Top 30 Quality Technician Interview Questions and Answers [Updated 2025]
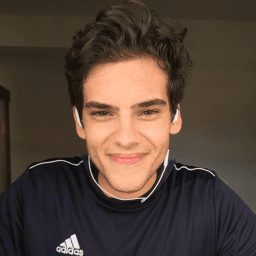
Andre Mendes
•
March 30, 2025
Preparing for a Quality Technician interview can be daunting, but fear not! This blog post gathers the most common interview questions for the Quality Technician role, providing you with example answers and insightful tips on crafting effective responses. Dive in to enhance your confidence and readiness, equipping yourself with the knowledge to impress potential employers and secure your next opportunity.
Download Quality Technician Interview Questions in PDF
To make your preparation even more convenient, we've compiled all these top Quality Technicianinterview questions and answers into a handy PDF.
Click the button below to download the PDF and have easy access to these essential questions anytime, anywhere:
List of Quality Technician Interview Questions
Behavioral Interview Questions
Can you describe a time when you identified a significant quality issue? How did you handle it?
How to Answer
- 1
Use the STAR method: Situation, Task, Action, Result.
- 2
Focus on your role in identifying the issue.
- 3
Describe the tools or processes you used to analyze the problem.
- 4
Explain the steps you took to resolve the issue.
- 5
Share the positive outcome or lessons learned.
Example Answers
In my previous role, I noticed a recurring defect in our assembly line. I gathered data, analyzed the workflow, and identified a faulty calibration in the machinery. I worked closely with maintenance to fix the issue, which reduced defects by 30% in the following month.
Tell me about an experience where you had to collaborate with another team to improve quality standards. What was your role?
How to Answer
- 1
Identify a specific project or situation where collaboration occurred.
- 2
Describe your role and responsibilities clearly.
- 3
Explain the quality issue that prompted the collaboration.
- 4
Outline the actions taken with the other team.
- 5
Share the results or improvements achieved from the collaboration.
Example Answers
In my previous role, I collaborated with the production team to reduce defects in our products. I was responsible for analyzing quality data and identifying patterns. We held joint meetings to discuss potential causes and implemented a new checklist during production. This reduced defects by 30% over three months.
Don't Just Read Quality Technician Questions - Practice Answering Them!
Reading helps, but actual practice is what gets you hired. Our AI feedback system helps you improve your Quality Technician interview answers in real-time.
Personalized feedback
Unlimited practice
Used by hundreds of successful candidates
Describe a situation where you had to quickly adapt to a change in quality standards or protocols. How did you approach it?
How to Answer
- 1
Think of a specific situation where standards changed suddenly.
- 2
Explain how you assessed the new requirements quickly.
- 3
Describe the steps you took to implement the changes.
- 4
Mention any collaboration with team members for support.
- 5
Highlight the positive outcome or learning from the experience.
Example Answers
In my previous role, our company switched to a new quality standard unexpectedly. I quickly reviewed the new guidelines, identified gaps in our current practices, and organized a meeting with my team to ensure everyone was aligned. Together, we updated our processes and implemented a checklist to meet the new requirements, which led to a successful audit.
Give an example of how your attention to detail helped prevent a potential quality problem in your previous work.
How to Answer
- 1
Choose a specific situation from your past experience.
- 2
Clearly describe the problem that was identified.
- 3
Explain the steps you took to address the issue.
- 4
Highlight the outcome and how it prevented a quality issue.
- 5
Emphasize what you learned and how it improved future processes.
Example Answers
In my previous role, I noticed a discrepancy in the dimensions of a batch of components. I double-checked the specifications and found an error in the design documents. I immediately alerted my supervisor, and we corrected the specifications before production, avoiding any defective products. This experience taught me the importance of verifying details in documents.
Have you ever taken the lead on a quality improvement project? What were the results?
How to Answer
- 1
Choose a specific project highlighting your role.
- 2
Focus on the problem you identified and the strategy you implemented.
- 3
Mention collaboration with teams or departments.
- 4
Quantify the results with metrics or improvements.
- 5
Reflect on what you learned and how it can apply to future projects.
Example Answers
I led a project to reduce defects in our production line by analyzing failure reports. I coordinated with the engineering team to implement new testing protocols, which reduced defects by 30% over three months. This experience taught me the importance of cross-department communication.
Can you provide an example of a time when you took the initiative to improve a quality process? What was the outcome?
How to Answer
- 1
Identify a specific quality process you improved.
- 2
Explain the challenge or problem that needed addressing.
- 3
Describe the actions you took and why you chose them.
- 4
Mention any tools or methods you used to implement the change.
- 5
Share the measurable outcome or benefits resulting from your initiative.
Example Answers
In my last job, I noticed the inspection process was causing delays. I initiated a review and suggested a new checklist that reduced inspection time by 30%. As a result, we met deadlines consistently and improved overall efficiency.
Tell me about a time you learned something new that significantly impacted your work as a Quality Technician.
How to Answer
- 1
Choose a specific learning experience related to quality control processes.
- 2
Explain what you learned and how you learned it.
- 3
Describe how this new knowledge improved a specific aspect of your work.
- 4
Use quantifiable results if possible to highlight the impact.
- 5
Reflect on the importance of continuous learning in quality assurance.
Example Answers
I learned about a new statistical analysis software during a training session. This helped me identify trends in defects more quickly, reducing our response time by 20% and improving overall quality metrics.
Describe a situation where your efforts resulted in measurable quality improvements. What metrics did you use?
How to Answer
- 1
Choose a specific project or process where you initiated change
- 2
Explain the problem and the impact on quality before your intervention
- 3
Detail the actions you took to improve quality
- 4
Present tangible metrics that demonstrate the improvement
- 5
Conclude with the positive outcome for the team or company
Example Answers
In a previous role, I identified high defect rates in our assembly line. I led a team to conduct root cause analysis and implemented a new quality checklist. As a result, defect rates dropped from 5% to 1% over three months, significantly improving overall production yield.
Can you describe how you've communicated quality issues to non-technical stakeholders in the past?
How to Answer
- 1
Use simple, clear language to explain technical terms.
- 2
Provide specific examples or anecdotes to illustrate your points.
- 3
Focus on the impact of the quality issue on their work or the project.
- 4
Engage them by asking for their input or perspective on the issue.
- 5
Highlight any positive outcomes or improvements resulting from the communication.
Example Answers
In my previous role, I identified a flaw in our product design. I presented it to the sales team in straightforward terms, focusing on how it could affect customer satisfaction. Together, we brainstormed potential solutions, which led to a design adjustment that increased our product ratings.
Don't Just Read Quality Technician Questions - Practice Answering Them!
Reading helps, but actual practice is what gets you hired. Our AI feedback system helps you improve your Quality Technician interview answers in real-time.
Personalized feedback
Unlimited practice
Used by hundreds of successful candidates
Technical Interview Questions
What quality inspection tools and techniques are you familiar with, and how have you used them in your previous roles?
How to Answer
- 1
List specific tools like calipers, micrometers, or CMMs.
- 2
Mention techniques such as SPC, FMEA, or root cause analysis.
- 3
Provide a brief example of how you applied each tool or technique.
- 4
Highlight any measurable impact your actions had on quality.
- 5
Be prepared to discuss any challenges faced and how you overcame them.
Example Answers
I am familiar with calipers and micrometers for precise measurements. In my last role, I used these tools to inspect incoming components, which led to a 15% reduction in defects.
Can you explain the importance of ISO standards in quality management? Give an example of how you have applied them.
How to Answer
- 1
Start with a brief definition of ISO standards and their role in quality management.
- 2
Highlight the benefits of implementing ISO standards, such as consistency and customer satisfaction.
- 3
Provide a specific example of a process or project where you applied ISO standards.
- 4
Mention any measurable outcomes or improvements from using ISO standards.
- 5
Keep the explanation concise and focused on real-world applications.
Example Answers
ISO standards provide a framework for consistent quality management, ensuring products meet customer expectations. In my previous role, I implemented ISO 9001 for our production process, which improved our defect rate by 20%, enhancing customer satisfaction.
Don't Just Read Quality Technician Questions - Practice Answering Them!
Reading helps, but actual practice is what gets you hired. Our AI feedback system helps you improve your Quality Technician interview answers in real-time.
Personalized feedback
Unlimited practice
Used by hundreds of successful candidates
How do you utilize statistical process control (SPC) in your quality assessments? Can you provide an example?
How to Answer
- 1
Explain the role of SPC in identifying process variations.
- 2
Mention specific tools or charts you use, like control charts or process capability analysis.
- 3
Discuss how you analyze data to make informed quality decisions.
- 4
Provide a concrete example that illustrates your approach.
- 5
Highlight the impact of your SPC implementation on quality improvement.
Example Answers
I use SPC to monitor production processes and identify any variations. For example, I implemented control charts for a bottling line which allowed us to pinpoint when the fill levels deviated from specifications. This led to reducing defects by 20%.
What methods do you use for root cause analysis in your quality investigations?
How to Answer
- 1
Use the 5 Whys technique to drill down to the root cause.
- 2
Apply Fishbone diagrams to categorize possible causes.
- 3
Collect data and evidence to support your analysis.
- 4
Collaborate with team members to gain diverse perspectives.
- 5
Document findings and create action plans to prevent recurrence.
Example Answers
I typically use the 5 Whys method, which helps me identify the core issue by asking 'why' multiple times until the root cause is found. For example, if a defect occurs, I keep asking why until I uncover the underlying problem.
Describe your experience with creating and maintaining quality documentation. What tools have you used?
How to Answer
- 1
Highlight specific quality documentation types you have created, like inspection reports or quality manuals
- 2
Mention any relevant standards or regulations you adhered to, such as ISO or Six Sigma
- 3
Include the tools and software you have used, like Excel, Quality Management System (QMS), or specific procedures
- 4
Provide an example that demonstrates your attention to detail and organizational skills
- 5
Discuss how you ensure documentation is up to date and accessible for team members
Example Answers
In my previous role, I created and maintained inspection reports and process documentation following ISO 9001 standards. I used tools like Microsoft Excel for data collection and a Quality Management System to manage records. I ensure all documents are reviewed quarterly for accuracy and compliance.
What experience do you have with quality management software? Which tools have you implemented in your work?
How to Answer
- 1
Identify specific quality management software you have used.
- 2
Explain any roles you had in implementing or managing the software.
- 3
Highlight outcomes or improvements resulting from using the software.
- 4
Mention any training or certifications related to the tools.
- 5
Be prepared to discuss how you adapted to new software.
Example Answers
I have extensive experience with Minitab for statistical analysis and quality control. In my previous role, I implemented it to analyze defect rates, which led to a 20% reduction in errors over six months.
How do you ensure compliance with industry safety and quality standards? Can you give a specific example?
How to Answer
- 1
Discuss relevant standards like ISO, ASTM or industry-specific regulations
- 2
Mention regular training and updates for yourself and the team
- 3
Describe a systematic approach to audits and inspections
- 4
Provide an example where you identified a compliance issue and resolved it
- 5
Highlight the importance of documenting processes and outcomes
Example Answers
In my previous role, I ensured compliance with ISO 9001 standards by conducting monthly training sessions for the team, reviewing our processes regularly and performing internal audits. Once, I identified a deviation in our testing procedures that could affect quality, implemented corrective actions, and updated our documentation to prevent future issues.
Can you explain how you perform a failure mode and effects analysis (FMEA)? What is its importance in quality control?
How to Answer
- 1
Start by defining FMEA and its purpose in identifying potential failure points.
- 2
Outline the steps: Identify failure modes, assess effects, assign severity, occurrence, and detection ratings.
- 3
Explain how to calculate the risk priority number (RPN) to prioritize issues.
- 4
Discuss the impact of FMEA on improving product reliability and safety.
- 5
Mention collaboration with cross-functional teams to gather insights.
Example Answers
FMEA is a structured approach to identify potential failures in a product or process. I begin by listing failure modes, then assess their effects on performance. Each mode gets ratings for severity, occurrence, and detection, leading to a risk priority number (RPN) that helps prioritize remediation efforts. This analysis is crucial for enhancing product reliability and ensuring customer safety.
What key performance indicators do you consider critical in measuring quality performance?
How to Answer
- 1
Identify which KPIs align with the specific industry or company goals
- 2
Discuss both operational and financial KPIs for a well-rounded view
- 3
Mention KPIs that track customer satisfaction and defect rates
- 4
Include how to use KPIs for continuous improvement
- 5
Explain the importance of real-time data tracking and reporting
Example Answers
I consider defect rate, customer satisfaction score, and process efficiency as critical KPIs. Tracking defect rates helps identify areas for improvement, while customer satisfaction reflects the end result of our quality efforts. Process efficiency ensures we maintain productivity while upholding standards.
What is your experience with benchmarking quality metrics against other organizations or industry standards?
How to Answer
- 1
Identify specific quality metrics you have used for benchmarking.
- 2
Mention any tools or methods employed for gathering data.
- 3
Include examples of organizations or standards referenced.
- 4
Discuss the outcomes of your benchmarking efforts.
- 5
Highlight any improvements made as a result of the benchmarks.
Example Answers
In my previous role, I benchmarked defect rates against industry standards like ISO 9001. I used statistical tools to gather data and found that our rates were above the industry average. This led to implementing a new training program that reduced defects by 15%.
Don't Just Read Quality Technician Questions - Practice Answering Them!
Reading helps, but actual practice is what gets you hired. Our AI feedback system helps you improve your Quality Technician interview answers in real-time.
Personalized feedback
Unlimited practice
Used by hundreds of successful candidates
Situational Interview Questions
If a batch of products failed quality inspection, what steps would you take to investigate the issue?
How to Answer
- 1
Review inspection criteria to identify specific failures
- 2
Gather data from the inspection reports for analysis
- 3
Inspect a sample of the failed products for common defects
- 4
Consult with production staff for insights on potential issues
- 5
Develop a report summarizing findings and suggest corrective actions
Example Answers
I would start by reviewing the inspection criteria to pinpoint the exact reasons for the failures. Then, I would analyze the inspection reports for any patterns or trends. Following that, I'd inspect a sample of the failed products myself to understand the defects better. I'd also talk to the production team to gather insights before compiling a report with my findings and recommendations for improvements.
Imagine you are tasked with implementing a new quality process, but your team is resistant to change. How would you handle this?
How to Answer
- 1
Understand the reasons for resistance by opening a dialogue with the team
- 2
Clearly explain the benefits of the new quality process for the team and the organization
- 3
Involve the team in the implementation process to gain their buy-in
- 4
Provide training and resources to ease the transition
- 5
Celebrate small wins to build momentum and reinforce positive changes
Example Answers
I would start by having one-on-one conversations to understand why the team is resistant. Then, I would present data showing how the new process could improve our efficiency and quality. I'd include them in planning meetings to give them ownership of the changes.
Don't Just Read Quality Technician Questions - Practice Answering Them!
Reading helps, but actual practice is what gets you hired. Our AI feedback system helps you improve your Quality Technician interview answers in real-time.
Personalized feedback
Unlimited practice
Used by hundreds of successful candidates
You have multiple quality checks to perform in a limited timeframe. How would you prioritize your tasks?
How to Answer
- 1
Identify critical quality checks that impact product safety or compliance first
- 2
Assess the time each task requires and estimate the total time available
- 3
Group similar tasks together to maximize efficiency
- 4
Communicate with team members to understand dependencies and urgencies
- 5
Be flexible and ready to adjust priorities based on real-time observations
Example Answers
I would first identify which quality checks are crucial for safety and compliance, ensuring those are done before others. Next, I would allocate time estimates for each task and proceed with grouping similar tasks to complete them more efficiently. Regular communication with team members would also help adjust any priorities as needed.
What would you do if you received negative feedback from a client regarding product quality? How would you address their concerns?
How to Answer
- 1
Acknowledge the client's concerns without being defensive
- 2
Gather all relevant information about the issue reported
- 3
Communicate with your team to identify the root cause of the problem
- 4
Develop an action plan to resolve the issue and prevent recurrence
- 5
Follow up with the client to ensure their concerns are addressed
Example Answers
I would start by acknowledging the client’s feedback and expressing my commitment to resolving the issue. Next, I would gather detailed information about the defect and then consult with my team to determine its cause. After that, I would create a plan to address the issue and communicate this back to the client, ensuring they feel valued and heard.
If you noticed a lack of quality awareness among new employees, what strategies would you implement to improve their understanding?
How to Answer
- 1
Conduct an engaging orientation session focused on quality principles
- 2
Implement a mentorship program pairing new employees with experienced staff
- 3
Create visually appealing quality reminders and guidelines in work areas
- 4
Organize interactive workshops that involve hands-on quality control exercises
- 5
Encourage regular team discussions where quality concerns can be voiced and addressed
Example Answers
I would start with an interactive orientation session where I introduce basic quality concepts and their importance to our processes. Then, I would implement a mentorship program to have experienced staff guide new employees in real scenarios.
Suppose you find trends in quality reports indicating potential problems down the line. What actions would you take?
How to Answer
- 1
Analyze the data to identify specific issues and root causes.
- 2
Collaborate with relevant teams to discuss findings and potential impacts.
- 3
Develop a corrective action plan to address the identified trends.
- 4
Implement monitoring procedures to track the effects of changes.
- 5
Report findings and recommendations to management for further support.
Example Answers
I would first analyze the quality reports to pinpoint the exact trends and underlying causes. Then, I would bring together key stakeholders to discuss these findings and assess potential impacts on production. Together, we would create a corrective action plan and implement monitoring to ensure the effectiveness of our solutions.
If you were uncertain about how to proceed with a quality issue, what steps would you take to escalate or address the situation?
How to Answer
- 1
Review available documentation and quality standards related to the issue
- 2
Consult with team members for insights or similar past experiences
- 3
Identify the appropriate supervisor or manager to approach for further assistance
- 4
Gather relevant data and evidence to support the issue before escalation
- 5
Stay calm and communicate clearly to ensure the issue is understood
Example Answers
First, I would review the related quality standards and any documentation. I would then consult with my colleagues for their insights. If I'm still unsure, I would gather the relevant data and escalate the issue to my supervisor with all the necessary details.
How would you approach working with manufacturing teams to ensure they understand and meet quality requirements?
How to Answer
- 1
Establish clear communication channels with the manufacturing teams
- 2
Provide training sessions focused on quality standards and procedures
- 3
Utilize visual aids and documentation to simplify quality requirements
- 4
Encourage feedback from the teams to improve quality processes
- 5
Conduct regular audits and follow-ups to ensure compliance with quality metrics
Example Answers
I would start by organizing training sessions to explain quality standards and encourage open communication. Visual aids, like charts and checklists, can help simplify complex requirements. I would also seek regular input from the manufacturing teams to adapt our processes as needed.
Imagine you predict a recurring defect pattern in products. How would you approach preventing it?
How to Answer
- 1
Identify the root cause of the defect by analyzing data from production.
- 2
Collaborate with cross-functional teams to develop corrective actions.
- 3
Implement process changes or design modifications to eliminate the cause.
- 4
Establish a monitoring system to detect early signs of the defect.
- 5
Conduct regular training for staff on quality standards and procedures.
Example Answers
I would start by analyzing production data to identify patterns and root causes. Then, I would work with engineering and production teams to design solutions, such as modifying processes. Finally, I'd set up a monitoring system to catch any early signs of the defect.
How would you incorporate continuous improvement practices in the everyday functions of a quality department?
How to Answer
- 1
Establish regular team meetings to discuss quality metrics and areas for improvement
- 2
Implement a system for collecting and analyzing feedback from production teams
- 3
Utilize tools like Six Sigma or Lean to identify waste and optimize processes
- 4
Encourage a culture of accountability where team members take ownership of quality issues
- 5
Set measurable goals for quality improvements and track progress over time
Example Answers
I would start by holding weekly meetings to review quality metrics. This way, the team can share insights on what’s working and what isn’t, fostering a collaborative environment focused on improvement.
Don't Just Read Quality Technician Questions - Practice Answering Them!
Reading helps, but actual practice is what gets you hired. Our AI feedback system helps you improve your Quality Technician interview answers in real-time.
Personalized feedback
Unlimited practice
Used by hundreds of successful candidates
Quality Technician Position Details
Salary Information
Recommended Job Boards
CareerBuilder
www.careerbuilder.com/jobs/quality-technicianZipRecruiter
www.ziprecruiter.com/Jobs/Quality-TechnicianThese job boards are ranked by relevance for this position.
Related Positions
Ace Your Next Interview!
Practice with AI feedback & get hired faster
Personalized feedback
Used by hundreds of successful candidates
Ace Your Next Interview!
Practice with AI feedback & get hired faster
Personalized feedback
Used by hundreds of successful candidates