Top 30 Line Leader Interview Questions and Answers [Updated 2025]
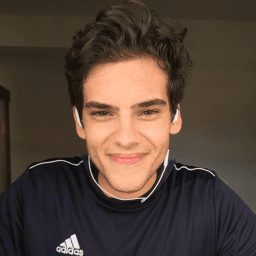
Andre Mendes
•
March 30, 2025
Are you preparing for a Line Leader interview and want to make a great impression? This blog post is your ultimate guide, featuring the most common interview questions tailored for the Line Leader role. Dive into expertly crafted example answers and insightful tips designed to help you respond confidently and effectively. Whether you're new to leadership or a seasoned pro, these strategies will elevate your interview game.
Download Line Leader Interview Questions in PDF
To make your preparation even more convenient, we've compiled all these top Line Leaderinterview questions and answers into a handy PDF.
Click the button below to download the PDF and have easy access to these essential questions anytime, anywhere:
List of Line Leader Interview Questions
Behavioral Interview Questions
Can you describe a time when you successfully led a team to achieve a specific goal on the production line?
How to Answer
- 1
Start with a clear situation that defines the context.
- 2
Identify the specific goal that was set for the team.
- 3
Explain the actions you took as a leader to guide the team.
- 4
Highlight the results achieved and how they benefited the production line.
- 5
Reflect on any lessons learned for future improvement.
Example Answers
In my previous role, our team was tasked with increasing production efficiency by 20% within three months. I organized daily briefings to assess progress and identify bottlenecks. By implementing a new workflow and encouraging team feedback, we achieved a 25% increase in efficiency. This not only met our goal but also improved team morale.
Describe a situation where you had to resolve a conflict between team members on the line. What was the outcome?
How to Answer
- 1
Identify the specific conflict and the individuals involved.
- 2
Explain the steps you took to mediate and resolve the issue.
- 3
Highlight communication techniques you used to ensure all voices were heard.
- 4
Describe the outcome and any improvements in team dynamics.
- 5
Mention any follow-up actions to prevent future conflicts.
Example Answers
In one instance, two team members disagreed over the assembly process. I brought them together to discuss their perspectives. Using active listening, I facilitated a conversation where both could express their concerns. We found a compromise that blended both their ideas, which improved efficiency and team morale.
Don't Just Read Line Leader Questions - Practice Answering Them!
Reading helps, but actual practice is what gets you hired. Our AI feedback system helps you improve your Line Leader interview answers in real-time.
Personalized feedback
Unlimited practice
Used by hundreds of successful candidates
Tell me about a time you encountered a major problem on the production line. How did you handle it?
How to Answer
- 1
Identify a specific problem you faced on the production line.
- 2
Describe the impact of the problem on operations or productivity.
- 3
Explain the steps you took to analyze and solve the issue.
- 4
Highlight the outcome and what you learned from the experience.
- 5
Keep your answer focused and relevant to the position.
Example Answers
During a rush order, a key machine malfunctioned and halted production. I quickly gathered the team to assess the situation and determined the issue was a faulty sensor. We worked together to bypass the sensor temporarily, allowing us to continue operations. I also contacted maintenance to ensure a permanent fix. As a result, we met our deadline and learned the importance of quick collaboration.
Give an example of how you adapted to a sudden change in production priorities.
How to Answer
- 1
Describe the situation clearly and briefly.
- 2
Explain the specific change in production priorities.
- 3
Detail your immediate response to the change.
- 4
Highlight the outcome of your actions.
- 5
Emphasize any collaboration with your team.
Example Answers
In my previous role, we had a sudden order increase for one product line while another was scaled back. I immediately gathered my team to assess our current resources and shifted our focus to the higher-priority order, reallocating staff and adjusting schedules. This collaboration allowed us to meet the new demand without sacrificing quality, and we delivered on time.
Describe a time when you had to communicate an important message to your team. How did you ensure everyone understood?
How to Answer
- 1
Identify the key message you needed to communicate
- 2
Choose an appropriate method to convey the message (e.g., meeting, email)
- 3
Engage your team by encouraging questions
- 4
Summarize the main points at the end of the communication
- 5
Follow up to confirm understanding or provide additional information if needed
Example Answers
In a recent project, I needed to inform my team about new safety protocols. I scheduled a team meeting, presented the key points clearly, and encouraged questions to address any confusion. After the meeting, I sent a summary email and asked for confirmation from each team member that they understood the changes.
Can you provide an example of how you managed your time effectively under a tight production deadline?
How to Answer
- 1
Identify a specific project with a tight deadline.
- 2
Outline the steps you took to prioritize tasks.
- 3
Mention any tools or techniques you used to stay organized.
- 4
Discuss how you communicated with your team to ensure alignment.
- 5
Include the outcome and what you learned from the experience.
Example Answers
In my last role, we had a critical order with a 48-hour turnaround. I prioritized tasks by creating a timeline and breaking down the workload. I used a project management tool to assign responsibilities and set reminders for myself and the team. Daily check-ins ensured everyone was on track, and we delivered the order on time with zero defects.
Tell me about a time you worked with other department leaders to improve overall production efficiency.
How to Answer
- 1
Choose a specific project where you collaborated with other departments.
- 2
Describe the challenge you faced and how different leaders contributed.
- 3
Explain the actions taken and the role you played in the process.
- 4
Highlight the results in terms of improved efficiency or productivity.
- 5
Use metrics or data to quantify the improvements when possible.
Example Answers
In my last role, I worked with the logistics and production teams to streamline our supply chain. We identified bottlenecks causing delays. By implementing a bi-weekly meeting, we coordinated better on inventory levels. This collaboration led to a 15% increase in timely product delivery over three months.
Describe an instance where you took initiative to improve an aspect of the line operation.
How to Answer
- 1
Reflect on a specific situation where you identified a problem.
- 2
Explain the steps you took to address the issue.
- 3
Highlight the outcome of your actions, using metrics if possible.
- 4
Mention any collaboration with team members or management.
- 5
Show how this improvement enhanced productivity or safety.
Example Answers
In my last role, I noticed that our assembly line was experiencing frequent slowdowns due to a backup in the packing station. I initiated a cross-training program for operators so they could assist in packing during peak times, which reduced downtime by 20% and improved overall efficiency.
Technical Interview Questions
What steps do you take to ensure the production line operates smoothly and efficiently?
How to Answer
- 1
Monitor production metrics regularly
- 2
Communicate with team members to address issues
- 3
Perform routine equipment checks and maintenance
- 4
Implement standard operating procedures (SOPs)
- 5
Encourage a culture of continuous improvement
Example Answers
I ensure the production line operates smoothly by closely monitoring our key production metrics and addressing any discrepancies immediately. I also conduct regular team meetings to keep everyone informed and engaged.
How do you implement quality control measures on the production line?
How to Answer
- 1
Establish clear quality standards for products.
- 2
Implement regular inspection points during the production process.
- 3
Utilize statistical process control to monitor quality data.
- 4
Train staff on quality control procedures and techniques.
- 5
Encourage a culture of quality through feedback and continuous improvement.
Example Answers
I implement quality control by first defining the quality standards for each product. Then, I set up inspection points throughout the production line to detect any issues early. I also train the team to recognize defects and encourage them to report any concerns immediately.
Don't Just Read Line Leader Questions - Practice Answering Them!
Reading helps, but actual practice is what gets you hired. Our AI feedback system helps you improve your Line Leader interview answers in real-time.
Personalized feedback
Unlimited practice
Used by hundreds of successful candidates
What safety protocols do you follow to maintain a safe working environment on the production line?
How to Answer
- 1
Discuss specific safety protocols you have implemented.
- 2
Mention training and communication with team members.
- 3
Emphasize personal accountability and responsibility in following safety procedures.
- 4
Provide examples of how you address safety violations or concerns.
- 5
Highlight your experience with audits or safety assessments.
Example Answers
I ensure that everyone is trained on proper PPE usage and hold regular safety meetings to discuss protocols. I also perform daily checks for compliance and encourage team members to report any unsafe conditions immediately.
How do you handle regular equipment checks and maintenance on the line?
How to Answer
- 1
Establish a routine schedule for equipment checks.
- 2
Train team members to identify potential issues.
- 3
Document all maintenance activities for accountability.
- 4
Communicate with maintenance personnel regularly.
- 5
Utilize maintenance logs to track performance and issues.
Example Answers
I set a weekly schedule for equipment checks and ensure every team member is trained to spot common problems. This way, we maintain high standards and address issues promptly.
How do you use production data to make improvements or solve issues on the line?
How to Answer
- 1
Identify key performance metrics to track, like cycle time and defect rates.
- 2
Regularly analyze data trends to spot recurring issues early.
- 3
Engage team members in data discussions to gather insights and suggestions.
- 4
Implement small experiments based on data findings to test improvements.
- 5
Document results and share successful strategies with the team.
Example Answers
I track cycle time and defect rates closely. When I see that the cycle time increases, I analyze the data and engage the team to find the causes, often resulting in process adjustments that lead to improvements.
How do you manage inventory and materials to ensure smooth production operations?
How to Answer
- 1
Implement a just-in-time inventory system to reduce excess stock.
- 2
Regularly review and forecast material needs based on production schedules.
- 3
Ensure strong communication with suppliers for timely deliveries.
- 4
Utilize inventory management software to track levels in real-time.
- 5
Train team members on proper inventory handling and storage practices.
Example Answers
I implement a just-in-time inventory approach to keep stock levels optimal, ensuring we have just what we need for production without excess.
Which KPIs do you believe are most important to track for optimizing line performance?
How to Answer
- 1
Identify KPIs relevant to your manufacturing line such as production efficiency, quality rates, and downtime.
- 2
Explain how each KPI impacts overall performance and productivity.
- 3
Use specific examples from past experiences to illustrate your points.
- 4
Discuss how you would monitor and analyze these KPIs regularly.
- 5
Mention how adjusting strategies based on KPI feedback can lead to improvements.
Example Answers
I believe production efficiency, quality rates, and downtime are the most crucial KPIs. For instance, in my last role, by focusing on reducing downtime, we improved our output significantly.
How do you apply Lean manufacturing principles to improve productivity on the line?
How to Answer
- 1
Identify waste in the current processes and eliminate it.
- 2
Standardize work procedures to ensure consistency and efficiency.
- 3
Encourage continuous improvement by involving the team in problem-solving.
- 4
Use visual management tools to track performance and progress.
- 5
Implement pull systems to optimize workflow and reduce inventory.
Example Answers
I focus on identifying waste in our current processes, such as excess movement or waiting times, and work with the team to eliminate these inefficiencies. For instance, we reduced changeover times by standardizing procedures.
What strategies do you use to schedule shifts effectively and ensure coverage at all times?
How to Answer
- 1
Analyze historical data to predict peak times and adjust schedules accordingly
- 2
Utilize scheduling software to automate shift assignments and track availability
- 3
Communicate clearly with team members about their preferred shifts and availability
- 4
Cross-train employees to fill in for each other when needed
- 5
Create a backup plan with on-call staff to handle sudden absences
Example Answers
I analyze past scheduling data to identify peak hours and adjust the staff schedule to ensure we have adequate coverage during those times. I also use scheduling software that allows employees to indicate their availability, making it easier to fill shifts efficiently.
Describe how you might integrate new technologies or systems into your production line.
How to Answer
- 1
Identify specific technologies that align with production goals
- 2
Engage team members in the integration process
- 3
Conduct pilot tests before full implementation
- 4
Train staff to ensure smooth transition
- 5
Monitor and evaluate the impact post-implementation
Example Answers
To integrate new technology, I would first research automation options that can enhance efficiency, such as robotic arms for assembly. I would then involve the team in workshops to gather their input and ensure buy-in, followed by a pilot test to iron out any issues before scaling up.
Don't Just Read Line Leader Questions - Practice Answering Them!
Reading helps, but actual practice is what gets you hired. Our AI feedback system helps you improve your Line Leader interview answers in real-time.
Personalized feedback
Unlimited practice
Used by hundreds of successful candidates
What reporting practices do you follow to keep upper management informed about line performance?
How to Answer
- 1
Implement daily production summary reports with key metrics.
- 2
Schedule weekly performance review meetings with management.
- 3
Use dashboards for real-time visibility of line performance.
- 4
Highlight trends and anomalies in your reports for efficient decision-making.
- 5
Ensure clear communication of any issues and proposed solutions.
Example Answers
I provide daily production summaries that include output numbers, efficiency rates, and any downtime incidents. This keeps management updated at a glance.
Situational Interview Questions
If faced with an unexpected delay on the line, how would you prioritize tasks to get back on schedule?
How to Answer
- 1
Assess the cause of the delay immediately
- 2
Identify critical tasks that must be completed to resume production
- 3
Delegate tasks effectively among team members
- 4
Communicate with the team to ensure everyone is aligned
- 5
Monitor progress closely and adjust priorities as needed
Example Answers
I would start by identifying the root cause of the delay, then focus on the critical tasks that directly impact production. I would assign those tasks to team members based on their strengths and ensure everyone knows their responsibilities. I would also keep an open line of communication to track our progress and make necessary adjustments.
Imagine a key piece of equipment breaks down during a shift. What steps would you take to address this immediately?
How to Answer
- 1
Quickly assess the situation to confirm the breakdown
- 2
Engage and communicate with team members about the issue
- 3
Implement immediate safety measures to prevent accidents
- 4
Notify maintenance and request urgent repairs
- 5
Consider alternative solutions to keep the line running if possible
Example Answers
First, I would confirm the equipment is indeed down by checking for any visible issues. Then, I would inform my team about the breakdown and ensure everyone is aware. I would take safety precautions right away, like shutting down the equipment if necessary, to keep everyone safe. Next, I would notify maintenance for urgent repairs. Depending on the situation, I might explore temporary workarounds to minimize downtime.
Don't Just Read Line Leader Questions - Practice Answering Them!
Reading helps, but actual practice is what gets you hired. Our AI feedback system helps you improve your Line Leader interview answers in real-time.
Personalized feedback
Unlimited practice
Used by hundreds of successful candidates
If you notice your team’s morale is low, how would you go about improving it?
How to Answer
- 1
Observe specific behaviors that indicate low morale.
- 2
Initiate a team meeting to discuss challenges and listen to everyone's concerns.
- 3
Recognize efforts and achievements of team members publicly.
- 4
Encourage team bonding activities to strengthen relationships.
- 5
Implement small wins or changes that can be completed quickly to boost confidence.
Example Answers
I would start by having a team meeting to openly discuss the issues affecting morale, allowing everyone to share their concerns. Recognizing individual contributions can help uplift spirits, and I would suggest a team-building activity to foster better relationships.
Suppose the line produces a batch of defective products. What actions would you take to rectify the issue and prevent future occurrences?
How to Answer
- 1
Identify the root cause of the defects through analysis
- 2
Communicate with the team to ensure everyone is aware of the issue
- 3
Implement immediate corrective actions to address the current batch
- 4
Document the findings and share them for further training
- 5
Review and update processes to prevent recurrence
Example Answers
First, I would analyze the production process to find the root cause of the defects. Then, I would gather the team and inform them of the situation. After that, we would implement a corrective action, like halting production of the defective batch. I would document everything and recommend training sessions to avoid this issue in the future.
A new method is introduced that could improve efficiency by 20%. How would you approach evaluating and possibly implementing it?
How to Answer
- 1
Gather information on the new method and its benefits.
- 2
Assess the current processes to identify potential integration points.
- 3
Conduct a pilot test with a small team to evaluate the effectiveness.
- 4
Collect feedback from the team during the pilot.
- 5
Analyze data post-pilot to decide on full implementation.
Example Answers
I would start by researching the new method and how it works. Next, I'd evaluate our current processes to see where this method can fit in. I would then run a pilot test with a small group to gauge its effectiveness and gather feedback from the team to refine the approach before a full rollout.
If a safety incident occurs, what are your immediate priorities and the subsequent steps you would take?
How to Answer
- 1
Ensure the safety of all individuals involved.
- 2
Assess the situation to determine the severity of the incident.
- 3
Report the incident to the appropriate authorities as per protocol.
- 4
Implement emergency procedures if necessary.
- 5
Document the incident and gather all relevant information for a follow-up.
Example Answers
My first priority would be to ensure everyone's safety by removing any immediate dangers. Then, I would assess the situation to understand what happened, report it according to our safety protocols, and activate emergency procedures if required. Finally, I would document everything for further investigation.
Imagine you need to reallocate resources on the production line due to a sudden priority change. How would you manage this?
How to Answer
- 1
Assess the immediate impact of the priority change on current operations.
- 2
Engage with team members to gather input on resource allocation.
- 3
Communicate clearly about the changes and expected outcomes.
- 4
Implement changes quickly but carefully to minimize disruption.
- 5
Monitor the production line closely after reallocating resources for any issues.
Example Answers
First, I would evaluate how the priority shift affects our current workflow. Then, I would consult with the team to get their insights on how best to reallocate resources. After that, I would communicate the new plan, ensuring everyone understands their roles. I would then make the adjustments, overseeing the process closely to address any hiccups in real-time.
How would you handle training a new team member with varying levels of experience on the production line?
How to Answer
- 1
Assess the new member's current skills and experience level first.
- 2
Customize the training plan to fit their knowledge and pace.
- 3
Pair them with a more experienced colleague for mentorship.
- 4
Provide clear, step-by-step instructions and hands-on practice.
- 5
Schedule regular check-ins to track progress and address concerns.
Example Answers
I would start by assessing the new team member's skills to tailor their training. For someone with more experience, I would assign complex tasks earlier while ensuring I still support them with resources they might need.
You identify a bottleneck causing delays on the line. What approach would you take to address this challenge?
How to Answer
- 1
Analyze the specific causes of the bottleneck
- 2
Engage with team members for their insights and suggestions
- 3
Implement a trial solution to test effectiveness
- 4
Monitor results and gather feedback
- 5
Document the changes for future reference
Example Answers
I would start by analyzing the data to identify the specific cause of the bottleneck. After that, I would gather input from my team, as they often have valuable insights. Then, I would implement a temporary solution to see if it alleviates the delays. Finally, I would monitor the results closely and document what worked or didn’t for future improvements.
A new project requires close collaboration with another department. How would you facilitate this collaboration to ensure success?
How to Answer
- 1
Initiate a kickoff meeting with both departments to align goals.
- 2
Establish clear roles and responsibilities to avoid overlap.
- 3
Use collaborative tools for ongoing communication and updates.
- 4
Schedule regular check-ins to monitor progress and address issues.
- 5
Encourage open feedback to improve team dynamics and collaboration.
Example Answers
I would start by organizing a kickoff meeting where both departments can discuss project goals and expectations. This sets a clear direction and helps everyone understand their roles.
Don't Just Read Line Leader Questions - Practice Answering Them!
Reading helps, but actual practice is what gets you hired. Our AI feedback system helps you improve your Line Leader interview answers in real-time.
Personalized feedback
Unlimited practice
Used by hundreds of successful candidates
Line Leader Position Details
Recommended Job Boards
CareerBuilder
www.careerbuilder.com/jobs/production-line-leaderZipRecruiter
www.ziprecruiter.com/Jobs/Production-Line-LeaderThese job boards are ranked by relevance for this position.
Related Positions
- Production Leader
- Production Line Worker
- Line Operator
- Production Worker
- Production Line Assembler
- Sign Maker
- Box Worker
- Body Maker
- Tube Pusher
- End Maker
Similar positions you might be interested in.
Ace Your Next Interview!
Practice with AI feedback & get hired faster
Personalized feedback
Used by hundreds of successful candidates
Ace Your Next Interview!
Practice with AI feedback & get hired faster
Personalized feedback
Used by hundreds of successful candidates