Top 27 Laminator Interview Questions and Answers [Updated 2025]
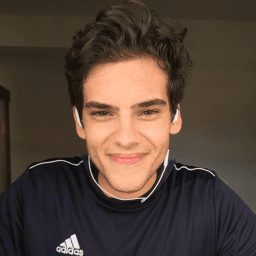
Andre Mendes
•
March 30, 2025
Preparing for a laminator job interview can be daunting, but knowing what to expect is half the battle. This blog post dives into the most common interview questions for the laminator role, providing you with example answers and effective tips to help you stand out. Whether you're a seasoned professional or new to the field, this guide will equip you with the insights needed to impress your interviewers.
Download Laminator Interview Questions in PDF
To make your preparation even more convenient, we've compiled all these top Laminatorinterview questions and answers into a handy PDF.
Click the button below to download the PDF and have easy access to these essential questions anytime, anywhere:
List of Laminator Interview Questions
Behavioral Interview Questions
Can you describe a time when you encountered a significant issue while laminating materials? How did you resolve it?
How to Answer
- 1
Identify a specific laminating issue you faced.
- 2
Explain the impact of the issue on the project or materials.
- 3
Detail the steps you took to troubleshoot and resolve the issue.
- 4
Highlight any skills or techniques you used in the resolution.
- 5
Discuss the outcome and any lessons learned from the experience.
Example Answers
In my previous job, I noticed air bubbles forming under the laminate during a large project. This was affecting the quality of the finish. I quickly stopped the laminator, checked for any misalignment, and recalibrated the machine. After restarting, I carefully monitored the process to ensure a smooth finish. The project was completed on time, and we had zero complaints from the client.
Tell me about a successful project where you collaborated with others in your laminating work. What was your role?
How to Answer
- 1
Identify a specific project that highlights teamwork.
- 2
Outline your role and responsibilities clearly.
- 3
Mention the skills or techniques you used in laminating.
- 4
Describe the outcome and any measurable results.
- 5
Reflect on what you learned from the collaboration.
Example Answers
In a project at my last job, I worked with a team to create a series of laminated product samples for a client. My role was to manage the laminating process, ensuring that we used the right materials and techniques. We produced a high-quality prototype that impressed the client, leading to a 25% increase in orders.
Don't Just Read Laminator Questions - Practice Answering Them!
Reading helps, but actual practice is what gets you hired. Our AI feedback system helps you improve your Laminator interview answers in real-time.
Personalized feedback
Unlimited practice
Used by hundreds of successful candidates
Give an example of how your attention to detail has made a difference in the quality of laminated products.
How to Answer
- 1
Identify a specific instance where you noticed a detail that others missed.
- 2
Explain the steps you took to address the issue.
- 3
Discuss the positive outcome resulting from your attention to detail.
- 4
Use metrics or feedback to highlight the improvement.
- 5
Keep your answer focused and relevant to the laminating process.
Example Answers
In a previous role, I noticed that some laminated sheets had air bubbles. I took the initiative to adjust the machine's settings and retrain my team on proper application techniques. As a result, we reduced defects by 30% in the next batch, which led to higher customer satisfaction.
Describe a situation where you had to adapt your laminating process due to unexpected changes or challenges.
How to Answer
- 1
Identify the unexpected change you encountered.
- 2
Explain how you assessed the situation quickly.
- 3
Detail the adjustments you made to the laminating process.
- 4
Share the positive outcome or what you learned.
- 5
Keep your response concise and focused on your actions.
Example Answers
While laminating a large batch of documents, the laminator jammed unexpectedly. I quickly turned off the machine, removed the jammed sheets, and adjusted the settings to accommodate the thickness. After recalibrating, I successfully completed the batch on time, ensuring quality and customer satisfaction.
How have you prioritized tasks when working on multiple laminating projects with tight deadlines?
How to Answer
- 1
Identify project deadlines and specific requirements for each task
- 2
Assess the complexity and time needed for each laminating project
- 3
Communicate with team members about priorities and resource allocation
- 4
Create a step-by-step plan to tackle tasks in the order of urgency and importance
- 5
Continuously review and adjust priorities as new projects come in
Example Answers
In my previous role, I kept a checklist of all incoming laminating projects along with their deadlines. I prioritized based on urgency and complexity, ensuring I addressed the most critical tasks first while communicating with my team to allocate the necessary resources.
Discuss a time when you had to communicate complex instructions to a team member regarding laminating techniques.
How to Answer
- 1
Identify a specific project where you communicated lamination techniques.
- 2
Use clear and simple language, avoiding jargon.
- 3
Break down the instructions into step-by-step procedures.
- 4
Check for understanding by asking questions.
- 5
Provide feedback and support during the lamination process.
Example Answers
During a project to laminate educational materials, I explained the process step-by-step. I started with preparing the materials, then demonstrated the machine settings, and finally showed how to trim the edges. I paused to ask if my colleague had any questions, ensuring they understood each part before proceeding.
Describe a time when you took the lead on a laminating project. What challenges did you face, and how did you overcome them?
How to Answer
- 1
Identify a specific laminating project you led.
- 2
Explain the unique challenges faced during the project.
- 3
Describe the steps you took to address those challenges.
- 4
Highlight the outcome and any positive feedback received.
- 5
Reflect on what you learned for future projects.
Example Answers
I led a laminating project for a company brochure. One challenge was that the laminator jammed frequently. I researched the issue and discovered it was due to incorrect settings. I adjusted the temperature and pressure, resulting in a smooth production. The final product received praise for its quality.
What steps have you taken to keep up with advancements in laminating technology and techniques?
How to Answer
- 1
Attend workshops or training sessions on new laminating equipment.
- 2
Join industry forums or online communities to share and learn about innovations.
- 3
Subscribe to trade magazines focused on laminating and printing.
- 4
Follow manufacturers' updates and product releases to stay informed.
- 5
Experiment with new laminating materials and techniques in your current work.
Example Answers
I regularly attend workshops on laminating technology, which helps me understand the latest equipment. I also subscribe to a couple of trade magazines to keep up with innovations.
Tell me about a time when you introduced a new technique or process in your laminating work. What was the outcome?
How to Answer
- 1
Identify a specific technique you introduced.
- 2
Explain the problem it aimed to solve.
- 3
Describe the steps you took to implement it.
- 4
Share measurable outcomes or improvements.
- 5
Reflect on any feedback received from colleagues or supervisors.
Example Answers
I introduced a temperature control technique that ensured even lamination. This addressed the issue of bubbles forming during the process. I implemented it by adjusting the machine settings and conducting trials. As a result, we reduced bubble complaints by 30%, and my supervisor praised the improved quality.
Technical Interview Questions
What types of laminating machines are you experienced with, and what are their key operational features?
How to Answer
- 1
List specific types of laminators you have used, such as roll, pouch, or cold laminators
- 2
Highlight the main features of each type, like speed, temperature control, or feed capacity
- 3
Mention any relevant brands you have experience with for credibility
- 4
Discuss the environments you have worked in, such as print shops or corporate settings
- 5
Share any additional skills, like maintenance knowledge or troubleshooting experience
Example Answers
I have experience with both roll and pouch laminators. The roll laminator I used ran at 10 feet per minute with adjustable temperature settings, perfect for larger projects. The pouch laminator offered a quick warm-up time and could accommodate different pouch sizes, making it versatile for various documents.
Can you explain the differences between various laminating materials and the impact they have on the final product?
How to Answer
- 1
Identify common laminating materials like PVC, polyester, and nylon.
- 2
Discuss the thickness and finish of the laminating material.
- 3
Explain how different materials affect durability and appearance.
- 4
Mention specific applications for each type of laminating material.
- 5
Consider environmental factors or certifications if relevant.
Example Answers
There are several types of laminating materials like PVC, which is cost-effective and durable, and polyester, which offers a crystal clear finish. Thicker laminates provide better durability, while the choice of finish can impact gloss and texture. For instance, PVC is often used for low-cost projects, while polyester might be preferred for professional presentations.
Don't Just Read Laminator Questions - Practice Answering Them!
Reading helps, but actual practice is what gets you hired. Our AI feedback system helps you improve your Laminator interview answers in real-time.
Personalized feedback
Unlimited practice
Used by hundreds of successful candidates
What quality control measures do you implement during the laminating process to ensure product consistency?
How to Answer
- 1
Conduct regular inspections of the film and substrate for defects before laminating.
- 2
Monitor temperature and pressure settings consistently to match product specifications.
- 3
Perform test runs to check adhesion and finish quality on sample materials.
- 4
Use checklists to document each step of the process for consistency.
- 5
Maintain equipment regularly and calibrate it to ensure optimal performance.
Example Answers
I always inspect the film and substrate for any defects prior to laminating. This initial check helps prevent issues downstream. I also monitor temperature and pressure closely to ensure they align with specifications.
What safety protocols do you follow when operating laminating equipment?
How to Answer
- 1
Always wear appropriate personal protective equipment, including gloves and safety glasses
- 2
Inspect the laminator for any damage or wear before use
- 3
Keep hands and loose clothing away from moving parts during operation
- 4
Ensure the machine is properly calibrated and set before starting the laminating process
- 5
Follow specific manufacturer's instructions and safety guidelines for the equipment
Example Answers
I prioritize safety by wearing gloves and safety glasses while laminating. I also check the equipment for any damages before use and keep my hands clear of moving parts.
How do you troubleshoot common issues that arise during the laminating process?
How to Answer
- 1
Identify the symptoms of the problem, like bubbling or wrinkling.
- 2
Check the machine settings, ensuring the temperature and pressure are correct.
- 3
Inspect the lamination film for defects or compatibility issues.
- 4
Clean the rollers and feeding mechanisms to avoid jams.
- 5
Test with a sample before proceeding with a large batch.
Example Answers
I first identify the issue by looking for bubbles or wrinkles during the process. Then, I check the machine settings to make sure the temperature and pressure are optimal. If everything seems fine, I inspect the film for defects.
Can you discuss any finishing techniques you apply after laminating and why they are important?
How to Answer
- 1
Mention common finishing techniques like trimming, corner rounding, and adding holes for binding.
- 2
Explain the purpose of each technique, such as improving aesthetics or functionality.
- 3
Emphasize the importance of quality control in ensuring the final product meets standards.
- 4
Share how these techniques enhance durability or usability for end users.
- 5
Provide examples of projects where you successfully utilized these finishing techniques.
Example Answers
After laminating, I usually trim edges to remove excess material, which gives a clean look. I also round corners to prevent peeling, as sharp edges can wear quickly. This attention to detail ensures a professional finish that lasts longer.
Are you familiar with any software used for managing laminating processes or orders? Can you describe your experience?
How to Answer
- 1
Research common laminating software before the interview.
- 2
Mention any specific software you've used, like PrintSmith or EFI.
- 3
Explain how the software improved workflow or order management.
- 4
Share a brief example of a situation where you used the software effectively.
- 5
Emphasize your willingness to learn new software if needed.
Example Answers
In my last role, I used PrintSmith to manage laminating orders which streamlined our workflow. It allowed me to track jobs in real-time, reducing turnaround time by 20%.
How do you measure the success of your laminating processes in terms of efficiency and output?
How to Answer
- 1
Identify key performance indicators like speed, quality, and waste.
- 2
Track output quantity against preset targets regularly.
- 3
Analyze downtime and identify causes for inefficiencies.
- 4
Collect feedback from team members on process adjustments.
- 5
Use data to optimize settings for different materials and projects.
Example Answers
I measure success by analyzing the speed of the laminating process, ensuring it meets our output targets, and minimizing waste. I frequently check the quality of the finished product and adjust settings as needed.
What routine maintenance tasks do you believe are essential for keeping laminating machines in optimal condition?
How to Answer
- 1
Regularly clean the rollers to prevent adhesive buildup.
- 2
Check and replace worn or damaged parts, such as belts and blades.
- 3
Ensure proper lubrication of moving parts as per the manufacturer's schedule.
- 4
Inspect electrical connections and power supply for safety.
- 5
Maintain a clean workspace to avoid dust and debris interference.
Example Answers
I believe essential tasks include cleaning the rollers frequently to avoid adhesive and ensuring that all moving parts are well-lubricated to prevent wear and tear.
What signs do you look for when identifying potential problems during the laminating process?
How to Answer
- 1
Check for bubbles or wrinkles in the laminate film
- 2
Monitor the temperature settings; too high or low can cause issues
- 3
Listen for unusual noises from the laminator, indicating mechanical problems
- 4
Observe the evenness of the laminate application; uneven coverage is a red flag
- 5
Ensure proper feed alignment; misalignment can cause jams or incomplete lamination
Example Answers
I look for bubbles or wrinkles in the laminate, as they indicate issues with adhesion. I also monitor the temperature settings closely to avoid problems.
Don't Just Read Laminator Questions - Practice Answering Them!
Reading helps, but actual practice is what gets you hired. Our AI feedback system helps you improve your Laminator interview answers in real-time.
Personalized feedback
Unlimited practice
Used by hundreds of successful candidates
Situational Interview Questions
If a customer reports that a batch of laminated products did not meet their specifications, how would you handle the situation?
How to Answer
- 1
Listen carefully to the customer's concerns and gather specifics about the issue
- 2
Apologize for the inconvenience and assure them you will investigate the matter
- 3
Review production parameters and quality control measures quickly
- 4
Communicate your findings to the customer and propose a solution or replacement
- 5
Follow up to ensure the customer is satisfied and prevent future issues
Example Answers
I would first listen to the customer's concerns and gather details on what specifications were not met. I would apologize for any inconvenience and assure them I would investigate the situation promptly. After reviewing our production process, I would communicate my findings and propose a solution, such as a replacement or refund. Finally, I would follow up with the customer to ensure their satisfaction.
Imagine you are producing laminated materials, and you notice a recurring defect. What steps would you take to investigate and improve the process?
How to Answer
- 1
Identify the specific defect and document its frequency and conditions
- 2
Review the current laminating process and equipment settings
- 3
Collect feedback from team members involved in the process
- 4
Test different materials and laminating techniques to identify variations
- 5
Implement changes and monitor results to ensure improvement
Example Answers
First, I would record the details of the defect, noting when and how often it occurs. Then, I’d analyze the laminating process to check if any settings or materials might need adjustments. Gathering input from my colleagues could provide additional insights. After that, I would experiment with alternative materials and methods to see if improvements could be made. Lastly, I’d track the outcomes of any changes to confirm that they effectively reduced the defects.
Don't Just Read Laminator Questions - Practice Answering Them!
Reading helps, but actual practice is what gets you hired. Our AI feedback system helps you improve your Laminator interview answers in real-time.
Personalized feedback
Unlimited practice
Used by hundreds of successful candidates
If you were asked to laminate a large order with limited materials, how would you manage the resources to meet the deadline?
How to Answer
- 1
Assess the size and type of items to be laminated.
- 2
Prioritize the most critical items for lamination.
- 3
Calculate the available material and how much each item requires.
- 4
Consider using alternative lamination techniques if applicable.
- 5
Communicate with your team and stakeholders about progress and any potential challenges.
Example Answers
I would start by evaluating the order to identify the most critical items that need to be laminated first. I would assess the available materials to determine how much I can laminate. Then, I would prioritize those items based on urgency and ensure transparency with my team about our resources and timeline.
How would you approach a conflict with a colleague regarding the preferred laminating technique for a project?
How to Answer
- 1
Listen actively to your colleague's perspective on the technique.
- 2
Clearly explain your rationale for your preferred laminating method.
- 3
Suggest conducting a small test with both techniques for comparison.
- 4
Focus on the project's goals and what method achieves them best.
- 5
Maintain a collaborative attitude and be open to compromise.
Example Answers
I would first listen to my colleague's reasoning behind their preferred technique. Then, I would share my insights and suggest we run a test with both methods to see which is more effective for our project's needs.
You are given a new laminating material that you are unfamiliar with. How would you ensure that the quality is up to standard?
How to Answer
- 1
Review the manufacturer's specifications and guidelines for the new material.
- 2
Conduct test laminations on sample materials to evaluate compatibility and finish.
- 3
Check for adhesion quality and any bubbling or wrinkling issues after lamination.
- 4
Consult with colleagues or industry experts for insights on similar materials.
- 5
Document results from tests to establish a quality baseline for future reference.
Example Answers
I would start by reviewing the manufacturer's specifications to understand the properties of the new laminating material. Then, I would perform test laminations on different substrates to see how well it adheres and holds up. I would look for any defects like bubbling or wrinkles before documenting my findings.
If a client requests a specific laminate finish that is not typically used, how would you address their needs?
How to Answer
- 1
Ask clarifying questions to understand the client's vision.
- 2
Research the requested finish and check feasibility.
- 3
Discuss alternative options that might achieve a similar effect.
- 4
Communicate openly about any limitations or potential issues.
- 5
Confirm the client's preferences before proceeding with a decision.
Example Answers
I would start by asking the client detailed questions about the specific finish they're looking for. Then, I would research if we can achieve that effect and present any viable alternatives if necessary. Keeping the client informed is key.
You have been given a tight deadline for a new laminating project. What planning strategies would you implement to meet the deadline?
How to Answer
- 1
Assess the scope of the project to understand requirements and materials needed
- 2
Create a detailed timeline with specific milestones
- 3
Prioritize tasks based on urgency and complexity
- 4
Communicate with team members to delegate responsibilities
- 5
Monitor progress regularly and adjust the plan as needed
Example Answers
I would start by assessing the project requirements and materials. Then, I would create a detailed timeline that includes key milestones. I would prioritize tasks and communicate clearly with my team to ensure everyone knows their responsibilities.
If you were under significant pressure during a busy production day, how would you maintain focus and quality in your work?
How to Answer
- 1
Prioritize tasks by focusing on the most critical ones first.
- 2
Take brief breaks to clear your mind and reset your focus.
- 3
Double-check your work regularly to catch errors early.
- 4
Communicate with team members to share responsibilities and resolve issues.
- 5
Stay organized by keeping your workstation tidy and having materials ready.
Example Answers
During busy days, I prioritize tasks by handling the most urgent laminations first. I take short breaks to refresh my mind, which helps me stay focused.
Laminator Position Details
Recommended Job Boards
Randstad USA
www.randstadusa.com/jobs/q-fiberglass-laminator/These job boards are ranked by relevance for this position.
Related Positions
- Laminating Machine Operator
- Waterproofer
- Fiberglass Laminator
- Lumper
- Stapler
- Liner Installer
- Plastic Finisher
- Laster
- Lumpia Wrapper Maker
- Carton Liner
Similar positions you might be interested in.
Ace Your Next Interview!
Practice with AI feedback & get hired faster
Personalized feedback
Used by hundreds of successful candidates
Ace Your Next Interview!
Practice with AI feedback & get hired faster
Personalized feedback
Used by hundreds of successful candidates