Top 29 Laminating Machine Operator Interview Questions and Answers [Updated 2025]
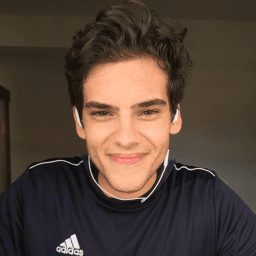
Andre Mendes
•
March 30, 2025
Preparing for a Laminating Machine Operator interview can be daunting, but we're here to help streamline your preparation. In this blog post, we cover some of the most common interview questions for this role, complete with example answers and practical tips on how to respond effectively. Whether you're a seasoned operator or new to the field, these insights will equip you with the confidence to impress your potential employer.
Download Laminating Machine Operator Interview Questions in PDF
To make your preparation even more convenient, we've compiled all these top Laminating Machine Operatorinterview questions and answers into a handy PDF.
Click the button below to download the PDF and have easy access to these essential questions anytime, anywhere:
List of Laminating Machine Operator Interview Questions
Behavioral Interview Questions
Can you describe a time when you worked with a team to solve a problem during the laminating process?
How to Answer
- 1
Identify a specific issue you faced as a team during laminating.
- 2
Explain your role and the actions you took to contribute.
- 3
Describe the solution the team implemented and its outcome.
- 4
Emphasize teamwork and communication throughout the process.
- 5
Highlight any lessons learned or improvements made for future processes.
Example Answers
In my previous job, we faced frequent paper jams in the laminating machine. I organized a team meeting to discuss the issue, where I shared my observations and suggested a new feeding technique. After implementing this change, we reduced jams by 30%. This experience taught us the importance of clear communication and proactive problem-solving.
Tell me about a conflict you faced while operating a laminating machine and how you resolved it.
How to Answer
- 1
Identify a specific conflict related to machine operation.
- 2
Explain the impact of the conflict on production or workflow.
- 3
Describe the steps you took to resolve the issue.
- 4
Highlight any collaboration with team members during the resolution.
- 5
Conclude with the positive outcome and what you learned from the experience.
Example Answers
Once, the laminating machine jammed during a large production run, causing delays. I immediately informed my supervisor and stopped the machine to prevent further damage. After working with a colleague to clear the jam, we recalibrated the settings. This experience taught me the importance of quick communication and teamwork, and we were able to catch up on production by working overtime.
Don't Just Read Laminating Machine Operator Questions - Practice Answering Them!
Reading helps, but actual practice is what gets you hired. Our AI feedback system helps you improve your Laminating Machine Operator interview answers in real-time.
Personalized feedback
Unlimited practice
Used by hundreds of successful candidates
Describe a situation where you had to troubleshoot a malfunction in the laminating machine. What steps did you take?
How to Answer
- 1
Identify the specific malfunction and symptoms clearly.
- 2
Explain the steps taken to diagnose the issue.
- 3
Describe any tools or methods used during troubleshooting.
- 4
Share the outcome after the issue was resolved.
- 5
Highlight any lessons learned for future maintenance.
Example Answers
At my previous job, the laminating machine began producing wrinkled laminates. I checked the film tension and found it was too tight. I adjusted the tension settings, ran a test, and confirmed the issue was resolved. This experience taught me the importance of regular tension checks.
Can you provide an example of how you adapted to changes in production schedules or tasks?
How to Answer
- 1
Think of a specific situation where the schedule changed unexpectedly.
- 2
Describe your immediate reaction to the change.
- 3
Explain the steps you took to adapt and ensure production continued smoothly.
- 4
Highlight any teamwork or communication that helped with the transition.
- 5
Conclude with the positive outcome resulting from your adaptability.
Example Answers
In my previous role, our production schedule changed due to a supplier delay. I quickly reassessed the tasks and shifted focus to prioritize the available materials. I communicated with my team to ensure everyone was aligned, and we were able to maintain a steady output, ultimately meeting our weekly targets.
Describe a time you noticed a safety hazard while operating machinery. What did you do?
How to Answer
- 1
Think of a specific incident where you identified a safety risk.
- 2
Explain the steps you took to address the hazard immediately.
- 3
Mention who you informed about the hazard and why communication is important.
- 4
Reflect on any changes or improvements made to prevent future issues.
- 5
Emphasize your commitment to safety and compliance with regulations.
Example Answers
While operating the laminating machine, I noticed a frayed wire that could potentially cause a short circuit. I immediately unplugged the machine and reported the issue to my supervisor. Together, we arranged for maintenance to replace the wire, ensuring no one else was at risk while using the equipment.
Have you ever trained someone else on operating a laminating machine? How did you approach it?
How to Answer
- 1
Describe the trainee's experience level to set context.
- 2
Focus on step-by-step instructions you provided.
- 3
Mention any resources or materials you used during training.
- 4
Include how you assessed their understanding and progress.
- 5
Highlight any follow-up support you offered post-training.
Example Answers
I trained a new hire with no experience. I broke down the process into clear steps, demonstrating each one while using a training manual. I provided hands-on practice sessions and checked in regularly to ensure they understood.
Have you ever suggested or implemented an improvement to the laminating process? What was it and what was the outcome?
How to Answer
- 1
Identify a specific improvement you suggested or implemented.
- 2
Explain the rationale behind your suggestion and how it addressed a problem.
- 3
Describe the implementation process and any challenges faced.
- 4
Share measurable outcomes or improvements resulting from the change.
- 5
Highlight what you learned from the experience.
Example Answers
I suggested reducing the temperature on the laminating machine because we were experiencing warping in some materials. After implementing it, we saw a 30% reduction in defects and the process ran smoother.
What motivates you the most while working as a laminating machine operator?
How to Answer
- 1
Identify personal values related to quality and precision.
- 2
Mention satisfaction from producing high-quality finished products.
- 3
Express appreciation for teamwork and contributing to a larger goal.
- 4
Highlight enjoyment in learning new skills or improving processes.
- 5
Share enthusiasm for maintaining equipment and ensuring smooth operations.
Example Answers
I am motivated by the satisfaction of producing high-quality laminated products that meet our client's standards. Seeing the final product gives me a sense of achievement.
Technical Interview Questions
What types of laminating machines have you operated, and what are the key differences between them?
How to Answer
- 1
Identify the types of laminating machines you have experience with, such as roll laminators or pouch laminators.
- 2
Highlight specific features or differences between each type, like size, speed, or end product application.
- 3
Mention any relevant settings or adjustments you made during operation.
- 4
Emphasize your familiarity with maintenance or troubleshooting for different machines.
- 5
Keep your response concise but informative, demonstrating your expertise.
Example Answers
I have operated both roll laminators and pouch laminators. Roll laminators are great for larger prints and have a higher speed, whereas pouch laminators are better suited for smaller items and allow for more control over thickness.
Can you explain the different types of laminating materials and their specific applications?
How to Answer
- 1
Know the common types of laminating materials such as thermal, pressure-sensitive, and self-laminating films
- 2
Discuss specific applications like documents, identification cards, and photos for each type
- 3
Mention any benefits associated with each material type, like durability or ease of use
- 4
Use examples from personal experience or industry knowledge to showcase understanding
- 5
Keep the answer organized by type, highlighting key differences succinctly
Example Answers
There are a few main types of laminating materials. Thermal laminates are commonly used for documents as they provide a strong, glossy finish. Pressure-sensitive laminates work well for items like ID cards since they don’t require heat. Self-laminating films are great for quick jobs, often used for classroom materials.
Don't Just Read Laminating Machine Operator Questions - Practice Answering Them!
Reading helps, but actual practice is what gets you hired. Our AI feedback system helps you improve your Laminating Machine Operator interview answers in real-time.
Personalized feedback
Unlimited practice
Used by hundreds of successful candidates
What routine maintenance tasks do you perform on a laminating machine to ensure optimal performance?
How to Answer
- 1
Check and clean the rollers regularly to prevent adhesive build-up
- 2
Inspect the heating elements for proper temperature control
- 3
Lubricate any moving parts according to the manufacturer's specifications
- 4
Examine the machine for wear and tear to prevent breakdowns
- 5
Replace any worn or damaged parts immediately to maintain efficiency
Example Answers
I regularly clean the rollers to avoid adhesive residue, inspect the heating elements for temperature accuracy, and lubricate moving parts as instructed by the manual.
How do you assess the quality of a laminated product before it leaves the production line?
How to Answer
- 1
Check for uniform adhesion across the entire surface
- 2
Inspect for bubbles or wrinkles in the laminate
- 3
Verify correct thickness of the laminate against specifications
- 4
Examine edges for clean cuts and no peeling
- 5
Conduct visual inspections and use measuring tools as needed
Example Answers
I assess quality by checking for uniform adhesion, ensuring there are no bubbles or wrinkles, and measuring the thickness to confirm it meets specifications.
What parameters do you adjust on a laminating machine to achieve the desired finish?
How to Answer
- 1
Adjust the temperature for the type of laminate being used
- 2
Set the speed according to the thickness of the material being laminated
- 3
Regulate the pressure to avoid damage and ensure adhesion
- 4
Choose the correct film type for the desired finish (glossy or matte)
- 5
Monitor the rollers for proper alignment and cleanliness
Example Answers
To achieve the desired finish, I adjust the temperature based on the laminate type, set the speed for the material thickness, and regulate the pressure to ensure proper adhesion without damaging the project.
What common issues do you encounter with laminating machines, and how do you typically fix them?
How to Answer
- 1
Identify specific issues like jams, bubbles, or inconsistent sealing.
- 2
Explain the steps taken to troubleshoot each issue.
- 3
Mention tools or techniques used for repairs.
- 4
Highlight preventive measures to avoid problems.
- 5
Emphasize teamwork or communication if needed for complex issues.
Example Answers
One common issue is jams in the laminating feed. I typically clear the jam by carefully removing the material and checking for debris. Regular maintenance helps minimize this problem.
How do you determine the correct temperature and pressure settings for different laminating jobs?
How to Answer
- 1
Refer to the laminating machine's manual for recommended settings.
- 2
Consider the type of laminate and material being used; different materials require different settings.
- 3
Test on a sample before starting the main job to ensure quality.
- 4
Adjust settings based on feedback from the initial test run.
- 5
Document effective settings for future reference.
Example Answers
I start by checking the machine manual for preset settings based on the materials I'm using. Then, I run a test laminate to see how they respond before adjusting if needed.
What types of documentation do you keep while operating a laminating machine?
How to Answer
- 1
List the types of documents, such as production logs and maintenance records
- 2
Mention the importance of tracking material usage and quality control checks
- 3
Include safety inspection logs to ensure compliance with regulations
- 4
Emphasize regular updates to documentation for accuracy
- 5
Highlight communication with team members regarding changes
Example Answers
I keep detailed production logs to track output, material usage, and any quality issues that arise during operation.
What lamination techniques do you find most effective for different types of projects?
How to Answer
- 1
Identify specific lamination techniques like hot laminating and cold laminating.
- 2
Discuss how the choice of technique impacts durability and finish quality.
- 3
Provide examples of projects ideal for each technique.
- 4
Mention any equipment or materials that enhance the results.
- 5
Highlight the importance of matching the lamination method to the project requirements.
Example Answers
For printed marketing materials, I prefer hot laminating as it provides a glossy finish and better durability. Cold laminating is great for documents that need to remain flexible, like maps.
Are you familiar with any software used for monitoring or controlling laminating machines? If so, which ones?
How to Answer
- 1
List specific software you have used
- 2
Describe your experience with each software
- 3
Mention how the software improved your efficiency or effectiveness
- 4
If you haven't used any, express willingness to learn new tools
- 5
Be honest about your level of familiarity
Example Answers
I have experience with the GenuSys software, which I used to monitor the temperature and pressure settings on the laminating machine. It helped me ensure consistent quality and reduce waste during production.
Don't Just Read Laminating Machine Operator Questions - Practice Answering Them!
Reading helps, but actual practice is what gets you hired. Our AI feedback system helps you improve your Laminating Machine Operator interview answers in real-time.
Personalized feedback
Unlimited practice
Used by hundreds of successful candidates
Situational Interview Questions
If you notice that the lamination is bubbling, how would you respond to this issue during production?
How to Answer
- 1
Stop the machine immediately to prevent further defects.
- 2
Inspect the bubbling area to identify the cause.
- 3
Check temperature and pressure settings as they may be incorrect.
- 4
Adjust the machine settings if necessary and restart the process.
- 5
Communicate the issue to your supervisor to ensure quality control.
Example Answers
If I notice bubbling, I would stop the machine right away to prevent further damage. Then, I'd check the affected area and review the temperature and pressure settings. After making any necessary adjustments, I would restart and monitor the results closely.
What steps would you take if the laminating machine abruptly stops working during a critical production run?
How to Answer
- 1
Stay calm and assess the situation quickly.
- 2
Check for any visible error messages or warning lights.
- 3
Inspect the machine for obvious blockages or jams.
- 4
Refer to the troubleshooting manual for guidance.
- 5
Communicate with your supervisor and maintenance team immediately.
Example Answers
I would first stay calm and check for any error codes or warning lights on the machine. Then, I'd inspect for any visible jams or blockages. If nothing is apparent, I'd consult the troubleshooting manual and notify my supervisor and the maintenance team for assistance.
Don't Just Read Laminating Machine Operator Questions - Practice Answering Them!
Reading helps, but actual practice is what gets you hired. Our AI feedback system helps you improve your Laminating Machine Operator interview answers in real-time.
Personalized feedback
Unlimited practice
Used by hundreds of successful candidates
If a team member disagrees with your approach to a laminating task, how would you handle the situation?
How to Answer
- 1
Listen carefully to the team member's concerns without interrupting.
- 2
Acknowledge their viewpoint and validate their experience.
- 3
Share your reasoning behind your approach clearly and concisely.
- 4
Suggest a compromise or trial of both methods if feasible.
- 5
Maintain a positive attitude and focus on team collaboration.
Example Answers
I would first listen to my team member's concerns, acknowledging their viewpoint. Then, I would clearly explain my reasoning, and if possible, suggest trying both approaches to see which works better.
How would you prioritize your tasks if you were behind schedule on multiple laminating jobs?
How to Answer
- 1
Assess the deadlines for each job and identify the most urgent.
- 2
Consider the complexity of each job; prioritize simpler tasks that can be completed quickly.
- 3
Communicate with your team or supervisor about the situation for support.
- 4
Focus on maintaining quality while working efficiently; don’t compromise on standards.
- 5
Review workflow or equipment settings to identify any immediate improvements.
Example Answers
I would first check the deadlines and prioritize the jobs that are due soon. Next, I'd tackle the simpler tasks to get them off my plate quickly. I would also keep my team informed so we could possibly share the workload.
How would you handle a situation where a customer is dissatisfied with a laminated product due to a production error?
How to Answer
- 1
Acknowledge the customer's feelings and concerns immediately.
- 2
Apologize for the inconvenience caused by the error.
- 3
Ask for specifics about the issue to understand the problem.
- 4
Offer a solution, such as a replacement or a refund.
- 5
Follow up with the customer to ensure satisfaction after the solution is provided.
Example Answers
I would first acknowledge the customer's concerns and apologize for the production error. Then, I'd ask them to share the specifics of the issue so I can understand what went wrong. After that, I would offer to replace the product or issue a refund, based on their preference. Finally, I would follow up with them to confirm that they are satisfied with the resolution.
What would you do if you witnessed a colleague ignoring safety protocols near the laminating machine?
How to Answer
- 1
Stay calm and observe the situation carefully.
- 2
Approach the colleague privately and express your concerns.
- 3
Remind them of the safety protocols and the importance of following them.
- 4
If they continue to ignore the protocols, report the issue to a supervisor.
- 5
Always prioritize safety and the well-being of all team members.
Example Answers
I would first observe the situation to ensure I understand what's happening. Then, I would speak to my colleague privately to address my concerns about their actions and remind them of the safety protocols. If they don't change their behavior, I would escalate the issue to my supervisor.
If a new employee is struggling to learn the laminating machine, how would you assist them?
How to Answer
- 1
Offer hands-on demonstrations using the machine with them observing.
- 2
Encourage questions to clarify any confusing parts of the process.
- 3
Provide simplified step-by-step written instructions as a reference.
- 4
Set up practice sessions for them to familiarize with the machine.
- 5
Pair them with an experienced operator for mentorship and support.
Example Answers
I would offer to demonstrate the operation of the machine while the new employee watches, ensuring they understand each step. Then, I would encourage them to ask questions and provide them with simplified instructions they can refer to later.
How would you respond if there was a fire emergency during a laminating job?
How to Answer
- 1
Stay calm and assess the situation quickly
- 2
Activate the fire alarm and notify the supervisor
- 3
Use the closest fire extinguisher if it's safe to do so
- 4
Evacuate the area following the designated emergency exit plan
- 5
Do not use elevators during evacuation
Example Answers
In the event of a fire, I would first remain calm and quickly assess the situation. I would activate the fire alarm and inform my supervisor immediately. If it's safe, I would attempt to use a fire extinguisher to put out the fire. Then, I would follow the emergency exit plan to evacuate everyone safely.
How would you handle a situation where you ran low on laminating materials unexpectedly?
How to Answer
- 1
Notify your supervisor immediately about the shortage.
- 2
Assess current jobs in progress to prioritize their completion.
- 3
Check inventory for alternative materials that can be used.
- 4
Order more laminating materials as soon as possible to prevent delays.
- 5
Document the incident for future reference and to improve inventory management.
Example Answers
If I ran low on laminating materials, I'd first inform my supervisor to keep them in the loop. Then, I'd look at the work I have underway and focus on completing the most urgent jobs. I'd also check if there are any alternative materials available that could be used temporarily.
What would you do if you were under significant pressure to meet a tight deadline while operating the laminating machine?
How to Answer
- 1
Stay calm and assess the situation quickly.
- 2
Prioritize tasks based on urgency and importance.
- 3
Communicate with your team to delegate responsibilities.
- 4
Follow safety protocols to avoid mistakes.
- 5
If necessary, adjust machine settings to accelerate production.
Example Answers
I would take a deep breath to stay calm, then quickly assess the machine's status. I would prioritize any immediate repairs and communicate with my team to delegate tasks, ensuring we hit the deadline safely.
Don't Just Read Laminating Machine Operator Questions - Practice Answering Them!
Reading helps, but actual practice is what gets you hired. Our AI feedback system helps you improve your Laminating Machine Operator interview answers in real-time.
Personalized feedback
Unlimited practice
Used by hundreds of successful candidates
Laminating Machine Operator Position Details
Recommended Job Boards
These job boards are ranked by relevance for this position.
Related Positions
Ace Your Next Interview!
Practice with AI feedback & get hired faster
Personalized feedback
Used by hundreds of successful candidates
Ace Your Next Interview!
Practice with AI feedback & get hired faster
Personalized feedback
Used by hundreds of successful candidates