Top 30 Cornice Maker Interview Questions and Answers [Updated 2025]
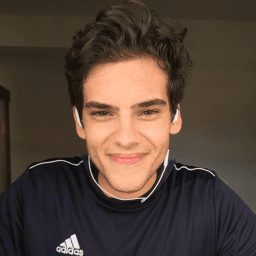
Andre Mendes
•
March 30, 2025
Preparing for a Cornice Maker interview can be daunting, but we're here to help you excel. This blog post provides a comprehensive guide to the most common interview questions for the Cornice Maker role, complete with example answers and effective answering tips. Whether you're new to the field or a seasoned professional, this article will equip you with the insights needed to impress your potential employers.
Download Cornice Maker Interview Questions in PDF
To make your preparation even more convenient, we've compiled all these top Cornice Makerinterview questions and answers into a handy PDF.
Click the button below to download the PDF and have easy access to these essential questions anytime, anywhere:
List of Cornice Maker Interview Questions
Behavioral Interview Questions
What is the most valuable lesson you have learned from a mistake made while making a cornice?
How to Answer
- 1
Identify a specific mistake from past experiences
- 2
Explain the impact of the mistake on your work
- 3
Discuss the corrective action you took
- 4
Share the lesson learned and how it improved your skills
- 5
Connect the lesson to future cornice projects
Example Answers
I once miscalculated the measurements for a cornice, resulting in a piece that didn't fit properly. This taught me the importance of double-checking measurements and using a check-list before cutting materials. Now I ensure to measure twice and confirm dimensions with colleagues to avoid errors.
Can you describe a time when you worked as part of a team to complete a cornice project? What was your role?
How to Answer
- 1
Identify a specific project where teamwork was essential.
- 2
Clearly outline your role and contributions to the project.
- 3
Mention any challenges the team faced and how you overcame them together.
- 4
Highlight teamwork skills such as communication and collaboration.
- 5
Conclude with the successful outcome of the project.
Example Answers
In my previous job, we had a tight deadline to install cornices in a renovated building. I was the lead installer, coordinating with the design team and the subcontractors. We faced time constraints, but by organizing daily briefings and delegating tasks effectively, we completed the project on time and received positive feedback from the client.
Don't Just Read Cornice Maker Questions - Practice Answering Them!
Reading helps, but actual practice is what gets you hired. Our AI feedback system helps you improve your Cornice Maker interview answers in real-time.
Personalized feedback
Unlimited practice
Used by hundreds of successful candidates
Tell me about a situation where you encountered a significant challenge while crafting a cornice. How did you handle it?
How to Answer
- 1
Identify a specific challenge you faced while crafting a cornice
- 2
Describe the steps you took to resolve the issue
- 3
Emphasize the skills you used to overcome the challenge
- 4
Talk about the outcome and what you learned from the experience
- 5
Keep your answer focused and to the point
Example Answers
Once, while crafting a cornice for a historical home, I miscalculated the measurements. To fix it, I re-evaluated the design, adjusted the dimensions, and created a new template. I used my carpentry skills to ensure precision. In the end, the client was thrilled with the final product, and I learned the importance of double-checking measurements.
Describe how you prioritize your tasks when working on multiple cornice projects with tight deadlines.
How to Answer
- 1
List out all tasks with deadlines and dependencies.
- 2
Assess the urgency and importance of each project.
- 3
Break projects into smaller tasks and set milestone deadlines.
- 4
Communicate with team members to align priorities.
- 5
Regularly review and adjust priorities based on project progress.
Example Answers
I start by listing all ongoing projects and their deadlines. Then, I rank them by urgency and importance. This helps me focus on critical tasks first, and I break them into smaller tasks to manage my time better.
Have you ever had to deal with a difficult client regarding a cornice design? What was the outcome?
How to Answer
- 1
Listen actively to the client's concerns to understand their perspective
- 2
Stay calm and professional even if the client is upset
- 3
Offer solutions or alternatives to meet the client's needs
- 4
Document the conversation for clarity and future reference
- 5
Follow up with the client after the resolution to ensure satisfaction
Example Answers
In a recent project, a client was unhappy with the proposed cornice design. I listened to their concerns carefully, and after understanding their vision, I suggested some design alterations that incorporated their ideas while adhering to my professional standards. The outcome was a design they loved, and we completed the project successfully.
Describe a time when you received constructive criticism on your work. How did you respond to it?
How to Answer
- 1
Choose a specific instance that had a clear outcome.
- 2
Explain the criticism you received and why it was important.
- 3
Describe your emotional response and how you processed it.
- 4
Detail the steps you took to improve or adjust your work.
- 5
Conclude with the positive outcomes from the experience.
Example Answers
During a project on creating custom cornices, my supervisor pointed out that my design lacked creativity. I initially felt disappointed but realized it was a chance to grow. I sought inspiration from different styles and applied those ideas, resulting in a much more innovative design that the client loved.
Have you ever suggested a new technique or process that improved your work? What was it?
How to Answer
- 1
Think of a specific time you identified an inefficiency.
- 2
Describe the technique or process you suggested clearly.
- 3
Explain the impact of your suggestion on your work or team.
- 4
Use metrics if possible to show improvement.
- 5
Keep your answer focused and relevant to cornice making.
Example Answers
In my previous job, I noticed that we were spending a lot of time measuring and cutting the cornices. I suggested using a laser level for more accurate measurements, which reduced our cutting errors by 30%. This not only saved time but also improved the overall quality of our installations.
Can you describe an experience where you collaborated with an architect or designer on a cornice project?
How to Answer
- 1
Start with the project context and your role in it
- 2
Explain how you interacted with the architect or designer
- 3
Highlight any challenges faced and how you resolved them
- 4
Emphasize the successful outcome of the collaboration
- 5
Keep it focused on your contribution and skills
Example Answers
In my last project, I worked on a historic renovation where I collaborated with an architect to design custom cornices. I communicated regularly with the architect to ensure the details matched the building's style. We encountered issues with the ceiling height, but I proposed adjustable moldings that worked perfectly. The final result was praised by the client for its authenticity.
Situational Interview Questions
What would you do if, during installation, you find that the cornice does not fit as expected?
How to Answer
- 1
Assess the situation calmly and determine the cause of the misfit
- 2
Check your measurements and the installation area for any discrepancies
- 3
Consider making adjustments to the cornice or the installation space if feasible
- 4
Communicate with your team or client about the issue and your plan to resolve it
- 5
Document the issue and solution for future reference
Example Answers
I would first assess why the cornice doesn't fit, checking both my measurements and the installation area. Then, I would see if gentle adjustments can be made to fit it properly. If not, I'd inform my supervisor or the client to discuss the best course of action.
If you notice a safety hazard while at a job site, what actions would you take?
How to Answer
- 1
Assess the hazard quickly but carefully.
- 2
Inform your supervisor or site manager immediately.
- 3
Take action to secure the area if safe to do so.
- 4
Document the hazard and the actions taken.
- 5
Follow up to ensure the hazard is addressed.
Example Answers
I would first assess the hazard to understand the risk it poses. Then, I would notify my supervisor about the issue right away to ensure proper action is taken. If it's safe, I would try to block access to the hazard.
Don't Just Read Cornice Maker Questions - Practice Answering Them!
Reading helps, but actual practice is what gets you hired. Our AI feedback system helps you improve your Cornice Maker interview answers in real-time.
Personalized feedback
Unlimited practice
Used by hundreds of successful candidates
If a client requests a change to the cornice design just before installation, how would you handle it?
How to Answer
- 1
Listen carefully to the client's request and understand their vision.
- 2
Explain the implications of the change, including time and cost adjustments.
- 3
Offer options or alternatives that meet the client's need while maintaining feasibility.
- 4
Confirm the new details in writing to ensure clarity and agreement.
- 5
Stay calm and professional, showing your willingness to accommodate reasonable requests.
Example Answers
I would first listen closely to the client's request to ensure I fully understand what they want. I would then explain if the change would affect the timeline or cost and suggest alternatives if needed. Finally, I would document the agreed changes to avoid any confusion later.
Imagine you are halfway through a project when you realize you have ordered the wrong materials. What steps would you take next?
How to Answer
- 1
Assess the impact of the wrong materials on the project timeline.
- 2
Communicate with your team and supervisor about the issue.
- 3
Identify the correct materials needed for the project.
- 4
Check if replacement materials can be sourced quickly.
- 5
Adjust the project plan accordingly to minimize delays.
Example Answers
I would first evaluate how the wrong materials affect our timeline. Then, I'd inform my team and supervisor immediately. Next, I would find out the correct materials and check with suppliers for availability. If possible, I would expedite the order to minimize delays and update our project plan.
You and a coworker have different ideas on how to approach a cornice design. How will you resolve this?
How to Answer
- 1
Listen to your coworker's ideas openly.
- 2
Share your perspective clearly and respectfully.
- 3
Look for common ground and shared goals.
- 4
Suggest a collaborative approach or compromise.
- 5
If needed, involve a third party for additional feedback.
Example Answers
I would start by listening to my coworker's design ideas to understand their perspective fully. Then, I'd share my thoughts and try to identify the strengths of both approaches. Together, we could find a united design that incorporates the best elements of each idea.
If your team is running low on supplies halfway through the job, how would you manage the situation?
How to Answer
- 1
Assess the current supply situation and determine what is running low
- 2
Communicate clearly with your team about the supply issue
- 3
Identify alternative solutions or substitutes if possible
- 4
Contact suppliers to restock immediately or find local hardware stores
- 5
Keep the project timeline in mind and inform stakeholders of delays
Example Answers
First, I would quickly check our inventory to see what is low. Then, I would inform my team so we can brainstorm alternatives. If needed, I would reach out to our supplier to expedite the order.
A last-minute design change requires different dimensions for the cornice. How will you ensure it fits within the schedule?
How to Answer
- 1
Assess the time required to implement the new dimensions
- 2
Communicate promptly with the team and stakeholders about the changes
- 3
Propose a revised timeline adjusting for any delays caused by the change
- 4
Identify any resources that can expedite the process, like additional tools or personnel
- 5
Prioritize tasks that can be adjusted without disrupting the entire schedule
Example Answers
I would first assess how long the design change will take and communicate this to my team immediately. If the change requires too much time, I’d suggest a revised timeline. Meanwhile, I’d look for resources to help speed up the process, like reallocating workers or using different tools.
If a customer complains about the installation of their cornice after the job is done, how would you address this?
How to Answer
- 1
Listen carefully to the customer's concerns without interrupting.
- 2
Acknowledge their feelings and confirm their issues are valid.
- 3
Ask for specific details about what is wrong with the installation.
- 4
Offer a prompt solution, such as scheduling a follow-up visit.
- 5
Ensure to follow up after the resolution to confirm their satisfaction.
Example Answers
I would first listen to the customer’s concerns and make sure I understand the specific issue. I would then acknowledge their frustration and let them know I will take care of it. I would propose a time to revisit and resolve the installation issue promptly.
If you are asked to revise your cornice design after a client review, how would you proceed?
How to Answer
- 1
Listen carefully to the client's feedback and take notes.
- 2
Ask clarifying questions if any feedback is unclear.
- 3
Consider the client's preferences and the practicality of changes.
- 4
Revise the design iteratively and present the updates clearly.
- 5
Follow up with the client to ensure the new design meets their expectations.
Example Answers
I would first listen to the client’s feedback and write down their main concerns. If anything is unclear, I would ask questions to understand better. Then, I’d revise the design to incorporate their suggestions while ensuring it remains practical. I would present the new design and check back with the client to ensure it aligns with their vision.
During installation, you notice that the new cornice piece is warped. How would you solve this problem?
How to Answer
- 1
Assess the degree of warping and determine if it can be fixed.
- 2
Check tools available and consider using a heat source to adjust the curve.
- 3
If the warp is severe, consider replacing the piece with a new one.
- 4
Ensure the surface where it will be installed is level and suitable.
- 5
Secure the piece with adhesive or brackets once corrected.
Example Answers
First, I would assess how warped the cornice piece is. If it’s slight, I could use a heat gun to gently reshape it. For a more severe warp, I’d consider replacing it. I’d make sure the installation area is level, then secure it properly once it’s in place.
Don't Just Read Cornice Maker Questions - Practice Answering Them!
Reading helps, but actual practice is what gets you hired. Our AI feedback system helps you improve your Cornice Maker interview answers in real-time.
Personalized feedback
Unlimited practice
Used by hundreds of successful candidates
Technical Interview Questions
What types of materials do you prefer to use for cornice making and why?
How to Answer
- 1
Identify key materials commonly used in cornice making.
- 2
Explain the benefits of each material you mention.
- 3
Consider mentioning your personal preference based on experience.
- 4
Relate the materials to the project requirements such as durability or aesthetics.
- 5
Keep your answer concise and focused on your expertise.
Example Answers
I prefer using polyurethane for cornice making because it's lightweight, easy to install, and resistant to moisture. It allows for intricate designs while maintaining durability.
Can you explain how to properly use a miter saw for cutting cornice moldings?
How to Answer
- 1
Ensure the miter saw is set to the correct angle for the cornice molding cut.
- 2
Secure the molding firmly against the fence before making the cut.
- 3
Use a steady and controlled motion to lower the saw blade onto the molding.
- 4
Wear safety goggles and keep hands clear of the blade at all times.
- 5
Check your measurements twice before cutting to avoid mistakes.
Example Answers
To use a miter saw for cornice moldings, first set the angle on the saw according to the molding's cut requirements. Then, secure the molding against the fence and lower the blade smoothly for a clean cut, always keeping your hands clear.
Don't Just Read Cornice Maker Questions - Practice Answering Them!
Reading helps, but actual practice is what gets you hired. Our AI feedback system helps you improve your Cornice Maker interview answers in real-time.
Personalized feedback
Unlimited practice
Used by hundreds of successful candidates
What is your process for designing a cornice that fits a specific architectural style?
How to Answer
- 1
Research the architectural style to understand its key features and historical context
- 2
Consider the proportions and scale of the cornice in relation to the overall building
- 3
Sketch initial ideas and incorporate design elements that reflect the style
- 4
Select materials that match both the aesthetic and the functional requirements
- 5
Get feedback from clients or colleagues to refine the design before finalization
Example Answers
I start by researching the specific architectural style, looking for key details such as moldings or motifs. Then, I create preliminary sketches that emphasize those features, ensuring the scale complements the building's proportions. After that, I choose materials that suit the style, like wood for traditional looks or metal for modern designs, and I always seek feedback to improve my designs.
What techniques do you use for ensuring the cornice is securely attached to the wall?
How to Answer
- 1
Use a level to ensure the cornice is straight before attachment
- 2
Pre-drill holes for screws to prevent splitting the material
- 3
Utilize adhesive along with screws for a stronger bond
- 4
Select appropriate fasteners based on wall type (drywall, plaster, etc.)
- 5
Allow adequate time for adhesive to set if used
Example Answers
I always use a level to ensure the cornice is straight before attaching it. I pre-drill holes to avoid splitting the cornice and use a combination of adhesive and screws for a secure hold.
How do you ensure a smooth finish on a wooden cornice before installation?
How to Answer
- 1
Start with high-quality wood free from knots or imperfections.
- 2
Sand the surface thoroughly using progressively finer grits to eliminate rough spots.
- 3
Apply primer or sealant to enhance adhesion and smoothness of the finish.
- 4
Use a paint or finish that is suitable for wood and allows for smooth application.
- 5
Inspect the finished cornice for any blemishes and sand lightly if necessary.
Example Answers
To ensure a smooth finish on a wooden cornice, I begin with selecting high-quality wood, then sand it using fine grit paper from coarse to fine. I also apply a primer to help the final finish adhere better and achieve a smoother look.
How do you estimate the amount of material needed for a cornice installation?
How to Answer
- 1
Measure the length of the installation area accurately.
- 2
Calculate the height and depth required for the cornice design.
- 3
Consider the profile and style of the cornice when estimating material.
- 4
Add extra material for waste and cuts, typically around 10%.
- 5
Consult manufacturer specifications for coverage and product dimensions.
Example Answers
To estimate materials for cornice installation, I first measure the area where the cornice will go. I then calculate the required height and depth based on the design. I also include an additional 10% for waste and check the manufacturer's specs for how much each piece covers.
Do you have experience with design software for creating cornice designs? Which software do you use?
How to Answer
- 1
Mention specific design software you are familiar with
- 2
Include how long you have used the software
- 3
Explain how you use the software in your design process
- 4
Highlight any unique features or tools in the software that help in cornice design
- 5
Share a brief example of a project where you used the software effectively.
Example Answers
I have experience using AutoCAD and SketchUp for creating cornice designs. I've been using AutoCAD for 3 years, which helps me create precise 2D drawings. I also like using SketchUp for 3D visualizations, as it allows clients to see the final look more clearly.
Can you describe your method for creating a pattern for complex cornice designs?
How to Answer
- 1
Start by gathering design inspirations and understanding the space where the cornice will be installed.
- 2
Sketch preliminary designs on paper to visualize shapes and dimensions.
- 3
Use specific measurements of the area to ensure proper fit and alignment of the cornice.
- 4
Select materials that match the design intention, considering weight and durability.
- 5
Create a detailed pattern template using cardboard or a similar material to test the design before final production.
Example Answers
I begin by researching styles that suit the room and sketch initial designs. Then, I take precise measurements of the wall heights and widths to create a tailored pattern. After that, I build a cardboard model to see how it looks before crafting it in my chosen material.
What finishing techniques do you find most effective for enhancing the aesthetics of a cornice?
How to Answer
- 1
Discuss the importance of paint or stain for color enhancement.
- 2
Mention the role of gilding or metallic finishes for elegance.
- 3
Talk about the value of texture, such as using a textured paint or glaze.
- 4
Include the use of decorative trim or moldings to add visual interest.
- 5
Highlight the impact of proper sealing and maintenance to preserve the finish.
Example Answers
I find that using a satin or eggshell finish paint enhances the cornice's aesthetics by adding depth while still being easy to clean. Gilding the edges can also elevate the elegance of the design.
What are the challenges you face when cutting intricate designs in cornice materials?
How to Answer
- 1
Identify specific materials that are difficult to cut, like plaster or wood.
- 2
Talk about the precision required for intricate designs and how it affects your approach.
- 3
Mention tools and techniques you use to overcome cutting challenges.
- 4
Consider the impact of design complexity on time management.
- 5
Discuss safety concerns related to cutting intricate patterns.
Example Answers
One challenge I face is cutting intricate designs in hardwood, as it requires precise control. I use specialized saws and take my time to avoid mistakes.
Don't Just Read Cornice Maker Questions - Practice Answering Them!
Reading helps, but actual practice is what gets you hired. Our AI feedback system helps you improve your Cornice Maker interview answers in real-time.
Personalized feedback
Unlimited practice
Used by hundreds of successful candidates
What are the different installation methods you employ for ceiling cornices versus wall cornices?
How to Answer
- 1
Identify the differences in support structures for ceilings and walls.
- 2
Discuss the tools and materials specific to each installation method.
- 3
Mention the importance of alignment and leveling for aesthetics.
- 4
Explain how the type of cornice may affect installation technique.
- 5
Share personal experience or techniques that ensure quality installation.
Example Answers
For ceiling cornices, I typically use adhesive and sometimes screws for extra support, while wall cornices often just require adhesive. The key is ensuring that the ceiling cornice is perfectly level, as it's more visible.
Cornice Maker Position Details
Recommended Job Boards
ZipRecruiter
www.ziprecruiter.com/Jobs/CorniceThese job boards are ranked by relevance for this position.
Related Positions
- Garland Maker
- Wreath Maker
- Roof Fitter
- Door Trimmer
- Part Maker
- Tile Edger
- Hand Bender
- Heading Maker
- Cap Maker
- Screen Maker
Similar positions you might be interested in.
Ace Your Next Interview!
Practice with AI feedback & get hired faster
Personalized feedback
Used by hundreds of successful candidates
Ace Your Next Interview!
Practice with AI feedback & get hired faster
Personalized feedback
Used by hundreds of successful candidates