Top 30 Carbider Interview Questions and Answers [Updated 2025]
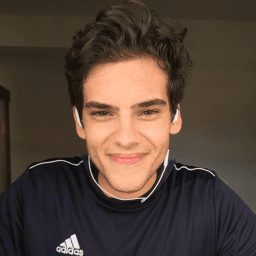
Andre Mendes
•
March 30, 2025
Preparing for a Carbider interview? You've come to the right place! This blog post compiles the most common interview questions for the Carbider role, complete with example answers and expert tips to help you respond effectively. Whether you're a seasoned professional or new to the field, our insights will boost your confidence and readiness for your upcoming interview. Dive in to master the art of interview success!
Download Carbider Interview Questions in PDF
To make your preparation even more convenient, we've compiled all these top Carbiderinterview questions and answers into a handy PDF.
Click the button below to download the PDF and have easy access to these essential questions anytime, anywhere:
List of Carbider Interview Questions
Behavioral Interview Questions
Can you describe a time when you faced a significant challenge in carbide production and how you overcame it?
How to Answer
- 1
Identify a specific challenge related to carbide production.
- 2
Explain the impact of the challenge on production or quality.
- 3
Describe the steps you took to solve the issue.
- 4
Highlight any collaboration with team members or departments.
- 5
Conclude with the positive outcomes of your actions.
Example Answers
In my previous role, we faced a significant challenge with tool wear rates in carbide cutting tools. This was impacting our production efficiency and quality. I organized a team meeting to analyze the wear patterns, and we discovered that our coolant mix was suboptimal. We adjusted the coolant formulation, ran tests, and saw a 25% reduction in wear rates, which improved our production efficiency significantly.
Tell us about a time you worked on a team to improve the carbide manufacturing process. What was your role?
How to Answer
- 1
Describe the specific team project you were involved in
- 2
Explain your role and contributions clearly
- 3
Highlight the outcome or improvement made
- 4
Include metrics or data if possible to quantify success
- 5
Reflect on what you learned from the experience
Example Answers
In my previous role, I was part of a team that worked to reduce defects in our carbide tools. My role was to analyze the production data and identify patterns. By implementing a new quality control approach, we reduced defects by 20% over three months.
Don't Just Read Carbider Questions - Practice Answering Them!
Reading helps, but actual practice is what gets you hired. Our AI feedback system helps you improve your Carbider interview answers in real-time.
Personalized feedback
Unlimited practice
Used by hundreds of successful candidates
Describe a situation where you had to quickly adapt to a change in carbide processing techniques. How did you handle it?
How to Answer
- 1
Start with a specific example of when the change occurred.
- 2
Explain the impact of the change on your work or team.
- 3
Detail the steps you took to adapt, including any learning or training.
- 4
Highlight a positive outcome resulting from your adaptation.
- 5
Conclude with what you learned and how it improved your skills.
Example Answers
In my previous role, we switched to a new carbide grinding technique. I quickly learned the new process through online resources and hands-on training. By collaborating with my team, we implemented the changes and saw a 15% increase in efficiency. This experience taught me the importance of flexibility and continuous learning.
Can you give an example of how you prioritized safety in a past project involving carbide tools?
How to Answer
- 1
Choose a specific project where safety was a key concern.
- 2
Explain the safety procedures you implemented.
- 3
Detail any training or equipment used to enhance safety.
- 4
Discuss the outcome of your safety measures.
- 5
Keep your answer focused and relevant to carbide tools.
Example Answers
In a project involving carbide cutting tools, I ensured safety by implementing a rigorous PPE protocol. We provided all team members with proper gloves, goggles, and masks, and conducted a training session on safe tool handling. As a result, we had zero accidents during the project.
Describe a time when you took the initiative to improve a process in the carbide manufacturing line.
How to Answer
- 1
Select a specific instance where you identified an inefficiency.
- 2
Explain the steps you took to analyze and implement changes.
- 3
Highlight the positive outcome or metrics that improved.
- 4
Be clear about your role and how you influenced the team.
- 5
Use a STAR format: Situation, Task, Action, Result.
Example Answers
In my previous role, I noticed our carbide grinding process was slower than expected. I analyzed the workflow and identified that we could reduce downtime by reorganizing the tool storage nearby. After implementing the new layout, we reduced grinding time by 15%, leading to an increase in overall production.
Can you provide an example of how you effectively communicated complex technical information to non-technical team members?
How to Answer
- 1
Identify a specific situation where communication was key.
- 2
Use simple language and avoid jargon to explain the technical terms.
- 3
Highlight the method you used, such as visuals or analogies.
- 4
Emphasize the positive outcome of the communication.
- 5
Mention any feedback received from team members.
Example Answers
In a project about data migration, I created a simple flowchart to illustrate the process. I explained each step using everyday language, which helped the marketing team understand our data needs. They appreciated the clarity and could provide valuable insights.
Have you ever mentored someone in the carbide field? What approach did you take to support their development?
How to Answer
- 1
Highlight a specific mentoring experience
- 2
Describe the mentee's goals and challenges
- 3
Explain the methods you used to support them
- 4
Share a positive outcome or success story
- 5
Reflect on what you learned as a mentor
Example Answers
I mentored a junior engineer who was new to carbide applications. I first identified his goal to improve his machining techniques. I provided him with resources, conducted weekly check-ins, and arranged hands-on practice sessions. As a result, he became more confident and improved his production efficiency by 20%.
Tell me about a time when you received critical feedback. How did you respond?
How to Answer
- 1
Choose a specific example that had a significant impact.
- 2
Explain the feedback clearly and what it meant to you.
- 3
Describe your initial reaction honestly but positively.
- 4
Detail the steps you took to address the feedback.
- 5
Share the outcome and what you learned from the experience.
Example Answers
In my last job, my manager criticized my presentation style. At first, I felt defensive, but I took notes and realized I could improve. I practiced more and sought feedback from colleagues. My next presentation received much better reviews, and I learned the importance of adapting my style to the audience.
Don't Just Read Carbider Questions - Practice Answering Them!
Reading helps, but actual practice is what gets you hired. Our AI feedback system helps you improve your Carbider interview answers in real-time.
Personalized feedback
Unlimited practice
Used by hundreds of successful candidates
Technical Interview Questions
What types of materials do you consider essential in carbide manufacturing?
How to Answer
- 1
Highlight key materials such as tungsten, cobalt, and titanium carbide.
- 2
Discuss the importance of material purity and quality in production.
- 3
Mention the role of binders and additives in enhancing tool performance.
- 4
Emphasize the significance of selecting materials based on application needs.
- 5
Be prepared to explain how different materials affect tool durability and functionality.
Example Answers
In carbide manufacturing, essential materials include tungsten and cobalt, as they provide toughness and wear resistance. The purity of these materials is crucial for high-quality end products.
Can you explain the step-by-step process of producing carbide tools?
How to Answer
- 1
Start with the selection of raw materials, focusing on tungsten carbide and cobalt.
- 2
Explain the powder mixing process, ensuring even distribution of the components.
- 3
Describe the pressing process where the mixed powder is shaped under high pressure.
- 4
Outline the sintering process, where the pressed pieces are heated to bond them without melting.
- 5
Finish with quality inspection and surface treatment to achieve the desired specifications.
Example Answers
The process begins with selecting tungsten carbide and cobalt as the raw materials. Next, the two powders are mixed to ensure consistency. After that, the mixture is pressed into a shape under high pressure. Then, the shaped material undergoes sintering at high temperatures to form a solid piece. Finally, each tool is inspected for quality and may receive additional surface treatments.
Don't Just Read Carbider Questions - Practice Answering Them!
Reading helps, but actual practice is what gets you hired. Our AI feedback system helps you improve your Carbider interview answers in real-time.
Personalized feedback
Unlimited practice
Used by hundreds of successful candidates
What equipment and machinery are you most familiar with in carbide production?
How to Answer
- 1
Identify the specific machines you have used in carbide production.
- 2
Mention any safety protocols you follow when operating the equipment.
- 3
Explain how you maintain or troubleshoot the machinery.
- 4
If applicable, talk about the types of carbide produced using the machines.
- 5
Conclude with any relevant certifications or training you have received.
Example Answers
I am most familiar with the high-pressure press used for forming tungsten carbide. I always follow strict safety protocols, and I have experience troubleshooting minor issues with the hydraulic system. I also have training in CNC operation for precision machining of carbide products.
How do you ensure the quality of carbide products during the manufacturing process?
How to Answer
- 1
Implement strict raw material checks before production
- 2
Utilize automated systems for precision measurements
- 3
Conduct regular training for operators on quality standards
- 4
Establish a feedback loop for continuous improvement
- 5
Perform thorough inspections at multiple stages of production
Example Answers
I ensure quality by starting with stringent checks on raw materials to verify they meet specifications. Then, I use automated measurement systems during production to maintain precision, alongside regular training sessions for operators on our quality standards.
What tests do you typically conduct to assess the durability of carbide products?
How to Answer
- 1
Mention specific tests like hardness, wear resistance, and impact testing.
- 2
Explain the significance of each test in assessing durability.
- 3
Discuss any standards or benchmarks you follow.
- 4
Highlight any tools or methods you use for testing.
- 5
Share any personal experiences or results if relevant.
Example Answers
I typically conduct hardness tests using a Rockwell hardness tester to assess the material's resistance to indentation. I also perform wear resistance tests with a pin-on-disc setup to simulate real-world conditions.
What are some common problems you have encountered with carbide tools and how have you resolved them?
How to Answer
- 1
Identify specific problems like chipping, wear, or breakage.
- 2
Describe the steps you took to troubleshoot and resolve the issues.
- 3
Include any tools or techniques you used in the resolution process.
- 4
Mention any preventative measures implemented to avoid future problems.
- 5
Keep your answers focused on practical, real-world examples.
Example Answers
One common problem I've encountered is chipping on carbide inserts during machining. I noticed it was often caused by excessive feed rates. To resolve this, I adjusted the feed and speed parameters and monitored the tool closely. I also implemented a regular inspection schedule to catch any wear early.
What industry standards do you follow for carbide manufacturing?
How to Answer
- 1
Mention specific standards like ISO 9001 for quality management.
- 2
Discuss adherence to ASTM standards relevant to carbide properties.
- 3
Include reference to safety standards such as OSHA regulations.
- 4
Talk about customer-specific standards and requirements you follow.
- 5
Emphasize continuous improvement practices based on industry benchmarks.
Example Answers
In my experience, I follow ISO 9001 for quality management to ensure consistency in carbide manufacturing. Additionally, I adhere to ASTM standards for material properties to meet customer requirements.
How do you stay updated with the latest advancements in carbide technology?
How to Answer
- 1
Follow industry-specific journals and publications for the latest research on carbide technologies
- 2
Attend relevant conferences and seminars to network and learn about new advancements
- 3
Join professional organizations or online forums focused on carbide technology for community insights
- 4
Subscribe to newsletters from leading companies in the carbide field to receive updates on innovations
- 5
Engage with thought leaders and influencers on social media platforms like LinkedIn to gain diverse perspectives
Example Answers
I stay updated by reading industry journals such as the Journal of Materials Science and attending conferences like the International Conference on Carbide Materials, which helps me learn about the latest research and applications.
How do you use data analysis in the carbide production process?
How to Answer
- 1
Identify key data points such as temperature, pressure, and raw material quality.
- 2
Explain how you analyze data to optimize production parameters.
- 3
Discuss using statistical tools for quality control and process improvement.
- 4
Mention any software or tools you utilize for data analysis in production.
- 5
Provide examples of how data analysis led to cost savings or efficiency improvements.
Example Answers
In carbide production, I analyze data on temperature and pressure during synthesis to ensure optimal conditions. By monitoring these variables, I can adjust them in real-time to improve yield.
What are the first steps you take when troubleshooting a malfunctioning carbide machine?
How to Answer
- 1
Inspect the machine for visible damage or loose components.
- 2
Check power supply and ensure all controls are functional.
- 3
Review the machine's error logs or indicators for specific issues.
- 4
Perform a basic test run to gather more data about the malfunction.
- 5
Consult the machine manual for troubleshooting steps related to the symptoms.
Example Answers
First, I visually inspect the machine for any obvious damage or loose parts. Then, I check the power supply and ensure that the controls are responding correctly. After that, I look at the error logs to pinpoint any specific errors.
Don't Just Read Carbider Questions - Practice Answering Them!
Reading helps, but actual practice is what gets you hired. Our AI feedback system helps you improve your Carbider interview answers in real-time.
Personalized feedback
Unlimited practice
Used by hundreds of successful candidates
What innovations in carbide technology do you believe will shape the future of the industry?
How to Answer
- 1
Identify recent advancements in carbide technology
- 2
Focus on applications that improve performance or efficiency
- 3
Consider sustainability aspects of new technologies
- 4
Mention potential impacts on manufacturing or costs
- 5
Stay updated with industry trends and research studies
Example Answers
One innovation shaping the carbide industry is the development of nanostructured carbide materials, which enhance wear resistance and toughness, making tools last longer and reducing costs over time.
Situational Interview Questions
Imagine you discover a defect in a batch of carbide tools right before shipping. What steps would you take?
How to Answer
- 1
Identify and document the defect clearly
- 2
Assess the root cause of the defect with the team
- 3
Communicate the issue to management and stakeholders
- 4
Implement corrective actions to prevent future defects
- 5
Decide on the next steps for the affected batch: rework, scrap, or hold for inspection
Example Answers
First, I would document the specific defect with photos and descriptions, then notify my supervisor. Next, I would gather the team to analyze the root cause and discuss preventive measures.
If you were overseeing a team that was not meeting production targets in carbide manufacturing, how would you address this?
How to Answer
- 1
Analyze the cause of the production shortfall through data review.
- 2
Engage with the team to identify obstacles they face.
- 3
Implement targeted training or process improvements based on findings.
- 4
Set clear, achievable goals with the team and monitor progress.
- 5
Encourage open communication to foster a collaborative environment.
Example Answers
I would start by analyzing production data to pinpoint where the issues are originating. Then, I would hold one-on-one meetings with team members to discuss their challenges and gather suggestions. Based on this feedback, I might introduce specific training sessions to enhance skills and optimize our processes. I would also set clear goals for improvement and regularly check in on our progress together.
Don't Just Read Carbider Questions - Practice Answering Them!
Reading helps, but actual practice is what gets you hired. Our AI feedback system helps you improve your Carbider interview answers in real-time.
Personalized feedback
Unlimited practice
Used by hundreds of successful candidates
How would you handle a disagreement between team members regarding the best methods for carbide processing?
How to Answer
- 1
Encourage open communication between team members to express their viewpoints
- 2
Facilitate a discussion that focuses on evidence and data supporting each approach
- 3
Suggest a trial period for both methods to evaluate their effectiveness
- 4
Promote a collaborative decision-making process to foster team unity
- 5
Document the decision and the rationale to refer back to in the future
Example Answers
I would first ensure that both team members have the chance to express their perspectives fully. Then, I would gather relevant data on both methods and facilitate a discussion around the findings. If needed, we could run a trial period to see which approach yields better results before making a final decision.
Suppose you need to implement a new technology in carbide production that the team is resistant to adopt. What would you do?
How to Answer
- 1
Assess the reasons for resistance by engaging with the team.
- 2
Communicate the benefits of the new technology clearly and effectively.
- 3
Provide training and support to ease the transition.
- 4
Involve team members in the implementation process for ownership.
- 5
Gather feedback and adjust the approach based on their input.
Example Answers
I would first hold a meeting to understand why the team is resistant. Then, I would explain the benefits of the new technology, addressing their concerns. By offering training sessions, I would ensure they feel comfortable with the change. Additionally, I'd invite team members to participate in the implementation, making it a collaborative process.
You notice that safety equipment is not being used correctly by some team members. How would you address this situation?
How to Answer
- 1
Observe the situation to understand why equipment is not being used correctly.
- 2
Address the issue immediately and informally with the individuals involved.
- 3
Provide a clear explanation of the importance of using safety equipment properly.
- 4
Offer assistance or additional training if needed to ensure compliance.
- 5
Follow up to ensure that proper usage has improved and reinforce positive behavior.
Example Answers
I would first observe the team to see why the safety equipment is not being used correctly. Then, I would have an informal chat with the team members involved to explain the importance of safety and how to use the equipment properly. If necessary, I'd offer further training.
How would you manage a situation where production demands have suddenly increased and your current capacity is not enough?
How to Answer
- 1
Assess the current production workflow and identify bottlenecks
- 2
Communicate with the team about the urgency and need for flexibility
- 3
Explore options for overtime or additional shifts to increase output
- 4
Consider reallocating resources or prioritizing critical orders
- 5
Seek assistance from management for potential quick hires or temporary support
Example Answers
I would first identify where the production bottlenecks are and address them. Then, I would discuss with my team to see if we can work overtime or add extra shifts to meet the demand.
You are part of a cross-functional team tasked with reducing costs in carbide production. What contributions would you make?
How to Answer
- 1
Identify specific areas in the production process where waste occurs
- 2
Suggest using more efficient equipment or technologies to increase yield
- 3
Consider collaborating with suppliers for bulk purchasing discounts
- 4
Propose a review of workforce efficiency and training needs
- 5
Analyze previous production data to pinpoint cost reduction opportunities
Example Answers
I would analyze the production line to identify any bottlenecks or wasteful practices. By improving cycle times and reducing unnecessary steps, we could cut costs significantly.
If you had to choose between maintaining a high production rate and ensuring high quality, how would you make your decision?
How to Answer
- 1
Evaluate the context: Understand the specific situation and priorities.
- 2
Prioritize quality if it impacts safety or brand reputation.
- 3
Suggest a balanced approach to optimize both aspects.
- 4
Share examples from past experiences where quality was prioritized but production was still maintained.
- 5
Communicate the long-term benefits of quality over short-term production gains.
Example Answers
In a situation where quality significantly impacts safety, I would prioritize quality over production rates. For example, in my last role, we had to delay a product release to ensure all safety standards were met, which later led to increased customer loyalty.
In a scenario where resources are limited, how would you prioritize tasks in carbide production?
How to Answer
- 1
Assess production goals and deadlines to determine critical tasks
- 2
Identify bottlenecks in the process that need immediate attention
- 3
Evaluate resource availability and allocate them to priority tasks
- 4
Communicate with the team to ensure everyone understands priorities
- 5
Be flexible and ready to adjust priorities as situations change
Example Answers
In carbide production, I would first review our deadlines to identify tasks that are critical for meeting them. Next, I would look for any immediate bottlenecks, such as equipment needing maintenance, and prioritize fixing those before moving on to less urgent tasks. I'd ensure the team is aligned on these priorities to avoid any confusion.
Carbider Position Details
Related Positions
- Rider
- Carroter
- Carbon Cleaner
- Carbonizer
- Car Builder
- Carburetor Specialist
- Car Filler
- Cribber
- Cartridge Loader
- Carrier Driver
Similar positions you might be interested in.
Ace Your Next Interview!
Practice with AI feedback & get hired faster
Personalized feedback
Used by hundreds of successful candidates
Ace Your Next Interview!
Practice with AI feedback & get hired faster
Personalized feedback
Used by hundreds of successful candidates