Top 30 Casing Trimmer Interview Questions and Answers [Updated 2025]
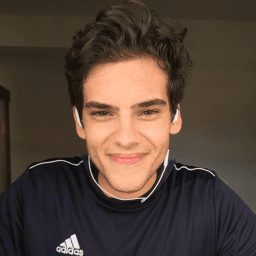
Andre Mendes
•
March 30, 2025
Navigating the interview process for a Casing Trimmer position can be challenging, but preparation is key to success. In this post, we present the most common interview questions for this specialized role, along with example answers and insightful tips on how to respond effectively. Whether you're a seasoned professional or a newcomer to the field, this guide will help you confidently tackle your next interview.
Download Casing Trimmer Interview Questions in PDF
To make your preparation even more convenient, we've compiled all these top Casing Trimmerinterview questions and answers into a handy PDF.
Click the button below to download the PDF and have easy access to these essential questions anytime, anywhere:
List of Casing Trimmer Interview Questions
Technical Interview Questions
What types of machines have you worked with for trimming casings, and how familiar are you with their operation?
How to Answer
- 1
Identify specific machinery you have experience with.
- 2
Describe your familiarity level: novice, proficient, or expert.
- 3
Mention any training you received on these machines.
- 4
Include any metrics or outcomes from your work with these machines.
- 5
Show enthusiasm for learning new technologies.
Example Answers
I have worked mainly with hydraulic casing trimmers and know them very well. I was trained for a month and successfully improved trimming precision by 30% during my last job.
How familiar are you with lean manufacturing principles and how do you apply them in your work?
How to Answer
- 1
Explain your understanding of lean principles like waste reduction and continuous improvement.
- 2
Provide specific examples of how you've implemented lean practices in your previous roles.
- 3
Mention any tools or methodologies you've used, such as Kaizen or 5S.
- 4
Discuss the impact of these practices on efficiency or quality in your work.
- 5
Show enthusiasm for applying lean principles in the Casing Trimmer position.
Example Answers
I am very familiar with lean manufacturing principles, particularly waste reduction and continuous improvement. In my previous role, I applied 5S to organize our workspace, which led to a 20% increase in efficiency and a reduction in errors.
Don't Just Read Casing Trimmer Questions - Practice Answering Them!
Reading helps, but actual practice is what gets you hired. Our AI feedback system helps you improve your Casing Trimmer interview answers in real-time.
Personalized feedback
Unlimited practice
Used by hundreds of successful candidates
What techniques do you use to ensure that each casing is trimmed to the precise specifications required?
How to Answer
- 1
Familiarize yourself with the specifications for casing trimming.
- 2
Use calibrated tools to measure the casing before and after trimming.
- 3
Perform regular maintenance on trimming equipment for accuracy.
- 4
Implement a double-check system where another technician verifies the trimming.
- 5
Document the trimming process and any adjustments made for future reference.
Example Answers
I always start by reviewing the specifications for the casing size. I use calibrated tools to measure each casing both before and after trimming to ensure accuracy. I also keep my trimming equipment well-maintained to prevent any discrepancies.
What regulations do you follow in your work to ensure compliance with industry standards?
How to Answer
- 1
Identify key industry regulations relevant to casing trimmers
- 2
Explain how you implement these regulations in your work
- 3
Provide examples of past experiences where you ensured compliance
- 4
Mention any training or certifications related to industry standards
- 5
Emphasize the importance of safety and quality in your approach
Example Answers
In my work, I follow the OSHA safety standards to ensure a safe environment. I regularly conduct safety checks and ensure that all equipment meets the regulatory requirements. For example, I completed a training on safety compliance last year that reinforced the importance of these regulations.
How do you document your work to ensure compliance and quality control?
How to Answer
- 1
Use standard templates for documentation to maintain consistency.
- 2
Log all modifications made during the trimmer process with timestamps.
- 3
Implement a checklist for quality control measures and sign off on each step.
- 4
Regularly review documentation for accuracy and compliance with regulations.
- 5
Store documents in an organized digital system for easy access and retrieval.
Example Answers
I use standard templates for documenting my work, ensuring consistency across all records. After each trimming session, I log any adjustments I made along with timestamps to create a clear history of my work. Furthermore, I follow a quality control checklist and sign off on each step to confirm compliance.
What safety measures should be taken when operating casing trimming machinery?
How to Answer
- 1
Always wear appropriate personal protective equipment such as gloves, goggles, and hard hats.
- 2
Inspect machinery for any damage or wear before use to prevent accidents.
- 3
Ensure all safety guards are in place and functioning properly.
- 4
Keep the work area clean and free from obstructions that could cause tripping.
- 5
Follow manufacturer guidelines and safety protocols during operation.
Example Answers
When operating casing trimming machinery, it is crucial to wear safety goggles and gloves. Inspect the machine for any damage before starting, ensure all safety guards are intact, and maintain a clear workspace to prevent accidents.
What measurement tools do you use to ensure accuracy in your work, and how do you calibrate them?
How to Answer
- 1
Mention specific tools such as calipers, micrometers, or gauges.
- 2
Explain the process of calibration for each tool.
- 3
Discuss how you regularly verify measurement accuracy.
- 4
Provide examples of situations where accurate measurements were crucial.
- 5
Emphasize your attention to detail and precision in your work.
Example Answers
I primarily use digital calipers and micrometers for precision measurements. I calibrate them using a calibration block, checking against known standards monthly to ensure they are within tolerance.
What types of materials have you worked with in trimming casing, and what are the challenges associated with each?
How to Answer
- 1
Identify different casing types you've trimmed such as PVC, metal, and fiberglass.
- 2
Explain specific challenges for each material, like toughness or splintering.
- 3
Mention your techniques for overcoming these challenges.
- 4
Include any tools or equipment that facilitated your work.
- 5
Be concise but descriptive to show your expertise.
Example Answers
I've worked with PVC, metal, and fiberglass casings. PVC can be brittle, leading to cracks if not handled gently. For metal, the challenge is ensuring clean cuts without burrs, which I address using specialized blades.
Describe the regular maintenance tasks you perform on casing trimming equipment.
How to Answer
- 1
Start with daily visual inspections for wear and damage
- 2
Discuss lubrication of moving parts according to the schedule
- 3
Mention checking and replacing blades or trimming accessories as needed
- 4
Include cleaning procedures to remove debris and maintain efficiency
- 5
Emphasize the importance of documenting maintenance activities
Example Answers
I perform daily visual inspections to check for any wear or damage on the casing trimmer. I also ensure that the moving parts are lubricated regularly, and I replace blades whenever they show signs of dulling. Additionally, I clean the machine after each use to prevent buildup of debris and document all maintenance tasks in a log.
What is the importance of precision in casing trimming, and how do you ensure it?
How to Answer
- 1
Emphasize the role of precision in preventing leaks and maintaining structural integrity.
- 2
Discuss the consequences of imprecision like increased rework or failure.
- 3
Explain your methods for ensuring precision, such as using calibrated tools and following strict procedures.
- 4
Highlight the importance of training and practice in achieving precise results.
- 5
Mention the use of checklists or quality control measures to verify accuracy.
Example Answers
Precision in casing trimming is critical to prevent leaks and ensure the integrity of the final product. I ensure precision by regularly calibrating my tools, following standard operating procedures, and performing routine checks on my work to confirm proper dimensions.
Don't Just Read Casing Trimmer Questions - Practice Answering Them!
Reading helps, but actual practice is what gets you hired. Our AI feedback system helps you improve your Casing Trimmer interview answers in real-time.
Personalized feedback
Unlimited practice
Used by hundreds of successful candidates
How do you troubleshoot common issues that arise with casing trimming equipment?
How to Answer
- 1
Start by identifying the specific issue the equipment is facing.
- 2
Check for clear signs of malfunction such as unusual noises or lack of power.
- 3
Inspect all connections and components for wear and tear.
- 4
Refer to the equipment manual for troubleshooting tips related to the specific problem.
- 5
Test the equipment after making adjustments to confirm that the issue is resolved.
Example Answers
I begin troubleshooting by observing the equipment for any unusual sounds or performance issues. I then check power connections and look for any visible wear and tear. If the issue persists, I consult the manual for guidance on specific troubleshooting steps.
Behavioral Interview Questions
Describe a time when your attention to detail prevented a major issue in your work.
How to Answer
- 1
Think of a specific instance where your attention to detail made a difference.
- 2
Focus on the impact of your actions on the project or team.
- 3
Use the STAR method: Situation, Task, Action, Result.
- 4
Highlight any tools or methods you used to ensure accuracy.
- 5
Conclude with what you learned from the experience.
Example Answers
In my last job, we had a critical deadline and I noticed a discrepancy in our data reports. I cross-checked the data, found an error that would have led to an incorrect decision. I corrected it, communicated with my team, and we submitted an accurate report on time, which saved the company from potential financial loss.
Give an example of how you have successfully worked as part of a team to achieve a goal in a previous job.
How to Answer
- 1
Identify a specific project where teamwork was essential.
- 2
Describe your role and contributions clearly.
- 3
Highlight the goal of the team and the outcome of your collaboration.
- 4
Use positive language to show the impact of teamwork.
- 5
Mention any skills or techniques you used to facilitate cooperation.
Example Answers
In my last job, we had a project to improve assembly line efficiency. I worked as part of a team of 5 to redesign the workflow. I contributed by organizing meetings and tracking our progress, leading to a 15% increase in output within 3 months.
Don't Just Read Casing Trimmer Questions - Practice Answering Them!
Reading helps, but actual practice is what gets you hired. Our AI feedback system helps you improve your Casing Trimmer interview answers in real-time.
Personalized feedback
Unlimited practice
Used by hundreds of successful candidates
Tell me about a challenging situation you faced on the job and how you handled it.
How to Answer
- 1
Choose a specific situation relevant to your work experience.
- 2
Describe the challenge clearly and succinctly.
- 3
Explain the steps you took to address the problem.
- 4
Highlight the positive outcome or what you learned.
- 5
Keep your answer structured and focused on your role.
Example Answers
In my previous job as a production assistant, we faced a sudden machine breakdown during peak hours. I quickly assessed the situation, coordinated with the maintenance team, and implemented a temporary manual process to keep production going. As a result, we minimized downtime by 30% and learned to establish a backup plan for future incidents.
Can you give an example of how you adapted to a significant change in your work environment or processes?
How to Answer
- 1
Think of a specific situation where change was necessary.
- 2
Describe the change clearly and how it affected your work.
- 3
Explain the steps you took to adapt to this change.
- 4
Highlight any positive outcomes or learnings from the experience.
- 5
Keep the focus on your role and contributions during the change.
Example Answers
At my previous job, the company switched to a new production software that changed our workflow. I took the initiative to learn the software quickly and organized training sessions for my team. This helped us transition smoothly and reduce downtime by 20%.
Describe a time when you had to manage multiple tasks with competing deadlines. How did you prioritize?
How to Answer
- 1
Identify a specific situation where deadlines conflicted.
- 2
Explain how you assessed the importance and urgency of each task.
- 3
Discuss the criteria you used to prioritize, like impact or due dates.
- 4
Describe the actions you took to manage your time effectively.
- 5
Reflect on the outcome and what you learned from the experience.
Example Answers
In my previous role as a production assistant, I faced a situation where I had two major projects due in the same week. I prioritized them by assessing which project had a higher impact on our client's goals and conversed with my manager for input. I created a schedule that allocated specific time blocks to each task, allowing me to finish both on time without sacrificing quality.
How do you handle stressful situations that arise in the workplace?
How to Answer
- 1
Stay calm and take deep breaths to maintain focus.
- 2
Assess the situation quickly to identify what is causing the stress.
- 3
Prioritize tasks and create a clear plan to tackle the problem.
- 4
Communicate with team members if collaboration is needed.
- 5
Reflect on past experiences to find effective coping strategies.
Example Answers
In stressful situations, I first take a moment to breathe and collect my thoughts. Then, I evaluate the issue at hand, prioritize my actions, and communicate with my team if needed to ensure we handle the pressure efficiently.
Describe a time when you had to communicate an important issue to your supervisor and how you did it.
How to Answer
- 1
Choose a specific situation where communication was critical.
- 2
Explain the issue clearly and its potential impact.
- 3
Describe how you approached your supervisor: in-person, email, etc.
- 4
Highlight your thought process and consideration for timing.
- 5
Mention the outcome and any follow-up actions you took.
Example Answers
In my previous job, I noticed a recurring defect in our casing trimmers. I gathered data and prepared a report, then scheduled a meeting with my supervisor to discuss it. I highlighted the potential impact on production efficiency and suggested a solution. My supervisor appreciated the proactive approach, and we implemented changes that reduced defects by 20%.
Have you ever identified a process that could be improved and took the initiative to make changes?
How to Answer
- 1
Identify a specific example of a process you improved.
- 2
Explain the steps you took to analyze the process.
- 3
Highlight the impact of your changes on efficiency or quality.
- 4
Mention any tools or techniques you used to implement the improvements.
- 5
Conclude with a reflection on the importance of continuous improvement.
Example Answers
In my previous role, I noticed that the inventory management process often resulted in delays. I analyzed the workflow and introduced a new software tool that streamlined tracking. This reduced our inventory errors by 25%, significantly improving our efficiency.
Situational Interview Questions
You are given a large order with a tight deadline. How would you manage your time to ensure timely completion while maintaining quality?
How to Answer
- 1
Prioritize the key tasks that need to be done first.
- 2
Break down the order into manageable parts and set mini-deadlines.
- 3
Communicate clearly with the team about expectations and progress.
- 4
Quality checks should be integrated into the workflow, not just at the end.
- 5
Stay organized with a checklist or scheduling tool to track progress.
Example Answers
I would begin by prioritizing the tasks based on urgency and complexity, creating a timeline for each section of the order. I would break the order into smaller parts, assign specific timelines for each part, and regularly check in with the team to ensure we're on track. Before completing each section, I would implement quality checks to maintain high standards.
If you have a disagreement with a coworker about the best way to perform a task, how would you handle it?
How to Answer
- 1
Listen to your coworker's perspective fully before responding.
- 2
Express your view calmly and respectfully, using facts to support it.
- 3
Seek common ground and find a solution that incorporates both ideas if possible.
- 4
Suggest involving a supervisor or a third party if the disagreement persists.
- 5
Be open to feedback and willing to compromise for the team's benefit.
Example Answers
I would first listen carefully to my coworker's viewpoint and understand their reasoning. Then, I would share my perspective, backed by relevant experience, and suggest a collaborative solution that combines our ideas.
Don't Just Read Casing Trimmer Questions - Practice Answering Them!
Reading helps, but actual practice is what gets you hired. Our AI feedback system helps you improve your Casing Trimmer interview answers in real-time.
Personalized feedback
Unlimited practice
Used by hundreds of successful candidates
You believe there is a more efficient way to trim casings with the existing equipment. How would you propose and implement this change?
How to Answer
- 1
Analyze current trimming workflow for inefficiencies
- 2
Identify specific changes using existing equipment
- 3
Communicate benefits to the team with clear data
- 4
Pilot the new method on a small scale
- 5
Gather feedback and adjust the process accordingly
Example Answers
I would first assess the current workflow to pinpoint where delays occur. After identifying inefficiencies, I would propose using a different attachment on the trimming machine to speed up the process. I would present data showing potential time savings to the team and pilot the change on a small batch to measure its effectiveness. Based on feedback, I'd refine the process before wider implementation.
If you witness a safety incident on the factory floor, what actions would you take immediately?
How to Answer
- 1
Assess the situation to ensure it's safe to approach.
- 2
Call for help or notify your supervisor immediately.
- 3
Provide assistance to the injured if qualified to do so.
- 4
Secure the area to prevent further incidents.
- 5
Document the incident as required by safety protocol.
Example Answers
I would first ensure my own safety and then immediately call for my supervisor to report the incident. If an injury has occurred and I'm trained in first aid, I would assist until help arrives. After that, I would secure the area.
If a critical piece of equipment fails during production, how would you address the issue to minimize downtime?
How to Answer
- 1
Immediately notify the maintenance team and supervisor.
- 2
Assess the extent of the equipment failure quickly.
- 3
Implement temporary measures to keep production going if possible.
- 4
Document the failure details for future analysis and prevention.
- 5
Review and adjust production schedules as necessary.
Example Answers
I would first notify the maintenance team and my supervisor to ensure the issue is being addressed. Then, I would assess the failure to understand its impact and determine if we can implement any temporary solutions. While waiting for repairs, I would document everything for future reference.
How would you assist in training a new employee who is unfamiliar with trimming equipment?
How to Answer
- 1
Begin with an overview of trimming equipment and its safety procedures
- 2
Demonstrate the use of the equipment step by step
- 3
Encourage the new employee to practice under supervision
- 4
Provide a detailed manual or checklist for reference
- 5
Schedule regular feedback sessions to address questions and progress
Example Answers
I would start by explaining the safety protocols and basic operation of the trimming equipment. Then, I would demonstrate the process while explaining each step, before allowing the new employee to try it with my supervision.
If you need information from another department to complete your task, how would you go about obtaining it?
How to Answer
- 1
Identify the specific information you need and why it's important.
- 2
Reach out to the relevant person in that department via email or direct message.
- 3
Be clear and concise in your request, explaining your task and the information needed.
- 4
Offer to provide context or feedback to encourage cooperation.
- 5
Follow up politely if you don’t receive a response within a reasonable time.
Example Answers
I would first clarify exactly what information I need from the other department. Then, I'd send a concise email to the relevant person, explaining my project and why their input is crucial. I’d also offer to discuss it further if they need more context.
Imagine you notice a batch of casings has been trimmed inaccurately. What steps would you take to address the situation?
How to Answer
- 1
Immediately stop the production to prevent further errors.
- 2
Assess the extent of the inaccuracies in the trimmed casings.
- 3
Identify the root cause of the inaccurate trimming.
- 4
Implement corrective actions and retrain staff if necessary.
- 5
Document the issue and the steps taken to resolve it.
Example Answers
First, I would stop the production line to avoid further issues. Then, I would check how many casings are affected and gather data on the trimming process. I would investigate whether it was a machine malfunction or a human error. After addressing the cause, I would retrain the team and document the incident for future reference.
Your company is investing in new trimming technology. How would you prepare for the transition?
How to Answer
- 1
Assess the current trimming processes and identify pain points.
- 2
Research the new technology's features and benefits for your operations.
- 3
Develop a training plan for staff to ensure smooth adoption.
- 4
Create a timeline for implementation with key milestones and checkpoints.
- 5
Gather feedback from team members during the transition to make necessary adjustments.
Example Answers
I would first analyze our current trimming processes to pinpoint inefficiencies. Then, I would thoroughly research the new technology to understand how it could enhance our operations. I'd form a training schedule for the team to adapt quickly and set up a timeline for the rollout, ensuring that we address any concerns along the way.
In the event of a fire or other emergency, what is your role and how do you ensure safety?
How to Answer
- 1
Prioritize safety and follow company emergency protocols
- 2
Identify your specific role in the emergency plan
- 3
Conduct regular safety drills and training
- 4
Communicate clearly with team members during emergencies
- 5
Report hazards and participate in safety improvements
Example Answers
In case of a fire, my first role is to follow the emergency protocols established by the company. I would ensure that everyone evacuates safely and quickly while I guide them to the nearest exit.
Don't Just Read Casing Trimmer Questions - Practice Answering Them!
Reading helps, but actual practice is what gets you hired. Our AI feedback system helps you improve your Casing Trimmer interview answers in real-time.
Personalized feedback
Unlimited practice
Used by hundreds of successful candidates
You receive negative feedback on your work. How do you handle it and what steps do you take to improve?
How to Answer
- 1
Listen carefully to the feedback without interrupting.
- 2
Ask clarifying questions to understand the specifics.
- 3
Reflect on the feedback and identify areas for improvement.
- 4
Create an action plan with specific steps to address the feedback.
- 5
Follow up with the person who gave feedback to show progress.
Example Answers
I listen to the feedback carefully and take notes. I ask questions to make sure I understand the points being made. Then, I think about how I can improve in those areas and create a plan to implement changes. After making adjustments, I follow up with the feedback provider to discuss my progress.
Casing Trimmer Position Details
Related Positions
- Metal Trimmer
- Trim Installer
- Cushion Maker
- Liner Installer
- Cushion Filler
- Jointer
- Truss Maker
- Plastic Fabricator
- Cable Maker
- Harnessmaker
Similar positions you might be interested in.
Ace Your Next Interview!
Practice with AI feedback & get hired faster
Personalized feedback
Used by hundreds of successful candidates
Ace Your Next Interview!
Practice with AI feedback & get hired faster
Personalized feedback
Used by hundreds of successful candidates