Top 33 Steamer-Blocker Interview Questions and Answers [Updated 2025]
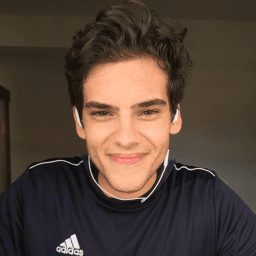
Andre Mendes
•
March 30, 2025
Preparing for a Steamer-Blocker interview can be daunting, but we've got you covered with the most common interview questions for this role. In this post, you'll find example answers and insightful tips to help you respond effectively and confidently. Whether you're a seasoned professional or new to the field, our guide will equip you with the tools you need to impress your interviewers and land the job.
Download Steamer-Blocker Interview Questions in PDF
To make your preparation even more convenient, we've compiled all these top Steamer-Blockerinterview questions and answers into a handy PDF.
Click the button below to download the PDF and have easy access to these essential questions anytime, anywhere:
List of Steamer-Blocker Interview Questions
Behavioral Interview Questions
Can you describe a time when you worked closely with a team to solve a difficult problem in the steaming process?
How to Answer
- 1
Identify a specific problem you faced with the steaming process.
- 2
Highlight your role in the team and your contributions.
- 3
Explain the steps your team took to address the problem.
- 4
Share the outcome or results of your team's efforts.
- 5
Reflect on the lessons learned and how it improved future processes.
Example Answers
In my last project, our team faced an issue with inconsistent steaming results affecting quality. I led a brainstorming session to identify potential causes, we discovered a temperature control problem. By adjusting the equipment settings and implementing a new monitoring system, we achieved consistent results. This not only solved the immediate problem but also improved our steaming process for subsequent projects.
Tell us about a situation where you had to adapt to changes in a production schedule. How did you handle it?
How to Answer
- 1
Identify a specific change in the production schedule you experienced.
- 2
Explain your initial reaction and the steps you took to adapt.
- 3
Highlight any collaboration with team members or stakeholders.
- 4
Discuss the outcome and what you learned from the experience.
- 5
Emphasize your ability to remain flexible and proactive under pressure.
Example Answers
In my last project, the production schedule was moved up by two weeks. I quickly organized a team meeting to reallocate tasks and prioritize key deliverables. We communicated with all stakeholders to ensure alignment. As a result, we met the new deadline and learned the importance of flexibility.
Don't Just Read Steamer-Blocker Questions - Practice Answering Them!
Reading helps, but actual practice is what gets you hired. Our AI feedback system helps you improve your Steamer-Blocker interview answers in real-time.
Personalized feedback
Unlimited practice
Used by hundreds of successful candidates
Give an example of a conflict you had with a coworker regarding the steaming process. How did you resolve it?
How to Answer
- 1
Identify a specific conflict related to the steaming process.
- 2
Describe your approach to addressing the conflict directly and respectfully.
- 3
Highlight any compromises or team collaboration to resolve the issue.
- 4
Emphasize positive outcomes or lessons learned from the experience.
- 5
Keep the focus on professional communication and problem-solving.],
- 6
sampleAnswers
Example Answers
In my last position, a coworker and I disagreed on the temperature settings for the steamer. I thought we should use a lower setting for delicate items, but they preferred higher for efficiency. I suggested we test both settings on a few samples. After some trials, we found the lower temperature produced better results, which we both agreed on. This not only resolved our conflict but also improved our steaming process.
Describe a time when you implemented a new technique or process in steam blocking. What was the outcome?
How to Answer
- 1
Choose a specific technique or process you implemented.
- 2
Explain the reason for the change and the problem it addressed.
- 3
Describe the steps you took to implement it.
- 4
Include measurable outcomes to demonstrate success.
- 5
Reflect on any challenges faced and how you overcame them.
Example Answers
In my previous role, I introduced a new pressure monitoring system for steam blocking that improved efficiency. I analyzed the existing methods and found that we consistently faced pressure drops. By implementing the new system, we reduced pressure loss by 20% within three months, resulting in smoother operations and fewer downtime incidents.
Have you ever led a team in a steaming project? How did you motivate your team to meet the goals?
How to Answer
- 1
Identify a specific steaming project you led.
- 2
Briefly describe your leadership style and approach.
- 3
Discuss how you set clear goals and expectations.
- 4
Mention specific motivational techniques you used.
- 5
Share the outcome and what your team achieved.
Example Answers
In my previous role, I led a steaming project to develop a new feature for our platform. I motivated my team by clearly communicating our project goals and deadlines. I implemented weekly check-ins to celebrate small wins and keep everyone engaged. As a result, we not only met our deadlines but exceeded our performance metrics by 20%.
Can you tell me about a time you received constructive feedback about your steaming processes? How did you respond?
How to Answer
- 1
Choose a specific example of feedback you received.
- 2
Explain the context and the nature of the feedback clearly.
- 3
Detail how you implemented the feedback and what changes you made.
- 4
Discuss the positive outcome that resulted from your changes.
- 5
Reflect on what you learned from the experience.
Example Answers
In a previous project, my manager noted that my steaming process took longer than needed. I analyzed the steps I was taking and realized I wasn't optimizing my setup. After adjusting my prep time and equipment layout, I reduced the steaming time by 20%. This not only improved efficiency, but also allowed us to meet project deadlines more comfortably.
Describe a time when you had to learn new steaming techniques quickly. How did you approach it?
How to Answer
- 1
Identify a specific situation where rapid learning was necessary
- 2
Explain the techniques you needed to learn and why they were important
- 3
Describe the steps you took to learn the techniques, such as researching or practicing
- 4
Mention any resources you used, like tutorials or seeking help from colleagues
- 5
Share the outcome and what you learned from the experience
Example Answers
In my previous job, I had to learn new steaming techniques for fabric care in just a week. I started by watching online tutorials and taking notes on the key methods. I then practiced during my shifts with guidance from a senior colleague. This approach helped me master the techniques quickly, and I was able to improve our team's efficiency in handling delicate fabrics.
Describe how you set and achieve your personal and professional goals in your role.
How to Answer
- 1
Start by identifying specific goals related to your role.
- 2
Explain your process for setting realistic and measurable goals.
- 3
Discuss how you track your progress and adjust your goals as needed.
- 4
Provide examples of goals you've successfully achieved.
- 5
Emphasize the importance of feedback and learning in goal setting.
Example Answers
In my role, I set specific goals like improving customer satisfaction metrics by 20%. I break this down into actionable steps, such as training sessions and regular feedback loops. I track my progress weekly and adjust my strategies based on what works best.
Don't Just Read Steamer-Blocker Questions - Practice Answering Them!
Reading helps, but actual practice is what gets you hired. Our AI feedback system helps you improve your Steamer-Blocker interview answers in real-time.
Personalized feedback
Unlimited practice
Used by hundreds of successful candidates
How do you stay motivated on repetitive tasks associated with steam blocking?
How to Answer
- 1
Set small, achievable goals to break the monotony.
- 2
Use a timer to focus on tasks in short bursts with breaks.
- 3
Find ways to gamify your tasks to make them more engaging.
- 4
Switch up your environment or workspace to maintain interest.
- 5
Remind yourself of the larger impact and purpose of your work.
Example Answers
I break down the tasks into smaller goals, focusing on completing one at a time. This approach keeps me motivated as I can celebrate small wins.
Technical Interview Questions
What types of steam blocking equipment are you familiar with, and what maintenance practices do you follow?
How to Answer
- 1
List specific types of steam blocking equipment you have worked with, like valves or traps.
- 2
Mention maintenance tasks such as regular inspections or cleaning schedules.
- 3
Include any experience with troubleshooting common issues in steam blocking.
- 4
Highlight the importance of safety protocols in maintenance practices.
- 5
Be prepared to discuss how you document maintenance activities.
Example Answers
I am familiar with steam traps and isolation valves. My maintenance practice includes monthly inspections and cleaning of traps to ensure they function properly. I also document any repairs and follow safety protocols during all maintenance work.
Can you explain the steaming process and how it affects the final product quality in blocking?
How to Answer
- 1
Define steaming in the context of blocking clearly.
- 2
Explain the purpose of steaming in loosening the fibers.
- 3
Discuss how steaming can eliminate wrinkles and set the shape.
- 4
Mention the impact of moisture on fabric structure and finish.
- 5
Conclude with the importance of quality control in the steaming process.
Example Answers
Steaming is a process where steam is applied to fabrics during blocking to relax fibers. This helps eliminate wrinkles and allows the fabric to hold its intended shape, thereby improving the final product quality.
Don't Just Read Steamer-Blocker Questions - Practice Answering Them!
Reading helps, but actual practice is what gets you hired. Our AI feedback system helps you improve your Steamer-Blocker interview answers in real-time.
Personalized feedback
Unlimited practice
Used by hundreds of successful candidates
What strategies do you use to improve efficiency in the steaming and blocking process?
How to Answer
- 1
Assess the workflow and identify bottlenecks.
- 2
Implement a standardized steaming method for consistency.
- 3
Utilize appropriate equipment and tools to save time.
- 4
Train team members to ensure everyone is skilled and efficient.
- 5
Monitor results and adjust procedures based on feedback.
Example Answers
I analyze the steaming and blocking workflow to identify bottlenecks, then implement standardized methods to enhance efficiency. Training the team ensures everyone works at peak performance.
How do you troubleshoot common steam blocking issues, such as uneven steam distribution?
How to Answer
- 1
Check the steam valve for blockages and ensure it is functioning correctly
- 2
Inspect the steam distribution system for leaks or bends that could obstruct flow
- 3
Verify that the steam pressure is at the recommended level for even distribution
- 4
Clean and maintain steam traps to prevent buildup and ensure smooth operation
- 5
Conduct a visual inspection of steam coils and pipes for signs of corrosion or damage
Example Answers
To troubleshoot uneven steam distribution, I first check the steam valve for any blockages and confirm it's operating correctly. Then, I inspect the distribution system for any leaks or bends that could be causing the issue. It's also important to ensure the steam pressure is set to the recommended levels.
What methods do you use to ensure the quality of the items post-steaming?
How to Answer
- 1
Inspect each item for wrinkles and marks after steaming
- 2
Test fabric durability and appearance through touch and visual checks
- 3
Implement consistency checks with a checklist for common quality issues
- 4
Have a second set of eyes review items to catch any overlooked problems
- 5
Document any issues and establish a feedback loop for continuous improvement
Example Answers
I inspect each item thoroughly for any wrinkles or marks and ensure that it meets our quality standards. I also use a checklist to verify durability and visual appeal.
What safety regulations are most relevant to the steamer-blocker role, and how do you ensure compliance?
How to Answer
- 1
Identify key safety regulations relevant to steam operation and blocking equipment.
- 2
Explain how you stay updated with regulatory changes through training or resources.
- 3
Describe your process for conducting safety checks and audits regularly.
- 4
Highlight examples of how you implement safety protocols in daily operations.
- 5
Mention any certifications or training related to safety standards in your field.
Example Answers
In my role, I focus on OSHA regulations and industry standards related to steam operations. I stay updated by attending safety workshops and actively participating in safety meetings. I conduct regular safety audits to ensure compliance and train the team on proper blocking procedures, which has reduced incidents significantly.
How does the type of fabric affect your steaming techniques and times?
How to Answer
- 1
Identify different fabric types and their characteristics.
- 2
Explain how delicate fabrics need lower temperatures and shorter steaming times.
- 3
Mention that heavier fabrics may require more heat and longer steaming.
- 4
Provide examples of fabrics like silk, cotton, and polyester.
- 5
Discuss the importance of testing on a hidden area first.
Example Answers
For delicate fabrics like silk, I use a lower steaming temperature and limit the time to avoid damage. Heavy fabrics, such as denim, require a higher heat and more time to ensure all wrinkles are removed.
What steps do you follow when diagnosing issues with steam application?
How to Answer
- 1
Gather information on the issue from users or logs
- 2
Reproduce the problem in a controlled environment
- 3
Check for known issues or updates in documentation
- 4
Isolate components to identify the source of the problem
- 5
Apply fixes or workarounds, then validate the solution
Example Answers
I first gather all relevant information from users and review logs to understand the issue. Then, I try to reproduce it in a controlled environment. After isolating components, I check for any known issues. Finally, I apply a fix and ensure the problem is resolved with testing.
How do you determine the optimal steaming time for different types of fabrics?
How to Answer
- 1
Identify the type of fabric and its care instructions
- 2
Test a small area to see how it reacts to steam
- 3
Consider the thickness and weave of the fabric
- 4
Adjust steaming time based on the fabric's response
- 5
Use a fabric steaming guide as a reference for different materials
Example Answers
For delicate fabrics like silk, I start with 10 to 15 seconds of steam, checking for wilting or water spots. If the fabric takes the steam well, I proceed with caution, keeping it quick.
What is your experience with routine maintenance on steam blocking equipment?
How to Answer
- 1
Highlight specific types of steam blocking equipment you have worked with
- 2
Explain the maintenance tasks you performed regularly
- 3
Mention any relevant safety protocols you followed
- 4
Include any troubleshooting or repair experiences
- 5
Emphasize your attention to detail and problem-solving skills
Example Answers
In my previous role, I worked with steam block valves, performing weekly inspections to check for leaks and pressure issues. I followed all safety protocols and documented any irregularities diligently.
Don't Just Read Steamer-Blocker Questions - Practice Answering Them!
Reading helps, but actual practice is what gets you hired. Our AI feedback system helps you improve your Steamer-Blocker interview answers in real-time.
Personalized feedback
Unlimited practice
Used by hundreds of successful candidates
How do you use data or feedback to improve ratings in your steam blocking operations?
How to Answer
- 1
Analyze user feedback regularly to identify common issues and areas for improvement.
- 2
Track key performance metrics like response times and user engagement levels.
- 3
Test changes based on data insights and gather feedback post-implementation.
- 4
Prioritize improvements that directly impact user experience and satisfaction ratings.
- 5
Communicate your findings and adjustments with your team to ensure alignment.
Example Answers
I regularly review user feedback to pinpoint common pain points. For instance, if many users report delays, I analyze response times and look for bottlenecks. After implementing a faster response protocol, I follow up with users to see if their experience has improved.
Situational Interview Questions
If you notice that the steam is not reaching the required temperature during a batch, what steps would you take?
How to Answer
- 1
Check the steam pressure gauges to verify if they are within normal ranges.
- 2
Inspect the steam system for any visible leaks or blockages.
- 3
Adjust the steam supply valves if they are not open sufficiently.
- 4
Verify that the equipment settings are correctly configured for the batch process.
- 5
Consult with the operations team if the issue persists after initial checks.
Example Answers
I would first check the steam pressure gauges to confirm they are at the right levels. If not, I would inspect for leaks or blockages. Then, I would adjust the steam valves and ensure all equipment settings are correct.
If you are faced with multiple steaming requests from different departments, how would you prioritize them?
How to Answer
- 1
Assess the urgency of each request based on deadlines.
- 2
Consider the impact of each steaming on overall business goals.
- 3
Communicate with department heads to clarify priorities.
- 4
Use a scoring system to evaluate requests objectively.
- 5
Stay flexible and be prepared to adjust priorities as needed.
Example Answers
I would first evaluate the deadlines for each request to understand which steaming is most urgent. Then, I would consider how each request aligns with our core business objectives. If needed, I'd reach out to relevant department heads to confirm priorities. Lastly, I would keep a flexible approach to adapt to any changes.
Don't Just Read Steamer-Blocker Questions - Practice Answering Them!
Reading helps, but actual practice is what gets you hired. Our AI feedback system helps you improve your Steamer-Blocker interview answers in real-time.
Personalized feedback
Unlimited practice
Used by hundreds of successful candidates
What would you do if you encountered a safety hazard while operating steaming equipment?
How to Answer
- 1
Immediately stop the operation of the steaming equipment.
- 2
Assess the safety hazard to understand the nature and extent.
- 3
Notify a supervisor or safety officer about the hazard right away.
- 4
Implement control measures to mitigate the hazard if trained to do so.
- 5
Document the incident and your response for future reference.
Example Answers
If I encountered a safety hazard while operating steaming equipment, I would immediately stop the operation to prevent any accidents. Then, I would assess the hazard and notify my supervisor to ensure proper action is taken. If I could safely address it, I would implement controls, and I would document everything afterward.
Imagine you have a deadline approaching and an unexpected equipment failure occurs. How would you handle this situation?
How to Answer
- 1
Quickly assess the situation to understand the impact of the equipment failure.
- 2
Communicate the issue to your team and seek input on potential solutions.
- 3
Prioritize tasks and create a backup plan to meet the deadline.
- 4
Consider reaching out to maintenance or technical support for assistance.
- 5
Stay calm and maintain a solution-oriented mindset throughout the process.
Example Answers
First, I would assess what specific equipment has failed and how that impacts our deadline. I would then inform my team about the situation and collectively brainstorm solutions. If possible, I would delegate some tasks to keep progress ongoing while contacting tech support for immediate repair options.
If a client is dissatisfied with the steaming results, how would you approach the situation to resolve their concerns?
How to Answer
- 1
Listen actively to the client's concerns without interruptions
- 2
Acknowledge the issue and express understanding of their dissatisfaction
- 3
Ask specific questions to identify the root cause of the dissatisfaction
- 4
Offer actionable solutions or alternatives to address their concerns
- 5
Follow up after implementing changes to ensure satisfaction
Example Answers
I would first listen to the client's concerns fully and acknowledge their feelings. Then, I would ask what specific aspects of the steaming they were unhappy with to better understand the issue. Based on their feedback, I would propose possible adjustments, such as changing the steaming duration or temperature. Finally, I would check back with them to ensure they are satisfied with the new approach.
How would you handle a situation where a team member is consistently not following safety protocols?
How to Answer
- 1
Address the issue directly with the team member in a private setting
- 2
Clarify the importance of safety protocols for everyone’s wellbeing
- 3
Listen to their perspective and understand any underlying issues
- 4
Encourage a team culture that prioritizes safety and accountability
- 5
Follow up with management if the behavior continues and impacts safety
Example Answers
I would first speak privately with the team member to address the specific safety protocols they are ignoring. I would explain how vital these protocols are for everyone's safety and ask if there are any reasons for their non-compliance. After understanding their perspective, I would encourage them to adhere to the rules and suggest solutions if they’re facing challenges.
If you were tasked with training a new employee on steam blocking, what key points would you emphasize?
How to Answer
- 1
Explain the basic concept of steam blocking and its importance in the workflow.
- 2
Highlight the common tools and methods used in steam blocking.
- 3
Discuss potential challenges and how to overcome them.
- 4
Demonstrate the process through a practical example or scenario.
- 5
Emphasize the importance of communication and teamwork in steam blocking activities.
Example Answers
First, I would explain that steam blocking is about managing workflow efficiently by preventing bottlenecks. Then, I would introduce the specific tools we use, such as blocking software or manual methods. I'd highlight common pitfalls like lack of communication and share a scenario where teamwork helped resolve a blocking issue.
If you could change one aspect of the current steaming process, what would it be and why?
How to Answer
- 1
Identify a specific aspect of the steaming process that has room for improvement.
- 2
Use data or feedback to support your suggestion.
- 3
Explain how the change would benefit the team or overall performance.
- 4
Be clear and concise in your explanation.
- 5
Show enthusiasm for enhancing efficiency or user experience.
Example Answers
I would streamline the pre-steaming setup by implementing a checklist system. This would reduce time spent preparing by ensuring all equipment is ready and accounted for, thus boosting overall productivity.
What would you do if you were given a task that you felt was outside your expertise regarding steaming?
How to Answer
- 1
Acknowledge the task and its requirements
- 2
Assess specific areas where you lack expertise
- 3
Seek help from colleagues or mentors
- 4
Research thoroughly to gain necessary knowledge
- 5
Communicate your progress and ask for feedback
Example Answers
I would first evaluate what specific aspects of steaming I am unsure about. Then, I would reach out to a more experienced colleague for guidance and use online resources to fill in my knowledge gaps before starting the task.
How would you approach creating a more sustainable steaming process while maintaining quality?
How to Answer
- 1
Assess current steaming process for energy and water usage
- 2
Research alternative materials or equipment that enhance sustainability
- 3
Implement a training program for staff on sustainable practices
- 4
Monitor quality metrics to ensure standards are maintained
- 5
Gather feedback from team on improvements and adjustments
Example Answers
I would start by analyzing the existing steaming process to identify areas of high energy and water consumption. Then, I would explore eco-friendly steaming equipment that preserves quality, such as energy-efficient steamers. Additionally, I believe in training the team on sustainable practices and regularly reviewing quality metrics to ensure we meet our standards.
Don't Just Read Steamer-Blocker Questions - Practice Answering Them!
Reading helps, but actual practice is what gets you hired. Our AI feedback system helps you improve your Steamer-Blocker interview answers in real-time.
Personalized feedback
Unlimited practice
Used by hundreds of successful candidates
What strategies would you implement to resolve a disagreement about steaming methods within your team?
How to Answer
- 1
Encourage open communication to express differing viewpoints.
- 2
Facilitate a meeting focused on understanding each method's pros and cons.
- 3
Use evidence or data to support the effectiveness of each steaming method.
- 4
Seek external input from experienced professionals or resources.
- 5
Aim for a consensus or compromise that incorporates valuable elements from each method.
Example Answers
I would start by encouraging team members to openly share their opinions and concerns regarding the steaming methods. Then, I would organize a meeting to discuss the pros and cons of each method based on data or past experiences.
Steamer-Blocker Position Details
Related Positions
- Garment Steamer
- Blocker
- Hand Blocker
- Deblocker
- Soot Blower
- Strainer
- Lens Blocker
- Sterilizer
- Stemmer
- Slip Sheeter
Similar positions you might be interested in.
Ace Your Next Interview!
Practice with AI feedback & get hired faster
Personalized feedback
Used by hundreds of successful candidates
Ace Your Next Interview!
Practice with AI feedback & get hired faster
Personalized feedback
Used by hundreds of successful candidates