Top 30 Quality Supervisor Interview Questions and Answers [Updated 2025]
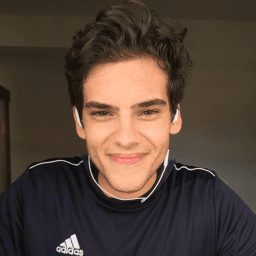
Andre Mendes
•
March 30, 2025
Navigating the interview process for a Quality Supervisor role can be daunting, but preparation is key to success. In this updated guide, we delve into the most common interview questions you may encounter, offering insightful example answers and practical tips to help you respond with confidence and clarity. Whether you're aiming to refine your interview techniques or gain a competitive edge, this resource equips you for a standout performance.
Download Quality Supervisor Interview Questions in PDF
To make your preparation even more convenient, we've compiled all these top Quality Supervisorinterview questions and answers into a handy PDF.
Click the button below to download the PDF and have easy access to these essential questions anytime, anywhere:
List of Quality Supervisor Interview Questions
Behavioral Interview Questions
Can you describe a time when you led a team in solving a major quality issue?
How to Answer
- 1
Choose a specific example with clear context.
- 2
Explain the quality issue and its impact on the company.
- 3
Describe your leadership role and the actions you took.
- 4
Highlight collaboration with team members and stakeholders.
- 5
Emphasize the results and improvements achieved.
Example Answers
In my previous role, we faced a significant defect rate in one of our products. I assembled a cross-functional team, and we conducted a root cause analysis. I facilitated brainstorming sessions to generate solutions. We implemented new testing protocols, which reduced defects by 30% in three months.
Describe a situation where you had to communicate complex quality standards to a diverse team. How did you ensure understanding?
How to Answer
- 1
Identify a specific situation you handled involving quality standards.
- 2
Explain the diverse backgrounds of your team members.
- 3
Describe the methods you used to simplify complex information.
- 4
Discuss how you confirmed that everyone understood the standards.
- 5
Mention any follow-up activities you did to reinforce the quality standards.
Example Answers
In my previous role, we had a diverse team with members from engineering, production, and quality control. I organized a workshop where I broke down the quality standards into key visual aids and simple terms. I used real examples relevant to each department and asked for feedback to ensure everyone understood.
Don't Just Read Quality Supervisor Questions - Practice Answering Them!
Reading helps, but actual practice is what gets you hired. Our AI feedback system helps you improve your Quality Supervisor interview answers in real-time.
Personalized feedback
Unlimited practice
Used by hundreds of successful candidates
Give an example of a time when you identified a potential quality problem before it occurred. What actions did you take?
How to Answer
- 1
Start with a specific situation you encountered.
- 2
Explain how you noticed the potential problem.
- 3
Describe the proactive measures you took to prevent it.
- 4
Highlight the positive outcomes of your actions.
- 5
Keep your answer structured and to the point.
Example Answers
At my previous company, I noticed a trend of increasing defect rates in a specific production line. I reviewed production data and identified that a machine was not calibrated correctly. I immediately scheduled a calibration check and retrained the operators. As a result, we reduced defects by 30% in the following month.
Can you provide an example of how you introduced an innovation that improved quality processes?
How to Answer
- 1
Identify a specific quality issue you faced in your role.
- 2
Describe the innovative solution you implemented to address it.
- 3
Explain the positive impact this had on quality processes.
- 4
Use metrics or feedback to quantify the improvement.
- 5
Mention collaboration with team members or stakeholders if applicable.
Example Answers
In my previous role, we struggled with inconsistent product inspections. I introduced a mobile app for inspectors to log data in real-time. This innovation reduced errors by 30% and sped up our reporting process significantly.
Describe a difficult decision you had to make regarding a quality process. What was the outcome?
How to Answer
- 1
Identify a specific quality issue and explain its significance
- 2
Describe the decision-making process, including any alternatives considered
- 3
Focus on the outcome and highlight how it impacted the team or project
- 4
Emphasize any lessons learned from the experience
- 5
Keep your answer structured: situation, action, result
Example Answers
In my previous role, we faced a significant defect rate in a product line. I had to decide whether to halt production until we fixed the issue or to continue and risk customer dissatisfaction. I chose to halt production to implement a more thorough quality check process. As a result, we reduced defects by 40%, and our customers reported higher satisfaction.
Provide an example of how you fostered teamwork in a quality improvement project.
How to Answer
- 1
Choose a specific project with measurable outcomes.
- 2
Highlight your role in facilitating collaboration.
- 3
Use examples of communication methods you employed.
- 4
Describe how you resolved conflicts within the team.
- 5
Emphasize the results achieved through teamwork.
Example Answers
In a project to reduce defects, I organized weekly meetings where team members could share their insights. I facilitated discussions that encouraged open communication. By involving everyone in decision-making, we reduced defects by 20%.
Tell me about a quality improvement project you managed. How did you ensure it stayed on track?
How to Answer
- 1
Start by describing the project clearly and its goals
- 2
Mention specific quality metrics you were targeting
- 3
Explain the steps you took to plan and execute the project
- 4
Discuss how you monitored progress and addressed issues
- 5
Conclude with the results and any lessons learned
Example Answers
I managed a project to reduce defects in our manufacturing line by 20%. I set clear quality metrics, used a control chart to track progress weekly, and held regular team meetings to address any issues. By the end, we achieved a 25% reduction in defects and improved overall efficiency.
Describe a challenging quality problem you solved in the past. What was your approach?
How to Answer
- 1
Choose a specific quality issue you faced.
- 2
Explain the root cause analysis you conducted.
- 3
Describe the solution you implemented.
- 4
Highlight the positive outcome and lessons learned.
- 5
Be concise and focused on your role in the solution.
Example Answers
In a previous role, we faced a high defect rate in a product due to a faulty component. I led a root cause analysis, identifying that a supplier's materials were substandard. I collaborated with the supplier to improve their processes and switched to a quality-assured component. As a result, defects dropped by 40%, and production efficiency improved significantly.
Have you ever mentored someone in quality assurance? What was the outcome?
How to Answer
- 1
Choose a specific mentoring experience to describe
- 2
Focus on the mentee's goals and how you helped achieve them
- 3
Mention any tools or techniques you used in the mentoring process
- 4
Highlight the outcomes and any measurable improvements
- 5
Reflect on what you learned from the experience
Example Answers
I mentored a junior QA analyst on automated testing. We set goals for her to learn testing frameworks, and I provided weekly sessions. She implemented automated tests that improved our release process by 25%. I learned the importance of structured mentoring.
Don't Just Read Quality Supervisor Questions - Practice Answering Them!
Reading helps, but actual practice is what gets you hired. Our AI feedback system helps you improve your Quality Supervisor interview answers in real-time.
Personalized feedback
Unlimited practice
Used by hundreds of successful candidates
Technical Interview Questions
What are the key components of a quality management system (QMS)?
How to Answer
- 1
Identify the main components of a QMS such as documentation, processes, and continuous improvement.
- 2
Use industry terminology but keep explanations clear and straightforward.
- 3
Mention how these components contribute to overall quality and customer satisfaction.
- 4
Provide examples of standards like ISO 9001 to support your answer.
- 5
Tailor your response to the specific industry you are applying to.
Example Answers
A QMS typically includes components like policy documentation, quality planning, process management, and performance evaluation. For instance, ISO 9001 outlines the need for documented processes and continual improvement to enhance customer satisfaction.
What is the difference between ISO 9001 and ISO 14001?
How to Answer
- 1
Define each standard briefly.
- 2
Highlight key focus areas: quality vs. environmental management.
- 3
Mention the applicability of each standard in industries.
- 4
Include a sentence on certification processes.
- 5
Conclude with the benefits of each standard.
Example Answers
ISO 9001 focuses on quality management systems to ensure customer satisfaction while ISO 14001 emphasizes environmental management to enhance sustainability. Both can be applied in various industries but serve different purposes in organizational goals and values.
Don't Just Read Quality Supervisor Questions - Practice Answering Them!
Reading helps, but actual practice is what gets you hired. Our AI feedback system helps you improve your Quality Supervisor interview answers in real-time.
Personalized feedback
Unlimited practice
Used by hundreds of successful candidates
How do you utilize statistical process control (SPC) in improving quality processes?
How to Answer
- 1
Explain what SPC is and its importance in quality control
- 2
Describe specific tools or methods you use within SPC, like control charts
- 3
Provide an example of a situation where you implemented SPC
- 4
Highlight the impact of using SPC on process outcomes or product quality
- 5
Emphasize teamwork and communication in SPC implementation
Example Answers
In my previous role, I used control charts to track defect rates in production. By analyzing the data, we pinpointed issues in a specific machine, which led to a 15% reduction in defects after corrective actions were taken.
How do you perform risk assessment in quality management?
How to Answer
- 1
Identify potential risks in the quality processes through brainstorming and historical data analysis
- 2
Evaluate the impact and likelihood of each risk using a risk matrix
- 3
Prioritize risks based on their severity and likelihood
- 4
Implement control measures to mitigate the highest priority risks
- 5
Review and update the risk assessment regularly to adapt to any changes
Example Answers
I conduct risk assessments by first identifying risks through team discussions and past quality issues. Then, I use a risk matrix to evaluate each risk's impact and likelihood, prioritizing them to focus on the biggest threats. Finally, I implement measures to mitigate high-priority risks and review this process quarterly.
What documentation do you consider essential for maintaining quality standards?
How to Answer
- 1
Identify key documents like quality manuals and standard operating procedures (SOPs)
- 2
Mention quality control plans that outline measurement and testing methods
- 3
Include records for training and competence of personnel involved in quality processes
- 4
Discuss the importance of audit reports and corrective action documentation
- 5
Emphasize the role of compliance documentation with industry standards
Example Answers
I believe essential documentation includes quality manuals, SOPs for processes, and quality control plans that detail measurement criteria. Additionally, training records for staff ensure everyone is competent in quality tasks.
What key performance indicators (KPIs) do you use to measure quality performance?
How to Answer
- 1
Identify relevant KPIs for the specific industry or sector.
- 2
Include both quantitative and qualitative metrics in your answer.
- 3
Explain how each KPI contributes to improving quality.
- 4
Mention how you track and report on these KPIs effectively.
- 5
Discuss any tools or software you use to measure these indicators.
Example Answers
I use KPIs such as defect rates, customer complaints, and first-pass yield to measure quality performance. These indicators help pinpoint areas needing improvement. I track these metrics through our quality management system to ensure timely reporting and action.
What methods do you use to conduct process improvement within quality management?
How to Answer
- 1
Identify key quality metrics to monitor performance.
- 2
Use root cause analysis to identify areas of improvement.
- 3
Implement the Plan-Do-Check-Act (PDCA) cycle for structured improvements.
- 4
Involve the team in brainstorming sessions for diverse ideas.
- 5
Regularly review and adjust processes based on feedback and outcomes.
Example Answers
I focus on key quality metrics, conduct root cause analysis for issues, and use the PDCA cycle to implement improvements effectively.
What are the steps you take to prepare for a quality audit?
How to Answer
- 1
Review previous audit reports to identify areas of improvement
- 2
Gather all relevant documentation and quality records
- 3
Conduct a self-audit or pre-audit to identify potential issues
- 4
Ensure all team members are aware of the audit and their roles
- 5
Follow up on corrective actions from previous audits to show improvement
Example Answers
I first review the previous audit reports to understand what issues were raised. Then, I gather all necessary documents and quality records. Next, I conduct a self-audit with my team to find any potential problems before the actual audit.
How do you ensure your team complies with all relevant quality regulations and standards?
How to Answer
- 1
Conduct regular training sessions on quality standards for the team.
- 2
Implement a checklist system to ensure compliance during daily operations.
- 3
Review quality metrics and reports frequently to identify areas for improvement.
- 4
Encourage open communication within the team about quality issues.
- 5
Perform regular audits and provide feedback to team members.
Example Answers
I conduct regular training sessions to keep my team updated on quality standards, and we use checklists to ensure compliance during our operations.
How do lean manufacturing principles integrate with quality control practices?
How to Answer
- 1
Explain lean principles like waste reduction and continuous improvement.
- 2
Discuss how quality control ensures consistent output in lean processes.
- 3
Highlight the role of employee involvement in both lean and quality.
- 4
Describe specific tools from lean that enhance quality, like Kaizen or 5S.
- 5
Connect these principles to overall productivity and customer satisfaction.
Example Answers
Lean manufacturing focuses on eliminating waste and improving efficiency. By integrating quality control practices, we ensure that each step in the process produces consistent outcomes. Tools like Kaizen promote continuous improvement, which directly enhances our quality metrics.
Don't Just Read Quality Supervisor Questions - Practice Answering Them!
Reading helps, but actual practice is what gets you hired. Our AI feedback system helps you improve your Quality Supervisor interview answers in real-time.
Personalized feedback
Unlimited practice
Used by hundreds of successful candidates
Situational Interview Questions
How would you assess the performance of your team in maintaining quality standards?
How to Answer
- 1
Define clear quality metrics for assessment
- 2
Monitor team adherence to quality processes regularly
- 3
Conduct performance reviews that include quality outcomes
- 4
Encourage team feedback to identify improvement areas
- 5
Use data analysis to track quality trends over time
Example Answers
I would set specific quality metrics like defect rates and process compliance. Regular audits and team reviews would help assess how well the team meets these standards.
If a quality audit uncovers a recurring issue in the production line, how would you address it?
How to Answer
- 1
Identify the root cause of the recurring issue through data analysis.
- 2
Involve the production team in brainstorming solutions for the problem.
- 3
Implement corrective actions and monitor their effectiveness.
- 4
Train employees on the new procedures to prevent recurrence.
- 5
Document the findings and the steps taken for future audits and improvements.
Example Answers
First, I would analyze the audit data to identify the root cause of the recurring issue. Then, I would convene a meeting with the production team to discuss potential solutions. After implementing a corrective action, I would monitor the production line closely to ensure the changes are effective and provide training to the staff on the new procedures.
Don't Just Read Quality Supervisor Questions - Practice Answering Them!
Reading helps, but actual practice is what gets you hired. Our AI feedback system helps you improve your Quality Supervisor interview answers in real-time.
Personalized feedback
Unlimited practice
Used by hundreds of successful candidates
If you have two team members disagreeing on the interpretation of quality standards, how would you resolve the conflict?
How to Answer
- 1
Listen to both team members to understand their perspectives
- 2
Encourage open communication and a collaborative discussion
- 3
Refer to documented quality standards for clarification
- 4
Find common ground and agree on a way forward
- 5
If necessary, involve a third party for mediation
Example Answers
I would first listen to both team members to understand their viewpoints. Then, I would facilitate a discussion to clarify the quality standards. If needed, I would refer to our documentation to resolve any ambiguities.
Imagine the quality benchmarks have changed significantly. What steps would you take to adapt the existing processes?
How to Answer
- 1
Evaluate the new quality benchmarks to understand the changes in requirements.
- 2
Communicate changes to the team and align them around new expectations.
- 3
Review and update existing processes to meet or exceed the new benchmarks.
- 4
Implement training sessions to ensure the team is equipped with necessary skills.
- 5
Monitor and assess results after changes to ensure compliance and effectiveness.
Example Answers
I would start by thoroughly evaluating the new benchmarks to identify which specific areas our current processes need to change. Next, I would hold a meeting with the team to discuss these changes and ensure everyone understands the new expectations. After that, I would review our existing processes, update relevant protocols, and implement any necessary training to fill skill gaps. Finally, I would keep a close eye on our performance metrics to ensure we are meeting the new quality standards effectively.
Your team is tasked with reducing defects by 20% within a month. How would you approach this challenge?
How to Answer
- 1
Conduct a root cause analysis to identify major defect sources
- 2
Set clear, measurable goals for the team focused on those areas
- 3
Implement targeted training for team members on quality standards
- 4
Utilize data tracking to monitor progress and adjust strategies weekly
- 5
Encourage open communication and feedback within the team
Example Answers
First, I would perform a root cause analysis to pinpoint where most defects are occurring. Next, I would set specific goals for reducing defects in those key areas and provide targeted training for the team. I would track our progress with weekly data reviews to ensure we’re on track.
You need to improve quality, but your budget is limited. How would you prioritize your initiatives?
How to Answer
- 1
Identify the most critical areas affecting quality.
- 2
Use data to assess the impact of potential initiatives.
- 3
Focus on low-cost improvements that can have high returns.
- 4
Engage employees for their insights and suggestions.
- 5
Implement quick wins to demonstrate immediate progress.
Example Answers
I would start by analyzing data to identify the top quality issues impacting our products. Next, I would gather employee feedback to pinpoint inexpensive improvements. Prioritizing quick wins, like minor process adjustments, can demonstrate immediate benefits, which can help garner more support for further initiatives.
How would you implement a training program to improve quality awareness within the organization?
How to Answer
- 1
Assess current quality awareness levels through surveys.
- 2
Develop training modules focused on key quality principles.
- 3
Incorporate hands-on exercises and real case studies.
- 4
Schedule regular training sessions and refreshers for all staff.
- 5
Measure the impact of training through follow-up assessments.
Example Answers
To implement a training program, I would start by assessing employees' current awareness through surveys. Based on the results, I would create targeted training modules discussing quality principles and incorporate hands-on exercises. Regular refresher courses would keep the information fresh, and I'd measure the impact with follow-up assessments.
A major client has complained about quality issues repeatedly. How would you handle this situation to restore customer confidence?
How to Answer
- 1
Acknowledge the client's concerns and express empathy.
- 2
Investigate the root cause of the quality issues promptly.
- 3
Communicate your findings and planned corrective actions clearly to the client.
- 4
Implement changes to improve quality and prevent recurrence.
- 5
Follow up with the client to ensure satisfaction after changes are made.
Example Answers
I would first reach out to the client to apologize for the issues and assure them that I take their concerns seriously. Next, I would assemble a team to investigate the quality problems and identify the root causes. After gathering insights, I would communicate a detailed action plan to the client, showing how we intend to address their concerns. Finally, I would schedule follow-up meetings to ensure we restore their confidence over time.
If a serious quality defect is found in shipped products, how would you manage the situation?
How to Answer
- 1
Acknowledge the seriousness of the defect immediately
- 2
Communicate openly with all stakeholders including customers and internal teams
- 3
Investigate the root cause to prevent future occurrences
- 4
Develop a corrective action plan to address the current defect
- 5
Monitor the effectiveness of the actions taken and follow up with stakeholders
Example Answers
First, I would assess the situation and acknowledge the defect to all relevant parties. I would inform customers promptly and transparently. Next, I would initiate a root cause analysis to understand how the defect occurred and then implement a corrective action plan to address it and prevent future issues. Finally, I would keep all stakeholders updated throughout the resolution process.
How would you handle a situation where the production department is resistant to implementing a new quality procedure?
How to Answer
- 1
First, listen to the concerns of the production team without interrupting.
- 2
Provide clear evidence or data showing the benefits of the new procedure.
- 3
Involve production staff in the implementation process to gain their insights.
- 4
Offer training sessions to ensure everyone understands the new procedure.
- 5
Follow up regularly to address any ongoing issues or resistance.
Example Answers
I would start by listening to the production team's concerns about the new quality procedure. It's important to understand their perspective. Then, I would present data that highlights the positive impact of the new procedure on product quality and efficiency. Involving them in the rollout could also help them feel more invested in the change.
Don't Just Read Quality Supervisor Questions - Practice Answering Them!
Reading helps, but actual practice is what gets you hired. Our AI feedback system helps you improve your Quality Supervisor interview answers in real-time.
Personalized feedback
Unlimited practice
Used by hundreds of successful candidates
Quality Supervisor Position Details
Recommended Job Boards
ZipRecruiter
www.ziprecruiter.com/Jobs/Quality-SupervisorThese job boards are ranked by relevance for this position.
Related Positions
Ace Your Next Interview!
Practice with AI feedback & get hired faster
Personalized feedback
Used by hundreds of successful candidates
Ace Your Next Interview!
Practice with AI feedback & get hired faster
Personalized feedback
Used by hundreds of successful candidates