ISO standards.
- 3
Discuss practical experience implementing or auditing these standards.
- 4
Include examples of how adherence to these standards improved product quality.
- 5
Mention any training or courses completed on quality management and ISO standards.
Example Answers
I have worked with ISO 9001 for three years in my previous role, where I helped implement quality management processes and assisted in internal audits to ensure compliance.
What statistical methods have you used in quality assurance, and how do they apply to your inspections?
How to Answer
- 1
Identify key statistical methods like control charts and hypothesis testing that you have used.
- 2
Explain how these methods help in analyzing inspection data and maintaining quality standards.
- 3
Provide specific examples of situations where these methods improved quality outcomes.
- 4
Discuss how you interpret statistical results in the context of product compliance and defects.
- 5
Mention tools or software you utilize for statistical analysis in your quality assurance processes.
Example Answers
I frequently use control charts to monitor process stability. For instance, during an inspection of automotive parts, I created control charts to visualize defect rates over time, which helped identify a process out of control and effectively reduced defects by 20%.
How do you approach root cause analysis when identifying a quality issue?
How to Answer
- 1
Define the problem clearly and gather all relevant data.
- 2
Use tools like the 5 Whys or Fishbone diagram to explore causes.
- 3
Involve team members or stakeholders for diverse perspectives.
- 4
Prioritize the causes based on their impact on quality.
- 5
Implement corrective actions and monitor outcomes to ensure resolution.
Example Answers
I start by clearly defining the quality issue and collecting data related to it. Then I apply the 5 Whys technique to trace back to the root cause. Once identified, I collaborate with my team to brainstorm potential solutions and implement the most effective one. Finally, I monitor the results to verify that the issue has been resolved.
How do you prepare quality inspection reports, and what key elements do you include?
How to Answer
- 1
Gather all data from inspections and tests before report writing
- 2
Include detailed findings with clear descriptions of any defects
- 3
Use structured formats for clarity, such as bullet points or tables
- 4
Summarize overall quality trends and provide actionable insights
- 5
Ensure to include any corrective actions taken or necessary follow-ups
Example Answers
I prepare quality inspection reports by first collecting all inspection data and organizing it into a structured format. I include detailed findings on any defects observed, along with photographic evidence when applicable. Each report summarizes the overall quality and highlights any trends or recurring issues, ensuring that actionable insights are clear for the team.
Describe your experience with conducting or preparing for quality audits.
How to Answer
- 1
Summarize your relevant experience with specific examples.
- 2
Mention the types of audits you have participated in, like internal or external.
- 3
Highlight your role in the audit process, such as preparing documentation or leading the audit team.
- 4
Discuss any tools or methodologies you used to ensure quality compliance.
- 5
Explain the outcomes of the audits, including improvements made based on findings.
Example Answers
In my previous role at XYZ Corp, I prepared for internal audits by compiling training records and quality documentation. I also participated in the audit team, focusing on ensuring compliance with ISO 9001 standards, which resulted in a successful audit with zero non-conformities.
Don't Just Read Quality Assurance Specialist Questions - Practice Answering Them!
Reading helps, but actual practice is what gets you hired. Our AI feedback system helps you improve your Quality Assurance Specialist interview answers in real-time.
Personalized feedback
Unlimited practice
Used by hundreds of successful candidates
Situational Interview Questions
Imagine a customer issues a complaint about a product defect. What steps would you take to handle the situation?
How to Answer
- 1
Listen carefully to the customer's complaint without interrupting.
- 2
Acknowledge the issue and express empathy for their experience.
- 3
Gather all relevant details about the defect and the customer's usage.
- 4
Investigate the issue by reviewing product specifications and quality records.
- 5
Provide a clear resolution or next steps to the customer promptly.
Example Answers
First, I would listen to the customer and ensure I understand their complaint completely. Then, I would acknowledge their frustration and express empathy. After that, I would collect details such as when they purchased the product and the specific defect. Next, I would investigate the issue by checking our quality records and find out if this has occurred before. Finally, I would communicate with the customer about the findings and offer a solution, whether it’s a replacement or repair.
If you discovered a critical defect in a major production run, how would you address it?
How to Answer
- 1
Immediately notify your supervisor and the production team about the defect
- 2
Assess the extent of the defect and its impact on the production schedule
- 3
Initiate a containment plan to prevent further defective products from being produced
- 4
Work with the team to identify the root cause of the defect
- 5
Document the findings and develop an action plan for future prevention
Example Answers
First, I would notify my supervisor and the production team to halt the run if necessary. Then, I would evaluate the scope of the defect and how it affects our deadlines. After that, I'd implement a containment strategy to stop any more defective products from being produced and begin investigating the cause to ensure it doesn’t happen again.
Don't Just Read Quality Assurance Specialist Questions - Practice Answering Them!
Reading helps, but actual practice is what gets you hired. Our AI feedback system helps you improve your Quality Assurance Specialist interview answers in real-time.
Personalized feedback
Unlimited practice
Used by hundreds of successful candidates
You need to train a new team member on quality inspection procedures. How would you approach this task?
How to Answer
- 1
Start with an overview of the quality inspection process and its importance.
- 2
Use hands-on demonstrations to show inspection techniques in action.
- 3
Provide clear documentation or a checklist for reference.
- 4
Encourage questions and ensure understanding through discussions.
- 5
Schedule follow-up sessions for practice and feedback.
Example Answers
I would begin by explaining the overall quality inspection process and why it’s crucial for product quality. Then, I’d demonstrate the key inspection techniques, using actual products to illustrate. After that, I'd provide a detailed checklist for them to follow, making sure to encourage them to ask questions throughout. Finally, I'd set up a few practice sessions for them to apply what they've learned.
How would you handle a situation where an unexpected quality issue arises during a client visit?
How to Answer
- 1
Stay calm and composed in front of the client
- 2
Acknowledge the issue promptly and communicate it transparently
- 3
Assess the situation quickly to determine the impact
- 4
Propose a plan to address the issue and involve the client
- 5
Follow up with the client after the visit to ensure satisfaction
Example Answers
I would first acknowledge the issue to the client and explain how we are going to address it. I would then assess the situation to minimize any impact on the client visit and outline the steps we will take to resolve the quality issue. After the visit, I would ensure we follow up with the client to confirm the issue was fully resolved.
If you observe a recurring defect pattern across products, what actions would you take to propose improvements?
How to Answer
- 1
Identify the root cause of the defects through data analysis.
- 2
Collaborate with relevant teams to discuss findings and brainstorm solutions.
- 3
Document the defect patterns and proposed improvements clearly.
- 4
Implement a trial phase for proposed solutions to test effectiveness.
- 5
Establish a monitoring process to ensure continual compliance and improvement.
Example Answers
First, I would analyze the defect data to identify common trends and root causes. Then, I’d involve the production and engineering teams in a meeting to share insights and brainstorm potential solutions. After that, I would document our findings and propose specific improvements. Before full implementation, I’d suggest a trial of the solutions to see their effectiveness, followed by a monitoring plan to track improvements.
How would you manage a situation where a key supplier consistently fails to meet quality standards?
How to Answer
- 1
Analyze the root cause of the quality issues with the supplier.
- 2
Establish clear communication and set expectations for quality standards.
- 3
Implement a corrective action plan with the supplier and monitor progress.
- 4
Explore alternative suppliers while maintaining a good relationship with the current one.
- 5
Document all findings and actions taken for future reference.
Example Answers
I would first investigate to understand why the supplier is failing to meet the standards. It's important to communicate openly with them about the issues. Together, we would create a corrective action plan that outlines the necessary changes, and I'd monitor their progress closely.
You are asked to increase the efficiency of the inspection process without compromising quality. What would you do?
How to Answer
- 1
Identify current bottlenecks in the inspection process
- 2
Implement technology to automate routine tasks
- 3
Train the team on best practices to improve inspection speed
- 4
Regularly review and refine inspection criteria
- 5
Increase collaboration between teams to streamline communications
Example Answers
I would start by analyzing the current inspection process to identify any bottlenecks. Then I would implement automation in areas like data entry or routine checks. Training the team on efficient practices and conducting regular reviews would also be key steps.
How would you facilitate effective collaboration between the quality assurance team and another department to resolve a cross-functional quality issue?
How to Answer
- 1
Identify key stakeholders from both teams.
- 2
Establish clear communication channels from the start.
- 3
Set common goals to align efforts and priorities.
- 4
Schedule regular check-ins to monitor progress and discuss issues.
- 5
Encourage open feedback and shared problem-solving sessions.
Example Answers
I would start by meeting with stakeholders from both teams to understand their perspectives. Then, I would set up a shared project management tool to track the issue and ensure everyone is aligned on our goals. Regular check-ins would help us stay on track and address any obstacles as they arise.
During an inspection, a critical piece of testing equipment fails. What is your course of action?
How to Answer
- 1
Immediately assess the situation and understand the impact of the failure.
- 2
Notify your supervisor or relevant team members about the equipment failure.
- 3
Consult the equipment manual for troubleshooting steps if applicable.
- 4
If the equipment cannot be quickly fixed, switch to backup equipment if available.
- 5
Document the failure and communicate it in your inspection report.
Example Answers
First, I would assess the situation to determine how the equipment failure affects the inspection. Then, I'd notify my supervisor and consult the manual for troubleshooting. If it can't be resolved quickly, I would switch to any available backup equipment and document everything thoroughly.
If you are under pressure to meet inspection deadlines, but need to ensure thorough quality checks, how would you manage this balance?
How to Answer
- 1
Prioritize critical inspections that directly impact safety and compliance.
- 2
Communicate openly with your team about the pressure and seek support to manage workload.
- 3
Use a checklist to streamline your inspection process without missing key details.
- 4
Utilize your experience to quickly identify and focus on high-risk areas.
- 5
Stay organized and allocate specific time blocks for each inspection task.
Example Answers
I would prioritize inspections based on risk factors, ensuring that any high-risk items are addressed first. Clear communication with my team would help distribute the workload effectively.
Don't Just Read Quality Assurance Specialist Questions - Practice Answering Them!
Reading helps, but actual practice is what gets you hired. Our AI feedback system helps you improve your Quality Assurance Specialist interview answers in real-time.
Personalized feedback
Unlimited practice
Used by hundreds of successful candidates
Quality Assurance Specialist Position Details
Salary Information
Recommended Job Boards
These job boards are ranked by relevance for this position.
Related Positions
Ace Your Next Interview!
Practice with AI feedback & get hired faster
Personalized feedback
Used by hundreds of successful candidates
Ace Your Next Interview!
Practice with AI feedback & get hired faster
Personalized feedback
Used by hundreds of successful candidates