Top 31 Embosser Interview Questions and Answers [Updated 2025]
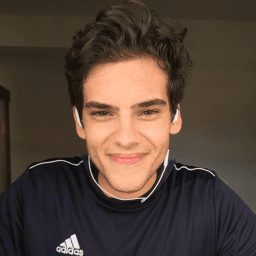
Andre Mendes
•
March 30, 2025
Preparing for an embosser role interview can be daunting, but we're here to help you shine with confidence. Our comprehensive guide covers the most common interview questions for embossers, complete with insightful example answers and practical tips on how to respond effectively. Dive in to enhance your interview skills and increase your chances of landing that job with ease and assurance.
Download Embosser Interview Questions in PDF
To make your preparation even more convenient, we've compiled all these top Embosserinterview questions and answers into a handy PDF.
Click the button below to download the PDF and have easy access to these essential questions anytime, anywhere:
List of Embosser Interview Questions
Behavioral Interview Questions
Describe a time when you worked as part of a team to complete an embossing project. What was your role?
How to Answer
- 1
Use the STAR method: Situation, Task, Action, Result.
- 2
Clearly state your specific role in the project.
- 3
Highlight collaboration efforts with team members.
- 4
Mention any challenges faced and how you overcame them.
- 5
Conclude with the outcome of the project and what you learned.
Example Answers
In my previous role at ABC Company, we had a project to emboss custom wedding invitations. I was responsible for the setup of the embossing machine, ensuring it was calibrated correctly. This required coordination with the graphic designer to align the designs precisely. We faced a challenge when the machine jammed, but I worked with a colleague to troubleshoot and solve the issue quickly. The final product was well-received, and we completed the project ahead of schedule, which improved our team's reputation.
Can you provide an example of a challenge you faced while operating an embossing machine and how you overcame it?
How to Answer
- 1
Identify a specific challenge related to the embossing machine.
- 2
Describe the situation clearly and concisely.
- 3
Explain the steps you took to address the challenge.
- 4
Highlight the outcome and what you learned from the experience.
- 5
Keep your answer focused on your role and actions.
Example Answers
While operating the embossing machine, I faced a challenge when the embossing plates became misaligned, resulting in poor quality output. I stopped the machine, realigned the plates according to the specifications, and performed a test run. The output improved significantly, and I learned the importance of regular checks before starting a production run.
Don't Just Read Embosser Questions - Practice Answering Them!
Reading helps, but actual practice is what gets you hired. Our AI feedback system helps you improve your Embosser interview answers in real-time.
Personalized feedback
Unlimited practice
Used by hundreds of successful candidates
Tell me about a situation where your attention to detail made a significant difference in the quality of the embossed product.
How to Answer
- 1
Choose a specific example from your experience.
- 2
Highlight the mistake that could have happened due to lack of detail.
- 3
Explain the steps you took to ensure quality.
- 4
Mention the outcome and how it benefited the team or project.
- 5
Keep it concise and focused on your role in the situation.
Example Answers
In my previous job, we had a batch of embossed invitations. I noticed while inspecting the samples that the logo was slightly off-center. I immediately discussed it with the team and corrected the position before we began mass production. This prevented the entire batch from being rejected and saved the company time and money.
How do you prioritize tasks when multiple embossing jobs have tight deadlines?
How to Answer
- 1
Assess the urgency and importance of each job.
- 2
Communicate deadlines clearly with your team and clients.
- 3
Organize tasks by starting with the most critical job first.
- 4
Use a scheduling tool to manage overlapping deadlines.
- 5
Be flexible and ready to adjust priorities as new information comes in.
Example Answers
I prioritize by assessing which jobs are most urgent and essential. I then communicate with my team to ensure everyone is aligned on deadlines, and I tackle the critical tasks first while using a scheduling tool to keep track of everything.
Describe a time when you had to give constructive feedback to a colleague about their embossing work.
How to Answer
- 1
Focus on a specific instance where feedback was necessary.
- 2
Be clear about the issue you noticed in their embossing work.
- 3
Emphasize how you communicated the feedback tactfully.
- 4
Describe the positive outcome or improvement that resulted from your feedback.
- 5
Ensure you mention any follow-up support you provided afterwards.
Example Answers
In a recent project, I noticed my colleague's embossing lacked depth. I approached them privately, highlighting the areas where the texture could be enhanced and suggested techniques they could use. They appreciated my input and improved their work significantly.
Tell me about a new technique or technology in embossing that you have recently learned and how you applied it.
How to Answer
- 1
Identify a specific technique or technology you learned.
- 2
Describe the source where you learned about it.
- 3
Explain how you implemented it in your work.
- 4
Share the outcome or results of applying this technique.
- 5
Relate it to improving efficiency, quality, or creativity.
Example Answers
I recently learned about digital embossing technology through a webinar. I applied it by integrating a digital embossing machine into our production line, which increased our productivity by 20% and enhanced design precision.
What is your proudest achievement in your embossing career so far?
How to Answer
- 1
Reflect on past projects that you found rewarding
- 2
Choose an achievement that had a significant positive impact on your team or company
- 3
Quantify your achievement, if possible, with specific figures or outcomes
- 4
Highlight any skills you used or developed during this achievement
- 5
Offer context that shows the challenges you overcame to reach this achievement
Example Answers
My proudest achievement was leading a project where I developed a new embossing technique that increased production efficiency by 20%. This not only saved costs but also boosted team morale as we were able to meet tight deadlines.
Describe a successful collaboration with another team or department on an embossing project.
How to Answer
- 1
Start with a clear project overview and the teams involved
- 2
Highlight the specific roles each team played
- 3
Explain how communication and coordination were managed
- 4
Share the outcomes and successes of the collaboration
- 5
Mention any challenges faced and how they were overcome
Example Answers
In our last embossing project, we collaborated with the design team to create a custom packaging solution. The design team provided the artwork while my team focused on embossing techniques. We had weekly check-ins to discuss progress and adjust timelines as needed. The final product increased customer engagement and we received excellent feedback on its quality. We faced a challenge with the embossing pressure, but by working closely, we refined the process and delivered a perfect result.
What motivates you to excel in the field of embossing?
How to Answer
- 1
Identify personal passion for craftsmanship and precision
- 2
Discuss enjoyment of creating tangible, quality products
- 3
Mention the importance of customer satisfaction and feedback
- 4
Highlight the satisfaction that comes from overcoming challenges
- 5
Connect your motivation to industry trends and innovations
Example Answers
I'm motivated by my passion for craftsmanship. Embossing allows me to create beautiful, high-quality products that people appreciate.
Don't Just Read Embosser Questions - Practice Answering Them!
Reading helps, but actual practice is what gets you hired. Our AI feedback system helps you improve your Embosser interview answers in real-time.
Personalized feedback
Unlimited practice
Used by hundreds of successful candidates
How do you seek out opportunities for professional development in the embossing industry?
How to Answer
- 1
Attend industry conferences to network and learn about new techniques.
- 2
Join professional associations related to embossing and participate in their events.
- 3
Take online courses or workshops specific to embossing technology advancements.
- 4
Follow industry leaders on social media to stay updated on trends and best practices.
- 5
Engage with forums or communities dedicated to embossing for peer learning.
Example Answers
I actively attend industry conferences where I can connect with experts and learn about the latest embossing technologies. For example, last year I attended the National Embossing Convention, which offered workshops and insights that I still apply today.
Technical Interview Questions
What types of embossing machines are you familiar with, and what are their key operational differences?
How to Answer
- 1
Identify the types of embossing machines you know, such as flatbed or rotary.
- 2
Explain the key features of each type, like speed and application.
- 3
Mention any specific brands or models you have experience with.
- 4
Discuss the pros and cons of each machine in terms of usability and output.
- 5
Link your experiences with practical examples of projects you’ve worked on.
Example Answers
I am familiar with flatbed and rotary embossing machines. Flatbed machines are great for detailed designs and are slower, while rotary machines are faster and suited for high-volume production. I've worked on a flatbed machine that produced unique packaging designs and could achieve intricate patterns that rotary machines struggle with.
Explain the importance of selecting the right materials for embossing and the potential impact of wrong choices.
How to Answer
- 1
Identify different materials commonly used in embossing such as paper types and metal.
- 2
Discuss how material choice affects the clarity and durability of the embossing.
- 3
Mention the impact on cost and production time due to material selection.
- 4
Explain potential failures that can occur with incorrect materials, like smudging or tearing.
- 5
Highlight the significance of matching materials to the project requirements.
Example Answers
Choosing the right materials for embossing is crucial because it affects the quality of the finished product. For instance, using a high-quality cardstock can enhance clarity while cheaper papers may tear or smudge.
Don't Just Read Embosser Questions - Practice Answering Them!
Reading helps, but actual practice is what gets you hired. Our AI feedback system helps you improve your Embosser interview answers in real-time.
Personalized feedback
Unlimited practice
Used by hundreds of successful candidates
What steps do you take to ensure quality control during the embossing process?
How to Answer
- 1
Establish clear standards for embossing quality before starting.
- 2
Regularly inspect the embossing equipment for alignment and calibration.
- 3
Conduct sample checks on materials before full production.
- 4
Implement a checklist to verify each step of the embossing process.
- 5
Train team members on quality expectations and troubleshooting.
Example Answers
To ensure quality control during embossing, I start with clear quality standards and regularly check equipment for proper alignment. I also conduct sample checks on materials before beginning the run.
How do you perform regular maintenance on embossing equipment to ensure optimal performance?
How to Answer
- 1
Follow the manufacturer's maintenance schedule for the equipment.
- 2
Inspect and clean the embossing plates and rollers after each use.
- 3
Lubricate moving parts regularly to prevent wear and tear.
- 4
Check electrical connections and test controls periodically for proper operation.
- 5
Keep a maintenance log to track service dates and issues.
Example Answers
I adhere to the manufacturer's maintenance schedule, ensuring that I check and clean the embossing plates and rollers after each use. I also lubricate the moving parts regularly and inspect the electrical connections to confirm they're functioning properly.
What do you understand about design specifications that are critical for successful embossing?
How to Answer
- 1
Understand the material being embossed and its properties.
- 2
Identify the appropriate thickness and pressure for embossing.
- 3
Ensure designs are clean with clear lines and details.
- 4
Consider the production processes and machinery capabilities.
- 5
Be aware of color contrast and its impact on embossed designs.
Example Answers
Successful embossing relies on understanding the material properties. For example, thinner materials may require less pressure to avoid damage, while thicker materials can handle more pressure. Also, designs must be clean and precise to ensure a clear final product.
Can you explain how temperature and pressure affect the embossing process?
How to Answer
- 1
Define embossing and its purpose in printing and manufacturing.
- 2
Explain the role of temperature in softening materials for better impression.
- 3
Discuss how pressure impacts the depth and clarity of the embossing.
- 4
Mention the materials commonly used and how they respond to these factors.
- 5
Provide real-world examples or experiences related to temperature and pressure adjustments.
Example Answers
Embossing is a technique used to create raised designs on materials. Higher temperatures can help soften materials like plastic or paper, making them more pliable. Increased pressure during the embossing process ensures a clear and deep impression, which is crucial for quality output.
What safety measures do you follow while operating embossing machines?
How to Answer
- 1
Always wear appropriate personal protective equipment, such as gloves and safety glasses.
- 2
Ensure that all safety guards are in place before operating the machine.
- 3
Keep hands away from moving parts and avoid distractions while operating.
- 4
Regularly inspect the machine for any defects or maintenance needs.
- 5
Follow the manufacturer's guidelines and standard operating procedures at all times.
Example Answers
I always wear safety glasses and gloves when operating the embossing machine. I make sure that all safety guards are properly in place and I focus entirely on the task without distractions.
What training have you received in relation to embossing and how has it prepared you for this role?
How to Answer
- 1
Highlight specific embossing training programs you've completed.
- 2
Include hands-on experience with embossing tools and machines.
- 3
Mention any relevant certifications or workshops you've attended.
- 4
Discuss how this training has developed your skills and confidence in embossing.
- 5
Connect your training to the requirements of the embosser position you're applying for.
Example Answers
I completed a comprehensive embossing training program where I learned to operate various types of embossing machines. This training included hands-on practice, which allowed me to develop my skills in creating high-quality embossed products. Additionally, I attended a workshop on advanced techniques, which greatly enhanced my understanding of intricate designs.
How comfortable are you with reading and interpreting technical drawings for embossing designs?
How to Answer
- 1
Emphasize your experience with technical drawings
- 2
Mention specific software or tools you use
- 3
Explain your understanding of design elements
- 4
Provide examples of past projects involving embossing
- 5
Show willingness to learn and adapt if necessary
Example Answers
I have extensive experience interpreting technical drawings, especially using software like AutoCAD, which I regularly use for embossing projects.
Describe the embossing process from start to finish, including any considerations at each stage.
How to Answer
- 1
Start with material preparation, ensuring quality and type meets project requirements.
- 2
Explain the design stage, focusing on creating accurate and detailed molds for embossing.
- 3
Discuss the embossing process, including setup of the machine and alignment of materials.
- 4
Mention quality checks during and after embossing to ensure consistency and adherence to specifications.
- 5
Wrap up with post-processing considerations, like trimming and finishing touches if necessary.
Example Answers
The embossing process begins with selecting and preparing the right material, ensuring it can hold the embossed shape. Next, we design the mold carefully to reflect the desired pattern. During embossing, we set up the machine, ensuring the material is well aligned before applying heat and pressure. We conduct quality checks throughout to catch any defects early, and finally, we might trim the edges and apply protective coatings to enhance durability.
Don't Just Read Embosser Questions - Practice Answering Them!
Reading helps, but actual practice is what gets you hired. Our AI feedback system helps you improve your Embosser interview answers in real-time.
Personalized feedback
Unlimited practice
Used by hundreds of successful candidates
What troubleshooting steps do you take when an embossing job is not turning out as expected?
How to Answer
- 1
Check the material type and make sure it's compatible with the embossing process
- 2
Inspect the embossing plates for any wear, damage or misalignment
- 3
Verify the machine settings such as pressure and temperature match specifications
- 4
Look for any debris or buildup on the machine that could affect the process
- 5
Run a test job with a smaller design to isolate the issue
Example Answers
First, I check if the material is suitable for embossing. It's crucial to ensure compatibility. Then, I inspect the embossing plates for any damage and adjust machine settings like pressure to see if that resolves the issue.
Situational Interview Questions
Imagine you receive a complaint about the quality of an embossed item. How would you address this issue with your team?
How to Answer
- 1
Acknowledge the complaint promptly and gather details about the issue
- 2
Consult with the team to understand the production process involved
- 3
Identify potential causes for the quality issue based on the team's input
- 4
Implement a plan to correct any identified issues and prevent future occurrences
- 5
Communicate the resolution and steps taken back to the complainant
Example Answers
First, I would acknowledge the complaint and ask for specifics to understand the issue better. Then, I would meet with the team to review our production process and pinpoint any deviations. Based on our findings, we could implement changes to our quality checks and inform the complainant of our action plan to avoid future issues.
How would you approach introducing a new embossing technique that your team has never used before?
How to Answer
- 1
Research the new embossing technique thoroughly.
- 2
Prepare a presentation to outline benefits and methods.
- 3
Conduct a hands-on workshop for the team to practice.
- 4
Gather team feedback and address concerns.
- 5
Implement the technique gradually with support.
Example Answers
I would start by researching the new technique and creating a presentation that highlights its benefits. Then, I would organize a workshop where the team can try it out. Afterward, I would collect their feedback to refine our approach and ensure a smooth implementation.
Don't Just Read Embosser Questions - Practice Answering Them!
Reading helps, but actual practice is what gets you hired. Our AI feedback system helps you improve your Embosser interview answers in real-time.
Personalized feedback
Unlimited practice
Used by hundreds of successful candidates
If you encountered a malfunction in the embossing machine during a critical production run, what immediate steps would you take?
How to Answer
- 1
Assess the situation quickly to understand the type of malfunction.
- 2
Ensure safety protocols are followed for yourself and the team.
- 3
Stop the machine to prevent further damage or risk.
- 4
Communicate with your supervisor and team about the issue.
- 5
Begin troubleshooting or follow maintenance procedures as trained.
Example Answers
I would first assess the malfunction to identify whether it's a mechanical issue or a power supply problem. I'd ensure everyone is safe, then stop the machine to avoid any further complications. I would report the issue to my supervisor and collaborate with the team to troubleshoot, using standard operating procedures.
How would you handle a situation where a team member is consistently missing quality standards in their embossing work?
How to Answer
- 1
Observe their embossing process to identify specific issues.
- 2
Provide constructive feedback in a private setting.
- 3
Offer assistance and share best practices for quality work.
- 4
Set up follow-up meetings to monitor progress.
- 5
Encourage open communication about challenges they face.
Example Answers
I would first observe their embossing technique to pinpoint where the quality standards are being missed. Then, I would have a private conversation to share my observations and provide constructive feedback. I would also offer to work together to improve their technique and set follow-up meetings to ensure they feel supported and to monitor their progress.
You noticed that some part of the embossing process is slower than it should be. What strategies would you implement to improve efficiency?
How to Answer
- 1
Identify the specific bottleneck in the embossing process.
- 2
Analyze the root cause of the slowdown, whether it's equipment, material, or personnel.
- 3
Implement targeted training for operators to enhance their skills.
- 4
Explore equipment upgrades or maintenance to ensure optimal performance.
- 5
Set metrics to measure efficiency before and after changes.
Example Answers
I would first analyze the embossing line to pinpoint where the slowdown occurs, whether it's due to equipment failure or operator inefficiency. After identifying the issue, I would address it by providing additional training or adjusting the work process accordingly.
If your department's embossed supplies are running low, how would you manage the workshop's workflow?
How to Answer
- 1
Assess the current inventory of embossed supplies immediately
- 2
Prioritize tasks based on urgency and production deadlines
- 3
Communicate with team members about the supply status
- 4
Coordinate with suppliers for urgent replenishment
- 5
Adjust the workflow to accommodate reduced capacity temporarily
Example Answers
I would first check the inventory and identify how much we have left. Then, I'd prioritize jobs that are most urgent and communicate with the team to keep everyone informed about the situation. I would reach out to suppliers to expedite our next order and adjust our workflow as necessary to minimize disruptions.
If a client requests a specific embossing pattern that you are unsure how to create, how would you proceed?
How to Answer
- 1
Ask the client for more details about the design they envision
- 2
Research or refer to existing designs for inspiration
- 3
Consult with colleagues or experts who may have experience with similar patterns
- 4
Suggest alternatives that match the client's vision while you learn more
- 5
Provide a timeline for when you can deliver the final design or prototype
Example Answers
I would first ask the client to describe their vision in detail and clarify any specifics about the embossing pattern. Then, I'd research similar patterns to see how they were made and consult with my colleagues for advice.
How would you handle a last-minute project request from management that conflicts with your current workload?
How to Answer
- 1
Assess your current priorities and deadlines quickly.
- 2
Communicate openly with management about your workload.
- 3
Negotiate deadlines or clarify the importance of the new request.
- 4
Consider delegating tasks if possible to manage your time.
- 5
Stay flexible and positive while seeking solutions.
Example Answers
I would first review my current tasks to see if there's flexibility. Then, I would discuss with management to understand the urgency of the new request and negotiate a feasible deadline without compromising my existing commitments.
If you saw a colleague struggling with their embossing work, how would you approach them to offer help?
How to Answer
- 1
Assess the situation quietly before intervening.
- 2
Approach your colleague in a friendly and non-intrusive manner.
- 3
Ask if they would like some assistance or if they need help.
- 4
Share relevant tips or techniques based on your experience.
- 5
Encourage an open dialogue to address their specific challenges.
Example Answers
I would observe my colleague to see what specific issues they are facing. Then I would approach them kindly and ask, 'Hey, I noticed you seem to be having a bit of trouble with your embossing. Would you like some help with it?' If they agree, I would share any tips that worked for me and offer to demonstrate.
Embosser Position Details
Recommended Job Boards
CareerBuilder
www.careerbuilder.com/jobs/EmbosserZipRecruiter
www.ziprecruiter.com/Jobs/-EmbosserThese job boards are ranked by relevance for this position.
Related Positions
- Impregnator
- Button Puncher
- Roller Operator
- Blower
- Dry Roller
- Roller Painter
- Embalmer
- Engraver
- Bosher
- Edge Roller
Similar positions you might be interested in.
Ace Your Next Interview!
Practice with AI feedback & get hired faster
Personalized feedback
Used by hundreds of successful candidates
Ace Your Next Interview!
Practice with AI feedback & get hired faster
Personalized feedback
Used by hundreds of successful candidates