Top 29 Failure Analysis Technician Interview Questions and Answers [Updated 2025]
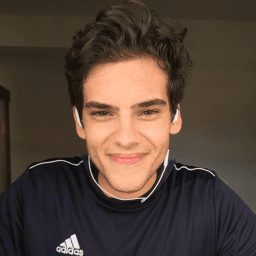
Andre Mendes
•
March 30, 2025
Navigating the interview process for a Failure Analysis Technician role can be daunting, but preparation is key to success. In this post, we delve into the most common interview questions you'll encounter, providing example answers and effective strategies to enhance your responses. Whether you're a seasoned professional or a newcomer, gain the confidence to articulate your expertise and stand out to potential employers.
Download Failure Analysis Technician Interview Questions in PDF
To make your preparation even more convenient, we've compiled all these top Failure Analysis Technicianinterview questions and answers into a handy PDF.
Click the button below to download the PDF and have easy access to these essential questions anytime, anywhere:
List of Failure Analysis Technician Interview Questions
Technical Interview Questions
What methods do you use to perform root cause analysis of product failures?
How to Answer
- 1
Start by mentioning specific methodologies like 5 Whys or Fishbone Diagram.
- 2
Discuss how you collect and analyze data related to the failure.
- 3
Emphasize the importance of teamwork with engineers and quality control.
- 4
Explain how you validate your findings through testing and experiments.
- 5
Mention documenting the process and outcomes for future reference.
Example Answers
I typically use the 5 Whys method to identify the underlying issues. For example, I dug deeper into a power failure and found misconfigured settings in the firmware as the root cause. I also collaborate with the engineering team to ensure that the findings are validated through controlled tests.
Explain how you would conduct a failure analysis on a metal component that fractured unexpectedly.
How to Answer
- 1
Gather the fractured component and document its condition.
- 2
Identify and record the failure mode and location of the fracture.
- 3
Conduct a visual inspection for signs of stress, corrosion, or poor manufacturing.
- 4
Perform mechanical testing if possible to assess material properties.
- 5
Analyze the findings to determine root causes and suggest improvements.
Example Answers
First, I would collect the fractured metal component and take photographs for documentation. Then, I would examine the fracture surface visually to identify any signs of fatigue or stress. Next, I would look for material defects or corrosion, and if necessary, I would conduct hardness tests to evaluate the material properties. Finally, I would compile my findings and propose corrective actions, such as adjusting the manufacturing process.
Don't Just Read Failure Analysis Technician Questions - Practice Answering Them!
Reading helps, but actual practice is what gets you hired. Our AI feedback system helps you improve your Failure Analysis Technician interview answers in real-time.
Personalized feedback
Unlimited practice
Used by hundreds of successful candidates
What laboratory techniques are you proficient in for conducting failure analysis?
How to Answer
- 1
Identify specific techniques you have hands-on experience with
- 2
Mention any relevant tools or equipment you are familiar with
- 3
Discuss any analytical methods, such as microscopy or spectroscopy
- 4
Highlight your ability to interpret data from these techniques
- 5
Connect your skills to how they can benefit the company's goals
Example Answers
I am proficient in optical microscopy and scanning electron microscopy, which I use to analyze surface failures. Additionally, I have experience with X-ray diffraction for material identification, helping to determine the root causes of failures effectively.
How do you use microscopy in failure analysis, and what specific techniques are you familiar with?
How to Answer
- 1
Explain the role of microscopy in identifying failure mechanisms.
- 2
Mention specific microscopy techniques you have used, like SEM or optical microscopy.
- 3
Describe how you analyze samples using these techniques.
- 4
Provide examples of failures you analyzed and the microscopy techniques used.
- 5
Be concise and focus on how your experience relates to the job requirements.
Example Answers
In failure analysis, I use microscopy to identify the root causes of failures. I have hands-on experience with SEM and optical microscopy. For instance, I analyzed a fracture in a metal part using SEM, which revealed microstructural defects that contributed to the failure.
Describe the process you follow to analyze data collected during failure analysis.
How to Answer
- 1
Start by explaining the initial data collection methods.
- 2
Detail how you categorize and organize the data.
- 3
Discuss the tools and software you use for analysis.
- 4
Explain how you interpret the results and findings.
- 5
Conclude with how you document and communicate your conclusions.
Example Answers
I begin by collecting data using both observational techniques and instrumentation. Then, I categorize the data by types of failures and organize it into spreadsheets for easier analysis. I use statistical software to identify trends and root causes, and I summarize my findings in a report that outlines the failures and possible solutions.
What is your experience with failure analysis of electronic components and circuits?
How to Answer
- 1
Start with your overall experience in failure analysis.
- 2
Mention specific types of electronic components you have worked with.
- 3
Describe methodologies or tools you used in your analyses.
- 4
Provide an example of a significant failure you analyzed.
- 5
Emphasize the outcomes or improvements that resulted from your analysis.
Example Answers
I have over three years of experience in failure analysis, primarily focusing on semiconductor components. I have used techniques such as SEM and X-Ray imaging in my analyses. For instance, I investigated a chip that failed during testing, identifying a design flaw that led to a redesign and improved performance.
Which software tools are you proficient in using for conducting failure analysis?
How to Answer
- 1
Identify specific software tools you have experience with.
- 2
Mention how you've used these tools in past projects.
- 3
Highlight any certifications or formal training related to these tools.
- 4
Discuss the strengths of the tools in relation to failure analysis.
- 5
Be prepared to describe a memorable instance when you used a particular tool.
Example Answers
I am proficient in using Minitab and SolidWorks. In my last project, I utilized Minitab for statistical analysis of failure data, which helped us identify key trends and improve product reliability. I have also completed a training course on SolidWorks for modeling and analysis.
Discuss the role of non-destructive testing in failure analysis and your experience with it.
How to Answer
- 1
Start with a clear definition of non-destructive testing (NDT) and its importance.
- 2
Explain how NDT is used to detect defects without damaging the component.
- 3
Share specific NDT methods you have experience with, like ultrasonic or X-ray testing.
- 4
Describe a successful instance where you used NDT in a failure analysis project.
- 5
Highlight the benefits of using NDT in terms of cost, efficiency, and safety.
Example Answers
Non-destructive testing is crucial in failure analysis as it allows us to identify defects without destroying the component. In my previous role, I frequently used ultrasonic testing to find cracks in welds, which helped us prevent potential failures. For example, during a project on pipeline integrity, I discovered a critical flaw that saved the company from a costly shutdown.
Explain the principles of fracture mechanics and how they apply to failure analysis.
How to Answer
- 1
Define fracture mechanics and its importance in understanding material failure.
- 2
Discuss key concepts such as stress intensity factor and fracture toughness.
- 3
Explain how these principles help in identifying failure modes and predicting failure.
- 4
Provide an example of a real-world application in failure analysis.
- 5
Use clear and precise language to convey technical details simply.
Example Answers
Fracture mechanics studies how materials break under stress and the propagation of cracks. Key concepts include the stress intensity factor, which quantifies the stress concentration at the crack tip, and fracture toughness, which indicates a material's resistance to crack growth. In failure analysis, these principles help us determine why a component failed by assessing the stresses it experienced and identifying critical flaws.
How would you perform thermal analysis on a component suspected of failing due to thermal fatigue?
How to Answer
- 1
Identify the specific areas of the component that might be affected by thermal fatigue.
- 2
Select appropriate thermal analysis methods such as DSC or TGA based on material type.
- 3
Conduct a controlled heating and cooling cycle to simulate operational conditions.
- 4
Monitor temperature changes and thermal properties during the analysis.
- 5
Analyze the results to identify signs of thermal fatigue like cracking or changes in material properties.
Example Answers
I would first focus on the areas where heat concentration is highest and inspect physically for any visible damage. Then, I'd use DSC to measure thermal transitions and possibly TGA to assess weight changes at elevated temperatures. After simulating the thermal cycles, I would analyze the data for signs of fatigue.
Don't Just Read Failure Analysis Technician Questions - Practice Answering Them!
Reading helps, but actual practice is what gets you hired. Our AI feedback system helps you improve your Failure Analysis Technician interview answers in real-time.
Personalized feedback
Unlimited practice
Used by hundreds of successful candidates
Behavioral Interview Questions
Tell me about a time you encountered a challenging technical problem in a failure analysis, and how you resolved it.
How to Answer
- 1
Choose a specific technical problem you faced.
- 2
Explain the context and why it was challenging.
- 3
Describe the steps you took to analyze and resolve the issue.
- 4
Highlight the outcome and what you learned.
- 5
Connect your experience to the skills needed for the technician role.
Example Answers
In my last role, we faced an issue with recurrent failures in a batch of electronic components. The failures were sporadic and difficult to replicate. I systematically tested each component, analyzing data logs and running simulations. Ultimately, I found that a specific soldering technique was causing weak connections. After recommending a revised process, the failure rate dropped significantly, enhancing production reliability.
Describe an experience where your attention to detail led to a successful outcome in a failure analysis.
How to Answer
- 1
Choose a specific project where you played a key role.
- 2
Highlight the specific details you focused on.
- 3
Explain how your attention to detail directly impacted the result.
- 4
Use metrics or outcomes to quantify success if possible.
- 5
Keep the answer structured: situation, action, result.
Example Answers
In my previous role, I worked on a project analyzing a failure in a circuit board. I noticed that a solder joint was improperly aligned during assembly. I documented this detail and suggested a rework, which ultimately reduced failure rates by 30%.
Don't Just Read Failure Analysis Technician Questions - Practice Answering Them!
Reading helps, but actual practice is what gets you hired. Our AI feedback system helps you improve your Failure Analysis Technician interview answers in real-time.
Personalized feedback
Unlimited practice
Used by hundreds of successful candidates
Give an example of how you worked with a team to complete a failure analysis project.
How to Answer
- 1
Identify a specific project and your role in the team.
- 2
Highlight the team's objectives and challenges faced.
- 3
Describe the steps taken collaboratively to analyze the failure.
- 4
Mention the tools or methods used during the analysis.
- 5
Conclude with the outcome of the project and lessons learned.
Example Answers
In a project investigating a circuit board failure, I collaborated with three engineers. We set clear goals to identify the defect's root cause by analyzing data from tests. Each team member focused on different components, and we shared findings in regular meetings. We used software for data analysis, which helped us pinpoint the failure to a specific chip. This experience taught us the importance of open communication.
Describe a situation where you had to communicate complex results from a failure analysis to a non-technical audience.
How to Answer
- 1
Identify the key message or outcome from the analysis.
- 2
Use simple, relatable language to explain technical terms.
- 3
Provide an analogy or visual to help clarify your points.
- 4
Be prepared to answer questions and clarify your explanation.
- 5
Gauge the audience's understanding and adjust your communication accordingly.
Example Answers
In my previous role, I analyzed a component failure and found it was due to thermal stress. I summarized the findings without jargon, explaining thermal stress as the overheating of a material. I used a rubber band analogy, describing how it weakens after being stretched too much, making it relatable to the audience.
Tell us about a time you had to quickly adapt to a new tool or technology in failure analysis.
How to Answer
- 1
Select a specific instance that showcases your adaptability.
- 2
Mention the tool or technology you had to learn.
- 3
Describe the context and what was at stake.
- 4
Explain the steps you took to learn and implement the tool.
- 5
Conclude with the outcome and what you learned from the experience.
Example Answers
In my previous role, I was introduced to a new software for data analysis called XyloTech. When I learned that our team would need to use it to analyze failure trends, I quickly enrolled in an online course to get familiar with its features. Within a week, I was able to lead a project using the new tool, resulting in a 20% increase in our analysis efficiency.
Situational Interview Questions
You are given a failure analysis task with a tight deadline. How would you manage your time and resources to ensure timely completion?
How to Answer
- 1
Break down the task into smaller steps to understand priorities
- 2
Set clear milestones and deadlines for each step
- 3
Communicate with stakeholders about progress and any issues
- 4
Utilize tools and resources efficiently to avoid bottlenecks
- 5
Stay focused on critical aspects that impact the deadline
Example Answers
I would start by breaking down the analysis into key components and prioritizing each. Then, I would set a timeline for each part, ensuring I communicate any roadblocks to my team to stay aligned and on schedule.
Imagine you receive conflicting results from two different tests in a failure analysis. How would you proceed?
How to Answer
- 1
Review both test procedures to ensure they were correctly followed.
- 2
Analyze the conditions under which each test was conducted.
- 3
Consult with team members or experts to gather additional insights.
- 4
Perform follow-up tests if feasible to clarify the conflicting results.
- 5
Document all findings and rationales for future reference.
Example Answers
I would first check that both tests were performed under the correct conditions and according to their protocols. Then, I would analyze the context around each test to see if any variables could explain the different outcomes. If necessary, I would consult with my colleagues for their perspectives and run additional tests to confirm the results.
Don't Just Read Failure Analysis Technician Questions - Practice Answering Them!
Reading helps, but actual practice is what gets you hired. Our AI feedback system helps you improve your Failure Analysis Technician interview answers in real-time.
Personalized feedback
Unlimited practice
Used by hundreds of successful candidates
If you were to choose between two techniques to analyze a failure, what factors would influence your decision?
How to Answer
- 1
Consider the type of failure and what data is needed for analysis.
- 2
Evaluate the resources available such as time, tools, and expertise.
- 3
Think about the reliability and accuracy of each technique.
- 4
Take into account past experiences with similar failures.
- 5
Assess the potential impact of the findings on future processes.
Example Answers
I would choose the technique that best suits the specific type of failure, ensuring that I have the necessary tools and expertise available. If one technique has proven more reliable in past experiences, I would be inclined to select that option.
A colleague from another department disagrees with your failure analysis findings. How would you approach resolving this?
How to Answer
- 1
Remain calm and professional during the discussion
- 2
Ask the colleague to explain their perspective clearly
- 3
Review the data together to identify differences in interpretation
- 4
Seek common ground and be open to feedback
- 5
If necessary, involve a neutral third party or supervisor for mediation
Example Answers
I would start by listening to my colleague's concerns and asking them to explain their viewpoint. Once I understand their perspective, we could go through the data together to see if we can identify any discrepancies in our analyses and find a resolution that reflects our findings accurately.
How would you prioritize multiple failure analysis requests when resources are limited?
How to Answer
- 1
Evaluate the impact of each failure on operations and safety
- 2
Consider customer deadlines and contractual obligations
- 3
Assess the complexity and time required for each analysis
- 4
Communicate with stakeholders to understand urgency
- 5
Create a ranking system to systematically prioritize requests
Example Answers
I would start by assessing which failure impacts production safety the most, prioritizing those requests. Then, I would check for any customer commitments to ensure we meet necessary deadlines. Finally, I would estimate the time required for each analysis to better manage our limited resources.
If you notice that the standard procedure for failure analysis is inefficient, what steps would you take to improve it?
How to Answer
- 1
Observe the current procedure and note inefficiencies
- 2
Gather feedback from team members about their challenges
- 3
Analyze data and results to identify bottlenecks
- 4
Propose specific changes or tools that could enhance efficiency
- 5
Document the improved process and share it with the team for further input
Example Answers
I would first observe the current procedure for any inefficiencies. After that, I would gather feedback from my colleagues to understand their pain points. Based on this information, I might propose specific changes, such as integrating new software tools to streamline data analysis.
In a case where your analysis results could cause a significant business impact, how would you ensure the accuracy and integrity of your report?
How to Answer
- 1
Review data thoroughly before presenting results.
- 2
Use multiple validation methods to cross-check findings.
- 3
Document your analysis process for transparency.
- 4
Seek peer review or a second opinion on your work.
- 5
Communicate uncertainties and assumptions clearly.
Example Answers
To ensure the accuracy of my report, I would first double-check the data and calculations, then apply different methods to validate the results. Documentation of my analysis would be critical, and I would also consult with colleagues to confirm my findings.
You are presented with incomplete data in a failure analysis scenario. How would you handle this situation?
How to Answer
- 1
Identify which data is missing and why it is important.
- 2
Consult with team members or stakeholders to gather additional insights.
- 3
Use existing data to make educated assumptions where possible.
- 4
Document all assumptions and the limitations of the analysis.
- 5
Propose a plan to obtain the missing data and follow up.
Example Answers
First, I would analyze what specific data is missing and how it affects the analysis. Then, I would reach out to my team to discuss any previous knowledge they have about the incident. Using the existing data, I would make informed assumptions but clearly document them to highlight the uncertainty. Lastly, I would outline a strategy to collect the needed data and propose timelines for follow-up.
A client asks you to expedite an analysis which usually takes longer. How would you handle this request?
How to Answer
- 1
Acknowledge the client's urgency and the importance of the request.
- 2
Assess the feasibility of expediting the analysis considering available resources.
- 3
Communicate clearly any potential impacts on quality or thoroughness.
- 4
Propose an alternative timeline that balances urgency with thoroughness.
- 5
Confirm the client's expectations and ensure transparency in the process.
Example Answers
I would first reassure the client that I understand their need for a faster analysis. Then, I would evaluate if we can allocate additional resources to meet their request. If speeding up the process might compromise quality, I would explain that and suggest a realistic timeline that prioritizes thoroughness while trying to meet their needs.
You are tasked with conducting multiple analyses, each needing specialized equipment that is in high demand. How would you ensure fair and efficient allocation?
How to Answer
- 1
Assess the urgency and importance of each analysis request.
- 2
Establish a clear and transparent scheduling system for the equipment.
- 3
Communicate with all stakeholders to understand their needs and timelines.
- 4
Implement a priority system based on project deadlines and equipment availability.
- 5
Regularly review allocation to ensure it meets changing demands.
Example Answers
I would first assess each analysis request to determine which are most urgent. Then, I would create a transparent scheduling system, communicating with team members throughout the process to ensure everyone is informed. This way, we can prioritize based on deadlines effectively.
Don't Just Read Failure Analysis Technician Questions - Practice Answering Them!
Reading helps, but actual practice is what gets you hired. Our AI feedback system helps you improve your Failure Analysis Technician interview answers in real-time.
Personalized feedback
Unlimited practice
Used by hundreds of successful candidates
How would you approach developing a new method for analyzing a completely new type of failure you haven't encountered before?
How to Answer
- 1
Research existing analytical methods for similar failures.
- 2
Break down the characteristics of the new failure to understand its nature.
- 3
Collaborate with colleagues or experts in related fields for insights.
- 4
Create a series of experiments to test hypotheses about the failure.
- 5
Document and iterate your method based on findings during testing.
Example Answers
First, I would research existing methods to see if there are techniques applicable to the new failure. Then, I would analyze the specific characteristics of the failure to pinpoint key factors. Collaborating with colleagues could provide fresh perspectives and ideas. I would design experiments to test different hypotheses about the cause of the failure, iterating my approach as I gather data.
Describe how you would handle a situation where two team members have opposing views on the outcome of a failure analysis.
How to Answer
- 1
Listen to both perspectives to understand their reasoning.
- 2
Encourage open dialogue to clarify each point of view.
- 3
Seek evidence and data that supports each argument.
- 4
Facilitate a collaborative discussion to find common ground.
- 5
Suggest a third-party review or additional testing if needed.
Example Answers
I would first listen to both team members to fully understand their viewpoints. Then, I would encourage an open discussion where they can clarify their arguments. After gathering all information, I would look for any data that can support either perspective. If needed, I would suggest bringing in a third-party expert to conduct a review or propose additional tests to reach a conclusion.
How would you manage a situation where a client is unhappy with the time it is taking to conduct a failure analysis?
How to Answer
- 1
Acknowledge the client's frustration immediately
- 2
Communicate what you are doing to expedite the process
- 3
Set realistic expectations about timelines and outcomes
- 4
Keep the client updated on any progress or changes
- 5
Offer to discuss their concerns further to build trust
Example Answers
I would first acknowledge the client's frustration and assure them that I am doing everything I can to speed up the analysis. I would explain the steps we are taking to address the issues and provide regular updates on our progress.
Failure Analysis Technician Position Details
Recommended Job Boards
These job boards are ranked by relevance for this position.
Related Positions
Ace Your Next Interview!
Practice with AI feedback & get hired faster
Personalized feedback
Used by hundreds of successful candidates
Ace Your Next Interview!
Practice with AI feedback & get hired faster
Personalized feedback
Used by hundreds of successful candidates