Top 30 Gasser Interview Questions and Answers [Updated 2025]
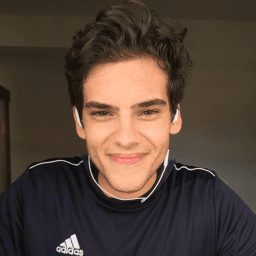
Andre Mendes
•
March 30, 2025
Preparing for a Gasser role interview? Our latest blog post is your go-to resource for mastering the most common interview questions you'll encounter. Dive into a curated list of essential questions, complete with example answers and insightful tips on how to respond effectively. This guide ensures you're well-equipped to impress your interviewers and secure that coveted position. Read on to boost your confidence and ace your interview!
Download Gasser Interview Questions in PDF
To make your preparation even more convenient, we've compiled all these top Gasserinterview questions and answers into a handy PDF.
Click the button below to download the PDF and have easy access to these essential questions anytime, anywhere:
List of Gasser Interview Questions
Behavioral Interview Questions
Can you describe a time when you worked as part of a team to solve a problem related to gas processing?
How to Answer
- 1
Select a specific example from your experience.
- 2
Highlight your role within the team during the problem-solving process.
- 3
Discuss the steps taken to identify and address the gas processing issue.
- 4
Mention the outcome or results achieved as a team.
- 5
Reflect on what you learned from the experience.
Example Answers
In my previous position, our team encountered a gas leak during processing. I coordinated with the safety and engineering departments to quickly assess the situation. We implemented a temporary shutdown and devised a repair plan. As a result, we minimized downtime and ensured safety, which improved our overall processing efficiency by 15%. I learned the importance of clear communication in emergencies.
Tell me about a conflict you had with a coworker regarding safety procedures. How did you resolve it?
How to Answer
- 1
Focus on a specific incident involving safety procedures.
- 2
Explain the differing viewpoints clearly and objectively.
- 3
Describe the steps you took to address and resolve the conflict.
- 4
Highlight the importance of safety in your resolution.
- 5
Mention any follow-up actions or improvements that resulted.
Example Answers
In my last job, a coworker and I disagreed about wearing protective gear in certain areas. I felt it was essential for our safety, while my coworker thought it was unnecessary. I initiated a discussion where we brought in our supervisor for additional input. We reviewed the safety guidelines together, which clarified the importance of the gear. This led to a team meeting where we reinforced the importance of safety compliance, and my coworker became more diligent about following the procedures.
Don't Just Read Gasser Questions - Practice Answering Them!
Reading helps, but actual practice is what gets you hired. Our AI feedback system helps you improve your Gasser interview answers in real-time.
Personalized feedback
Unlimited practice
Used by hundreds of successful candidates
Describe a situation where you had to quickly adapt to changes in safety regulations or technology in your work environment.
How to Answer
- 1
Choose a specific situation that highlights your adaptability.
- 2
Explain the changes in safety regulations or technology clearly.
- 3
Describe your immediate actions and thought process.
- 4
Focus on the positive outcomes of your adaptation.
- 5
Consider including metrics or feedback to demonstrate success.
Example Answers
In my previous role as a plant operator, we were suddenly required to implement new safety protocols due to updated regulations. I quickly reviewed the new guidelines, organized a training session for my team, and ensured everyone was compliant. As a result, we passed our safety audit with no issues.
Give an example of a time you identified a potential hazard in the gassing process and how you addressed it.
How to Answer
- 1
Think of a specific incident where you noticed a hazard.
- 2
Describe the hazard clearly and why it was a concern.
- 3
Explain the steps you took to mitigate the hazard.
- 4
Highlight any collaboration with team members or safety protocols.
- 5
Mention the outcome and any changes made to improve safety.
Example Answers
During a routine gassing process, I noticed a gas leak due to a damaged valve. I immediately stopped the process, informed my supervisor, and initiated the emergency shut-off. We fixed the valve and implemented regular checks on all valves to prevent future leaks.
Have you ever taken the initiative to improve a gas handling process? What was the outcome?
How to Answer
- 1
Identify a specific gas handling process you improved.
- 2
Briefly describe the problem you noticed.
- 3
Explain the initiative you took and why it was important.
- 4
Mention the outcome, focusing on measurable results or improvements.
- 5
Conclude with what you learned from the experience.
Example Answers
I noticed that our gas leak detection system was slow to alert us to potential issues. I took the initiative to redesign the alerts to be more responsive, reducing alarm times by 30%. This improvement enhanced our safety protocols and ensured faster responses to leaks.
Have you ever trained new team members on gas handling procedures? How did you approach the training?
How to Answer
- 1
Start with a brief overview of your training experience.
- 2
Emphasize the importance of safety and compliance during training.
- 3
Describe the methods you used to deliver the training effectively.
- 4
Mention how you tailored the training to different learning styles.
- 5
Include any feedback you received from trainees to show effectiveness.
Example Answers
Yes, I have trained new team members on gas handling procedures. I started by explaining the safety protocols, emphasizing compliance with standards. I used hands-on demonstrations and engaged the trainees with quizzes to ensure understanding. I also adapted my approach based on their learning preferences. Afterward, I received positive feedback on how the training helped them feel more confident.
Can you recall a time when you received constructive feedback on your performance? How did you respond?
How to Answer
- 1
Choose a specific example from your experience
- 2
Explain the feedback clearly and honestly
- 3
Describe your immediate reaction to the feedback
- 4
Discuss the actions you took in response
- 5
Mention the positive outcome or learning from the situation
Example Answers
In my previous role, I received feedback from my manager about my presentation skills. I initially felt a bit defensive, but I recognized the truth in her comments. I took a course on public speaking and practiced more. After implementing this feedback, my presentations became more engaging, and I received compliments from the team.
Describe a project where you led a team to increase efficiency in gas processing. What was your strategy?
How to Answer
- 1
Start with a clear description of the project and the team setup.
- 2
Explain the efficiency issue you identified in gas processing.
- 3
Outline specific strategies or technologies you implemented.
- 4
Discuss how you measured the success of your strategies.
- 5
Mention any challenges faced and how you overcame them.
Example Answers
In a recent project, I led a team of 5 engineers to optimize our gas processing facility. We identified that our gas compression stage was too inefficient, leading to delays. We implemented a new scheduling system and upgraded our compressors, which reduced processing time by 20%. Success was measured through our KPIs, and we overcame resistance by involving the team in decision-making.
What role do you believe a strong safety culture plays in gas handling operations?
How to Answer
- 1
Emphasize the importance of safety culture in preventing accidents.
- 2
Discuss how it encourages proactive behavior among employees.
- 3
Highlight its role in compliance with regulations and standards.
- 4
Mention the impact on operational efficiency and team morale.
- 5
Provide real-world examples or data to support your points.
Example Answers
A strong safety culture is crucial in gas handling operations as it prevents accidents by fostering a mindset of vigilance and responsibility among workers. This culture encourages team members to speak up about safety concerns, which can lead to proactive measures that prevent incidents.
What motivates you to perform your best in the gasser role?
How to Answer
- 1
Identify specific personal values that align with the role
- 2
Discuss how team dynamics drive your performance
- 3
Mention goals or outcomes that inspire you
- 4
Use examples from past experiences to illustrate your motivations
- 5
Express enthusiasm for the challenges and growth opportunities the role offers
Example Answers
I am motivated by the team's success and the opportunity to contribute to a common goal. In my previous job, working together to overcome challenges drove me to excel and achieve great results.
Don't Just Read Gasser Questions - Practice Answering Them!
Reading helps, but actual practice is what gets you hired. Our AI feedback system helps you improve your Gasser interview answers in real-time.
Personalized feedback
Unlimited practice
Used by hundreds of successful candidates
Technical Interview Questions
Explain how you would troubleshoot a gas leak detection system that is not functioning properly.
How to Answer
- 1
Start by checking the power supply to the system to ensure it is operational.
- 2
Inspect sensors for any physical damage or disconnection that might affect functionality.
- 3
Run diagnostics if available to identify error codes or malfunctions.
- 4
Test the system with known gas sources to check sensor response.
- 5
Review system logs and settings to ensure proper configuration.
Example Answers
First, I would check the power supply to make sure the gas leak detection system is powered on and functioning. Then, I would inspect all sensors for any signs of damage or disconnection.
What types of gas processing equipment are you experienced with, and what is your role in its operation?
How to Answer
- 1
Identify specific types of gas processing equipment you have worked with
- 2
Describe your direct role in operating or maintaining that equipment
- 3
Focus on relevant experiences that highlight your technical skills
- 4
Mention any safety protocols or procedures you followed
- 5
Keep your answer concise and to the point, limit to key experiences
Example Answers
I have experience working with compressors and separators. In my previous role, I operated and performed routine maintenance on these machines, ensuring they functioned efficiently and safely.
Don't Just Read Gasser Questions - Practice Answering Them!
Reading helps, but actual practice is what gets you hired. Our AI feedback system helps you improve your Gasser interview answers in real-time.
Personalized feedback
Unlimited practice
Used by hundreds of successful candidates
What safety standards do you follow when working with gases, and how do you ensure compliance?
How to Answer
- 1
Mention specific safety standards relevant to gas handling such as OSHA or NFPA.
- 2
Describe personal protective equipment (PPE) you utilize.
- 3
Include safety procedures like leak detection and ventilation.
- 4
Explain training and regular safety audits you participate in.
- 5
Discuss emergency response plans and drills in place.
Example Answers
I follow OSHA and NFPA standards for gas safety, ensuring that my team always wears PPE, including gloves and goggles. We conduct regular leak tests and maintain good ventilation in all work areas. I keep up with training sessions and participate in safety audits to ensure compliance.
Can you describe the techniques you use to measure gas flow rates and ensure accuracy?
How to Answer
- 1
Start by mentioning specific flow measurement devices you are familiar with.
- 2
Explain how you calibrate these devices to ensure accuracy.
- 3
Discuss any methods you use to validate the measurements.
- 4
Include any relevant standards or protocols you follow.
- 5
Mention any software tools or data analysis techniques you use.
Example Answers
I typically use mass flow meters and orifice plates for measuring gas flow rates. To ensure accuracy, I calibrate these devices regularly according to manufacturer's specifications. I also cross-check readings using a secondary device to validate the measurements, following ISO standards for flow measurement.
What steps do you take to respond to a gas leak emergency?
How to Answer
- 1
Evacuate the area immediately and ensure everyone's safety
- 2
Notify emergency services and report the leak
- 3
Avoid using electrical devices or flames to reduce fire risk
- 4
Secure the area and prevent others from entering until help arrives
- 5
Provide accurate information to responders about the situation
Example Answers
In the event of a gas leak, I would first ensure everyone's safety by evacuating the area. Then I would notify emergency services and explicitly describe the location and nature of the leak. I would also secure the area to prevent unauthorized access until professionals arrive.
What quality control measures do you implement to ensure the integrity of gas products?
How to Answer
- 1
Discuss regular inspections and audits of gas products.
- 2
Mention calibration and maintenance of measurement equipment.
- 3
Explain use of quality control charts to monitor production.
- 4
Describe training programs for staff on quality standards.
- 5
Include compliance with industry regulations and safety standards.
Example Answers
I implement regular audits and inspections to ensure gas products meet safety standards. Additionally, I ensure all measurement equipment is properly calibrated and maintained.
What experience do you have with compliance to environmental regulations in gas handling?
How to Answer
- 1
Identify specific regulations you have worked with
- 2
Discuss your roles in ensuring compliance
- 3
Provide examples of how you managed compliance issues
- 4
Mention any training or certifications relevant to environmental regulations
- 5
Highlight your understanding of the impact of non-compliance
Example Answers
In my previous role as a gas technician, I ensured compliance with the EPA regulations by conducting regular inspections and audits of our gas handling processes. I also trained my team on the importance of these regulations to minimize environmental risks.
What methods do you use to control gas emissions during processing?
How to Answer
- 1
Explain specific technologies or systems you implement.
- 2
Discuss regular monitoring and compliance checks you perform.
- 3
Mention training practices for staff on emission controls.
- 4
Include methods for capturing and reducing emissions during processing.
- 5
Highlight any innovations or improvements you have initiated.
Example Answers
I implement scrubbers and filtration systems to minimize gas emissions and routinely monitor our processes to ensure compliance with regulations.
How do you analyze performance data from gas processing to identify areas for improvement?
How to Answer
- 1
Gather relevant performance data such as throughput, efficiency, and downtime.
- 2
Use statistical tools to analyze trends and patterns in the data.
- 3
Identify bottlenecks or anomalies that impact performance.
- 4
Benchmark performance against industry standards or past performance.
- 5
Collaborate with cross-functional teams to validate findings and implement solutions.
Example Answers
I gather data on throughput and efficiency metrics, then use trend analysis to identify any drops in performance. By looking at historical data, I can spot patterns and compare them against industry benchmarks.
Can you explain how you would approach optimizing the gas mixing process for better efficiency?
How to Answer
- 1
Analyze current gas mixing data to identify inefficiencies.
- 2
Implement monitoring systems to track gas proportions in real-time.
- 3
Experiment with different mixing techniques or equipment.
- 4
Collaborate with team members to gather insights and suggestions.
- 5
Evaluate the impact of changes using key performance indicators.
Example Answers
I would start by analyzing the current gas mixing data to find where inefficiencies occur. Then, I would install monitoring systems that allow us to track gas proportions and adjust them in real-time for optimal results.
Don't Just Read Gasser Questions - Practice Answering Them!
Reading helps, but actual practice is what gets you hired. Our AI feedback system helps you improve your Gasser interview answers in real-time.
Personalized feedback
Unlimited practice
Used by hundreds of successful candidates
Situational Interview Questions
If you discover a malfunction in the gasser's pressure control system, what immediate actions would you take?
How to Answer
- 1
Assess the nature of the malfunction to understand its severity
- 2
Activate emergency protocols to safeguard personnel and equipment
- 3
Isolate the affected system to prevent further damage or risk
- 4
Notify your supervisor and relevant personnel about the issue
- 5
Document the malfunction and the actions taken for future reference
Example Answers
First, I would evaluate the issue to determine if it's critical or can be monitored. If it poses an immediate danger, I would activate emergency protocols and isolate the system. Then I would inform my supervisor and document the steps taken.
How would you communicate a critical safety issue concerning gas handling to your team?
How to Answer
- 1
Identify the critical safety issue clearly and concisely
- 2
Use simple language to explain the risks involved
- 3
Communicate the necessary immediate actions to take
- 4
Ensure all team members understand their roles in the situation
- 5
Follow up with a summary message for clarity and record keeping
Example Answers
I would start by clearly stating the safety issue, such as a gas leak detected in area X. Then, I would explain the risks of exposure and potential hazards. I would instruct everyone to evacuate the area and follow safety protocols immediately. Afterward, I would ensure everyone understood their responsibilities and send out a follow-up message summarizing the issue and actions taken.
Don't Just Read Gasser Questions - Practice Answering Them!
Reading helps, but actual practice is what gets you hired. Our AI feedback system helps you improve your Gasser interview answers in real-time.
Personalized feedback
Unlimited practice
Used by hundreds of successful candidates
Imagine you have to assess the risk of a new gas blending process. What factors would you consider?
How to Answer
- 1
Identify potential hazards associated with each gas involved.
- 2
Evaluate the process conditions such as temperature and pressure.
- 3
Consider regulatory compliance and industry standards.
- 4
Assess the equipment reliability and maintenance history.
- 5
Analyze human factors, including operator training and experience.
Example Answers
I would first evaluate the hazards of each gas, like toxicity and flammability. Then, I would analyze the blending conditions, ensuring they're within safe limits. I would also check compliance with safety regulations and the reliability of our equipment before considering operator training and experience level.
You have multiple gas cylinders to process, but limited time. How would you prioritize which ones to work on first?
How to Answer
- 1
Identify cylinders with immediate safety hazards and address them first
- 2
Prioritize cylinders based on their purpose or usage urgency
- 3
Consider the size and weight of the cylinders for efficient handling
- 4
Evaluate the distance to transport the cylinders to determine efficiency
- 5
Consult with team members or protocols for any specific prioritization guidelines
Example Answers
I would first check for any cylinders that pose a safety hazard and ensure those are processed immediately. Next, I would prioritize cylinders based on their urgency for active projects or scheduled uses. Lastly, I would consider handling ease and transport distance.
How would you collaborate with maintenance staff when an issue arises with the gas delivery system?
How to Answer
- 1
Communicate clearly and calmly about the issue at hand
- 2
Identify the specific problem and gather relevant data before discussing with maintenance
- 3
Schedule a joint meeting to discuss the issue and potential solutions
- 4
Ensure all voices are heard and encourage input from maintenance staff
- 5
Follow up after the issue is resolved to evaluate the collaboration process
Example Answers
I would first assess the situation and gather all relevant information regarding the gas delivery issue. Then, I would present this data to the maintenance staff in a meeting, ensuring we all understand the problem. Collaboration is key, so I would encourage their insights and work together to develop a solution.
If you're faced with a new piece of gas processing equipment that you have never worked with before, how would you approach learning it?
How to Answer
- 1
Research the equipment's specifications and operation manuals.
- 2
Consult with experienced colleagues or mentors for insights.
- 3
Attend training sessions or workshops if available.
- 4
Observe the equipment in operation to understand its functionality.
- 5
Take notes and create a quick reference guide for future use.
Example Answers
I would start by reviewing the equipment's manuals and specifications to understand its basic functions. Then, I would reach out to a colleague who has experience with it for tips and best practices. If there's a training available, I would sign up for that to gain hands-on experience.
If you had to manage a limited budget for gas handling supplies, how would you allocate resources?
How to Answer
- 1
Prioritize critical supplies that ensure safety and compliance
- 2
Evaluate cost-effective alternatives without sacrificing quality
- 3
Allocate a portion of the budget for emergency or unexpected expenses
- 4
Consider bulk purchasing for items with long-term use
- 5
Plan for future needs based on usage trends and maintenance schedules
Example Answers
I would first allocate funds to essential safety equipment and regulatory compliance items. Then I'd look for bulk purchasing options on regular supplies to save costs. Finally, I'd set aside some budget for unforeseen needs or repairs.
If you noticed a team member struggling with their workload, what steps would you take to support them?
How to Answer
- 1
Start by having a private conversation to understand their challenges.
- 2
Offer to help prioritize their tasks to manage workload better.
- 3
Suggest sharing tasks temporarily if workload allows.
- 4
Encourage open communication and check in regularly after the conversation.
- 5
Offer resources or advise on techniques for time management.
Example Answers
I would first talk to them privately to understand their situation. Then, I would help them prioritize tasks and suggest we share some of their workload if possible.
If a regulatory inspector arrives unexpectedly, how would you handle the situation?
How to Answer
- 1
Stay calm and composed to convey professionalism.
- 2
Greet the inspector warmly and introduce yourself.
- 3
Inquire about the purpose of their visit, ensuring you understand their needs.
- 4
Provide access to necessary documents and areas without delay.
- 5
Communicate with your supervisor immediately to keep them informed.
Example Answers
I would greet the inspector promptly, introduce myself, and calmly ask about the purpose of their visit. Then, I'd ensure they have access to any required documents or areas and notify my supervisor right away.
If the gas purity levels were not meeting standards, what steps would you take to determine the cause?
How to Answer
- 1
Check calibration of measurement equipment for accuracy
- 2
Review recent changes in processes or materials that could affect purity
- 3
Analyze historical data for trends or patterns in purity levels
- 4
Conduct sampling and testing of the gas at various stages of production
- 5
Consult with team members or experts who may have insights into the issue
Example Answers
I would first check the calibration of the measuring equipment to ensure it's providing accurate readings. Then, I would review any recent changes to our materials or processes that could be impacting gas purity. If needed, I would analyze our historical data to identify any trends that correlate with dips in purity levels.
Don't Just Read Gasser Questions - Practice Answering Them!
Reading helps, but actual practice is what gets you hired. Our AI feedback system helps you improve your Gasser interview answers in real-time.
Personalized feedback
Unlimited practice
Used by hundreds of successful candidates
Gasser Position Details
Recommended Job Boards
ZipRecruiter
www.ziprecruiter.com/Jobs/GasserThese job boards are ranked by relevance for this position.
Related Positions
Similar positions you might be interested in.
Ace Your Next Interview!
Practice with AI feedback & get hired faster
Personalized feedback
Used by hundreds of successful candidates
Ace Your Next Interview!
Practice with AI feedback & get hired faster
Personalized feedback
Used by hundreds of successful candidates